способы защиты металлов в домашних условиях
Металлы используются практически везде. Основная проблема этих материалов в том, что они подвержены коррозии. Ржавчина постепенно разрушает структуру детали и выводит её из строя. Чтобы избежать разрушения материала, проводится антикоррозийная обработка. Обработку можно осуществить не только на производстве, но и дома.
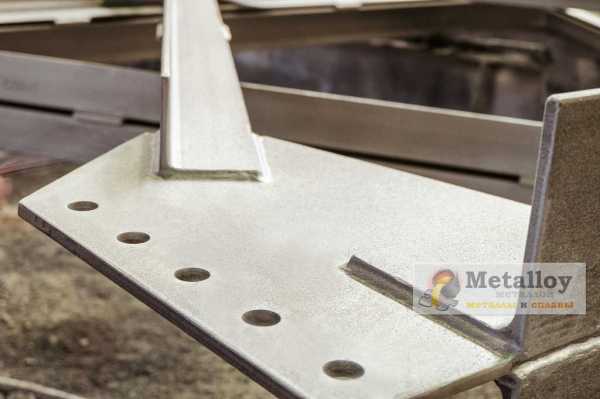
Антикоррозийная обработка металла
Виды коррозии
За всё время работы с металлическими изделиями, люди выделили несколько видов коррозии металла:
- Почвенная — тип коррозии, которая поражает конструкции, находящиеся в земле. Из-за особенного состава грунта, наличия грунтовых вод, происходят химические процессы, вызывающие появление ржавчины.
- Атмосферная — процесс окисления, протекающий в ходе контакта водяных паров воздуха с металлической поверхностью. Чем больше вредных веществ в воздухе, тем быстрее появиться коррозия.
- Жидкостная — такому виду коррозии подвержены металлоконструкции, находящиеся в воде. Если в жидкости содержится соль, процесс разрушения материала будет протекать быстрее.
Выбор антикоррозийного состава зависит от того, в какой среде будет эксплуатироваться металлическая деталь.
Характерные типы поражения ржавчиной
Существует несколько типов поражения стали коррозией. Они различаются по внешнему виду и глубине поражения материала:
- Поверхностная коррозия. Представляет собой слой ржавчины, который может распространяться по всей поверхности изделия или находиться на отдельных его местах.
- Ржавчина в отдельных местах, которая начинает уходить вглубь материала.
- Образование глубинных трещин.
- Окисления одного компонента из металлического сплава.
- Ржавчина по всей поверхности, которая уходит вглубь материала.
Могут проявляться комбинированные типы поражения деталей ржавчиной.
Способы защиты от коррозии
Существуют разные виды антикоррозийной защиты металлоконструкций. Большинство деталей и заготовок обрабатывается с помощью промышленных растворов и оборудования. Однако, существуют и бытовые методы обработки металлических поверхностей.
Промышленные
Если говорить о промышленных средствах от ржавчины на металле, можно выделить такие виды обработки:
- Лакокрасочное покрытие.
- Термическая обработка.
- Защитный слой из металла. Наносится с помощью специального оборудования при высокой температуре и давлении.
- Добавление легирующих примесей в металл при его плавке. Этот процесс называется пассивация.
- Электрозащита.
- Использование ингибиторов. Это вещества, которые останавливают протекание химических реакций, приводящих к появлению ржавчины.
Существуют и другие методы обработки, которые используются на производстве. Выбор технологии зависит от того, в какой среде будет эксплуатироваться металлоконструкция.
Бытовые
Бытовые средства от ржавчины представляют собой лакокрасочные покрытия. Для защиты металлов используется:
- металлическая пудра;
- различные полимеры;
- смолы на основе силикона;
- ингибиторы.
Если металлическая поверхность уже повреждена, нужно использовать другие составы. Для этого подходят специальные смолы, стабилизаторы, грунты и преобразователи.
Как провести обработку своими руками?
Существуют различные способы защиты металла от коррозии, которые можно применять в домашних условиях. Для них не требуется применение дорогого оборудования и мощных химических составов.
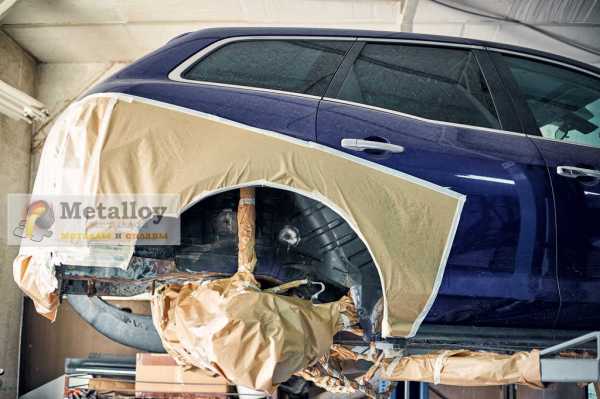
Подготовка к обработке металла
Защитные краски
Краски, которые используются для защиты металлов, можно разделить на несколько видов:
- эпоксидные;
- алкидные;
- акриловые.
У лакокрасочных материалов есть ряд преимуществ:
- защитные составы быстро высыхают;
- для нанесения не нужно обладать дополнительными навыками;
- покрытие изменяет цвет металла;
- долговечность.
Мастера в частных мастерских используют серебрянку. После нанесения она образует надёжный слой окиси алюминия. Эпоксидные смеси подходят для деталей, которые будут использоваться при высоких нагрузках.
Стандартная схема антикоррозийной обработки
Защита металлоконструкций от коррозии — это технологический процесс, который требует соблюдения этапов работы. Наносится защитный слой после финишной обработки металла. Этапы нанесения защиты:
- обрабатываемая поверхность очищается от ржавчины, грязи, налёта;
- после очистки заготовка обезжиривается;
- когда обезжиривание закончено, наносится слой грунта;
- после высыхания грунта наносится два слоя защитного состава.
При проведении работ нужно пользоваться защитными очками, респиратором и перчатками.
Нормы и правила СНиП
На государственных предприятиях защита от коррозии считается важнейшим моментом, который утверждается официальным документом СНиП 2.03.11 — 85. В нём указываются такие методы защиты металла:
- покрытие лакокрасочными материалами;
- пропитка заготовки антикоррозийным составом;
- оклейка специальными плёнками.
В документе указывается какие методы можно использовать в определённых средах. При самостоятельной антикоррозийной обработке нужно учитывать правила и рекомендации из официального документа.
Антикоррозийная обработка применяется для защиты металлических изделий и продления их долговечности. При выборе защитного раствора нужно учитывать сферу эксплуатации детали.
metalloy.ru
Методы антикоррозионной защиты
Не только металлы, но и другие инструментальные или конструкционные материалы, в той или иной мере подвержены разрушительному воздействию внешней среды, в том числе коррозии. На протяжении многих лет значительная часть строительных конструкций и различных механизмов производится из производных железа – чугуна и стали, которые в особенности страдают от такой разновидности коррозии, как ржавление, а потому требуют эффективной антикоррозионной защиты.
Борьба с коррозией железных изделий и конструкций является важнейшей производственной и эксплуатационной задачей. С ростом знаний о мире и развитием научно-технического потенциала человечество разработало множество различных методик антикоррозионной защиты металлических поверхностей. В каждой конкретной ситуации выбор того или иного метода защиты от ржавления определяется условиями эксплуатации изделия или его хранения, а также требованиями к его надежности, химической устойчивости и т.д.
Сегодня успешно применяются такие основные методы защиты от ржавления, как:
- нанесение покрытий (как металлических, так и неметаллических),
- использование ингибиторов коррозии,
- химическая и электрохимическая защита.
Рассмотрим эти технологии более подробно.
Металлические антикоррозионные покрытия
В наше время защита поверхностей из металла от негативного воздействия внешней среды с помощью создания металлических покрытий широко применяется в самых разных отраслях. Например, таким образом защищают детали машин и части приборов, а также металлоконструкции. Для создания защиты выбирается металл, который обладает хорошей стойкостью в конкретной среде. Металлические антикоррозионные покрытия могут также способствовать улучшению износостойкости изделия.
Существует два основных типа металлических покрытий – катодное и анодное.
Катодные позволяют создать механическую защиту металлической поверхности и образуются при участии металлов, которые обладают электродным потенциалом, превышающим в электролитической среде потенциал основного металла. Для создания катодного покрытия стальных изделий используют никель, медь, олово.В случае использования анодного покрытия металлические поверхности защищают при помощи металла, обладающего большим отрицательным потенциалом. Нужно отметить, что срок службы таких покрытий увеличивается при возрастании толщины покрытия. Для железоуглеродистых сплавов защищающее покрытие может быть образовано цинком, кадмием. Листовая сталь защищается цинковым покрытием очень часто.
Металлические покрытия могут наноситься на изделия различными методами, при этом самым распространенным являются:
- горячий метод,
- гальванизация,
- плакирование,
- металлизация,
- напыление.
В случае применения горячего метода нанесения покрытия изделие погружается в емкость с расплавленным металлом, после чего вынимается и охлаждается. Именно таким способом часто осуществляют цинкование (покрытие цинком) и лужение (покрытие оловом). Горячее цинкование обычно используют для антикоррозионной защиты кровельного железа, труб и проволоки, а лужение – для обработки внутренних поверхностей пищевых емкостей (например, котлов).
Метод гальванизации использует физические законы, определяющие прохождение тока через жидкость-электролит. Катодом в этом случае является защищаемое изделие, а анодом – металл, который нужно нанести. Если через электролит пропустить ток, анод будет растворяться в электролите, после чего катионы будут перемещаться на изделие. Этот метод позволяет наносить покрытие из самых разных металлов на любые изделия, а толщина покрытия может варьироваться в значительных переделах.
Термомеханическое покрытие изделий из металла, или плакирование, предполагает совместную горячую прокатку изделия и защитного металла, при этом надежное сцепление обеспечивается за счет диффузии под влиянием давления и температуры.
Неметаллические защитные покрытия
При нанесении таких покрытий применяют краски, эмали, лаки, смазки, пластики и прочие материалы (они могут быть органическими или неорганическими). Можно с уверенностью сказать, что такая антикоррозионная защита является наиболее популярной. Неметаллические покрытия обладают рядом преимуществ по сравнению с металлическими – например, могут быть легко нанесены на изделие и практически так же легко удалены с защищаемой поверхности, не влияют на важные свойства металла, относительно дешевы.
В случае правильного выбора лакокрасочных материалов и при условии соблюдения технологий нанесения такие покрытия имеют значительный срок службы (до 5 лет). Кстати, компания «Анкор» предлагает большой модельный ряд оборудования для окраски и нанесения защитных покрытий.
Отдельной разновидностью неметаллических покрытий можно считать консервационные смазки, которые наносятся на изделия перед длительным хранением или транспортировкой. Такие смазки могут при необходимости обновляться.
Ингибиторы коррозии и химическая защита
Появлению ржавчины можно эффективно противостоять, используя ингибиторы коррозии. При ингибировании в агрессивную среду вводятся в небольших количествах особые вещества, которые уменьшают скорость коррозии или препятствуют ее возникновению. Сфера применения ингибиторов коррозии – тепловые коммуникации, трубопроводы, нефтедобыча, химическая промышленность.
К методикам химической защиты относится искусственное создание на металлической поверхности защитных пленок (например, оксидных). Подобные тонкие пленки создаются посредством воздействия на изделие сильных химических реагентов. Процесс создания оксидных пленок принято называть оксидированием. Оксидирование широко применяется для защиты поверхностей из магния, алюминия, сплавов этих металлов.
Еще одним способом химической защиты является фосфатирование – наведение пленок из фосфатов марганца и железа. При этом образуются пленки более прочные, чем оксидные.
Другие способы антикоррозионной защиты
В некоторых случаях для того, чтобы защитить металлические поверхности, могут применяться протекторы. Это одна из разновидностей электрохимической защиты. Данный метод использую, когда имеются конструкции, которые контактируют с электролитом; к поверхности конструкции крепят протекторы (пластины из металла, обладающего меньшим по сравнению с защищаемой поверхностью электродным потенциалом). Таким образом создается гальваническая пара «протектор (анод) / изделие (катод)». Со временем протектор разрушается и требует замены.
Подобным образом обеспечивают антикоррозионную защиту корпусов морских кораблей и подводных лодок, протектором обычно служат цинковые пластины. Используется данный способ и при эксплуатации подземных трубопроводов.
Еще одним современным методом обеспечения коррозионной стойкости является легирование. Так, сталь гораздо лучше сопротивляется воздействию агрессивной среды при добавлении в ее состав хрома. Устойчивость сталей к воздействию кислот повышается при добавлении никеля. Если добавить в сплав медь, возрастет сопротивляемость коррозии в кислой среде при высоких температурах.
Антикоррозионная защита металлических конструкций и изделий имеет огромное народнохозяйственное значение, потому что увеличивает срок эксплуатации и увеличивает надежность механизмов и важных металлических сооружений (железных дорог и мостов, газо- и нефтепроводов, линий электропередач и т.д.).
www.ankoromsk.ru
способы защитить металл от ржавчины в быту, выбор покрытия
Интенсивное развитие производства стали, как правило, предполагает поиск новых средств и способов, которые позволяли бы предотвращать разрушение изделий из металла. Создание инновационных методик, связанных с защитой от коррозии, — это постоянный процесс. Изделия, сделанные практически из любого металла, могут терять свою работоспособность из-за воздействия химических и физических факторов извне. Последствия этого можно увидеть в виде ржавчины.
Разновидности коррозии
Перед тем как защитить металл от ржавчины, следует узнать о существующих видах. Способ обеспечения антикоррозийной защиты находится в прямой зависимости от условий применения деталей. Потому принято выделять следующие типы:
- коррозия, которая связана с явлениями атмосферного характера;
- разрушение структуры металла в воде из-за наличия в ней солей и бактерий;
- деструктивные процессы, происходящие в грунте (почвенная коррозия).
Способы антикоррозионной защиты при этом должны подбираться в индивидуальном порядке, руководствуясь тем, в каких условиях будет эксплуатироваться изделие из металла.
Что касается типов поражения конструкций, то они могут быть следующими:
- ржавчина находится на всей поверхности изделия отдельными участками или сплошным покрытием;
- имеет вид пятен и проникает вглубь элемента;
- разрушает молекулы металла, приводя к трещинам;
- масштабное ржавление, при котором разрушается не только поверхность, но и более глубокие слои.
Типы разрушения бывают и комбинированными. В некоторых ситуациях их очень сложно определить на глаз, особенно при точечном ржавлении.
Принято выделять химическую коррозию. При контакте с нефтяными продуктами, спиртами и иными агрессивными веществам происходит особая реакция, которая сопровождается высокой температурой и выделениями газа.
При электрохимической коррозии поверхность металлического сплава соприкасается с водой (электролитом). При этом осуществляется диффузия материала. Электролит обуславливает появление электротока, а электроны металла замещаются и приходят в движение, в результате чего возникает ржавчина.
Обеспечение защиты от коррозии и выплавка стальных изделий — две взаимосвязанные вещи. Коррозия причиняет существенный ущерб постройкам хозяйственного или промышленного назначения. Кроме того, этот процесс может привести к катастрофе, если говорить, например, об опорах электропередач, мостах, заграждениях и т. д.
Защита от коррозии в промышленности и быту
Необходимо обеспечить металлу надежную защиту от коррозии. Все условия, когда требуется защита металлов от коррозии, кратко можно поделить на промышленные и бытовые.
В промышленности существует несколько вариантов антикоррозийной защиты:
- Нанесение на поверхность стали каких-то других металлов. При этом на изделии образуется защитное покрытие. Зачастую для данной цели применяется алюминий, кобальт и хром.
- Применение специальных протекторов и анодов. При контакте детали с водой происходит разрушение протектора, который образует защитное покрытие. Такая методика часто используется в производстве деталей для морских буровых установок и судов.
Промышленные способы обеспечения антикоррозийной защиты очень разнообразны. К ним относится и покрытие специальной стекловолоконной эмалью, и химическая защита, и многие другие.
Антикоррозийная защита материала в домашних условиях подразумевает применение ЛКМ-покрытий и химических средств. Свойства защитного плана обеспечивают сочетанием разных элементов: смол на основе силикона, ингибиторов, полимеров, металлической стружки и пудры.
Следует отметить, что перед окрашиванием детали, ее нужно обработать специальным преобразователем коррозии или грунтовкой, иначе ее эксплуатационные свойства будут быстро уменьшаться.
Сегодня в продаже встречается несколько разновидностей преобразователей ржавчины:
- Средства-грунтовки. Характеризуются высокой адгезией с металлическими поверхностями, способствуют выравниванию покрытия перед покраской. Во многих грунтовках содержатся ингибиторы, тормозящие коррозийные процессы. Кроме того, заблаговременное нанесение слоя грунтовки позволяет сэкономить на окрашивании.
- Химические препараты. Преобразуют окись железа в более безопасные вещества, которым не страшна коррозия. Такие средства называются стабилизаторами.
- Составы, преобразующие ржавчину в обычные соли.
- Масла и смолы, уплотняющие и связывающие ржавчину, обеспечивая ее нейтрализацию.
Специалисты советуют подбирать краску и грунтовку какого-то одного производителя, чтобы их химический состав не имел особых отличий.
Краски для покрытия металлических изделий
Краски, предназначенные для обработки металлических поверхностей, бывают обычными и термостойкими. В большинстве случаев применяются три типа составов: эпоксидные, акриловые и алкидные. Есть и специальные краски антикоррозийного типа, которые обладают следующими достоинствами:
- эффективно защищают покрытие от атмосферных воздействий и перепадов температур;
- с легкостью наносятся валиком, кисточкой или распылителем;
- многие из них являются быстросохнущими;
- обладают широким выбором расцветок;
- отличаются долговечностью.
Что касается самых недорогих и доступных средств, то тут следует обратить внимание на обыкновенную серебрянку. В составе этого покрытия есть алюминиевая пудра, образующая защитную пленку на обработанном им изделии.
Этапы работ по борьбе с коррозией в быту
Методы борьбы с коррозией металлов предполагают определенную последовательность. Следует перечислить основные этапы этой работы:
Перед тем как наносить преобразователь или грунтовую смесь, поверхность необходимо полностью очистить от маслянистых пятен, следов коррозии и различного рода загрязнений. Для этих мер можно воспользоваться болгаркой или щетками с металлическим ворсом.
- После этого можно приступать к нанесению слоя грунтовки, которая затем должна впитаться и как следует просохнуть.
- Далее на поверхность наносится пара слоев. Перед тем как наносить второй слой, нужно дождаться полного высыхания первого. В процессе работы обязательно нужно пользоваться защитными очками, перчатками и специальным респиратором, так как все применяемые вещества и составы являются токсичными.
Антикоррозийная защита металлических сплавов — очень непростой процесс. В промышленности он начинается на стадии расплавления стали. Производители ЛКМ-покрытий занимаются совершенствованием своей продукции, увеличивая ее долговечность и стойкость.
obrabotkametalla.info
основные методы и их особенности
Одной из серьезных угроз для инструментов и конструкций, выполненных из металла, является коррозия. По этой причине большую актуальность приобретает проблема их защиты от столь неприятного процесса. При этом сегодня известно немало методов, которые позволяют достаточно эффективно решить эту проблему.Антикоррозионная защита — зачем она нужна
Коррозия представляет собой процесс, сопровождающийся разрушением поверхностных слоев конструкций из стали и чугуна, возникающий в результате электрохимического и химического воздействия. Негативным следствием этого становится серьезная порча металла, его разъедание, что не позволяет использовать его по назначению.
Экспертами было проведено достаточно доказательств тому, что ежегодно порядка 10% от общего объема добычи металла на планете уходит на устранение потерь, связанных с воздействием коррозии, из-за которой происходит расплавление металлов и полная потеря эксплуатационных свойств металлическими изделиями.
При первых признаках воздействия коррозии изделия из чугуна и стали становятся менее герметичными, прочными. В то же время ухудшаются такие качества, как теплопроводность, пластичность, отражательный потенциал и некоторые иные важные характеристики. В дальнейшем конструкции и вовсе нельзя применять по назначению.
Вдобавок к этому именно с коррозией связывают большинство производственных и бытовых аварий, а также и некоторые экологические катастрофы. Трубопроводы, используемые для транспортировки нефти и газа, имеющие значительные участки, покрытые ржавчиной, могут в любой момент лишиться своей герметичности, что может создать угрозу для здоровья людей и природы в результате прорыва подобных магистралей. Это дает понимание того, почему так важно предпринимать меры по защите конструкций из металла от коррозии, прибегая к помощи традиционных и новейших средств и методов.
К сожалению, пока не удалось создать такой технологии, которая бы смогла полностью защитить стальные сплавы и металлы от коррозии. При этом имеются возможности для задержания и уменьшения негативных последствий подобных процессов. Эта задача решается посредством использования большого количества антикоррозионных средств и технологий.
Предлагаемые сегодня методы борьбы с коррозией могут быть представлены в виде следующих групп:
- Использование электрохимических методов защиты конструкций;
- Создание защитных покрытий;
- Разработка и производство новейших конструкционных материалов, демонстрирующих высокую стойкость к коррозионным процессам;
- Добавление в коррозионную среду особых соединений, благодаря которым можно замедлить распространение ржавчины;
- Грамотный подход к выбору подходящих деталей и конструкций из металлов для сферы строительства.
Защита изделий из металла от коррозии
Обеспечить способность защитного покрытия выполнять поставленные перед ним задачи можно за счет целого ряда специальных свойств:
- Устойчивость к износу и высокий уровень твердости;
- Повышенные характеристики прочности сцепления с поверхностью обрабатываемого изделия;
- Наличие коэффициента теплового расширения, предусматривающего незначительное отклонение от расширения защищаемой конструкции;
- Высокий уровень защиты от негативного воздействия со стороны вредных факторов внешней среды.
Создавать подобные покрытия следует тем расчетом, чтобы они располагались на всей площади конструкции в виде максимально равномерного и сплошного слоя.
Доступные сегодня защитные покрытия для металла могут быть классифицированы на следующие типы:
- металлические и неметаллические;
- органические и неорганические.
Подобные покрытия получили широкое распространение во многих странах. Поэтому им будет уделено особое внимание.
Борьба с коррозией при помощи органических покрытий
Чаще всего для защиты металлов от коррозии прибегают к такому эффективному методу, как использование лакокрасочных составов. Этот метод на протяжении многих лет демонстрирует высокую эффективность и несложность в плане реализации.Использование подобных соединений в борьбе против ржавчины предусматривает достаточно преимуществ, среди которых простота и доступная цена не являются единственными:
- Используемые покрытия могут придавать обрабатываемому изделию различный цвет, в результате это позволяет не только надежно защитить изделие от ржавчины, но и обеспечить конструкциям более эстетичный внешний вид;
- Отсутствие сложностей с реставрацией защитного слоя в случае его повреждения.
Увы, однако у лакокрасочных составов имеются и определенные недостатки, к числу которых нужно отнести следующие:
- низкий коэффициент термической стойкости;
- низкая устойчивость в водной среде;
- низкая стойкость к воздействию механического характера.
Это вынуждает, чему не противоречат требования действующих СНиП, прибегать к их помощи в ситуации, когда изделия подвергаются воздействию со стороны коррозии с максимальной скоростью 0,05 мм в год, при этом расчетный срок службы не должен превышать 10 лет.
Ассортимент предлагаемых сегодня на рынке лакокрасочных составов может быть представлен в виде следующих элементов:
- Краски. Под ними подразумеваются суспензии пигментов, характеризующихся минеральной структурой;
- Лаки. Представлены в виде растворов и масел, присутствующих в растворителях органического происхождения. При их использовании эффект достигается лишь по завершении полимеризации смолы или масла или же в момент испарения, вызванного воздействием дополнительных катализаторов или же нагревом;
- Пленкообразователи. Речь идет о природных и искусственных соединениях. Среди них наибольшую известность получила олифа, которую используют в целях защиты конструкций из стали и чугуна;
- Эмали. Имеют вид лаковых растворов, содержащих группу подобранных пигментов в измельченном виде;
- смягчители и разнообразные пластификаторы. Сюда следует отнести адипиновую кислоту, представленную в виде эфира, дибутилфтолат, касторовое масло, трикрезилфосфат, каучук, а также иные элементы, благодаря которым можно повысить эластичность защитного слоя;
- этилацетат, толуол, бензин, спирт, ксилол, ацетон и другие. К помощи перечисленных компонентов прибегают для улучшения адгезии используемых лакокрасочных составов;
- Инертные наполнители. Представлены в виде мельчайших частиц асбеста, талька, мела и каолина. Благодаря их применению пленки приобретают повышенную устойчивость к коррозии, при этом удается добиться уменьшения расхода иных компонентов лакокрасочных покрытий;
- Пигменты и краски;
- Катализаторы, которые в среде специалистов именуются как сиккативы. Их польза заключается в сокращении времени, необходимого для высыхания защитных составов. Наибольшее распространение получили кобальтовые и магниевые соли жирных органических кислот.
При выборе того или иного лакокрасочного состава следует обращать внимание на условия эксплуатации обрабатываемых конструкций из металла. Применять материалы на основе эпоксидных элементов желательно для тех изделий, которые будут эксплуатироваться в атмосферах, содержащих испарения хлороформа, двухвалентного хлора, а также для обработки изделий, которые планируется использовать в разных типах кислот.
Высокую стойкость к кислотам демонстрируют и лакокрасочные материалы, содержащие полихлорвинил. Вдобавок к этому к ним прибегают в целях обеспечения защиты металла, который будет контактировать с маслами и щелочами. Если же возникает задача в обеспечении защиты конструкций, которые будут взаимодействовать с газами, то обычно выбор останавливают на материалах, содержащих полимеры.
Решая вопрос с предпочтительным вариантом защитного слоя, следует обращать внимания на требования отечественных СНиП, предусмотренных для конкретной отрасли промышленности. Подобные саннормы содержат перечень таких материалов и способов защиты от коррозии, к которым допускается прибегать, а также те, которые не следует применять. Скажем, если обратиться к СНиПу 3.04.03-85, то там представлены рекомендации по защите строительных сооружений различного назначения:
- систем трубопроводов, используемых для транспортировки газа и нефти;
- обсадных стальных труб;
- тепломагистралей;
- конструкций, выполненных из стали и железобетона.
Обработка неметаллическими неорганическими покрытиями
Метод электрохимической или химической обработки позволяет создавать на изделиях из металла особые пленки, не допускающие негативное воздействие со стороны коррозии. Обычно для этой цели применяются фосфатные и оксидные пленки, при создании которых учитываются требования СНиП, поскольку подобные соединения отличаются по механизму защиты для различных конструкций.Фосфатные пленки
Останавливать выбор на фосфатных пленках рекомендуется, если необходимо обеспечить защиту от коррозии изделий из цветных и черных металлов. Если обратиться к технологии подобного процесса, то он сводится к помещению изделий в раствор цинка, железа или марганца в виде смеси с кислыми фосфорными солями, которые предварительно нагреты до отметки 97 градусов. Создаваемая пленка представляется отличной основой, чтобы в дальнейшем можно было покрыть ее лакокрасочным составом.
Важным моментом является то, что долговечность фосфатного слоя находится на довольно низком уровне. Также он обладает и другими недостатками — низкой эластичностью и прочностью. К фосфатированию прибегают в целях обеспечения защиты деталей, эксплуатация которых проходит в условиях высоких температур или соленой водной среды.
Оксидные пленки
Свою сферу применения имеют и оксидные защитные пленки. Они создаются при воздействии на металлы растворами щелочей посредством использования тока. Довольно часто для оксидирования применяют такой раствор, как едкий натр. Среди специалистов процесс создания оксидного слоя часто именуется воронением. Это обусловлено созданием на поверхности мало и высокоуглеродистых сталей пленки, имеющей привлекательный черный цвет.
Способ оксидирования является востребованным в тех случаях, когда возникает задача по сохранению изначальных геометрических размеров. Чаще всего защитное покрытие подобного типа создается на точных приборах и стрелковом вооружении. Обычно пленка имеет толщину не более 1,5 микрона.
Дополнительные способы
Существуют и другие способы защиты от коррозии, которые основываются на использовании неорганических покрытий:
- Пассивирование. Суть его сводится к помещению обрабатываемого изделия из металла в растворы нитратов или хроматов.
- Анодирование. Для этого метода применяют специальные ванны, для приготовления которых используют щавелевую кислоту (5-10%), хромовый ангидрид (3%) и серную кислоту (190 грамм на литр раствора).
- Эмалирование. В основе этого метода лежит использование сочетания компонентов, представленных сплавленным полевым шпатом, цинком, мелом, песком, титаном и иными веществами.
Заключение
У каждого инструмента и конструкции, которая выполнена из стали, имеется ограниченный срок службы. При этом не всегда изделие может демонстрировать его в том виде, который заложен изначально производителем. Этому могут помешать различные негативные факторы, в том числе и коррозия. В целях защиты от неё приходится прибегать к различным методам и средствам.
Учитывая всю важность процедуры по защите от коррозии, необходимо правильно подобрать метод, а для этого важно учитывать не только условия эксплуатации изделий, но и их изначальные свойства. Подобный подход позволит обеспечить надежную защиту от ржавчины, в результате изделие сможет гораздо дольше использоваться по своему прямому назначению.
Оцените статью: Поделитесь с друзьями!stanok.guru
Лучшие способы защиты от коррозии металлов
Под воздействием внешних факторов (жидкости, газы, агрессивные химические соединения) разрушаются любые материалы. Не являются исключением и металлы. Коррозийные процессы нейтрализовать полностью невозможно, но вот снизить их интенсивность, повысив тем самым эксплуатационный срок металлоконструкций или иных, в состав которых входит «железо», вполне возможно.
Способы антикоррозийной защиты
Все способы защиты от коррозии можно условно классифицировать как методики, которые применимы или до начала эксплуатации образца (группа 1), или уже после его ввода в строй (группа 2).
Первая
- Повышение сопротивляемости «химическому» воздействию.
- Исключение прямого контакта с агрессивными веществами (изоляция поверхностная).
Вторая
- Снижение степени агрессивности окружающей среды (в зависимости от условий эксплуатации).
- Использование ЭМ полей (к примеру, «наложение» внешних эл/токов, регулирование их плотности и ряд других методик).
Применение того или иного способа защиты определяется индивидуально для каждой конструкции и зависит от нескольких факторов:
- вид металла;
- условия его эксплуатации;
- сложность проведения антикоррозийных мероприятий;
- производственные возможности;
- экономическая целесообразность.
В свою очередь, все методики подразделяются на активные (подразумевающие постоянное «воздействие» на материал), пассивные (которые можно охарактеризовать как многоразового применения) и технологические (использующиеся на этапе изготовления образцов).
Активные
Катодная защита
Целесообразно использовать, если среда, с которой контактирует металл – электропроводящая. На материал подается (систематически или постоянно) большой «минусовой» потенциал, который делает в принципе невозможным его окисление.
Протекторная защита
Заключается в катодной поляризации. Образец связывается контактом с материалом, который более подвержен окислению в данной токопроводящей среде (протектором). По сути, он является своего рода «громоотводом», принимая на себя весь «негатив», который создают агрессивные вещества. Но такой протектор нуждается в периодической замене на новый.
Поляризация анодная
Применяется крайне редко и заключается в поддержании «инертности» материала по отношению к внешним воздействиям.
Пассивные (поверхностная обработка металла)
Создание защитной пленки
Одна из самых распространенных и малозатратных методик борьбы с коррозией. Для создания поверхностного слоя используются вещества, которые должны соответствовать следующим основным требованиям – быть инертными по отношению к агрессивным хим/соединениям, не проводить эл/ток и обладать повышенной адгезией (хорошо скрепляться с основой).
Все используемые вещества в момент обработки металлов находятся в жидком или «аэрозольном» состоянии, от чего зависит и способ их нанесения – окраска или напыление. Для этого применяются лакокрасочные составы, различные мастики и полимеры.
Прокладка металлоконструкций в защитных «желобах»
Это характерно для разного вида трубопроводов и коммуникаций инженерных систем. В данном случае роль изолятора играет воздушная «прослойка» между внутренними стенками канала и поверхностью металла.
Фосфатирование
Металлы подвергаются обработке специальными средствами (окислителями). Они вступают с основой в реакцию, в результате чего на ее поверхности происходит отложение малорастворимых хим/соединений. Довольно эффективный способ защиты от влаги.
Покрытие более устойчивыми материалами
Примерами использования такой методики служат часто встречающиеся в быту изделия с хромировкой (о хромировании читайте здесь), с серебрением, «оцинковкой» и тому подобное.
Как вариант – защита керамикой, стеклом, покрытие бетоном, цементными растворами (обмазка) и так далее.
Пассивация
Смысл заключается в том, чтобы резко снизить химическую активность металла. Для этого производится обработка его поверхности соответствующими спецреактивами.
Снижение агрессивности среды
- Использование веществ, которые снижают интенсивность коррозийных процессов (ингибиторов).
- Осушка воздуха.
- Его хим/очистка (от вредных примесей) и ряд других методик, которые могут применяться и в быту.
- Гидрофобизация почвы (засыпки, введение в нее спецвеществ) с целью снижения агрессивности грунта.
Обработка ядохимикатами
Используется в случаях, когда есть вероятность развития так называемой «биокоррозии».
Технологические способы защиты
Легирование
Самый известный способ. Смысл в том, чтобы на основе металла создать сплав, инертный по отношению к агрессивным воздействиям. Но реализуется только в промышленных масштабах.
Как следует из приведенной информации, не все методики антикоррозийной защиты можно применять в быту. В этом плане возможности «частника» существенно ограничены.
ismith.ru
Альтернативные способы антикоррозионной защиты судов
В мире создано бесчисленное количество специализированных лакокрасочных материалов, повышающих стойкость корабельных конструкций к воздействиям атмосферы и морской воды. Однако до сих пор не ясно, как предохранять от коррозии подводные части судов и сварные швы оборудования, работающего в самых экстремальных условиях.
Для того чтобы судовое оборудование не теряло своей эффективности, инженеры должны быть знакомы со всеми технологиями, продлевающими срок его эксплуатации. Кроме того, в перечень их обязанностей включено умение определять, какие именно детали подлежат ремонту, а какие нуждаются в замене. При этом им необходимо просчитывать возможный объем затрат на восстановительные работы.
На сегодняшний день существуют различные способы защиты морских конструкций, но при выборе одного из них важно учитывать следующие параметры: место нанесения покрытия (будет ли поверхность погружаться под воду), требуемый срок службы, очередность выполнения оперативных задач, время монтажа и, разумеется, ограниченность бюджета.
Если средства позволяют, инженеры предпочитают останавливаться на износостойких металлических сплавах, способных противостоять экстремальному воздействию морской среды. Однако известны и другие менее затратные решения.
Когда такие части судна, как вентили, насосы, соединительные детали, необходимо предохранить от повреждений, лучшим выходом становится нанесение тонкого защитного слоя на сварные швы. Подобное покрытие должно выдерживать высокие нагрузки и не терять своих эксплуатационных характеристик от нахождения в щелочной среде.
Защита сварных швов обязательна, если речь идет о корабельных конструкциях, погружаемых под воду, к примеру, винтах и грейферах. Как правило, при их изготовлении используются разнородные металлы, которые в значительной степени подвержены электрохимической коррозии. Нанесение дополнительного покрытия на швы не только увеличит срок службы нового оборудования, но и восстановит сооружения, которые уже подверглись корродированию.
Защита сварных швов обязательна, если речь идет о корабельных конструкциях, погружаемых под воду
Укрепление швов может быть полезным даже для приборов, находящихся в закрытых помещениях, в частности, в машинном отделении. Обычная нержавеющая сталь применяется для предохранения фланцевых уплотнений вентилей и насосов. Если среда особенно агрессивна, рекомендуется использовать сталь более высокого качества, а также хромоникелевые и твердые сплавы. Крупные партии этих металлов очень дороги, однако нанесение тонкого слоя (порядка 3 мм) гарантирует отличную стойкость, что сократит дальнейшие расходы на ремонт.
Защитные материалы
В числе металлов, на которые стоит обращать внимание, − аустенитная, ферритная/мартенситная, двухфазная нержавеющая сталь и некоторые хромоникелевые сплавы. Главным недостатком аустенитной стали считается недостаточная стойкость к агрессивным воздействиям. Двухфазные и хромоникелевые материалы при сварке проявляют те же защитные свойства, что и углеродистая сталь.
Перед восстановлением все оборудование обычно обрабатывают, а затем автоматически наплавляют сварной шов или прибегают для этих целей к ручной сварке. Одним из наиболее эффективных материалов является никель-алюминиевая бронза.
Способы защиты
Углеродистая и низколегированная сталь наравне с коррозионно-устойчивыми сплавами применяются уже в течение нескольких лет и представляют собой хорошую альтернативу твердым сплавам как с технической, так и с экономической точки зрения.
Если детали сделаны из обычной стали, то на сварные швы можно нанести специальный защитный слой, который впоследствии не разрушится и не будет смещаться в сторону.
Технология сварки
После первичного осмотра поверхностей, требующих дополнительной обработки, специалисты могут выбрать устраивающий их способ сварки и подходящее для этих целей решение. Защита швов предполагает применение разнородных материалов. Более детально стоит рассмотреть несколько из них.
В первую очередь внимания заслуживает дуговая сварка вольфрамовым электродом (GTAW). В качестве электрода используется стержень, изготовленный из вольфрама, температура его плавления превышает максимальную температуру при сварочных работах. Сам процесс осуществляется в среде защитного газа (аргон, гелий, азот и их смесях) для предохранения шва и электрода от атмосферного воздействия, а также для устойчивого горения дуги.
Вольфрамовый электрод закрепляется в токопроводящем устройстве специальной горелки, к которой по шлангам подводится токоведущий провод и аргон. Истекающая из сопла горелки струя инертного газа оттесняет воздух и надежно защищает электрод, дугу и сварочную ванну от окисления и азотирования. Если возникает необходимость в добавочном (присадочном) металле для усиления шва (валика), то в дугу подается присадочная проволока, как правило, с таким же составом, что и свариваемый металл.
Поскольку данный процесс предполагает надежную изоляцию от кислорода и азота, то этот способ подходит главным образом для скрепления изделий из титана, циркония алюминия, магния и других химически активных металлов либо для изготовления конструкций из коррозиеустойчивой стали.
Дуговая сварка вольфрамовым электродом позволяет работать даже с небольшими участками диаметром 15 мм, кроме того, такой метод приемлем для неоднородных поверхностей, при контакте с которыми постоянно приходится регулировать положение сварочной головки. Среди таких областей могут быть фланцевые уплотнения или целые клапанные корпусы с отверстиями. Аналогичным образом обстоит ситуация с объектами неправильной формы или внутренними пространствами насосов и вентилей.
Наплавка стальным электродом (GMAW) используется достаточно ограниченно ввиду трудности получения сварного соединения без отбеливания и образования трещин. Такой способ применяют для заварки дефектов отливок и ремонта металлических деталей. Лучшие результаты достигаются при работе с электродами с карбидообразующими элементами в покрытии, в частности, содержащими до 70% ванадия. Он, поступая в шов, связывает углерод основного металла в мелкодисперсные карбиды ванадия, в результате чего структура шва получается ферритной с включением карбидов ванадия. По этой причине углерод шва не влияет на образование цементита, так как почти целиком используется для получения карбида ванадия, следовательно, не происходит отбеливания.
При сварке электродами поверхность должна быть хорошо очищена. Сначала в стенки наплавляют облицовочные валики электродами диаметром 3 мм, не допуская разогрева металла, делая наплавку вразброс. После этого заполняют разделку отдельными валиками электродов, не разогревая деталь. Работу следует выполнять медленно.
Сварка стальным электродом, наряду с электрошлаковым методом и сваркой под флюсом, применяются в том случае, если поверхность имеет большую площадь. Высокий коэффициент наплавки позволяет говорить об их экономичности. Существуют и другие способы обработки, которые не подразумевают использование стандартных одножильных проводов. Они подходят в основном для широких поверхностей, подверженных сильному истиранию.
Подбор типа сварки определяется несколькими факторами: площадью участка, его доступностью, видом сплава, толщиной слоя, пределом содержания химических элементов, положением шва при сварке и стандартами неразрушающего контроля. Как правило, автоматическая сварка обеспечивает лучший коэффициент наплавки и оптимальное качество нанесения состава, соответствующее результатам специальных оценочных испытаний. Механизация процесса требуется, если некоторые из областей не представляется возможным покрыть вручную.
Углеродистая и низколегированная сталь наравне с коррозионноустойчивыми сплавами представляют собой хорошую альтернативу твердым сплавам
К сварке под флюсом обращаются при работе с большими поверхностями, которые легко поддаются обработке. Для этих целей применяются провода диаметром от 2,4 мм, поэтому подложка должна быть достаточно толстой, чтобы выдерживать высокую тепловую нагрузку и интенсивность самого процесса.
Относительно недавно были разработаны методы, при которых отбираются провода диаметром 1,2 мм. Это позволяет наносить покрытие на более тонкие детали, контролировать толщину наплавленного металла и при этом сохранять скорость сварки 5 кг в час. Существуют комбинации расходных материалов, которые можно наносить в один слой при сварке под флюсом. Они сочетаются с двухфазной и ферритной/мартенситной сталью.
Ранее после покрытия швов металлом применялась повторная обработка, но с развитием технологий ее стали использовать все реже, зачищая лишь некоторые участки. Впрочем, это не относится к местам уплотнения или прилегания прокладки, потому что их подготовка требует большой осторожности.
Метод наплавки слоя сварного шва в настоящее время очень распространен в нефтегазовой, химической, энергетической и судостроительной отраслях промышленности, поскольку подготовка к нему не требует особых денежных затрат и проводится достаточно быстро.
Выбор способов защиты огромен, что подразумевает обычную ручную дуговую сварку и тепловую сварку вольфрамовым электродом (TIG) с использованием множества головок, и даже лазерный метод. Несколько лет назад некоторые из металлов плохо поддавались обработке, но эту проблему удалось решить за счет приведения в соответствие требований к качеству защитного материала стали с предписаниями к уровню подготовки поверхностей.
Новаторский проект
Эффективность защиты швов в судостроительной отрасли была доказана несколькими компаниям, в том числе и Arc Energy. Ее специалисты смогли разработать программу по сокращению расходов при строительстве судов. Два последних проекта включали в себя изготовление 24 труб для системы циркуляции морской воды, которая охлаждала ядерные реакторы на двух кораблях класса Astute, сконструированных фирмой BAE Systems.
Разработчики поставили перед собой цель повысить производительность и максимально снизить затраты. Так как на некоторых судах применялись трубные заготовки из дорогого медно-никелевого сплава, возникла необходимость в поиске высококлассной альтернативы. Недостатком сплава также оказалась длительность поставки, что подрывало графики строительства. В качестве замены было предложено использовать углеродистую сталь в сочетании с подходящим коррозиеустойчивым сплавом. Материалы наносили на участки, которые были подвержены воздействию морской воды.
Восемь двухметровых стальных труб и шестнадцать метровых концевых секций диаметром 430 мм были полностью покрыты сплавом, даже в местах уплотнения. В соответствии со стандартом ASTM A694 F65, в качестве основного материала Arc Energy применяла кованую сталь, подходящую для систем, работающих при высоком давлении. Медно-никелевый сплав, отличающийся стойкостью в хлоридной среде, служил сварочным материалом. Чтобы обеспечить химическую совместимость подложки и сплава, был нанесен слой толщиной 5 мм. Кроме того, для лучшей прочности поверхность подверглась предварительной обработке.
После нанесения покрытия, последующей обработки и неразрушающего контроля специалисты компании изготовили специальные детали для скрепления трех основных компонентов секции. Наружную поверхность сооружения покрыли алюминиевым составом. Также было решено спроектировать специальные балки и опорные конструкции, провести чистовую обработку.
Еще один проект, реализованный инженерами Arc Energy, представлял собой защиту некоторых труднодоступных частей судна Astute. Эти детали должны быть выполнены из того же типа стали, что и весь корпус. Поскольку сталь не обеспечивала оптимального уровня коррозионной устойчивости и герметичности, а некоторые участки вступали в непосредственный контакт с морской водой, возникла необходимость в защитном покрытии для сварных швов. Выбор был сделан в сторону сплава Monel 400 (70% никеля и 30% меди).
Как можно было убедиться, защита сварных швов судового оборудования обладает рядом преимуществ. Она предназначена для наиболее уязвимых зон и позволяет заменить дорогостоящие антикоррозионные материалы на более экономичные. Такой способ универсален и не зависит от размера и формы объектов, будь то палубный насос или коробка силовой передачи, так как в любом случае можно подобрать удовлетворяющий всем запросам сплав.
Данная технология защиты широко применяется на нефтяных платформах. Инженеры-проектировщики отмечают существенную выгоду и возросший срок службы материалов, что возможно только при работе с проверенными поставщиками, чья продукция отвечает требованиям стандарта ISO 3834, регулирующего качество сварочного процесса.
Алан Робинсон
www.lkmportal.com
виды, особенности обработки :: BusinessMan.ru
Металл является одним из самых востребованных материалов, применяемых в строительстве и промышленности. Несмотря на то что в некоторых областях его успешно заменяет легковесный и более практичный стеклокомпозит, актуальность традиционных конструкций сохраняется на довольно высоком уровне. Способствуют этому и применение дополнительных мер обработки материала, исключающих негативные факторы эксплуатации. Среди таких действий выделяется антикоррозионная защита металлоконструкций, благодаря которой технологи исключают поражение ржавчиной. В итоге увеличивается срок службы конструкций, на протяжении которого сохраняются оптимальные технико-физические характеристики объекта.
Общие сведения об антикоррозийной защите металла
Защита металлической поверхности от коррозии предусматривает наружную обработку материала специальными средствами, которые формируют слой, предотвращающий негативные процессы разрушения структуры. В качестве основы для обрабатывающих компонентов могут рассматриваться лакокрасочные материалы, те же металлы и сплавы. Важно отметить, что антикоррозионная защита металлоконструкций не предполагает универсальность. В зависимости от условий эксплуатации объекта, характеристик конкретной марки используемого металла и возлагаемых на него конструкцию нагрузок, подбирается конкретное средство обработки. Различаются и сами подходы к обеспечению покрытия поверхностей, что объясняется разнообразием спектра угроз, от которых защищается металл. Функция антикоррозийного покрытия редко сводится только лишь к созданию барьера перед ржавчиной – нанесенный слой, как правило, оберегает конструкцию от биологических и механических воздействий.
Проект защиты от коррозии
Оценкой характеристик конкретного металла, а также условий его использования занимаются специалисты, разрабатывающие проект защиты. Для каждой сферы применения конструкций предусматриваются свои нормативы, которые описывает ГОСТ. Антикоррозионная защита металлоконструкций, используемых в регионах с расчетной температурой воздушной среды до — 40 °С, к примеру, ориентируется на требования ГОСТ 9.401. В этом случае материал для покрытия должен подбираться так, чтобы особенности его соответствовали требованиям к морозостойкости. Разумеется, кроме температурных воздействий рассчитываются и другие контакты металлической структуры с агрессивными средами. Если внешние воздействия предполагают неагрессивный характер, то проект может рекомендовать использование защитно-декоративных покрытий.
Разновидности защитных средств
Существуют разные подходы к разделению защитных средств от коррозии. В частности, распространена классификация по назначению целевого материала. Выделяют покрытия, которые используются в обработке индустриальных конструкций, морских судов, трубопроводов, резервуаров и объектов, эксплуатируемых на открытом воздухе. Как видно, в каждом случае предполагаются свои особенности взаимодействия материала с окружающей средой. С поправкой на характер эксплуатации и выбирается антикоррозионная защита металлоконструкций. Виды покрытий для трубопроводов, например, в основе своей представлены лакокрасочными составами, а для защиты судов чаще применяются металлизированные напыления. Впрочем, ответственные с точки зрения эксплуатации металлоконструкции редко обрабатываются одним средством. Чаще всего применяется комплекс мер, включающий и технологии металлизированного напыления, и лакокрасочные составы.
Методы обработки защитным покрытием
К наиболее распространенным и традиционным способам антикоррозийной защиты стоит отнести лакокрасочные покрытия. Данная методика подходит для бытового применения, если нужно облагородить и в то же время уберечь от разрушения металлический забор, лестницу или кровельное покрытие из профнастила. Более эффективные методы связаны уже с промышленной обработкой. В эту категорию входит антикоррозионная защита металлоконструкций путем оцинковки, термической обработки, легированием, фаолитированием и т. д. Однако, чем сложнее и эффективнее методика, тем она дороже. Применение современных технологичных способов не всегда оправдывается экономически, даже если речь идет о промышленном использовании конструкций. Теперь стоит детальнее рассмотреть конкретные методики антикоррозийной обработки.
Нанесение лакокрасочных покрытий
Основой для разработки специализированных составов, способных предотвратить коррозийные процессы, зачастую выступают традиционные лакокрасочные смеси. За счет внесения в состав особых растворителей, пластификаторов и пигментов достигаются оптимальные качества покрытия. Например, эмаль для антикоррозионной защиты металлоконструкций должна обладать повышенными свойствами к адгезии и в то же время формировать надежный с точки зрения механической безопасности слой. Металлические конструкции обычно используют в суровых условиях, поэтому физическая стойкость является одним из главных направлений совершенствования защитных средств. Что касается технологии обработки, то она реализуется классическим способом с применением малярного инструмента.
Холодное цинкование
Второй по популярности и весьма эффективный метод защиты поверхностей от коррозии. В процессе реализации этой технологии объект погружается в расплав, который в дальнейшем и становится тем самым барьером перед угрозой ржавчины. Надо отметить, что по данной методике чаще всего обрабатываются стальные конструкции, а также соединяющие элементы в виде болтов и гаек. Нередко используют и дополнительные операции обработки, за счет которых укрепляется антикоррозионная защита металлоконструкций. СНиП под номером 2.01-19-2004, в котором описаны способы защиты строительных конструкций, указывает на возможность использования в качестве альтернативы или дополнения технологий хроматирования и кадмирования. После этого наносится финальное лакокрасочное покрытие.
Алитирование
Еще один способ металлизации конструкций, повышающий сопротивляемость поверхности материала к процессам коррозии. В качестве активного вещества используют порошкообразные смеси на основе ферроалюминия. Если предыдущий метод предполагает покрытие в виде цинка, то в данном случае формируется алюминиевое напыление. На поверхность объекта наносится покрытие металлизированного порошка, после чего выполняется изоляционная обмазка. Далее элемент готовится к диффузионному отжигу и обрабатывается специальной краской на той же основе алюминия. Продолжаются антикоррозионные работы по защите металлоконструкций погружением конструкции в алюминиевый расплав с выдержкой, параметры которой варьируются в зависимости от требований к конечному результату. Как показывает практика, алитирование наделяет металлические поверхности наиболее высокими характеристиками износостойкости.
Фаолитирование
Данная технология представляет собой нечто среднее между основательной обработкой металлизированными смесями и поверхностным нанесением лакокрасочного слоя. Защитный барьер в этом случае формируется посредством смеси на основе кислотоупорной термореактивной пластмассы. В итоге получается антикоррозийное и теплозащитное покрытие, которое также противодействует воздействию химически агрессивных солей. К достоинствам, которыми обладает данная антикоррозионная защита металлоконструкций, относят возможность применения в условиях высоких температур. Однако, для создания качественного покрытия перед непосредственной обработкой следует предварительно наносить бакелитовую лаковую основу.
Заключение
Средства противодействия коррозии регулярно улучшаются и становятся все доступнее не только для крупных предприятий, но и для рядовых пользователей. Появление новых методик обработки упрощает и сам процесс нанесения покрытий. При этом немаловажную роль играет проектирование антикоррозионной защиты металлоконструкций, которые используются в составе коммуникационной инфраструктуры, промышленном оборудовании и строительстве. Дело в том, что материалы, формирующие защитный барьер, сами по себе зачастую выступают активными химическими реагентами. Поэтому возрастает ответственность технологов, подбирающих оптимальные средства для обработки металлов с учетом особенностей их эксплуатации.
businessman.ru