Как проходит радиографический контроль сварных соединений
При соединении металлов с помощью сварки у неопытных мастеров могут возникнуть трудности. В частности, они могут просто не увидеть всех дефектов сварного шва, которые образовались из-за ошибок сварщика. Визуального контроля недостаточно, чтобы выявить скрытые недочеты. И если в условиях домашней сварки это не критично, то на крупном производстве бракованные изделия лишают прибыли.
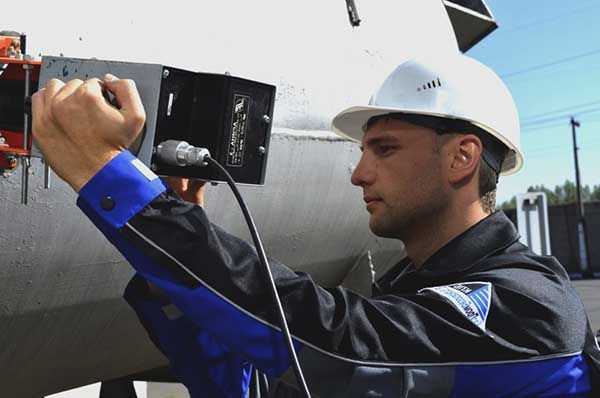
Существует множество видов контроля сварных швов. От визуального, когда сварщик просто осматривает шов на предмет видимых дефектов, до передовых способов, для которых необходимо специальное оборудование. Об одном из таких способов мы и хотим вам рассказать. В этой статье вы узнаете, что такое радиографический контроль сварных соединений и какова его методика.
Содержание статьи
Общая информация
Радиографический метод контроля сварных соединений (также рентгенография, рентгеноскопия, рентгенографический контроль) — метод контроля качества с применением рентгеновских лучей. Специальный аппарат устанавливает на место сварного шва. Здесь все по аналогии с рентген аппаратом для снимков костей человека. Рентгеновские лучи пронизывают металл и в случае обнаружения внутренних дефектов легко выходят наружу. Ну а если структура шва плотная и не имеет дефектов, то луч просто не пройдет.
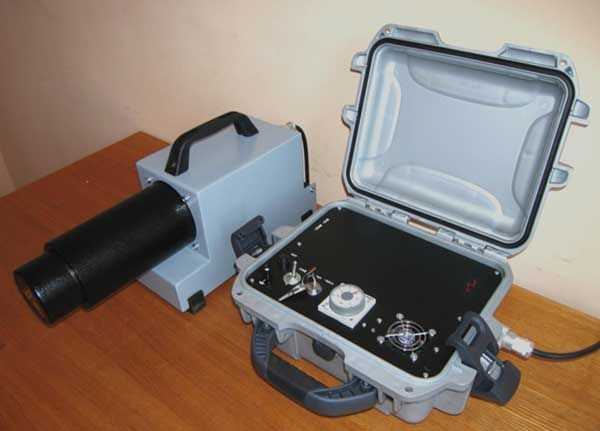
Специальное устройство регистрирует прохождение лучей и делает снимок. На снимке без проблем можно обнаружить наличие дефектов, их размеры и точное расположение. Рентгеновский контроль сварных соединений — это один из наиболее точных методов контроля качества швов. Его часто используют при проверке трубопровода, ответственных изделий, металлоконструкций, к которым предъявлены повышенные требования качества. Особенно заметна популярность радиографического контроля в строительной сфере.
Принцип работы
«Сердцем» рентгеновского аппарата является излучатель, который генерирует и выпускает лучи. Излучатель представляет собой вакуумный сосуд, который содержит анод, катод и его накал. Все эти частицы заряжены и являются электродами. Во время их сильного ускорения как раз и образуются рентгеновские лучи. Это простейшее объяснение.
Читайте также: СНИП и контроль качества
Для интересующихся объясним подробнее. Катод испускает электроны, которые ускоряются от электрического потенциала, образующегося между анодом и катодом. В этот момент рентгеновские лучи уже начинают образовываться, но их недостаточно. Однако, лучи все же сталкиваются с анодом и начинается их торможение. Из-за этого лучи начинают генерироваться сильнее. В тот же момент из-за столкновения начинают появляться электроны анода. Так образуются лучи, достаточные для формирования полноценного излучения.
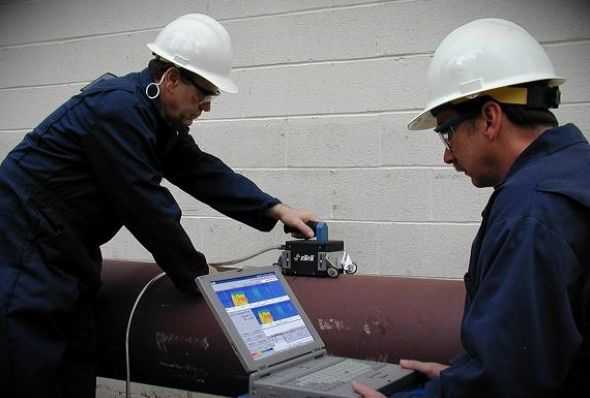
Далее лучи выходят и пускаются в заданном направлении. Лучи сталкиваются с металлом и в случае наличия дефектов проходят сквозь него. Либо поглощаются металлом, если дефектов нет. Здесь нужно уточнить, что лучи поглощаются не полностью, некоторые частицы все же остаются. Именно они попадают на пленку и позволяют сделать снимок. На снимке фиксируется количество лучей, прошедших сквозь металл. Если дефектов много, то и лучей тоже будет много. За счет такой особенности и получается узнать размер дефекта и его расположение.
Особенности рентгеновских лучей
Чтобы лучше понять суть рентгенографии нужно разобраться с особенностями самих лучей, благодаря которым как раз и возможен контроль. Лучи обладают свойствами, которые позволяют им проходить сквозь материалы. В нашем случае металл. Чем выше плотность металла, тем хуже проходят лучи. И, соответственно, чем ниже плотность металла, тем лучше они проходят. Здесь все просто: наименьшая плотность присутствует как раз в местах с дефектами.
Поэтому лучи беспрепятственно проходят сквозь металл и это фиксируется на специальном устройстве. Ну а если у шва нет дефектов и структура плотная, то лучи не пройдут, а просто поглотятся металлом. И чем выше плотность, тем больше степень поглощения.
Что касается снимков, то здесь тоже все просто. Существуют химические вещества, которые при контакте с рентгеновским излучением начинают буквально «светиться». Такими веществами покрывается светочувствительная часть фотопластинки, на которой затем появится снимок. Этот принцип является основой для создания рентгеновских снимков сварных швов.
Теперь о некоторых других особенностях. Наверняка вы слышали, что рентгеновское излучение в большом количестве может пагубно влиять на здоровье человека. Это правда. Лучи легко воздействуют на ткани и клетки, облучая их за считанные минуты. В больших дозах это может привести к лучевой болезни. Так что нужно соблюдать осторожность, если вы используете радиографический метод контроля сварных соединений.
Еще один интересный факт: благодаря излучения привычный нам воздух способен проводить электрический ток. Это связано с тем, что рентгеновские лучи ионизируют воздух и расщепляют его частицы на небольшие составляющие, которые в свою очередь имеют электрический заряд.
Плюсы и минусы метода
Плюсы:
- Рентгенографический контроль сварных соединений — один из самых достоверных методов контроля качества швов.
- С помощью этого метода за считанные минуты выявляются дефекты любого уровня.
- Есть возможность определить точный размер и расположение дефекта.
- Контроль занимает мало времени и требует только рентген-аппарат.
- Возможен контроль сварных соединений трубопроводов и любых других сложных систем.
Минусы:
- Качество контроля напрямую зависит от настройки рентген-аппарата.
- Современные рентген-аппараты стоят дорого, особенно компактные модели, которые так популярны в строительной сфере.
- Для работы понадобится специальная светочувствительная пленка, которая также стоит недешево.
- Этот метод контроля сварных швов сопряжен с опасностью для здоровья.
Методика контроля
Методика радиографического контроля проста и во многом схожа с обычной рентгенографией, которую мы делаем в поликлинике. Сначала контролер или ответственное лицо устанавливает необходимые настройки аппарата, учитывая плотность металла. Помните, что именно плотность влияет на конечный результат.
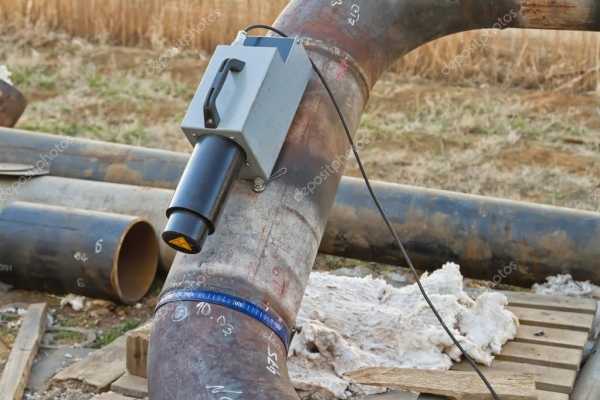
Далее подготавливается сварное соединение. Нужно удалить шлак, обработать валик шва и зачистить металл. Затем либо деталь помещается в аппарат (если контроль стационарный в отдельной комнате), либо аппарат помещается на соединение (если контроль выездной и используются компактные модели). Шов должен находиться между излучателем и пленкой. Излучатель включается, лучи проходят сквозь металл и попадают на пленку. Мы получаем снимок, на котором видны все дефекты. Теперь можно выключить аппарат и подождать 10-20 секунд. Затем деталь извлекается из ренигенографа (или рентгенограф снимается с металла). Снимки отдаются специалисту для их изучения или остаются у контролера.
Техника безопасности
Как мы уже говорили, данный метод контроля сопряжен с некоторой опасностью для здоровья. Не нужно пренебрегать этим, думая, что небольшие дозы радиации не повлияют на вас. Если вы работаете контролером и постоянно имеете дело с рентгенографией, то соблюдайте следующие рекомендации.
Во-первых, самое главное правило при работе с рентгеном — нужно экранировать прибор. Это не даст лучам распространяться за пределы зоны контроля. Для этих целей можно использовать металлические листы. Если вы работаете в помещении, то его стены также должны быть оборудованы экранирующими пластинами. Так лучи не будут представлять опасности для других работников, находящихся на объекте или в цеху.
Во-вторых, постарайтесь как можно меньше времени проводить рядом с аппаратом. Если вы проводите радиографический метод контроля сварных соединений на улице, то лучше отойдите в сторону. Если вы работаете в помещении, то постарайтесь сократить время своего пребывания в нем. Также на вас должны быть средства индивидуальной защиты. В помещении и рядом с аппаратом на улице не должны проходить посторонние работники.
В-третьих, перед началом работ нужно убедиться, что аппарат работает исправно и все настройки выставлены правильно. Большинство несчастных случаев связаны именно с неправильной настройкой или неисправностью рентгена.
В-четвертых, следите за дозой лучей, которые вы получаете при каждом контроле. Да, небольшие дозы не вредны для здоровья, но они обладают свойством накапливания и в конечном итоге могут стать причиной серьезных заболеваний. Следите, чтобы полученная вами доза радиации успевала выводиться из организма до начала следующего контроля. Чтобы узнать дозу можно использовать дозиметр.
В-пятых, не забывайте, что из-за лучей воздух может сильно ионизироваться, что приведет к образованию электрического тока. Следите за допустимым значением ионизации воздуха, особенно, если работаете в закрытом помещении.
Вместо заключения
Вот и все, что мы хотели рассказать вам о рентгенографическом методе контроля. Это один из самых точных и достоверных способов выявить скрытые от глаз дефекты. С его помощью можно провести контроль как на производстве, так и на выезде, поскольку производители предлагают компактные модели. Их легко можно взять с собой и выполнять контроль даже под открытым небом.
Конечно, радиографический контроль сварных соединений требует определенных знаний и опыта, чтобы читать снимки. Но вместе с тем вы получаете навык, который поможет вам безошибочно выявлять дефекты даже в идеальных на вид швах. А вы использовали в работе рентгенограф? Поделитесь в комментариях своим опытом контроля качества швов с помощью данного прибора, это будет полезно для наших читателей. Желаем удачи в работе!
svarkaed.ru
Сварной шов и методы проведения радиографического контроля сварных соединений
Производство и установка сварочных конструкций осуществляется в строгом соответствии со строительными нормами, техническими условиями и правилами, обозначенными в ГОСТе. Все существующие сегодня способы контролировать сварной шов, а также другие металлические изделия дают возможность выявлять всевозможные дефекты, которые можно повстречать на практике сварки.
Соответствующие методы контроля применяются в зависимости от ответственности сварных швов и конструкций. Самыми целесообразными комплексными испытаниями на сегодняшний день считают те, что включают целый ряд параллельно использующихся методов контроля, например, ультразвуковой контроль сварных швов и радиографическая дефектоскопия.
Радиографический контроль и цели его проведения
Рентгеновская дефектоскопия или же радиографический контроль сварочных швов, соединений чаще всего применяется с целью проверки уровня качества магистральных газо- и нефтепроводов, технологических трубопроводов, промышленных трубопроводов, металлоконструкций, а также композитных материалов и технологического оборудования в самых разных отраслях промышленности.
Рентгенографический контроль производят с целью выявления поверхностных и внутренних дефектов, к примеру, шлаковых включений, газовых пор, микротрещин, подрезов и шлаковых включений.
Наряду с другими физическими методами контроля радиографический выступает одним из самых эффективных и надёжных средств выявления всевозможных дефектов. Выявленные дефекты: искусственные включения, нарушения геометрии
Основан данный метод дефектоскопии на различном поглощении рентгеновских лучей материалами.
Такие дефекты, как включения инородных материалов, различные трещины, поры и шлаки проводят к ослаблению в той или иной степени рентгеновских лучей. Регистрация интенсивности лучей при помощи рентгенографического контроля помогает определить не только наличие, а и расположение разнообразных неоднородностей проверяемого материала.
Данный метод показал свой высокий уровень эффективности на практике в процессе контроля качества, которому подвергаются сварочные швы и соединения.
Преимущества рентгенографического метода:
- Максимально точная локализация даже самых мельчайших дефектов;
- Молниеносное обнаружение дефектов сварочных соединений и швов;
- Возможность произведения чёткой оценки микроструктуры: величины вогнутости, выпуклости корня шва даже в самых недоступных местах для внешнего осмотра.
Радиографическая дефектоскопия, контролирующая сварочные конструкции также даёт возможность обнаруживать внутренние дефекты в виде пор, непроваров, вольфрамовых, шлаковых, окисных и других включений, подрезов и трещин, усадочных раковин и прочего.
Согласно общим положениям ГОСТа 7512 82 Установки неразрушающего контроль
Радиографический контроль не используют при:
- Наличии непроваров и трещин, величина раскрытия которых меньше стандартных значений, а плоскость раскрытия не соответствует направлению просвечивания;
- Любых несплошностях и включениях, имеющих размер в направлении просвечивания меньше удвоенной чувствительности контроля;
- Всяческих несплошностях и включениях в случае, когда их изображения на снимках совершенно не соответствуют изображениям построенных деталей, резких перепадов трещин металла, который просвечивается, а также острых углов.
Наиболее достоверный способ проконтролировать основной металл и сварной шов – провести дефектоскопию с рентгеновским просвечиванием металлов. Только так можно определить и вид, и характер обнаруженных дефектов, с высокой точностью определить их месторасположение и заархивировать результаты контроля в конечном итоге.
Принцип работы радиографической установки
Радиографический контроль относится, в первую очередь, к системам цифровой дефектоскопии радиационного типа. Радиационное изображение в данных системах превращается в цифровой массив (изображение), который впоследствии подвергается разным видам цифровой обработки, а затем выводится на монитор персонального компьютера в виде полутонового изображения. К слову, нередко металлография (классически метод) использует для исследования, а также контроля металлических материалов радиометрические установки.
Поскольку метод базируется на принципе измерения рентгеновского излучения или гамма-излучения, которое проходит сквозь материал контролируемого объекта, детектором для контроля выступает фотодиод со сцинтиллятором, наклеенным на него. Сцинтиллятор под воздействием излучений испускает видимый свет, выход которого пропорционален квантовой энергии. В конечном итоге исходящее световое излучение вызывает ток внутри фотодиода.
Таким образом, детектор преобразовывает проходящее сквозь контролируемое изделие излучение в электрические сигналы, величина которых прямо пропорциональна интенсивности лучей гамма.
Приёмник излучения рентгена – это линейка сцинтилляционных детекторов, которые по отдельности оснащены собственными усилителями, образующими единый независимый канал с детекторами. Количество детекторов в линейке строго зависит от необходимой ширины контролируемой зоны. Все каналы детекторного блока опрашиваются по очереди, а с помощью АЦП (аналого-цифровой преобразователь) все полученные сигналы приобретают цифровой вид. Впоследствии полученный в ходе опроса детекторных блоков цифровой массив передаётся на ПК.
Посредством перемещения детекторных блоков по отношению к контролируемому сварочному соединению получают непрерывно считываемый массив данных, записывающийся в память ПК с целью последующего и более детального исследования, архивирования. Для оперативной оценки качества в лаборатории контроля в реальном времени эти данные выводятся в виде полутонового изображения прямо на монитор.
Главные требования к рентгеновским аппаратам
В процессе радиометрическом методе флуктуации интенсивности проходящего сквозь объект энергетического спектра не оказывают никакого воздействия на чувствительность контроля, так как изображение, фиксируемое на пленке рентгена изображение определяют посредством интегральной дозы излучения в период экспозиции.
Именно поэтому во время радиографического контроля разрешается применять рентгеновские аппараты любого существующего типа. В большинстве случаев изготовители рентген-аппаратов не приводят никаких данных о флуктуации интенсивности излучений, поскольку данная величина не является критичной.
Стоит отметить, что радиометрия представляет собой метод измерения при построчном сборе данных в режиме реального времени.
Для сканирования одной строки могут потребоваться десятые доли секунды. Исходя из этого рентген аппарату предъявляются 2 основных требования, а именно:
1) Плотность потока гамма-излучения, проходящего сквозь контролируемую толщину проверяемого объекта, должна быть настолько велика, чтобы этого времени было достаточно для регистрации изменения толщины объекта вдоль просканированной области
2) Интенсивность гамма-излучения обязательно должна быть постоянной
Таким образом, для качественного радиометрического контроля необходимы высокостабильные источники ионизирующего излучения, имеющего максимально возможную плотность лучевого потока, а также максимальный энергетический спектр.
С целью сравнения современных рентгеновских аппаратов панорамного типа с постоянным потенциалом разработан специальный переносной прибор, обеспечивающий проведение измерений интенсивности излучения в полевых условиях.
Виды радиометрических аппаратов:
- Аппараты, которые обладают фиксированной частотой флуктуаций интенсивности гамма-излучения. Регулярные перемены интенсивности рентгеновского излучения создают на изображении поперечные полосы. При этом среднеквадратичные отклонения в интенсивности излучения в несколько раз превышают статистические шумы. Возможно ослабление данных флуктуаций программным способом. С этой целью радиометрическую установку оснащают программами, определяющими спектральную долю флуктуаций для каждого аппарата. Подобные рентгеновские аппараты считаются условно применимыми для радиометрического контроля сварочных швов и соединений.
- Рентгеновские аппараты с постоянным потенциалом, которые обладают высокочастотными флуктуациями, случайными во времени. У таких приборов величина отклонений интенсивности гамма-излучения более одного процента. В радиометрическом контроле сварочных конструкций не рекомендуется применять такие устройства.
- Идеальным вариантом является оборудование, стабильность излучения которого превышает 0,5 процентов, а частота флуктуаций имеет показатель не более 0,1 Гц. Низкочастотные изменения интенсивности излучения столь незначительной величины можно легко устранить на изображении программным способом.
Специалисты рекомендуют рентгеновский программный аппарат модели РПД200П, который после соответствующей модификации системы питания показал, что может успешно применяться в процессе проведения радиометрического контроля высокого качества.
Развивающаяся стремительными темпами вычислительная и электронная техника открывает широкие возможности для удешевления и усовершенствования радиометрической аппаратуры.
Проведённые с помощью аппарата РПД200П панорамного типа измерения доказывают, что на базе оборудования этого типа можно создать целые радиометрические комплексы.
elsvarkin.ru
Радиографический контроль сварных соединений: методы, дефекты, видео
Возможностью применять радиографический метод контроля сварных соединений мы обязаны немецкому физику Вильгельму Рентгену. В 1895 году он открыл электромагнитное излучение на коротких волнах. Эти лучи были названы в честь него рентгеновскими.
Первое широкое применение рентгеновские лучи нашли в медицине. Метод позволил спасти много человеческих жизней. В свою очередь, рентгеновский контроль сварных соединений помогает спасти сварные швы от образовавшихся в процессе сварки дефектов. Метод рентгеновской дефектоскопии позволяет обнаружить в сварных соединениях трещины, раковины, пустоты, полости, инородные включения.
Радиографический контроль сварных соединений это — это метод контроля, позволяющий обнаружить имеющиеся внутри сварных швов погрешности, основанный на изменении характеристик рентгеновских лучей при столкновении с ними. Такой контроль возможен благодаря способности этих волн проникать вглубь металла достаточно глубоко. Контроль этим методом проводится согласно ГОСТу 75-12, в котором перечислены все контролируемые этим способом дефекты.
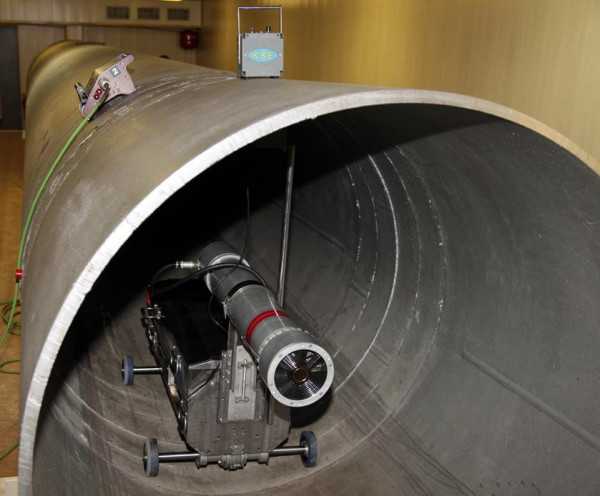
Область применения
После окончания процесса сваривания и остывания конструкции необходимо оценить качество работы и при обнаружении недостатков принять меры. Контроль начинается с визуального осмотра. При наличии дефектов, имеющихся внутри шва необходимо прибегнуть к другим методам поиска. Они должны относиться к категории неразрушаемых. Не все обладают необходимой точностью. Рентгенография сварных соединений является одним из неразрушаемых способов, дающим точную информацию о состоянии внутри сварного шва.
В дефектоскопии используется возможность рентгеновских лучей проникнуть вглубь на значительное расстояние благодаря тому, что их длина волны является небольшой. При сварке могут возникнуть ситуации, когда выбран неправильный режим или в сварочную ванну попали посторонние предметы. Образование невидимого брака понизит прочность и надежность всей конструкции, которая сможет выдержать меньшие нагрузки, чем планировалось.
Радиографический контроль сварных швов требует наличия специального оборудования. Затраты на него целесообразны в тех случаях, когда требования к характеристикам соединений высокие. Другой вариант — контроль конструкций, где другие методы применять затруднительно или невозможно. Примером может служить рентгенографический контроль сварных соединений трубопроводов.
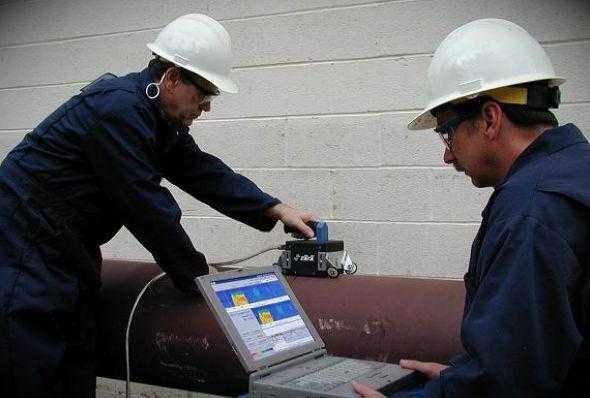
Существуют лаборатории, специализирующиеся на контроле сварных соединений, где имеется все необходимое оборудование, и работают грамотные профессионалы. При желании контроль можно провести самостоятельно, овладев необходимыми навыками. Имеется возможность взять для этого прибор в аренду. Большой популярностью пользуются портативные аппараты. Они применяются как для контроля трубопроводов, так и для профильных и листовых соединений. Стационарные аппараты могут быть спроектированы индивидуально для решения конкретных задач.
Радиографический контроль сварных соединений трубопроводов проводится согласно отраслевому нормативному документу ОСТ 36-59, где указаны все требования к свариванию этих конструкций. В нем, в частности, сказано, что все данные по проведенному контролю заносятся в специальный журнал и хранятся в течение 10 лет после начала эксплуатации объекта.
Принцип работы
Рентгенография основана на свойстве лучей проникать внутрь материалов, в том числе металлов. Эта способность понижается с увеличением плотности металла и увеличивается с понижением плотности. Поскольку в местах с пустотами и трещинами плотность становится меньше, это сразу регистрируется прибором. При отсутствии дефектов структура металла остается стабильно плотной, и рентгеновские лучи поглотятся материалом. Чем выше плотность, тем степень поглощения будет выше.
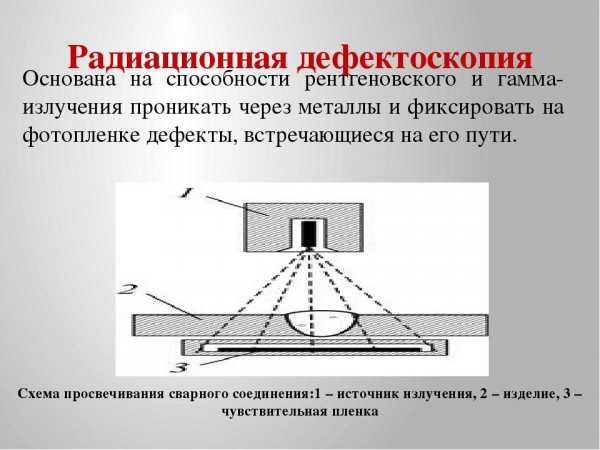
Основным элементом аппарата для рентгеноскопии сварных швов служит излучатель, представляющий собой рентгеновские трубки. Его функция — генерировать лучи и выпускать их. Конструктивно излучатель представляет вакуумный сосуд. В нем имеются анод и катод, между которыми образуется электрический потенциал. При сильном ускорении электронов появляются рентгеновские лучи, и задается направление их выхода.
Лучи, прошедшие сквозь металл, падают на специальную светочувствительную пленку. На ней остается отпечаток, по которому можно судить, что находится внутри материала. Полную картину покажет расшифровка рентгеновских снимков сварных соединений. При желании или необходимости получать сведения постоянно, используют сцинтилляторы. Это дает возможность выводить изображение на монитор.
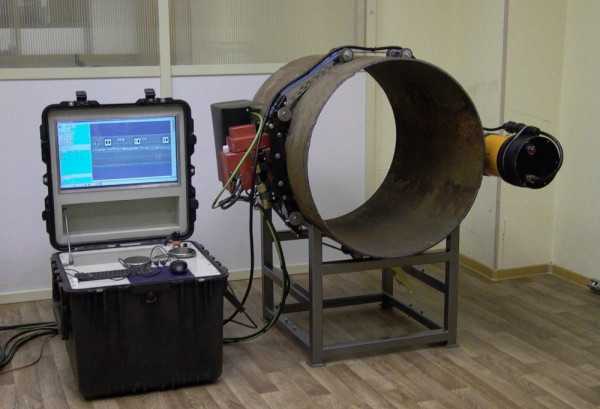
Имеется возможность сделать фотографии, получив рентгенограмму. На рентгенограмме будет иметься негативное изображение соединения. При наличии включений или, наоборот, пустот появятся их очертания другого цвета. Полученную рентгенограмму следует сравнить с типовой рентгенограммой для этого типа свариваемых деталей. Метод позволяет точно и оперативно оценить состояние сварного шва.
Подготовка к контролю
Перед началом процесса следует произвести подготовительные операции. Части будущего соединения внимательно осматривают. При наличии на них загрязнений и шлаков необходимо тщательно их очистить и обезжирить растворителем или спиртом. Это делается для того, чтобы наружные дефекты при просвечивании не вносили искажение в окончательный результат.
Пленки заряжают в соответствующие кассеты. Все соединения разделяют на отдельные интервалы и маркируют их. Это делается для того, чтобы можно было точно определить, какой снимок относиться к конкретному участку свариваемого шва. В том же порядке маркируют кассеты и пленки. Если шов имеет большую протяженность, возможен выборочный рентген-контроль сварных швов.
Также необходимо подготовить оборудование, предназначенное для радиографии сварных швов. Вначале необходимо выбрать подходящий источник излучения. Критериями являются чувствительность, толщина металла и его плотность, конфигурация деталей, требуемая производительность. К примеру, для радиографического контроля сварных соединений, где возможны дефекты, имеющие большой размер, подходят изотопы, обладающие высокой энергией. Это обеспечит небольшое время просвечивания. Выбор пленки обусловлен толщиной металла и его плотностью. На приборах выставляют оптимальные режимы.
Методика процесса
Рентгенография сварных швов проходит несколько этапов:
- Выбрать источник излучения.
- Выбрать подходящий тип пленки.
- Установить на оборудовании оптимальные режимы.
- Поместить аппарат внутри изделия или снаружи и включить его.
- Начать просвечивание сварного шва.
- Вынуть пленку и проявить ее.
- Произвести расшифровку.
- Занести результаты в журнал установленной формы.
Выбранную кассету закрепляют на изделии. Для получения хорошей резкости изображения и определения достоверного размера дефекта на приборе следует установить эталон чувствительности. Эталон должен быть изготовлен из материала, характеристики которого приближены к характеристикам свариваемого металла.
В ГОСТе 7512 указаны три предпочтительных типов эталонов, применяемых для рентгена сварных швов:
- Канавочные. Пластина, имеющая шесть канавок. Ширина у них одинаковая, а глубина разная.
- Проволочные. Имеет семь проволок.
- Пластинчатые. Пластина, имеющая отверстия нужных форм и размеров.
Проверяемые изделия можно разместить по отношению к аппарату двумя способами. Если они небольшие и могут поместиться в помещении, соединения помещаются внутри стационарного аппарата. При выездном контроле применяют компактные модели оборудования и устанавливают их на изделие.
Чтобы осуществить рентгенографический контроль сварных соединений шов следует размещать строго между излучателем и светочувствительной пленкой. После включения излучателя рентгеновские лучи начнут проходить через металл и попадать на пленку. Через несколько секунд снимок будет готов. Аппарат выключают. Кассету с пленкой вынимают и отдают для обработки и расшифровывания. После того, как будет понятно, что результат получен, аппарат можно снять с изделия или извлечь из него. Иначе, необходимо сделать повторный контроль.
Расшифровка
Расшифровку рентгенограмм осуществляют в затененном помещении на негатоскопе. Он представляет собой устройство, назначением которого является просмотр на просвет радиографических снимков, в том числе рентгенограмм. В негатоскопе предусмотрена возможность регулировки яркости освещения. При слишком большом его значении мелкие дефекты могут быть пропущены.
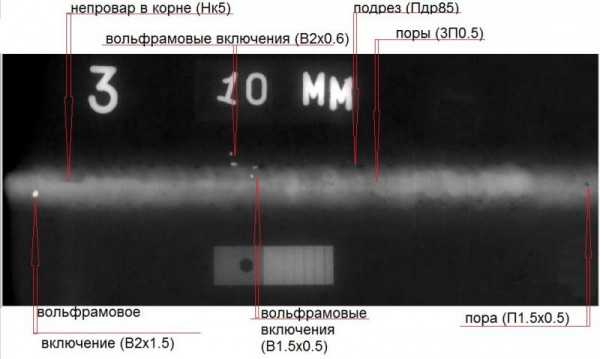
После расшифровки составляется заключение. Перед тем, как прибегнуть к этому методу, необходимо узнать, какие дефекты сварного шва выявляются с помощью радиографического контроля. К ним относятся:
- подрезы;
- непровары;
- трещины;
- поры;
- инородные включения;
- шлаки.
Помимо этого, можно оценить величину вогнутости и выпуклости в местах, где визуальный осмотр невозможен. При записи результатов используются сокращения. Так, «Т» означает трещину, «Н» — непровар, «П» — пору, «Ш» — шлак, «В» — включение вольфрама, Пдр» — подрез. Рядом с буквами ставят размеры дефекта. Учитывается также характер распределения.
По этому признаку недостатки делятся на группы:
- Отдельные.
- Цепочки. На одной линии более трех дефектов.
- Скопления. Расположение в одном месте не менее трех дефектов.
Размер дефекта обозначается в миллиметрах.
Преимущества
К достоинствам метода относятся:
- достоверность;
- быстрота контроля;
- определение места расположения;
- оценка размера;
- выявление скрытых недостатков;
- широкая область применения.
К недостаткам относится высокая цена оборудования, и необходимость изучения правил его использования.
Безопасность
При всех своих достоинствах метод является потенциально опасным для здоровья. Поэтому необходимо выполнять экранирование прибора. Контролер не должен находиться без необходимости в зоне облучения. Доступ туда посторонним лицам должен быть запрещен. Для этого следует вывесить предупреждающие знаки.
При работе в помещении его стены надо покрыть экранирующими пластинами. Контролер должен быть обеспечен комплектом защитной одежды. Перед началом процесса необходимо проверить исправность оборудования.
Интересное видео
osvarka.com
На главную | База 1 | База 2 | База 3 |
Поиск по реквизитамПоиск по номеру документаПоиск по названию документаПоиск по тексту документа |
Искать все виды документовДокументы неопределённого видаISOАвиационные правилаАльбомАпелляционное определениеАТКАТК-РЭАТПЭАТРВИВМРВМУВНВНиРВНКРВНМДВНПВНПБВНТМ/МЧМ СССРВНТПВНТП/МПСВНЭВОМВПНРМВППБВРДВРДСВременное положениеВременное руководствоВременные методические рекомендацииВременные нормативыВременные рекомендацииВременные указанияВременный порядокВрТЕРВрТЕРрВрТЭСНВрТЭСНрВСНВСН АСВСН ВКВСН-АПКВСПВСТПВТУВТУ МММПВТУ НКММПВУП СНЭВУППВУТПВыпускГКИНПГКИНП (ОНТА)ГНГОСТГОСТ CEN/TRГОСТ CISPRГОСТ ENГОСТ EN ISOГОСТ EN/TSГОСТ IECГОСТ IEC/PASГОСТ IEC/TRГОСТ IEC/TSГОСТ ISOГОСТ ISO GuideГОСТ ISO/DISГОСТ ISO/HL7ГОСТ ISO/IECГОСТ ISO/IEC GuideГОСТ ISO/TRГОСТ ISO/TSГОСТ OIML RГОСТ ЕНГОСТ ИСОГОСТ ИСО/МЭКГОСТ ИСО/ТОГОСТ ИСО/ТСГОСТ МЭКГОСТ РГОСТ Р ЕНГОСТ Р ЕН ИСОГОСТ Р ИСОГОСТ Р ИСО/HL7ГОСТ Р ИСО/АСТМГОСТ Р ИСО/МЭКГОСТ Р ИСО/МЭК МФСГОСТ Р ИСО/МЭК ТОГОСТ Р ИСО/ТОГОСТ Р ИСО/ТСГОСТ Р ИСО/ТУГОСТ Р МЭКГОСТ Р МЭК/ТОГОСТ Р МЭК/ТСГОСТ ЭД1ГСНГСНрГСССДГЭСНГЭСНмГЭСНмрГЭСНмтГЭСНпГЭСНПиТЕРГЭСНПиТЕРрГЭСНрГЭСНсДИДиОРДирективное письмоДоговорДополнение к ВСНДополнение к РНиПДСЕКЕНВиРЕНВиР-ПЕНиРЕСДЗемЕТКСЖНМЗаключениеЗаконЗаконопроектЗональный типовой проектИИБТВИДИКИМИНИнструктивное письмоИнструкцияИнструкция НСАМИнформационно-методическое письмоИнформационно-технический сборникИнформационное письмоИнформацияИОТИРИСОИСО/TRИТНИТОсИТПИТСИЭСНИЭСНиЕР Республика КарелияККарта трудового процессаКарта-нарядКаталогКаталог-справочникККТКОКодексКОТКПОКСИКТКТПММ-МВИМВИМВНМВРМГСНМДМДКМДСМеждународные стандартыМетодикаМетодика НСАММетодические рекомендацииМетодические рекомендации к СПМетодические указанияМетодический документМетодическое пособиеМетодическое руководствоМИМИ БГЕИМИ УЯВИМИГКМММНМОДНМонтажные чертежиМос МУМосМРМосСанПинМППБМРМРДСМРОМРРМРТУМСанПиНМСНМСПМТМУМУ ОТ РММУКМЭКННАС ГАНБ ЖТНВННГЭАНДНДПНиТУНКНормыНормы времениНПНПБНПРМНРНРБНСПНТПНТП АПКНТП ЭППНТПДНТПСНТСНЦКРНЦСОДМОДНОЕРЖОЕРЖкрОЕРЖмОЕРЖмрОЕРЖпОЕРЖрОКОМТРМОНОНДОНКОНТПОПВОПКП АЭСОПНРМСОРДОСГиСППиНОСНОСН-АПКОСПОССПЖОССЦЖОСТОСТ 1ОСТ 2ОСТ 34ОСТ 4ОСТ 5ОСТ ВКСОСТ КЗ СНКОСТ НКЗагОСТ НКЛесОСТ НКМОСТ НКММПОСТ НКППОСТ НКПП и НКВТОСТ НКСМОСТ НКТПОСТ5ОСТНОСЭМЖОТРОТТПП ССФЖТПБПБПРВПБЭ НППБЯПВ НППВКМПВСРПГВУПереченьПиН АЭПисьмоПМГПНАЭПНД ФПНД Ф СБПНД Ф ТПНСТПОПоложениеПорядокПособиеПособие в развитие СНиППособие к ВНТППособие к ВСНПособие к МГСНПособие к МРПособие к РДПособие к РТМПособие к СНПособие к СНиППособие к СППособие к СТОПособие по применению СППостановлениеПОТ РПОЭСНрППБППБ-АСППБ-СППБВППБОППРПРПР РСКПР СМНПравилаПрактическое пособие к СППРБ АСПрейскурантПриказПротоколПСРр Калининградской областиПТБПТЭПУГПУЭПЦСНПЭУРР ГазпромР НОПРИЗР НОСТРОЙР НОСТРОЙ/НОПР РСКР СМНР-НП СРО ССКРазъяснениеРаспоряжениеРАФРБРГРДРД БГЕИРД БТРД ГМРД НИИКраностроенияРД РОСЭКРД РСКРД РТМРД СМАРД СМНРД ЭОРД-АПКРДИРДМРДМУРДПРДСРДТПРегламентРекомендацииРекомендацияРешениеРешение коллегииРКРМРМГРМДРМКРНДРНиПРПРРТОП ТЭРС ГАРСНРСТ РСФСРРСТ РСФСР ЭД1РТРТМРТПРУРуководствоРУЭСТОП ГАРЭГА РФРЭСНрСАСанитарные нормыСанитарные правилаСанПиНСборникСборник НТД к СНиПСборники ПВРСборники РСН МОСборники РСН ПНРСборники РСН ССРСборники ценСБЦПСДАСДАЭСДОССерияСЗКСНСН-РФСНиПСНиРСНККСНОРСНПСОСоглашениеСПСП АССП АЭССправочникСправочное пособие к ВСНСправочное пособие к СНиПСправочное пособие к СПСправочное пособие к ТЕРСправочное пособие к ТЕРрСРПССНССЦСТ ССФЖТСТ СЭВСТ ЦКБАСТ-НП СРОСТАСТКСТМСТНСТН ЦЭСТОСТО 030 НОСТРОЙСТО АСЧМСТО БДПСТО ВНИИСТСТО ГазпромСТО Газпром РДСТО ГГИСТО ГУ ГГИСТО ДД ХМАОСТО ДОКТОР БЕТОНСТО МАДИСТО МВИСТО МИСТО НААГСТО НАКССТО НКССТО НОПСТО НОСТРОЙСТО НОСТРОЙ/НОПСТО РЖДСТО РосГеоСТО РОСТЕХЭКСПЕРТИЗАСТО САСТО СМКСТО ФЦССТО ЦКТИСТО-ГК «Трансстрой»СТО-НСОПБСТПСТП ВНИИГСТП НИИЭССтП РМПСУПСССУРСУСНСЦНПРТВТЕТелеграммаТелетайпограммаТематическая подборкаТЕРТЕР Алтайский крайТЕР Белгородская областьТЕР Калининградской областиТЕР Карачаево-Черкесская РеспубликаТЕР Краснодарского краяТЕР Мурманская областьТЕР Новосибирской областиТЕР Орловской областиТЕР Республика ДагестанТЕР Республика КарелияТЕР Ростовской областиТЕР Самарской областиТЕР Смоленской обл.ТЕР Ямало-Ненецкий автономный округТЕР Ярославской областиТЕРмТЕРм Алтайский крайТЕРм Белгородская областьТЕРм Воронежской областиТЕРм Калининградской областиТЕРм Карачаево-Черкесская РеспубликаТЕРм Мурманская областьТЕРм Республика ДагестанТЕРм Республика КарелияТЕРм Ямало-Ненецкий автономный округТЕРмрТЕРмр Алтайский крайТЕРмр Белгородская областьТЕРмр Карачаево-Черкесская РеспубликаТЕРмр Краснодарского краяТЕРмр Республика ДагестанТЕРмр Республика КарелияТЕРмр Ямало-Ненецкий автономный округТЕРпТЕРп Алтайский крайТЕРп Белгородская областьТЕРп Калининградской областиТЕРп Карачаево-Черкесская РеспубликаТЕРп Краснодарского краяТЕРп Республика КарелияТЕРп Ямало-Ненецкий автономный округТЕРп Ярославской областиТЕРрТЕРр Алтайский крайТЕРр Белгородская областьТЕРр Калининградской областиТЕРр Карачаево-Черкесская РеспубликаТЕРр Краснодарского краяТЕРр Новосибирской областиТЕРр Омской областиТЕРр Орловской областиТЕРр Республика ДагестанТЕРр Республика КарелияТЕРр Ростовской областиТЕРр Рязанской областиТЕРр Самарской областиТЕРр Смоленской областиТЕРр Удмуртской РеспубликиТЕРр Ульяновской областиТЕРр Ямало-Ненецкий автономный округТЕРррТЕРрр Ямало-Ненецкий автономный округТЕРс Ямало-Ненецкий автономный округТЕРтр Ямало-Ненецкий автономный округТехнический каталогТехнический регламентТехнический регламент Таможенного союзаТехнический циркулярТехнологическая инструкцияТехнологическая картаТехнологические картыТехнологический регламентТИТИ РТИ РОТиповая инструкцияТиповая технологическая инструкцияТиповое положениеТиповой проектТиповые конструкцииТиповые материалы для проектированияТиповые проектные решенияТКТКБЯТМД Санкт-ПетербургТНПБТОИТОИ-РДТПТПРТРТР АВОКТР ЕАЭСТР ТСТРДТСНТСН МУТСН ПМСТСН РКТСН ЭКТСН ЭОТСНэ и ТЕРэТССЦТССЦ Алтайский крайТССЦ Белгородская областьТССЦ Воронежской областиТССЦ Карачаево-Черкесская РеспубликаТССЦ Ямало-Ненецкий автономный округТССЦпгТССЦпг Белгородская областьТСЦТСЦ Белгородская областьТСЦ Краснодарского краяТСЦ Орловской областиТСЦ Республика ДагестанТСЦ Республика КарелияТСЦ Ростовской областиТСЦ Ульяновской областиТСЦмТСЦО Ямало-Ненецкий автономный округТСЦп Калининградской областиТСЦПГ Ямало-Ненецкий автономный округТСЦэ Калининградской областиТСЭМТСЭМ Алтайский крайТСЭМ Белгородская областьТСЭМ Карачаево-Черкесская РеспубликаТСЭМ Ямало-Ненецкий автономный округТТТТКТТПТУТУ-газТУКТЭСНиЕР Воронежской областиТЭСНиЕРм Воронежской областиТЭСНиЕРрТЭСНиТЕРэУУ-СТУказУказаниеУказанияУКНУНУОУРврУРкрУРррУРСНУСНУТП БГЕИФАПФедеральный законФедеральный стандарт оценкиФЕРФЕРмФЕРмрФЕРпФЕРрФормаФорма ИГАСНФРФСНФССЦФССЦпгФСЭМФТС ЖТЦВЦенникЦИРВЦиркулярЦПИШифрЭксплуатационный циркулярЭРД |
Показать все найденныеПоказать действующиеПоказать частично действующиеПоказать не действующиеПоказать проектыПоказать документы с неизвестным статусом |
Упорядочить по номеру документаУпорядочить по дате введения |
files.stroyinf.ru
Радиографический контроль
Радиографический контроль (далее — РК) относится к неразрушающему контролю (НК) при проверке качества изделий на отсутствие скрытых дефектов. Принцип радиографического контроля заключается в способности рентгеновских волн к проникновению вглубь структуры материала.
Радиографический контроль обеспечивает проверку качества технологического оборудования, металлических конструкций, трубопроводов, композитных материалов, как в промышленных, так и в строительных отраслях, а также для обнаружения трещин в сварочных соединениях, пор, инородных элементов (окисных, шлаковых, вольфрамовых).
Кроме этого можно проверить наличие недоступных надрезов, для внешнего осмотра, выпуклостей и вогнутостей основания сварочного шва, превышения проплава. Методика радиографического контроля основана на свойстве рентгеновских лучей, обеспечивающих поглощение, зависящее от плотности элементов и структуры материала.
Данный метод (радиографический контроль) является основным для организации проверки качества сварочных соединений. Радиографический метод проверки сварочных соединений выполняется согласно требований ГОСТ(а) 7512-86.
Преимущества и недостатки
Такой способ контроля обладает, как определенными преимуществами, так и недостатками.
Преимущества
- Выявление и устранение скрытых дефектов внутри изделия.
- Точность замеряемых показаний.
- Вычисление относительных и абсолютных габаритных параметров бракованного участка.
- Нет надобности в контактном приспособлении.
- Скорость выявления изъянов (способ можно использовать, как в единичных, так и в контролировании потока).
- Покрытие технологических изъянов.
- Выявление изъянов, которые нельзя определить каким-либо другим способом.
- Оценка размера вогнутости и выпуклости сварочных соединений.
Недостатки
- Потребность в сложном специальном оборудовании, стоимость которого весьма высока, а это означает, что не каждое учреждение способно его приобрести, из-за ограниченного бюджета. В домашних условиях подобный способ вряд ли будет целесообразным.
- Потребность в специфических расходных материалах, получение которых затруднено.
- Обеспечение жёсткого контроля над использованием аппаратуры согласно инструкции и расходом материалов, так как, при неправильном их применении и сохранности, материалы могут оказаться опасными для здоровья, а иногда, и жизни работников (загрязнение радиоактивными элементами оборудования, спецодежды, человеческого тела, рабочих мест).
- Персонал, работающий с аппаратурой и материалами, обязан иметь высокую квалификацию, что подвластно далеко не каждому человеку.
Радиографический контроль не определяет следующие дефекты:
- Трещины и не провариваемые участки с раскрытием меньше 0,1 мм, при толщине проверяемого материала менее 40 мм, 0,2 мм – если материал толщиной от 40 до 100 и 0,3 мм – если толщина материала равняется от 100 до 150 мм.
- Трещины, не провариваемые участки, проверяемые плоскости которых не совпадают с вектором просвечивания.
- Если протяжность изъянов в просвечиваемом направлении менее двойного показания абсолютной чувствительности контрольной аппаратуры.
- Если изображение включений и прерывистых швов совпадает на радиографическом контроле с изображением сторонних деталей, остроугольных мест или резких перепадов по толщине свариваемых деталей.
Радиографический контроль сварных соединений
Со времен разработки первых методов соединения элементов с использованием сварочных технологий возник вопрос о контроле за качеством сварочных швов. Учитывая существующие технологии, конструкторы разработали различные способы, обеспечивающие довольно точно обнаружить дефекты конструкций, грозящие разрушению. Однако, универсального метода, способного удовлетворить запросы производственников, пока не существует. Поэтому сегодня, при выполнении сварочных работ, производственники вынуждены выбирать, наиболее подходящие для них методы контроля, которые их удовлетворяют:
• Более дешёвым и несложным процессом, без использования сложного оборудования, способного обеспечить удовлетворяющую оценку качества сварного шва.
• Достаточно сложным и дорогостоящим способом, применяемым только на производстве, которое располагает технологическими возможностями, показывая, при этом, объективную и полную картину.
Точные варианты дефектоскопии, приходится задействовать в таких обстоятельствах, когда качество шва составляет ключевую роль и дефекты недопустимы даже ничтожные. Именно, радиографическая проверка качества сварочных соединений удовлетворяет таким требованиям.
Предлагаемая методика радиографического контроля сварочных швов, основанная на свойствах просвечивания проверяемого участка гамма-лучами или рентгеновским излучением, относится к одной из наиболее точной.
В то же время, промышленная радиография относится к профессии, являющейся одной из наиболее вредных для здоровья людей. В методе применяются мощные гамма-источники (> 2 CI).
Проведение радиографического контроля
Суть процесса, регламентируемого ГОСТ(ом) 7512-86, заключается в просвечивании проверяемого участка гамма-лучами или рентгеновским излучением от источника, размещённого в специальной защитной капсуле. Именно, капсула обеспечивает защиту от вредного воздействия лучей на оборудование и персонал, находящихся поблизости. Так как однородный металл лучше поглощает лучи, чем пустоты, нарушающие структуру материала, дефектные участки обозначаются светлыми пятнами, с формой и размерами, соответствующими форме и размерам обнаруженных изъянов (трещин, пустот, шлаков и пр.). При этом, фиксация показаний дефектоскопии может осуществляться различными вариантами.
На бумагу или плёнку, с покрытой поверхностью химическим слоем элемента, чувствительного к излучению. Предлагаемая методика фиксирования дефектоскопических данных точна, однако понижает скорость выполнения исследования. Она неплохо зарекомендовала себя при производстве ограниченных партий изделий высокого качества.
При помощи специальных веществ, называемыми «сцинтилляторы», которые способны поглощать невидимые глазу лучи, с преобразованием их в видимый свет. Используя такой преобразователь, получаемое изображение высвечивается на мониторе, обеспечивая дефектоскопию сварочного шва в реальном режиме времени. Данная методика подходит для серийного производства, а также используется для проверки сварочных швов в монтируемых и ремонтируемых трубопроводах. Здесь капсула с вредным излучением, обычно, помещается внутри трубопровода, обеспечивая качественный контроль.
Для получения достоверных данных радиографического контроля, требуется исполнить некоторые условия.
- С поверхности проверяемого шва требуется удалить окалину, шлак и прочие загрязнения, которые могут повлиять на реальную картину.
- Плотность излучаемого потока обязана быть такой, чтобы регистрация толщины проверяемого участка стала возможной.
- В течение всего периода исследования плотность лучей должна иметь стабильный характер.
- Технологические карты для каждого контролируемого участка разрабатываются в соответствии с регламентом ГОСТ(а).
Характеристики излучаемого источника выбираются в зависимости от проверяемого изделия и его толщины. Правильные результаты будут получены только при выполнении перечисленных требований.
Безопасность при проведении радиографического контроля
При использовании методики радиографического контроля сварочных соединений, важнейшей проблемой является обеспечение мероприятий по технике безопасности.
Для недопущения распространения излучения, оборудование, на котором работает персонал, обязано надёжно экранироваться. Для обеспечения такой защиты можно использовать свинцовые листы. В то же время, сегодняшняя промышленность изготовляет и прочие материалы из пластиков или тканей. Главное – чтобы защитные материалы были герметичными и четко осуществляли своё предназначение.
Оператор, осуществляющий контроль, должен быть удалён от аппаратуры на максимально возможное расстояние, а при проверке, чтобы не было рядом посторонних лиц.
При возникновении острой необходимости нахождения людей в опасной зоне в период функционирования аппаратуры, персонал требуется снабдить индивидуальными защитными средствами. При этом, нужно максимально сократить время нахождения людей в зоне контроля, так как даже небольшие дозы облучения с течением времени накапливаются, негативно влияя на здоровье человека.
При работе с радиоактивными веществами, необходимо организовать их безопасную сохранность, а также доставку к рабочему месту.
Нельзя работать на заведомо неисправном оборудовании. Это может исказить не только показатели дефектоскопии, но и под угрозой может оказаться здоровье, как работающего персонала, так и сторонних лиц. Излучение, накопленное в изделии, может негативно воздействовать на людей, случайно оказавшихся рядом.
Оборудование для радиографического контроля
Контроль может выполняться: промышленной рентгеновской аппаратурой, гамма — дефектоскопами.
На выбор требуемого источника излучения влияет толщина материала, а также заданный класс геометрии и чувствительности просвечивания.
Рентгеновские дефектоскопы
К достоинству рентгеновских дефектоскопов стабильного излучения относится:
- Более высокая мощность.
- Способность к регулировке.
- Долговечность.
- Четкое и контрастное изображение.
Недостатком рентгеновских дефектоскопов является высокая стоимость, большие размеры и опасность для работников.
Гамма-дефектоскопы
Не взирая на то, что проверку сварочных швов рекомендуется выполнять рентгеновской аппаратурой, которая в сравнении с гамма-дефектоскопами создает более качественные радиографические снимки, гамма-дефектоскопы тоже обладают рядом достоинств, а именно:
- Низкой стоимостью.
- Небольшими габаритами.
- Малым оптическим фокусом.
К главному недостатку данной аппаратуры относится отсутствие возможности регулировки мощности, слабая контрастность, медленное затухание излучения источника и потребность в его замене.
Гамма-дефектоскопы, как правило, применяются, когда отсутствует возможность применить рентгеновскую аппаратуру постоянного действия (при проверке изделий небольшой толщины, если отсутствуют источники питания, при проверке труднодоступных участков).
Применение радиографического контроля
Несмотря на некоторые трудности, в отношении использования радиоактивной аппаратуры, радиография приобретает всё большую популярность. Причина такой популярности – высокая точность показаний. Не малое значение имеет способность обнаружения внутренних изъянов. При грамотном подходе, методика с успехом может применяться почти во всех сферах промышленного производства и в строительстве, к примеру, при:
- монтаже безопорных перекрытий или несущих конструкций многоэтажных зданий;
- изготовлении корпусов судов не зависимо от конструктивных характеристик, их набора и обшивки;
- прокладывании трубопроводов, для перекачивания разных марок топлива или воды, жидкой пищевой продукции или ядовитых химикатов;
- изготовлении деталей ракет и самолётов, подвергающихся огромным нагрузкам;
- проверке путепроводов, мостов и металлических конструкций, находящихся в длительном использовании;
- исследованиях коррозии;
- проверке состояния сварочных соединений оружейных деталей;
- изготовлении медицинского оборудования высокой точности.
Во всех перечисленных вариантах допускается использование радиографического метода контроля.
www.okorrozii.com
Рентгенографический контроль сварных соединений трубопроводов
Во время соединения металлических деталей с помощью сварки может возникнуть ситуация, которая затруднит образование нормального однородного шва. Когда в сварочную ванну попадают посторонние предметы или элементы, а также выбран неправильный режим сваривания, то вполне возможно образование брака. Это приводит к тому, что шов будет иметь более низкое качество и сможет выдержать меньшее количество нагрузок, чем предполагалось. Далеко не все виды дефектов можно увидеть сразу, так как зачастую они имеют скрытый характер. В особенности это относится к мелким трещинам и порам. Требования к сварным соединениям здесь могут быть очень высокими, так что любой недочет может привести к серьезным последствиям.
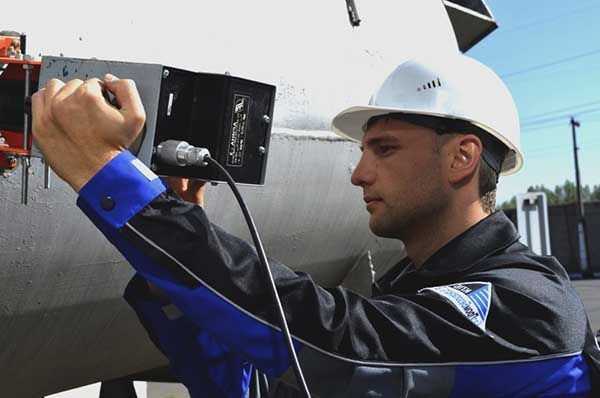
Рентгенографический контроль сварных соединений
Рентгенографический метод контроля сварных соединений это один из самых достоверных способов. Данный метод особенно популярен при проверке соединений технологических трубопроводов, различного ответственного оборудования, металлических конструкций и прочих материалов, применяющихся в самых разнообразных отраслях. Чаще всего высокие нагрузки встречаются в строительстве. Рентген контроль сварных соединений проводится по ГОСТ 7512-86.
Данный принцип основан на поглощении лучей плотными средами. Чем более плотная структура, тем меньше лучей пройдет наружу. Если внутри шва есть трещины, раковины, поры и прочие полые дефекты, то количество прохождения лучей здесь будет значительно большим. Регистрирующее устройство сможет выявить наличие дефекта, его размер, место расположения и другие особенности. Такими качествами не обладает ни один другой метод. Рентгеновский контроль сварных соединений является детальным показателем состояния локальных участков металлоконструкций
Свойства рентгеновских лучей
Лучи могут проходить через плотные непрозрачные тела, но чем выше плотность этих тел, тем ниже пропускание лучей. Проходимость зависит и от длины лучей. При большой длине им сложнее пройти сквозь плотные поверхности. Во время прохождения лучи поглощаются той поверхностью, с которой соприкасаются. Чем выше плотность, тем больше поглощение.
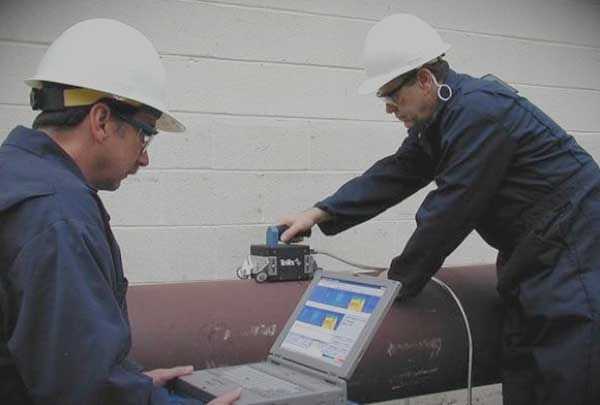
Принцип рентгенографическогой контроля сварных швов
Некоторые химические вещества при контакте с излучением получают видимое свечение. После окончания воздействия свечение прекращается, но некоторые вещества сохраняют заряд свечения еще на некоторое время. Это свойство является основой для создания рентгеновских снимков в данном методе. Воздействие лучей на светочувствительную часть фотопластинок создает изображение внутреннего состояния шва.
При воздействии лучей на клетки организма они производят определенные воздействия, которые зависят от типа ткани и интенсивности полученной дозы. Это может использоваться в медицине, но также имеет и обратный эффект, который проявляется в лучевой болезни.
Лучи могут ионизировать воздух, расщепляя составные части воздушной массы на отдельные частицы, имеющие электрический заряд. Из-за этого воздух может проводить электричество.
Преимущества
- Рентгенографический контроль сварных соединений трубопроводов является одним из самых точных и надежных методов дефектоскопии;
- Можно увидеть скрытые дефекты;
- Возможно определение абсолютных и относительных размеров бракованного места;
- Скорость проведения процедур достаточно высокая.
Недостатки
- Эффективность метода зависит от правильности установки параметров;
- Оборудование для его проведения имеет высокую стоимость;
- Здесь нужно использовать особую пленку для фиксации результата;
- Это опасный для здоровья метод дефектоскопии сварных швов.
Устройство и принцип работы оборудования
Излучающий элемент представлен в виде вакуумного сосуда, в котором находится три электрода: анод, накал катода и катод. Сами рентгеновские лучи возникают тога, когда заряженные частицы получают сильное ускорение. Это может случиться и при высокоэнергетическом переходе, что происходит в оболочке атомов. Рентгенографические трубки используют оба этих варианта. Основным конструктивным элементом устройства выступает анод и катод.
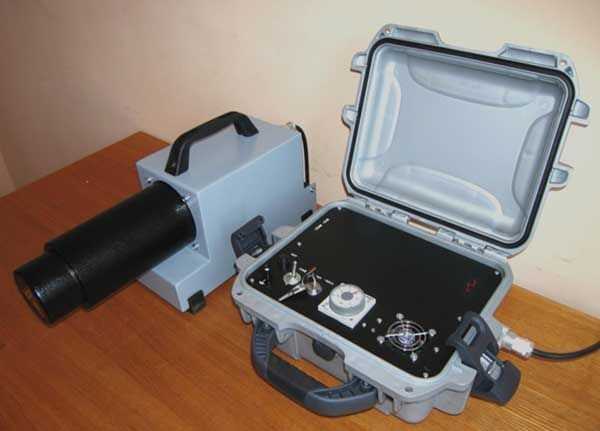
Устройство для рентгенографическогой контроля сварных соединений
Электроны, которые испускаются катодом получают ускорение от различных электрических потенциалов, находящихся в области между анодом и катодом. В это время рентгеновские лучи еще не испускаются, по причине малого своего количества. Они ударяются об анод, после чего происходит их резкое торможение. За счет этого происходит генерация лучей в рентгеновском диапазоне. В это же время из внутренних оболочек атомов анода выбиваются электроны. На места выбитых частиц становятся другие электроны. Выпускаемое излучение приобретает характерные черты, которыми обладает материал анода.
Когда лучи уже вышли, то они передвигаются в соответствии с заданным направлением сквозь выбранный участок шва. Затем они сталкиваются с плотной поверхностью и часть остается в металле. Остальные частицы, которым удалось прорваться, попадают на пленку. Там отображается интенсивность излучения в каждом отдельном месте. При наличии пустых мест в структуре наплавленного металла, количество лучей становится большим. Таким образом можно выявить где находится тот или иной дефект, а также какой он формы и размера.
Методика проведения контроля
Методика проведения рентгенографического контроля сварных соединений очень схожа с радиографическим контролем. Первым делом происходит настройка аппаратуры под определенную плотность металла, чтобы излучение смогло пройти сквозь его поверхность. Затем происходит подготовка сделанного шва к контролю. Для этого с него оббивают шлак, обрабатывают до требуемой высоты валика и зачищают саму поверхность.
После этого изделие перемещается в аппарат на то место, где будет происходить выпуск лучей. Оно должно находиться между излучателей и фотопленкой. Затем включается аппарат и лучи моментально проникают сквозь сварной шов, попадая в итоге на пленку. На ней отображаются все неровности интенсивности, которые показывают наличие дефектов.
«Важно!
Данный процесс может оказать вред здоровью, так что необходимо соблюдать все правила техники безопасности.»
Меры по технике безопасности
Чтобы сохранить свое здоровье при частом проведении подобных процедур, следует придерживаться ряда предписанных требований. В первую очередь, устройство должно быть экранировано, чтобы излучение не распространялось по всему помещению, а действовало только в строго направленное место. Для экранирования зачастую используют металлические пластины. Они же могут пригодиться для обустройства стен помещения, которые также должны быть ограждением для распространения излучения.
Во время работы следует держаться как можно дальше от излучателя, насколько это возможно. Также стоит уменьшить время пребывания в помещении во время работы техники. В данном месте не должно быть ни каких посторонних людей. Все работники должны иметь средства индивидуальной защиты.
Все работы должны проводиться только при условии, что техника исправна и правильно настроена. Стоит понимать, что минимальной дозы излучения сложно избежать, но она со временем накапливается, если процедуры проводятся часто и это может вызвать серьезные осложнения, перерастающие в хроническую профессиональную болезнь. Исходя из этого, необходимо следить за тем, какую дозу человек получает за один проход действия аппарата. Для этого используются специальные дозиметры. Также нужно обратить внимание на ионизацию воздуха в помещении, так как при сильно высоком ее уровне может случиться электрический разряд, потому что воздушная масса перестанет быть диэлектриком.
svarkaipayka.ru
Радиографический метод контроля сварных соединений и швов
Среди всех возможных разновидностей, радиографический контроль сварных соединений является одним из самых точных. Он очень востребован в профессиональной сфере, где производятся качественные изделия, рассчитанные на большую нагрузку. В них, как правило, не допускается наличие каких-либо непроваренных мест, микротрещин, раковин, пор и прочих видов брака. Далеко не все из них можно выявить визуально, поэтому, применяется именно такой способ контроля качества. Он относится к неразрушающему типу, поэтому, изделия после осмотра можно вводить в эксплуатацию.

Радиографический контроль сварных соединений
Радиографический контроль сварных соединений основан на принципе прохождения гамма лучей, а также рентгеновского излучения сквозь твердые поверхности. При прохождении лучи сталкиваются с материалом и лишь часть из них проходит. Если в сварном шве есть поры, раковины и прочие дефекты, создающие неоднородность структуры, то в них будет проходить большее количество лучей, чем в остальных участках. Это помогает точно выявить не только наличие брака, но и его размеры, тип и место расположения. Фиксируются результаты на специальной пленке, что является еще одним преимуществом данного метода. Данная процедура проводится по ГОСТ 7512-86.
Преимущества
- Один из самых точных методов неразрушимого контроля;
- Позволяет выявлять скрытые дефекты;
- Благодаря ему можно точно определить размеры и место расположения проблемного участка;
- Проводится за относительно короткий промежуток времени, так что не нужно будет долго ждать результатов;
- Радиографический метод сварных соединений является самым современным способом проведения контроля, который предназначен для ответственных объектов.
Недостатки
- Сложен в исполнении, так что не каждому человеку и организации он доступен;
- Требует применения дорогостоящего оборудования;
- Необходимо использовать уникальные расходные материалы;
- Представляет опасность для здоровья человека, так как работа ведется с вредными излучениями.
Устройство и принцип работы радиографической установки
Радиографический контроль сварных соединений производятся при помощи специального устройства, которым выступает радиографическая установка. Радиационное изображение, которое поступает на нее, преобразуется в цифровое изображение. Это изображение затем обрабатывается и выводится на отображающее устройства. Данный метод становится возможным благодаря тому, что детектором для контролирования процедуры выступает фотодиод, на котором установлен сцинтиллятор. Лучи воздействуют на сцинтиллятор, после чего выпускают видимый свет. Выход данного света пропорционален полученной квантовой энергии. Таким образом, исходящее излучение света вызывает ток в самом фотодиоде.
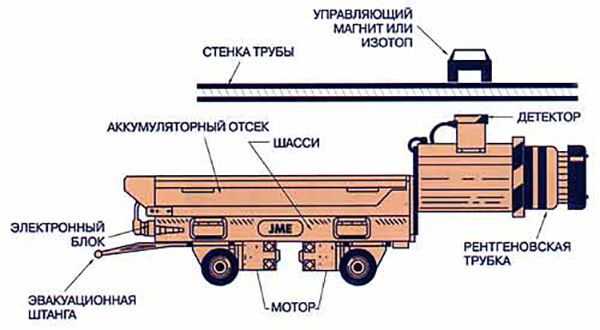
Радиографическая установка
Радиографический метод контроля базируется на преобразовании детектором проходящего сигнала, проникающего сквозь металлическое изделие. Чем выше интенсивность пройденных гамма лучей, а это возможно только при наличии полых дефектов, тем выше уровень освещенности на получаемом изображении. Стоит отметить, что контроль стыков радиографическим методом требует не один детектор, а несколько. Каждый из них снабжается собственным усилителем, которые объединяются в один независимый канал, куда входят все имеющиеся детекторы. Чем больше необходимая ширина контролируемого участка, тем большее количество детекторов требуется. Все каналы в данном случае опрашиваются по очереди.
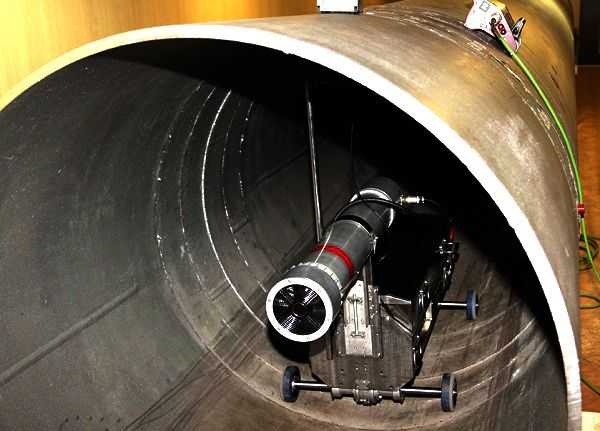
Радиографическая установка для контроля сварных швов
Такое устройство способно контролировать практически все виды сварных соединений и швов. Стоит отметить, что световое излучение является аналоговым сигналом, поэтому, для его преобразования в цифровой формат требуется специальный аналогово-цифровой преобразователь. Весь массив информации передается на компьютерное устройство. Там данные сохраняются для архивирования и дальнейшего, более детального, изучения. На экране данные отображаются в виде полутонового изображения.
Методика проведения контроля
Радиографический контроль сварных соединений при настроенной аппаратуре проводится достаточно просто:
- На первом этапе изделие подготавливают к просвечиванию, для чего нужна очистка поверхности от шлака и других лишних предметов;
- Затем изделие помещается так, чтобы шов находился между излучателем и приемником машины;
- Затем идет включение лучей аппарата, которые проходят сквозь металл шва и попадают на датчик с другой стороны;
- Затем датчик считывает полученную информацию и выводит данные на экран или на специальную пленку, где их можно сохранить для дальнейшего использования.
Требования к устройствам
Когда происходит радиографический контроль сварных соединений, то на интенсивность проходящих лучей нельзя оказать ни какого действия. Это же касается чувствительности контроля. Изображение, которое фиксируется на пленке, определяется посредством интегральной дозы излучения, которое проходило в период экспозиции.
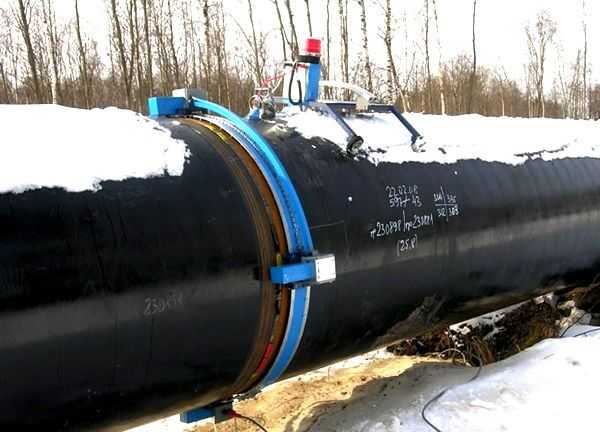
Контроль сварных соединений радиографическим способом
Это является одной из причин, что в то время, когда происходит радиографический контроль сварных соединений, разрешают применять практически любые рентгеновские аппараты. Такая величина как флуктуация для данного метода не является критичной. Все время сканирования занимает десятые доли секунды. Исходя из этого, выделяют два основных требования:
- Плотность гамма-лучей в потоке, который проходит сквозь толщину контролируемого изделия, должна быть достаточно большой, чтобы можно было зарегистрировать изменение толщины объекта на сканируемой области;
- На протяжении всего времени изучения интенсивность лучей должна иметь постоянный характер.
Все этого говорит о том, чтобы радиографический контроль сварных швов прошел как можно более качественно, необходимо иметь стабильный источник ионизирующего излучения с максимально большой плотностью потока лучей и максимальным энергетическим спектром.
Меры по технике безопасности
Инструкция техники безопасности, при таком процессе как радиографический контроль сварных соединений, предполагает выполнения ряда требований, таких как:
- Экранирование самого прибора, чтобы не было широкого распространения вредного излучения;
- Сделать расстояние от человека до устройства как можно большим;
- Ограничить промежуток времени пребывания в зоне потенциальной опасности;
- Использовать средства индивидуальной защиты, такие как свинцовые щитки.
Место, где проходит радиографический контроль сварных швов, должно иметь защитное покрытие, которым зачастую выступают свинцовые листы. В помещении не должно быть посторонних людей, так как проводить процедуру должны только специалисты. Если техника не исправна, то использовать ее нельзя, потому что это может вызвать непредсказуемые последствия. Радиографический метод неразрушающего контроля оказывает минимальное воздействие на человека, но при частом столкновении с ним полученная радиация накапливается, поэтому, необходимо следить за тем, чтобы не превысить минимально допустимую дозу облучения.
svarkaipayka.ru