Оборудование для производства клееного и профилированного бруса
Деревянные постройки не теряют актуальности, популярным материалом в строительстве является клееный сосновый брус. Оборудование для производства клееного бруса позволяет производить детали разного сечения и длины, эта особенность упрощает подбор и монтаж брусков на стройплощадке, непроходных каналах.
Необходимые материалы для производства
Процесс производства клееного бруса
Для организации производственного процесса понадобится качественное оборудование для производства профилированного бруса и соответствующее помещение, вмещающее основную линию агрегатов: автоматическая линия, сырье и персонал. Для изготовления качественного бруса применяются такие виды древесины, как ель, сосна, кедр либо лиственница, сырье часто закупается в лесопильных хозяйствах.
Для производства используются следующие заготовки:
- необрезанные элементы;
- обрезанные доски;
- пиловочник.
Для их склеивания могут понадобиться различные виды клея:
- резорциновые;
- меламиновые;
- полиуретановые.
Они отличаются по цвету шва, уровню токсичности и характеру затвердения.
Основные этапы производства
Процесс изготовления стройматериала состоит из нескольких этапов:
- Прием сырья – этот этап предполагает визуальный осмотр сырья при получении на складе.
- Сортировка древесины – во время этой процедуры удаляется некачественный пиломатериал, а отсортированные бревна складываются в штабеля.
- Сушка пиломатериала – она осуществляется в специальных камерах и занимает около 7–8 дней.
- Предварительная строжка – этап необходим для выявления и устранения дефектов сырья. Для этого применяется четырехсторонний станок.
- Торцовка – процесс, направленный на устранение дефектов, конечный продукт – ламели высокого качества.
- Сращивание полученных ламелей – этап, включающий обработку подготовленных материалов клеем, а также помещение их в отдел накопителя.
- Окончательная строжка – чистовая обработка материала.
- Прессовка – процесс помещения строганных ламелей в прессовочный автомат. Там они находятся в течение получаса под высокой нагрузкой.
- Завершающие этапы: контроль качества и упаковка.

Контроль качества готового клееного бруса
Первые три этапа могут быть исключены из основного списка. Это допускается, когда специалист закупает сырье уже подготовленное, просушенное.
Какое оборудование нужно
Для предприятия необходимо оборудование для производства бруса определенной направленности:
- дисковая пилорама, применяемая для нарезки досок;
- профильно-брусующий станок;
- четырехсторонний станок для фрезерования пиломатериала;
- станок для нарезки чашек в брусе (могут применяться ручные чашкорезы).
Дополнительно для подготовки бруса понадобятся:
- сушильные камеры;
- линии торцевого сращивания ламелей;
- станок для нанесения клея;
- пресс для склеивания.
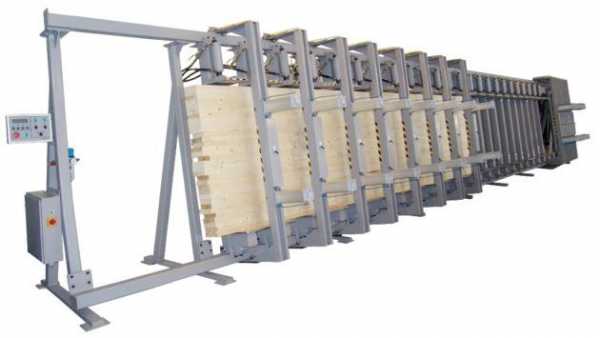
Пресс для склейки бруса
За счет постоянной модернизации для производства профилированного бруса разрабатываются новые модели станков, они включают множество функций. Такие универсальные станки значительно экономят расходы на приобретение оборудования и место для его размещения.
При помощи даже одной такой машины могут выполняться три основные работы:
- распиловка;
- обработка;
- расщепление;
- фрезерование.
Такие аппараты стоят довольно дорого, но мощность агрегатов, их продуктивность и качество позволяют получить большую прибыль от реализации изделия. Дополнительные приспособления позволяют использовать отходы для производства упоров под стальные трубопроводы, такие детали являются востребованными во время стройки промышленных зданий.
Особенности четырехстороннего станка
Каждый тип оборудования обладает рядом характеристик, на которые следует обращать внимание при покупке.
Четырехсторонний станок для фрезеровки необходим для обеспечения равномерности толщины бруса по всей длине. Во многом уровень такой машины зависит от качества фрезы. Чем больше насадок, тем универсальнее автомат. С увеличением функций увеличивается разнообразие бруса, производимого на конкретном агрегате.
Поэтому при покупке важно учесть:
- Присутствие нескольких фрез – увеличение ассортимента повлияет на спрос покупателей.
- Каретки для подачи материала – они могут быть автоматическими либо ручными.
От этих параметров зависит производительность труда персонала.
Особенности станка для нарезания чашек
Чашкорезы необходимы для изготовления эстетически привлекательного и надежного крепления бруса при строительстве.
Качественные соединения обеспечат герметичность, мобильность сборки и надежность узла. Часто такие станки оснащены насадками:
- для изготовления прямых чашек;
- для косых вариантом чашек;
- для разного угла наклона.
Разнообразие насадок сокращает производственный цикл и увеличивает ассортимент товаров.
Любое производство бруса требует присутствие клеевых машин. Оптимальным вариантом для производства являются клеенаносящие установки ленточного типа. Они условно делятся на две большие группы станков.
Постоянной циркуляции – такие аппараты наносят на ламели клей непрерывной полосой. Перед началом процесса настраивается расход клея, а остатки, пролитого либо неиспользованного материала, попадают в бак. Оттуда он удаляется насосом и вновь отправляется в резервуар для нового этапа. При таком производстве исключены потери клеевых компонентов, промывка оборудования не требуется.
Смесевого нанесения – такие станки оборудованы статическим миксером различного диаметра с витками разного направления. Через нее подается клеевая смесь под определенным давлением, после чего она попадает в трубку.
Система строго ограничена: подача клея происходит только при условии, что под ней расположена ламель, а заканчивается после ее прохождения. Такой подход обеспечивает максимальную экономию.
Особенности пресса
Для производства бруса важно подобрать качественный пресс. Он представляет собой горизонтальные либо вертикальные станки. Подбирать модель следует с учетом желаемых параметров готовой продукции и возможностей производственной площади:
- Горизонтальный пресс занимает много места, но обеспечивает равномерность нагрузки и удобство сборки.
- Вертикальный пресс более компактный вариант, но в нем деталь обязана находиться в определенном положении.
Работа с универсальными станками
Универсальный станок для производства бруса
Универсальные станки – оптимальный вариант оборудования.
Технологический процесс выглядит следующим образом: дерево подается во фрезерный отсек, проходит стадии обработки, а на выходе получается готовым профилированным брусом.
Преимуществами такого типа станков являются:
- компактность и экономия площади;
- отсутствие необходимости набора большого штата;
- уменьшение длительности производственного цикла.
Высокая стоимость агрегатов окупаема в дальнейшей эксплуатации. Приобретая оборудование для производства клееного бруса, важно учесть тип древесины и клея. Такой метод избавит от большого количества отходов.
Покупка оборудования часто бывает заменена арендой, многие предприятия сдают в аренду профессиональные линии, обеспечивая предприятие сырьем.
Видео по теме: Линия для производства клееного бруса
promzn.ru
Оборудование для производства клееного бруса.
В наше время клееный брус часто применяется при строительстве. Его используют в разных отраслях строительства: от строительства частных домов до строительства таких огромных зданий, как аквапарки, бассейны, складские комплексы, развлекательные центры. Чаще всего их (брусья) изготавливают из ели либо сосны, реже используют лиственницу и кедр. Процесс производства клееного бруса поясняется достоинствами этого материала.
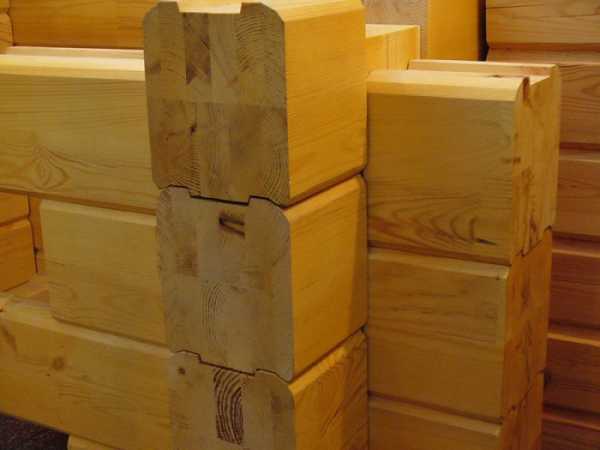
Технология производства состоит из нескольких стадий:
• 1 стадия
Сначала брёвна распиливают на доски точного размера и высушивают, следуя строгим правилам. Сушат именно доски, а не бревна, так как тонкую доску просушить легче, чем огромное бревно, отсюда, и процент влажности будет ниже!
• 2 стадия
После сушки, материал проходит тщательную проверку на наявность дефектов, а те места в доске, где они есть, удаляют. Затем доски, без изъянов, обрабатывают антисептиками и антипиренами.
• 3 стадия
В начале 3 стадии доски острагивают, а затем из ламели – хорошо высушенных и отсортированных досок – на спецпрессах происходит склеивание брусьев. Кстати, досок может быть и 2, и 3, и 5 штук. Это даёт возможность регулировать толщину брусьев. При склеивании пользуются специальными прочными и водостойкими клеями. Склеивание проходит по международным стандартам. При склеивании брусьев также соблюдают важное правило: направление «древесных колец» обязательно задаётся в противоположные стороны – это нужно для того, чтобы брус был прочнее, при смене влажности не менял свою форму, а также, чтобы улучшить звукоизоляцию.
Так как клееный брус – это материал нового поколения, то, очевидно, что для его производства требуется спецоборудование.
1) Лесопильный станок
В производстве раскройку пиломатериалов производят с помощью специальных лесопильных станков. Лесопильные станки по способу подачи материала можно разделить на 2 типа: станки позиционного и станки проходного типа.
2) Многопильный станок
Многопильный станок нужен, в основном, как раз-таки для распила огромного бруса на доски дисковыми пилами. К сожалению, этот способ имеет ряд недостатков. К примеру, если для обработки на таком станке предлагается брус с большим диаметром, то нужно использовать пилы большей толщины, а это, в свою очередь, ведёт к увеличению толщины пропила и, соответственно, к потере древесины. Современная техника не стоит на месте: проблема решена. В производстве стали пользоваться двухвальными многопильными станками.
3) Вакуумное или откидное устройство (для разборки штабеля)
4) Влагомер
Производит проверку и отбраковывает чрезмерно влажные или очень сухие заготовки.
5) Четырёхсторонний станок продольного фрезерования
Выполняет качественную добротную обработку сторон ламели, тем самым вскрывает дефекты. Предназначается для профильной обработки брусьев со всех сторон с целью получения так называемой половой вагонки, а также плинтусов, досок, реек и других фасонных изделий в производстве.
6) Линия оптимизации
Предназначена для удаления пороков дерева, заранее промаркированных оператором. Это происходит в автоматическом режиме. Линии оптимизации или сращивания, которые используются в современном производстве, имеют достаточную автоматизацию. Данная особенность помогает производителю экономить средства. После удаления пороков линия сращивания выполняет фрезеровальные работы с минишипом на торцах заготовки. Затем она наносит на заготовки клей и прессует их.
7) Клеенаносящий станок и строгальным станком
Чаще всего эти два станка находятся рядом с целью ускорения работы. Итак, клеенаносящий станок предназначен для нанесения клеевых материалов с двух сторон на брусья, как раз-таки для склеивания щитов. Клеенаносящий станок состоит из следующих частей:
o Два конвейера отвода заготовки
o Два конвейера подачи заготовки
o Клеенаносящий вал
o Прижимной вал
8) Прессовые устройства
Существует две системы прессов. Это гидравлическая система и система LUST. Самые современные клеевые устройства делают возможным осуществлять прессовку ежечасно. Но какую бы систему производитель не выбрал, цель у него будет одна: добиться того, чтобы клей схватился. Также важную роль занимает ручной инструмент.
Хотим сказать ещё несколько слов о технологии производства. Вышеописанное нами представляет собой схему общей принципиальной технологической обработки натурального дерева (древесины). Это и есть весь путь: от бревна к готовой продукции – в нашем случае, клееным брусьям. Дорогие читатели, вы увидели и переработку круглого, свежеспиленного дерева, и запрессовку ламелей.
И в завершении статьи хотим рассказать вам о достоинствах и недостатках клееных брусьев. Современные технологии производства данного материала позволяют использовать его почти во всех значимых отраслях деревянного строительства. Широко применяется брус из-за несомненного преимущества его перед монолитом дерева. Преимуществ у клееного бруса много, но мы вам расскажем о самых значимых из них.
Отменное качество поверхности. Это преимущество можно объяснить тем, что при обработке из пиломатериала вырезаются все изъяны и сучки, и ещё, брусья тщательно подбирают по уникальности, по цвету и так далее.
Клееный брус хранит свои геометрические размеры, форму на протяжении всего срока службы несмотря ни на что.
Изделие обладает прочностью, так, брусья на шестьдесят процентов прочнее, чем древесина.
Деревянный дом, построенный именно из клееных брусьев, а не из монолитных брёвен, обладает значительными теплотехническими характеристиками.
По выше объяснённым нами причинам поверхность, сделанная из клееных брусьев, очень ровная. Стена, выполненная из данного изделия, смотрится монолитом. Декоративная отделка, как наружная, так и внутренняя ей практически не нужна.
Итак, обширное применение клееных брусьев в строительстве – это вариант, который подойдёт практически каждому. Отдельная тема – это бизнес по изготовлению такого материала, как клееный брус. Таковой бизнес является перспективным. Им занимаются многие, кто не побоялся его организовать, предприниматели довольно успешно!
ideamaniya.ru
технология изготовления клееного бруса от GoodWood
Клееный брус, в отличие от других материалов, является высокотехнологичным продуктом. Соответственно, для производства качественного клееного бруса необходимо строгое соблюдение технологии. Наша компания пришла к тому, что без собственного производства клееного бруса нам не обойтись. Только в этом случае мы можем гарантировать, что брус соответствует техническим условиям, т.е. со временем не треснет, не потемнеет и его теплоизоляция будет на должном уровне. На сегодняшний день производственные мощности компании GOOD WOOD насчитывают 2 собственных завода в Зеленограде общей площадью 10 000 кв. м.
Технология производства клееного бруса поэтапно:
- Первая торцовка
- Распиливание бревна (бревно — доски)
- Сушка
- Вскрытие дефектов (первое строгание)
- Оптимизация (доски — ламели)
- Сращивание (ламели — плети)
- Второе строгание (рейсмусование)
- Нанесение клея
- Прессование (плети — клееный брус)
- Профилирование (клееный брус — клееный профилированный брус)
- Торцовка
- Зарезание чашек (пазов)
Спрос на эту продукцию в последнее время сильно возрос, и, как обычно у нас происходит, появилась целая индустрия по выпуску некачественных материалов. Их использование резко снижает эффект от вложенных средств.
В активе компании новейшее оборудование от ведущих европейских производителей, сушильные камеры MuhlbockVanichek, производственные линии от лидеров — Hundegger и SMB, мы также используем при изготовлении немецкое и американское оборудование Weinig и Leademac. Качество обработки и точность у этих станков не может сравниться с лучшими немецкими станками. Для того чтобы при изготовлении бруса на дешевых станках обеспечить вхождение шипов в пазы, необходимо увеличивать зазоры, что ведет к ухудшению теплоизоляционных свойств.
Завод по производству клееного бруса GOOD WOOD полностью автоматизирован, на каждой стадии происходит автоматический контроль качества. Это позволяет свести процент брака к минимуму. Мы сушим древесину с использованием мягких режимов сушки при влажности 8–10 %.
Строгие стандарты качества и технические условия, принятые
www.gwd.ru
Оборудование для производства клееных деревянных конструкций
- Оборудование для изготовления клееного бруса, клееного щита, балок, ДУО и ТРИО
- Механизация строгального производства
- Механизация линий по производству клееного бруса
- Наклонные штабелеукладчики
- Вакуумная разборка штабелей
- Триммеры
- Автоматические линии сортировки и укладка штабелей для строганных изделий
- Механизация процессов обвязки и упаковки готовых пакетов и изделий
Технология производства клееного бруса
Производство клееного бруса состоит из нескольких стадий. Первый этап — изготовление досок. Исходным сырьем являются бревна, которые распиливаются на отдельные доски. На втором этапе отобранные доски сушатся при невысокой температуре в специальных сушильных камерах, где они высыхают до 8-12% влажности. После сушки и кондиционирования пиломатериалы поступают в цех (фото).
Затем на торцовочных станках из досок вырезаются сучки, гниль, трещины и другие пороки. В итоге получаются небольшие доски, которые сращиваются по длине при помощи мини-шипов (которые формируются на шипорезном станке) и получаются доски (так называемые ламели).
Следующий этап производства клееного бруса — ламели склеивают между собой с помощью клея. На торцах различных по длине отрезков ламелей фрезеруется зубчатый профиль, далее ламели под давлением склеивают друг с другом до необходимой длины. При таком рациональном производстве теоретически можно получать ламели бесконечной длины.
Причем соседние ламели при склеивании совмещают таким образом, чтобы древесные волокна находились в разном направлении. Это приводит к усилению прочностных свойств готового клееного бруса, тем самым достигается его высокая устойчивость к деформациям. Хорошее прилегание ламелей при склеивании достигается использованием специальных гидравлических прессов.
И, наконец, заключительным этапом в производстве клееного бруса является его профилирование на четырехстороннем станке, когда в готовом изделии вырезаются пазы и гребни, а после этого — отверстия для нагелей. Этот этап также является очень важным, так как по своей сути — это уже подготовка непосредственно к строительству дома. На этом процесс изготовления бруса заканчивается. На рисунке представлен технологический процесс изготовления клееного бруса.
Сопряжение внутренних и наружных стен выполняют способами, обеспечивающими прочное соединение брусьев в конструкцию рамного типа. При этом все стеновые элементы должны быть из древесины одной породы и иметь одинаковые размеры по высоте сечения.
bgnw.ru
Технология производства бруса
О существовании такого строительного материала как доска знают, конечно, все. Но не многим известно, как делают брус, чтобы он имел возможность эффективно противостоять воздействию разрушающих факторов. Многие свойства древесины зависят от породы дерева. Но некоторые можно придать дополнительно при помощи специальной обработки.
Технология производства бруса
Собственно сам технологический процесс производства начинается на лесозаготовительных хозяйствах. Там выбирают наиболее подходящие по возрасту деревья, после чего их спиливают и на сортиментовозах транспортируют на пилораму. Для производства бруса подойдут только деревья с ровным стволом, поэтому далеко не каждое дерево может в будущем стать строительным материалом.
Все ветки удаляются непосредственно после спиливания дерева, так что на дальнейшую обработку отправляется только ствол. Ветки тоже идут в производство, но для других целей. Они могут в будущем стать дровами или будут перемолоты для создания топливных древесных гранул. При попадании на пилораму стволы сортируют по толщине и породам дерева, если в этом есть необходимость. Но зачастую в одной партии доставляются деревья одной породы и одного года высадки, так что они имеют примерно одинаковый диаметр.
Если планируется производство материала с минимальной влажностью, сырье отправляется в сушильные камеры, где в зависимости от его состояния может провести до нескольких недель, пока уровень влажности не будет понижен до установленной отметки. При изготовлении бруса естественной влажности этот этап пропускают и приступают сразу непосредственно к обработке. Не зависимо от того, какой формы брус будет на выходе, сначала каждый ствол попадает на станок, который снимает кору и верхний слой древесины.
После обработки заготовка имеет идеальную круглую форму без каких-либо впадин или выступов. Дальнейший процесс обработки зависит от вида производимого материала. При изготовлении обыкновенного бруса округлая заготовка поступает на оборудование для отпиливания круглых частей. На выходе получается прямоугольный параллелепипед. После этого он распиливается на доски установленных габаритов, упаковывается и отправляется на склад готовой продукции или сразу к заказчику.
Какие размеры бруса будут выбраны в качестве окончательного варианта зависит от технического задания. Современное оборудование дает возможность задать конкретные настройки с точностью до миллиметра, так что при выполнении индивидуального заказа у предприятия не возникнет трудностей. Станок для бруса оцилиндрованной формы придает всем заготовкам одинаковый диаметр. Параметры оператор задает вручную, а обработка идет полностью в автоматическом режиме. Это позволяет получать идеальный результат за короткое время.
После обработки и придания брусу нужного диаметра, он поступает на станок, который пропиливает на одной из сторон специальную канавку. При строительстве она служит для лучшей стыковки деталей между собой. Когда форма готова, производится шлифовка бруса до гладкого состояния. Профилированный материал имеет самую сложную и трудоемкую технологию производства. Начальные этапы полностью соответствуют изготовления обыкновенного бруса, но после получения формы параллелепипеда он отправляется не на склад, а на еще одну обработку. Из заготовок будут выпилены деревянные профили со специальными пазами. Для этого используются фрезы для бруса разной формы.
После обработки доски шлифуют до гладкого состояния и упаковывают. Профилированный брус очень хорош при строительстве различных объектов. Благодаря пазам конструкции собираются очень оперативно, не имеют между собой зазоров и не требуют использования монтажных материалов. Хотя последнее свойство зачастую игнорируют и для верности все равно скрепляют детали между собой специальными средствами.
Особенности изготовления клееного бруса
Процесс изготовления клееного бруса также отличается своей трудоемкостью. Для его производства заготовку зарезают на тонкие пластинки, которые должны иметь влажность не выше 10%. Затем в специальной камере под высоким давлением эти пластинки склеивают между собой водостойким клеем. Качество бруса, изготовленного таким способом, считается наилучшим. Материал получает дополнительную твердость, которая недостижима для древесины в природных условиях. А благодаря обработке клеем он получает полную защиту от влаги и всевозможных вредителей.
Для изготовления данного материала чаще используют древесину одной породы, но иногда может применяться и метод межпородного соединения. Таким путем достигается сочетания уникальных свойств в брусе, когда допустим необходима твердая сердцевина и мягкая поверхность. Используется этот метод очень редко и в основном по специальному заказу.
Кроме перечисленных способов производства есть еще один, полностью соответствующий традициям древнего зодчества. Он основывается на возведении строения из необработанных стволов, которые еще называют «дикий» брус. Эта работа несет в себе дополнительные трудности, так как очень тяжело подгонять материалы разных размеров друг к другу. К тому же, остаются очень большие щели, которые приходится замазывать специальными веществами.
Такое строительство пропагандируют только любители исторических реконструкций с максимальной достоверностью. Но необработанное дерево имеет одно преимущество перед калиброванным брусом. Оно менее подвержено рассыханию. Но этот недостаток обработанного материала легко устраняется при помощи защитного лака или других специальных жидкостей. А при соблюдении всех технологий сушки такой недостаток и вовсе сводится на нет. Зато прочность бруса после обработки заметно выше, чем имеет древесина в природе. Это достигается при помощи соблюдения особых условий производства.
Трещины в брусе — это неизбежное явление даже для самого качественного материала. Ничего страшного в их появлении нет, если вовремя принять меры. Нужно затолкать в полость трещины джут, а затем замазать его мастикой под цвет древесины. Это убережет от дальнейшего расширения борозды и позволит не допустить влагу в середину материала.
promplace.ru
Производство профилированного бруса своими руками
Производство профилированного бруса сегодня поставлено на поток. Это и неудивительно, ведь материал пользуется огромным спросом при строительстве домов. Он имеет множество положительных сторон, но обладает и некоторыми недостатками. Перед применением профилированного бруса необходимо ознакомиться со всеми характеристиками.
Характеристика профилированного бруса
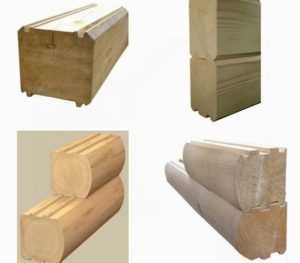
Виды профилированного бруса
Профилированный брус – это современный строительный материал, для производства которого используется хвойные деревья: сосна, ель или кедр. Поверхность материала шлифуется, что обеспечивает его практически идеальную гладкость.
Профилированное изделие изготавливается по новым современным технологиям.
Ему придается уникальная форма с шипами и пазами. Благодаря этому древесина плотно прилегают друг к другу, что повышает теплоизоляцию воздвигаемой конструкции.
Преимущества при строительстве из профилированного бруса
Преимущества строительства из профилированного бруса заключается в следующем:
Строительство дома из профилированного бруса
- изделие имеет идеальную герметическую форму, поэтому различные выступы, впадины и т. д. не испортят внешний вид возводимого здания;
- изделие обладает точными линейными размерами, благодаря чему сборка конструкции происходит легко и быстро;
- плотное прилегание древесины друг к другу обеспечивает повышенную теплоизоляцию помещения и защищает его от проникновения влаги внутрь;
- нет потребности в организации тяжелого фундамента, можно обойтись ленточным или столбчатым основанием;
- привлекательный внешний вид профилированной конструкции позволяет отказаться от наружной и внутренней отделки помещения;
- использование при строительстве профилированного клееного бруса или камерной сушки, сэкономит время для усадки помещения.
Использование профилированного элемента в строительстве помогает избежать таких проблем, как образование щелей, растрескивание, расширение межвенцовых швов, благодаря чему нет потребности конопатить щели.
Замковая система соединения позволяет возводить конструкции из профилированного бруса даже непрофессионалам.
Классификация строительного элемента
При производстве такие изделия классифицируют по следующим признакам:
- структура;
- габариты;
- тип профиля;
- степень влажности;
- наружный вид.
Профилированный строительный элемент бывает следующих габаритов:
Размеры и сечения профилированного бруса
- 100х100;
- 150х150;
- 200х200.
Для возведения жилых конструкций обычно используются изделия, габариты которого составляют 100х100.
По своему строению выделяют такие разновидности:
- клееный брус;
- из цельного бревна;
- двойной материал, который обладает повышенной теплоизоляцией.
Материал классифицируют по форме следующим образом:
- прямоугольный;
- Д-образный.
Классификация по типу профиля:
- с одним шипом;
- с двумя шипами;
- со скошенной фаской;
- с гребенкой, т. е. с большим количеством шипов;
- финский профиль с широкими пазами, расположенными сверху и снизу.
Финский профиль
При воздвижении жилых сооружений обычно применяется древесина с финским профилем или гребенкой.
Такой выбор объясняется тем, что конструкции из него воздвигаются быстрее и являются более надежными, чем сооружения из другого материала.
По уровню влажности выделяют следующие виды:
- высушенный естественным путем;
- высушенный в специальной камере.
Для воздвижения помещений специалисты советуют использовать изделия камерной сушки. Дело в том, что они отбраковываются тщательным образом, это позволяет поставлять на рынок только качественное сырье. Если же древесина высохла естественным образом, то она может деформироваться или растрескаться. Но и такие изделия поступают на строительный рынок. Поэтому специалисты рекомендуют перед обретением товара спрашивать у продавца, как именно был высушен брус.
Изготовление бруса
Компенсационный пропил
Производство профилированного бруса осуществляется в несколько этапов. Для начала лес сортируется, отбирается только качественная древесина, у которой нет дефектов. Далее, делается калибровка по габаритам сечения материала и выполняется компенсационный пропил. Именно он препятствует растрескиванию при сушке и усадке строения. Затем изделие перемещают на станок, обрабатывается с четырех сторон и шлифуется.
После этого производится профиль и чаши для соединения брусьев с углов. Это выполняется в тех случаях, когда производитель создает комплект для воздвижения сооружения. Все брусья в этом случае тестируются на качество соединения. Их собирают и смотрят на то, как плотно они прилегают друг к другу. Изделия с некачественной сцепкой отбраковываются.
На последнем процессе производства бруса, изделие помещается в специальное устройство – камерную сушку. Именно здесь испаряется вся лишняя влага. Иногда этапы производства меняются местами, и сначала выполняется сушка и только после этого делается калибровка.
Для более качественного производства бруса обрабатывают антисептиком. Но часто производители игнорируют это. Поэтому о наличие антисептической обработки профилированного элемента следует поинтересоваться у продавца.
Производство клееного материала немного отличается от производства другого бруса:
Технология производства клееного бруса
- сначала выполняется производство ламелей из подготовленной древесины;
- отбор качественного материала;
- обработка ламелей антисептиками и антипиренами;
- соединение ламелей с помощью специального клея, который наносится по всей длине;
- выполнение замкового соединения;
- отделка и обработка лаком, если этот процесс предусмотрен производством.
Теплый брус
Еще происходит производство теплого бруса. В этом случае есть один нюанс – внутренние ламели заменяются экструдированным пенополистиролом.
Использование теплого бруса для строительства стен дома
Некоторые обыватели, планирующие строительство дома, полагают, что целесообразнее заниматься производством профилированной древесины своими руками. Это актуально только в том случае, если будет строиться крупногабаритное сооружение, площадь которого составляет более 250 м2. Дело в том, что для производства таких изделий потребуется специальное оборудование. Его стоимость окупится, если будет изготовлено большое количество материала. Если все-таки есть твердое решение заняться самостоятельным производством этого вида древесины, то следует приобрести или арендовать станок, обладающий следующими функциями:
- возделывание материала многопильным способом, т. е. обрабатываются одновременно все четыре стороны бревна;
- строгание, шлифование и профилирование материала;
- изготовления чаш различных разновидностей.
Без станка при производстве можно и обойтись, если имеется строганная древесина. В этом случае из строганного бруса сделать необходимые изделия можно с помощью циркулярной пилы или фрезы. Этими инструментами можно легко выполнить замковые соединения, характерные для профилированного бруса.
Преимущества и недостатки
Профилированный брус имеет множество преимуществ перед другими материалами:
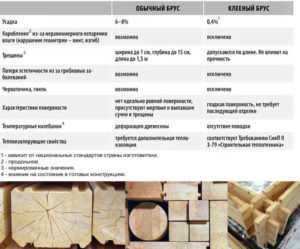
Сравнительные характеристики цельного и клееного бруса
- привлекательный внешний вид изделий;
- экологичность – он не причиняет вред здоровью человека;
- низкая теплопроводность, если использовать такой материал при строительстве, то внутри помещения всегда будет тепло;
- низкая стоимость, которая в несколько раз меньше, чем цена на другие изделия из необработанной древесины;
- небольшое расходование материала при возведении конструкции;
- брусья пропускают воздух, что обеспечивают низкую влажность внутри помещения.
Помимо достоинств, у профилированного бруса имеются и недостатки.
Если изделие при производстве плохо просушено, и оно было установлено в основании конструкции, то через какое-то время произойдет ее проседание, что вызовет необходимость ремонта и дополнительных затрат.
Стены получаются очень тонкими, и из-за этого в зимний период внутри конструкции может быть холодно, поэтому использование профилированного бруса при строительстве жилого дома предполагает дополнительно утепление стен.
Материал обладает повышенной степенью возгораемости, что вызывает необходимость его обработки специальным составом, препятствующим возникновение пожара.
После возведения конструкции будет невозможно сделать перепланировку или пристройку.
Правила выбора профилированного элемента
Дом из профилированного бруса
Чтобы избежать проблем с постройкой, нужно выбирать только качественные строительные материалы. Специалисты рекомендуют приобретать профилированный брус у производителя. В этом случае можно познакомиться с процессом производства и посмотреть на уже воздвигнутые сооружения.
Кроме того, у производителя есть возможность заказать изделия с нужными габаритами. Поскольку при покупке заключается соответствующий договор, то при обнаружении дефектом можно будет предъявить претензию продавцу, вернуть товар и получить обратно свои деньги или обменять изделия на аналогичные, но без недостатков.
При выборе производителя следует обратить внимание на месторасположения завода и проверить всю документацию. Должны иметься сертификаты качества, соответствующие разрешения и лицензии. Рекомендуется ознакомиться с отзывами о производстве в интернете.
Профилированный брус – это материал, упрощающий возведение помещений и сокращающий время его усадки. Он обладает многими положительными характеристиками, поэтому на сегодняшний день пользуется огромным спросом у застройщиков.
Видео: Производство бруса
promzn.ru
Линия изготовления клееных деревянных конструкций (стеновой брус прямолинейная балка). Производительность 6000 куб.м в год.
« назад
ОПИСАНИЕ ЛИНИИ.
Линия клееного конструкционного бруса производительностью 6000 куб.м. готовой продукции в год (при односменной работе). Линия является бюджетным вариантом высокопроизводительных линий производства КДК (клееных деревянных конструкций), предлагаемых нашей компанией.
Линия является полностью механизированной. В комплект включены новейшие запатентованные технологические единицы оборудования: четырехсторонний строгальный станок, вертикальный пресс с механизмом загрузки и т.д.
СХЕМА ЛИНИИ.
СПЕЦИФИКАЦИЯ ОБОРУДОВАНИЯ.
№ поз. | Наименование |
---|---|
3 | Неприводной транспортер длина — 6500 мм ширина — 500 мм высота — 800 мм диаметр роликов — 60…89 мм дистанция между роликами — 600 мм |
4 | Строгальный станок (импортный б/у после капремонта). Предназначен для чернового строгания заготовок перед линиями сращивания или калибровки заготовок после линии сращивания. |
5 | Приводной транспортер длина — 6500 мм ширина — 500 мм высота — 800 мм диаметр роликов — 60…89 мм дистанция между роликами — 500 мм скорость подачи — 30…120 м/мин установленная мощность — 0,37…1,1 кВт |
6 | Поперечный транспортер длина — 6500 мм ширина — 6000 мм высота — 800 мм шаг цепи — 19,05 мм количество транспортирующих секций — 5 скорость подачи — 0…40 м/мин установленная мощность — 0,75 кВт |
7 | Рольганг разметки дефектов, имеет разметочный стол, пневмосбрасыватель и подающий транспортер длина — 6500 мм ширина — 500 мм высота — 800 мм диаметр роликов — 60…89 мм дистанция между роликами — 500 мм скорость подачи — 30…120 м/мин Давление в пневмосистеме — 6 бар установленная мощность — 0,37…1,1 кВт |
8 | Полуавтоматическая торцовка |
9 | Приводной транспортер |
10 | Поперечный транспортер длина — 2500 мм ширина — 3000 мм высота — 800 мм шаг цепи — 19,05 мм количество транспортирующих секций — 5 скорость подачи — 0…40 м/мин установленная мощность — 0,75 кВт |
12 | Линия сращивания ламелей Состав линии: Рольганг для ручного формирования пачки длина — 3000 мм ширина — 550 мм ширина пачки ламелей — 500 мм высота — 800 мм Двусторонний полуавтоматический шипорезный станок Max. размер зашипованного пиломатериала 100×250×3000 мм ширина шипорезной каретки 500 мм Скорость подачи шипорезной каретки до 10 м/мин Привод подачи шипорезной каретки — электромеханический Кол-во фрезерных шпинделей – 2 шт Мощность каждого шпинделя — 22 кВт Частота вращения шпинделя 5000 об/мин Диаметр шпинделя 50 мм Рабочая высота шпинделя 250 мм 2 торцовочных пильных узла Мощность торцовочных пильных узлов=5,5 кВт Мощность привода гидростанции=4,5 кВт 2 клеенаносящих устройства Рабочая высота клеенамазки пиломатериала 250 мм Мощность клеенаносящего устройства=0,35 кВт Диаметр патрубка системы аспирации фрезерного шпинделя — 200 мм Объем воздуха при аспирации фрезерного шпинделя — 2000 куб/ч Скорость потока воздуха при аспирации фрезерного шпинделя — 25 м/с Диаметр патрубка системы аспирации торцовочного устройства — 120 мм Объем воздуха при аспирации торцовочного устройства — 1200 куб/ч Скорость потока воздуха при аспирации торцовочного устройства — 25 м/с Рольганг для ручного разобщения пачки с поперечным транспортером длина — 2500 мм ширина — 3000 мм высота — 800 мм шаг цепи — 19,05 мм количество транспортирующих секций — 5 скорость подачи — 0…40 м/мин установленная мощность — 0,75 кВт Устройство предварительной сборки шипового соединения, состоит из двух пар гидромоторов, имеющих разные угловые скорости Пресс для сращивания по длине со встроенной торцовкой длина — 8000 мм ширина — 900 мм высота — 1600 мм скорость работы — 5…10 тактов/мин Установленная мощность — 7,5 кВт Рабочее давление гидравлики — 200 бар Рабочее давление пневматики — 6 бар Усилие прессования — до 25 тонн |
14 | Линия пакетирования ламелей, предназначена для пакетирования ламелей после линии сращивания и укладки штабелей на поперечный накопитель ламелей длина — 12000 мм ширина — 650 мм высота — 1000 мм высота на входе — 800 мм ширина принимаемой ламели до — 300 мм высота формируемого штабеля — 500 мм |
15 | Буферный склад для выдержки ламелей длина — 12000 мм ширина — 6000 мм высота — 350 мм кол-во рабочих зон — 1 шаг цепи — 25.4 мм скорость подачи — 3 м/мин установленная мощность — 4.5 кВт |
16 | Механизмом разгрузки буферного склада, привод подъема и опускания электромеханический |
17 | Скоростной транспортер, служит для скоростной подачи ламелей в строгальный станок перед нанесением клея или для приема ламелей после нанесения клея и их подачи в пресс длина — 12000 мм ширина — 500 мм высота — 1500 мм высота на входе — 1400 мм диаметр роликов — 60 мм шаг роликов — 600 мм длина роликов — 400 мм скорость подачи — до 120 м/мин установленная мощность — 1.5 кВт |
18 | Строгальный станок (импортный б/у после капремонта), Двухшпиндельный станок для плоскостной обработки заготовок с двух сторон. Предназначен для чернового строгания заготовок перед линиями сращивания или калибровки заготовок после линии сращивания. Скорость подачи — 90 м/мин |
19 | Клееналивная установка (устанавливается поставщиком клея) |
20 | Приемный транспортер, служит для приема ламелей после нанесения клея и их подачи в пресс. Имеет пневматические сбрасыватели в обе стороны и откидные направляющие для подачи ламелей в пресс. длина — 12000 мм ширина — 500 мм высота — 1500 мм высота на входе — 1400 мм диаметр роликов — 60 мм шаг роликов — 600 мм длина роликов — 400 мм скорость подачи — до 250 м/мин установленная мощность — 1.5 кВт |
21 | Вертикальный пресс для склейки бруса с механизмом загрузки и выгрузки длина -12500 мм ширина — 1600 мм высота — 2600 мм рабочая длина — 5000…12000 мм рабочая ширина — до 300 мм рабочая высота — 1400 мм установленная мощность — 15 кВт |
22 | Неприводные ролики для транспортировки пачки бруса |
23 | Роликовые шины для клееного бруса длина — 1600 мм ширина — 12500 мм высота — 800 мм количество транспортирующих секций — 11 |
24 | Неприводной транспортер для клееного бруса повышенной грузоподъемности длина — 12000 мм ширина — 500 мм высота — 800 мм диаметр роликов — 80 мм дистанция между роликами — 600 мм |
25 | Строгальный станок DX-443, Четырехшпиндельный станок для плоскостной обработки заготовок с четырех сторон. Предназначен для чернового строгания заготовок перед линиями сращивания или калибровки заготовок после линии сращивания. Максимальная ширина строгания — 400 мм Максимальная высота строгания — 300 мм Диаметр шпинделей — 50 мм Диаметр патрубка системы аспирации — 200 мм Требуемый объем воздуха для аспирации (каждый шпиндель) — 3500 Куб/ч Скорость потока воздуха в системе аспирации — 25 м/с Частота вращения шпинделей — 5000 об/мин Скорость подачи материала — 5…50 м/мин Диаметр инструмента — 160…260 мм Длина станка — 2800 мм Ширина станка — 1850 мм Высота — 2300 мм Масса — 7200 кг Мощность шпинделя — 15…30 кВт |
26 | Неприводной транспортер для клееного бруса повышенной грузоподъемности длина — 12000 мм ширина — 500 мм высота — 800 мм диаметр роликов — 80 мм дистанция между роликами — 500 мм |
27 | Стол-накопитель профилированного бруса длина — 2500 мм ширина — 12500 мм высота — 800 мм |
Производство клееных деревянных конструкций (шипорезный станок):
Производство клееных деревянных конструкций (линия сращивания):
Производство клееных деревянных конструкций (калибровка ламелей, прессование):
Производство клееных деревянных конструкций (буферный склад, пресс для сращивания):
Производство клееных деревянных конструкций (строгание на станке DXL 643):
« назад
neoparma.ru