цель внедрения на производстве, принципы, инструменты
Для успешной организации бизнеса важно применение системы бережливого производства. В самом названии этой системы заложен главный принцип – наладить работу таким образом, чтобы исключить лишние трудовые, временные, финансовые и другие затраты. Если говорить о том, что такое бережливое производство кратко, то оно представляет собой концепцию грамотного управления, которая позволяет оптимизировать любые бизнес-процессы.
Основные цели бережливого производства
Применение концепции позволяет достигнуть несколько целей. Обобщающей же целью внедрения бережливого производства является полномасштабное снижение затрат всех ресурсов, используемых в бизнесе, без ущерба для качества продукции, товара или услуги.
Потери, на выявление которых ориентировано внедрение бережного производства, касаются:
- Перепроизводства, когда производятся никому не нужные продукты либо выпускается слишком много продукции;
- Запасов, когда в производственный процесс поступает избыточное количество материалов, необходимых для изготовления продукта;
- Избыточной обработки – усилия, которое не влияет на итоговую ценность продукта для клиента-потребителя;
- Лишних движений при перемещении работников, инструментов, оборудования, что никак не влияет на улучшение продукции;
- Дефектов, брака продукции, которая проверяется, сортируется, при необходимости утилизируется, либо происходит смена ее сортности, производится ее ремонт, замена;
- Ожидания – затрат по времени, которые связаны с ожиданием работников, материалов, оборудования, информации;
- Транспортировкой – перемещением частей либо материалов внутри производственной организации.
Принципы и инструменты бережливого производства
Любая концепция строится на определенных по своим особенностям принципах. Основными принципами бережливого производства на предприятии является:
- Определение ценности производимого продукта для конечного клиента-потребителя.
- Определение потока создания ценности для выпускаемой продукции.
- Обеспечение непрерывности обновленного производства продукта.
- Стремление делать только то, что нужно конечному потребителю.
- Постоянное совершенствование бизнеса.
Рассмотрим более подробно каждый из вышеперечисленных 5 принципов внедрения бережливого производства.
Принцип №1 позволяет выявить, что ценно в выбранном продукте для конечного потребителя. Нередко на предприятии прилагаются лишние усилия, которые не влияют на ценность продукта. Именно их нужно определить, чтобы добиться желаемого результата от внедряемой системы.
Принцип №2 дает возможность определить потери в ходе производства продукта. Для этого следует описать все действия, предпринимаемые на предприятия, результатом которых является поставка продукта конечному потребителю.
Принцип №3 обеспечивает проведение модернизации действий в производственной цепочке так, чтобы они выполнялись в непрерывном режиме. Между действиями не должно быть временных и других потерь.
В ходе применения принципа №4 получается добиться производства продукта только того вида и в том количестве, которое требуется клиентам-потребителям. Учет потребностей последних обязателен, если поставлена цель организовать бережливое производство на предприятии.
Принцип №5 – очень важный при использовании технологии бережливого производства. Производство будет оставаться бережливым только путем постоянного его совершенствования, сокращения ненужных усилий и затрат.
В результате применения всех базовых принципов получится добиться существенного снижения издержек. Итог внедрения даст возможность:
- Предложить потребителю нужный ему продукт;
- Снизить стоимость продукта при необходимости;
- Повысить объемы продаж за счет удовлетворенного в своих потребностях клиента.
Методы, инструменты внедрения бережливого производства
- Картирование потока создания ценности – создаваемая схема графиков с изображением базисных показателей, позволяющая отобразить взаимосвязь всех производственных потоков.
- Вытягивающее поточное производство – детальная схема производственной организации, строящаяся на потребностях каждого последующего этапа.
- Канбан – система регулирования бизнес процессов как внутри предприятия, так и за его пределами, позволяет снизить потери, имеющие отношение к запасам, перепроизводству.
- Кайдзен — инструмент непрерывного совершенствования, заключающийся в постоянном улучшении качества.
- Система 5С — грамотно внедряемая технология создания максимально эффективного рабочего места.
- SMED система — переналадка оборудования, выполняемая в быстром режиме.
- Система TPM или Total Productive Maintenance —общий уход за производственным оборудованием.
- Система JIT или Just-In-Time (т.е. точно вовремя) – управленческий подход к организации производством, основанный на потребительском спросе. Дает возможность изготавливать продукцию в нужном объеме, точно в нужное время.
- Визуализация, которая позволяет видеть состояние производства, предупредить и отладить производственные процессы.
- U-образные ячейки – система расположения использующегося производственного оборудования в форме буквы «U».
Основные методы и инструменты бережливого производства являются практическими элементами для эффективного достижения поставленной цели.
Область применения инструментов бережливого производства
Сегодня методология бережливого производства применяется в различных производственных сферах. Она используется в разных отраслях, на больших и менее крупных предприятиях. Применение метода бережливого производства наблюдается в деятельности компаний, занимающихся:
- Производством
- Оказанием логистических услуг;
- Банкингом и торговлей;
- Созданием и внедрением информационных технологий;
- Строительством;
- Медицинским обслуживанием;
- Добычей нефти, различных полезных ископаемых и пр.
Важно, что бережливое производство на предприятии, занимающемся определенным видом деятельности, подлежит адаптации к конкретным производственным условиям. В этом случае всегда получается добиться повышение уровня эффективности работы, сокращая различного типа потери.
Статьи по теме «Бережливое производство»:
Поделиться в соц. сетях
Методы бережливого производства — блог RDV IT
Вопросы, рассмотренные в материале:
- Откуда в Россию пришло бережливое производство?
- Каковы принципы бережливого производства?
- Какие есть инструменты и методы бережливого производства?
- Как происходит внедрение методов бережливого производства?
- Каких ошибок избегать в процессе?
Задача по повышению производительности труда никогда не теряет актуальности. Управленцы постоянно озабочены тем, чтобы эффективность работы предприятия росла, неустанно ищут пути снижения затрат и увеличения количества выпускаемой продукции. Одним из способов добиться желаемых результатов являются методы бережливого производства. Они позволяют оптимизировать деятельность компании и добиться значительного роста производительности – от 20 до 400 % за один год. Даже частичное внедрение некоторых инструментов приводит к положительным итогам за короткие сроки. В чем суть этой методики? Давайте разбираться.
Откуда пришло бережливое производство
Родоначальником теории бережливого производства является Тайити Оно. Приступив в 1943 году к работе в Toyota Motor Corporation, он собирал и анализировал опыт мировых лидеров в этой отрасли, чтобы взять все лучшее для создания собственной системы. Она появилась в середине 50-х годов и получила название Производственная система Toyota, или Toyota Production System (TPS). На Западе ее стали называть Lean production, Lean manufacturing, Lean. Тайити Оно был не одинок в своем стремлении создать идеальную методику организации работы компании, в этом ему помогал Сигео Синго, которому принадлежит авторство инструмента SMED.
До японских новаторов похожие идеи пытался внедрять Генри Форд, но в 20-годы XX века к такому взгляду на производство зарождающийся крупный бизнес еще не был готов. Сегодня методы бережливого производства признаются и используются крупнейшими компаниями мира, в том числе Boeing, Alcoa и United Technologies (США), Porsche (Германия), Инструм-рэнд (Россия). После 1986 года, когда Масааки Имаи выпустил книгу «Kaizen: The Key to Japan’s Competitive Success», философия кайдзен стала распространяться по всему миру.
На стадии первоначального становления концепции бережливого производства она находила применение в основном в дискретном производстве, в частности, в автомобилестроении. Следующим этапом ее развития стала адаптация к условиям производства с непрерывным циклом. Впоследствии методы бережливого производства стали использоваться практически во всех сферах деятельности, включая здравоохранение, сферу услуг, коммунальное хозяйство и торговлю.
Сегодня принципы философии кайдзен не ограничиваются рамками предприятий. Они широко внедряются в сферу общения между потребителем и поставщиком, применяются для оптимизации процесса доставки товаров и послепродажного обслуживания. Многочисленные международные конференции, инициаторами проведения которых являются Lean Enterprise Institute (США) и Lean Enterprise Academy (Великобритания), помогают распространению лин-идей в логистике и оказании услуг.
В продвижении методов бережливого производства заинтересовано и государство: во многих странах на это выделяются специальные гранты. Предприятия сегодня вынуждены работать в условиях сильнейшей конкуренции, поэтому бережливое производство давно стало востребованным способом, помогающим в кризисной ситуации выпускать продукцию высокого качества, но по доступным для потребителей ценам.
5 принципов любого инструмента бережливого производства
Принцип № 1. Очень важно понимать, в чем конкретно заключается ценность товара или услуги для покупателя и клиента. В процессе создания продукта обычно задействовано много этапов, и на каждом из них осуществляются какие-то действия. Однако, с точки зрения конечного потребителя, одни из них важны, а другие нет. Если производитель четко представляет, какие процессы наиболее ценны для клиентов, он сможет сконцентрироваться на основных моментах, от которых зависит, будут ли удовлетворены покупатели.
Принцип № 2. Среди множества действий, выполняемых сотрудниками организации, всегда есть те, которые можно упростить, оптимизировать или удалить совсем без вреда для конечного результата. Чтобы обнаружить эти слабые звенья, необходимо сначала подробно описать все процессы, сопровождающие создание продукта.
Принцип № 3. Если между отдельными операциями наблюдаются простои, стоит задуматься о том, как перестроить производственный процесс для их исключения. Ситуации, когда дальнейшая работа не может быть продолжена из-за ожиданий любого рода, необходимо искоренить. Это сложный этап, поскольку для бесперебойной работы предприятия может понадобиться масштабная перестройка. Однако затраты на удаление причин простоев быстро окупятся.
Принцип № 4. Даже самый лучший продукт не представляет ценности, если он не востребован потребителем. Ориентация на нужды клиентов с точки зрения качества товара и его количества лежит в основе успешной деятельности любого предприятия.
Принцип № 5. Достичь совершенства сложно, но стремиться к постоянному росту эффективности производства – насущная потребность для всех компаний, которые хотят выигрывать в конкурентной борьбе. Методы бережливого производства, внедряемые на постоянной основе, могут стать надежной базой для оптимизации деятельности предприятия.
Самые популярные методы бережливого производства
5S
Добиться идеального качества выполнения производственных процессов невозможно без грамотной организации рабочего места.
Основные этапы:
- сортировка принадлежностей и инструментов, удаление лишнего;
- удобное расположение нужных вещей;
- содержание рабочего места в чистоте;
- создание стандартов, помогающих контролировать результат;
- постоянное совершенствование.
Проблемы, вызванные неправильной организацией производственного пространства, не так безобидны, как кажется на первый взгляд. Потери времени, которые неизбежно возникают из-за беспорядка на рабочем месте, в итоге приводят к низкой эффективности труда. Не глядя, взять инструмент с полки, где он находится всегда или полчаса искать его в груде других приспособлений – что более выгодно для предприятия в целом? Ответ очевиден.
Andon (Андон)
Инструмент, с помощью которого осуществляется визуальное и звуковое информирование о возникшей проблеме. Обнаружив неполадку на своем этапе работ, сотрудник подает сигнал, по которому прибывает старший смены и оперативно ликвидирует неисправность без остановки конвейера.
Такой подход позволяет быстро устранить неполадки, не допуская более серьезных поломок и сводя к минимуму вероятность длительного простоя.
Bottleneck analysis (Анализ узких мест)
Производственный процесс детально анализируется, чтобы найти этап, из-за которого невозможно увеличить выпуск продукции за определенный промежуток времени. Узкое место, или «бутылочное горлышко», тормозит рост производительности, а его расширение позволяет значительно улучшить итоговые показатели.
Continuous Flow (Непрерывный поток)
Любая задержка означает удорожание производства и снижение рентабельности. Грамотно выстроенный процесс означает полное отсутствие перерывов между отдельными операциями. Например, если работа над созданием продукта не может продолжаться, поскольку не прибыли комплектующие от поставщика, необходимо решать проблему с логистикой.
Gemba (Поле битвы)
Производственные процессы требуют постоянного участия руководства компании, ведь именно в цехах и на конвейере протекает основная деятельность предприятия.
Непосредственное присутствие топ-менеджеров не только дисциплинирует работников, но и сокращает до минимума время между выявлением проблемы и ее решением. Находясь в гуще событий, руководители компании лично контролируют процесс, благодаря чему значительно уменьшается срок утверждения и внесения необходимых изменений.
Heijunka (Планирование)
Этот метод управления бережливым производством основан на распределении заказов. Продукция не выпускается сплошным потоком, полученные заявки делятся на небольшие по объему партии. Для каждой назначаются сроки выполнения работ. При таком подходе проще следить за качеством, легче контролировать график производства и предотвращать вероятность его срыва. В результате заказчики получают свои партии вовремя, а предприятие работает без авралов с равномерной загрузкой мощностей.
Такая ориентированность компании на спрос повышает ее эффективность, поскольку сырье приобретается в объеме, необходимом для выпуска заказанного количества товаров. Замороженные активы в виде готовой непроданной продукции сведены к минимуму, вся партия уходит к заказчику сразу по окончании производственного процесса.
Hoshin Kanri (Развертывание политики)
Этот метод связывает воедино глобальные цели предприятия и ежедневную деятельность производственного звена. В результате нет отрыва стратегии от тактики, который характерен для многих компаний.
Происходит постоянный контакт между руководством и сотрудниками, для каждого работника формулируются цели, к достижению которых тот стремится. Управленцы и их подчиненные регулярно взаимодействуют, что положительно отражается на успешности предприятия.
Jidoka (Автономизация)
Задействованное в процессе выпуска продукции оборудование снабжается элементами интеллекта, благодаря чему у него появляется способность самостоятельно выявить проблему и подать сигнал.
В результате внедрения этого метода каждый сотрудник без труда следит за работой сразу нескольких автономных устройств. Кроме того, своевременное выявление и устранение неполадок позволяет минимизировать потери, ведь вероятность выпуска бракованных деталей практически исключена.
Kaizen (Постоянное улучшение)
Метод kaizen tools подразумевает формулирование общих целей и координацию усилий всех работников компании для создания и поддержания единой корпоративной культуры.
В результате такого подхода каждый сотрудник на своем месте делает все возможное для сокращения издержек, повышения эффективности и роста производительности. Эти усилия суммируются и в целом создают общую нацеленность на бережливое отношение к ресурсам, рабочему времени и конечному продукту.
JIT, Just in time (Точно в срок)
В основе функционирования производства при использовании этого метода лежит изготовление определенного количества продукции, которое заказал клиент. Понятие прогнозируемого спроса отходит на второй план. Для реализации такого подхода необходимо одновременное использование целого ряда инструментов бережливого производства − «Takt time», «Continuous Flow», «Kanban» и «Heijunka».
В результате происходит снижение запасов сырья и нереализованной продукции, можно обходиться производственными и складскими помещениями меньшего размера. Расходы предприятия снижаются, появляется возможность оптимизировать финансовые потоки.
Kanban (Вытягивающая система)
Данный метод ориентирован на регулирование потоков готовой продукции, как на этапе производства, так и после его завершения. Для оповещения о потребности в конкретных деталях или комплектующих применяются сигнальные карты.
В итоге внедрения этого лин-инструмента наблюдается снижение невостребованных складских запасов, сводятся к минимуму потери, упрощается инвентаризация.
KPI (Ключевые индикаторы производительности)
Для мотивации сотрудников компании используется система индикаторов, помогающая анализировать их деятельность по приоритетным направлениям работы предприятия.
KPI незаменимы при выявлении наиболее вероятных рисков, а также полезны для достижения стоящих перед коммерческой организацией стратегических целей.
Muda (Потери)
От того, что не является важным для конечного потребителя, необходимо избавляться. В этом смысл еще одного метода бережливого производства.
Анализ всех процессов, происходящих в компании, позволит определить, какие из них не имеют ценности для клиентов и должны быть упразднены.
PDCA (Планируй-Делай-Проверяй-Действуй)
Следующий метод направлен на внедрение различных улучшений или изменений:
- Планируй (тщательное планирование).
- Делай (претворение плана в жизнь).
- Проверяй (контроль полученных результатов).
- Действуй (анализ сделанного с точки зрения продуктивности, поиск вариантов для повышения эффективности).
OEE (Overall Equipment Effectiveness, Полная эффективность оборудования)
Метод нацелен на отслеживание потерь трех типов: по готовности, производительности и качеству.
В результате его внедрения становится ясно, какова степень эффективности используемой производственной базы. Максимальное значение показателя (100 %) говорит о том, что компания работает на идеальном оборудовании, вероятность выпуска бракованных изделий исключена, простоев и задержек не случается. Отставание по одной из составляющих приводит к снижению OEE.
Poka-Yoke (Защита от ошибки, Защита от дурака)
Этот метод бережливого производства предназначен для исключения вероятности возникновения различных ошибок в ходе создания продукта. В идеале компании стремятся к нулевому показателю дефектности.
Внедрение такого инструмента позволяет предприятию значительно экономить, поскольку затраты на предупреждение проблем, связанных с качеством, гораздо ниже тех, которые предстоят в случае их обнаружения спустя значительное время. Случаи, когда производители автомобилей отзывают целую партию машин из-за одной бракованной детали, нередки.
Анализ основных причин
Принцип «пяти почему», положенный в основу этого метода, позволяет выявлять и исключать из производственного процесса негативные факторы. Речь идет о том, что в каждом случае, когда выявляется отрицательный момент, необходимость его сохранения должна подтверждаться пятикратным «потому что…». Если убедительных доводов меньше, такой фактор необходимо устранить.
Visual Factory (Визуализация производства)
При помощи простых цветовых, звуковых и подобных им индикаторов упрощается обмен информацией между участниками производственного процесса. Это ускоряет реакцию сотрудников на возникновение проблемных или аварийных ситуаций.
VSM (Value Stream Mapping, Карта потока создания ценности)
Метод бережливого производства VSM помогает при выделении процессов, по итогам которых ценность продукта увеличивается. Наглядность такого подхода упрощает задачу менеджеров по долгосрочному планированию изменений.
TPM (Всеобщее обслуживание оборудования)
Говорить о том, насколько важна для производства постоянная готовность и полная исправность оборудования, излишне. Суть данного метода состоит в привлечении к обслуживанию станков и аппаратов не только сотрудников специального подразделения, но и всех остальных работников компании.
В итоге повышается личная ответственность персонала, небрежность в работе сводится к минимуму, количество аварий, а значит, и вынужденных простоев значительно снижается.
Takt time (Время такта)
Под этим термином скрывается показатель, характеризующий периодичность приобретения продукта покупателем. В зависимости от специфики компании он также может означать срок, в течение которого предприятие выполняет заказ на выпуск товара. Для его расчета применяется формула:
Время такта = Плановое время производства / Спрос потребителя
Этот метод бережливого производства необходим для определения производительности, адекватной имеющемуся потребительскому спросу на определенный продукт.
Стандартизированная работа
Когда в компании используется много единиц аналогичного оборудования, самым эффективным считается выполнение производственных операций по единому стандарту. Специалистами создается инструкция, в которой прописаны все действия работника на основе обобщения и компиляции имеющегося опыта. Документ дополняется в случае необходимости, в результате всегда действует его актуальный вариант.
Четкое следование стандартам сводит к минимуму вероятность появления брака и повышает производительность.
SMART (Умные цели)
В названии данного метода бережливого производства скрыты следующие слова: Specific, Measurable, Attainable, Relevant and Time-Specific. Это значит, что цели, которые ставит перед собой компания, должны быть конкретными, измеримыми, достижимыми, релевантными и иметь временные рамки для выполнения.
Если коммуникация между работниками и подразделениями предприятия не налажена, а задачи трактуются по-разному, потерь не избежать. Грамотно сформулированная цель помогает понять, к чему стремится организация в целом и каждый из сотрудников в частности.
Шесть причин снижения производительности
Главных факторов, негативно влияющих на производительность труда, шесть: поломки, частая наладка, незапланированные перерывы, снижение заданного темпа, отказ оборудования, проблемы с работниками.
Для компании, регулярно теряющей прибыль по этим причинам, такое положение служит важным сигналом. Исправить ситуацию поможет последовательное устранение всех факторов, вызывающих простой.
SMED (Быстрая переналадка)
Любое оборудование нуждается в регулярном обслуживании. Этот метод бережливого производства основан на смещении акцента с внутренних действий, то есть наладки с полной остановкой производственной линии, на внешние, когда работы проводятся без прекращения выпуска продукции.
В результате сокращается время, в течение которого предприятие простаивает, а срок службы оборудования, напротив, увеличивается благодаря постоянному обслуживанию в рабочем режиме.
Стремление к росту эффективности – основа развития каждой коммерческой организации. Даже если использовать не все 25 методов бережливого производства, а только отдельные инструменты оптимизации, вскоре можно будет отметить их положительное влияние на успешность компании.
Внедрение методов бережливого производства
Необходимость применения лин-концепции прекрасно осознают многие отечественные производственники. Опыт зарубежных и ведущих российских предприятий убедительно доказывает эффективность методов и инструментов бережливого производства. Однако процесс внедрения этой системы может протекать не так гладко, как в иностранных компаниях, и на это есть несколько причин.
Главное отличие между предприятиями в России и за рубежом состоит в различной степени прозрачности процессов и регулярности менеджмента. Отечественные компании вынуждены преодолевать самые разные бюрократические препоны и формальности, в результате чего их деятельность не столь открыта, как у западных коллег.
Для эффективного внедрения лин-инструментов придется ориентироваться на максимальную прозрачность бизнес-процессов, пытаться отойти от устоявшихся шаблонов. Российская специфика, на которую любят ссылаться бизнесмены, должна уступить место общемировому опыту организации и оптимизации производства.
Еще один фактор, тормозящий внедрение методов системы бережливого производства на отечественных предприятиях − стремление к извлечению максимальной прибыли за счет роста отпускной цены. Современные условия диктуют совершенно другой подход, а именно сокращение потерь, которое в конечном итоге позволит достичь цели в плане прибыльности предприятия, но не за счет потребителя, а в результате грамотного распределения временных и человеческих ресурсов при создании продукта.
Какие шаги должны предшествовать внедрению Lean manufacturing techniques?
В первую очередь, следует смириться с тем, что принципы и методы бережливого производства будут эффективны только в том случае, когда они работают постоянно, а не служат палочкой-выручалочкой при возникновении кризисных ситуаций. Это глобальный процесс, требующий от руководства предприятия внесения серьезных изменений в структуру компании.
Наибольшую сложность, как правило, вызывает необходимость отказаться от привычных шаблонов в деятельности и рядовых работников, и топ-менеджмента. Успех придет только через понимание неизбежности вносить изменения и готовность к длительному переходному периоду.
С чего начать?
Конечно, каждому предприятию, решившему внедрить основные методы бережливого производства, предстоит свой путь. Это связано со спецификой отрасли и устоявшейся структурой компании. Однако можно выделить ряд шагов, общих для всех, кто стремится оптимизировать работу на основе лин-концепции. Для подробного изучения этого вопроса можно порекомендовать книгу Джеймса Вумека и Дэниела Джонса «Бережливое производство. Как избавиться от потерь и добиться процветания вашей компании». Глава 11 содержит перечень основных шагов по внедрению.
-
Найдите агента перемен.
Миссию по внесению изменений в деятельность предприятия, как правило, возлагают на одного из руководителей. Он выступает инициатором глобальных перемен, на нем же лежит ответственность за их претворение в жизнь.
-
Раздобудьте знания.
Внедрение методов бережливого производства на предприятии требует постоянной подпитки знаниями со стороны агента перемен. Для остальных сотрудников он должен стать источником сведений по всем вопросам, имеющим отношение к новым инструментам. С получением знаний самим инициатором изменений никаких проблем не возникнет: есть масса литературы по теме, регулярно проводятся обучающие семинары, курсы и тренинги. Для вдохновения полезно посетить несколько предприятий, на которых эта система давно и с успехом действует.
-
Используйте (или создайте) кризис, который станет рычагом.
Не секрет, что пока дела в компании идут более-менее хорошо, о необходимости задействовать прогрессивные методы оптимизации мало кто задумывается. Кризисная ситуация может стать прекрасным поводом внедрить основные методы бережливого производства.
-
На время забудьте о стратегии.
Приоритетом на первом этапе должно стать стремление к устранению потерь.
-
Опишите потоки создания ценности.
Проанализируйте текущее положение дел, включая материальные, финансовые и информационные потоки. На основе полученного описания создайте карту того состояния, которого будет целью компании, удалив процессы, не представляющие ценности для клиента. Затем составляется план по переходу от имеющегося на данный момент положения к идеальному.
-
Как можно быстрее начните с доступной, но важной и видимой всем деятельности.
Быстрые результаты вдохновляют, поэтому для первых шагов рекомендуется выбирать те производственные участки, где перемены будут видимы и осязаемы. Другой вариант – начинать с оптимизации процессов, выполнение которых находится в плачевном состоянии, хотя для предприятия они чрезвычайно важны.
-
Требуйте немедленных результатов.
Методы бережливого производства требуют определенного времени для внедрения, но отсутствие каких бы то ни было результатов должно обеспокоить и заставить искать причину.
-
Как только появится удобная возможность, двигайтесь дальше.
За первыми результатами должно последовать распространение новых методов на другие участки, причем не только те, где непосредственно создается продукт, но и на работу офисных сотрудников. Философия кайдзен, распространяемая на все сферы деятельности компании, позволит постоянно совершенствовать протекающие в ней процессы.
Кратко этапы внедрения системы бережливого производства выглядят так:
- определение ценности для потребителя;
- построение карты создания ценности;
- организация непрерывного потока создания ценности;
- организация «вытягивания» продукта потребителем;
- непрерывное улучшение процессов.
Это всего лишь ориентир к действию, каждая компания исходит из собственных потребностей по оптимизации деятельности. Однако суть концепции неизменна: производство будет максимально эффективным, когда оно ориентировано на клиента, из него исключены процессы, не создающие ценность, а простои сведены к минимуму.
Топ-3 статей, которые будут полезны каждому руководителю:
3 типичные ошибки применения методов бережливого производства
- Самая частая ошибка, которую допускают руководители компаний, − восприятие методов бережливого производства в качестве повода сократить число работников и снизить себестоимость продукта. Такой подход противоречит философии кайдзен, которая направлена на оптимизацию имеющейся производственной системы путем сокращения потерь и ориентации на ценность товара для потребителей.
- У многих топ-менеджеров, впечатленных результатами деятельности компаний, которые используют методы бережливого производства, появляется соблазн внедрить один из инструментов без планомерной работы по переводу предприятия на систему в целом. Опасность заключается в том, что отдельные улучшения в работе могут проявиться, но ожидать серьезных изменений не приходится. Без системного подхода эти попытки оптимизировать потери и добиться высокой производительности обречены на провал.
- Сфера практического применения методов бережливого производства на начальном этапе внедрения должна быть ограничена. Огромная роль в этот период отводится агенту перемен – лидеру, который инициирует изменения, поддерживает других менеджеров знаниями и информацией, следит за планомерным и постепенным переходом деятельности компании на принципы лин-концепции. Сложность чаще всего заключается именно в поиске человека, мнение которого будет одинаково авторитетным и для руководящего звена, и для рядовых сотрудников предприятия.
Методы бережливого производства для сокращения потерь и увеличения эффективности
Вопросы, рассмотренные в материале:
- Что такое бережливое производство
- Какие методы использует бережливое производство
- Насколько методы бережливого производства эффективны в России
- Какие существуют методы внедрения бережливого производства
По максимуму исключить производственные потери и издержки стремится каждая современная компания. Для этого многие прибегают к такому методу управления, как бережливое производство. Концепция подразумевает участие всех без исключения сотрудников в оптимизации предприятия. Ниже мы подробно разберем методы бережливого производства, рассмотрим все необходимые инструменты и способы внедрения.
Что такое бережливое производство
Lean manufacturing, или lean production, что и переводится как «бережливое производство», это специфический способ управления организацией, направленный на то, чтобы вывести ее деятельность на качественно другой уровень путем избавления от потерь. К последним здесь относят все, что может сделать работу компании менее эффективной.
Концепция бережливого производства может быть распространена не только на само производство, но и на разработку и управление проектами, а также на процесс сбыта изделий потребителю.
В конце прошлого столетия методику бережливого производства разработали два инженера из Японии – Тайити Оно и Сигео Синго. Однако зачатки этой системы появились еще раньше. Какую цель преследовали создатели данной теории? В первую очередь, они хотели исключить лишние действия при получении того или иного продукта, который с их помощью не стал бы более ценным ни на каком этапе своего жизненного цикла. То есть бережливое производство – это не совсем технология. Будет точнее назвать ее управленческой концепцией, предполагающей, что предприятие полностью ориентировано на рынок, а в усовершенствовании заинтересован каждый работник.
Опыт внедрения методов бережливого производства в работу разных компаний наглядно продемонстрировал, что система дает отличные результаты. Сейчас ее используют во всевозможных сферах бизнеса, но первой организацией, в которую внедрили бережливое производство, была Toyota Production System.
Сегодня такие методы применяют во многих отраслях, к примеру:
- в медицине;
- в торговле;
- в логистике;
- при оказании услуг кредитными организациями;
- в образовании;
- при добыче нефти;
- в строительстве;
- в информационных технологиях.
В любой области методы бережливого производства дают возможность компании работать эффективнее и во много раз снизить издержки. Хотя для этого концепцию отдельно адаптируют под каждую организацию.
В наши дни предприятия, которые уже впустили в свою деятельность lean manufacturing, часто так и называют – «бережливые». От других организаций их отличают особые характеристики.
Прежде всего, «бережливые» предприятия считают персонал основой производственного процесса. Работники являются созидательной силой, а техническое и технологическое оснащение лишь помогают добиться поставленной цели. Философия бережливого производства такова, что успешной и эффективной компанию могут сделать только заинтересованные творческие люди с высоким потенциалом, а сами по себе технологии и стратегии никаких результатов не дадут.
Рекомендовано к прочтению
Вторая отличительная черта «бережливых» предприятий – это максимальная сосредоточенность на том, чтобы устранять потери и беспрерывно улучшать процесс производства на всех этапах. На это направлены ежедневные действия каждого работника компании. Все – от обычных работников до руководителей – принимают участие в модернизации.
Третье отличие «бережливых» предприятий заключается в том, что все решения глав компаний направлены не на то, чтобы получить выгоду здесь и сейчас, во внимание принимаются лишь перспективы развития в будущем. При этом бесполезные методы руководства, такие как командование, жесткий контроль, оценивание персонала с помощью сложных систем, исключаются.
Работа управленцев состоит в том, чтобы адекватно организовать процесс производства, вовремя выявлять неполадки, устранять их и пытаться предугадать. В любом работнике в первую очередь ценится именно способность находить брак на своем рабочем месте и устранять его.
Чтобы интегрировать методы lean production в деятельность того или иного предприятия, нужно понимать основные принципы, инструменты этой концепции и уметь работать с ними.
Главные принципы бережливого производства
Основных принципов бережливого производства немного. Они довольно просты, но воплощение их в жизнь требует серьезных усилий:
- Всегда стараться исключить действия, которые не принесут никакой пользы. Применять инструменты и методы бережливого производства для того, чтобы постоянно искать издержки и избавляться от них. Только так можно ожидать максимум эффективности.
- Узнать, что именно делает продукт ценным в глазах клиента. Ведь в итоге, для потребителя не имеют значения многие действия, производимые в организации. Лишь тогда, когда станет известно, что именно нужно покупателю, получится установить, какие из производственных процессов являются по-настоящему нужными.
- Вокруг интересов клиента должна строиться основная деятельность компании. То есть лучше всего производить только тот продукт, который необходим потребителю в нужном для него количестве. Это даст возможность убрать лишние действия, исключить ненужные затраты.
- Определить, без каких действий предприятию действительно не обойтись, и снизить потери. Чтобы оптимизировать деятельность компании, нужно подробно рассмотреть каждый этап с момента принятия заказа до получения продукции потребителем. Это наглядно покажет, какие методы бережливого производства могут усовершенствовать процессы.
- Преобразовать этапы создания продукта таким образом, чтобы получить целостный рабочий поток, и перестроить саму работу, исключая все возможные простои и потери. Вероятно, для этого понадобится изменить проекты или внедрить новые технологии и методы. Итогом должен стать процесс, в котором все манипуляции делают конечный продукт лучше, но не дороже.
При внедрении системы необходимо обязательно следовать данным принципам. Причем это касается абсолютно любой сферы, будь то управление финансами или проектами. Методы и инструменты бережливого производства позволяют сделать бизнес-процессы лучше и эффективнее, найти и уменьшить издержки, повысить производительность труда.
Основные методы бережливого производства
Чтобы разобраться в концепции lean manufacturing, можно прибегнуть к разным способам, но лучший результат даст изучение самих инструментов и методов бережливого производства. Обзор самых известных и популярных из них будет представлен ниже.
Методы бережливого производства можно использовать как угодно: вместе, по-отдельности, комбинируя между собой или соблюдая очередность. На выбор инструментов непосредственно влияют цели предприятия и проблемы, которые необходимо устранить. Но если применять их совместно, они станут прекрасным дополнением друг друга. Итак, перейдем к обзору.
- Отображение потока создания ценности (Value Stream Mapping).
Несложная графическая схема информационных и материальных потоков, которая показывает, что конкретно необходимо сделать, чтобы конечный потребитель получил продукт компании.
На карте потока создания ценности можно сразу выделить узкие места и все проанализировать, определив бессмысленные затраты и ненужные процессы, чтобы в итоге создать план оптимизации.
- Вытягивающее поточное производство (pull production).
Данная схема организации производственного процесса предполагает, что на каждом этапе объемы продукции рассчитываются на основе потребностей клиентов.
«Поток в одно изделие» считается идеальным, поскольку находящийся по потоку выше поставщик не выпускает продукцию до того времени, пока находящийся по потоку ниже заказчик этого не потребует. В результате получается, что каждая операция «вытягивает» продукт с предыдущей.
В вытягивающей схеме он используется для информирования, позволяя давать разрешение на выпуск изделий или их последующую передачу. Также канбан нужен, чтобы усовершенствовать планирование «активностей» производства. В их число, помимо основных, входит прогноз спроса, определение заданий и их распределение по мощностям, загрузка которых оптимизируется. Последнее предполагает «не делать ничего лишнего, не делать раньше времени, сообщать о возникающей потребности только тогда, когда это реально необходимо».
Представляет собой постоянное улучшение всего процесса создания ценности или каждого отдельного этапа для того, чтобы сделать продукт лучше и снизить издержки. Кайдзен можно рассматривать не только как философию, но и как метод управления, благодаря которому работники становятся заинтересованными в оптимизации, предлагают свои идеи и имеют возможность быстро их реализовать.
Метод позволяет организовать рабочее пространство таким образом, чтобы сделать его рациональным. Состоит система 5S, соответственно, из пяти шагов:
- Сэйри (сортировка) – все вещи делятся на необходимые и лишние. От последних избавляются.
- Сэйтон (соблюдение порядка) – хранение нужных вещей организуется таким образом, чтобы их было легко отыскать и использовать по назначению.
- Сэйсо (содержание в чистоте) – рабочее пространство должно тщательно прибрано.
- Сэйкэцу (стандартизация или поддержание порядка) – это условие нужно для того, чтобы выполнялись первые три правила.
- Сицукэ (совершенствование, появление привычки) – формируется привычка придерживаться установленных правил, технологий и процедур.
- Система SMED («смена штампа за 1 минуту»).
Данный метод подразумевает оперативную перенастройку оборудования, что дает возможность поменять инструмент или провести переналадку станка буквально в одно касание, то есть за несколько минут или секунд.
Выполнять переналадку в десятки или сотни раз быстрее позволяют следующие методы:
- внутренние и внешние операции наладки совершаются по-отдельности;
- внутренние действия становятся внешними;
- крепеж не используется или заменяется на функциональные зажимы;
- применяется дополнительная оснастка.
- Система TPM (Total Productive Maintenance).
Это эффективное обслуживание оборудования, в котором принимают участие все сотрудники. Благодаря применению TPM оборудование становится более качественным и позволяет добиваться лучших результатов, так как своевременно проходит профилактическое обслуживание.
Главный принцип данной системы – это предупреждение и выявление дефектов технического оснащения на ранней стадии, когда они еще не успели привести к большим проблемам.
В основе системы ТРМ лежит создание графика профилактического техобслуживания, а также смазки оборудования, чистки и проверки на работоспособность. Это позволяет повышать показатель эффективности оборудования (OEE).
- Система JIT (Just-In-Time) – точно вовремя.
Этот метод управления позволяет доставлять материалы с предыдущей операции или от поставщика не раньше того времени, когда они понадобятся. С помощью Just-In-Time можно резко снизить объем незавершенного производства, материалов и готовых изделий на предприятии.
- Визуализация.
Это любое средство, которое дает возможность понять, каким образом должна выполняться та или иная работа. При этом детали, оснастка, тары и иные индикаторы состояния производства размещаются так, чтобы можно было без труда узнать, в норме система или нет.
- U-образные ячейки.
Оборудование размещают в форме буквы U, то есть станки расставляются подковообразно в соответствии с последовательностью операций. В результате последняя стадия обработки той или иной детали находится совсем рядом с начальной стадией. Это позволяет оператору запускать новый производственный цикл без промедлений.
Потери в бережливом производстве
Различают 8 видов потерь:
1. Перепроизводство.
Нарастить производительность стремятся многие компании, так как это самый понятный метод получения большей прибыли. Но очень часто руководители предприятий забывают, что количество выпущенной продукции должно соответствовать спросу, а продать излишки просто не получится.
В результате получается такая ситуация, когда продукт, который совсем недавно был в дефиците, начинает пылиться на складе. Причем такой момент удивительным образом наступает всегда внезапно, какими бы ни были причины.
В попытках хоть как-то сбыть лишний, а возможно и подпорченный товар, компаниям приходится нелегко. О получении прибыли здесь уже и речи не идет. Лишь бы компенсировать потери и избежать убытков.
Чтобы не допустить подобных проблем, необходимо:
- выпускать продукцию только тогда, когда она требуется, и лишь столько, сколько нужно потребителю, то есть работать под заказ;
- производить мелкие партии изделий, которые точно удастся продать, а если спрос упадет, быстро переориентироваться на другой продукт;
- совершать переналадки оборудования максимально быстро, чтобы уменьшить издержки и сделать производство мелкими партиями прибыльным.
Из этого можно заключить, что производство товаров крупными партиями становится все менее рентабельным. Современные потребители довольно капризны и постоянно хотят разнообразия ассортимента.
2. Транспортировка.
Каким бы ни было производство, в любом случае это ряд последовательных действий, в ходе которых сырье или полуфабрикаты превращаются в готовый продукт. При этом материалы должны передаваться от операции к операции. Даже если изготовление конвейерное, процедура передачи ценностей существует, потому что к конвейеру нужно доставить сырье, а произведенную продукцию отгрузить на склад.
Сама по себе транспортировка не добавляет продукту ценности и даже требует дополнительных затрат на топливо, электричество, транспортное обслуживание, строительство гаражей, дорог и т. д. Кроме того, на перевозку или переноску тратится время, появляется вероятность повреждений. Однако ни одно предприятие обойтись без этих действий не может.
Чтобы снизить издержки при транспортировке материалов и изделий, необходимо разработать карту маршрутов транспорта, а также проанализировать, насколько та или иная перевозка целесообразна. Лишние действия следует исключить. Для этого можно провести перепланировки, перераспределить ответственность и сделать так, чтобы запасы всегда были рядом.
3. Ожидание.
Когда планирование и производство не согласованы друг с другом, появляются издержки, связанные с ожиданием обработки заготовок. В нашей стране на предприятиях такое происходит постоянно.
Планирование – это не так просто, как может показаться на первый взгляд. Сначала нужно проанализировать множество разных факторов. Среди них можно выделить состояние рынка, структуру заказов, производительность оборудования, график работы персонала и т. п. Помимо того, чтобы сделать планирование качественным, нужны отличные знания математики и четкое взаимодействие отделов сбыта, закупок и производства.
На издержки из-за ожидания влияет не только неудачное планирование, но и неравномерная пропускная способность технического оснащения. В последнем случае перед операцией с наименьшей пропускной способностью заготовки и полуфабрикаты копятся чаще всего.
4. Запасы.
Сегодня большинство людей прекрасно понимают, что в запасах ничего хорошего нет. Чем же они плохи? В первую очередь тем, что деньги на резерв извлекаются из оборота, но ценность свою теряют. Наши соотечественники привыкли все заготавливать, это кажется необходимым.
Однако на самом деле запасы:
- представляют собой замороженные деньги из оборота;
- это лишние траты, поскольку склады требуют обслуживания, а за логистику и работу сотрудников тоже надо платить;
- не позволяют выявить производственные проблемы, например, неправильное планирование, отсутствие взаимопонимания с поставщиками, неравномерный производственный поток и многое другое.
Запасы создают впечатление, что в производстве все благополучно, но на самом деле это не так, и потери просто скрыты.
5. Дефекты.
Когда предприятие производит изделия, не соответствующие запросам потребителя, все равно приходится вкладывать средства в сырье, труд людей, переработку и утилизацию продукции с дефектами. Чтобы минимизировать потери, связанные с получением брака, обычно в компании формируются специальные службы контроля.
Однако редко учитывается тот факт, что контролирующие подразделения не имеют достаточного влияния на производство. Поэтому с таких отделов спрашивать о причинах брака нет смысла.
Чтобы устранить издержки, связанные с выпуском брака, прежде всего, стоит выяснить, насколько эффективно работают органы, осуществляющие контроль. То есть не просто установить, пропускают они дефектные изделия или нет, но и узнать, каким образом контролирующие подразделения пытаются исключить причины появления брака. Как бы то ни было, контроль чаще всего проводят уже после того, как изделия будут изготовлены. Это значит, что контролеры просто не могут быстро реагировать на дефекты и добиваться высокого качества. Решение здесь только одно – внедрить метод управления качеством в сам процесс производства.
6. Излишняя обработка.
Стоит еще раз отметить, что покупатели будут платить лишь за те качества и свойства продукта, которые им необходимы. К примеру, если человек хочет приобрести телевизор, то за установленную стоимость он желает получить надежное устройство с характеристиками, соответствующими его требованиям. В этом случае телеприемник, имеющий какое-то совершенно ненужное для клиента дополнение и стоящий в два раза дороже, приобрести никто не захочет.
Обслуживание автоматического оборудования тоже является издержками излишней обработки. В качестве примера здесь можно привести работу персонала, который поправляет перекосившиеся на конвейере заготовки. Такие детали из-за перекоса мешают движению конвейера, поэтому за процессом следит работник. Но труд его – лишний.
7. Движения.
Причиной потерь могут стать совершенно ненужные, хаотичные и бессмысленные движения, то есть суета. Иногда с виду может показаться, что процесс кипит. Однако стоит разобраться в этой активности, как выяснится, что никакой ценности для конечного потребителя действия не несут. Поэтому лишние движения являются такими же потерями. Их источником обычно становится плохо организованный труд персонала. Это означает, что на предприятии нет качественных подробных инструкций, сотрудники плохо обучены или игнорируют правила трудовой дисциплины.
8. Потери творческого потенциала.
К этому пункту можно отнести такие ситуации, когда сотрудник компании стремится что-то усовершенствовать, чувствует в себе силы, имеет необходимые знания, но проявить себя ему просто не дают возможности. Очень часто таким работникам мешает реализовать свои идеи нежелание руководства, нехватка средств и времени или неблагоприятная атмосфера в коллективе. В результате человек теряет свой энтузиазм и приходит к мнению, что он для этой системы всего лишь мелкое звено, которое легко заменить.
По этой причине к основным методам и задачам концепции бережливого производства относят необходимость заинтересовать каждого сотрудника в оптимизации предприятия. Работники должны быть вовлечены в непрерывное усовершенствование процессов (кайзен), чтобы потенциал каждого из них был использован в полной мере.
Насколько эффективны методы бережливого производства в России
По данным медиахолдинга «Эксперт», в нашей стране методы lean manufacturing начали применять лишь 15 лет назад.
Однако уже за первые три года внедрения системы были получены потрясающие результаты:
- В такой отрасли тяжелой промышленности, как черная металлургия, удалось сократить время переналадки на 70 %.
- На предприятиях по сборке автомобильных узлов, а также в нефтеперерабатывающих и приборостроительных компаниях потери сократились на 30 %.
- В сфере добычи нефти стало требоваться на 25 % работников меньше, чем раньше.
- Приборостроительные компании сократили производственные площади на 30 %.
- В сфере цветной металлургии техническое оснащение стало эффективнее на 45 %.
- На предприятиях по добыче нефти объем незавершенного производства упал вдвое.
- В авиационной промышленности и приборостроении производственный цикл сократился на 60 %.
К итогам применения методов бережливого производства на российских и зарубежных предприятиях к 2019 году можно отнести следующее:
- Удалось освободить пятую часть производственных площадей автомобильной промышленности.
- В электронной промышленности таких площадей стало на 20 % меньше.
- Объем запасов при производстве товаров массового потребления снижен на 35 %, производственный цикл – на 25 %, а сам объем такого производства вырос более чем в два раза.
- Скорость производства в области авиационной промышленности увеличилась в 4 раза.
- Затрат в сфере производства лекарственных препаратов сократились в 5 раз.
- Производительность труда в цветной металлургии увеличилась на 35 %.
Методы lean production сегодня внедрили такие компании РФ, как «КамАЗ», «Группа Газ», «ЕвроХим», «ТехноНИКОЛЬ», «Хлебпром», «Орифлэйм Косметикс», ВСМПО-АВИСМА, «Эксперт Волга», «Сигнал», «Русал» и многие другие.
Основной проблемой при внедрении бережливого производства в нашей стране остается нехватка специалистов по этому направлению. Применить методы системы и усовершенствовать бизнес-процессы с ее помощью могут немногие.
Методы внедрения бережливого производства
Можно ли использовать принципы lean production в работе отечественных предприятий? Чтобы дать ответ, стоит разобраться в других зарубежных системах такого типа и понять, как они применяются различными организациями.
- Технология внедрения lean manufacturing по Джеймсу Вумеку.
В процессе введения в действие методики бережливого производства необходимо выполнить следующие действия:
- определить проводника перемен;
- подробно изучить концепцию бережливого производства;
- выявить или создать проблемы;
- отодвинуть стратегические вопросы на второй план;
- разработать карты потоков создания ценностей;
- оперативно приступить к работе по решению главных вопросов;
- испытывать желание получить результат как можно быстрее;
- оптимизировать процессы по системе кайдзен.
Внедрение бережливого производства всегда начинают с продукта или услуги. Ведь именно готовая продукция интересна покупателям. Им не хочется знать ни про какие показатели, основные компетенции и активы. Поэтому для каждого вида товара нужна карта создания потока ценности. С ее помощью можно выявить издержки в этих потоках. Однако в первую очередь стоит определиться с самим изделием.
Это будет несложно, если предприятие за день выпускает всего несколько единиц продукции. Но есть множество компаний, которые производят сотни или даже тысячи товаров. В этом случае сформировать карту потока создания ценности для каждого продукта просто невозможно. Чтобы упростить процесс, продукцию разделяют на группы. Для этого чаще всего используют специальный инструмент – матрицу продуктовых семейств (МПС, Product Family Matrix).
В отдельные семейства могут быть объединены товары, к которым применяются одинаковые процессы. Вот их для начала и нужно выявить.
Такие процессы должны иметь идентичные этапы, чтобы в дальнейшем предприятие могло запустить целый поток, где несколько разных видов продукции будут проходить через одни и те же этапы, но, возможно, с минимальными отклонениями.
Таким образом, определенные товары, которые изначально считались абсолютно разными, могут проходить практически одинаковый цикл.
- Способ внедрения по Деннису Хоббсу.
Анализируя алгоритм применения методов lean production по Деннису Хоббсу, можно увидеть такую последовательность действий:
- Создание и старт проекта: определяется стратегическое видение будущего организации, формируется состав подразделений, а персонал проходит обучение. Перед каждой командой ставится цель, устанавливаются полномочия. Затем формируется план действий.
- Продукция, сырье и процессы производства тщательно изучаются, на основании чего составляются документы. Учитывая отходы, вариативность и возможность повторной обработки, выполняется выработка процессов. Исходя из этого, формируются товарные группы, определяются цепочки вытягивания, времена пополнения, а также основные составляющие системы «Канбан».
- Итоговая проверка: в ходе данного этапа заканчивают собирать нужные данные, окончательно определяются с компонентами системы канбан и последовательностями вытягивания для достижения цели.
- Планирование мощностей: согласно методам lean production формируются мощности, соответствующие рассчитанному объему ресурсов. Создается план, с помощью которого можно воплотить в жизнь систему канбан.
- Линии готовят к началам работ. Для этого проверяется их сбалансированность и готовность операторов переключаться. Также следует убедиться в эргономичности планировки и распределить задания работникам. Чтобы сократить объем незавершенного производства, разрабатывается соответствующий план. Затем внедряется специальный механизм оптимизации производственных процессов.
- Усвоение: работа линии проверяется, в результате чего дается оценка ее соответствию принципам бережливого производства. Определяется стратегия по исправлению выявленных отклонений, выясняется, есть ли все необходимое для того, чтобы управлять производственной линией согласно методам lean production.
Чтобы внедрить методологию в ту или иную компанию, выбирается ответственное лицо, которое организует всю работу и контролирует изменения. Этот сотрудник становится руководителем проекта по внедрению бережливого производства и может продолжать деятельность в данном направлении даже после того, как консультант покинет предприятие. Специалиста, который берет ответственность за проект, освобождают от других обязанностей либо нанимают на эту должность нового работника.
Чтобы реализовать внедрение методов бережливого производства в организацию, требуется в среднем от четырех месяцев до полугода.
Почему следует обращаться именно к нам
Мы с уважением относимся ко всем клиентам и одинаково скрупулезно выполняем задания любого объема.
Наши производственные мощности позволяют обрабатывать различные материалы:
- цветные металлы;
- чугун;
- нержавеющую сталь.
При выполнении заказа наши специалисты применяют все известные способы механической обработки металла. Современное оборудование последнего поколения дает возможность добиваться максимального соответствия изначальным чертежам.
Для того чтобы приблизить заготовку к предъявленному заказчиком эскизу, наши специалисты используют универсальное оборудование, предназначенное для ювелирной заточки инструмента для особо сложных операций. В наших производственных цехах металл становится пластичным материалом, из которого можно выполнить любую заготовку.
Преимуществом обращения к нашим специалистам является соблюдение ими ГОСТа и всех технологических нормативов. На каждом этапе работы ведется жесткий контроль качества, поэтому мы гарантируем клиентам добросовестно выполненный продукт.
Благодаря опыту наших мастеров на выходе получается образцовое изделие, отвечающее самым взыскательным требованиям. При этом мы отталкиваемся от мощной материальной базы и ориентируемся на инновационные технологические наработки.
Мы работаем с заказчиками со всех регионов России. Если вы хотите сделать заказ на металлообработку, наши менеджеры готовы выслушать все условия. В случае необходимости клиенту предоставляется бесплатная профильная консультация.
Бережливое производство, Lean, и Toyota production system
Бережливое производство – это система управления, при которой продукция изготавливается в точном соответствии с запросами потребителей и с меньшим числом дефектов по сравнению с продукцией, сделанной по технологии массового производства. При этом сокращаются затраты труда, пространства, капитала и времени.
Для чего именно нужно БП:
- Увеличение отдачи от капитала за счет сокращения запасов и сокращения времени с момента заказа до момента доставки.
- Обеспечение роста бизнеса посредством делегирования ответственности и высвобождения собственника или руководителя от текущих проблем.
- Снижение зависимости от ключевых специалистов и обеспечение быстрого процесса обучения.
- Изменение отношения к конкуренции через больший фокус на запросах клиентов, а не на сравнении своего предложения с другими представленными на рынке.
- Использование внутреннего потенциала сотрудников и предприятия за счет вовлечения каждого в процесс решения проблем.
1. Ориентация на потребителя
В массовом производстве мы пытаемся угадать, что нужно рынку, производим это и надеемся распродать. В бережливом производстве мы сначала ожидаем заказов, и производим под них. Закупаем столько сырья, сколько нужно (только под конкретные заказы). Кроме того, очень внимательно относимся к обратной связи от клиентов.
Сейчас удастся встретить мало предприятий, загружающих склады, а не работающих под заказ. Но так работали General Motors, Chrysler, и, конечно же, Генри Форд.
2. Поток вытягивания
Бережливое производство — это вытягивающее производство. В массовом производстве стараются максимально загрузить оборудование, чтобы оно не простаивало, а производило как можно больше (пока есть из чего делать — делаем). Это создает огромные запасы как незавершенного производства, так и готовой продукции. Все эти запасы лежат без движения, ржавеют, теряются, устаревают морально и аккумулируют в себе деньги.
В вытягивающем производстве оборудование делает детали только тогда, когда с последующего этапа приходит информация что они там нужны.
Система оповещения называется «канбан».
Таким образом сокращаются запасы сырья, незавершенного производства и готовой продукции.
В бережливом производстве всё совершенствование выстраивается от потока, который перестраивается и балансируется. Делается всё возможное, чтобы он стал как можно более быстрым и оптимальным. Все остальные инструменты совершенствования крутятся вокруг потока и нужны для того, чтобы сделать совершенным именно поток создания ценности.
Совершенствование направляется узким местом. Концентрируется на нем. «Узкое место» — это некое ограничивающее общую производительность линии звено. После того, как узкое место улучшено, какое-то другое место становится узким.
«Lean» — это переводится не «бережливый». Это тощий, поджарый, стройный. Бережливо относиться можно к какой угодно системе производства. Но Lean именно поджарый, лишенный запасов. Когда про организм говорят, что он поджарый? Когда у него нет (жировых) запасов.
Визуально различие в потоках можно оценить здесь: Задача по производственному управлению
3. Организация производственных ячеек
Вживую выглядит так:
Цель: повысить производительность труда. Один человек может достигнуть такого совершенства, что сможет обслуживать сразу несколько единиц оборудования.
4. Сокращение длительности выпуска заказа
Все, чем мы занимаемся, — это следим за временем между размещением заказа потребителем и получением денег за выполненную работу. Мы сокращаем этот промежуток времени, устраняя потери, которые не добавляют ценности (Тайити Оно, 1988).
Нужно добиваться того, чтобы с того момента, как клиент подал заявку до момента, когда он получил свой заказ, проходило как можно меньше времени.
В этом процессе нужно ориентироваться на два понятия: время цикла и время такта.
Время цикла (длительность выпуска заказа) — это длительность прохождения изделия по всему потоку от начала до конца.
Время такта — это частота, с которой готовые изделия выходят с линии. Целевое время такта определяется рыночным спросом (например: нам нужно 2 автомобиля в сутки).
Массовое производство имеет очень короткое время такта (выпускает как из пулемета), но очень длительное время цикла (каждая из единиц производится долго). помимо замораживания материальных средств в виде незавершенного производства это также очень снижает скорость производства редких марок продукции.
5. Гибкость
В массовом производстве переналадка оборудования делается крайне редко — оборудование производит детали гигантскими партиями. В бережливом производстве следует изготавливать детали небольшими партиями, поэтому требуется часто переналаживать оборудование. Именно поэтому в нем очень развит инструмент SMED «Быстрая переналадка
6. Устранение потерь
Для того, чтобы сократить время цикла, устраняют потери. Потери — это всё, что не добавляет ценности конечному продукту. Прибыль повышается за счет устранения потерь на производстве.
Виды потерь:
- Перепроизводство — вся непроданная продукция, загромождающая склад готовой продукции;
- Излишние запасы — на них потрачены деньги, но они лежат без дела. Портятся, теряются. Требуют инвентаризации. Всё это лишние затраты;
- Ожидание — людей, деталей, продукции. Всё, что находится без дела, стоит без движения в очереди куда-то;
- Транспортировка — уменьшить по времени и расстоянию;
- Лишние движения во время рабочих операций — не оптимизированная работа людей руками. Лишняя работа из-за несовершенства инструмента.
- Излишняя обработка — когда мы делаем то, что не нужно клиенту;
- Дефекты, брак;
- Нереализованный потенциал сотрудников.

7. Внутрицеховая логистика
Поток создания ценности, а также потоки снабжения по возможности должны двигаться в едином направлении, исключая возвратные и пересекающиеся потоки. Длина путей перемещения также должна быть максимально сокращена. Для этого используется инструмент «Диаграмма спагетти», с помощью которой анализируем все перемещения, после чего решаем, как их оптимизировать.
8. Всеобщее вовлечение в процесс совершенствования
Для того, чтобы устранять 8 видов потерь, этим постоянно должны заниматься все сотрудники компании во главе с первым лицом. Вовлечение в этот процесс первого лица — это ключевое условие успеха.
Для вовлечения очень полезно вот это: Дайджест позитива. Замечания наоборот
Для этого потребуется отказ от культуры порицания в пользу открытого признания проблем. Отказ решать проблемы методом замены людей или методом «найти и наказать виновных».
Иначе ваш процесс совершенствования поломается о то, что ваши сотрудники будут упорно совершенствовать только свою незаменимость.
Как это выглядит на практике: «2-секундный Лин. Как вырастить персонал и весело создать Лин-культуру», Пол Эйкерс
Или так: «Пятнадцатый камень сада Рёандзи», 1986 г, Владимир Цветов — Про менталитет японцев
Ключевая особенность совершенствования — непрерывность. Нельзя перестроить предприятие, а потом к этому вопросу не возвращаться. Проект — это что-то имеющее начало и конец. А процесс совершенствования должен быть вектором.
Как часто нужно тренироваться чтобы быть спортсменом? Постоянно. Как часто нужно повышать свою квалификацию чтобы быть профессионалом? Постоянно.
Также и с производством. Японцы в этом плане впереди всей планеты и у них краеугольный камень: постоянное совершенствование. Нон-стопом десятилетиями.
Как японцы считают порочно: повседневная работа + совершенствование
Как японцы считают правильно: повседневная работа = совершенствование
Совершенствование должно быть неуклонным. Нельзя 1 раз сделать что-то здоровое и жить до 100 лет. Правильный образ жизни нужно поддерживать на протяжении всей жизни непрерывно.
Подробнее про совершенствование: «Кайдзен. Ключ к успеху японских компаний», 1985 г., Масааки Имаи
Совершенствование наращивает определенную рутину: Силы на поддержание системы
Если сделать преобразования и больше к этому вопросу не возвращаться, то произойдет вот что: Предотвращение деградации системы после того, как некий проект будет успешно завершен
Также: Организация рационализаторской деятельности на заводе
9. Иди в гембу (иди и смотри)
Важнейший принцип совершенствования и вовлечения. Он заключается в том, что начальники не должны заниматься развитием предприятия из кабинетов. Они должны идти в цех и смотреть, как выполняется работа. Или идти и смотреть по месту, где происходит брак. Искать причину его возникновения. Японский начальник всегда идет на передовую. Туда, где создается ценность.
Придя на место создания ценности (на гембу) нужно искать корневые причины появления проблем. Не дергать верхушки, а копать до самого корня. Для этого есть метод «5 Почему?». 5 раз или больше под ряд задав вопрос «почему?» рабочему на участке, можно выяснить, «откуда ноги растут». И принять действенные меры. Подробнее: Симптомы: устранить нельзя использовать
Это что касается потока создания ценности. А вообще, проблемы нужно искать не только в гемба, но и в администрации.
10. Ориентированность на процесс, а не на результат
У нас могут похвалить, если ты как-то обманул систему и выкрутился из сиюминутной проблемы. Потырил детали из какого-то другого заказа (который отгружать через 2 дня, а не сегодня), или руками влез в приоритет работы участка изготовления металлических деталей для повторного изготовления каких-то деталей, потерянных на твоем заказе, который сегодня отгружать.
Заказ с грехом пополам отгрузили, и все такие «фух!» выдохнули. Сейчас нужно разобраться, почему так произошло на этом заказе. Как потеряли изготовленные детали, и почему вовремя не приехали покупные. Но подождите-ка! Мы только что забрали детали из заказа, который отгружать послезавтра! Теперь нужно срочно думать, как его отгружать. Кроме того, мы вмешались в приоритет металлического участка, и он теперь работает с запозданием, и с этим тоже нужно что-то срочно делать! Поэтому некогда сейчас заниматься выяснениями, почему так произошло. Да и потом: всё же получилось. Результат же есть. А это — самое главное! (нет)В бережливом производстве нужно именно постоянно совершенствовать процесс, и тогда уже он будет давать стабильный результат.
Подробнее: Почему результата недостаточно [Принцип Деминга №10 — Избегать пустых лозунгов]
11. Система 5S
5S – это система организации рабочего пространства, установления и поддержания порядка, чистоты, дисциплины и создания безопасных условий труда. Система 5S помогает быстро избавиться от накопившегося на производстве и в офисе хлама и исключить его появление в дальнейшем.
Система нужна для всеобщего вовлечения, а также для повышения производительности труда. Когда мы избавились от всего ненужного, разложили все предметы по местам, подписали их места хранения и следим за чистотой и порядком, это очень перестраивает сознание людей. Настраивает их на совершенствование. Также, становятся очень заметны люди, которые не хотят принимать в этом участия.
В Японии никто никогда не гнушался «совершенствованием ради совершенствования» без прямой денежной выгоды. Всё это создает философию, создает дух. Не всё измеряется деньгами. Есть еще и внутренняя энергия системы.
Подробнее:
Плохой 5S. Как не надо делать 5S
Система 5S на местах с непредсказуемой работой
Оптимизация ПК по системе 5S
12. Отказ от массового контроля
Отказ от массовых проверок продукции на выходе, а также отказ ставить сотрудника ОТК после каждого станка. Вместо этого возложение обязанностей с проверкой на самих рабочих на последующих стадиях выполнения работы. Такое возможно только в культуре совершенствования, где виновников не наказывают и не штрафуют, а просто пытаются выяснить, что вызвало брак и устранить возможность появление брака в будущем. Например при помощи внедрения способов защиты от непреднамеренных ошибок (Пока-ёке):
Тогда рабочие не будут бояться сообщать о бракованных деталях друг друга, и сотрудники ОТК не будут нужны в таком количестве.
Это лучше, чем проверять всю продукцию в самом конце, т.к. в конце на нее затрачено уже гораздо больше ресурсов, чем если бы брак был обнаружен на самых ранних этапах. Поэтому при возникновении брака на одном из участков конвейер останавливают, пока не выяснят в чем дело. Чтобы не гнать брак дальше. Японцы даже первыми придумали технологию, которая останавливает оборудование при возникновении брака автоматически.
13. Стандартизация + обучение на рабочем месте + контроль
Улучшения бессмысленны, если на рабочих местах нет стандартов. Потому что если стандарта нет — система быстро деградирует.
Стандартизировать операции нужно так: Что такое технологизация. Как и зачем ее делать
После того, как стандарты составлены, лучший опыт должен быть тиражирован посредством обучения: «Талантливые сотрудники. Воспитание и обучение в духе Дао Toyota», Дэвид Майер, Джеффри Лайкер
Потом выполнение стандартов надо будет контролировать: Как добиться надежного и долгосрочного развития компании из красной в янтарную(параллельная структура управления)
14. Визуализация
Для того, чтобы вовлеченные сотрудники могли улучшать процессы, процессы должны быть визуальны, понятны и стандартизированы. Всё должно быть визуализировано и прозрачно и обозначено. В мутной воде совершенно непонятно, что происходит и как всё устроено, поэтому нет идей как это улучшить. Не видно потерь. Цель в том, чтобы любой человек, придя на участок, не задавая вопросов понял, как тут всё устроено, как должно работать и не происходит ли нарушений.
Визуализация выглядит вот так:
15. Статистическое управление
Бережливое производство в своих решениях опирается на анализ и факты. А факты — это статистика. Руководство должно принимать решения на основании статистических данных о производстве.
Подробно рассмотрено в книге «7 инструментов управления качеством», Хитоси Кумэ
16. Картирование потока создания ценности (VSM)
Основной инструмент по выявлению потерь. Тяжелая артиллерия, так сказать. Можно сказать, что это огромная фотография рабочего дня всего процесса. Мы зарисовываем всё, что делается. Фиксируем время, информационные потоки, количество персонала на операциях, простои, дефекты и другую важную информацию. На основании всего этого мы делаем одну большую карту, созерцая которую ищем возможности для улучшений.
На стене — это архаичный метод. Можно в Экселе.
Меня иногда спрашивают какую КНИЖКУ прочитать, чтобы понять бережливое производство с нуляЧестно сказать, до сегодняшнего дня я подходящей книги не знал. Поэтому-то мне и пришлось самому написать заметку «Бережливое производство с нуля». И вот, наконец-то хорошая книжка появилась! Кто-то постарался. В ней хорошо проработана структура, и сделана крутая инфографика. Она во сто раз лучше аналогичной книжонки Майкла Вейдера.
У меня уже была заметка «Бережливое производство с нуля», и я решил приделать эту книгу к своей заметке, т.к. в книге написано то же самое. Написано так же просто, но более подробно. Поэтому кому после этой заметки захочется копнуть глубже, то можно скачать книгу по ссылке.
Еще по теме:
Пример: Внедрение производственной системы ОАО «НИПОМ» 2010 — 2013 гг
Эта книга уже для более опытных бережливцев: «Тойота Ката. Лидерство, менеджмент и развитие сотрудников», Майк Ротер
Книга человека, который создал японское качество: «Выход из кризиса. Новая парадигма управления людьми, системами и процессами», Эдвардс Деминг
Как это было в СССР еще до Тойоты: «Основы рационализации производства», 3-е издание, 1934 г. И.М. Бурдянский
Книга, состоящая из обзо
Инструмент | Суть мероприятий | Эффект |
5S | Правильная организация рабочего места:
| Достаточно быстрое выявление проблем в производстве, вызванных неправильной организацией рабочего места и сведение их к минимуму (например, избавление от залежей инструментов, которые использовались месяц назад, а сейчас только заставляют тратить время на поиск среди них нужного). |
Andon | Система, которая сразу же информирует о возникшей в процессе производства проблеме и позволяет остановить процесс, пока обнаруженный дефект не стал массовым. | Своевременная ликвидация проблемы, которая позволяет в дальнейшем не тратить ресурсы на ликвидацию последствий ошибки в глобальных масштабах. |
Bottleneck analysis (Анализ узких мест) | Нахождение «узкого» места производства («бутылочного горлышка»), не позволяющего создавать больше продукции за меньшее количество времени. Расширение «бутылочного горлышка» улучшает производительность и «выхлоп» производственных мощностей. | Происходит улучшение слабейшего элемента на производстве, иными словами: «Слабые звенья, прощайте!» |
Continuous Flow (Непрерывный поток) | Выстраивание производственных потоков оптимальным образом. Процесс, выстроенный верно, не подразумевает заполнения «буфера» и каких-либо длительных остановок между этапами производства. | Устранение таких потерь, как непродуманная транспортировка, излишние запасы, нерациональный расход времени. |
Gemba | Формирование понимания того, что все наиболее важное происходит на производстве, а не в кабинетах руководства. | Руководство вовлекается в производственный процесс, что позволяет укрепить дисциплину, уменьшить время реакции на возникающие проблемы и получать информацию из первоисточника. |
Heijunka (Планирование) | Умение планировать заказы особым образом. Заказы клиентов разделяются на несколько небольших партий, которые выстраиваются в определенном порядке. Появляется возможность производить разную продукцию максимально быстро и сократить вероятность возникновения рисков нарушения производственного процесса на разных стадиях и срыва сроков передачи готового продукта заказчику. | Данный lean tool ведет к тому, что снижается потребность иметь запас материалов, время производства. Он позволяет уменьшить потери за счет того, что каждый вид продукции изготавливается чаще, а запасы (иными словами, замороженные активы) сводятся к необходимому минимуму. При вынужденной остановке линии на предприятии есть вся необходимая клиенту продукция. |
Hoshin Kanri (Развертывание политики) | Налаживание связи между «стратегией» и «тактикой»: целями руководства с действиями представителей производства. | Руководство задает цели каждому из сотрудников, они двигаются в этом направлении. Достаточная коммуникация между руководством и рабочими позволяет уменьшить потери. В компанию должен быть внедрен таск-менеджер для использования инструмента Hoshin Kanri. |
Jidoka (Автономизация) | Оборудование подвергается частичной автоматизации. Поиск проблемы происходит в автоматическом режиме. Есть возможность остановить производство при обнаружении ошибки. | Один сотрудник может контролировать работу сразу нескольких устройств. Это приводит к снижению затрат на производство, а также сводит к минимуму затраты на ликвидацию ошибок (в сравнении с тем, если бы они были обнаружены не сразу же, а только в конце производственного цикла). |
Kaizen | Использование kaizen tools представляет собой объединение усилий всех сотрудников предприятия в направлении формирования особой корпоративной культуры и достижение общих целей. | Синергический эффект от объединения усилий сотрудников, направленных на уменьшение издержек, становится, по сути «вечным двигателем» прогрессирования бережливого производства на предприятии. |
JIT, Just in time | Производство и система поставки базируются на «вытягивании» необходимого клиенту на данный момент времени количества продукции. При этом прогнозируемый спрос в расчет практически не берется. Требует наличия на производстве таких систем, как «Continuous Flow», «Kanban», «Takt time» и «Heijunka». | Этот способ наиболее эффективен при необходимости снижения количества выпущенных изделий, запасов сырья и размера производственного помещения. Способствует оптимизации финансовых потоков. |
Kanban (Вытягивающая система) | Регулирует потоки выпущенной продукции и сырья внутри и за пределами производства. Потребность в комплектующих или готовой продукции определяется с помощью сигнальных карт. | Снижается количество потерь и излишек складских запасов. Положительно влияет на результаты проведения инвентаризации на складе. |
KPI | Система метрик применяется для анализа приоритетных сегментов деятельности компании. Является мощным стимулятором роста для сотрудников. | Ключевые индикаторы, которые могут изменять работники, позволяют своевременно определять потенциальные потери и риски, достигать стратегических целей, поставленных перед компанией. |
Muda | Избавление от всего, что не представляет ценности для заказчика (потребителя). | Узнав все возможные виды потерь, следует их своевременно обнаруживать и минимизировать, повышая качество работы персонала, оборудования и организации в целом. |
PDCA | Итеративный метод, позволяющий внедрять всяческие улучшения и/или проводить изменения:
| РDCA позволяет находить системный подход в решении возникающих проблем, внедрять улучшения и проводить эксперименты:
|
OEE | Позволяет отследить три вида потерь, относящиеся к функционированию оборудования: качество, готовность, производительность. | Позволяет понять, насколько эффективно эксплуатируется оборудование.Это сбалансированный показатель, позволяющий повысить прибыльность производства и улучшить его технологичность. Если ОЕЕ достигает 100%, значит, компания выпускает продукт без брака, настолько быстро, насколько это вообще возможно с учетом имеющихся технологий, не допуская простоев. |
Poka-Yoke | Создание методов, предотвращающих появление ошибок в процессе производства. Главная цель — добиться «0 % дефективности». | Затраты, связанные с предупреждением ошибок, значительно ниже, чем те, которые компания несет при регулярных инспекциях и, тем более, при исправлении брака, выявленного спустя длительное время. |
Анализ основных причин | Этим факторам нет места на производстве. Их выявление производится по принципу «пяти почему». То есть нужно задавать вопрос «Почему?» не менее 5 раз по отношению к каждому фактору, негативно влияющему на производство. | Устранение основных причин появления проблем позволяет избежать возникновения аналогичных ситуаций в будущем. |
Visual Factory (Визуализация производства) | Используются простые индикаторы. С их помощью осуществляется обмен информацией. | Каждый сотрудник понимает текущую ситуацию, опираясь на данные системы информации (цвет, звук и прочие сигналы). |
VSM | Инструмент Лин, позволяющий наглядно отделить процессы, добавляющие ценность, от не добавляющих ее. | Удобное решение для планирования изменений, планирующихся впоследствии. |
TPM | Метод бережливого производства, суть которого состоит в том, чтобы привлечь к обслуживанию оборудования каждого сотрудника компании, а не только специалистов-техников. Цель ТРМ — повысить срок эксплуатации оборудования и его эффективность. | Уменьшение количества простоев, ошибок в работе с оборудованием, аварий. Усиление чувства ответственности у каждого сотрудника. |
Takt time | Показатель периодичности, с которой клиент заказывает продукцию. Также время такта может отображать временной промежуток, в который компания предоставляет клиенту выпущенную продукцию. Можно рассчитать по формуле: Плановое время производства / Спрос потребителя. | Позволяет определить требуемую производительность определенного производственного участка с целью удовлетворения потребностей клиентов. |
Стандартизированная работа | Инструкция по близкому к идеальному выполнению определенной операции. Этот документ постоянно анализируется и обновляется. При наличии в компании одинакового оборудования оно должно работать по единому стандартизированному методу (оптимальному). Максимальная эффективность достигается при использовании интерактивных документов, которые можно быстро видоизменять и дополнять. | Уменьшаются потери (вследствие применения только лучшего опыта). Снижаются риски создания некачественного продукта. |
SMART | Данная аббревиатура содержит в себе следующие слова: Specific, Measurable, Attainable, Relevant, and Time-Specific. В русском варианте это звучит так: цель конкретна, измерима, достижима, релевантна, определена во времени. | При слабо продуманной коммуникации или ошибочном понимании задач неизбежно возникают потери. Устранить эту проблему позволяет правильно поставленная цель. |
6 причин снижения производительности | К самым распространенным причинам падения производительности относятся следующие: поломки, настройки, непродолжительные остановки, снижение скорости, отказы в работе, отказы в производстве. | Все эти причины являются призывом к действию. Сократить время простоя можно только при последовательном устранении всех проблем. |
SMED | Набор tools manufacturing, основанных на принципах бережливого производства, позволяющих намного быстрее проводить отладку оборудования (до 10 минут). Переналадка производится на основе двух действий: внутреннем и внешнем. Внутренние действия сопряжены с остановкой оборудования, а внешние могут выполняться и при работающем устройстве. Методика SMED подразумевает преобразование действий из внутренних во внешние. | Становится проще производить небольшие партии продукции, увеличивается время полезной работы оборудования. |
Бережливое производство — инструмент борьбы за эффективность / Хабр
В России сконцентрировано много промышленных предприятий различных направлений. Одной из проблем этих предприятий является нерациональное использование ресурсов. Это приводит к тому, что себестоимость продукции превышает аналогичную у зарубежных конкурентов.Для Выживания на рынке необходимо искать резервы по повышению эффективности производства. К сожалению, часть российских предприятий идут по пути сокращения операционных расходов за счет сокращения персонала без оптимизации бизнес-процессов. Это приводит к тому, что на сотрудников ложится дополнительный объем работы без повышения заработной платы, что в долгосрочной, а иногда и в краткосрочной, приводит к ухудшению качества продукции.
«Оптимизируй свой бизнес-процесс» — проще сказать, чем сделать! Сегодня у топ-менеджеров стол ломится от методов, стратегий, программ и лучших практик по оптимизации бизнес-процессов.
Но я хочу остановиться на гибридном решении, которое позволит Вам визуализировать существующие потери и сконцентрировать свое внимание на проблемах важных для Ваших клиентов. И это решение называется «Lean Six Sigma».
«Lean Six Sigma» — это американский Франкенштейн, объединивший в себе две методологии «Lean» и «Six Sigma». Методология «Lean» направлена на сокращение потерь и ускорение процессов, в то время как «Six Sigma» оперирует понятием удовлетворенность потребителя и направлена на снижение количество дефектов.
История появления и становления этих методологий весьма интересна и заслуживает отдельной статьи. Если будет интересно, то подготовлю отдельную статью по этой теме.
Если обратиться в компанию по обучению Lean 6 Sigma, то, в 99,9% случаев, в ответ Вы получите фразу: благодаря изучению «Lean Six Sigma» Вы узнаете, как оптимизировать бизнес-процесс.
Вот лишь часть результатов, которые дает применение «Lean Six Sigma» в мире:
- Рост производительности труда на 35-70%;
- Сокращение времени производственного цикла на 25-90%;
- Сокращение брака на 58-99%;
- Рост качества продукции на 40%;
- Увеличение времени работы оборудования в исправном состоянии до 98,87%;
- Высвобождение производственных площадей на 25-50%.
И если, Вы, глядя на эти результаты, подумали: вот сейчас внедрю и сразу решатся все проблемы, – то у меня для вас плохие новости! «Lean Six Sigma» не дает готовое решение Ваших проблем. Методология лишь позволит визуализировать Ваш процесс «как есть»!
Определить, что является потерей, а что нет, а уж тем более придумать как оптимизировать Ваш бизнес-процесс, Вам предстоит самим. «Lean Six Sigma»– есть способ изучения Ваших бизнес-процессов. Нового в нем ни чего нет – статистика, статистика и еще пару способов визуализации.
Работа на уровне «Шесть сигм» — это работа с 3,4 дефектными изделиями на миллион. Уровень дефектности 3,4 из миллиона это Выход годного на уровне 99,99966%. Многие скажут: достаточно и 99%, а в металлургии норматив ставят на уровне 96%. Давайте сравним Выход годного 99% и 99,99966%.
Давайте возьмем выход годного 99% (на металлургических предприятиях норматив выхода годного находится в диапазоне от 96% до 100%):
- потерянных писем на почте — 20 000 штук в год;
- ошибок в рецептах врачей — 200 000 штук в год;
- задержанных рейсов в аэропорту — 2 рейса в день.
Если взять 99,99966%, то результат будет совершенно иной:
- потерянных писем на почте — 6,8 штук в год;
- ошибок в рецептах врачей — 68 штук в год;
- задержанных рейсов в аэропорту -1 рейс в год.
Работа на уровне «Шесть сигм» позволяет получать значительную экономию на операции «контроль качества» или вовсе ее исключить, если Вы готовы жить с этим уровнем дефектности. Никто не спорит, что это нужная операция, но Вам за нее никто не заплатит!
В методологии нет ответа на вопрос: какой уровень дефектности применим для моего бизнеса? Найти ответ на этот вопрос Вам предстоит самим. Но как правило, у продукции есть ряд существенных характеристик, на которые влияют различные параметры, обеспечить необходимое качество, по каждой из этих характеристик, может только уровень «Шесть сигм». И Вы сами должны принять уровень дефектности, с которым Вы готовы мириться.
В таблице ниже приведен уровень дефектности в зависимости от уровня в сигмах:
Управленческий уровень
Управленческий уровень занимается созданием инфраструктуры для реализации проектов улучшений и развития системы бережливого производства в целом. На управленческом уровне происходит координация работы подразделений и именно на этом уровне слышен, так называемый, «Голос клиента».
«Голос клиента» – ожидание потребителя от Вашей продукции: качество, количество, сроки поставки, комплектация и другие параметры. Благодаря «Голосу клиента» «Lean Six Sigma» поможет Вам оптимизировать бизнес-процессы. Исходя из анализа «Голоса клиента» Вы поймете за что Клиент готов платить – все остальное Ваши убытки.
Типы потерь в бизнесе:
- Перепроизводство. Последствия: преждевременный расход сырья; дополнительные закупки материалов; избыточные запасы, потеря качества.
- Излишние запасы. Последствия: необходимость в дополнительных площадях; дополнительная рабочая сила; возможность повреждения и окончания срока годности; необходимость поиска.
- Излишняя транспортировка. Последствия: увеличение издержек на перемещение — повышение себестоимости; вероятность повреждения продукции при транспортировке.
- Излишние перемещения. Последствия: снижение производительности; повышение вероятности получения травмы.
- Простои и ожидание. Последствия: снижение производительности; повышение себестоимости.
- Излишняя обработка. Последствия: снижение производительности; повышение себестоимости.
- Дефекты и их устранение. Последствия: снижение производительности; повышение себестоимости.
- Неиспользование потенциала работников. Последствия: демотивация персонала; снижение производительности.
Внедрение «Lean Six Sigma» на управленческом уровне – отдельный вид сложного искусства балансировки на грани. Главное не перегнуть, внедряя ту или иную практику, особенно часто «эффективные» менеджеры перегибают с внедрением 5S: изменяют рабочее пространство так, что работать в нем становится невозможно. Как пример: на одном из предприятий я встретил штрафы за несоблюдение правил, которые в течение рабочего дня выполнять физически невозможно:
- Рабочее место: ремонтный стол гидравлических уравновешивающих устройств.
- Требование: отсутствие инструментов и рабочих жидкостей на полу и рабочем столе.
Первым делом, Вы как руководитель, будете создавать базовую инфраструктуру, позволяющую осуществлять стратегическое планирование развития бережливого производства в Вашем бизнесе:
1. Необходимо осуществить конфигурацию целей бизнеса и стратегии, исходя из текущего и желаемого состояний.
2. Создать структуру, которая займется развитием бережливого производства, а именно:
- разработает стратегию внедрения и развития бережливого производства, в том числе методологию и систему обучения персонала;
- стандартизует новые компетенции персонала;
- разработает и внедрит систему мониторинга и оценки достижения поставленных целей;
- разработает мотивационную и информационную составляющую для всего персонала.
После создания инфраструктуры необходимо перейти к формулированию целей для предстоящих проектов улучшений в Вашем бизнесе. В формировании целей могут быть полезны такие инструменты как матрица принятия решений и моделирование будущего состояния.
Рабочий уровень
Рабочий уровень занимается достижением целей, установленных на управленческом уровне. На данном уровне сосредоточена вся работа по улучшению бизнес-процессов.
Первоочередной задачей рабочего уровня является снижение вариативности процесса. В Политехнических институтах СССР учили: каким бы плохим процесс не был, главное, чтобы он был стабильным! Только после стабилизации процесса можно говорить об его оптимизации.
Перед постановкой цели для рабочего уровня Вы должны убедиться всего в двух вещах:
- Процесс стабилен. Стабильно хорош, стабильно плох – значения не имеет. Вы должны, с вероятностью 99,9%, отвечать на вопрос: что произойдет с процессом при изменении вот этого параметра?
- Существующие инструкции выполняются в полном объеме. Большая часть проблем в России заключается в том, что инструкцию никто не открывал. В рамках обходов производств, при реализации проектов на металлургических предприятиях, я прошу продемонстрировать мне инструкции: технологические и рабочие. Первым делом я смотрю на внешний вид инструкции – на металлургическом предприятии, инструкция не может быть идеально чистой. Если меня «устраивает» ее внешний вид, я уже спрашиваю знание критических моментов технологии. В один из своих обходов в производственном цехе, я попросил старшего мастера дать мне его технологическую инструкцию, представьте мое удивление, когда он мне достал запечатанную инструкцию, которую никто не разу не открыл за полгода с момента ее выдачи.
Если Вы уверены, что эти два пункта выполняются в полной мере, то можете смело переходить к постановке целей для проекта.
Методология «Lean 6 Sigma» сконцентрирована на процессном подходе. Все начинается с простого уравнения, которое знакомо еще со школы:
Где
Х – входы в процесс: параметры настройки персонал, материалы, электричество, вода и так далее;
Y – выход из процесса, его результат;
f – функция, трансформирующая все входы в результат;
ε – ошибка, которую мы себе оставляем: неуверенность в возможности процесса получать необходимый результат (желаемый результат возможно лежит за физическими возможностями оборудования), а также неуверенность в нашей способности адекватно измерить входы Х.
Погрешность может возникнуть из-за нашей ошибки, а также из-за самого процесса.
Как правило, в «Lean 6 Sigma», погрешность устанавливается на уровне 5%. Входы преобразуются в выходы проходя через процесс. Ваша задача понять, как изменение входов влияет на выход из процесса. Необходимо проанализировать каждый результат через призму совокупности входов, процесса и погрешности. И если Вы сможете понять, как это все взаимосвязано – Вы сможете улучшить процесс.
Проект начинается как некая практическая проблема, которую необходимо описать количественно. После выразить взаимосвязь входов и выходов статистически, на основе чего разработать статистическое решение. Схематически это выглядит так:
В реализации проектов «Lean 6 Sigma», как правило используются, следующие системы, инструменты и подходы:
— 5S;
— DMAIC;
— TPM;
— SMED.
5S
5S – система создания качественной и комплексной рабочей среды, применяемой для повышения уровня безопасности работы, производительности труда и качества его результатов. Система получила свое название от первых букв пяти японских слов:
Seiri – сортировка;
Seiton – систематизация;
Seiso – систематическая уборка;
Seiketsu – стандартизация;
Shitsuke – совершенствование (соблюдение).
Модные западные течения дополняют 5S понятием «Безопасность» (Safety) и именуют систему 5S+1. Принято считать, что система 5S зародилась в Японии, однако, при разработке методики использовались труды А.К. Гастева и СССР в сфере научной организации труда.
В рамках работы по 5S необходимо выполнить 5 последовательных шагов по итогам которых, Ваше рабочее место повысит Вашу рабочую эффективность.
TPM
Total Productive Maintenance (TPM) — это подход к управлению оборудованием на протяжении всего жизненного цикла, направленный на предупреждение отказов в его работе и снижение расходов на его обслуживание. Подход подразумевает, что ответственность за поддержание оборудования в исправном состоянии несут все работники, включая операторов, механиков, менеджеров и инженеров. TPM является системой, обеспечивающей идеальное совмещение эффективного использования производственных мощностей и затраты на поддержание их в рабочем состоянии за счет уменьшения поломок и простоев, а также увеличения производительности и совершенствования оборудования.
Целью внедрения TPM является устранение потерь:
- Выход из строя оборудования
- Высокое время переналадки и юстировки
- Холостой ход и мелкие неисправности
- Снижение быстродействия (скорости) в работе оборудования
- Дефектные детали
- Потери при вводе в действие оборудования.
SMED
SMED (Single Minute Exchange of Dies) — быстрая переналадка. Один из многих методов Бережливого производства, представляющий собой способ сокращения издержек и потерь при переналадке и переоснастке оборудования. Представляет собой набор теоретических и практических методов, которые позволяют сократить время операций наладки и переналадки оборудования. Изначально эта система была разработана для того, чтобы оптимизировать операции замены штампов и переналадки соответствующего оборудования, однако принципы «быстрой переналадки» можно применять ко всем типам процессов. Ярким примером SMED является pit-stop формулы 1.
DMAIC
DMAIC (аббревиатура от англ. define, measure, analyze, improve, control — определение, измерение, анализ, совершенствование, контроль) – подход к последовательному решению проблем, совершенствованию бизнес-процессов, используемый в управлении производством. Один из подходов, используемый в методологии «шести сигм». Согласно DMAIC, решение каждой задачи совершенствования процесса или устранения проблемы должно пройти через следующие этапы: define (определение), measure (измерение), analyze (анализ), improve (совершенствование) и control (контроль), для каждого из этапов в подходе предполагается конкретика, что необходимо осуществить на каждом из этапов. Считается, что именно такая последовательность обеспечивает структурированный подход, позволяющий пройти от определения сути проблемы к внедрению решений по совершенствованию с использованием лучших практик.
DMAIC, как и большинство методологий совершенствования основаны на цикле Деминга — PDCA (аббревиатура от англ. Plan, do, check, act).
В русском языке общепринят аналог аббревиатуры DMAIC — ОИАСК: определение — измерение — анализ — совершенствование — контроль.
На первом этапе — определение — необходимо определить заказчиков, обоснования проекта, рамки, цели и временные границы проекта.
На этапе измерение определяются основные метрики проекта, надёжность источника данных, актуальное состояние процесса.
Этап анализа заключается в исследовании возможностей процесса, причин проблемы, возможных рисков.
На этапе совершенствование осуществляется модификация процессов и систем, структурная декомпозиция работ.
Последний этап — контроль — предназначен для поддержания изменений процессов, подготовка отчётов и закрытия проекта.
На этом все, если кому-то будет интересно реально изучить каждый из инструментов и методик — предоставлю материал абсолютно бесплатно! Могу также тут сделать цикл обучающих статей от 5S до Lean 6 Sigma.
Организация Бережливого Производства по этапам
Организация Бережливого Производства с точки зрения лидера изменений. Взгляд на внедрение с практической стороны, как это было, как лучше сделать по-другому, и где можно избежать ошибок.
Содержание
Внедрение системы Бережливого Производства – практические наработки от лидера внедрения
Организация Бережливого Производства по этапам
Что самое сложное во внедрении и организации Производственной системы?
Управление на основе принципов Lean
Ошибки организации системы Бережливого Производства, которые стоят миллионы
Бережливое Производство консалтинг
Внедрение системы Бережливого Производства – практические наработки от лидера внедрения
Предлагаю свой практический опыт для внедрения системы Бережливого Производства. Проработав на позиции руководителя направления Производственной программы, пройдя от А до Я, все стадии и этапы, могу поделиться наработками.
Для начала, если интересно, можно почитать простое описание про Бережливое Производство, что есть что (про ЛИН-технологии, про Бережливое Производство, про Производственную программу).
Организация Бережливого Производства требует системного подхода, тщательной подготовки для внедрения. Необходимо пройти все этапы перед непосредственной реализацией кардинальных изменений.
Внедрение системы Бережливого Производства идет по 3 направлениям:
- Изменение мышления
- Управление на основе принципов ЛИН
- Оптимизация процессов
Создаем базу для внедрения Производственной системы по этапам.
Организация Бережливого Производства по этапам
1 этап
Внедрение системы Бережливого Производства начинается с подготовки персонала. В первую очередь необходимо выбрать лидера внедрения. Лидер внедрения – это человек с широкими полномочиями, который будет продвигать в массы Бережливое Производство. От выбора главного действующего лица зависит, будет у новой философии успешное внедрение, или полный провал. Этот момент крайне важен.
Критерии для отбора:
Психологическое образование или высший менеджмент. Опыт работы руководителем. Именно эффективным. Так как в первую очередь – Бережливое Производство, Лин – технологии – это работа с мышлением. Изменение способа мышления, а уже потом способа работы.
Уделить внимание характеру – не конфликтный, но принципиальный, с твердым характером и отсутствием страха перед начальством. Этот последний момент очень важен, так как придется очень часто общаться с руководством и отстаивать свои позиции и рассказывать о новой системе. Быть убедительным. Поэтому в списке компетенций надо – умение выступать, отсутствие страха перед публичными выступлениями. Быстрая обучаемость, способность передать мысли и обучение другим.
Итак. Такой человек подобран. Далее идет череда всех обучений по ЛИН-технологиям, включая историю возникновения, владение инструментами Бережливого Производства.
Конечно, только с опытом появится виртуозное владение инструментами. Поэтому, первичны – именно психологические характеристики данного специалиста. Всему остальному можно научиться.
2 этап
Обучение руководства. Тут надо уделить внимание не только самой методике Производственной программы, как сделать акцент на том, что руководитель должен поддерживать лидера внедрения во всем. У нас в организации это происходило достаточно мудро. Руководитель сам рассказывал сотрудникам о философии Кайдзен.
То есть задача максимум ТОП-руководству проникнуться идеей изменения и принять внутри себя. Сотрудники очень чувствуют фальшь. И если руководитель сам азартно и с эмоциями верит в лучшие перемены, то этим заражает всех окружающих. Это идеальная картина.
Этап 3
Рассказать о предстоящих изменениях, и о целях и принципах Бережливого Производства.
Надо понимать, что пиар компания не быстрая. Чтобы информация усвоилась и была принята хотя бы частично, необходимо проводить регулярные мероприятия. Презентации, семинары, посвятить этому вопросу время на командообразующих мероприятиях. Информационная сторона вопроса и эта подготовка сотрудников, поможет более мягко перенести потрясение от изменений.
Работа с мышлением – самая трудоемкая. Но без предварительной подготовки и эмоционально подогрева будет очень много сопротивления.
Человека трудно заставить что-то из под палки делать, а если это касается полной перекройки производства, то негативные последствия будут накапливаться, как снежный ком. Время, потраченное вначале, окупиться отсутствием срывов в середине и в конце проекта. Уменьшится саботаж.
Этап 4
Обучить сотрудников азам Бережливого производства, Всех сотрудников без исключения. Причем, линейный руководители должны выезжать на многодневные тренинги с элементами командообразования и обучения управленческим функциям.
Сотрудники могут пройти обучение дистанционно. Например, как это сделано в компании Мираторг. Создана программа с элементами геймификации, с интерактивными кейсами. И сотрудники, проходя уровень, играя, обучаются и сдают тесты.
Этап 5
Это самый важный этап при организации и внедрении Бережливого Производства. Работа с мышлением описана в отдельной главе ниже.
Этап 6
Закрепление в системе материальной мотивации четких критериев оценки работы + инициативность.
Этап 7
Выстраивание системы инноваций в компании. Тема настолько обширна, что написала целую статью, как мы развивали инновационную деятельность в своей компании.
Этап 8
Пилотный проект. Вот и все готово: цели объявлены, сотрудники подготовлены, руководители обучены. Можно приступить к апробации инструментов Бережливого Производства. Рекомендуется организовать пилотный проект на базе одного подразделения или локального бизнес-процесса.
Обратите внимание, будет очень хорошей поддержкой, если в пилотном проекте — руководитель энтузиаст с горящими глазами. Он своей энергетикой сдвинет горы, не то, что сотрудников )).
Длится пилотный проект – от 3 месяцев до 9. Лучше всего результаты можно увидеть на 5 и 6 месяц. Понять, что сделано правильно, что «подкрутить». И только после «подкрутки» можно переносить положительный опыт на всю организацию целиком.
Заканчиваются этапы подготовки при организации Бережливого Производства, начинается непосредственное внедрение системы ЛИН-технологий (Производственной системы) в компанию.
Этап 9
Это и будет непосредственное внедрение — оптимизация процессов. С целью уменьшения потерь и увеличения рентабельности бизнеса. Получить представление об оптимизации процессов на примере малого бизнеса можно тут.
Какие инструменты мы применяли можно также почитать в рубрике Бережливое Производство – описано много инструментов с практической стороны.
Что самое сложное во внедрении и организации Производственной системы?
Ответ прост — работа над изменением мышления. 99% всех провалов при внедрении Бережливого Производства объясняется пропуском этого этапа.
Вы никогда не сумеете решить возникшую проблему, если сохраните то же мышление и тот же подход, который привел вас к этой проблеме. Альберт Эйнштейн
Этой теме должно посвящено очень много времени при подготовке. Потому что, это основополагающий подготовительный этап. Чем крепче платформа, тем устойчивее сооружение.
Знаете, у строителей есть примета. Они могут по любому фундаменту определить, насколько хорошо и прочно, и долговечно здание. Чем глубже и усиленный фундамент, тем больше шансов простоять на века. И здесь та же история.
Наряду с обучение персонала по «отвлеченным» темам (тайм-менеджмент, креативность, командообразование, стрессоустойчивость, разрешение конфликтов) проводить регулярную пиар компанию по Lean-теме. Плюс новости, обсуждения в локальной сети результативных примеров.
Едва ли не самое значимое – корректировать способы управления и коммуникаций у линейных руководителей среднего звена.
Изменение мышления у руководителей
- «Увидеть своими глазами» – один из важнейших принципов, средство, позволяющее убедить руководителя и заставляющее его понять свою новую роль
- Система управления преобразованиями необходима для внедрения принципов «Лин», а не наоборот. Важен результат, а не видимые элементы программы
- Обязательно создайте заинтересованность руководителей в переменах, прежде чем задавать им вопросы и просить их действовать
- Обеспечьте быстрое достижение эффекта в пилотных проектах, чтобы эти примеры поддержали веру в успех
- Для свершения преобразований необходимо создать убедительную историю, обосновывающую необходимость изменений
- Сопротивление изменениям не должно быть для вас сюрпризом – это нормальная практика
- Не жалейте времени на поиски путей убеждения руководства, вместо того чтобы жаловаться, что оно не помогает вам. Обеспечить поддержку со стороны руководства – ваша прямая обязанность
- Очень часто, обсуждение руководителя основано, скорее, на слухах, чем на фактах
- Определите вопросы действительно первостепенной важности для руководителя, создайте команду лидеров преобразований, дайте каждому из них определить свою роль – и вы получите руководителей, преданных делу до конца!
Главной задачей у руководителей — изменить критические настроения, которые мешают раскрытию полного потенциала компании и сотрудников.
Мероприятия по изменению мышления не должны прерываться или заканчиваться. Этот блок работы настолько фундаментален, потому что российский менталитет отличается от японского менталитета. А философия Бережливого Производства базируется на японской системе Кайзен. (можно почитать статью про Кайдзен)
От текущих настроений | К мышлению согласно Lean |
Смещение ответственности «Компания должна создать условия, в которых я смогу добиться результатов» | Прозрачность и измеримость результатов «Оценивается продуктивность моей работы, и это единственный критерий оценки успешности всех сотрудников» |
Зависимость «Я считаю других виноватых в том, что происходи со мной» | «Один в поле воин» «У меня есть идеи, которые могут улучшить результаты проекта» |
Скептицизм «Существуют проблемы, которые нам не преодолеть» | Доверие в команде «Руководители открыто и четко ставят цели, и формулируют свои ожидания от сотрудников |
Ментальность «Или…, или…» «Мы фокусируемся на количестве в ущерб качеству | Ментальность «И…, и…» «Мы можем одновременно добиться успеха по многим направлениям деятельности банка (затраты, качество обслуживания) и завершить масштабное развертывание» |
Из этой таблицы напрашивается вывод – пора менять систему KPI (можно почитать статьи на эту тему)
Отдельно, не помещая в рамки «шагов» поговорим об управлении в стиле Lean.
Управление на основе принципов Lean
Этот вид менеджмента также предполагает огромную работу по изменению мышления самих руководителей. Не имея заинтересованности и азарта, веры в успех – трудно дойти до конца на этой должности.
К сожалению, действительно, были такие случаи в практике, что руководители или сами не выдерживали своего внутреннего сопротивления и увольнялись. Либо, после очередной провальной сертификации Производственной системы, происходила внутренняя ротация, и человек терял должность.
Руководство на основе ЛИН держится на принципах:
- Цель
- Сотрудники
- Взаимодействие
- Решение проблем
- Результативность
- Процесс
Необходимо учиться:
«Четко формулировать ожидания»
- Ставить четкие цели, исходя из потребностей бизнеса, и объяснять логику поставленных задач сотрудникам. Про постановку целей по SMART — читайте отдельно.
- Регулярно отслеживать выполнение поставленных целей, прозрачно обсуждая результаты каждого из сотрудников.
- Создать ощущение индивидуальной ответственности сотрудников, проводя двусторонние встречи с каждым членом команды для обсуждения результатов и постановки целей.
«Ценить, уважать и развивать своих сотрудников»
- Сделать так, чтобы сотрудники видели, что их точка зрения учитывается в принимаемых решениях
- Развивать людей, совершенствуя их навыки, а также с помощью наставничества и обратной связи
- Поддерживать предложения по улучшению, отмечать и вознаграждать их авторов.
«Работать в единой команде, с единой целью и едиными стандартами»
- Быть открытым к идеям других членов команды и воспринимать их как «шаг к общей цели».
- Активно взаимодействовать с различными подразделениями организации, копируя передовой опыт из других подразделений и регионов.
«Увидеть все собственными глазами»
- Рассматривать проблемы не из своего кабинета, а на месте их возникновения, быть готовым к встрече с рядовыми сотрудниками, чтобы получить информацию «из первых рук».
- Разбираться в истинных причинах возникающих проблем, а также решать проблемы системно.
- Искать творческие, простые и дешевые решения вместе с сотрудниками, предлагать свои идеи. Подробнее почитать про Гемба можно отдельно.
«Быть приверженцем стандартов»
- Всегда придерживаться стандартов работы компании, не создавать прецедентов «выборочного» поведения в отношении сотрудников или при принятии решений.
- Искать и устранять потери в работе организации, инициировать изменения процессов работы и замечать инициативы по улучшению процессов со стороны сотрудников (про потери можно почитать тут).
Нельзя не сказать об ошибках, которые стоят миллионы.
Ошибки организации системы Бережливого Производства, которые стоят миллионы
Переживания многих собственников по поводу финансовых риском имеют под собой реальную основу. Действительно, можно «угробить» катастрофически большой бюджет и не добиться результатов.
По анализу консалтинговых агентств – это ошибки:
- Лидер влияния – не имеет лидерских качеств и авторитета
- Руководство не прониклось идеей преобразования собственной компании
- Сотрудники ведут внутренний саботаж, скрытое сопротивление, которое трудно обнаружить. Потому что человек не выражает несогласия бурно, кивает головой, но ничего не делает. Этот вид внутреннего саботажа очень опасен, что его трудно рассмотреть на ранней стадии и обезвредить.
- Организация Бережливого Производства происходит слишком стремительно, пропустив этап работы с мышлением, приступив непосредственно к оптимизации процессов.
- Все и сразу. Слишком много подразделений для преобразований.
- Успокоение и потеря контроля через 3-6 месяцев. В этом случае, если не поддерживать постоянный Кайдзен, то есть риск «откатиться» на начальный уровень и даже ниже.
Подводя итоги,
Ключевые факторы успеха общей программы Лин Трансформации:
- Вовлеченность высшего руководства:
- Авторитетный куратор программы в организации
- Ограниченное количество параллельно идущих проектов для возможности сфокусироваться на Лин (лучше всего 1-2 пилотных проекта)
- Убедительная программа коммуникаций, показывающая необходимость изменений
- Оперативное управление участниками проекта для своевременного выявления возможных проблем
- Радикальные изменения и успехи, достигнутые в пилотном проекте:
- Сильные лидеры программы, способные управлять организацией/проектом на основании принципов Лин
- Большое количество квалифицированных, надежных и уважаемых участников программы (которые могут быть направлены в другие регионы после завершения пилота и стать «агентами перемен»)
- Радикальные изменения в пилоте формируют сильный сигнал и ожидания от всей программы преобразований Лин
- Стандартизация и Кайдзен. Распространение успешного опыта на всю компанию, на все бизнес-процессы. Поочередное проникновение системы Бережливого Производства во все смежные подразделения. Правильнее это сделать волнами, чтобы не утратить контроля над происходящим.
Вот и состоялась передача наработанного практического опыта.
Возможно, будут интересны статьи по темам: повышение производительности, эффективный руководитель, все о мотивации и KPI.
Бережливое Производство консалтинг
Внедрение системы Бережливого Производства – процесс многоэтапный и сложный. Без опыта и сопровождения затруднительно сделать правильные шаги. Консалтинг в сфере управления процессами предлагает широкий выбор специалистов. Однако, так как это — длительная и затратная перестройка всего бизнеса, обращайте внимание на опыт консультантов.
Бытует мнение, что в малом или микро бизнесе нечего оптимизировать. Однако эта очень дорогая ошибка, которая обходится либо финансовым потолком, либо банкротством. В любом бизнесе, где есть 3 человека — уже можно применять азы Бережливого Производства и совершенствовать процессы. А значит, выходить на новый уровень прибыли.
Готова сотрудничать в сфере внедрения, обучения сотрудников и руководителей Lean технологиям и инструментам Бережливого Производства.
Надеюсь, Вы нашли ответы, как нужно подготовиться, чтобы организация Бережливого Производства прошла гладко, и внедрение Производственной системы дало результаты в виде многократной повышении прибыли.
С верой в Ваш успех, Светлана Васенович
P.S. Скачивайте бесплатную инструкцию по управлению собственным бизнесом – Рестайлинг твоего бизнеса.
Простое руководство по системе бережливого производства
Система экономичного производства — эффективный способ сократить отходы и увеличить прибыль.
Вы хотите уменьшить количество отходов и повысить качество своей продукции?
Как насчет снижения стоимости инвентаря и увеличения прибыли?
Вы, наверное, тоже хотели бы повысить свою продуктивность, верно?
Эти улучшения обычно трудно найти на производстве.
Но компании по всему миру пожинают эти преимущества, внедряя один проверенный производственный метод…
Система бережливого производства.
Мы покажем вам, что это за система, основные принципы, лежащие в ее основе, основные сокращения отходов, которые вы можете ожидать от нее, и основные инструменты, которые вам понадобятся для ее реализации.
К концу вы получите четкое представление о бережливом производстве и о том, как оно может превратить ваше предприятие в эффективную электростанцию.
Что такое система бережливого производства?
Система бережливого производства, которую часто называют бережливым производством, бережливым производством или просто «бережливым производством», представляет собой систему для максимизации ценности продукта для потребителя при минимизации потерь без ущерба для производительности.
Одним из первых крупных пионеров «бережливого мышления» (хотя он этого не знал) был Генри Форд , который был основным спонсором и промоутером конвейера .
Но бережливое производство в том виде, в каком мы его знаем сегодня, уходит своими корнями в Toyota Production System (TPS), которая была создана Taiichi Ohno и Eiji Toyoda в Японии в период с 1948 по 1975 год.
До того, как он был известен как TPS, его просто называли , производство точно в срок .
Было 3 вещи, которые производственная система Toyota пыталась предотвратить:
Muda
Muda — японский термин, обозначающий «отходы». Муда — это все в вашем производственном процессе, которое создает отходы или затрудняет создание ценного продукта.
По данным Центра исследований бережливого предпринимательства (LERC) , 60% всех видов деятельности в обрабатывающей промышленности вообще не добавляют ценности.
Согласно TPS, есть 8 отходов, над устранением которых необходимо работать:
- Дефекты — ошибки, исправление которых требует дополнительного времени, ресурсов и денег.
- Перепроизводство — когда те, кто получает продукцию, не готовы к ней или не нуждаются в ней, потому что рабочие продолжают производить больше без необходимости.
- Ожидание — Когда работа должна быть остановлена, потому что кто-то перегружен, что-то сломалось, вы ждете одобрения или материалов, или потому что у вас что-то закончилось.
- Неиспользование талантов — Недостаточное использование талантов, навыков и знаний людей (не является частью исходных отходов TPS, но все чаще рассматривается как отходы нынешними производителями Lean).
- Транспортировка — Слишком большая транспортировка, приводящая к увеличению затрат, потере времени и повышенной вероятности повреждения и порчи продукта.
- Избыток запасов — когда предложение превышает реальный потребительский спрос, что маскирует реальное производство.
- Отходы движения — Любые лишние движения сотрудников или машин, которые не добавляют ценности продукту, услуге или процессу.
- Избыточная обработка — любая задача, которая обрабатывается больше, чем требуется
Эти 8 отходов можно запомнить, используя аббревиатуру DOWNTIME.
Мура
Mura — это японский термин, обозначающий «неравномерность работы». Мура — это все, что создает непоследовательные и неэффективные рабочие процессы.
Примером Mura может быть, если вы загрузите грузовик с на меньше поддонов, чем он может вместить за одну поездку, а затем загрузите его на больше, чем на поддонов, чем он может вместить во время второй поездки, что приведет к увеличению времени выполнения заказа на .
Мури
Muri — это японский термин, обозначающий «перегруженность людей и оборудования.«Мури — это все задачи или нагрузки, которые создают слишком большую нагрузку на ваших сотрудников или машины.
Мури может вызвать выгорание сотрудников — например, если у вас слишком много работы и вы не делегируете ее часть кому-то другому.
Или Мури может вызвать полную поломку фабричной машины — как в случае слишком долгого производства или слишком большого количества продуктов, чем разрешено стандартами этой машины.
Сводя к минимуму или исключая Muda, Mura и Muri, сторонники TPS и системы бережливого производства считают, что вы можете производить продукцию высочайшего качества, одновременно увеличивая свой доход и производительность.
Мы рассмотрим инструменты, которые помогут вам предотвратить «неравномерность в ваших операциях» и прекратить «перегружать людей и оборудование» на мгновение, но сначала давайте посмотрим, как философия TPS уступила место 5 краеугольных принципов бережливого производства.
Каковы 5 основных принципов бережливого производства?
В 1996 году была опубликована книга Бережливое мышление , навсегда закрепившая совершенно новый способ производства.
Авторы — Джеймс П.Womack и Daniel T. Jones — обобщили уроки, извлеченные из соблюдения TPS, до 5 принципов бережливого производства.
Эти 5 принципов по-прежнему лежат в основе любой системы бережливого производства.
Пять принципов:
Значение
Первый принцип бережливого производства — ценность, согласно которому компания должна поставлять покупателю наиболее ценный продукт. Таким образом, ценность определяется клиентом, а не компанией или ее менеджерами.
Поток создания ценности
Второй принцип бережливого производства — поток создания ценности, который гласит, что после того, как вы определили ценность, которую собираетесь предоставить своим клиентам, вы должны наметить этапы и процессы, необходимые для производства этих ценных продуктов.
В системе бережливого производства вы должны фактически растянуть каждый шаг вашего процесса, от сырья до готового продукта.
Цель состоит в том, чтобы определить каждый шаг, который не создает ценности, и найти способы их избежать.
Поток
Третий принцип бережливого производства — это поток, который гласит, что после того, как вы устранили большую часть или все отходы из своей системы, вы проходите процесс, обеспечивающий плавное выполнение всех ваших шагов по добавлению стоимости, без перерывов, задержек или узких мест.
Тянуть
Четвертый принцип бережливого производства — тяга, который гласит, что продукты должны создаваться «точно в срок», чтобы материалы не складывались, а клиенты получали свои заказы за недели, а не за месяцы.
Совершенство
Пятый принцип бережливого производства — это совершенство. Он гласит, что бережливое мышление и улучшение процессов должны стать ключевой частью корпоративной культуры.
Lean — это не статическая система, она не работает одинаково для всех компаний, и менеджеры — не единственные, кто внедряет Lean — сотрудники также играют активную роль в обеспечении экономичности компаний.
Чтобы сделать систему бережливого производства более конкретной и менее абстрактной, давайте рассмотрим несколько инструментов, которые вам понадобятся для внедрения бережливого производства в ваш бизнес.
Какие инструменты бережливого производства являются наиболее полезными и действенными?
Чтобы избавиться от Муда, Муры и Мури, вам нужно будет реализовать целый ряд инструментов и научиться ими пользоваться.
Вот краткий список некоторых из наиболее важных инструментов в системе бережливого производства:
Система 5S
Система 5S — это метод организации материалов на рабочем месте для более быстрого доступа и лучшего обслуживания. Эта система необходима для устранения отходов, которые производятся некачественными рабочими станциями и инструментами в плохом состоянии.
Пять S:
- Seiri (Сортировать) — Удалите все ненужные элементы для текущего производства, оставив только то, что необходимо.
- Seiton (Set In Order) — Организуйте оставшиеся элементы и пометьте их соответствующим образом.
- Seiso (Shine) — Ежедневно очищайте и проверяйте рабочее место и все, что в нем.
- Seiketsu (Стандартизация) — Запишите свои стандарты для этапов сортировки, установки в порядок и очистки, указанных выше.
- Shitsuke (Sustain) — Примените стандарты, которые вы установили для своей компании, и сделайте их привычными для всех в вашей организации.
Планирование, выполнение, проверка, действие (PDCA)
PDCA — это четырехэтапный метод постоянного улучшения вашего процесса и продуктов. Он применяет научный метод к производству, чтобы вы могли добиваться лучших результатов на протяжении всей жизни вашего бизнеса.
Вот каждый шаг:
- План — Определите цели процесса и необходимые изменения для их достижения.
- Do — Внедрить изменения.
- Проверка — Оцените результаты с точки зрения производительности.
- Акт — Стандартизируйте и стабилизируйте изменения или начните цикл заново, в зависимости от результатов.
Heijunka (Регулирование производства и спроса)
Хейдзунка (выравнивание производства и спроса) — это метод, специально разработанный для уменьшения муры (неравномерности) путем производства товаров меньшими партиями с постоянной скоростью.
Это помогает сократить время выполнения заказа и сократить запасы. , поскольку каждый продукт или его вариант производятся чаще с предсказуемой скоростью.
Кайдзен (постоянное улучшение)
Кайдзен — это практика постоянного наблюдения, выявления и внедрения дополнительных улучшений в производственный процесс.
Он побуждает всех руководителей и сотрудников участвовать в процессе улучшения производства.
Кайдзен гарантирует, что отходы будут постепенно сокращаться благодаря коллективным талантам и знаниям всех сотрудников компании, работающих вместе, чтобы ежедневно устранять малейшие недостатки.
Канбан (система вытягивания)
Канбан (вытягивающая система) позволяет сотрудникам «тянуть» работу на свои рабочие места, когда они будут готовы. Это предотвращает перегрузку сотрудников Muri и позволяет руководителям и сотрудникам сосредоточиться на нужных задачах в нужное время без лишних затрат усилий или времени.
Как отслеживать запасы в системе бережливого производства?
Хранение запасов обычно рассматривается как проблема в бережливом производстве. Чем ближе вы сможете свести инвентарь к нулю, тем лучше.
Но вам все равно нужен способ управления запасами, поступающими на ваш склад, вместе с вашими заказами на покупку, заказами клиентов и т. Д.
Поскольку бережливое производство требует от вас гибкости и скорости при поступлении заказов, необходима система управления запасами, которая может быстро реагировать и выполнять заказы так быстро, как они вам нужны.
Вы не получите этого с помощью ручного управления запасами электронных таблиц .
Но вы можете получить его из облачного управления запасами .
Узнайте, как это сделать…
Сделайте бережливое производство проще с помощью DEAR Inventory
DEAR автоматизирует заказы на закупку, чтобы быстро получать товары, когда они вам нужны, отслеживать важные KPI для постоянного улучшения ваших процессов и рабочего процесса, а также дает вам подробное представление о ваших производственных затратах для сокращения отходов и повышения производительности. Если вы серьезно относитесь к бережливому производству, DEAR сделает этот процесс намного более плавным.
Начните бесплатную 14-дневную пробную версию DEAR Inventory сегодня!
Попробовать DEAR бесплатно
Кредитная карта не требуется
.Что такое бережливое производство? Бережливое производство и бережливое предприятие
Глоссарий качества Определение: бережливое производство
Бережливое производство определяется как набор методов управления, направленных на повышение эффективности и результативности за счет устранения потерь. Основной принцип бережливого производства заключается в сокращении и устранении видов деятельности и потерь, не создающих добавленной стоимости.
Бережливое производство (производство) против бережливого предприятия
Бережливое производство, или бережливое производство, — это система методов и действий для управления производством или обслуживанием.Методы и действия различаются в зависимости от конкретного приложения, но в их основе лежит один и тот же принцип: устранение всех видов деятельности, не создающих добавленной стоимости, и потерь в бизнесе.
Бережливое предприятие распространяет эту концепцию на весь поток создания ценности или цепочку поставок: самый экономичный завод не может полностью реализовать свой потенциал, если ему приходится работать с не бережливыми поставщиками и субподрядчиками.
Внедрение примера бережливого производства
Какие семь типов отходов (муда) в бережливом производстве?
Отходы, или muda на японском языке, определяется как выполнение ненужной работы в результате ошибок, плохой организации или общения.
Специалисты по качеству часто спорят, есть ли семь или восемь потерь бережливого производства. Восьмая трата бережливого производства уникальна из семи первоначальных, поскольку ее устранение может принести непосредственную пользу сотрудникам, а также работодателю.
Восемь муда бережливого производства можно запомнить, используя аббревиатуру DOWNTIME .
- D Эффекты
- O версия
- Вт и
- N задействованные таланты
- T Транспортировка
- I инв.
- M otion
- E xtra-обработка
Учебники по бережливому производству
Примеры использования бережливого производства
Использование принципов бережливого производства во всей организации может предложить вам конкурентное преимущество за счет снижения эксплуатационных расходов и повышения производительности.Преимущества внедрения бережливого производства оптимизируются в сочетании с кайдзен-событиями, шестью сигмами, теорией ограничений и другими методологиями улучшения.
Следующие ниже тематические исследования более подробно рассматривают результаты, достигнутые организациями при использовании бережливых методологий и подходов. Вы также можете найти больше примеров успеха в области качества, посетив ASQ Quality Resources.
Lean Six Sigma повышает эффективность компании по предоставлению финансовых услуг (PDF) Организация, предоставляющая финансовые услуги, использовала подход Lean Six Sigma, который включал в себя кайдзен-события для улучшения контроля процессов и увеличения производительности.Всего за четыре месяца в рамках девяти проектов быстрого реагирования удалось сэкономить 220 000 долларов США, что открыло путь к более крупным стратегическим улучшениям.
Непрерывное совершенствование в двух компаниях (PDF) Тодд Шнайдер делится уроками, извлеченными из помощи по интеграции непрерывного совершенствования в операции двух компаний. Примеры проектов по усовершенствованию у его нынешнего работодателя, Serigraph, показывают, как команды использовали «Шесть сигм» для повышения урожайности более чем на 20%, сэкономив 40 000 долларов за 10 месяцев, и улучшив управление материальными ресурсами поставщиков, сэкономив 192 000 долларов в год.
Лучший способ выполнять портативные рентгеновские снимки (PDF) Многофункциональная группа медицинского центра Аврора Сент-Люк использовала простые инструменты для разработки новой процедуры проведения портативных рентгеновских снимков. Усовершенствования процесса привели к снижению затрат на оплату труда работников, повышению производительности и безопасности пациентов.
Barnes-Jewish Hospital повышает качество ухода за пациентами, переходя на бережливое производство. (PDF) Учебная программа по бережливому производству в Barnes-Jewish Hospital объединяет образовательную программу для всех сотрудников с целенаправленным улучшением потоков создания ценности.
Проблема преодоления успеха (PDF) Сочетание теории ограничений, шести сигм и бережливого производства помогло лаборатории тестирования ДНК применить целостный подход к совершенствованию процессов. Пересмотр рабочего процесса и планировки лаборатории и введение новых правил работы увеличили производительность без увеличения затрат.Индустрия доброй воли Юго-Восточного Висконсина: интеграция качества и социальной ответственности (PDF) Индустрия доброй воли Юго-Восточного Висконсина использует методы бережливого производства и мероприятия кайдзен для улучшения процессов и повышения социальной ответственности.За два года внедрения бережливого производства компания Goodwill провела 16 мероприятий по совершенствованию процессов, что позволило сэкономить около 2,8 миллиона долларов на рабочей силе и расходных материалах.
Это вопрос времени: судовые сервисные службы используют быстрый кайдзен для сокращения длительных сроков ремонта (PDF) Группа калибровочной лаборатории Йокосука, Судоремонтного завода ВМС США и Японского регионального центра технического обслуживания использовала серию мероприятий кайдзен, чтобы сократить время обслуживания время на 68%. Команда квалифицировалась как финалист конкурса International Team Excellence Award 2008 ASQ.
Соединяем все вместе: лучшая организация материалов улучшает судоремонтный сервис (PDF) Сотрудники производственного цеха Sasebo на судоремонтном заводе США и Японском региональном центре технического обслуживания использовали экономичный подход 5S, чтобы создать новый способ управления запасами материалов . Команда сократила время, затрачиваемое на поиск запчастей, на 80% и стала финалистом конкурса ASQ 2008 International Team Excellence Award.
Экологичность с помощью Lean (PDF) Группа международной торговли юридического отдела JDSU использовала инструменты бережливого производства для устранения потерь в процессах управления импортом.Создав безбумажный процесс, команда увеличила объем работы на 500% и устранила не менее 70 000 бумажных копий в год.
Повышение производительности за счет рационального проектирования складов «шесть сигм» (PDF) Команда по совершенствованию «бережливого производства и шести сигм» в New Breed Logistics использовала инструменты обеспечения качества, такие как картографирование потока создания ценности, диаграммы PICK и 5 Whys, чтобы увеличить поток продукции и удовлетворить требования клиентов к упаковке. В результате сверхурочные работы сократились на 30%, производительность увеличилась на 5%, точность доставки достигла 100%, а удовлетворенность клиентов повысилась, что привело к дополнительному бизнесу.Оптимизация процесса регистрации дает большие результаты для руководителя сферы здравоохранения (PDF) Компания Kaiser Permanente Colorado использовала Lean Six Sigma для оценки и улучшения процессов регистрации в Medicaid. Трехмесячный проект привел к увеличению числа участников Medicaid на 45% при одновременном увеличении доходов Medicaid более чем на 1 миллион долларов в год.
Отделение неотложной помощи рекомендует бережливое производство для улучшения процессов (PDF) Когда отделение неотложной помощи Медицинского центра Mercy использовало методы бережливого производства для улучшения процесса, показатели удовлетворенности пациентов поднялись с 30-го до 95-го процентиля.Картирование потока создания ценности помогло выявить и исключить шаги, не приносящие добавленной стоимости.
Корпорация Pall: профиль «совершенства процессов» (PDF) «Совершенство процессов» корпорации Pall объединяет бережливое производство, шесть сигм, показатели на панели инструментов и участие команды. Эта комбинация обеспечивает соответствие усилий по улучшению бизнес-императивов и способствует формированию культуры подотчетности.
Инструменты бережливого производства и шести сигм для быстрого сокращения циклических затрат (PDF) Финансовые лидеры должны взять на себя руководящие роли в развертывании «бережливого производства и шести сигм» для снижения затрат в медицинских организациях: начните сегодня с «Обхода менеджеров по качеству отходов».”
Lean and Six Sigma: A One-Two Punch (PDF) При использовании командного подхода «Шесть сигм / кайдзен» результаты достигаются быстрее благодаря участию сотрудников от цеха до высшего руководства.
Вы можете поделиться результатами бережливого производства? Пусть ASQ опубликует вашу историю успеха.
.Как внедрить бережливое производство
Осознание преимуществ бережливого производства — повышение эффективности, гибкости и способности реагировать на запросы клиентов — начинается с достижения согласованности во всей организации. Это первые шаги, которые мы рекомендуем любой организации, желающей масштабно внедрить экономичное производство.
Найди свою причину
Команды и организации обычно знают, что они делают. Они понимают, как они это делают — но почему? Это более сложный вопрос, но важный.
Как объяснил Саймон Синек в своем широко популярном выступлении на TED, понимание того, почему ваши действия являются самым важным фактором успеха практически во всем — дома, на работе и в жизни. Это также важно при принятии нового образа мышления, в основе которого лежит внедрение бережливого производства.
Если вы собираетесь убедить всех в своей команде, отделе или предприятии в том, что им необходимо изменить свое фундаментальное представление о работе, вам нужно будет объяснить, почему.
Почему в вашей организации происходит это изменение? Чтобы восстановить связь с вашими клиентами, стать более инновационным, достичь прибыльности, процветать в будущей мировой экономике? Выясните, что это за причина для вашей организации (и активно ее социализируйте), и у вас будет гораздо больше шансов успешно внедрить бережливое производство.
Признание и решение конфликтных потребностей
За годы исследований, посвященных изучению экономичных производственных организаций (а также бережливых предприятий в других отраслях), Уомак и Джонс сформулировали, что для того, чтобы практиковать бережливое производство на уровне предприятия, организации должны признать и удовлетворить три потребности:
- Потребности отдельных лиц: Отдельные лица должны иметь возможность сохранять свою работу и получать от нее удовольствие
- Потребности в функциях: Организации должны быть организованы по функциям для сохранения и роста организационных знаний; но по-настоящему гибким организациям нужны люди, которые объединяются в межфункциональные команды
- Потребности компаний: компании должны иметь возможность рассчитывать затраты и анализировать выгоды по видам деятельности, и, следовательно, ценить контроль над гибкостью / экономичностью
В традиционных организациях , практически невозможно удовлетворить все три из этих потребностей и поддерживать высокий уровень гибкости — конфликты между тремя потребностями неизбежно негативно сказываются на способности организации быть экономичной.
К счастью, по мере того, как все больше компаний справлялись с этими проблемами, появлялись новые решения, которые позволяют предприятиям достичь благоприятного баланса между «индивидуальными возможностями, функциональной мощью и благополучием компаний-членов», — говорят авторы. Бережливое управление портфелем относится к применению бережливого мышления для управления портфелями предприятий, программ и продуктов, чтобы помочь организациям удовлетворить все три потребности.
Найдите чемпиона (или станьте им)
В зависимости от корпоративной культуры вашей организации переход на бережливое производство может быть смелым шагом.Это заставит всех в организации сопротивляться, ставить под сомнение и больше говорить: «Нет». Это может потребовать принятия сложных решений в интересах сокращения отходов. Заметный и активный поборник бережливого производства — тот, кто будет праздновать победы, способствовать обсуждениям и вдохновлять других на дальнейшее развитие — может иметь решающее значение для преодоления проблем, связанных с преобразованием культурных изменений.
Если ваша организация переходит на бережливое производство сверху вниз, то вы, вероятно, получите поддержку своего нового, постоянно улучшающегося поведения.Но если вы внедряете бережливое производство в рамках инициативы на низовом уровне, вам понадобится помощь.
Если ваш поборник бережливого производства — это кто-то, уже занимающий руководящую позицию в организации, он может многое сделать, чтобы поддержать вашу инициативу бережливого производства и повысить ее шансы «застрять».
Фактически, из более чем 3000 опрошенных практиков бережливого производства мы обнаружили, что самые эффективные команды бережливого производства имели руководителя в 69% случаев.
Облегчите работу своего руководителя, информируя его: регулярно делитесь своими знаниями, используйте данные для демонстрации роста, публикуйте интересные статьи о бережливом производстве, приглашайте их участвовать в стендапах и ретроспективах.Если вы поддерживаете команду, примите участие и узнайте как можно больше о принципах бережливого производства, чтобы вы могли действительно практиковать бережливое лидерство.
Овладейте основами
Хотя концепции, лежащие в основе бережливого производства, просты, их может быть сложно реализовать в нашей сложной, постоянно меняющейся рабочей среде. Чтобы научиться думать, реагировать и действовать бережливым образом, вам необходимо переобучить свой мозг — и поначалу метод бережливого производства может показаться нелогичным.
Укрепите свои худые мышцы, читая книги по бережливому производству, чтобы узнать теорию и принципы.Узнайте об инструментах и методах бережливого производства и потренируйтесь применять их в своей работе. Стимулируйте бережливое обучение в своих командах, организуя «обед и учись» и создавая форумы, где люди могут делиться своим опытом, задавать вопросы и учиться вместе.
Многие организации добиваются успеха в привлечении внешних инструкторов по бережливому производству для запуска своих внедрений бережливого производства. Коучи по бережливому производству могут проводить семинары, отвечать на вопросы, делиться ресурсами и направлять ваши команды к устойчивому успеху с внедрением бережливого производства.
Составьте карту вашего потока создания ценности
Когда вы освоитесь с принципами и практиками бережливого производства, приступайте к составлению карты потока создания ценности.
Цель упражнения по картированию потока создания ценности — помочь вам понять, как ценность проходит через вашу команду и вашу организацию.
Выполнение упражнения предоставит множество возможностей для важных, проясняющих разговоров, которые помогут вам начать позитивные изменения.
Используйте Канбан, чтобы воплотить в жизнь свой поток создания ценности
.Бережливое производство: основы и результаты
07.12.2017 Концепция бережливого производства основана на идеях системы производства автомобилей Toyota.
Ключевые принципы бережливого производства — снижение всех затрат, оптимизация производства; вовлечение сотрудников в процесс повышения эффективности предприятия.
Фактически внедрение бережливого производства может повысить производительность труда до 400% в течение первого года.Использование даже одного из его принципов позволяет повысить эффективность работы предприятия на 30-50%.
Как начать внедрение бережливого производства?
В первую очередь необходимо проанализировать текущую ситуацию на предприятии и подготовить инструменты для дальнейшего мониторинга. Например, внедрить систему для персонала и оборудования — для мониторинга всех действий сотрудников и передвижения транспорта, оценки временных затрат на различные операции и выявления слабых мест. Такой анализ помогает определить:
- Неэффективная организация рабочего места, например, необходимость постоянно перемещаться между разным оборудованием или шкафами для хранения инструментов.
После внедрения системы мониторинга RealTrac на предприятии было установлено, что около 15% рабочего времени сотрудники тратят на то, чтобы добраться до общего кабинета за нужным инструментом и вернуться на место. По этим результатам было принято решение выделить каждому сотруднику свое место под инструмент — это привело к увеличению производительности труда на 15%. - Необоснованное перемещение товаров или материалов, например, неэффективная планировка магазинов и участков.
Используя систему RealTrac для мониторинга производительности погрузчиков и перемещения производственных деталей, было выявлено, что каждый элемент дважды попадает на сварочную станцию. Между двумя процессами на участке сварки деталь была отправлена на участок обработки поверхности, и на всех этапах был простой из-за ожидания подходящего погрузчика. Во время этой доработки сварочный пост располагался рядом с местом обработки — это позволяло экономить более 400 минут в месяц. - Неиспользованные свойства товара, например, дорогая упаковка товара, дополнительные функции, чрезмерно сложный дизайн
На основании результатов исследования рынка компания-производитель автобусов выяснила, что потребители не обращают особого внимания на качество окраски.И по этим результатам процесс окрашивания невидимых поверхностей был значительно упрощен, что позволило снизить ежемесячные затраты на несколько сотен тысяч рублей. - Простой производственного оборудования или персонала, из-за ожидания заказов на завершение предыдущей операции, поломки оборудования и т. Д.
Система мониторинга RealTrac позволяет отслеживать простои оборудования или персонала. Следовательно, в вышеупомянутом автомобильном производстве такие простои были из-за частых простоев оборудования.Проблема была устранена за счет содержания СТО в цехе — в результате время простоя персонала и оборудования сократилось на 26 человеко-часов в месяц. - Перепроизводство — когда выпуск превышает потребительский спрос.
По результатам маркетинговых исследований, предприятие приняло решение временно прекратить выпуск излишков продукции. Сосредоточив внимание на выпуске сезонных товаров, пользующихся спросом сейчас, прибыль компании по итогам квартала выросла на десятки миллионов рублей. - Дополнительные запасы материалов и сырья.
Учитывая стоимость дополнительно арендуемых складских площадей, а также тот факт, что длительное хранение на складе влияет на свойства материалов, компания решила поставлять запчасти ежедневно в количестве, определенном производственным планом. Это позволило снизить затраты на хранение и транспортировку комплектующих к месту проведения работ. - Причина дефектов в работе, приводящая к производству бракованной продукции.
В связи с высоким процентом бракованной продукции на предприятии руководству приходилось контролировать работу всего производства с помощью продукта Интернет вещей RealTrac. Поскольку система непрерывно собирала все данные с оборудования, в случае обнаружения неисправностей производственный процесс останавливался, и система отправляла уведомление. Постепенно работа оборудования была полностью отлажена, а количество бракованной продукции сократилось более чем на 80%.
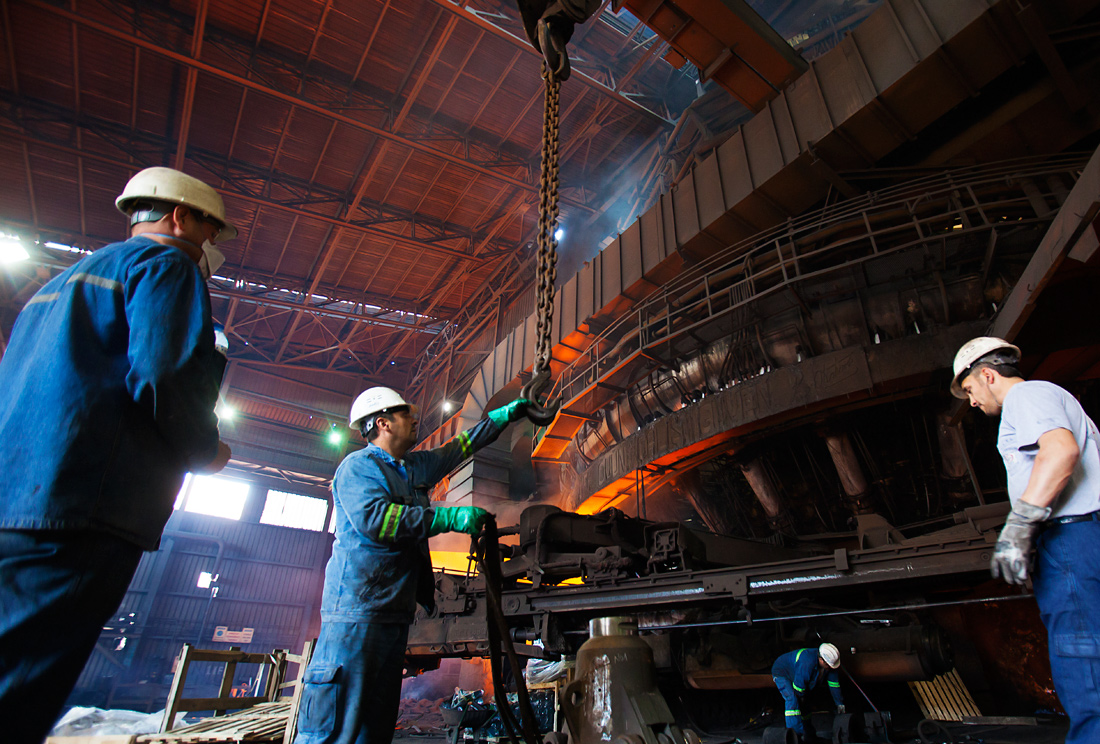
Увеличение производительности без увеличения производственных мощностей.
Шаг 1. Создание наглядной схемы изделия. Необходимо отображать: каждый этап информационных и материальных потоков, длительность этапов, время, необходимое для перехода между ними. На этом этапе можно внести некоторые изменения для оптимизации процесса.
Шаг 2. Определение точек защемления .Это может быть неэффективное использование персонала и оборудования, неоптимальное размещение оборудования, стандартные производственные ошибки, неиспользуемые единицы на производственных площадях.
Шаг 3. Визуализация бизнес-процессов. На этом этапе можно обозначить границы объектов на полу, выделить наиболее опасное оборудование, указать места хранения инструментов, установить стенды с описанием алгоритмов всех технологических операций, демонстрацией изображений бракованной продукции и другими инструкциями.
Шаг 4. Моделируя процессы, учитываем снижение затрат при транспортировке, переезде и ожидании. На этом этапе вы можете протестировать разные алгоритмы, сравнить производительность на практике, оценить эффективность различных способов оптимизации производства.
Прохождение этих этапов позволило компании-производителю конфет:
сократить количество сотрудников на производственной линии с 15 до 11 человек
увеличить производство с 6000 до 9000 комплектов кондитерских изделий
увеличить производительность предприятия на 35-37% без запуска дополнительных линий
Используя тот же алгоритм, крупный распределительный центр улучшил свои складские площади.В рамках внедрения бережливого производства на складе компании были установлены указатели номеров эстакад, а также нанесены схемы движения по территории.
Дополнительно реконструированы складские площади. В результате водители меньше времени проводили на территории центра, а благодаря перепланировке удалось уменьшить площадь склада более чем на 30%.
Бережливые инновации. Как это работает на практике?
Один из крупнейших логистических центров России реализовал концепцию бережливого производства.Ключевой целью было ускорить формирование пакетов заказов, чтобы снизить риски повторной сортировки и отказа от предоставления.
Руководство предприятия внедрило описанный выше алгоритм, а также внимательно изучило улучшающие предложения сотрудников и результаты опросов клиентов.
В результате были применены следующие решения:
Технология Pick-to-Light . В процессе комплектации заказа над ячейкой с нужными товарами загорается световой сигнал.Оператор нажимает кнопку выключения света, подтверждая, что товар упакован.
Распределение товаров по зонам . В зависимости от популярности товара, он попадает в одну из трех зон, быстрая — 20% товаров, по которым нужно выполнить 80% заказов, всего 30% товаров, которые нужно положить в каждую десятую. заказ, реже — с менее популярными товарами.
Th е принцип «под рукой».» Самые продаваемые товары расположены на расстоянии вытянутой руки, и даже чтобы взять товары из верхней ячейки, достаточно пройтись по ней.
Визуализация. В зоне сбора заказов пол обозначен и есть другие дополнительные знаки, интуитивно понятные даже для новичков. Большинство паспортных табличек при необходимости можно переместить в другую зону для перераспределения потоков или персонала.
Технологический процесс упаковки отходов. Вся использованная упаковка (гофрокартон) автоматически доставляется в зону прессования. Это сокращает время, затрачиваемое персоналом на упаковку, и снижает уровень загрязнения воздуха. Прессованный картон продается партнерам для дальнейшей обработки, что также приносит дополнительный доход.
Весовой контроль. Заказы взвешиваются, и результат сравнивается с прогнозируемой ставкой, которая определяется как сумма веса каждой позиции.Если вес не совпадает, заказ отправляется на дополнительную проверку.
Напольное покрытие специальное. Так как сотрудники склада весь день находятся на ногах, на полу установлено специальное ортопедическое покрытие, которое снижает нагрузку на ноги и позвоночник, а также снижает риск получения травм из-за противоскользящей поверхности.
Понятные данные по производительности труда. Скорость комплектования каждой линии отображается на мониторе в реальном времени.Это создает конкурентный эффект и делает систему KPI более прозрачной для сотрудников. Кроме того, руководство может оценить производительность каждого коллектора и выявить слабые места в линии.
Вовлечение сотрудников в процесс оптимизации . Сотрудников поощряют выдвигать идеи о том, как постоянно улучшать производительность; их вознаграждают даже за идеи, которые не будут реализованы.
Благодаря внедрению вышеперечисленных решений в логистическом центре снизилась ротация персонала.Повышена эргономика и безопасность эксплуатации; уменьшено количество жалоб от клиентов по поводу неправильного оформления заказа. В течение шести месяцев после внедрения бережливого производства продуктивность комплексов заказов увеличилась на 20%.
Этот и многие другие примеры подтверждают: бережливое производство действительно повышает эффективность предприятия. В конечном итоге, важно привлекать сотрудников и высокие технологии, анализировать каждый бизнес-процесс в компании, заботиться о клиентах и подрядчиках и быть готовым к масштабным позитивным изменениям.
.