Как делают деревянные карандаши
В далеком 1912 году по указу царского правительства в Томске была создана фабрика, где пилили кедровую дощечку для карандашей, производимых на территории всей страны.
На сегодняшний день «Сибирская карандашная фабрика» — единственный на территории бывшего Советского Союза производитель карандашей и карандашной дощечки из сибирского кедра, древесина которого применяется для производства карандашей высшей ценовой категории.
Как же делают карандаши, знакомые нам с самого детства?
Производство карандашей начинается с лесной биржи, где складируется заготовленный кедр. Сейчас здесь находится больше трех тысяч кубов дерева. Областные власти очень помогли фабрике в обеспечении материалом и в этом году здесь планируют произвести около 85 миллионов карандашей.
— Древесина, которую мы закупаем, поступает к нам не в результате варварской рубки, – говорит Анатолий Лунин, директор фабрики. – В подавляющем большинстве это санитарная рубка перестоявшегося кедра, который уже не дает орех. Кедр растет до 500 лет, но шишки на нем появляются где-то до 250-летнего возраста, после чего он начинает умирать, его поражают различные насекомые. Если срубить его в этот период, быстрее вырастет новый кедр.
До момента распила бревна проходят обязательную подготовку: каждое бревно нужно вымыть, чтобы приставшие куски земли или глины с камнями случайно не повредили пилы. Для этого дерево с лесной биржи помещают и выдерживают в специальном бассейне с теплой водой. Летом его здесь держат недолго, до двадцати минут, но в зимний период бревно находится в бассейне до тех пор, пока не оттает — на это может уходить до трех часов. А через 369 часов или 16,5 суток и 26 различных технологических операций из бревна получатся готовые карандаши.
На лесопилке из бревна делают вот такой брус:
Производство деревянного карандаша чрезвычайно требовательно к качеству материала, в дело идет только чистая прямая древесина. И если для столярных изделий наличие таких дефектов, как, например, сучки, не катастрофично, то карандаш из такого дерева уже не сделать. Поэтому сказать заранее, сколько карандашей получится из одного бруса, очень сложно.
Чтобы уменьшить количество отходов, на предприятии ищут разные способы увеличения глубины переработки древесины. Один из таких способов – расширение ассортимента выпускаемой продукции. Так, из дощечки, которая не годится для производства карандаша, планируют наладить выпуск деревянных пазлов-раскрасок для детей и средств от моли. Что-то идет на производство коротких карандашей, как для магазинов «IKEA», а часть, на производство вот таких деревянных шампуров:
Полученный из бревна брус распиливают на короткие отрезки, каждый из которых затем распускают на десять дощечек. Чтобы все дощечки были одинаковыми, их нужно откалибровать. Для этого их прогоняют через специальный станок. На выходе из него дощечки имеют одинаковый размер и строго перпендикулярные грани.
Затем откалиброванные дощечки помещают в автоклав. По своему внешнему виду он напоминает бочку, к которой подведено множество труб разного диаметра. При помощи этих труб в камере можно создавать вакуум, нагнетать давление и подавать внутрь всевозможные растворы.
В результате этих процессов из дощечки удаляются содержащиеся в ней смолы, и древесина импрегнируется (пропитывается) парафином. На сегодняшний день это не самый простой, но один из самых эффективных способов улучшить важные свойства материала и защитить дерево от вредного воздействия окружающей среды.
«Облагороженные» после обработки в автоклаве карандашные дощечки остается как следует просушить, а затем — отправить непосредственно на карандашное производство. На этом процесс изготовления дощечки можно считать завершенным. Так выглядят дощечки после обработки в автоклаве
— Основной принцип и технология производства с тех пор как в Томске начали делать карандаши, не меняется, — говорит Анатолий Лунин. — Все процессы на нашей фабрике хорошо отлажены. Модернизация оборудования выражается в замене некоторых узлов, или переходе на более экономичные моторы, использование новых фрез. Приходят какие-то новые материалы, мы что-то меняем в приемке и оценке, но сама технология остается неизменной.
Готовая дощечка поступает в цех белого карандаша, где для начала в ней на станке нарезают канавки, куда затем будут уложены стержни (слово «белый» в данном случае означает то, что карандаш на данном этапе еще не окрашен). Дощечки подаются с одной стороны станка, по дороге их поверхность шлифуется для склейки, особой фрезой в ней выпиливаются углубления. На ближнем краю станка дощечки автоматически укладываются в стопку. Толщина отшлифованной дощечки с нарезанными канавками составляет 5 мм, что равно половине толщины будущего карандаша.
На следующем этапе дощечки склеивают попарно между собой, чтобы получился один карандашный блок.
Станок плавно подает первую дощечку и укладывает стержни в ее канавки. Вслед за этим из другого устройства «выезжает» вторая дощечка, уже смазанная водорастворимым клеем, и аккуратно ложится на первую. Получившиеся карандашные блоки зажимают в пневматическом прессе и стягивают струбцинами.
Если дощечку на фабрике изготавливают самостоятельно, то стержень, в основном, закупают в Китае. Там его начали производить по «сухой» технологии, которая не требует обжига в печи при высокой температуре.
Вследствие этого, себестоимость стержня оказалась настолько низкой, что львиная доля производителей карандаша перешла именно на такой стержень.
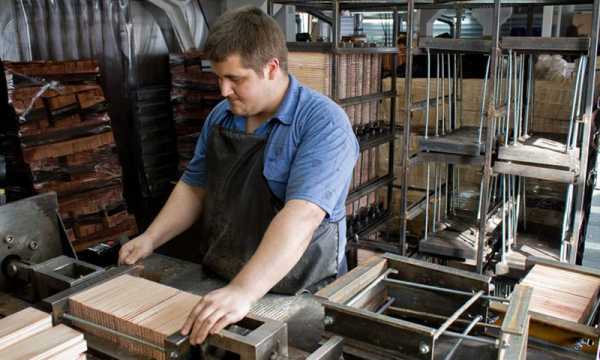
Чтобы грифель карандаша не ломался внутри корпуса, на фабрике применяют технологию дополнительного проклеивания стержня специальной клеевой системой. После этой операции склеенные блоки выдерживают в специальной сушильной камере несколько часов.
В камере довольно жарко. Горячий воздух нагнетается вентилятором, поддерживая температуру порядка 35-40 градусов. Древесине нужно хорошо просохнуть, чтобы в дальнейшем карандаш за один проход стал гладким и получил нужную геометрию. Карандаш с «простым» грифелем сохнет здесь не менее двух часов, а цветной – не менее четырех. Из-за того, что цветной содержит больше жировых веществ, ему требуется больше времени, чтобы просохнуть.
По прошествии этого времени блоки разбирают, укладывают в тележки с указанием всех дальнейших параметров и отправляют на следующий станок, который разделит их на отдельные карандаши.
Своей формой станок похож на тот, который делает канавки в дощечках, но у него есть и свои особенности. Заготовки помещают в загрузочный бункер.
Они проходят по транспортным узлам, торцуются, отпиливаются и на выходе получается привычный деревянный карандаш, только еще не окрашенный.
Двойная фреза, которая разделяет блоки, задает и форму будущего карандаша, причем делается это все за один проход. Именно от типа профиля режущей фрезы зависит то, каким будет карандаш – шестигранным или круглым.
Совсем недавно на фабрике освоили производство трехгранного карандаша. Оказалось, что спрос на такую форму растет. Покупателей привлекает эргономичность и естественность расположения пальцев на гранях, что, безусловно, облегчает обучение письму детей.
Рядом со станком стоит рабочий стол сортировщицы. Ее задача — перебрать сделанные карандаши, отобрать «годные» и отделить дефектные. К дефектам относятся сколы стержня на торце, шероховатости, ожоги древесины и тому подобное. Над столом висит памятка с нормами по браку. В каждый стоящий на столе лоток помещается 1440 карандашей.
Отсортированные карандаши на специальном лифте поднимаются на следующий этаж, где их будут красить.
Краску закупают в сухом виде и разводят до нужной густоты в лаборатории красок. Сама покраска происходит достаточно быстро.
Устройство непрерывно выталкивает окрашенные карандаши на конвейер. Длина и скорость движения транспортерной ленты рассчитаны таким образом, чтобы карандаш высыхал, пока движется на ней.
Доезжая до противоположного конца конвейера, карандаши попадают в один из трех приемников, откуда они отправляются обратно на следующее покрытие.
В среднем каждый карандаш покрывается тремя слоями краски и двумя слоями лака — здесь все зависит от желания заказчика. Покрасить карандаш можно тоже практически в любой цвет. Фабрика выпускает наборы из шести, двенадцати, восемнадцати и двадцати четырех цветов. Некоторые карандаши покрывают только лаком.
После покраски, карандаши отправляют в цех финишной отделки. В этом месте они приобретают тот окончательный вид, в котором дойдут до потребителя. На карандаши наносят штамп, надевают ластик и затачивают.
Способов нанесения штампов довольно много, но на «Сибирской карандашной фабрике» это делают с помощью фольги разных цветов. Такой метод называется термостатированием. Рабочая часть станка нагревается, и штамп через фольгу переносится на карандаш — так он не будет облезать и марать руки. Сам штамп может быть любым, его специально заказывают у гравировщика. В зависимости от сложности, на его изготовление уходит около пяти дней.
На часть карандашей, если это необходимо, надевают ластик.
Последняя операция – это заточка. Затачиваются карандаши на шлифовальной шкурке, надетой на барабан и движущейся с большой скоростью. Это происходит очень быстро, буквально за считанные секунды.
Кроме заточки станок можно настроить на выполнение вальцовки – обработки обратной торцевой части карандаша под небольшим наклоном. Теперь карандаши готовы к упаковке, их отправляют в следующее помещение. Там карандаши собирают в набор, складывают в коробку и направляют потребителю.
Упаковку под нужное количество карандашей печатают в Новосибирске. Она поступает в плоском виде, поэтому сначала ей придают объем. Потом через комплектовочные станки необходимое количество карандашей раскладывают в заданной цветовой гамме. Специальный станок позволяет собирать набор из двенадцати цветов. В конце карандаши раскладывают по коробочкам.
На вопрос, не планирует ли фабрика, по примеру китайских предприятий, перейти на производство карандаша из более дешевых пород дерева или пластмассы Анатолий Лунин признается:
— Я подумывал попробовать сделать экономичный карандаш из низкосортной осины, но это другая технология, и пускай уж китайцы этим занимаются. Меня больше интересует тема увеличения полезного выхода за счет повышения качества переработки древесины. А с точки зрения экологии, производить что-либо лучше из возобновляемого сырья. Пластмассовый карандаш никогда не сгниет, а деревянный за несколько лет полностью разложится.
Остается только пожелать, чтобы в век глобальной компьютеризации нашлось место простому деревянному карандашу.
animalworld.com.ua
«Как делают карандаши из сибирского кедра» в блоге «Производство»
В далеком 1912 году по указу царского правительства в Томске была создана фабрика, где пилили кедровую дощечку для карандашей, производимых на территории всей страны.
Много времени прошло с тех пор. Были в этой истории свои взлеты и падения. В 1999 году фабрика была признана банкротом, а уже в 2004 году известная чешская компания «KOH-I-NOOR Hardtmuth a.s.» вошла в состав ее собственников. На сегодняшний день «Сибирская карандашная фабрика» является единственным на территории бывшего Советского Союза производителем карандашей и карандашной дощечки из Сибирского кедра, древесина которого применяется для производства карандашей высшей ценовой категории. Осенью 2012 года продукция «Сибирской карандашной фабрики», пройдя экспертизу комиссии, стала лауреатом конкурса «Лучшие товары и услуги Томской области», а затем и дипломантом всероссийского конкурса «100 лучших товаров России».
Как же производят карандаши, получившие такое признание потребителей?
ПОДГОТОВКА
Производство карандаша начинается с лесной биржи, где складируется заготовленный кедр. Сейчас здесь находится больше трех тысяч кубов дерева. В прошлом году власти Томской области сильно помогли фабрике в обеспечении материалом. В этом году тут планируют произвести около 85 миллионов карандашей.
— Древесина, которую мы закупаем, поступает к нам не в результате варварской рубки, – говорит Анатолий Лунин, директор фабрики. – В подавляющем большинстве – это санитарная рубка перестоявшегося кедра, который уже не дает орех. Кедр растет до 500 лет, но шишки на нем появляются где-то до 250, после чего он начинает умирать и поражаться различными насекомыми. Если его срубить в этот период, быстрее вырастет новый кедр.
Каждое бревно с лесной биржи сначала проходит обязательную подготовку. Прежде, чем его распилить, дерево помещают и выдерживают в специальном бассейне с теплой водой. Это делают для того, чтобы пристывшие куски земли или глины с камнями случайно не повредили пилы. Летом его здесь держат недолго, до двадцати минут, но в зимний период бревно держат в бассейне до тех пор, пока оно не оттает. На это уходит до трех часов.
В правой верхней части фотографии как раз виден ствол дерева, приготовленный к погружению в бассейн. Через 369 часов или 16,5 суток, пройдя 26 различных технологических операций, из него получатся готовые карандаши.
На лесопилке из бревна делают вот такой брус.
Производство деревянного карандаша чрезвычайно требовательно к качеству материала. В дело идет только чистая прямая древесина, и если для столярных изделий наличие таких дефектов, как, например, сучки не катастрофично, то карандаш из такого дерева уже не сделать, поэтому заранее сказать, сколько карандашей получится из одного бруса очень сложно.
Чтобы уменьшить количество отходов, на предприятии ищут разные способы увеличения глубины переработки древесины. Один из таких способов – расширение ассортимента выпускаемой продукции. Так, из дощечки, которая не годится для производства карандаша, к лету планируют наладить выпуск деревянных пазлов-раскрасок для детей и средств от моли. Что-то идет на производство коротких карандашей, как для магазинов «IKEA», а часть, на производство вот таких деревянных шампуров.
Полученный из бревна брус распиливают на короткие отрезки, каждый из которых затем распускают на десять дощечек. Чтобы все дощечки были одинаковыми их нужно откалибровать. Для этого их прогоняют через специальный станок. На выходе из него дощечки имеют одинаковый размер и строго перпендикулярные грани.
Затем откалиброванные дощечки помещают в автоклав.
По своему внешнему виду он напоминает бочку, к которой подведено множество труб разного диаметра. При помощи этих труб в камере можно создавать вакуум, нагнетать давление и подавать внутрь всевозможные растворы. В результате этих процессов из дощечки удаляются содержащиеся в ней смолы, и древесина импрегнируется (пропитывается) парафином.
На сегодняшний день это не самый простой, но один из самых эффективных способов улучшить важные свойства материала и защитить дерево от вредного воздействия окружающей среды.
Так выглядят «облагороженные» карандашные дощечки после обработки в автоклаве.
Их остается как следует просушить, и отправить на карандашное производство. На этом процесс изготовления дощечки можно считать завершенным.
ПРОИЗВОДСТВО
Готовая дощечка поступает в цех белого карандаша, где для начала в ней на станке нарезают канавки, куда затем будут уложены стержни. Слово «белый» в данном случае означает то, что карандаш здесь еще не окрашенный.
Дощечка подается на дальнем конце в правой части фотографии. По дороге ее поверхность шлифуется для склейки, и особой фрезой в ней выпиливаются углубления. На ближнем краю станка дощечки автоматически укладываются в стопку.
Так выглядит отшлифованная дощечка с нарезанными канавками.
Сейчас ее толщина 5 миллиметров, что равно половине толщины будущего карандаша. На следующем этапе дощечки склеивают попарно между собой, чтобы получился один карандашный блок. Вот как это выглядит.
Станок плавно подает первую дощечку и укладывает стержни в ее канавки.
Вслед за этим из другого устройства «выезжает» вторая дощечка, уже смазанная водорастворимым клеем, и аккуратно ложится на первую.
Получившиеся карандашные блоки зажимают в пневматическом прессе и стягивают струбцинами.
Если дощечку на фабрике изготавливают самостоятельно, то стержень в основном закупают в Китае. Там его начали производить по сухой технологии, которая не требует обжига в печи при высокой температуре. Вследствие этого, себестоимость стержня оказалась настолько низкой, что львиная доля производителей карандаша перешла на такой стержень.
Чтобы грифель карандаша не ломался внутри корпуса, на фабрике применяют технологию дополнительного проклеивания стержня специальной клеевой системой.
После этой операции склеенные блоки выдерживают в специальной сушильной камере несколько часов.
В камере довольно жарко. Горячий воздух нагнетается вентилятором, поддерживая температуру в районе 35-40 градусов. Древесине нужно хорошо просохнуть, чтобы в дальнейшем карандаш за один проход стал гладким и получил нужную геометрию. Карандаш с «простым» грифелем сохнет здесь не менее двух часов, а цветной – не менее четырех. Из-за того, что цветной содержит больше жировых веществ, ему требуется больше времени, чтобы просохнуть.
По прошествии этого времени блоки разбирают, укладывают в тележки с указанием всех дальнейших параметров и отправляют на следующий станок, который разделит их на отдельные карандаши.
Своей формой станок похож на тот, который делал канавки в дощечках, но есть у него и свои особенности. Заготовки помещают в загрузочный бункер. Они проходят по транспортным узлам, торцуются, пилятся и на выходе получается привычный деревянный карандаш, только еще не окрашенный.
Двойная фреза, которая разделяет блоки, задает и форму будущего карандаша, причем делается это все за один проход.
Именно от типа профиля режущей фрезы зависит то, каким будет карандаш – шестигранным или круглым.
Совсем недавно на фабрике освоили производство трехгранного карандаша. Оказалось, что спрос на такую форму растет. Покупателей привлекает эргономичность и естественность расположения пальцев на гранях, что, безусловно, облегчает ребенку обучение письму.
Рядом со станком стоит рабочий стол сортировщицы.
Ее задача перебрать сделанные карандаши, отобрать «годные» и отделить дефектные. К дефектам относятся сколы стержня на торце, шероховатости, ожоги древесины и т.д. Над столом висит памятка с нормами по браку.
В каждый стоящий на столе лоток, помещается 1440 карандашей.
Отсортированные карандаши на специальном лифте поднимаются на следующий этаж, где их будут красить.
ПОКРАСКА И УПАКОВКА
Краску закупают в сухом виде и разводят до нужной густоты в лаборатории красок.
Покраска происходит достаточно быстро. Устройство непрерывно выталкивает окрашенные карандаши на конвейер.
Длина и скорость движения транспортерной ленты рассчитаны таким образом, чтобы карандаш высыхал, пока движется на ней.
Доезжая до противоположного конца конвейера, карандаши попадают в один из трех приемников.
Оттуда они отправляются обратно на следующее покрытие.
В среднем, каждый карандаш покрывается тремя слоями краски и двумя слоями лака. Здесь все зависит от желания заказчика. Покрасить карандаш можно тоже практически в любой цвет. Фабрика выпускает наборы из шести, двенадцати, восемнадцати и двадцати четырех цветов. Некоторые карандаши покрывают только лаком.
После покраски, карандаши отправляют в цех финишной отделки. В этом месте они приобретает тот окончательный вид, в котором дойдут до потребителя. На карандаши наносят штамп, надевают ластик и затачивают.
Этот станок наносит штамп.
Способов его нанесения довольно много, но на предприятии это делают с помощью фольги разных цветов. Такой метод называется термостатированием. Рабочая часть станка нагревается, и штамп через фольгу переносится на карандаш. Так он не будет облазить и марать руки.
Сам штамп может быть любым, его специально заказывают у гравировщика. В зависимости от сложности, на его изготовление уходит около пяти дней.
На часть карандашей, если это необходимо, надевают ластик.
Последняя операция – это заточка.
Затачиваются карандаши на шлифовальной шкурке, надетой на барабан и движущейся с большой скоростью.
Это происходит очень быстро, буквально за считанные секунды.
Кроме заточки станок можно настроить на выполнение вальцовки – обработки обратной торцевой части карандаша под небольшим наклоном.
Теперь карандаши готовы к упаковке, и для того, чтобы сделать это, их отправляют в следующее помещение.
Там их собирают в набор, складывают в коробочку и посылают потребителю.
Упаковку под нужное количество карандашей печатают в Новосибирске. Она поступает в плоском виде, и сначала ей придают объем.
Потом через комплектовочные станки необходимое количество карандашей раскладывают в заданной цветовой гамме.
Этот станок позволяет собирать набор из двенадцати цветов.
В конце карандаши раскладывают по коробочкам.
Здесь на стенде представлены образцы продукции, которую выпускает фабрика.
Во время экскурсии мы спросили про модернизацию оборудования. «Сейчас в мире существует двенадцать фабрик, – сообщил Анатолий Лунин. – И на всех похожее оборудование. В Томске делают карандаш с 30-х годов. С тех пор основной принцип и технология производства не меняется. Все процессы хорошо отлажены. Модернизация оборудования выражается в замене некоторых узлов, или переходе на более экономичные моторы, использование новых фрез. Приходят какие-то новые материалы, мы что-то меняем в приемке и оценке, но сама технология остается неизменной».
На вопрос, не планируют ли фабрика, по примеру китайских предприятий, перейти на производство карандаша из более дешевых пород дерева или пластмассы Анатолий Лунин признался: «Я подумывал попробовать сделать экономичный карандаш из низкосортной осины, но это другая технология, и пускай уж китайцы этим занимаются. Меня больше интересует тема увеличения полезного выхода за счет повышения качества переработки древесины. А с точки зрения экологии, производить что-либо лучше из возобновляемого сырья. Пластмассовый карандаш никогда не сгниет, а деревянный за несколько лет полностью разложится».
Остается только пожелать, чтобы в мире глобальной компьютеризации, нашлось место простому деревянному карандашу.
Текст, фото: Евгений Мыцик
sdelanounas.ru
Made in Tomsk: Как делают карандаши из сибирского кедра — Как это работает
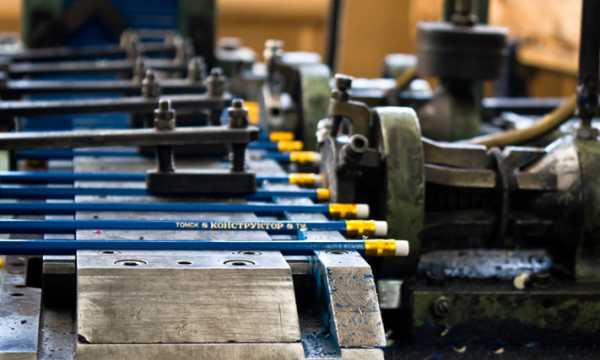
20 марта 2013 / Томский Обзор / Фото: Томский Обзор
В далеком 1912 году по указу царского правительства в Томске была создана фабрика, где пилили кедровую дощечку для карандашей, производимых на территории всей страны.
И сегодня «Сибирская карандашная фабрика» — единственный на территории бывшего Советского Союза производитель карандашей и карандашной дощечки из сибирского кедра, древесина которого применяется для производства карандашей высшей ценовой категории. Осенью прошлого года продукция «Сибирской карандашной фабрики», пройдя экспертизу комиссии, стала лауреатом конкурса «Лучшие товары и услуги Томской области», а затем и дипломантом всероссийского конкурса «100 лучших товаров России».
Как же производят карандаши, получившие столь массовое и заслуженное признание?
ПОДГОТОВКА
Производство карандашей начинается с лесной биржи, где складируется заготовленный кедр. Сейчас здесь находится больше трех тысяч кубов дерева. В прошлом году областные власти очень помогли фабрике в обеспечении материалом и в этом году здесь планируют произвести около 85 миллионов карандашей.
— Древесина, которую мы закупаем, поступает к нам не в результате варварской рубки, – говорит Анатолий Лунин, директор фабрики. – В подавляющем большинстве это санитарная рубка перестоявшегося кедра, который уже не дает орех. Кедр растет до 500 лет, но шишки на нем появляются где-то до 250-летнего возраста, после чего он начинает умирать, его поражают различные насекомые. Если срубить его в этот период, быстрее вырастет новый кедр.
До момента распила бревна проходят обязательную подготовку: каждое бревно нужно вымыть, чтобы пристывшие куски земли или глины с камнями случайно не повредили пилы. Для этого дерево с лесной биржи помещают и выдерживают в специальном бассейне с теплой водой. Летом его здесь держат недолго, до двадцати минут, но в зимний период бревно находится в бассейне до тех пор, пока не оттает — на это может уходить до трех часов. А через 369 часов или 16,5 суток и 26 различных технологических операций из бревна получатся готовые карандаши.
На лесопилке из бревна делают вот такой брус:
Производство деревянного карандаша чрезвычайно требовательно к качеству материала, в дело идет только чистая прямая древесина. И если для столярных изделий наличие таких дефектов, как, например, сучки, не катастрофично, то карандаш из такого дерева уже не сделать. Поэтому сказать заранее, сколько карандашей получится из одного бруса, очень сложно.
Чтобы уменьшить количество отходов, на предприятии ищут разные способы увеличения глубины переработки древесины. Один из таких способов – расширение ассортимента выпускаемой продукции. Так, из дощечки, которая не годится для производства карандаша, к лету планируют наладить выпуск деревянных пазлов-раскрасок для детей и средств от моли. Что-то идет на производство коротких карандашей, как для магазинов «IKEA», а часть, на производство вот таких деревянных шампуров:
Полученный из бревна брус распиливают на короткие отрезки, каждый из которых затем распускают на десять дощечек. Чтобы все дощечки были одинаковыми, их нужно откалибровать. Для этого их прогоняют через специальный станок. На выходе из него дощечки имеют одинаковый размер и строго перпендикулярные грани.
Затем откалиброванные дощечки помещают в автоклав. По своему внешнему виду он напоминает бочку, к которой подведено множество труб разного диаметра. При помощи этих труб в камере можно создавать вакуум, нагнетать давление и подавать внутрь всевозможные растворы. В результате этих процессов из дощечки удаляются содержащиеся в ней смолы, и древесина импрегнируется (пропитывается) парафином. На сегодняшний день это не самый простой, но один из самых эффективных способов улучшить важные свойства материала и защитить дерево от вредного воздействия окружающей среды.
«Облагороженные» после обработки в автоклаве карандашные дощечки остается как следует просушить, а затем — отправить непоредственно на карандашное производство. На этом процесс изготовления дощечки можно считать завершенным.
Так выглядят дощечки после обработки в автоклаве
— Основной принцип и технология производства с тех пор как в Томске начали делать карандаши, не меняется, — говорит Анатолий Лунин. — Все процессы на нашей фабрике хорошо отлажены. Модернизация оборудования выражается в замене некоторых узлов, или переходе на более экономичные моторы, использование новых фрез. Приходят какие-то новые материалы, мы что-то меняем в приемке и оценке, но сама технология остается неизменной.
ПРОИЗВОДСТВО
Готовая дощечка поступает в цех белого карандаша, где для начала в ней на станке нарезают канавки, куда затем будут уложены стержни (слово «белый» в данном случае означает то, что карандаш на данном этапе еще не окрашен). Дощечки подаются с одной стороны станка, по дороге их поверхность шлифуется для склейки, особой фрезой в ней выпиливаются углубления. На ближнем краю станка дощечки автоматически укладываются в стопку. Толщина отшлифованной дощечки с нарезанными канавками составляет 5 мм, что равно половине толщины будущего карандаша.
На следующем этапе дощечки склеивают попарно между собой, чтобы получился один карандашный блок. Станок плавно подает первую дощечку и укладывает стержни в ее канавки. Вслед за этим из другого устройства «выезжает» вторая дощечка, уже смазанная водорастворимым клеем, и аккуратно ложится на первую. Получившиеся карандашные блоки зажимают в пневматическом прессе и стягивают струбцинами.
Если дощечку на фабрике изготавливают самостоятельно, то стержень, в основном, закупают в Китае. Там его начали производить по «сухой» технологии, которая не требует обжига в печи при высокой температуре. Вследствие этого, себестоимость стержня оказалась настолько низкой, что львиная доля производителей карандаша перешла именно на такой стержень.
Чтобы грифель карандаша не ломался внутри корпуса, на фабрике применяют технологию дополнительного проклеивания стержня специальной клеевой системой. После этой операции склеенные блоки выдерживают в специальной сушильной камере несколько часов.
В камере довольно жарко. Горячий воздух нагнетается вентилятором, поддерживая температуру порядка 35-40 градусов. Древесине нужно хорошо просохнуть, чтобы в дальнейшем карандаш за один проход стал гладким и получил нужную геометрию. Карандаш с «простым» грифелем сохнет здесь не менее двух часов, а цветной – не менее четырех. Из-за того, что цветной содержит больше жировых веществ, ему требуется больше времени, чтобы просохнуть.
По прошествии этого времени блоки разбирают, укладывают в тележки с указанием всех дальнейших параметров и отправляют на следующий станок, который разделит их на отдельные карандаши.
Своей формой станок похож на тот, который делает канавки в дощечках, но у него есть и свои особенности. Заготовки помещают в загрузочный бункер. Они проходят по транспортным узлам, торцуются, пилятся и на выходе получается привычный деревянный карандаш, только еще не окрашенный.
Двойная фреза, которая разделяет блоки, задает и форму будущего карандаша, причем делается это все за один проход. Именно от типа профиля режущей фрезы зависит то, каким будет карандаш – шестигранным или круглым.
Совсем недавно на фабрике освоили производство трехгранного карандаша. Оказалось, что спрос на такую форму растет. Покупателей привлекает эргономичность и естественность расположения пальцев на гранях, что, безусловно, облегчает обучение письму детей.
Рядом со станком стоит рабочий стол сортировщицы. Ее задача — перебрать сделанные карандаши, отобрать «годные» и отделить дефектные. К дефектам относятся сколы стержня на торце, шероховатости, ожоги древесины и тому подобное. Над столом висит памятка с нормами по браку. В каждый стоящий на столе лоток помещается 1440 карандашей.
Отсортированные карандаши на специальном лифте поднимаются на следующий этаж, где их будут красить.
ПОКРАСКА И УПАКОВКА
Краску закупают в сухом виде и разводят до нужной густоты в лаборатории красок. Сама покраска происходит достаточно быстро. Устройство непрерывно выталкивает окрашенные карандаши на конвейер. Длина и скорость движения транспортерной ленты рассчитаны таким образом, чтобы карандаш высыхал, пока движется на ней. Доезжая до противоположного конца конвейера, карандаши попадают в один из трех приемников, откуда они отправляются обратно на следующее покрытие.
В среднем каждый карандаш покрывается тремя слоями краски и двумя слоями лака — здесь все зависит от желания заказчика. Покрасить карандаш можно тоже практически в любой цвет. Фабрика выпускает наборы из шести, двенадцати, восемнадцати и двадцати четырех цветов. Некоторые карандаши покрывают только лаком.
После покраски, карандаши отправляют в цех финишной отделки. В этом месте они приобретают тот окончательный вид, в котором дойдут до потребителя. На карандаши наносят штамп, надевают ластик и затачивают.
Способов нанесения штампов довольно много, но на «Сибирской карандашной фабрике» это делают с помощью фольги разных цветов. Такой метод называется термостатированием. Рабочая часть станка нагревается, и штамп через фольгу переносится на карандаш — так он не будет облезать и марать руки. Сам штамп может быть любым, его специально заказывают у гравировщика. В зависимости от сложности, на его изготовление уходит около пяти дней.
На часть карандашей, если это необходимо, надевают ластик.
Последняя операция – это заточка. Затачиваются карандаши на шлифовальной шкурке, надетой на барабан и движущейся с большой скоростью. Это происходит очень быстро, буквально за считанные секунды.
Кроме заточки станок можно настроить на выполнение вальцовки – обработки обратной торцевой части карандаша под небольшим наклоном. Теперь карандаши готовы к упаковке, их отправляют в следующее помещение. Там карандаши собирают в набор, складывают в коробоку и направляют потребителю.
Упаковку под нужное количество карандашей печатают в Новосибирске. Она поступает в плоском виде, поэтому сначала ей придают объем. Потом через комплектовочные станки необходимое количество карандашей раскладывают в заданной цветовой гамме. Специальный станок позволяет собирать набор из двенадцати цветов. В конце карандаши раскладывают по коробочкам.
На вопрос, не планирует ли фабрика, по примеру китайских предприятий, перейти на производство карандаша из более дешевых пород дерева или пластмассы Анатолий Лунин признается:
— Я подумывал попробовать сделать экономичный карандаш из низкосортной осины, но это другая технология, и пускай уж китайцы этим занимаются. Меня больше интересует тема увеличения полезного выхода за счет повышения качества переработки древесины. А с точки зрения экологии, производить что-либо лучше из возобновляемого сырья. Пластмассовый карандаш никогда не сгниет, а деревянный за несколько лет полностью разложится.
Остается только пожелать, чтобы в век глобальной компьютеризации нашлось место простому деревянному карандашу.
Текст, фото: Евгений Мыцик
obzor.city
Как делают карандаши из сибирского кедра
В далеком 1912 году по указу царского правительства в Томске была создана фабрика, где пилили кедровую дощечку для карандашей, производимых на территории всей страны.На сегодняшний день «Сибирская карандашная фабрика» — единственный на территории бывшего Советского Союза производитель карандашей и карандашной дощечки из сибирского кедра, древесина которого применяется для производства карандашей высшей ценовой категории.
Как же производят карандаши, знакомые нам с самого детства?
Производство карандашей начинается с лесной биржи, где складируется заготовленный кедр. Сейчас здесь находится больше трех тысяч кубов дерева. Областные власти очень помогли фабрике в обеспечении материалом и в этом году здесь планируют произвести около 85 миллионов карандашей.
— Древесина, которую мы закупаем, поступает к нам не в результате варварской рубки, – говорит Анатолий Лунин, директор фабрики. – В подавляющем большинстве это санитарная рубка перестоявшегося кедра, который уже не дает орех. Кедр растет до 500 лет, но шишки на нем появляются где-то до 250-летнего возраста, после чего он начинает умирать, его поражают различные насекомые. Если срубить его в этот период, быстрее вырастет новый кедр.
До момента распила бревна проходят обязательную подготовку: каждое бревно нужно вымыть, чтобы приставшие куски земли или глины с камнями случайно не повредили пилы. Для этого дерево с лесной биржи помещают и выдерживают в специальном бассейне с теплой водой. Летом его здесь держат недолго, до двадцати минут, но в зимний период бревно находится в бассейне до тех пор, пока не оттает — на это может уходить до трех часов. А через 369 часов или 16,5 суток и 26 различных технологических операций из бревна получатся готовые карандаши.
На лесопилке из бревна делают вот такой брус:
Производство деревянного карандаша чрезвычайно требовательно к качеству материала, в дело идет только чистая прямая древесина. И если для столярных изделий наличие таких дефектов, как, например, сучки, не катастрофично, то карандаш из такого дерева уже не сделать. Поэтому сказать заранее, сколько карандашей получится из одного бруса, очень сложно.
Чтобы уменьшить количество отходов, на предприятии ищут разные способы увеличения глубины переработки древесины. Один из таких способов – расширение ассортимента выпускаемой продукции. Так, из дощечки, которая не годится для производства карандаша, планируют наладить выпуск деревянных пазлов-раскрасок для детей и средств от моли. Что-то идет на производство коротких карандашей, как для магазинов «IKEA», а часть, на производство вот таких деревянных шампуров:
Полученный из бревна брус распиливают на короткие отрезки, каждый из которых затем распускают на десять дощечек. Чтобы все дощечки были одинаковыми, их нужно откалибровать. Для этого их прогоняют через специальный станок. На выходе из него дощечки имеют одинаковый размер и строго перпендикулярные грани.
Затем откалиброванные дощечки помещают в автоклав. По своему внешнему виду он напоминает бочку, к которой подведено множество труб разного диаметра. При помощи этих труб в камере можно создавать вакуум, нагнетать давление и подавать внутрь всевозможные растворы.
В результате этих процессов из дощечки удаляются содержащиеся в ней смолы, и древесина импрегнируется (пропитывается) парафином. На сегодняшний день это не самый простой, но один из самых эффективных способов улучшить важные свойства материала и защитить дерево от вредного воздействия окружающей среды.
«Облагороженные» после обработки в автоклаве карандашные дощечки остается как следует просушить, а затем — отправить непосредственно на карандашное производство. На этом процесс изготовления дощечки можно считать завершенным. Так выглядят дощечки после обработки в автоклаве
— Основной принцип и технология производства с тех пор как в Томске начали делать карандаши, не меняется, — говорит Анатолий Лунин. — Все процессы на нашей фабрике хорошо отлажены. Модернизация оборудования выражается в замене некоторых узлов, или переходе на более экономичные моторы, использование новых фрез. Приходят какие-то новые материалы, мы что-то меняем в приемке и оценке, но сама технология остается неизменной.
Готовая дощечка поступает в цех белого карандаша, где для начала в ней на станке нарезают канавки, куда затем будут уложены стержни (слово «белый» в данном случае означает то, что карандаш на данном этапе еще не окрашен). Дощечки подаются с одной стороны станка, по дороге их поверхность шлифуется для склейки, особой фрезой в ней выпиливаются углубления. На ближнем краю станка дощечки автоматически укладываются в стопку. Толщина отшлифованной дощечки с нарезанными канавками составляет 5 мм, что равно половине толщины будущего карандаша.
На следующем этапе дощечки склеивают попарно между собой, чтобы получился один карандашный блок.
Станок плавно подает первую дощечку и укладывает стержни в ее канавки. Вслед за этим из другого устройства «выезжает» вторая дощечка, уже смазанная водорастворимым клеем, и аккуратно ложится на первую. Получившиеся карандашные блоки зажимают в пневматическом прессе и стягивают струбцинами.
Если дощечку на фабрике изготавливают самостоятельно, то стержень, в основном, закупают в Китае. Там его начали производить по «сухой» технологии, которая не требует обжига в печи при высокой температуре.
Вследствие этого, себестоимость стержня оказалась настолько низкой, что львиная доля производителей карандаша перешла именно на такой стержень.
Чтобы грифель карандаша не ломался внутри корпуса, на фабрике применяют технологию дополнительного проклеивания стержня специальной клеевой системой. После этой операции склеенные блоки выдерживают в специальной сушильной камере несколько часов.
В камере довольно жарко. Горячий воздух нагнетается вентилятором, поддерживая температуру порядка 35-40 градусов. Древесине нужно хорошо просохнуть, чтобы в дальнейшем карандаш за один проход стал гладким и получил нужную геометрию. Карандаш с «простым» грифелем сохнет здесь не менее двух часов, а цветной – не менее четырех. Из-за того, что цветной содержит больше жировых веществ, ему требуется больше времени, чтобы просохнуть.
По прошествии этого времени блоки разбирают, укладывают в тележки с указанием всех дальнейших параметров и отправляют на следующий станок, который разделит их на отдельные карандаши.
Своей формой станок похож на тот, который делает канавки в дощечках, но у него есть и свои особенности. Заготовки помещают в загрузочный бункер.
Они проходят по транспортным узлам, торцуются, отпиливаются и на выходе получается привычный деревянный карандаш, только еще не окрашенный.
Двойная фреза, которая разделяет блоки, задает и форму будущего карандаша, причем делается это все за один проход. Именно от типа профиля режущей фрезы зависит то, каким будет карандаш – шестигранным или круглым.
Совсем недавно на фабрике освоили производство трехгранного карандаша. Оказалось, что спрос на такую форму растет. Покупателей привлекает эргономичность и естественность расположения пальцев на гранях, что, безусловно, облегчает обучение письму детей.
Рядом со станком стоит рабочий стол сортировщицы. Ее задача — перебрать сделанные карандаши, отобрать «годные» и отделить дефектные. К дефектам относятся сколы стержня на торце, шероховатости, ожоги древесины и тому подобное. Над столом висит памятка с нормами по браку. В каждый стоящий на столе лоток помещается 1440 карандашей.
Отсортированные карандаши на специальном лифте поднимаются на следующий этаж, где их будут красить.
Краску закупают в сухом виде и разводят до нужной густоты в лаборатории красок. Сама покраска происходит достаточно быстро.
Устройство непрерывно выталкивает окрашенные карандаши на конвейер. Длина и скорость движения транспортерной ленты рассчитаны таким образом, чтобы карандаш высыхал, пока движется на ней.
Доезжая до противоположного конца конвейера, карандаши попадают в один из трех приемников, откуда они отправляются обратно на следующее покрытие.
В среднем каждый карандаш покрывается тремя слоями краски и двумя слоями лака — здесь все зависит от желания заказчика. Покрасить карандаш можно тоже практически в любой цвет. Фабрика выпускает наборы из шести, двенадцати, восемнадцати и двадцати четырех цветов. Некоторые карандаши покрывают только лаком.
После покраски, карандаши отправляют в цех финишной отделки. В этом месте они приобретают тот окончательный вид, в котором дойдут до потребителя. На карандаши наносят штамп, надевают ластик и затачивают.
Способов нанесения штампов довольно много, но на «Сибирской карандашной фабрике» это делают с помощью фольги разных цветов. Такой метод называется термостатированием. Рабочая часть станка нагревается, и штамп через фольгу переносится на карандаш — так он не будет облезать и марать руки. Сам штамп может быть любым, его специально заказывают у гравировщика. В зависимости от сложности, на его изготовление уходит около пяти дней.
На часть карандашей, если это необходимо, надевают ластик.
Последняя операция – это заточка. Затачиваются карандаши на шлифовальной шкурке, надетой на барабан и движущейся с большой скоростью. Это происходит очень быстро, буквально за считанные секунды.
Кроме заточки станок можно настроить на выполнение вальцовки – обработки обратной торцевой части карандаша под небольшим наклоном. Теперь карандаши готовы к упаковке, их отправляют в следующее помещение. Там карандаши собирают в набор, складывают в коробку и направляют потребителю.
Упаковку под нужное количество карандашей печатают в Новосибирске. Она поступает в плоском виде, поэтому сначала ей придают объем. Потом через комплектовочные станки необходимое количество карандашей раскладывают в заданной цветовой гамме. Специальный станок позволяет собирать набор из двенадцати цветов. В конце карандаши раскладывают по коробочкам.
На вопрос, не планирует ли фабрика, по примеру китайских предприятий, перейти на производство карандаша из более дешевых пород дерева или пластмассы Анатолий Лунин признается:
— Я подумывал попробовать сделать экономичный карандаш из низкосортной осины, но это другая технология, и пускай уж китайцы этим занимаются. Меня больше интересует тема увеличения полезного выхода за счет повышения качества переработки древесины. А с точки зрения экологии, производить что-либо лучше из возобновляемого сырья. Пластмассовый карандаш никогда не сгниет, а деревянный за несколько лет полностью разложится.
Остается только пожелать, чтобы в век глобальной компьютеризации нашлось место простому деревянному карандашу.
Оригинал взят отсюда
Жми на кнопку, чтобы подписаться на «Как это сделано»!
Если у вас есть производство или сервис, о котором вы хотите рассказать нашим читателям, пишите Аслану ([email protected]) и мы сделаем самый лучший репортаж, который увидят не только читатели сообщества, но и сайта Как это сделано
Подписывайтесь также на наши группы в фейсбуке, вконтакте, одноклассниках, в ютюбе и инстаграме, где будут выкладываться самое интересное из сообщества, плюс видео о том, как это сделано, устроено и работает.
Жми на иконку и подписывайся!
— http://kak_eto_sdelano.livejournal.com/
— https://www.facebook.com/kaketosdelano/
— https://www.youtube.com/kaketosdelano
— https://vk.com/kaketosdelano
— https://ok.ru/kaketosdelano
— https://twitter.com/kaketosdelano
— https://www.instagram.com/kaketosdelano/
Официальный сайт — http://ikaketosdelano.ru/
Мой блог — http://aslan.livejournal.com
Инстаграм — https://www.instagram.com/aslanfoto/
Facebook — https://www.facebook.com/aslanfoto/
Вконтакте — https://vk.com/aslanfoto
kak-eto-sdelano.livejournal.com
Как делают карандаши — Мастерок.жж.рф — LiveJournal
В далеком 1912 году по указу царского правительства в Томске была создана фабрика, где пилили кедровую дощечку для карандашей, производимых на территории всей страны.
На сегодняшний день «Сибирская карандашная фабрика» – единственный на территории бывшего Советского Союза производитель карандашей и карандашной дощечки из сибирского кедра, древесина которого применяется для производства карандашей высшей ценовой категории.
Как же производят карандаши, знакомые нам с самого детства?
Производство карандашей начинается с лесной биржи, где складируется заготовленный кедр. Сейчас здесь находится больше трех тысяч кубов дерева. Областные власти очень помогли фабрике в обеспечении материалом и в этом году здесь планируют произвести около 85 миллионов карандашей.
— Древесина, которую мы закупаем, поступает к нам не в результате варварской рубки, – говорит Анатолий Лунин, директор фабрики. – В подавляющем большинстве это санитарная рубка перестоявшегося кедра, который уже не дает орех. Кедр растет до 500 лет, но шишки на нем появляются где-то до 250-летнего возраста, после чего он начинает умирать, его поражают различные насекомые. Если срубить его в этот период, быстрее вырастет новый кедр.
До момента распила бревна проходят обязательную подготовку: каждое бревно нужно вымыть, чтобы приставшие куски земли или глины с камнями случайно не повредили пилы. Для этого дерево с лесной биржи помещают и выдерживают в специальном бассейне с теплой водой. Летом его здесь держат недолго, до двадцати минут, но в зимний период бревно находится в бассейне до тех пор, пока не оттает – на это может уходить до трех часов. А через 369 часов или 16,5 суток и 26 различных технологических операций из бревна получатся готовые карандаши.
На лесопилке из бревна делают вот такой брус:
Производство деревянного карандаша чрезвычайно требовательно к качеству материала, в дело идет только чистая прямая древесина. И если для столярных изделий наличие таких дефектов, как, например, сучки, не катастрофично, то карандаш из такого дерева уже не сделать. Поэтому сказать заранее, сколько карандашей получится из одного бруса, очень сложно.
Чтобы уменьшить количество отходов, на предприятии ищут разные способы увеличения глубины переработки древесины. Один из таких способов – расширение ассортимента выпускаемой продукции. Так, из дощечки, которая не годится для производства карандаша, планируют наладить выпуск деревянных пазлов-раскрасок для детей и средств от моли. Что-то идет на производство коротких карандашей, как для магазинов «IKEA», а часть, на производство вот таких деревянных шампуров:
Полученный из бревна брус распиливают на короткие отрезки, каждый из которых затем распускают на десять дощечек. Чтобы все дощечки были одинаковыми, их нужно откалибровать. Для этого их прогоняют через специальный станок. На выходе из него дощечки имеют одинаковый размер и строго перпендикулярные грани.
Затем откалиброванные дощечки помещают в автоклав. По своему внешнему виду он напоминает бочку, к которой подведено множество труб разного диаметра. При помощи этих труб в камере можно создавать вакуум, нагнетать давление и подавать внутрь всевозможные растворы.
В результате этих процессов из дощечки удаляются содержащиеся в ней смолы, и древесина импрегнируется (пропитывается) парафином. На сегодняшний день это не самый простой, но один из самых эффективных способов улучшить важные свойства материала и защитить дерево от вредного воздействия окружающей среды.
«Облагороженные» после обработки в автоклаве карандашные дощечки остается как следует просушить, а затем – отправить непосредственно на карандашное производство. На этом процесс изготовления дощечки можно считать завершенным. Так выглядят дощечки после обработки в автоклаве
— Основной принцип и технология производства с тех пор как в Томске начали делать карандаши, не меняется, – говорит Анатолий Лунин. – Все процессы на нашей фабрике хорошо отлажены. Модернизация оборудования выражается в замене некоторых узлов, или переходе на более экономичные моторы, использование новых фрез. Приходят какие-то новые материалы, мы что-то меняем в приемке и оценке, но сама технология остается неизменной.
Готовая дощечка поступает в цех белого карандаша, где для начала в ней на станке нарезают канавки, куда затем будут уложены стержни (слово «белый» в данном случае означает то, что карандаш на данном этапе еще не окрашен). Дощечки подаются с одной стороны станка, по дороге их поверхность шлифуется для склейки, особой фрезой в ней выпиливаются углубления. На ближнем краю станка дощечки автоматически укладываются в стопку. Толщина отшлифованной дощечки с нарезанными канавками составляет 5 мм, что равно половине толщины будущего карандаша.
На следующем этапе дощечки склеивают попарно между собой, чтобы получился один карандашный блок.
Станок плавно подает первую дощечку и укладывает стержни в ее канавки. Вслед за этим из другого устройства «выезжает» вторая дощечка, уже смазанная водорастворимым клеем, и аккуратно ложится на первую. Получившиеся карандашные блоки зажимают в пневматическом прессе и стягивают струбцинами.
Если дощечку на фабрике изготавливают самостоятельно, то стержень, в основном, закупают в Китае. Там его начали производить по «сухой» технологии, которая не требует обжига в печи при высокой температуре.
Вследствие этого, себестоимость стержня оказалась настолько низкой, что львиная доля производителей карандаша перешла именно на такой стержень.
Чтобы грифель карандаша не ломался внутри корпуса, на фабрике применяют технологию дополнительного проклеивания стержня специальной клеевой системой. После этой операции склеенные блоки выдерживают в специальной сушильной камере несколько часов.
В камере довольно жарко. Горячий воздух нагнетается вентилятором, поддерживая температуру порядка 35-40 градусов. Древесине нужно хорошо просохнуть, чтобы в дальнейшем карандаш за один проход стал гладким и получил нужную геометрию. Карандаш с «простым» грифелем сохнет здесь не менее двух часов, а цветной – не менее четырех. Из-за того, что цветной содержит больше жировых веществ, ему требуется больше времени, чтобы просохнуть.
По прошествии этого времени блоки разбирают, укладывают в тележки с указанием всех дальнейших параметров и отправляют на следующий станок, который разделит их на отдельные карандаши.
Своей формой станок похож на тот, который делает канавки в дощечках, но у него есть и свои особенности. Заготовки помещают в загрузочный бункер.
Они проходят по транспортным узлам, торцуются, отпиливаются и на выходе получается привычный деревянный карандаш, только еще не окрашенный.
Двойная фреза, которая разделяет блоки, задает и форму будущего карандаша, причем делается это все за один проход. Именно от типа профиля режущей фрезы зависит то, каким будет карандаш – шестигранным или круглым.
Совсем недавно на фабрике освоили производство трехгранного карандаша. Оказалось, что спрос на такую форму растет. Покупателей привлекает эргономичность и естественность расположения пальцев на гранях, что, безусловно, облегчает обучение письму детей.
Рядом со станком стоит рабочий стол сортировщицы. Ее задача – перебрать сделанные карандаши, отобрать «годные» и отделить дефектные. К дефектам относятся сколы стержня на торце, шероховатости, ожоги древесины и тому подобное. Над столом висит памятка с нормами по браку. В каждый стоящий на столе лоток помещается 1440 карандашей.
Отсортированные карандаши на специальном лифте поднимаются на следующий этаж, где их будут красить.
Краску закупают в сухом виде и разводят до нужной густоты в лаборатории красок. Сама покраска происходит достаточно быстро.
Устройство непрерывно выталкивает окрашенные карандаши на конвейер. Длина и скорость движения транспортерной ленты рассчитаны таким образом, чтобы карандаш высыхал, пока движется на ней.
Доезжая до противоположного конца конвейера, карандаши попадают в один из трех приемников, откуда они отправляются обратно на следующее покрытие.
В среднем каждый карандаш покрывается тремя слоями краски и двумя слоями лака – здесь все зависит от желания заказчика. Покрасить карандаш можно тоже практически в любой цвет. Фабрика выпускает наборы из шести, двенадцати, восемнадцати и двадцати четырех цветов. Некоторые карандаши покрывают только лаком.
После покраски, карандаши отправляют в цех финишной отделки. В этом месте они приобретают тот окончательный вид, в котором дойдут до потребителя. На карандаши наносят штамп, надевают ластик и затачивают.
Способов нанесения штампов довольно много, но на «Сибирской карандашной фабрике» это делают с помощью фольги разных цветов. Такой метод называется термостатированием. Рабочая часть станка нагревается, и штамп через фольгу переносится на карандаш – так он не будет облезать и марать руки. Сам штамп может быть любым, его специально заказывают у гравировщика. В зависимости от сложности, на его изготовление уходит около пяти дней.
На часть карандашей, если это необходимо, надевают ластик.
Последняя операция – это заточка. Затачиваются карандаши на шлифовальной шкурке, надетой на барабан и движущейся с большой скоростью. Это происходит очень быстро, буквально за считанные секунды.
Кроме заточки станок можно настроить на выполнение вальцовки – обработки обратной торцевой части карандаша под небольшим наклоном. Теперь карандаши готовы к упаковке, их отправляют в следующее помещение. Там карандаши собирают в набор, складывают в коробку и направляют потребителю.
Упаковку под нужное количество карандашей печатают в Новосибирске. Она поступает в плоском виде, поэтому сначала ей придают объем. Потом через комплектовочные станки необходимое количество карандашей раскладывают в заданной цветовой гамме. Специальный станок позволяет собирать набор из двенадцати цветов. В конце карандаши раскладывают по коробочкам.
На вопрос, не планирует ли фабрика, по примеру китайских предприятий, перейти на производство карандаша из более дешевых пород дерева или пластмассы Анатолий Лунин признается:
— Я подумывал попробовать сделать экономичный карандаш из низкосортной осины, но это другая технология, и пускай уж китайцы этим занимаются. Меня больше интересует тема увеличения полезного выхода за счет повышения качества переработки древесины. А с точки зрения экологии, производить что-либо лучше из возобновляемого сырья. Пластмассовый карандаш никогда не сгниет, а деревянный за несколько лет полностью разложится.
Остается только пожелать, чтобы в век глобальной компьютеризации нашлось место простому деревянному карандашу.
источник
А теперь посмотрим на анимированный процесс не на этой фабрике, но про все те же карандаши:
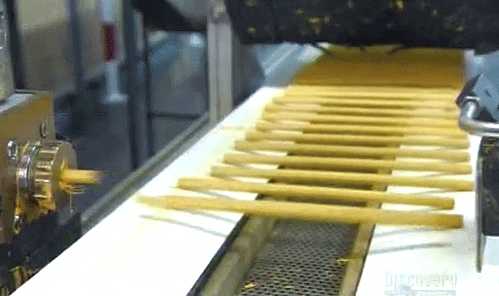
Вот еще немного из серии как это делается: вот Как делают стеклянные шарики, а вот Как сделать 20 миллионов зубочисток в сутки. Еще как это делается в гифках ТУТ, ТУТ и ТУТ Оригинал статьи находится на сайте ИнфоГлаз.рф Ссылка на статью, с которой сделана эта копия — http://infoglaz.ru/?p=46307
masterok.livejournal.com
Карандаши из веток своими руками
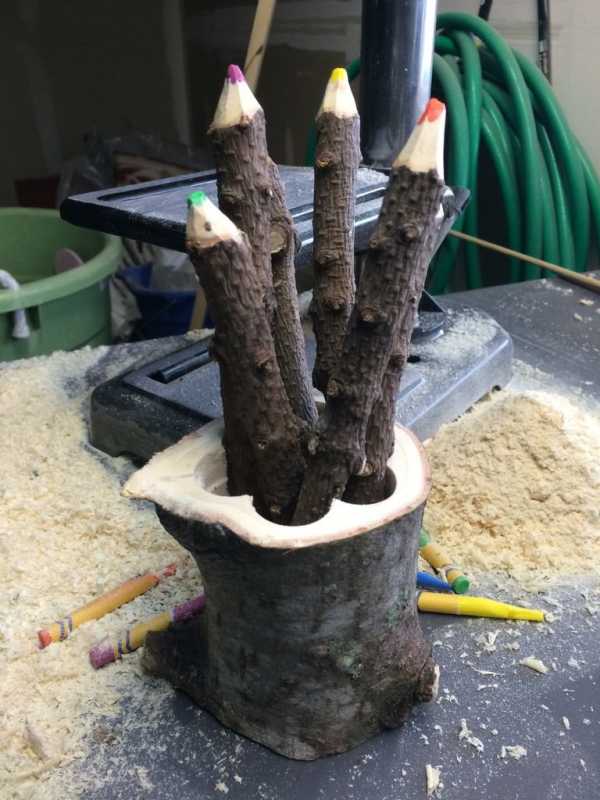
Оригинальные уличные карандаши с такой же экологичной подставкой для них вы можете сделать самостоятельно. В качестве исходных материалов могут использоваться любые ветви деревьев, даже сосна или ель, которые вы собрались выкидывать после новогодних праздников. Такие забавные карандаши придутся детям по душе, ими можно рисовать не только на крупных листах ватмана, но и на асфальте.
Материалы
Для изготовления карандашей из веток своими руками, вам нужно будет подготовить:
- ветки дерева;
- небольшой кусок ствола дерева;
- дрель;
- сверла;
- кольцевые сверла;
- восковые карандаши;
- острый нож;
- шлифовальную машинку или наждачную бумагу;
- ножовку или пилу.
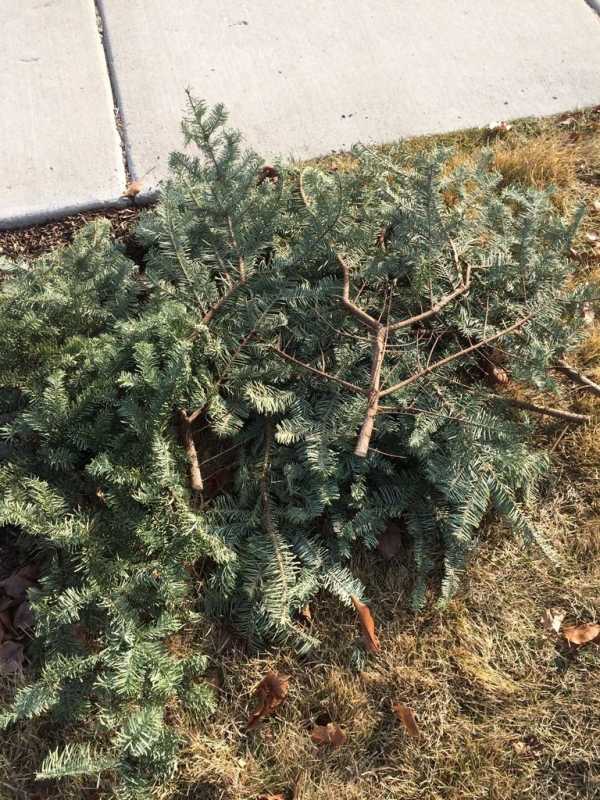
Шаг 1. Для изготовления карандашей вам необходимо будет взять несколько веток. Количество их будет зависеть от желаемого количества карандашей. Диаметр ветки для изготовления одного экземпляра в данном случае составил 1,8 см. Вы можете сделать свои карандаши толще или тоньше, исходя из своих же предпочтений.
Все ветки обрежьте до одинаковой длины и очистите кору их от пыли. Если есть острые выступы или зазубрины, срежьте их.
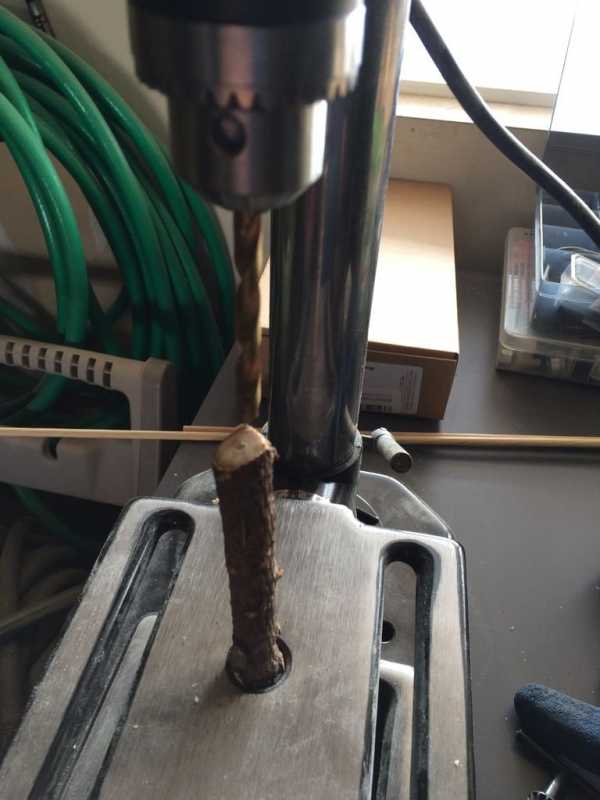
Шаг 2. Теперь в каждом из карандашей необходимо просверлить отверстия для заливки грифеля. Этот этап работы делайте максимально аккуратно, чтобы сверло не ушло в сторону и не поранило вас. До конца веток отверстие не пробуривайте. В противном случае, грифель, будучи еще теплым, вытечет.

Шаг 3. Восковые мелки раскрошите, и растопите их по цветам в одноразовых стаканчиках. Пока воск еще теплый, залейте его в пробуренные отверстия карандашей и оставьте последние в вертикальном положении до полного застывания грифеля.
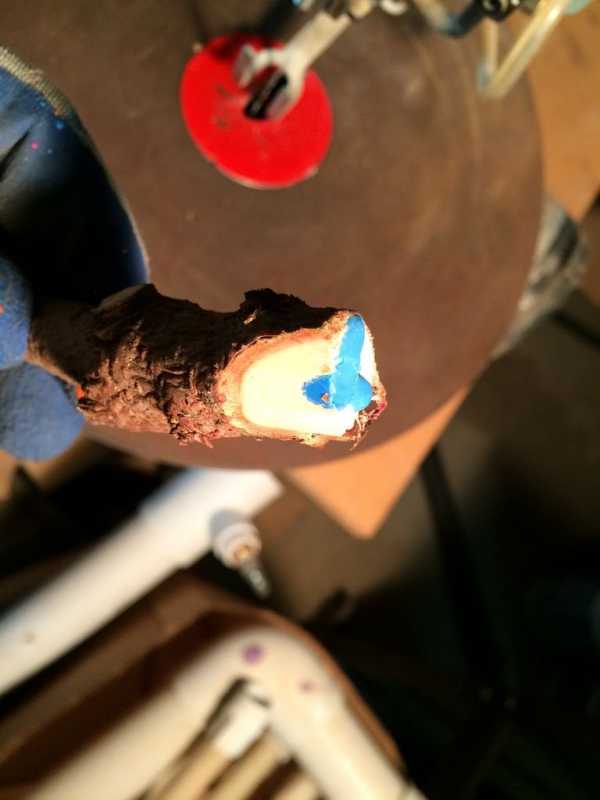
Шаг 4. Теперь карандаши вам нужно будет заточить. Используйте для этого острый нож, но при этом работайте аккуратно, особенно если древесина, взятая в качестве исходного материала, жесткая. Заточите все карандаши.
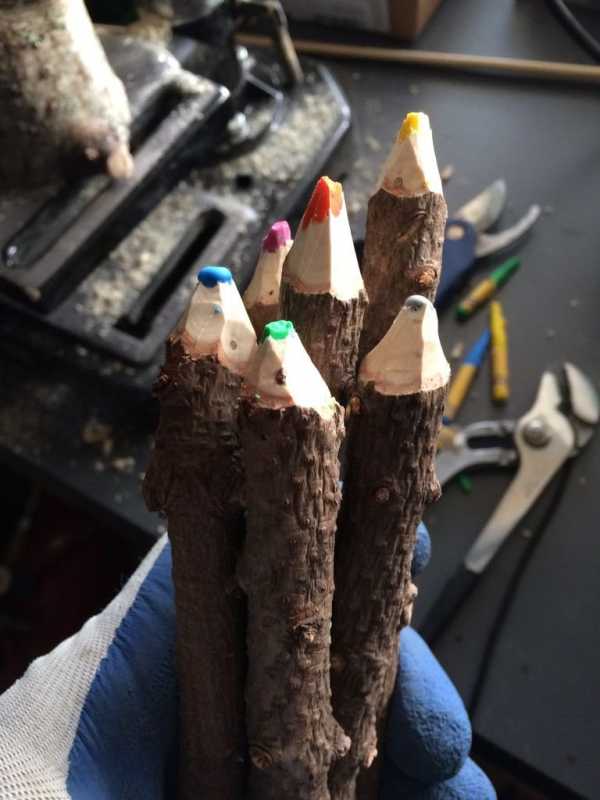
Шаг 5. Для удобства хранения столь оригинальных карандашей можно сделать подставку ей под стать. Определяясь с размерами подставки, исходите из высоты, диаметра и количества сделанных экземпляров для рисования. Обрежьте кусок ствола соответствующего диаметра. Места срезов отшлифуйте.
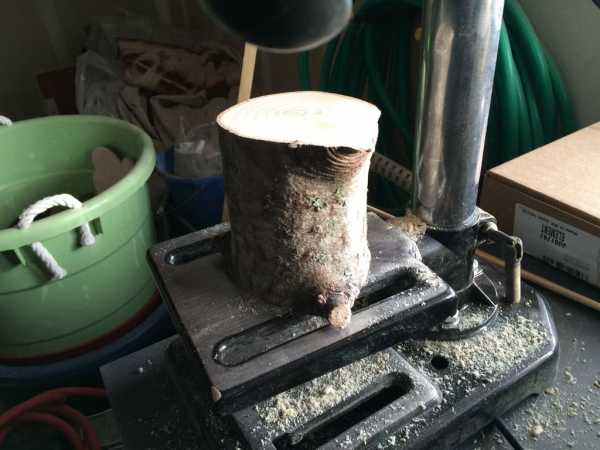
Шаг 6. Внутреннее содержимое подставки вырежьте кольцевым сверлом. Отверстия не должны быть сквозными. Отшлифуйте внутреннюю часть подставки и отправьте в нее карандаши.
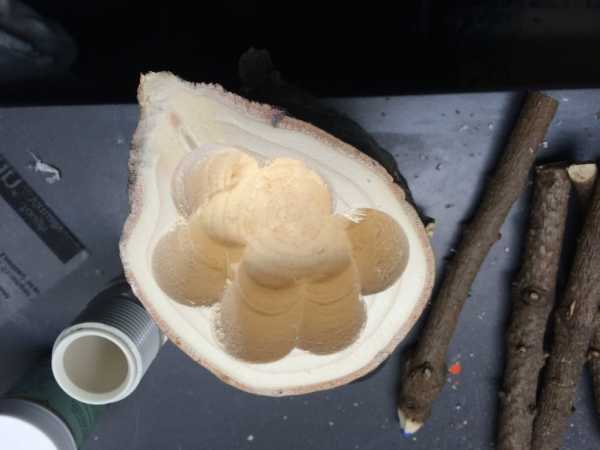
Подставка с оригинальными карандашами готова!
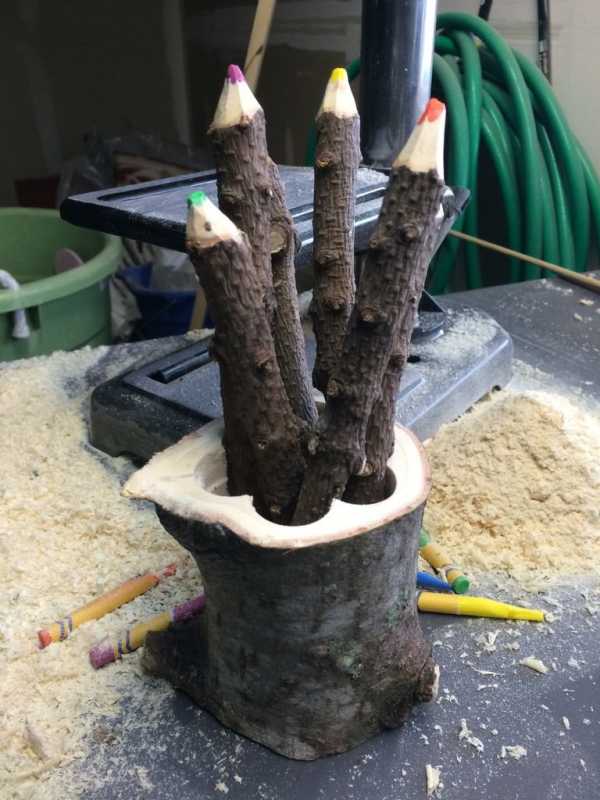
rukikryki.ru
Из какого дерева делают карандаши?
Оболочка для карандашей Древесина для изготовления оболочки карандашей должна обладать рядом специфических свойств: Быть легкой, мягкой и прочной, не ломаться и не крошиться в процессе изготовления карандашей. Иметь одинаковое сопротивление разрезанью волокон как вдоль, так и поперек, не должна расслаиваться. Срез при резании острым ножом должен быть гладким, блестящим, стружка должна завиваться, не скалываться и не ломаться. Древесина должна быть малогигроскопичной, т. е. не должна поглощать влагу. Всем этим качествам соответствует виргинский можжевельник, произрастающий в США. Ни одна из древесных пород, произрастающих в России, в полной мере не соответствует всем этим требованиям. Наиболее близкой по своим свойствам и строению является древесина кедра и липы, но для применения в карандашном производстве ее необходимо предварительно подвергнуть специальной обработке – парафинированию (т. е. облагораживанию). <img src=»//content.foto.my.mail.ru/bk/seks-masina1955/_answers/i-74.jpg» >
Из сосны наверняка!!!! Хотя я не уверина!!!))))))))
Из карандашного =)))
Деревянная оболочка — это сосна.
В идеале-из кедра. Но сейчас-из чего угодно. Вплоть до пластмассы.
было время-делали из кедра
карандашным деревом называют можжевельник виргинский
Раньше делали из кедра, сейчас не знаю.
Из крабовых палочек!
Карандаш был изобретен в 1775 году французом Николя Жак Конте. Идея заковать в футляр легко оставляющий след на бумаге, но пачкающий руки, графит, сохранила имя изобретателя и бизнесмена в веках. Фирма «Конте» до сих пор является одним из лидеров производства карандашей. Первоначально графит заправлялся в металлическую трубочку, часто золотую и карандаш кроме своей основной функции — письма на бумаге, нёс и некоторую статусную нагрузку, как предмет роскоши. Сейчас, благодаря поистине универсальному характеру своего применения, привычности и удобству пользования, карандаш в нашем сознании предстает таким же привычным и извечным благом, как колесо или спички, но история карандаша весьма непроста. Прототипы современного карандаша известны уже в средние века. Так, вставлявшиеся в металлические зажимы свинцовые, серебряные стержни дававшие темно-серые или коричневые тона употреблялись в 12-16 веках. В 14 веке появился так называемый итальянский карандаш из глинистого сланца, который дает матовый оттенок и слабую черноту. С 17-го века получили распространение графитные карандаши, которые отличались малой интенсивностью и лёгким блеском. К этому же периоду относится и широкое использование карандашей из порошка жженой кости, скреплённого растительным клеем, они давали сильный черный матовый штрих. С прототипами скорее всего и связано появление слова «карандаш» . Оно восходит к тюркскому karadas «черный камень» и турецкому karatas – “чёрный сланец”. Лингвисты связывают с ним также слово карандыш – крошка, карапуз, маленький человек, указывая на близость его значения с немецким словом «stift» — карандаш карапуз. Первые месторождения графита открыты 1654 году, что не так-то и давно. И сам графит и без золотых трубок был недёшев. А найден он был в Англии в графстве Кемберли в небольшом количестве и королева, не уверенная в скором изобретении шариковых и гелиевых ручек и тем более лазерных принтеров, дозволяла добывать графит не дольше шести недель в году, чтобы сохранить этот минерал и для потомков. В России же, богатой графитом и лесом, Михаил Ломоносов силами жителей одной деревни Архангельской губернии развернул производство карандаша в деревянной оболочке и ввёл в мировой обиход понятие «гросс» – дюжина дюжин. Гросс — дневная норма выработки карандашей одним мастером с одним подмастерьем. До сих пор во всём мире — «гросс» единица измерения количества именно карандашей. С оправкой графитового стержня в деревянную оболочку вид и принцип действия карандаша уже не изменяется более двухсот лет. Совершенствуется производство, оттачивается качество, количество выпускаемых карандашей становится астрономическим, но идея трения слоистой красящей субстанции о шершавую поверхность остается удивительно жизнеспособной. Изобретение карандаша в деревянной оправе, в силу удобства пользования, а также сравнительной простоты и дешевизны их изготовления, облегчило процесс закрепления и распространения информации. Чтобы оценить преимущества этого новшества, необходимо вспомнить, что письменность многие века была сопряжена с такими атрибутами, как гусиные и, позже, металлические перья, чернила или тушь. Человек пишущий был прикован к столу. Появление карандаша позволило вести записи в пути или в процессе работы, когда надо было моментально зафиксировать что-то. Недаром в наш язык прочно вошел фразеологический оборот: «взять на карандаш» .
У нас это был тест по ИЗО еще какое влеяние оказывает золото на шее, из какого дерева делают карандаши
touch.otvet.mail.ru