Технология гранулирования комбикормов
Главная > Кормопроизводство > Технология гранулирования комбикормов6 ноября 2018 просмотры
Гранулирование кормов — это процесс агломерации, то есть объединения мелких частиц в более крупные частицы, под действием механических процессов увлажнения, нагрева и давления.
Для чего гранулировать комбикорм
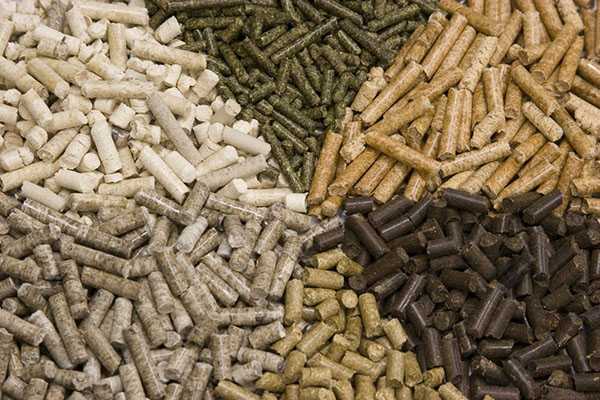
Для грануляции есть три основные причины, которые важно хорошо осознать, потому что именно они должны побуждать производителей и потребителей кормов к осуществлению этой недешевой операции:
- Улучшение эффективности корма
- Происходит желатинизация и разрыв длинных молекул составляющих корма, что улучшает усвоение смесей животными.
- Исчезает расслоение составляющих корма, поэтому животные потребляют однородный сбалансированный корм все время.
- Уменьшаются затраты на корма, потому что животные (особенно птица) не могут выбирать любимые составляющие и выбрасывать из кормушки нелюбимые.
- Улучшение механических характеристик корма
- Увеличивается удельный вес, что положительно влияет на эффективность перевозок и емкостей для хранения.
- Улучшаются характеристики текучести.
- Улучшается гигиена корма, снижается количество микробов.
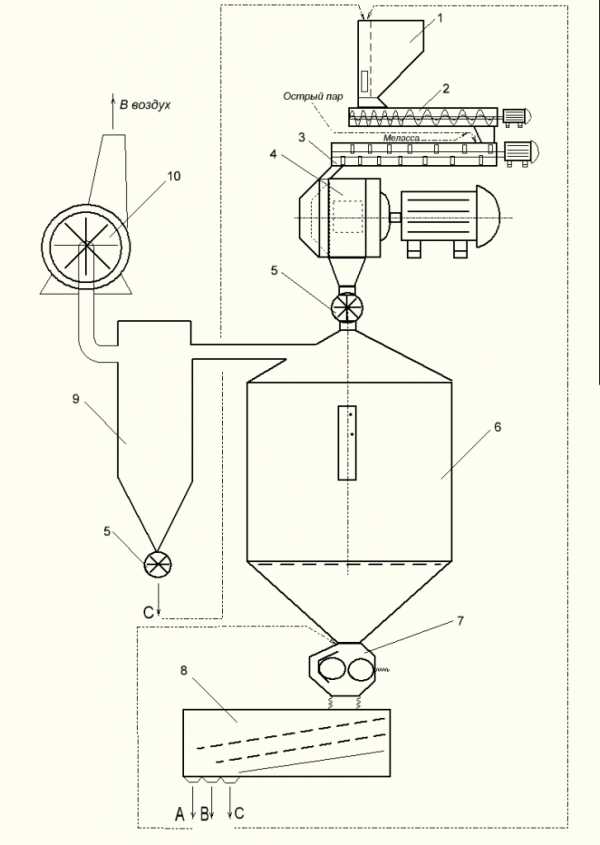
Рис.1 Принципиальная схема линии грануляции
Где 1 – специальный бункер; 2 — шнековый дозатор; 3 — кондиционер; 4 – гранулятор; 5 – шлюзовой затвор; 6 – охладитель; 7 – вальцы; 8 – просеиватель; 9 – циклон; 10 – вентилятор.
Работает линия следующим образом. Рассыпной корм из специального бункера отбирается дозирующим шнеком для подачи в кондиционер. Обороты шнека переменные для регулирования необходимой подачи. Так же должен быть переменным шаг навивки шнека, чтобы «растягивать» продукт.
В лопастном кондиционере продукт насыщается острым паром (с возможным добавлением мелассы). Это позволяет его разогреть до 70-80°С, увлажнить и размягчить. При прохождении через отверстия гранулятора температура массы возрастает еще на 5-15°С.
Шлюзовой затвор отсекает полость гранулятора от охладителя. В охладителе через слой гранул протягивается наружный воздух. Здесь гранула затвердевает, подсушивается и охлаждается почти до температуры окружающей среды. Далее на вальцах гранулу можно измельчить в крупку, или, направив по байпасному (обводному) каналу, подать на просеиватель.
Отобранная пылевидная фракция вместе с пылью из циклона возвращаются обратно на грануляцию через отдельный отсек специального бункера (фракция С). Крупная фракция с верхнего сита (фракция А) может направляться на повторное измельчение на вальцах.
Как видим, линия сложная. В ней к каждой машине предъявляются особые требования. Именно поэтому операторы, которые на ней работают, должны иметь основательные знания всех процессов, которые происходят, и хорошо представлять, какое регулирование на какие характеристики влияет. К сожалению, сейчас, по моим наблюдениям, не более чем один из пяти операторов гранулятора соответствует квалификационным требованиям. Это означает, что администрация предприятия не понимает значения обучения своего персонала и теряет выгоду там, где могла бы ее иметь.
Обзор отдельных машин технологии гранулирования
Специальный бункер на линии гранулирования
К бункеру (рис.2.) предъявляются особые требования, поскольку там находится трудно-текучая измельченная масса.
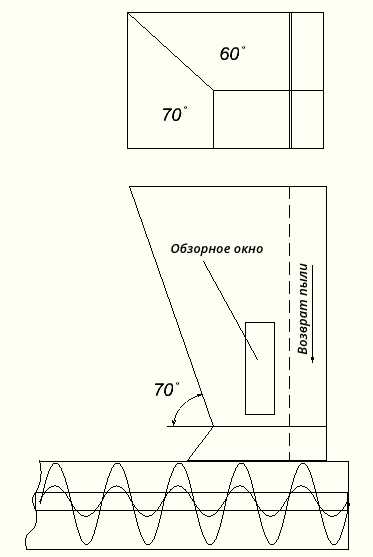
Рис 2. Специальный бункер
Стенки бункера должны быть крутыми, желательно с разными углами наклона, что приводит к различным скоростям движения вдоль каждой стенки и предотвращает образование сводов.
Желательно, чтобы объем бункера мог обеспечивать не менее 2-х часов работы гранулятора.
Нижнее выходное отверстие должно быть с расширением к низу.
В бункере должен быть вертикальный отсек для сброса пылевидной фракции.
Также, в основной части бункера рекомендуется иметь наблюдательное окно лицом к оператору. По этому окну оператор ориентируется об окончании порции одного рецепта в бункере и своевременно подает сигнал о возможности производства другого рецепта для уменьшения технологических простоев.
Желательно, чтобы на стенках бункера были установлены вибраторы. Причем, лучше, чтобы включение вибраторов осуществлялось автоматически и нециклично во время работы дозирующего шнека.
Между бункером и дозирующим шнеком желательно устанавливать шибер с квадратным отверстием (см. Лекцию 3 Дозирование).
Дозирующий шнек на линии гранулирования
Работа и конструкция дозирующего шнека достаточно изложены в описании работы всей линии. Эта машина достаточно надежная и особых хлопот не доставляет.
Хотя, при производстве престартеров на матрице с тоненькими отверстиями 2 … 2,5 мм можно столкнуться с проблемой необходимости очень малых подач. В этом случае частотные регуляторы, которые управляют оборотами дозирующего шнека, не могут достаточно обеспечить крутящий момент при малых оборотах.
В таких случаях мы достигали стабильных малых подач с помощью шибера с квадратными отверстиями, который описан выше.
Также иногда нам приходилось модернизировать дозирующий шнек и оснащать его форсунками для распыления воды в жаркий летний период, когда сырье было пересушено и времени нахождения продукта в кондиционере было недостаточно. Такой прием существенно повышал прочность гранул и снижал энергозатраты на основном двигателе гранулятора на 15 … 20%.
Кондиционер на линии гранулирования
Кондиционер является чрезвычайно важной машиной, которая требует периодического контроля. В принципе, это простой вал с лопатками, которые могут устанавливаться под разным углом, который вращается с постоянной скоростью.
Теоретически, он только транспортирует сыпучий продукт и пар с одного конца трубы в другой конец и перемешивает их между собой. Однако, задача стоит таким образом, чтобы время нахождения продукта в кондиционере было как можно большим, чтобы влага успела впитаться в частицы сухой зерновой массы. В связи с этим возникает ограничение: с одной стороны, производительность кондиционера не должна быть меньше, чем производительность дозирующего шнека; с другой стороны, она должна быть как можно меньше.
Очень хорошо, если продукт находится в кондиционере до 40 секунд, но в большинстве случаев это 20 секунд и меньше. Чтобы этого достичь, часто приходится часть лопаток поворачивать в обратную сторону. Только эти лопатки не должны быть напротив загрузочного окна, иначе произойдет забивание продукта в дозирующем шнеке.
Чтобы увеличить время кондиционирования некоторые производители увеличивают длину кондиционера, или ставят два вала параллельно.
Так или иначе, у кого есть грануляционная линия, я советую посвятить время изучению этого вопроса и настройке лопаток на максимальное время кондиционирования. В моей практике даже были случаи, когда приходилось заменять электродвигатель и привод, установленный заводом-изготовителем, чтобы достичь желаемого результата. Но оно того стоило!
Грануляторы
Грануляторы бывают двух типов: с плоской и цилиндрической матрицей. Они могут быть маленькими, с мощностью около 15 кВт и огромными — до 600 кВт. Диаметр отверстий матрицы 2-19 мм. Толщина матрицы от 3 до 15 см. Грануляторы используют не только для грануляции кормов, а также и для грануляции соломы, жома, древесных опилок, животного помета и т.д..
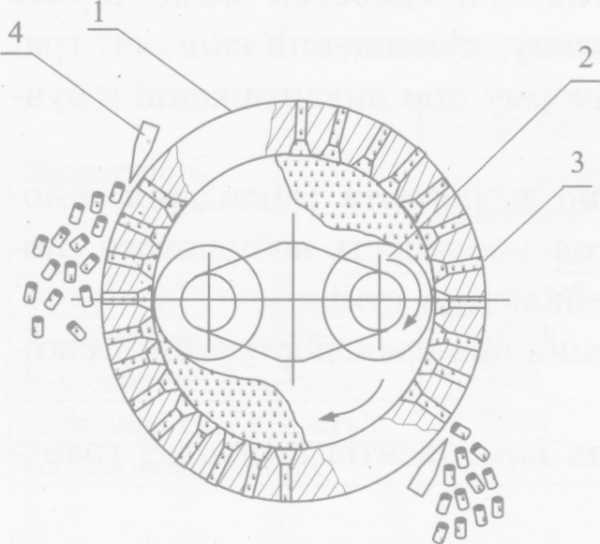
Рис.3 Гранулирование цилиндрической матрицей
1 — матрица; 2 — прессующий ролик; 3 — фильеры; 4 — нож
Процесс гранулирования заключается в сжатии рассыпного комбикорма в клиновом зазоре между прессующими роликами и внутренней поверхностью матрицы до состояния, когда он под действием влаги, тепла и давления приобретает термопластичные свойства.
На этом этапе происходит предварительное сжатие рассыпного комбикорма. В дальнейшем, по мере роста давления растут упругие и пластические деформации, возникают значительные усилия расклинивания.
Когда напряжение сжатия превзойдет силы сопротивления сжатого комбикорма, он продавливается через фильеры (отверстия) матрицы 1, приобретая форму гранул, диаметр которых близок к диаметру фильеры матрицы. Длина гранул определяется положением ножа 4. Как правило, длина гранул не должна превышать полтора диаметра.
Работа ролика в грануляторе
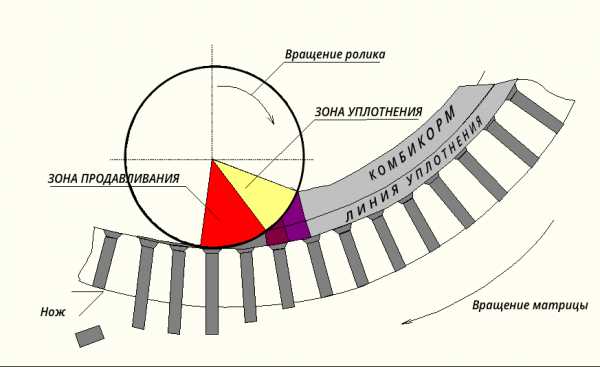
Рис.4 Работа ролика
Ролики сильно изнашиваются, так как имеют меньший диаметр и чаще вступают в работу, а потому должны иметь очень прочную и твердую поверхность, которая предотвращает скольжение.
Чем тоньше слой продукта, тем проще ролику на него накатиться и продавить через отверстие. Чем толще слой продукта, тем больше оказывается горизонтальная составляющая реакции ролика, что вызывает скольжение. В таком случае продукт накапливается перед роликом и возникает сильная вибрация, которая может повредить весь узел.
Оператор гранулятора должен немедленно сбросить продукт через предохранительный клапан, перекрыть подачу пара и стабилизировать работу гранулятора, уменьшив подачу дозирующим шнеком.
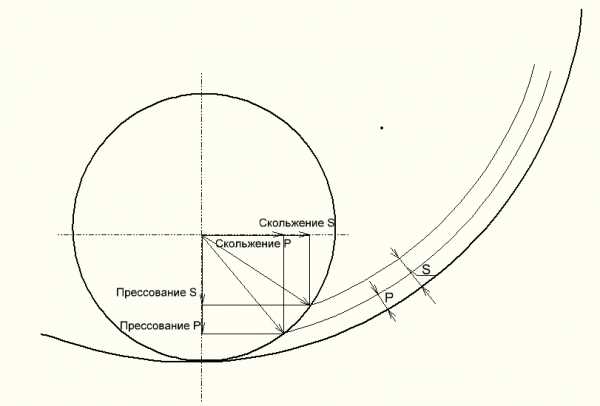
Рис.5 Силы прессования
Существует три типа поверхности роликов:
- Наваренная прочным карбидным электродом (шершавая).
- С канавками по образующей рабочей поверхности (похожа на широкую шестерню).
- С засверленными углублениями на рабочей поверхности (перфорированная).
Тип поверхности ролика выбирается методом индивидуального подбора. Чаще всего встречается 2 тип.
Важно! Следить за равномерным износом боковой поверхности ролика. Этот износ полностью зависит от угла наклона забрасывающих лопаток на конусе матрицы. Это очень тонкая настройка. Но, если вы не осуществите ее правильно, то и ролики и матрица будут выходить из строя в два раза быстрее, чем ожидается. А качество гранул также будет неудовлетворительным.
Иногда встречаются случаи слишком частого выхода из строя подшипников на роликах. В этом случае стоит проверить систему смазки и температурные характеристики применяемого масла. А случается, что режимы работы гранулятора настолько тяжелые, что приходится заменять и тип подшипника.
Состояние рабочей поверхности матрицы
Также крайне важно следить за состоянием рабочей поверхности матрицы. При сильном ее сносе достичь качественной гранулы не удастся.
Предлагаю внимательно рассмотреть и понять конструктивные особенности отверстия матрицы, которые изображены на рис.6. Понятно, что при износе поверхности существенно уменьшается компрессионное соотношение D/d.
Также при частой реставрации со шлифовкой рабочей поверхности, уменьшается общая и эффективная толщина матрицы. А вместе с ней ухудшается другой важный показатель — рабочее соотношение h/d, которое задает время нахождения материала в отверстии и формирования прочности гранулы.

Рис.6 Отверстие матрицы в разрезе
Разрез отверстия матрицы: В — полная толщина; h — эффективная толщина; t — глубина выхода; d — диаметр гранулы;
D — входной диаметр; Ф — входной угол; h/d — рабочее соотношение; D / d — компрессионное соотношение.
Охладители на линии гранулирования
Горячая гранула через шлюзовой затвор попадает в охладитель.
В принципе, любая сушилка может выполнять функции охладителя. Но в нашей промышленности, как правило, используются охладители четырех типов: вертикальные — охлаждающие колонки и противоточные охладители; и горизонтальные — цепные и барабанные.
О всех этих машинах, их преимуществах и недостатках, стоит поговорить отдельно. Сейчас же мы кратко рассмотрим некоторые особенности самого популярного в последнее время противоточного охладителя.
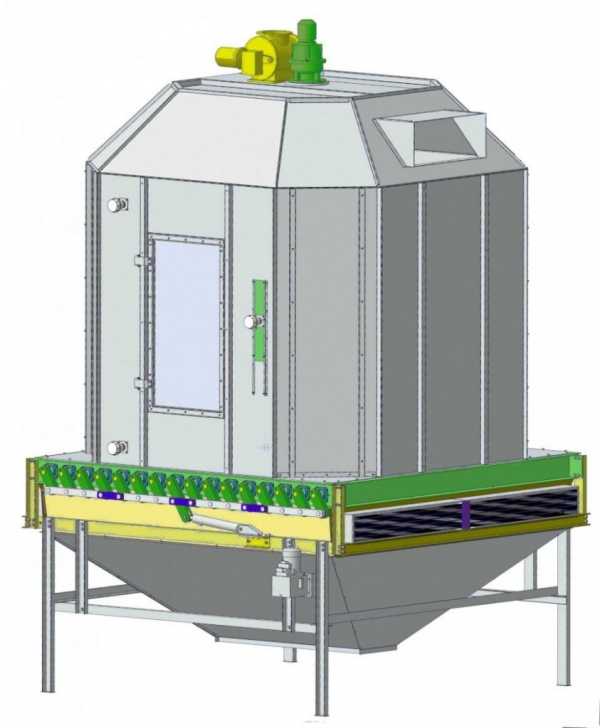
Рис.7 Противоточный охладитель
Данный тип охладителя приобрел популярность из-за высокой производительности, простоты конструкции и надежности. В этом охладителе слой гранул выполняет роль воздушного фильтра, через который продувается наружный воздух. Именно поэтому, надо понимать, что гранулу не удастся охладить ниже температуры окружающего воздуха tвнеш.
Производители оборудования гарантируют, что достаточной температурой гранул является tвнеш + 5°С. То есть, если в помещении, где расположен охладитель + 10°С, приемлемой температурой гранул является 15°С. Если в этом помещении 32°С, то приемлемой температурой гранул является 37°С. Это обычные законы физики, с которыми надо смириться. Производители оборудования честны перед пользователями (эксплуатационщиками) этого оборудования…
Но производителей кормов это приводит к головной боли, когда ночная температура падает на 15-20 градусов, а в бункерах готовой продукции находятся теплые комбикорма, произведенные днем. И они начинают отсыревать.
В нашей зоне мы встречаемся с такими проблемами во второй половине лета и во время морозных ночей зимой. Есть несколько технических и организационных мер по борьбе с этим явлением.
Вот некоторые из них:
- обеспечить качественное вентилирование бункеров готовой продукции;
- производить корма, которые будут храниться в накопительных бункерах, ночью.
Другой аспект, на который нужно обратить внимание при эксплуатации противоточных охладителей — это разная температура гранул на выходе. Дело в том, что вытяжной патрубок конструктивно направлен в сторону и смещен относительно центра.
Воздух «ленивый» и ищет пути наименьшего сопротивления. Если отсутствует верхний шлюзовой затвор (я встречал такие случаи), основная масса воздуха будет извлекаться из гранулятора вхолостую.
В стандартном же случае основная масса воздуха протягивается через тонкий слой гранул со стороны воздушного патрубка, а не по диагонали. Таким образом, с противоположной стороны гранула будет теплее, и это может вызвать проблемы при хранении. Чтобы уравновесить потоки воздуха с обеих сторон мы прикрывали отверстия для забора воздуха со стороны вытяжного патрубка, чтобы заставить больше воздуха забирать с противоположной стороны.
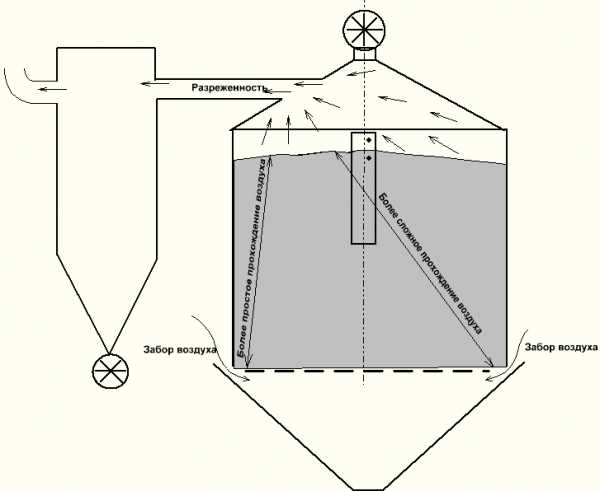
Рис.8. Движение воздуха в охладителе
Вальцы линии гранулирования
Строение вальцев показано на рис.9. С их регулировкой и восстановлением боковых поверхностей роликов постоянно приходится иметь дело.
Поверхностный слой вальцев цементирован на глубину до 10 мм и имеет высокую твердость и износостойкость. Поэтому, при их износе есть возможность до двух (иногда трех) раз реставрировать их путем шлифования цилиндрической поверхности и нарезки зубцов.
Следует помнить, что после каждой обработки боковая площадь уменьшается, вальцы вступают в работу чаще, а потому срок работы реставрированных вальцов уменьшается. Как правило, время реставрации занимает время не менее одной недели, а поэтому на предприятиях должны быть как минимум два комплекта роликов.
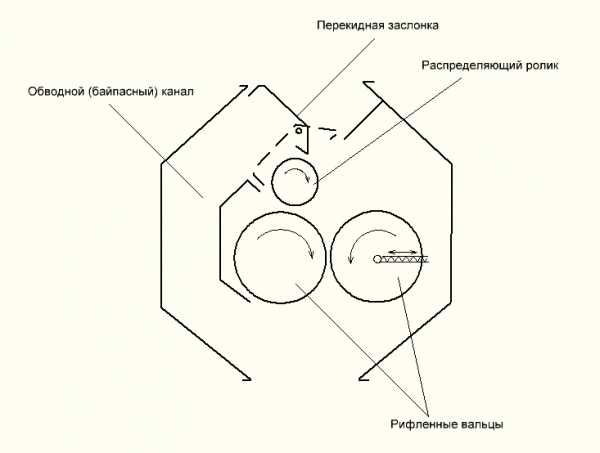
Рис.9 Элементы конструкции вальцов
Просеиватели на линии гранулирования
В нашей промышленности используют возвратно-поступательные или дисковые просеиватели. Лучше всего, когда просеиватели имеют два сита. Хотя, я встречал и просеиватели только с одним ситом, предназначенным для отбора пыли.
Если сравнивать работу возвратно-поступательных и дисковых просеивателей, я предпочитаю вторые: меньше шума, меньше травмируют гранулу, меньшая высота машины, дольше служит сито.
К их недостаткам можно отнести большую цену всей машины и ее сменной части — просеивающего диска.
Хотя, последнюю проблему мы успешно преодолевали, изготавливая диски собственными силами — раскроем листа и сваркой полуавтоматическим сварочным аппаратом. В любом случае, размеры отверстий сит нужно подбирать индивидуально.
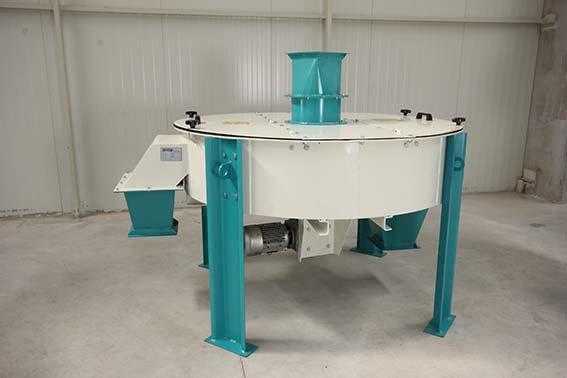
Рис.10 Внешний вид дискового просеивателя гранул
Вот мы рассмотрели почти все машины линии грануляции. Оставили без внимания только вентиляцию и систему обеспечения паром. Некоторые мелкие предприятия работают без пара, только добавляют простую или горячую воду. В таких случаях качество грануляции значительно ухудшается.
Система обеспечения паром — это отдельная сложная тема, которая включает водоподготовку, парообразование, капле-отделение, возврат конденсата и тому подобное. При введении в корма патоки, система усложняется еще больше, но прочность гранул и вкусовые качества кормов сильно улучшаются. И тот, кто имеет возможность вводить мелассу в корм, никогда об этом не пожалеет. Но, это темы других лекций, если наши уважаемые читатели проявят к ним интерес.
При всем разнообразии аспектов при работе линии грануляции есть два основных, которые чаще всего беспокоят производителей: это прочность гранул и желание повысить производительность.
Что влияет на качество и производительность гранулирования?
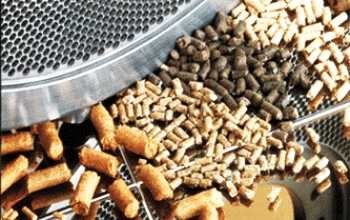
Как бы мы не настраивали машины, следует всегда помнить, что прочность гранулы больше зависит от рецептуры! И, если ваше предприятие стремится к успеху, ваш специалист по составлению рецептов должен в этом вопросе глубоко разобраться и руководствоваться не только критериям питательность/цена, но и дополнительными характеристиками смеси. Здесь я коротко о них напомню:
- Более 5% жиров в рецепте приводит к хрупкости гранул;
- Чем больше белка, тем лучше — гранула пластифицируется, становится прочной;
- Высокое содержание минеральной части цементирует гранулу. Гранулы для несушек, обычно достаточно прочные;
- Пшеница и отруби — гранула прочная;
- Высокое содержание кукурузы — приводит к хрупкости гранул;
- Введение мелассы склеивает частицы между собой, словно карамель. Очень положительно влияет на прочность и уменьшает образование пыли.
Но, когда у нас неожиданно возникают проблемы с качеством гранул, мы, как ни странно, не беремся за анализ рецептов. В первую очередь мы проверяем работу охладителя: не выходит ли из него теплая гранула. Если по какой-то причине (а чаще всего из-за осадка в воздушных трубах) из охладителя выходит не достаточно холодная гранула — будут проблемы и с ее хрупкостью. Другой негативный фактор — повышенная относительная влажность воздуха, что случается в период осенней непогоды.
Что влияет на производительность грануляции?
На производительность грануляции наибольшее влияние оказывает диаметр отверстий матрицы. При диаметре отверстий 5 мм производительность гранулятора больше в 5 раз, чем при диаметре 2,5 мм. Именно поэтому, выпуск гранул малых диаметров очень затратный. Из-за этого многие для производства пре-стартеров и стартеров производят гранулы на матрицах с отверстиями 4,5-5мм, а затем «колют» их на вальцах и просеивают крупку.
Как проверить прочность гранул?
Проверка прочности гранул производится на специальных приборах путем воздействия на навеску заданной массы лопаток, которые вращаются в замкнутом объеме с этими гранулами. После «травмирования» гранул в течение 1 минуты навеска просеивается на ситах 1,5 мм и определяется содержание фракции пыли. Чем меньше пыли, тем гранула прочнее.
Влажность сырья и гранул
В предыдущих лекциях мы несколько раз говорили о потерях массы сырья, например, при помоле, хранении или очистке. Грануляция же — одна из немногих операций при производстве комбикормов, где у нас есть возможность увеличить вес продукта с помощью добавления воды. Именно поэтому опытные производители уделяют этому аспекту очень серьезное внимание, ведь, в конце концов, здесь можно законно заработать (или не заработать) большие деньги. Посчитайте, во сколько на вашем предприятии оценивается дополнительный выход продукции, например, на 0,5%? Стоит ли за это побороться?
Но, чтобы этого достичь, нужно модернизировать линию и дополнительно научить операторов и, желательно, поощрить их премиальными. Дополнительное введение жидкости возможно и в дозаторе, и в кондиционере. Здесь важны все параметры: время экспозиции, предыдущая влажность смеси, дисперсность распыления воды, влажность мелассы, если она добавляется.
Производительность гранулятора и величина потребляемого основным двигателем тока также изменяются, как правило, в лучшую сторону. Однако, сам режим гранулирования становится менее стабильным, увеличивается вероятность пробуксовки.
В этом случае, если не обеспечить надежную автоматизацию отсечения подачи воды, то произойдет «заливка» зерновой массы водой и преобразование ее в тесто с последующей утилизацией. Каждому запуску этой системы в работу должен предшествовать предварительный расчет, основанный на начальной влажности измельченной массы и желаемой конечной влажности гранул. При этом надо учесть, что при охлаждении гранула также потеряет и влажность. Что тут говорить о необходимости более частого контроля влажности и температуры гранул на выходе из охладителя!
Существуют компании, которые поставляют специальное компьютеризированное оборудование для доувлажнения и контроля влажности гранул. У меня в этом также был опыт с известным европейским авторитетом. Однако, при всей его дороговизне и многократных приездах специалистов, система не заработала уверенно и от нее пришлось отказаться. А вот простые технические решения при заинтересованности операторов работали четко и приносили хороший результат.
Завершение
Ну вот, дорогие друзья, мы закончили наш короткий курс из пяти лекций по технологии производства кормов. Надеюсь, он был полезным для специалистов, профессионально занимающихся производством кормов. Возможно, он также был интересен некоторым потребителям кормов и пролил свет на нашу внутреннюю кухню? Возможно, он прибавит вашего уважения к тем, кто занимается этим непростым и кропотливым делом — производством пищи для ваших животных?
Я буду искренне благодарен получить ваши комментарии и пожелания. Понятно, что в таких рамках невозможно осветить все тонкости процесса, с которыми приходилось сталкиваться в течение 20 лет, с момента, когда я начал заниматься этим делом. Также, я не хотел слишком растягивать материал, чтобы не утомить вас и чтобы вы дочитали его до конца. Ну, а удалось ли мне это, судить вам.
Искренне ваш, Ярошенко Владимир
Автор курса: Владимир Владимирович Ярошенко — эксперт по промышленному производству комбикормов, многолетний консультант рубрики «Производство кормов» информационного портала soft-agro.com.
Скачать статью в формате .pdf
С нетерпением жду отзывы и комментарии. Большое Вам спасибо!
Нашли этот материал полезным? Поделитесь с коллегами в соцсетях или отправьте ссылку прямо на почту!
Хотите получить больше информации по технологиям производства комбикормов? Подписывайтесь на наш новый вводный (бесплатный) курс «Технология производства комбикормов»
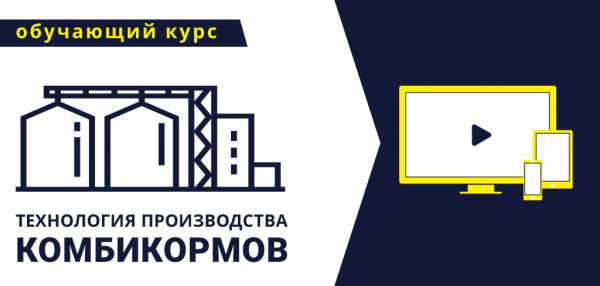
soft-agro.com
Производство комбикорма в домашних условиях
Производство комбикорма как бизнес привлекательный для малых инвестиций. Спрос –стабильный, потребитель покупает этот продукт десятками килограммами по розничной цене. Для запуска производства потребуется минимальный набор недорогого оборудования. А со временем можно быстро развиться до полноценной производственной полу-автоматизированной линии.
Комбикорм – это расходный продукт, в котором нуждаются фермы по производству мяса и молока и домашние хозяйства. Бизнес по производству гранулированного корма для животных имеет высокую доходность, активную оборачиваемость капитала. Чтобы товар пользовался спросом, обеспечим его качество. Этот показатель в сельском хозяйстве чрезвычайно важен.
Хорошо усваивается корм – повышается скорость роста скотины, улучшается соотношение килограмма питания на килограмм мяса. Чем выше качество комбинированных кормов, тем выше эффективность фермы. Но нужно решить еще одну задачу – снизить себестоимость продукта без потери качества. Покупать питание для сельскохозяйственных животных по высоким ценам будут единицы.
Что входит в состав комбикорма?
Основа гранулированного питания для животных – фуражное зерно. Оно в два раза дешевле классового зерна. Чтобы обогатить корм клетчаткой, добавим травяную муку. А луговую траву косить можно бесплатно.
Снизив расходы на основные компоненты комбикорма, бизнесмен может продавать его по выгодной для покупателя оптовой цене. Фермеры, как правило, приобретают корма мешками по 30 кг или даже тоннами. А повысить качество продукта позволяет бесплатная травяная мука.
Процент содержания клетчатки в разных кормах:
- 30-35% — для кроликов;
- 20-25% — для коров;
- 15-20% — для свиней;
- 10-15% — для кур.
В состав практически всех комбикормов входят злаки, богатые жирами, белками и углеводами и шрот, содержащий витамин Е. Такое питание бедно на другие полезные микроэлементы. Добавляя травяную, или витаминную, муку, предприниматель решает сразу несколько задач:
- в комбикорме много клетчатки, которая важна для нормального его усвоения;
- происходит травление организма животного, что необходимо для полноценного развития;
- корм содержит витамины, поддерживающие здоровье животного и обеспечивающие качество мяса.
Клетчатка, благодаря своей ячеистой структуре, впитывает жидкость и набухает. Объем пищи, попавшей в организм животного, увеличивается. В результате облегчается магистральное перемещение корма по кишечнику. Соответственно, улучшается усвояемость и повышается прирост.
В производство травяной муки берется обычное сено. Рекомендуется косить луговую траву, но можно люцерну и эспарцет. Скошенное сено сушится, измельчается и подается в гранулятор с другими компонентами.
Состав компонентов для животных и птиц
Компоненты и их соотношение зависят от типа питания сельскохозяйственного животного.
Кролики
Состав комбикорма для кроликов в домашних условиях:
- молотый ячмень – 25%;
- молотая кукуруза – 15%;
- пшеничные отруби – 5%;
- шрот подсолнечника – 20%;
- травяная мука – 35%.
Недостаток клетчатки в рационе кроликов приводит к вздутию живота и падежу поголовья. Этому сельскохозяйственному животному важно соблюдать систему травления пищи!
35% витаминной муки удовлетворяет суточную потребность животного в клетчатке. Приготовленный таким образом корм дает прирост мяса от 1 кг в месяц. Выживаемость кроликов повышается. Их все равно нужно кормить травой. Но к свежей траве, они слишком чувствительны: может попасться ядовитое растение, роса на травинках.
Свиньи
Комбикорм для свиней приготовленный своими руками, рецепт:
- молотая кукуруза – 20%;
- молотый ячмень – 20%
- молотая пшеница – 10%;
- шрот подсолнечника – 30%;
- травяная мука – 20%;
- поваренная соль – 0,2%.
В день свинья съедает 2,7-3 кг. 5,5 кг такого комбикорма дают 1 кг прироста чистого мяса. Для сравнения: обычного корма понадобится 7 кг.
Куры
Состав комбикорма для бройлеров в домашних условиях:
- молотая пшеница – 25%;
- молотый ячмень – 25%;
- молотая кукуруза – 17%;
- шрот подсолнечника – 15%;
- травяная мука – 15%;
- молотый ракушечник – 3%.
Шрота можно дать меньше, но не больше. В противном случае повышается жирность курицы, несушки плохо несут яйца.
В рецепт комбикорма для бройлеров, сделанный своими руками, следует обязательно включить ракушечник. Это источник кальция, необходимого для усиления костей и формирования скорлупы. Где взять? Подойдет строительный блок ракушник, сделанный из морского дна.
Коровы
Рецепт комбикорма для коров:
- молотый ячмень – 20%;
- молотая кукуруза – 15%;
- пшеничные отруби – 15%;
- шрот подсолнечника – 25%;
- травяная мука – 25%;
- поваренная соль – 0,5%.
Комбикорм в рационе коров – не единственный вид питания. Но в разведении животного он играет важную роль: повышается жирность молока, улучшается прирост чистого мяса.
Гранулированный комбикорм в домашних условиях
Для примера возьмем линию производства кормов из ячменя, кукурузы, шрота и травяной муки. В комплект линии входит только недорогое оборудование для производства комбикорма в домашних условиях:
Наименование оборудование | Технические характеристики | Вес и габариты | Стоимость |
Комбикормовый гранулятор | Мощность двигателя – 2,2 кВт, 1500 об./мин; производительность – 60-130 кг/час | Масса – 58 кг; размеры – 75 х 41 х 76 см | 400$ |
Дробилка зерновых культур | Мощность двигателя – 900 Вт; 4000 об./мин; производительность – 230 кг/час | Загрузка бункера – 20 кг | 280$ |
Маслопресс (для производства шрота) | Мощность – 2 кв./час; производительность – 5 л/час | Вес – 45 кг | 400$ |
Сушилка | 550$ | ||
Измельчитель для сена | Мощность двигателя – 4 кВт | Вес – 65 кг; размеры – 53,6 х 65,1 х 141,5 см | 500$ |
Мотокоса | Мощность – 1,7 кВт; 6000 об./мин | Масса – 8 кг, размер бака – 1,2 л | 50$ |
Таким образом, на начальном этапе понадобится 2190 долларов для обустройства производственной линии. Плюс ежемесячные расходы на аренду помещения, электроэнергию и сырье.
Мини завод по производству комбикормов работает по следующей схеме:
- Покос луговой травы или люцерны. Просушка сена на сушилке, измельчение травяной муки.
- Дробление зерновых, кукурузы, ячменя.
- Прессование фуражных семян подсолнечника через маслопресс (маслобойку). На выходе – шрот и техническое подсолнечное масло с фузом.
- Отстаивание технического масла. Фуз можно засыпать в мешок из лавсановой ткани и положить под пресс.
- Загрузка ингредиентов в гранулятор – получение готового продукта.
- Дозировка всех компонентов по рецептуре состава необходимого для конкретного вида с/х животных.
- Прессование гранулятором сыпучих кормов для формирования легкоусвояемых гранул.
Пропорции берем в зависимости от типа корма. Размер гранул можно изменить с помощью различных насадок.
Если средства на открытие собственного дела ограничены, можно некоторые компоненты на начальном этапе закупать. Впоследствии, когда появятся свободные средства, комплектуется полная линия.
businessideas.com.ua
Гранулирование комбикормов
Гранулированные комбикорма имеют, как правило, форму небольших цилиндриков диаметром от 2,4 до 20 мм, длина их обычно не превышает 1,5…2 диаметров. Размеры гранул зависят от их применения. Мелкие гранулы предназначены в основном для молодняка птиц (цыплят, утят и т. д.), гранулы размером около 5 мм используют для взрослой птицы, рыбы, крупные гранулы — для крупного рогатого скота, свиней, лошадей.
Каждая гранула представляет собой полный набор всех питательных веществ, заключенных в комбикорме, тогда как при кормлении рассыпным комбикормом птицы едят только то, что им нравится, оставляя часть комбикорма. Гранулированные комбикорма также важны для жвачных животных и свиней. Удобны гранулы для рыб, так как целая гранула долго может находиться в воде, сохраняя питательные вещества.
Некоторые исследователи считают, что благодаря высокой температуре и увлажнению при пропаривании и прессовании повышается питательность комбикорма вследствие декстринизации крахмала и частичной денатурации белков. В то же время имеются данные о частичном разрушении некоторых аминокислот, например метионина, частичном снижении количества биологически активных веществ. Однако результаты кормления гранулированными комбикормами птиц и животных говорят о том, что такие комбикорма не хуже, чем рассыпные. Многие исследования свидетельствуют о более высокой питательной ценности гранулированных комбикормов.
Гранулированные комбикорма имеют еще одно важное достоинство — повышенную объемную массу, хорошо транспортируются механическим и пневматическим транспортом без нарушения однородности, удобны для бестарных перевозок и полной механизации раздачи корма на фермах. Гранулированный комбикорм лучше хранится, в процессе гранулирования возможно частичное обеззараживание комбикорма.
На комбикормовых заводах применяют два способа производства гранулированных комбикормов — сухой и влажный. При первом способе сухие рассыпные комбикорма перед прессованием пропаривают, иногда добавляют в них жидкие связующие добавки (мелассу, гидрол, жир и т. д.). При влажном способе в комбикорм добавляют горячую воду (70…80°С) в количестве, обеспечивающем получение теста с влажностью 30…35 %, затем из теста формуют гранулы, сушат и охлаждают.
Гранулирование сухим способом. Для этого используют пресс с вращающейся кольцевой матрицей. Наиболее распространены установки ДГ производительностью до 10 т/ч и прессы ДГВ и ДГЕ, имеющие несколько большую производительность. В комплект установки входят пресс-гранулятор, охладительная колонка, измельчитель гранул.
Вначале комбикорм поступает через питатель-дозатор в смеситель. Питатель-дозатор представляет собой шнек, который приводится во вращение электродвигателем через редуктор и вариатор, позволяющий увеличить или уменьшить подачу комбикорма в десять раз.
В лопастном смесителе установлены форсунки для подачи горячей воды или какой-либо связующей жидкости, а также камеры для подачи пара. Подготовленный комбикорм поступает в прессующую часть гранулятора, представляющую собой вращающуюся кольцевую матрицу и два прессующих ролика (в некоторых конструкциях — три).
Продукт в прессующей части затягивается в клиновидный зазор между вращающейся матрицей и валком, приводимым во вращение материалом, (за счет трения). При перемещении продукта в клиновидном зазоре происходит прессование материала, что увеличивает его плотность. В момент, когда напряжение с
www.activestudy.info
Состав комбикорма для кроликов, свиней, кур и коров дает рентабельный бизнес
Интересная бизнес идея о производство гранулированного комбикорма с точки зрении качества и доходности. Кратко о концепции бизнеса. Состав гранулированного комбикорма для кроликов, свиней, кур и коров состоит из фуражного зерна, их состав содержит много клетчатки что одновременно улучшает качество комбикорма и повышает рентабельность бизнеса. Фуражное зерно в два раза дешевле стоит от стоимости классового зерна, а много клетчатки содержится в сене луговой травы, которую можно косить бесплатно. Оптовая стоимость гранулированного комбикорма на 10%-15% дороже стоимости классового зерна и на 110%-115% фуражного соответственно. Кроме того, в состав комбикорма должна обязательно входить клетчатка, которая содержится в травяной муке. Травяная мука одновременно снижает себестоимость гранулированного комбикорма и повышает его качество. Количество травяной муки, которая входит в состав комбикорма в процентном соотношении — до 35%. Таким образом, рентабельность доходности оборотной (грязной) прибыли приблизительно 150%. Бизнес обладает высокой скоростью реализации, комбикорм чаще всего покупают не килограммами, а мешками по 30кг, а то и тоннами. Все зависит от потребностей Ваших клиентов. Потребность в комбикормах очевидна, комбикорм это расходный продукт, который широко используется при производстве мясных и молочных продуктов, которые всегда имеют спрос. Усвояемость гранулированного комбикорма значительно выше, чем у обычных кормах. Это очень важный фактор при выращивании сельскохозяйственных животных на мясо, при высокой усвояемости повышается прирост в соотношении килограммов кормов на килограмм мяса. Плюс хорошая усвояемость кормов повышает скорость роста сельскохозяйственных животных.
Травяная мука, которая входит в состав комбикорма для кроликов, свиней, кур и коров играет важную роль
Процент содержания травяной муки в комбикорме по массе корма: для кроликов 30%-35%, для свиней 15%-20%, для кур 10%-15%, для коров 20%-25%. Травяная мука, которая обязательно должна входить в состав комбикорма содержит, играет очень важную роль. Ее еще называют витаминная мука. Дело в том, что основные компоненты комбикормов это злаковые культуры, которые имеют много жиров, белков, и углеводов, но бедны на витамины, еще шрот, который богатый на витамин Е немного улучшает ситуацию, но этого все равно очень мало. Таким образом, травяная мука дает не только большой процент содержания клетчатки такой важно при усвоении корма, системы травления и организма животного в целом, но и дополнительные витамины, которых нет в других компонентах. А витамины важны при разведении животных на мясо, от них зависит не только состояние здоровья животного, но и качество продукта, то есть мяса. Сама клетчатка имеет ячеистую структуру и свойство поглощать жидкость и набухать, увеличивая при этом объем пищи, который важен при магистральным перемещением по кишечнику и усвояемости соответственно. Объем пищи очень важен при усвояемости пищи он не должен быть низким иначе будут возникать различные заболевания. Травяную муку делают из обычного сена, желательно луговой травы, но можно косить и люцерну и эспарцет. После просушки сено измельчается и подается в гранулятор в месте с остальными компонентами, которые входят в состав в определенной дозировки в зависимости от типа комбикорма разных сельскохозяйственных животных. Ниже имеется перечень оборудования, которое входит в линию производства комбикормов. Там Вы увидите измельчитель сена, сушилка, и мото-коса вот и все что нужно на производство травяной муки.
Состав комбикорма для кроликов
При приготовлении комбикорма для кроликов необходим такой состав 25% ячмень молотый 15% кукуруза молота 5% отрубей пшеничных, 20% шрот подсолнечный (макуха) 35% травяной муки. Травяная мука играет очень важную роль и входит в состав приготовления комбикорма для кроликов. В рационе питания кроликов жизненно важно необходимый компонент это клетчатка. Если кролики будут недополучать должной дозы клетчатки в рацион питания у них нарушится система травления пищи и у них будут вздутые животики, после чего они начнут пропадать. Так устроенный их организм. Клетчатка играет роль в шарикообразных образованиях кала кролика. Она помогает связывать последы кролика в шарики. Данный состав комбикорма для кроликов улучшает усвояемость кормов, что в свою очередь дает хороший прирост мяса, который у кроликов самый высокий из всех сельскохозяйственных животных (кролика прирост уступает только курам). Но с этим комбикормам вы будете получать от 1кг и более прироста в месяц на каждого кролика. Состав комбикорма, в который входит 35% травяной муки позволяет дать кролику суточную норму клетчатки в помощь нормальной работы организма. Это позволяет исключить необходимость кормить кроликов свежей травой, что очень эффективно повышении выживаемости при разведении кроликов. Кролики очень чувствительны к свежей траве, например с росой или к ядовитым травам которые попадают вместе со свежей травой. Кролики сразу начитают дохнуть. А благодаря гранулированным комбикормам с 35% содержанием травяной муки их выживаемость возрастает в разы. Само обслуживание кроликов при кормлении значительно упрощается.
Состав комбикорма для свиней
При организации комбикорма для свиней необходимый такой состав: кукуруза молотая 20%, ячмень молотый 20%, пшеница молотая 10%, шрот подсолнечный 30%, мука травяная 20%, соль поваренная 0,2%. Для свиней клетчатка играет важную роль, и она должна обязательно быть включена в рацион питания. Свинья употребляет клетчатки меньше чем кролик, но приоритет тоже высокий. При выращивании свиней фермер должен обязательно давать состав комбикорма, который содержит много клетчатки, например травяную муку. Это помогает избежать множества болезней, улучшает прирост мяса за счет хорошего переваривания пищи, плюс свинья получает дополнительные витамины, которые не содержаться в злаковых кормах. Очень важную роль играет травяная мука в рационе кормления кормящих свиноматок, при таком рационе организм свиньи вырабатывает больше молока маленьким поросятам. Гранулированный комбикорм имеет лучшую усвояемость, что дает хороший прирост мяса. На 5,5 кг. Гранулированного комбикорма 1кг. Прироста мяса чистого выхода. Против обычного корма, у которого усвояемость значительно ниже. На 7 кг обычного корма 1кг мяса чистого выхода. У свиньи выход примерно 50%. То есть у 300кг. Свиньи 150 кг. Мяса чистого выхода.
Состав комбикорма для кур
Что бы приготовить правильный состав комбикорма для кур нам потребуется: пшеница молотая 25%, ячмень молотый 25%, 17% кукуруза молотая, шрот подсолнечный 15%, травяная мука 15%, ракушка молотая (можно из обычного ракушника) 3%. Для кур важно не переусердствовать с компонентом шрот подсолнечный. Если в состав комбикорма для кур превысить дозировку шрота у комбикорма подниматься жирность и куры будут плохо нести яйца. Такой компонент как ракушка найти не сложно. Достаточно измельчить один строительный блок ракушник. Эти строительные блоки делают из морского дна, его пилят на блоки. Для кур это очень полезный компонент в рационе, который обладает большим количеством кальция, что, способствует формированию скорлупы на куриные яйца. В ракушке содержаться полезные минералы. Травяная мука, которая входит в состав комбикорма для кур играет роль компонента с большим количеством клетчатки и дополнительных витаминов, которые не содержаться в обычных кормах. Такой состав комбикорма улучшает прирост куриного мяса, которое и так обладает самым высоким приростом против всех сельскохозяйственных животных. А также этот рецепт комбикорма даст здоровое поголовье птицы.
Состав комбикорма для коров
В состав комбикорма для коров входят такие компоненты: ячмень молотый 20%, отруби пшеничные 15%, кукуруза молотая 15%, шрот подсолнечный 25%, травяная мука 25%, соль поваренная 0,5%. Конечно в отличие от кроликов коров одним комбикормом не на кормишь, но он играет важную роль при разведении коров. В состав комбикорма входит довольно много клетчатки, что довольно очевидно и шрота подсолнечного, он придает небольшую жирность в рацион питания коров которые дают парное молоко. В молоке содержится большой процент жира. Корова получает еще клетчатку от дополнительных кормов, например силос, но исключить травяную муку из состава комбикорма нельзя, там она выполняет дополнительную функцию усвояемости других компонентов, которые входят в состав комбикорма. Прирост коров при питании обычными кормами приблизительно такой: на 15кг. корма 1 кг. мяса чистого выхода. Такой низкий прирост обусловлен разными факторами, например доение, процент выхода чистого мяса который составляет у коров 40% и другие. Но при кормлении коров гранулированным хорошо сбалансированным комбикормом с клетчаткой прирост значительно повышается за счет высокой усвояемости кормов.
Оборудование производства комбикорма для кроликов, свиней, кур и коров
Оборудование, которое требует технология производства гранулированного комбикорма. Реализация бизнеса. Примером возьмем такой состав комбикорма: ячмень, кукуруза, шрот подсолнечный, травяная мука. В организации полной лини производства необходимо такое оборудование:
| |
| |
| |
| |
| |
|
И того для стартапа бизнеса необходимо 4 700$ на оборудование. Еще нужно включить расходы на помещение, электроэнергию, фуражное зерно и заготовку сена. Сначала нужно накосить мотокосой сена, траву используйте луговую или люцерну. Просушите сено на сушилке и измельчите его на травяную муку. Потом измельчаются на дробилке зерновых кукуруза и ячмень, дальше через масло пресс нужно пропустить фуражные семена подсолнуха, что бы получить шрот подсолнечный. В идеале еще бы обзавестись фузодавкой – 400$. Она поможет Вам получить максимальное количество подсолнечного шрота. Дело в том, что когда вы продавливаете через шнэковый маслопресс семена подсолнуха на выходе вы получаете шрот подсолнечный и техническое (семена фуражные) подсолнечное масло в месте с фузом. Такое масло можно отстаивать, чтобы максимально отделить фуз от масла. А сам фуз продавить через фузодавку, что бы окончательно убрать из него масло. Если неохота затрачиваться на фузодавку 400$ можно пошить мешок из лавсановой ткани засыпать туда фуз и положить под камень или отжать автомобильным домкратом, это дольше, менее эффективнее, но работает и дешевле чем покупать фузодавку.
Гранулятор перерабатывает состав комбикорма и производит его в легкоусвояемых гранулах
Дальше, когда у нас готовы все компоненты мы прогоняем состав комбикорма через гранулятор комбикорма в пропорции в зависимости от типа комбикорма, который мы хотим получить. Гранулятор комбикорма позволяет менять насадки изменения размеров гранул. В кормлении крупного рогатого скота можно использовать крупные гранулы соответственно будет больше производительность гранулятора, а это экономия электроэнергии. Для кур несушек и кроликов, нужен гранулированный комбикорм с мелкими гранулами. Еще в дополнении к оборудованию можно добавить мини мельницу производства муки и отрубей в бизнес. Но это уже по усмотрению. Если у вас нет полного объема капитала, в начале некоторые компоненты можно покупать, а со временем можно приобрести оборудование для производства этих компонентов. Этот бизнес достаточно гибкий. Важно добавлять травяную муку, она очень полезна и существенно снижает себестоимость состава комбикорма, что делает бизнес привлекательным с точки зрения инвестирования. 1 килограмм травяной муки содержит 250г сырой клетчатки, 180г сырого протеина 170г сырой золы и 400г без азотистые экстрактивные вещества.
businessideas.com.ua
ГРАНУЛИРОВАННЫХ КОМБИКОРМОВ
Производство и использование гранулированных кормов
1.1. ОСНОВНЫЕ СПОСОБЫ ГРАНУЛИРОВАНИЯ ПОРОШКООБРАЗНЫХ МАТЕРИАЛОВ
Превращение дисперсных материалов в гранулы (зерна) с заданными физико-механическими свойствами может осуществляться различными способами.
В соответствии с ГОСТ 21669—76 в комбикормовой промышленности приняты следующие термины и определения.
Комбикорм — сложная однородная смесь очищенных и измельченных до необходимой крупности различных кормовых средств и микродобавок, вырабатываемая по научно обоснованным рецептам и обеспечивающая полноценное кормление животных.
Комбикорм-концентрат — комбикорм с повышенным содержанием протеина, минеральных веществ и микродобавок, скармливаемый с зерновыми, сочными или грубыми кормами для обеспечения биологически полноценного кормления животных.
Полнорационный комбикорм — полностью обеспечивающий потребность животных в питательных, минеральных и биологически активных веществах.
Гранулированный комбикорм — в виде
плотных комочков определенной формы и размеров.
Брикетированный комбикорм — в виде
плиток геометрически правильной формы определенных размеров.
Комбикормовая крупка — готовый продукт, получаемый измельчением гранулированного комбикорма.
Комбикормовая крошка — продукт, образую — IIIимея при разрушении гранулированных,- брикетированных комбикормов и комбикормовой крупки в процессе их производства, транспортирования и хранения.
В технической литературе, особенно в зарубежной, час — м| при описании процессов гранулирования и характерис — пмі основного продукта используется и другая термино — ми мя, в частности: пеллеты — гранулы, вафли — брике — M. I и другие. Однако широкого практического применения казанная терминология не нашла.
Известны принципиально различные способы связывй — ния сыпучих материалов в агрегаты — окатывание (накатывание) и прессование (брикетирование, таб — летирование, гранулирование). Выбор способа и средств для уплотнения дисперсных сред зависит от физико-механических свойств исходного материала и требований к показателям качества конечного продукта.
Ниже рассматриваются основные схемы технологических процессов гранулирования, принципы работы машин, отдельные конструктивные и кинематические особенности их рабочих органов, а также факторы, влияющие на процесс и качество продукции.
Гранулирование окатыванием — разновидность структурной нарастающей грануляции — можно сравнить с процессом образования снежного кома. Существуют теории послойного накатывания (процесс сухого гранулирования) и теория поверхностного натяжения (процесс влажного гранулирования). Основной отличительной особенностью процесса является перемещение (окатывание) гранулируемой массы по поверхностям аппарата, его рабочих органов и самого материала. Следовательно, при гранулировании этим способом происходит выбор самых благоприятных возможностей сцепления частиц порошка.
Кинетику процесса и механизм гранулообразования можно выяснить при изучении работы барабанного аппарата. Поступающий во вращающийся горизонтальный или наклонный барабан сыпучий материал при входе обрабатывается высокодиспергированной жидкостью, в большинстве случаев водой или водными растворами других веществ. Поэтому одним из основных условий образования гранул является гидрофильность сырья. При смачивании частицы порошка соединяются посредством, адсорбционных, капиллярных и сил поверхностного натяжения, окатываются по поверхностям аппарата, друг друга и внедряются в гранулы на конечной стадии* процесса. В результате продукт приобретает шарообразную форму, определенную плотность и размеры.
Гранулирование окатыванием осуществляется в цирку — ляционно-перекатывающем потоке обрабатываемого сыпучего вещества на барабанных, тарельчатых (дисковых), конических, лопастных или в развитом циркуляционном потоке вещества на вибрирующих и других подобных аппаратах. При окатывании большинство материалов необходимо увлажнять или добавлять к ним связующие компоненты. Технико-экономические показатели технологии и
качество готового изделия зависят от физико-химических свойств исходного материала, технологических и конструктивных факторов процесса и применяемого оборудования.
Серийное оборудование для окатывания пищевых и других сыпучих материалов малопроизводительно (до 1 т/ч), имеет большие металлоемкость и размеры.
Гранулированный комбикорм на дисковом грануляторе впервые в стране был изготовлен Институтом горючих ископаемых (ИГИ) в 1964 г. на Новотульском металлургическом заводе. В последующие 1965—1966 гг. ИГИ совместно с ВНИИ зерна провели опыты по гранулированию комбикормов на дисковых грануляторах диаметром 1500 и 3000 мм. Исследованиями установлено влияние крупности частиц рассыпного комбикорма на гранулообразование, основные этапы технологии и режимы гранулирования.
На Братцевской птицефабрике эксплуатировался цех по производству гранулированных комбикормов для цыплят, взрослой птицы и рыб методом окатывания.
Основными этапами технологического процесса при гранулировании комбикормов указанным способом являются: измельчение комбикорма до необходимого размера частиц, дозирование и увлажнение, накатывание увлажненного комбикорма на дисковом грануляторе, сушка гранул на специальных установках и сортирование гранул по фракциям.
Основные недостатки — это низкая (до 1 т/ч) производительность линии при значительных габаритах основного технологического оборудования (диаметр гранулятора 3 м), высокая энергоемкость, вызванная необходимостью измельчения комбикорма до размера частиц не более 0,3 мм и увлажнения до 40—42% с последующей сушкой і ранул до 14—15%, незначительное по сравнению с рассыпным комбикормом увеличение объемной массы готово — ю продукта. Кроме того, гранулы неоднородны по размеру (от 2 до 30 мм) и составу и со сравнительно большей вы — mi, таемостью питательных веществ.
Институтом технической теплофизики АН УССР разра — fioi. jna установка УСГ-1, принцип работы которой основан на методе скоростного окатывания. Составными частями мтаповки являются: собственно скоростной гранулятор, <мльсатор для приготовления эмульсий или растворов,
< сміїїопное устройство для сушки гранул в псевдоожиженном слое и классификатор, разделяющий гранулы на тре — г. и’мыс фракции. Оборудование предназначено для грану — .пфоиания различных порошкообразных материалов: мед
препаратов, алмазных порошков, катализаторов, удобрений и комбикормов. Размеры получаемых на установке гранул колеблются от 0,3 до 6 мм. Установка УСГ-1 с 1977 г. эксплуатируется в рыбколхозе «Банга» Латвийской ССР.
Гранулирование прессованием — один из наиболее распространенных’ в промышленности способов связывания сыпучих материалов в агрегаты, который относится к типичным процессам, направленным на получение определенной структуры с помощью внешних механических воздействий. Для этой цели применяют формирующие (прессующие материал в закрытой матрице), прокатывающие (прессующие материал между валками) и выдавливающие установки. Сущность процесса — объемное сжатие и сдвиг прессуемой смеси, в большинстве случаев ее пластификация и структурирование и затем формирование массы в гранулы.
Брикетирование основано на принципе формования материалов в замкнутом объеме с целью придания ему строго определенных форм и размеров. Основной операцией, обеспечивающей необходимое уплотнение исходных продуктов, является прессование. Процесс характеризуется оптимальными значениями достигнутых параметров давления и скорости прессования, имеющими первостепенное значение для технико-экономических показателей технологии и качества иізделия (Мартыненко Я. Ф., 1975, и др.).
В технике применяют прессы периодического действия (штемпельные, рычажные, карусельные, гидравлические и др.) и непрерывного ротационного принципа (кольцевіле, вальцовые). Наибольшее распространение получили вальцовые прессы, отличающиеся простотой конструкции, малой металло — и энергоемкостью, высокой производительностью.
Прессованием на вальцовых прессах вырабатывают брикетированные уголь, древесину, пластмассы, металлоизделия, пищевые продукты и др.
Этим способом получают также на межколхозных комбикормовых предприятиях брикеты для крупного рогатого скота, в состав которых входят измельченная солома, травяная резка, сухой свекловичный жом, концентраты и меласса. Брикетированные комбикорма выпускают как круглой формы диаметром до 130 мм, так и в виде плиток овальной или прямоугольной формы размерами 35Х Х35 мм, 40X60 мм, трапециевидные брикеты сечением 30X40 мм, 55X65 мм и др. Энергоемкость процесса брикетирования на 40—50% ниже по сравнению с гранулированием, что объясняется возможностью использования рассыпного комбикорма с размером частиц более 10 мм (Б$-
ляевский Ю. М., Сазонова ї. Н., 1977; Артюшин A. A., Рей — ссвич А. А., 1980, и др.).
С 1964 г. в ряде хозяйств Белоруссии для кормления рыбы применяли брикетированные корма. Механизированные линии по их приготовлению размещены непосредственно в рыбоводных хозяйствах. Они состоят из измельчителя зеленой растительности, двух кормораздатчиков, кормосме- сителя и торфобрикетного пресса. Брикеты получают массой 0,09—0,1 кг, влажностью до 18% и плотностью более единицы. Крошимость брикетов не превышает 5%, а водостойкость находится в пределах 2,5—3 ч. Важным является и то, что при изготовлении брикетированных кормов в их состав вводят до 10—35% местного сырья, зеленую массу, отходы различных производств.
Гранулирование выдавливанием, в зависимости от технологии подготовки исходного порошкообразного материала, может осуществляться двумя способами — влажным и сухим. При влажном гранулировании прессуемую массу с помощью дисперсионной среды (вязкие жидкости, вода) вначале переводят в пастообразное спластифициро — панное состояние, а затем подвергают формованию и кристаллизации.
Первый цех по производству гранулированных комбикормов способом влажного прессования в нашей стране был введен в эксплуатацию в 1956 г. на Саратовском комбикормовом заводе. Технология выработки гранул включала контрольное просеивание комбикорма, увлажнение горячей водой до 33—37% для образования тестообразной массы, прессование смеси, сушку гранул до стандартной влажности, охлаждение и просеивание гранул. Для этого использовали шнековые прессы, применяемые в макаронной промышленности МПД-11, ГМП-ТА *и шахтную сушилку непрерывного действия ВИС-2. Цех вырабатывал гранулированный комбикорм для кур-несушек. Вследствие небольшой производительности шнековых прессов (до L’00 кг/ч) и значительной энергоемкости процесса указанная технология не нашла широкого применения.
Из-за значительной энергоемкости, отсутствия специального оборудования и недостаточной разработки технологии влажное гранулирование комбикормов промышленно — I о внедрения у нас в стране не нашло. За рубежом влажное прессование рекомендуют применять, в основном, при из — ютовлении гранулированных кормов для форели. Целесообразность этого способа объясняется физическими свойствами прессуемой массы, влажность которой превышает
30% йз-за наличия в корме До 50% отходов Мясо-Молочной промышленности.
В Японии и в ряде других стран для промышленного выращивания ценных пород рыб и животных, а также для домашних животных в небольших количествах вырабатывают корма методом таблетирования. Этот способ прессового гранулирования представляет собой непосредственное формование сыпучих продуктов в таблетки заданных размеров и формы. В связи со спецификой механизма таблетирования продукт значительно уплотняется, в результате увеличивается его прочность. Таблетируемые комбикорма продолжительное время не раскисают в воде и сохраняют питательную ценность. Имеющиеся в промышленности наиболее распространенные эксцентриковые (ударные) и ротационные таблетирующие машины малопроизводительны, а технологический процесс, из-за необходимости тонкого измельчения прессуемой массы, энергоемок.
Известны таблетирующие машины ряда зарубежных фирм, выпускающие таблетки, покрытые специальными пленками. Способ покрытия пищевых продуктов и других изделий пленкообразующими веществами находит все большее распространение в мировой практике. За рубежом с этой целью применяют пленкообразующие полимеры, высокобелковые вещества, технические жиры и др.
В нашей стране работы по увеличению водостойкости гранулированных комбикормов для рыб путем покрытия их поверхности гидрофобными веществами проводили ВНИИКП, ВНИИПРХ, Львовский ордена Ленина политехнический институт (ЛОЛПИ) и др. Были опробованы такие вещества, как крахмал, технический жир, парафин, бентонитовые глины, поливиниловый спирт и др. Однако гранулы с искусственным покрытием имеют ряд недостатков, снижающих эффективность их производства и использования. Недостаточно разработана и технология обработки гранул различными пленкообразующими веществами. В результате, несмотря на определенный интерес и перспективность, промышленного применения указанный способ также не нашел.
Наибольшее распространение, как в нашей стране, так и за рубежом, получил способ сухого гранулирования комбикормов. После контроля по примесям рассыпной комбикорм подается в прессующую установку, где обрабатывается паром и посредством выдавливания смеси через отверстия матрицы формуется в гранулы, которые после охлаждения на специальной колонке и просеивания поступают в склад готовой продукции. Режимы прессования подбирают из расчета обеспечения технической производительности установки при требуемых показателях качества гранул. В охлажденных гранула», в зависимости от их назначения, допускается наличие до 5—10% мелких частиц (проход сита с отверстиями диаметром 2 мм) комбикорма. При необходимости из гранул вырабатывают крупку.
Технология сухого прессования имеет ряд преимуществ но сравне
msd.com.ua
Производство гранулированных комбикормов
Гранулированные комбикорма изготавливают для всех видов животных, птиц и рыб. Размеры гранул зависят от вида и возраста животных, способов кормления. Для взрослых птиц (кур, уток, гусей, индеек) диаметр гранул составляет 4,7…9,7 мм, взрослого крупного рогатого скота 4,7…19,0, взрослых овец 4,7…12,7 мм, лошадей 4,7…19,0, рыб 4,7 мм и т. д. Для молодняка птицы гранулированные комбикорма применяют в виде крупки.
Комбикорма гранулируют сухим и влажным способами. Сухое гранулирование проводят в установках ДГ, Б6-ДГВ, Б6-ДГЕ, имеющих производительность соответственно 7…10 т/ч, 9…11 и 14…15 т/ч. Производительность установок зависит от размера выпускаемых гранул: нижний предел при диаметре гранул 4,7 мм, верхний — при диаметре 19 мм.
Каждая установка состоит из пресса-гранулятора, охладителя гранул, измельчителя гранул, сортировочной машины для гранул (крупки). Кроме того, в линию может быть включен просеиватель для рассыпного комбикорма.
После контрольного просеивания на ситах с отверстиями 4…5 мм и сепарирования в магнитных сепараторах комбикорма гранулируют в прессах-грануляторах.
Рассыпной комбикорм в смесителе пропаривают сухим паром, который подают под давлением 0,35…0,4 МПа. При этом влажность комбикорма повышается до 13…17 %. Температура комбикорма после смесителя достигает 50…70°С, после пресса — 70…80 °С.
При гранулировании БВД, содержащих большое количество протеина животного происхождения, давление пара рекомендуют принимать 0,4…0,5 МПа, протеина растительного происхождения — 0,2…0,3 МПа. Расход пара составляет 60…80 кг на 1 т сырья. Если гранулированные комбикорма изготавливают для жвачных животных с высоким содержанием карбамида, давление пара принимают до 0,2 МПа и расход его — до 18…22 кг на 1 т.
При гранулировании можно применять связующие вещества с одновременным пропариванием или без пропаривания. В качестве таких веществ используют соленый гидрол, мелассу, кукурузный экстракт и другие, а также воду. Полученные гранулы охлаждают до температуры, превышающей температуру окружающей среды не более чем на 10 °С. Затем гранулы просеивают на ситах с отверстиями ∅ 2,0…2,5 мм и на металлотканых № 1,6…2,0.
Производство крупки из гранул. Для молодняка птиц требуются гранулы ∅ 2…3 мм, однако такие гранулы производить нецелесообразно из-за резкого снижения производительности прессов и повышения удельного расхода энергии. Процесс гранулирования при производстве таких гранул нестабилен, фильеры матриц забиваются комбикормом. Например, при переходе пресса с производства гранул ∅ 2,4 мм вместо 4,7 мм его производительность снижается примерно в четыре раза, а удельный расход энергии увеличивается более чем в два раза. Поэтому мелкие гранулированные комбикорма получают путем измельчения гранул ∅ 4,7…9,7 мм с последующим калиброванием на ситах с определенными размерами. Так, для цыплят и бройлеров от 1 до 30 дней остаток на сите с отверстиями ∅ 3 мм должен быть не больше 20 %, а проход сита с отверстиями 0 1 мм не должен превышать 18 %. Гранулы следует измельчать таким образом, чтобы получить минимум мелкой фракции, которую необходимо направлять на повторное гранулирование. Количество такой фракции не должно превышать 30 %, а выход крупки быть не менее 70 %. Измельчение проводят в вальцовом станке. Диаметр вальцов 205…250 мм, нарезка взаимно-перпен
www.activestudy.info
Размеры гранул при гранулировании комбикормов
Размеры и форма гранул зависят от их назначения.
Гранулы с размерами производят в США, Канаде, Англии и некоторых других странах. Размер гранул определяется количеством корма, которое животное может съедать без усилий.
Еще несколько лет тому назад для цыплят производили только мелкие гранулы диаметром 2,4 мм, однако они не получили широкого распространения, так как были слишком велики по размеру для цыплят малого возраста, а также в силу высокой стоимости их производства. При выработке же крупок из гранул диаметром 4,8 мм существенно повышается производительность гранулирующих установок, обеспечивается получение более однородных по размеру частиц комбикорма, который легче поедается и эффективнее усваивается птицами. Поэтому комбикормовые крупки нашли широкое применение для кормления цыплят в фермерских хозяйствах и считаются наиболее эффективным кормом по сравнению с мучнистыми и гранулированными комбикормами, особенно при системе бройлерного содержания.
Гранулирующие машины дают некоторые отклонения в длине, а иногда и в диаметре гранул. Это не имеет большого значения для взрослой птицы, но зато даже незначительные отклонения в размерах гранул (2,4 мм) отрицательно сказываются на цыплятах. Если гранулы имеют большие размеры, то цыпленок их не может проглотить. Кроме того, цыпленок склонен к избирательному поеданию корма, ест то, что ему лучше подходит, и оставляет гранулы большого размера. При этом получается много отходов.
Мелкие и более ровные по крупности фракции крупок являются нормальным кормом для цыплят в возрасте до 8 недель, т. е, до такого возраста, когда они будут способны принимать гранулы диаметром 3,2 мм. Взрослой птице дают гранулы диаметром 4,8 мм. В случае интенсивного кормления при ускоренном выращивании бройлеров период кормления комбикормовой крупкой сокращается до 5—6 недель.
При батарейном содержании кур-несушек фермеры кормят их крупкой крупных фракций или гранулами диаметром 3,2 мм в течение всей жизни.
Английская фирма «Ричард Сайзер» разработала специальную матрицу с отверстиями диаметром 2,4 мм, отличающуюся более высокой производительностью по сравнению с матрицами других фирм, так как ее применение исключает процесс измельчения, который дает до 30—40% пылевидных и крупных частиц, направляемых на повторное прессование и измельчение.
Для взрослой домашней птицы производят круглые гранулы диаметром 3,2; 4; 4,4 и 4,8 мм. Некоторые фермеры используют такие гранулы для кормления телят в возрасте до трех месяцев при интенсивном производстве говядины, а также для кормления овец и некоторых других животных.
Комбикорм для телят в возрасте от 3 до 6 месяцев (период выращивания) и от 6 до 10 месяцев (период приращивания говядины) производится в гранулах диаметром 9,5; 12,7 и 15,9 мм, а также квадратной формы размером 9,5X9,5; 12,7X12,7 и 15,9X15,9 мм. В незначительном количестве гранулы диаметром 9,5 и 12,7 мм используют для откорма свиней.
Для коров в период лактации изготовляют круглые гранулы диаметром 19 мм и квадратные 19X19 мм. Кроме того, производят брикеты различных размеров для разбрасывания на лугах в качестве подкормки.
Французская фирма «Сокам» выпускает матрицы для производства гранул следующих размеров: для цыплят и молодок — диаметром 3 мм, для кур — д
www.activestudy.info