Π’ΠΎΡΠ½ΠΎ Π² ΡΡΠΎΠΊ (Π’ΠΎΡΠ½ΠΎ Π²ΠΎΠ²ΡΠ΅ΠΌΡ, Π’ΠΠ‘, Just In Time, JIT) β Π½Π°ΠΈΠ±ΠΎΠ»Π΅Π΅ ΡΠ°ΡΠΏΡΠΎΡΡΡΠ°Π½Π΅Π½Π½Π°Ρ Π² ΠΌΠΈΡΠ΅ Π»ΠΎΠ³ΠΈΡΡΠΈΡΠ΅ΡΠΊΠ°Ρ ΠΊΠΎΠ½ΡΠ΅ΠΏΡΠΈΡ. ΠΡΠ½ΠΎΠ²Π½Π°Ρ ΠΈΠ΄Π΅Ρ ΠΊΠΎΠ½ΡΠ΅ΠΏΡΠΈΠΈ Π’ΠΠ‘ Π·Π°ΠΊΠ»ΡΡΠ°Π΅ΡΡΡ Π² ΡΠ»Π΅Π΄ΡΡΡΠ΅ΠΌ: Π΅ΡΠ»ΠΈ ΠΏΡΠΎΠΈΠ·Π²ΠΎΠ΄ΡΡΠ²Π΅Π½Π½ΠΎΠ΅ ΡΠ°ΡΠΏΠΈΡΠ°Π½ΠΈΠ΅ Π·Π°Π΄Π°Π½ΠΎ, ΡΠΎ ΠΌΠΎΠΆΠ½ΠΎ ΡΠ°ΠΊ ΠΎΡΠ³Π°Π½ΠΈΠ·ΠΎΠ²Π°ΡΡ Π΄Π²ΠΈΠΆΠ΅Π½ΠΈΠ΅ ΠΌΠ°ΡΠ΅ΡΠΈΠ°Π»ΡΠ½ΡΡ ΠΏΠΎΡΠΎΠΊΠΎΠ², ΡΡΠΎ Π²ΡΠ΅ ΠΌΠ°ΡΠ΅ΡΠΈΠ°Π»Ρ, ΠΊΠΎΠΌΠΏΠΎΠ½Π΅Π½ΡΡ ΠΈ ΠΏΠΎΠ»ΡΡΠ°Π±ΡΠΈΠΊΠ°ΡΡ Π±ΡΠ΄ΡΡ ΠΏΠΎΡΡΡΠΏΠ°ΡΡ Π² Π½Π΅ΠΎΠ±Ρ ΠΎΠ΄ΠΈΠΌΠΎΠΌ ΠΊΠΎΠ»ΠΈΡΠ΅ΡΡΠ²Π΅, Π² Π½ΡΠΆΠ½ΠΎΠ΅ ΠΌΠ΅ΡΡΠΎ ΠΈ ΡΠΎΡΠ½ΠΎ ΠΊ Π½Π°Π·Π½Π°ΡΠ΅Π½Π½ΠΎΠΌΡ ΡΡΠΎΠΊΡ Π΄Π»Ρ ΠΏΡΠΎΠΈΠ·Π²ΠΎΠ΄ΡΡΠ²Π°, ΡΠ±ΠΎΡΠΊΠΈ ΠΈΠ»ΠΈ ΡΠ΅Π°Π»ΠΈΠ·Π°ΡΠΈΠΈ Π³ΠΎΡΠΎΠ²ΠΎΠΉ ΠΏΡΠΎΠ΄ΡΠΊΡΠΈΠΈ. ΠΡΠΈ ΡΡΠΎΠΌ ΡΡΡΠ°Ρ ΠΎΠ²ΡΠ΅ Π·Π°ΠΏΠ°ΡΡ, Π·Π°ΠΌΠΎΡΠ°ΠΆΠΈΠ²Π°ΡΡΠΈΠ΅ Π΄Π΅Π½Π΅ΠΆΠ½ΡΠ΅ ΡΡΠ΅Π΄ΡΡΠ²Π° ΡΠΈΡΠΌΡ, Π½Π΅ Π½ΡΠΆΠ½Ρ. Π’ΠΠ‘ ΡΠ²Π»ΡΠ΅ΡΡΡ ΡΠ°ΠΊΠΆΠ΅ ΠΎΠ΄Π½ΠΈΠΌ ΠΈΠ· ΠΎΡΠ½ΠΎΠ²Π½ΡΡ ΠΏΡΠΈΠ½ΡΠΈΠΏΠΎΠ² Π±Π΅ΡΠ΅ΠΆΠ»ΠΈΠ²ΠΎΠ³ΠΎ ΠΏΡΠΎΠΈΠ·Π²ΠΎΠ΄ΡΡΠ²Π°. ΠΡΡΠΎΡΠΈΡ. Π¨ΠΈΡΠΎΠΊΠΎΠ΅ ΡΠ°ΡΠΏΡΠΎΡΡΡΠ°Π½Π΅Π½ΠΈΠ΅ ΡΠΈΡΡΠ΅ΠΌΡ Π’ΠΠ‘ Π½Π°ΡΠ°Π»ΠΎΡΡ Ρ ΠΊΠΎΠ½ΡΠ° 50-Ρ Π³ΠΎΠ΄ΠΎΠ² Π₯Π₯ Π²., ΠΊΠΎΠ³Π΄Π° ΡΠΏΠΎΠ½ΡΠΊΠ°Ρ ΠΊΠΎΠΌΠΏΠ°Π½ΠΈΡ Toyota Motors, Π° ΠΏΠΎΡΠΎΠΌ ΠΈ Π΄ΡΡΠ³ΠΈΠ΅ Π°Π²ΡΠΎΠΌΠΎΠ±ΠΈΠ»ΡΠ½ΡΠ΅ ΠΊΠΎΠΌΠΏΠ°Π½ΠΈΠΈ Π―ΠΏΠΎΠ½ΠΈΠΈ, Π½Π°ΡΠ°Π»ΠΈ Π²Π½Π΅Π΄ΡΡΡΡ ΡΠΈΡΡΠ΅ΠΌΡ ΠΊΠ°Π½Π±Π°Π½. Π Π½Π°ΡΡΠΎΡΡΠ΅Π΅ Π²ΡΠ΅ΠΌΡ ΡΠΈΡΡΠ΅ΠΌΠ° Β«Π’ΠΎΡΠ½ΠΎ Π² ΡΡΠΎΠΊΒ» ΡΠΈΡΠΎΠΊΠΎ ΠΈΡΠΏΠΎΠ»ΡΠ·ΡΠ΅ΡΡΡ Π² Π―ΠΏΠΎΠ½ΠΈΠΈ, Π‘Π¨Π ΠΈ ΠΠ²ΡΠΎΠΏΠ΅. ΠΡΠΈΠ½ΡΠΈΠΏ Π’ΠΠ‘ ΠΌΠΎΠΆΠ½ΠΎ ΠΏΡΠΈΠΌΠ΅Π½ΡΡΡ ΡΠ°ΠΊΠΆΠ΅ ΠΈ Π΄Π»Ρ ΠΏΠΎΠ²ΡΡΠ΅Π½ΠΈΡ Π½Π°Π΄Π΅ΠΆΠ½ΠΎΡΡΠΈ ΡΠ΅ΡΠ΅ΠΉ (ΠΡΠΈΠ½ΡΠΈΠΏ Π΄ΠΆΠΈΡ-Π½Π°Π΄Π΅ΠΆΠ½ΠΎΡΡΠΈ). ΠΡΠ΅Π΄ΠΏΠΎΡΡΠ»ΠΊΠΈ Π²Π½Π΅Π΄ΡΠ΅Π½ΠΈΡ ΡΠΈΡΡΠ΅ΠΌΡ Π’ΠΠ‘.
ΠΠΎΠΌΠΏΠΎΠ½Π΅Π½ΡΡ ΡΠΈΡΡΠ΅ΠΌΡ Π’ΠΠ‘.
ΠΡΡΠ΅ΠΊΡΠΈΠ²Π½ΠΎΡΡΡ. Π£ΡΡΠ΅Π΄Π½ΡΠ½Π½ΡΠ΅ Π΄Π°Π½Π½ΡΠ΅, ΠΏΠΎΠ»ΡΡΠ΅Π½Π½ΡΠ΅ ΠΏΡΠΈ ΠΎΠ±ΡΠ»Π΅Π΄ΠΎΠ²Π°Π½ΠΈΠΈ Π±ΠΎΠ»Π΅Π΅ 100 ΠΎΠ±ΡΠ΅ΠΊΡΠΎΠ² (ΡΠΌ. Π²ΡΠΎΡΠΎΠΉ ΠΈΡΡΠΎΡΠ½ΠΈΠΊ Π² ΡΠ°Π·Π΄Π΅Π»Π΅ Β«ΠΠΈΡΠ΅ΡΠ°ΡΡΡΠ°Β»), ΠΎΠΊΠ°Π·Π°Π»ΠΈΡΡ ΡΠ°ΠΊΠΈΠΌΠΈ:
Π°Π΄Π°ΡΠ° Π»ΠΈΠΊΠ²ΠΈΠ΄Π°ΡΠΈΠΈ Π²ΡΠ΅Π³ΠΎ Π½Π΅Π½ΡΠΆΠ½ΠΎΠ³ΠΎ, Π»Π΅ΠΆΠ°ΡΠ°Ρ Π² ΠΎΡΠ½ΠΎΠ²Π΅ ΠΎΡΠ³Π°Π½ΠΈΠ·Π°ΡΠΈΠΈ Π±Π΅ΡΠ΅ΠΆΠ»ΠΈΠ²ΠΎΠ³ΠΎ ΠΏΡΠΎΠΈΠ·Π²ΠΎΠ΄ΡΡΠ²Π° Π½Π° ΠΏΡΠ΅Π΄ΠΏΡΠΈΡΡΠΈΠΈ, Π΄ΠΎΡΡΠ°ΡΠΎΡΠ½ΠΎ ΡΠ»ΠΎΠΆΠ½Π°, ΡΠ°ΠΊ, ΠΊΠ°ΠΊ Π½Π΅ΠΎΠ±Ρ ΠΎΠ΄ΠΈΠΌΠΎ ΡΠ°Π·Π΄Π΅Π»ΠΈΡΡ Π²ΡΠ΅ ΠΏΡΠΎΠΈΠ·Π²ΠΎΠ΄ΡΡΠ²Π΅Π½Π½ΡΠ΅ ΠΎΠΏΠ΅ΡΠ°ΡΠΈΠΈ Π½Π° ΡΡΠΈ ΠΊΠ°ΡΠ΅Π³ΠΎΡΠΈΠΈ:
Π ΡΠΎΠΎΡΠ²Π΅ΡΡΡΠ²ΠΈΠΈ Ρ ΠΌΠ΅ΡΠΎΠ΄ΠΎΠΌ Β«Π±Π΅ΡΠ΅ΠΆΠ»ΠΈΠ²ΠΎΠ΅ ΠΏΡΠΎΠΈΠ·Π²ΠΎΠ΄ΡΡΠ²ΠΎΒ», Π΄Π»Ρ ΡΠΎΠ·Π΄Π°Π½ΠΈΡ Π³ΠΈΠ±ΠΊΠΎΠ³ΠΎ ΠΏΡΠ΅Π΄ΠΏΡΠΈΡΡΠΈΡ Π½Π΅ΠΎΠ±Ρ
ΠΎΠ΄ΠΈΠΌΠΎ ΡΡΠΎΠΊΡΡΠΈΡΠΎΠ²Π°ΡΡΡΡ Π½Π° ΡΡΠΊΠΎΡΠ΅Π½ΠΈΠΈ ΠΏΡΠΎΡ
ΠΎΠΆΠ΄Π΅Π½ΠΈΡ ΠΏΠΎΡΠΎΠΊΠ° ΠΏΡΠΎΠ΄ΡΠΊΡΠΈΠΈ ΡΠΊΠ²ΠΎΠ·Ρ ΠΏΡΠ΅Π΄ΠΏΡΠΈΡΡΠΈΠ΅, ΡΠ°Π·ΡΡΡΠ°Ρ ΡΡΠ΅Π½Ρ ΠΌΠ΅ΠΆΠ΄Ρ ΠΏΠΎΠ΄ΡΠ°Π·Π΄Π΅Π»Π΅Π½ΠΈΡΠΌΠΈ (ΠΌΠΎΠΆΠ΅Ρ Π±ΡΡΡ, Π΄Π°ΠΆΠ΅ ΠΈ Π² ΠΏΡΡΠΌΠΎΠΌ ΡΠΌΡΡΠ»Π΅). 5Π‘ β ΡΡΠΎ ΠΎΠ΄ΠΈΠ½ ΠΈΠ· Π²Π°ΠΆΠ½Π΅ΠΉΡΠΈΡ ΠΈΠ½ΡΡΡΡΠΌΠ΅Π½ΡΠΎΠ² Π±Π΅ΡΠ΅ΠΆΠ»ΠΈΠ²ΠΎΠ³ΠΎ ΠΏΡΠΎΠΈΠ·Π²ΠΎΠ΄ΡΡΠ²Π°, ΠΏΡΠ΅Π΄ΡΡΠ°Π²Π»ΡΡΡΠΈΠΉ ΡΠΎΠ±ΠΎΠΉ ΡΠΎΠ²ΠΎΠΊΡΠΏΠ½ΠΎΡΡΡ Π΄Π΅ΠΉΡΡΠ²ΠΈΠΉ, Π½Π°ΠΏΡΠ°Π²Π»Π΅Π½Π½ΡΡ Π½Π° ΡΠΌΠ΅Π½ΡΡΠ΅Π½ΠΈΠ΅ Π»ΠΈΡΠ½Π΅Π³ΠΎ ΠΈ ΡΠΎΠ·Π΄Π°Π½ΠΈΡ ΠΏΠΎΡΡΠ΄ΠΊΠ° Π½Π° ΡΠ°Π±ΠΎΡΠ΅ΠΌ ΠΌΠ΅ΡΡΠ΅, ΠΊΠ°ΠΊ Ρ ΡΠΎΡΠΊΠΈ Π·ΡΠ΅Π½ΠΈΡ ΡΠΈΠ·ΠΈΡΠ΅ΡΠΊΠΎΠ³ΠΎ ΠΏΠΎΡΡΠ΄ΠΊΠ°, ΡΠ°ΠΊ ΠΈ Ρ ΡΠΎΡΠΊΠΈ Π·ΡΠ΅Π½ΠΈΡ ΠΏΠΎΡΡΠ΄ΠΊΠ° Π² ΠΎΡΠ³Π°Π½ΠΈΠ·Π°ΡΠΈΠΈ ΡΠΏΡΠ°Π²Π»Π΅Π½ΠΈΡ:
ΠΠ»Ρ Π’ΠΠ Π²ΡΠ΅ Π±Π΅Π· ΠΈΡΠΊΠ»ΡΡΠ΅Π½ΠΈΡ Π·Π°ΠΏΠ°ΡΡ β ΡΡΠΎ Π±Π΅ΡΠΏΠΎΠ»Π΅Π·Π½ΠΎΠ΅. Π‘Π»Π΅Π΄ΠΎΠ²Π°ΡΠ΅Π»ΡΠ½ΠΎ, ΠΏΡΠΎΠΈΠ·Π²ΠΎΠ΄ΡΡΠ²ΠΎ Π²ΡΠ΅Π³ΠΎ ΡΠΎΠ³ΠΎ, ΡΡΠΎ Π½Π΅ Π±ΡΠ΄Π΅Ρ ΠΏΡΠΎΠ΄Π°Π½ΠΎ, ΡΠ°ΠΊΠΆΠ΅ ΡΠ²Π»ΡΠ΅ΡΡΡ Π±Π΅ΡΠΏΠΎΠ»Π΅Π·Π½ΡΠΌ, ΠΏΠΎΡΠΊΠΎΠ»ΡΠΊΡ Π³ΠΎΡΠΎΠ²Π°Ρ ΠΏΡΠΎΠ΄ΡΠΊΡΠΈΡ, ΠΏΡΠΎΠΈΠ·Π²Π΅Π΄Π΅Π½Π½Π°Ρ, Π½ΠΎ Π½Π΅ ΠΏΡΠΎΠ΄Π°Π½Π½Π°Ρ, β ΡΡΠΎ Π·Π°ΠΏΠ°ΡΡ Π³ΠΎΡΠΎΠ²ΠΎΠΉ ΠΏΡΠΎΠ΄ΡΠΊΡΠΈΠΈ, ΠΏΠ»ΡΡ Π΄Π΅Π½ΡΠ³ΠΈ, ΠΏΠΎΡΡΠ°ΡΠ΅Π½Π½ΡΠ΅ Π½Π° Π·Π°ΠΊΡΠΏΠΊΡ ΠΌΠ°ΡΠ΅ΡΠΈΠ°Π»ΠΎΠ² ΠΈ Π·Π°ΡΠΏΠ»Π°ΡΡ ΡΠ°Π±ΠΎΡΠΈΠΌ. Π’Π΅Ρ Π½ΠΈΠΊΠ° ΠΏΠ»Π°Π½ΠΈΡΠΎΠ²Π°Π½ΠΈΡ ΠΏΡΠΎΠΈΠ·Π²ΠΎΠ΄ΡΡΠ²Π° Π½Π° ΠΎΡΠ½ΠΎΠ²Π΅ ΡΠ°ΠΊΡΠΈΡΠ΅ΡΠΊΠΈΡ Π·Π°ΠΊΠ°Π·ΠΎΠ² ΠΊΠ»ΠΈΠ΅Π½ΡΠΎΠ² Π±ΠΎΠ»Π΅Π΅ ΡΡΡΠ΅ΠΊΡΠΈΠ²Π½Π°. Π‘ΠΎΠ²ΡΠ΅ΠΌΠ΅Π½Π½ΡΠ΅ ΡΡΠ΅Π΄ΡΡΠ²Π° Π°Π²ΡΠΎΠΌΠ°ΡΠΈΠ·Π°ΡΠΈΠΈ ΡΠΏΡΠ°Π²Π»Π΅Π½ΠΈΡ Π²ΡΠ΅ΠΉ ΡΠ΅ΠΏΠΎΡΠΊΠΎΠΉ ΠΏΠΎΡΡΠ°Π²ΠΎΠΊ ΠΏΠΎΠ·Π²ΠΎΠ»ΡΡΡ ΠΌΠΎΠΌΠ΅Π½ΡΠ°Π»ΡΠ½ΠΎ ΠΏΠ΅ΡΠ΅Π΄Π°Π²Π°ΡΡ ΠΈΠ½ΡΠΎΡΠΌΠ°ΡΠΈΡ ΠΈΠ· ΡΠΎΡΠΊΠΈ ΠΏΡΠΎΠ΄Π°ΠΆΠΈ Π½Π° ΠΏΡΠ΅Π΄ΠΏΡΠΈΡΡΠΈΠ΅ ΠΈ Π΄Π°Π»Π΅Π΅ β ΠΏΠΎΡΡΠ°Π²ΡΠΈΠΊΠ°ΠΌ. ΠΠΎΠΆΠ΅Ρ ΠΏΠΎΠΊΠ°Π·Π°ΡΡΡΡ, ΡΡΠΎ Π΄Π»Ρ Π’ΠΠ ΠΈΠ½ΡΠΎΡΠΌΠ°ΡΠΈΠΎΠ½Π½Π°Ρ ΡΠΈΡΡΠ΅ΠΌΠ° ΠΏΡΠ΅Π΄ΠΏΡΠΈΡΡΠΈΡ ΡΠ°ΠΊΠΆΠ΅ ΡΠ²Π»ΡΠ΅ΡΡΡ Π±Π΅ΡΠΏΠΎΠ»Π΅Π·Π½ΡΠΌ, Ρ.ΠΊ. Π½Π΅ ΡΠ²Π΅Π»ΠΈΡΠΈΠ²Π°Π΅Ρ ΠΏΠΎΡΡΠ΅Π±ΠΈΡΠ΅Π»ΡΠ½ΡΡ ΡΡΠΎΠΈΠΌΠΎΡΡΡ Π²ΡΠΏΡΡΠΊΠ°Π΅ΠΌΠΎΠΉ ΠΏΡΠΎΠ΄ΡΠΊΡΠΈΠΈ. ΠΠ΄Π½Π°ΠΊΠΎ, ΡΡΠΎ Π½Π΅ ΡΠΎΠ²ΡΠ΅ΠΌ ΡΠ°ΠΊ, Π²Π΅ΡΠ½Π΅Π΅ ΡΠΎΠ²ΡΠ΅ΠΌ Π½Π΅ ΡΠ°ΠΊ. ΠΠ½ΡΠΎΡΠΌΠ°ΡΠΈΠΎΠ½Π½Π°Ρ ΡΠΈΡΡΠ΅ΠΌΠ° Π½Π΅ΠΎΠ±Ρ ΠΎΠ΄ΠΈΠΌΠ° Π΄Π»Ρ ΠΏΡΠΈΠ΅ΠΌΠ° Π·Π°ΠΊΠ°Π·Π° ΠΊΠ»ΠΈΠ΅Π½ΡΠΎΠ², Π±ΡΡ Π³Π°Π»ΡΠ΅ΡΡΠΊΠΎΠ³ΠΎ ΡΡΠ΅ΡΠ°, ΠΎΡΡΠ»Π΅ΠΆΠΈΠ²Π°Π½ΠΈΡ Π·Π°ΠΏΠ°ΡΠΎΠ² (Π΄Π°ΠΆΠ΅ Π΅ΡΠ»ΠΈ ΠΈΡ Π½Π΅Ρ ΠΈΠ»ΠΈ ΠΏΠΎΡΡΠΈ Π½Π΅Ρ). ΠΠΎΠΏΡΠΎΡ ΠΏΠΎΠ»Π΅Π·Π½ΠΎΠ³ΠΎ ΠΈΠ»ΠΈ Π±Π΅ΡΠΏΠΎΠ»Π΅Π·Π½ΠΎΠ³ΠΎ Π² Π΄Π°Π½Π½ΠΎΠΌ ΡΠ»ΡΡΠ°Π΅ Π΄ΠΎΠ»ΠΆΠ΅Π½ ΡΠ΅ΡΠ°ΡΡΡΡ ΠΏΠΎ ΡΠ»Π΅Π΄ΡΡΡΠ΅ΠΌΡ ΠΏΡΠΈΠ½ΡΠΈΠΏΡ: Π°Π²ΡΠΎΠΌΠ°ΡΠΈΠ·Π°ΡΠΈΡ Π½Π΅ Π½ΡΠΆΠ½Π° ΡΠ°Π΄ΠΈ Π°Π²ΡΠΎΠΌΠ°ΡΠΈΠ·Π°ΡΠΈΠΈ. ΠΡΠΏΠΎΠ»ΡΠ·ΡΠΉΡΠ΅ ΡΠΈΡΡΠ΅ΠΌΡ ΡΠΎΠ»ΡΠΊΠΎ ΡΠ°ΠΌ, Π³Π΄Π΅ ΡΡΠΎ Π΄Π΅ΠΉΡΡΠ²ΠΈΡΠ΅Π»ΡΠ½ΠΎ Π½Π΅ΠΎΠ±Ρ ΠΎΠ΄ΠΈΠΌΠΎ. |
producm.ru
ΠΠ΅ΡΠ΅ΠΆΠ»ΠΈΠ²ΡΠΉ ΠΏΠΎΠ΄Ρ ΠΎΠ΄ / Β«ΡΠΎΡΠ½ΠΎ Π² ΡΡΠΎΠΊΒ»
ΠΠΎΠ΄Π΅Π»Ρ Π±Π΅ΡΠ΅ΠΆΠ»ΠΈΠ²ΠΎΠ³ΠΎ ΠΏΠΎΠ΄Ρ ΠΎΠ΄Π° (ΠΎΡ Π°Π½Π³Π». lean thinking) ΡΠ°ΠΊΠΆΠ΅ ΠΈΠ·Π²Π΅ΡΡΠ½Π° ΠΈ ΠΏΠΎΠ΄ Π΄ΡΡΠ³ΠΈΠΌΠΈ Π½Π°Π·Π²Π°Π½ΠΈΡΠΌΠΈ, Π² ΡΠ°ΡΡΠ½ΠΎΡΡΠΈ ΠΊΠ°ΠΊ Β«Π±Π΅ΡΠ΅ΠΆΠ»ΠΈΠ²ΠΎΠ΅ ΠΌΡΡΠ»Π΅Π½ΠΈΠ΅Β», Β«Π±Π΅ΡΠ΅ΠΆΠ»ΠΈΠ²ΠΎΠ΅ ΠΏΡΠΎΠΈΠ·Π²ΠΎΠ΄ΡΡΠ²ΠΎΒ», ΠΈΠ»ΠΈ ΡΠΈΠ»ΠΎΡΠΎΡΠΈΡ Toyota. ΠΡΠΈ Π±Π΅ΡΠ΅ΠΆΠ»ΠΈΠ²ΠΎΠΌ ΠΏΠΎΠ΄Ρ ΠΎΠ΄Π΅ ΠΊΠΎΠΌΠΏΠ°Π½ΠΈΡ ΡΡΠ°ΡΠ°Π΅ΡΡΡ ΠΈΠ·Π±Π°Π²ΠΈΡΡΡΡ ΠΎΡ ΠΏΠΎΡΠ΅ΡΡ ΠΈΠ»ΠΈ Π½Π΅ΡΡΡΠ΅ΠΊΡΠΈΠ²Π½ΠΎ Π²ΡΠΏΠΎΠ»Π½ΡΠ΅ΠΌΡΡ Π΄Π΅ΠΉΡΡΠ²ΠΈΠΉ (ΠΏΠΎ-ΡΠΏΠΎΠ½ΡΠΊΠΈ ΡΡΠΎ Π½Π°Π·ΡΠ²Π°Π΅ΡΡΡ Β«ΠΌΡΠ΄Π°Β»), Ρ. Π΅. ΠΎΡ Π²ΡΠ΅Π³ΠΎ, ΡΡΠΎ, ΠΊΠ°ΠΊ ΠΏΠΎΠ»Π°Π³Π°ΡΡ, Π½Π΅ Π½ΡΠΆΠ½ΠΎ Π΄Π»Ρ ΠΏΡΠΎΠΈΠ·Π²ΠΎΠ΄ΡΡΠ²Π° ΡΠΎΠ²Π°ΡΠ° ΠΈΠ»ΠΈ ΡΡΠ»ΡΠ³ΠΈ.
ΠΡΠΈ Π±Π΅ΡΠ΅ΠΆΠ»ΠΈΠ²ΠΎΠΌ ΠΏΠΎΠ΄Ρ ΠΎΠ΄Π΅ ΠΈΡΡΠΎΡΠ½ΠΈΠΊΠΎΠΌ Π²ΡΠ΅Ρ Π·ΠΎΠ» ΡΡΠΈΡΠ°ΡΡΡΡ Π·Π°ΠΏΠ°ΡΡ. ΠΡΠ»ΠΈ ΠΎΠ½ΠΈ Π±ΠΎΠ»ΡΡΠΈΠ΅, Π·Π° Π½ΠΈΠΌΠΈ ΠΊΡΠΎΡΡΡΡ ΡΠ΅ ΡΠ΅Π°Π»ΡΠ½ΡΠ΅ ΠΏΡΠΎΠ±Π»Π΅ΠΌΡ, Ρ ΠΊΠΎΡΠΎΡΡΠΌΠΈ ΡΡΠ°Π»ΠΊΠΈΠ²Π°Π΅ΡΡΡ ΠΊΠΎΠΌΠΏΠ°Π½ΠΈΡ. ΠΡΡΠ³ΠΈΠΌΠΈ ΡΠ»ΠΎΠ²Π°ΠΌΠΈ, ΠΈΡ Π½Π°Π»ΠΈΡΠΈΠ΅ ΠΌΠ΅ΡΠ°Π΅Ρ ΠΊΠΎΠΌΠΏΠ°Π½ΠΈΠΈ Π΄Π΅ΠΉΡΡΠ²ΠΎΠ²Π°ΡΡ Π±ΠΎΠ»Π΅Π΅ Π³ΠΈΠ±ΠΊΠΎ ΠΈ ΡΡΡΠ΅ΠΊΡΠΈΠ²Π½ΠΎ. ΠΡΠ»ΠΈ ΠΆΠ΅ ΠΊΠΎΠ»ΠΈΡΠ΅ΡΡΠ²ΠΎ Π·Π°ΠΏΠ°ΡΠΎΠ² ΡΠ΅Π»Π΅Π½Π°ΠΏΡΠ°Π²Π»Π΅Π½Π½ΠΎ ΡΠ½ΠΈΠΆΠ°Π΅ΡΡΡ, ΡΠ°ΠΊΡΠΈΡΠ΅ΡΠΊΠΈΠ΅ ΠΏΡΠΎΠ±Π»Π΅ΠΌΡ ΡΡΠ°Π½ΠΎΠ²ΡΡΡΡ ΠΎΡΠ΅Π²ΠΈΠ΄Π½ΡΠΌΠΈ, ΠΏΠΎΡΠ»Π΅ ΡΠ΅Π³ΠΎ Π·Π°ΠΏΠ°ΡΠ°ΠΌΠΈ ΠΌΠΎΠΆΠ½ΠΎ ΡΡΡΠ΅ΠΊΡΠΈΠ²Π½ΠΎ ΡΠΏΡΠ°Π²Π»ΡΡΡ.
ΠΠ΅ΡΠ΅ΠΆΠ»ΠΈΠ²ΡΠΉ ΠΏΠΎΠ΄Ρ ΠΎΠ΄ ΠΈ ΠΎΡΠΎΠ±Π΅Π½Π½ΠΎ Π΅Π³ΠΎ ΡΡΡΠ°ΡΠ΅Π³ΠΈΡ Β«ΡΠΎΡΠ½ΠΎ Π² ΡΡΠΎΠΊΒ» (Just-in-Time, JIT) ΡΠ²Π»ΡΡΡΡΡ Π²Π°ΡΠΈΠ°Π½ΡΠΎΠΌ ΡΠΏΠΎΠ½ΡΠΊΠΎΠΉ ΡΠΏΡΠ°Π²Π»Π΅Π½ΡΠ΅ΡΠΊΠΎΠΉ ΡΠΈΠ»ΠΎΡΠΎΡΠΈΠΈ, ΡΠ°Π·ΡΠ°Π±ΠΎΡΠ°Π½Π½ΠΎΠΉ Π’Π°ΠΉΠΈΡΠΈ ΠΠ½ΠΎ Π΄Π»Ρ ΠΏΡΠΎΠΈΠ·Π²ΠΎΠ΄ΡΡΠ²Π΅Π½Π½ΡΡ Π·Π°Π²ΠΎΠ΄ΠΎΠ² Toyota. ΠΠ΅ΡΠ΅ΠΆΠ»ΠΈΠ²ΡΠΉ ΠΏΠΎΠ΄Ρ ΠΎΠ΄ ΠΏΠΎΠ±ΡΠΆΠ΄Π°Π΅Ρ Π»ΡΠ±ΡΡ ΠΊΠΎΠΌΠΏΠ°Π½ΠΈΡ ΠΏΠΎΡΡΠΎΡΠ½Π½ΠΎ Π²ΡΡΠ²Π»ΡΡΡ ΠΈ Π»ΠΈΠΊΠ²ΠΈΠ΄ΠΈΡΠΎΠ²Π°ΡΡ ΠΈΡΡΠΎΡΠ½ΠΈΠΊΠΈ ΠΏΠΎΡΠ΅ΡΡ, Π΄ΠΎΠ±ΠΈΠ²Π°ΡΡΡ ΠΏΡΠΈ ΡΡΠΎΠΌ ΡΠ°ΠΊ Π½Π°Π·ΡΠ²Π°Π΅ΠΌΡΡ ΡΠ΅ΠΌΠΈ Π½ΡΠ»Π΅ΠΉ:
- Π½ΡΠ»Π΅Π²ΠΎΠ³ΠΎ ΡΠΈΡΠ»Π° Π΄Π΅ΡΠ΅ΠΊΡΠΎΠ²;
- Π½ΡΠ»Π΅Π²ΠΎΠ³ΠΎ ΡΠΈΡΠ»Π° ΠΈΠ·Π±ΡΡΠΎΡΠ½ΡΡ ΠΏΠ°ΡΡΠΈΠΉ;
- Π½ΡΠ»Π΅Π²ΠΎΠ³ΠΎ ΡΠΈΡΠ»Π° Π½Π°Π»Π°Π΄ΠΎΠΊ ΠΈ Π½Π°ΡΡΡΠΎΠ΅ΠΊ;
- Π½ΡΠ»Π΅Π²ΠΎΠ³ΠΎ ΡΠΈΡΠ»Π° ΠΏΠΎΠ»ΠΎΠΌΠΎΠΊ;
- Π½ΡΠ»Π΅Π²ΠΎΠ³ΠΎ ΡΠΈΡΠ»Π° (Π»ΠΈΡΠ½ΠΈΡ ) ΡΠ°Π·Π³ΡΡΠ·ΠΎΡΠ½ΠΎ-ΠΏΠΎΠ³ΡΡΠ·ΠΎΡΠ½ΡΡ ΡΠ°Π±ΠΎΡ;
- Π½ΡΠ»Π΅Π²ΠΎΠ³ΠΎ ΡΠΈΡΠ»Π° Π·Π°Π΄Π΅ΡΠΆΠ΅ΠΊ;
- Π½ΡΠ»Π΅Π²ΠΎΠ³ΠΎ ΡΠΈΡΠ»Π° ΠΎΡΠΊΠ»ΠΎΠ½Π΅Π½ΠΈΠΉ.
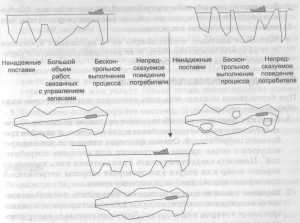
Π ΡΠΎΠΎΡΠ²Π΅ΡΡΡΠ²ΠΈΠΈ Ρ ΠΊΠΎΠ½ΡΠ΅ΠΏΡΠΈΠ΅ΠΉ ΡΠ΅ΠΌΠΈ Π½ΡΠ»Π΅ΠΉ Π±Π΅ΡΠ΅ΠΆΠ»ΠΈΠ²ΡΠΉ ΠΏΠΎΠ΄Ρ ΠΎΠ΄ ΠΎΡΠΈΠ΅Π½ΡΠΈΡΡΠ΅ΡΡΡ Π½Π° ΠΏΠΎΡΠΎΠΊΠΎΠ²ΠΎΠ΅ ΠΏΡΠΎΠΈΠ·Π²ΠΎΠ΄ΡΡΠ²ΠΎ ΠΈ Π΄Π΅Π»Π°Π΅Ρ ΡΡΠ°Π²ΠΊΡ Π½Π° Π΄ΠΎΡΡΠ°Π²ΠΊΡ ΠΏΡΠΎΠ΄ΡΠΊΡΠΈΠΈ ΠΏΠΎ ΡΡ Π΅ΠΌΠ΅ JIT.
ΠΠΎΠ³Π΄Π° ΡΠ»Π΅Π΄ΡΠ΅Ρ ΠΏΡΠΈΠΌΠ΅Π½ΡΡΡ ΠΌΠΎΠ΄Π΅Π»Ρ
Π₯ΠΎΡΡ Π±Π΅ΡΠ΅ΠΆΠ»ΠΈΠ²ΡΠΉ ΠΏΠΎΠ΄Ρ ΠΎΠ΄ ΡΠΆΠ΅ Π΄ΠΎΠΊΠ°Π·Π°Π» ΡΠ²ΠΎΡ ΠΎΡΠ΅Π½Ρ Π²ΡΡΠΎΠΊΡΡ ΡΡΡΠ΅ΠΊΡΠΈΠ²Π½ΠΎΡΡΡ ΠΏΡΠΈ Π²ΡΠΏΠΎΠ»Π½Π΅Π½ΠΈΠΈ ΠΏΠΎΠ²ΡΠΎΡΡΡΡΠΈΡ ΡΡ ΠΎΠΏΠ΅ΡΠ°ΡΠΈΠΉ Ρ Π±ΠΎΠ»ΡΡΠΈΠΌ ΠΎΠ±ΡΠ΅ΠΌΠΎΠΌ ΠΏΡΠΎΠ΄ΡΠΊΡΠΈΠΈ, ΠΈΠΌ ΠΌΠΎΠΆΠ΅Ρ Π²ΠΎΡΠΏΠΎΠ»ΡΠ·ΠΎΠ²Π°ΡΡΡΡ Π»ΡΠ±Π°Ρ ΠΊΠΎΠΌΠΏΠ°Π½ΠΈΡ, Π΅ΡΠ»ΠΈ ΡΠΎΠ»ΡΠΊΠΎ Π΅Π΅ ΡΡΠΊΠΎΠ²ΠΎΠ΄ΠΈΡΠ΅Π»ΠΈ ΠΈ ΠΌΠ΅Π½Π΅Π΄ΠΆΠ΅ΡΡ ΡΠ°Π·Π΄Π΅Π»ΡΡΡ ΠΎΡΠ½ΠΎΠ²Π½ΡΠ΅ ΠΏΠΎΠ»ΠΎΠΆΠ΅Π½ΠΈΡ, ΠΎΡΠ½ΠΎΡΡΡΠΈΠ΅ΡΡ ΠΊ Π±Π΅ΡΠ΅ΠΆΠ»ΠΈΠ²ΠΎΠΉ ΡΠΈΠ»ΠΎΡΠΎΡΠΈΠΈ.
- ΠΡΠ΄ΠΈ ΡΠ²ΠΎΠΈΠΌΠΈ Π³Π»Π°Π·Π°ΠΌΠΈ Π²ΠΈΠ΄ΡΡ Π²Π΅ΡΡ ΠΏΠΎΡΠΎΠΊ ΡΠΎΠ·Π΄Π°Π½ΠΈΡ ΡΠ΅Π½Π½ΠΎΡΡΠΈ Β«ΠΎΡ Π΄Π²Π΅ΡΠΈ Π΄ΠΎ Π΄Π²Π΅ΡΠΈΒ», Π° ΡΠ°ΠΊΠΆΠ΅ ΠΎΡΠ΄Π΅Π»ΡΠ½ΡΠ΅ ΠΏΡΠΎΡΠ΅ΡΡΡ.
- ΠΡΠ½ΠΎΠ²Π½ΡΠΌ ΠΎΠ³ΡΠ°Π½ΠΈΡΠ΅Π½ΠΈΠ΅ΠΌ Π΄Π»Ρ ΠΏΠΎΠ²ΡΡΠ΅Π½ΠΈΡ ΡΠ΅Π½ΡΠ°Π±Π΅Π»ΡΠ½ΠΎΡΡΠΈ ΡΠ²Π»ΡΡΡΡΡ ΠΏΠΎΡΠ΅ΡΠΈ.
- ΠΠΎΠ»ΡΡΠΎΠ΅ ΡΠΈΡΠ»ΠΎ Π½Π΅Π±ΠΎΠ»ΡΡΠΈΡ ΡΠ»ΡΡΡΠ΅Π½ΠΈΠΉ, ΠΎΡΡΡΠ΅ΡΡΠ²Π»ΡΠ΅ΠΌΡΡ Π±ΡΡΡΡΠΎ ΠΈ ΠΏΠΎΡΠ»Π΅Π΄ΠΎΠ²Π°ΡΠ΅Π»ΡΠ½ΠΎ, ΠΏΡΠΈΠ²Π΅Π΄Π΅Ρ ΠΊ Π±ΠΎΠ»Π΅Π΅ Π²ΡΡΠΎΠΊΠΈΠΌ ΡΠ΅Π·ΡΠ»ΡΡΠ°ΡΠ°ΠΌ, ΡΠ΅ΠΌ Π»ΡΠ±ΠΎΠ΅ Π°Π½Π°Π»ΠΈΡΠΈΡΠ΅ΡΠΊΠΎΠ΅ ΠΈΡΡΠ»Π΅Π΄ΠΎΠ²Π°Π½ΠΈΠ΅.
- ΠΠ·Π°ΠΈΠΌΠ½ΡΠ΅ Π²Π»ΠΈΡΠ½ΠΈΡ, Π²ΠΎΠ·Π½ΠΈΠΊΠ°ΡΡΠΈΠ΅ ΠΈΠ·-Π·Π° Π½Π°Π»ΠΎΠΆΠ΅Π½ΠΈΡ ΠΏΡΠΎΡΠ΅ΡΡΠΎΠΌ Π΄ΡΡΠ³ Π½Π° Π΄ΡΡΠ³Π°, ΠΌΠΎΠΆΠ½ΠΎ ΠΎΡΠ»Π°Π±ΠΈΡΡ, Π΅ΡΠ»ΠΈ ΠΏΠΎΡΡΠΎΡΠ½Π½ΠΎ Π·Π°Π½ΠΈΠΌΠ°ΡΡΡΡ ΡΠ»ΡΡΡΠ΅Π½ΠΈΠ΅ΠΌ ΠΏΠΎΡΠΎΠΊΠ° ΡΠΎΠ·Π΄Π°Π½ΠΈΡ ΡΠ΅Π½Π½ΠΎΡΡΠΈ.
ΠΠΎΡΠΎΠΊ ΡΠΎΠ·Π΄Π°Π½ΠΈΡ ΡΠ΅Π½Π½ΠΎΡΡΠΈ β Π½Π°Π±ΠΎΡ Π΄Π΅ΠΉΡΡΠ²ΠΈΠΈ ΠΏΠΎ ΠΏΡΠΎΠ΅ΠΊΡΠΈΡΠΎΠ²Π°Π½ΠΈΡ, ΠΎΡΠΎΡΠΌΠ»Π΅Π½ΠΈΡ Π·Π°ΠΊΠ°Π·Π° ΠΈ ΠΏΡΠΎΠΈΠ·Π²ΠΎΠ΄ΡΡΠ²Ρ: ΠΎΡ Π²ΠΎΠ·Π½ΠΈΠΊΠ½ΠΎΠ²Π΅Π½ΠΈΡ ΠΊΠΎΠ½ΡΠ΅ΠΏΡΠΈΠΈ Π΄ΠΎ Π·Π°ΠΏΡΡΠΊΠ° Π² ΠΏΡΠΎΠΈΠ·Π²ΠΎΠ΄ΡΡΠ²ΠΎ, ΠΎΡ Π·Π°ΠΊΠ°Π·Π° Π΄ΠΎ Π΄ΠΎΡΡΠ°Π²ΠΊΠΈ, ΠΎΡ Π΄ΠΎΠ±ΡΡΠΈ ΡΡΡΡΡ Π΄ΠΎ ΡΠΎΠ·Π΄Π°Π½ΠΈΡ Π³ΠΎΡΠΎΠ²ΠΎΠ³ΠΎ ΠΈΠ·Π΄Π΅Π»ΠΈΡ.
ΠΠ°ΠΊ ΡΠ»Π΅Π΄ΡΠ΅Ρ ΠΏΠΎΠ»ΡΠ·ΠΎΠ²Π°ΡΡΡΡ ΠΌΠΎΠ΄Π΅Π»ΡΡ
ΠΡΠΈ Π±Π΅ΡΠ΅ΠΆΠ»ΠΈΠ²ΠΎΠΌ ΠΏΠΎΠ΄Ρ ΠΎΠ΄Π΅ Π΅ΡΡΡ ΠΏΡΡΡ ΠΎΡΠ½ΠΎΠ²Π½ΡΡ ΡΠ°Π³ΠΎΠ², ΠΊΠΎΡΠΎΡΡΠ΅ Π½Π°Π΄ΠΎΒ ΠΎΠ±ΡΠ·Π°ΡΠ΅Π»ΡΠ½ΠΎ ΡΠ΄Π΅Π»Π°ΡΡ.
- ΠΡΡΠ²ΠΈΡΠ΅ ΡΠ°ΠΊΡΠΎΡΡ, ΡΠΏΠΎΡΠΎΠ±ΡΡΠ²ΡΡΡΠΈΠ΅ ΡΠΎΠ·Π΄Π°Π½ΠΈΡ ΡΠ΅Π½Π½ΠΎΡΡΠΈ. ΠΠΏΡΠ΅Π΄Π΅Π»ΠΈΡΠ΅, ΡΡΠΎ Π² Π΄Π°Π½Π½ΠΎΠΌ ΡΠ»ΡΡΠ°Π΅ ΡΠ²Π»ΡΠ΅ΡΡΡ ΡΠ΅Π½Π½ΠΎΡΡΡΡ, ΠΈ ΠΈΠ·ΡΡΠΈΡΠ΅ ΡΡΠ΅Π±ΠΎΠ²Π°Π½ΠΈΡ ΠΏΠΎΡΡΠ΅Π±ΠΈΡΠ΅Π»Π΅ΠΉ. ΠΡΠ΅Π½ΠΊΠ° ΡΠ°ΠΊΡΠΎΡΠΎΠ² ΡΡΠΎΠΈΠΌΠΎΡΡΠΈ Π΄ΠΎΠ»ΠΆΠ½Π° ΠΏΡΠΎΠ²ΠΎΠ΄ΠΈΡΡΡΡ Ρ ΡΠΎΡΠΊΠΈ Π·ΡΠ΅Π½ΠΈΡ Π²Π½ΡΡΡΠ΅Π½Π½ΠΈΡ ΠΈΠ»ΠΈ Π²Π½Π΅ΡΠ½ΠΈΡ ΠΏΠΎΡΡΠ΅Π±ΠΈΡΠ΅Π»Π΅ΠΉ . Π¦Π΅Π½Π½ΠΎΡΡΡ ΡΠ»Π΅Π΄ΡΠ΅Ρ Π²ΡΡΠ°ΠΆΠ°ΡΡ Π² ΠΏΠΎΠΊΠ°Π·Π°ΡΠ΅Π»ΡΡ ΡΠΎΠ³ΠΎ, Π½Π°ΡΠΊΠΎΠ»ΡΠΊΠΎ Ρ ΠΎΡΠΎΡΠΎ ΡΠΎΠ²Π°Ρ ΠΈΠ»ΠΈ ΡΡΠ»ΡΠ³Π° ΡΠ΄ΠΎΠ²Π»Π΅ΡΠ²ΠΎΡΡΠ΅Ρ Π·Π°ΠΏΡΠΎΡΡ ΠΏΠΎΡΡΠ΅Π±ΠΈΡΠ΅Π»Π΅ΠΉ ΠΏΡΠΈ ΠΎΠΏΡΠ΅Π΄Π΅Π»Π΅Π½Π½ΠΎΠΉ ΡΠ΅Π½Π΅ Π² ΠΎΠΏΡΠ΅Π΄Π΅Π»Π΅Π½Π½ΠΎΠ΅ Π²ΡΠ΅ΠΌΡ.
- ΠΡΡΠ²ΠΈΡΠ΅ ΠΏΠΎΡΠΎΠΊ ΡΠΎΠ·Π΄Π°Π½ΠΈΡ ΡΠ΅Π½Π½ΠΎΡΡΠΈ. Π£ΡΡΠ°Π½ΠΎΠ²ΠΈΡΠ΅ ΠΏΠΎΡΠ»Π΅Π΄ΠΎΠ²Π°ΡΠ΅Π»ΡΠ½ΠΎΡΡΡ Π²ΠΈΠ΄ΠΎΠ² Π΄Π΅ΡΡΠ΅Π»ΡΠ½ΠΎΡΡΠΈ, ΠΊΠΎΡΠΎΡΡΠ΅ Π΄ΠΎΠ±Π°Π²Π»ΡΡΡ ΡΠ΅Π½Π½ΠΎΡΡΡ ΠΊ Π°Π½Π°Π»ΠΈΠ·ΠΈΡΡΠ΅ΠΌΡΠΌ ΡΠΎΠ²Π°ΡΠ°ΠΌ ΠΈΠ»ΠΈ ΡΡΠ»ΡΠ³Π°ΠΌ. ΠΠ»Ρ ΡΡΠΎΠ³ΠΎ ΡΠΎΡΡΠ°Π²ΡΡΠ΅ ΠΊΠ°ΡΡΡ ΠΏΠΎΡΠΎΠΊΠ° ΡΠΎΠ·Π΄Π°Π½ΠΈΡ ΡΠ΅Π½Π½ΠΎΡΡΠΈ, Π½Π° ΠΊΠΎΡΠΎΡΠΎΠΉ Π²ΡΠ΅ Π½Π°Π½Π΅ΡΠ΅Π½Π½ΡΠ΅ Π½Π° Π½Π΅Π΅ Π²ΠΈΠ΄Ρ Π΄Π΅ΡΡΠ΅Π»ΡΠ½ΠΎΡΡΠΈ Π½Π΅ΠΎΠ±Ρ ΠΎΠ΄ΠΈΠΌΠΎ ΠΎΡΠ΅Π½ΠΈΡΡ Ρ ΡΠΎΡΠΊΠΈ Π·ΡΠ΅Π½ΠΈΡ ΡΠΎΠ³ΠΎ, ΠΏΠΎΠ²ΡΡΠ°ΡΡ ΠΎΠ½ΠΈ ΡΠ΅Π½Π½ΠΎΡΡΡ ΡΠΎΠ²Π°ΡΠ° ΠΈΠ»ΠΈ ΡΡΠ»ΡΠ³ΠΈ ΠΈΠ»ΠΈ Π½Π΅Ρ. Π Π½Π°ΠΊΠΎΠ½Π΅Ρ, ΡΠ°ΠΌ, Π³Π΄Π΅ ΡΡΠΎ Π²ΠΎΠ·ΠΌΠΎΠΆΠ½ΠΎ, ΠΈΡΠΊΠ»ΡΡΠΈΡΠ΅ Π²ΠΈΠ΄Ρ Π΄Π΅ΡΡΠ΅Π»ΡΠ½ΠΎΡΡΠΈ, ΠΊΠΎΡΠΎΡΡΠ΅ Π½Π΅ ΠΏΡΠΈΠ²ΠΎΠ΄ΡΡ ΠΊ ΡΠ²Π΅Π»ΠΈΡΠ΅Π½ΠΈΡ ΡΠ΅Π½Π½ΠΎΡΡΠΈ.
- Π‘ΠΎΡΡΠ°Π²ΡΡΠ΅ ΠΏΠΎΡΠΎΠΊ Π²ΠΈΠ΄ΠΎΠ² Π΄Π΅ΡΡΠ΅Π»ΡΠ½ΠΎΡΡΠΈ. ΠΠΎΠ±Π΅ΠΉΡΠ΅ΡΡ, ΡΡΠΎΠ±Ρ Π²Π°ΡΠ΅ ΠΏΡΠΎΠΈΠ·Π²ΠΎΠ΄ΡΡΠ²ΠΎ ΠΎΠ±Π΅ΡΠΏΠ΅ΡΠΈΠ²Π°Π»ΠΎ Π½Π΅ΠΏΡΠ΅ΡΡΠ²Π½ΡΠΉ ΠΏΠΎΡΠΎΠΊ ΡΠΎΠ²Π°ΡΠΎΠ² ΠΈ ΡΡΠ»ΡΠ³. Π§ΡΠΎΠ±Ρ Π²ΠΏΠΈΡΠ°ΡΡ Π²ΠΈΠ΄Ρ Π΄Π΅ΡΡΠ΅Π»ΡΠ½ΠΎΡΡΠΈ Π² ΠΏΠΎΡΠΎΠΊ ΡΠΎΠ·Π΄Π°Π½ΠΈΡ ΡΠ΅Π½Π½ΠΎΡΡΠΈ, ΠΏΠΎΡΡΠ΅Π±ΡΡΡΡΡ Π΄ΠΎΠΏΠΎΠ»Π½ΠΈΡΠ΅Π»ΡΠ½ΡΠ΅ ΡΡΠΈΠ»ΠΈΡ ΠΏΠΎ ΡΠΎΠ²Π΅ΡΡΠ΅Π½ΡΡΠ²ΠΎΠ²Π°Π½ΠΈΡ ΠΏΡΠΎΠΈΠ·Π²ΠΎΠ΄ΡΡΠ²Π°. ΠΠΎΠ΄ ΠΏΠΎΡΠΎΠΊΠΎΠΌ Π·Π΄Π΅ΡΡ ΠΏΠΎΠ½ΠΈΠΌΠ°Π΅ΡΡΡ Π½Π΅ΠΏΡΠ΅ΡΡΠ²Π½ΡΠΉ ΠΏΡΠΎΡΠ΅ΡΡ ΠΏΡΠΎΠ΄Π²ΠΈΠΆΠ΅Π½ΠΈΡ ΡΠΎΠ²Π°ΡΠ° ΠΈΠ»ΠΈ ΡΡΠ»ΡΠ³ΠΈ ΡΠ΅ΡΠ΅Π· ΡΠΈΡΡΠ΅ΠΌΡ Π΄ΠΎ ΡΠ΅Ρ ΠΏΠΎΡ, ΠΏΠΎΠΊΠ° ΠΏΡΠΎΠ΄ΡΠΊΡ Π½Π΅ ΠΎΠΊΠ°ΠΆΠ΅ΡΡΡ Ρ ΠΏΠΎΡΡΠ΅Π±ΠΈΡΠ΅Π»Ρ. ΠΡΠ½ΠΎΠ²Π½ΡΠΌΠΈ ΠΏΡΠ΅ΠΏΡΡΡΡΠ²ΠΈΡΠΌΠΈ Π΄Π»Ρ ΠΏΠΎΡΠΎΠΊΠΎΠ²ΠΎΠ³ΠΎ ΠΏΠΎΠ΄Ρ ΠΎΠ΄Π° ΡΠ²Π»ΡΡΡΡΡ ΠΎΡΠ΅ΡΠ΅Π΄ΠΈ Π½Π° Π²ΡΠΏΠΎΠ»Π½Π΅Π½ΠΈΠ΅ ΡΠ°Π±ΠΎΡ, ΡΠ΅ΡΠΈΠΉΠ½ΠΎΠ΅ ΠΏΡΠΎΠΈΠ·Π²ΠΎΠ΄ΡΡΠ²ΠΎ ΠΈ ΡΡΠ°Π½ΡΠΏΠΎΡΡΠΈΡΠΎΠ²ΠΊΡ. ΠΠ°ΡΡΠ΅ΡΡ ΡΡΠΎΠ³ΠΎ ΡΠΎΠ΄Π° ΡΠ²Π΅Π»ΠΈΡΠΈΠ²Π°ΡΡ ΠΏΡΠΎΠ΄ΠΎΠ»ΠΆΠΈΡΠ΅Π»ΡΠ½ΠΎΡΡΡ Π΄ΠΎΡΡΠ°Π²ΠΊΠΈ ΡΠΎΠ²Π°ΡΠ° ΠΈΠ»ΠΈ ΡΡΠ»ΡΠ³ΠΈ ΠΏΠΎΡΡΠ΅Π±ΠΈΡΠ΅Π»Ρ. Π ΡΠΎΠΌΡ ΠΆΠ΅ Π½Π°Π»ΠΈΡΠΈΠ΅ ΠΏΠΎΠ΄ΠΎΠ±Π½ΡΡ Π±Π°ΡΡΠ΅ΡΠΎΠ² ΠΏΡΠΈΠ²ΠΎΠ΄ΠΈΡ ΠΊ ΡΠΎΠΌΡ, ΡΡΠΎ ΡΠ°ΡΡΡ Π΄Π΅Π½Π΅Π³ ΠΎΠΊΠ°Π·ΡΠ²Π°Π΅ΡΡΡ Β«ΡΠ²ΡΠ·Π°Π½Π½ΠΎΠΉΒ», Π° Π²Π΅Π΄Ρ ΡΡΠΈ ΡΡΠ΅Π΄ΡΡΠ²Π° ΠΊΠΎΠΌΠΏΠ°Π½ΠΈΡ ΠΌΠΎΠ³Π»Π° Π±Ρ ΠΏΠΎΡΡΠ°ΡΠΈΡΡ Π±ΠΎΠ»Π΅Π΅ ΡΡΡΠ΅ΠΊΡΠΈΠ²Π½ΠΎ. ΠΠ΅ΡΠ΅Π΄ΠΊΠΎ Π·Π° ΡΡΠΈΠΌΠΈ ΠΏΡΠ΅ΠΏΡΡΡΡΠ²ΠΈΡΠΌΠΈ Π½Π΅ Π²ΠΈΠ΄Π½ΠΎ, ΠΊΠ°ΠΊΠΈΠΌΠΈ Π½Π° ΡΠ°ΠΌΠΎΠΌ Π΄Π΅Π»Π΅ ΡΠ²Π»ΡΡΡΡΡ ΠΏΠΎΡΠ»Π΅Π΄ΡΡΠ²ΠΈΡ ΡΠ±ΠΎΠ΅Π² ΡΠΈΡΡΠ΅ΠΌΡ ΠΈ Π²ΠΈΠ΄Ρ ΠΏΠΎΡΠ΅ΡΡ.
ΠΠΎΠ΄ Π²Π½ΡΡΡΠ΅Π½Π½ΠΈΠΌΠΈ ΠΏΠΎΡΡΠ΅Π±ΠΈΡΠ΅Π»ΡΠΌΠΈ ΠΏΠΎΠ½ΠΈΠΌΠ°Π΅ΡΡΡ ΠΏΠ΅ΡΡΠΎΠ½Π°Π» ΠΊΠΎΠΌΠΏΠ°Π½ΠΈΠΈ.
- ΠΡΠ³Π°Π½ΠΈΠ·ΡΠΉΡΠ΅ Π΄Π΅Π»ΠΎ ΡΠ°ΠΊ, ΡΡΠΎΠ±Ρ ΠΏΠΎΡΡΠ΅Π±ΠΈΡΠ΅Π»Ρ Β«Π²ΡΡΡΠ³ΠΈΠ²Π°Π»Β» ΡΠΎΠ²Π°Ρ ΠΈΠ»ΠΈ ΡΡΠ»ΡΠ³Ρ Π² Ρ ΠΎΠ΄Π΅ ΠΏΡΠΎΠΈΠ·Π²ΠΎΠ΄ΡΡΠ²Π΅Π½Π½ΠΎΠ³ΠΎ ΠΏΡΠΎΡΠ΅ΡΡΠ°. ΠΠΎΠ½ΡΡΠΎΠ»Ρ Π·Π° ΠΏΡΠΎΠ΄ΡΠΊΡΠΈΠ΅ΠΉ Π΄ΠΎΠ»ΠΆΠ΅Π½ ΠΎΡΡΡΠ΅ΡΡΠ²Π»ΡΡΡΡΡ Π½Π° ΠΎΡΠ½ΠΎΠ²Π΅ Β«Π²ΡΡΡΠ³ΠΈΠ²Π°ΡΡΠ΅ΠΉΒ» ΡΠΈΡΡΠ΅ΠΌΡΒ«. ΠΠ΅ΠΎΠ±Ρ ΠΎΠ΄ΠΈΠΌΠΎ Π΄ΠΎΠ±ΠΈΡΡΡΡ ΡΠΎΠΎΡΠ²Π΅ΡΡΡΠ²ΠΈΡ ΠΎΠ±ΡΠ΅ΠΌΠ° ΠΏΡΠΎΠΈΠ·Π²ΠΎΠ΄ΡΡΠ²Π° ΡΠ°ΠΊΡΠΈΡΠ΅ΡΠΊΠΎΠΌΡ ΡΠΏΡΠΎΡΡ ΠΏΠΎΡΡΠ΅Π±ΠΈΡΠ΅Π»Π΅ΠΉ. ΠΡΠΎΠ΄ΡΠΊΡΡ Π΄ΠΎΠ»ΠΆΠ½Ρ Β«Π²ΡΡΡΠ³ΠΈΠ²Π°ΡΡΡΡΒ» ΠΈΠ· ΡΠΈΡΡΠ΅ΠΌΡ Π½Π° ΠΎΡΠ½ΠΎΠ²Π΅ ΡΠ°ΠΊΡΠΈΡΠ΅ΡΠΊΠΎΠ³ΠΎ ΠΏΠΎΡΡΠ΅Π±ΠΈΡΠ΅Π»ΡΡΠΊΠΎΠ³ΠΎ ΡΠΏΡΠΎΡΠ°. ΠΠΎΡΠΎΠΊ ΡΠΎΠ·Π΄Π°Π½ΠΈΡ ΡΠ΅Π½Π½ΠΎΡΡΠΈ Π΄ΠΎΠ»ΠΆΠ΅Π½ ΡΠ΅Π°Π³ΠΈΡΠΎΠ²Π°ΡΡ Π½Π° ΡΠ΅Π°Π»ΡΠ½ΠΎΠ΅ ΠΏΠΎΠ»ΠΎΠΆΠ΅Π½ΠΈΠ΅ Π΄Π΅Π» ΠΈ ΠΏΡΠ΅Π΄ΠΎΡΡΠ°Π²Π»ΡΡΡ ΡΠΎΠ²Π°Ρ ΠΈΠ»ΠΈ ΡΡΠ»ΡΠ³Ρ ΡΠΎΠ»ΡΠΊΠΎ ΡΠΎΠ³Π΄Π°, ΠΊΠΎΠ³Π΄Π° ΠΏΡΠΎΠ΄ΡΠΊΡ Π½ΡΠΆΠ΅Π½ ΠΏΠΎΡΡΠ΅Π±ΠΈΡΠ΅Π»Ρ, Π½Π΅ ΡΠ°Π½ΡΡΠ΅ ΠΈ Π½Π΅ ΠΏΠΎΠ·ΠΆΠ΅.
- ΠΠΎΡΡΠΎΡΠ½Π½ΠΎ ΠΎΠΏΡΠΈΠΌΠΈΠ·ΠΈΡΡΠΉΡΠ΅ ΡΠΈΡΡΠ΅ΠΌΡ. ΠΠΎΠ±ΠΈΠ²Π°ΠΉΡΠ΅ΡΡ ΡΠΎΠ²Π΅ΡΡΠ΅Π½ΡΡΠ²Π° Π·Π° ΡΡΠ΅Ρ ΠΏΠΎΡΡΠΎΡΠ½Π½ΠΎΠ³ΠΎ ΡΠ»ΡΡΡΠ΅Π½ΠΈΡ ΠΏΡΠΎΡΠ΅ΡΡΠΎΠ², ΠΈΡΠΏΠΎΠ»ΡΠ·ΡΡ Π΄Π»Ρ ΡΡΠΎΠ³ΠΎ ΠΊΠ°ΠΉΠ΄Π·Π΅Π½, Π° ΡΠ°ΠΊΠΆΠ΅ Π·Π° ΡΡΠ΅Ρ ΡΡΡΡΠ°Π½Π΅Π½ΠΈΡ ΠΏΠΎΡΠ΅ΡΡ ΠΈ ΠΏΡΠΎΠ΄ΡΠΌΠ°Π½Π½ΠΎΠ³ΠΎ Π²Π΅Π΄Π΅Π½ΠΈΡ Π΄Π΅Π» Π² ΡΠ΅Π»ΠΎΠΌ.
ΠΡΠ²ΠΎΠ΄Ρ
Π Π΅Π°Π»ΠΈΠ·Π°ΡΠΈΡ Π±Π΅ΡΠ΅ΠΆΠ»ΠΈΠ²ΠΎΠ³ΠΎ ΠΏΠΎΠ΄Ρ ΠΎΠ΄Π° Π½Π° ΠΏΠ΅ΡΠ²ΡΠΉ Π²Π·Π³Π»ΡΠ΄ ΠΊΠ°ΠΆΠ΅ΡΡΡ Π»Π΅Π³ΠΊΠΈΠΌ Π΄Π΅Π»ΠΎΠΌ. ΠΠ΄Π½Π°ΠΊΠΎ, ΡΡΠΎΠ±Ρ Π΄ΠΎΠ±ΠΈΡΡΡΡ Π·Π΄Π΅ΡΡ ΡΡΠΏΠ΅Ρ Π°, Π½ΡΠΆΠ½ΠΎ ΡΡΠ΅ΡΡΡ ΡΠ°Π·Π»ΠΈΡΠ½ΡΠ΅ Π°ΡΠΏΠ΅ΠΊΡΡ ΠΈ ΡΠΎΡΡΠ°Π²Π»ΡΡΡΠΈΠ΅ (ΠΈ ΡΠ΄Π΅Π»Π°ΡΡ ΡΡΠΎ Π² ΡΠ»Π΅Π΄ΡΡΡΠ΅ΠΌ ΠΏΠΎΡΡΠ΄ΠΊΠ΅).
- ΠΠ°ΠΊΠΈΠ΅ ΡΠ΅Π·ΡΠ»ΡΡΠ°ΡΡ ΠΌΡ ΠΎΠΆΠΈΠ΄Π°Π΅ΠΌ ΠΏΠΎΠ»ΡΡΠΈΡΡ ΠΎΡ JIT? Π‘Π»Π΅Π΄ΡΠ΅Ρ Π»ΠΈ ΡΠ°ΡΡΠΌΠΎΡΡΠ΅ΡΡ Π·Π°ΡΠ°Π½Π΅Π΅ ΠΈΠ·Π΄Π΅ΡΠΆΠΊΠΈ ΡΠ΅Π°Π»ΠΈΠ·Π°ΡΠΈΠΈ ΠΈ ΡΠ΅ ΠΏΡΠ΅ΠΏΡΡΡΡΠ²ΠΈΡ, Ρ ΠΊΠΎΡΠΎΡΡΠΌΠΈ ΠΌΡ ΡΡΠΎΠ»ΠΊΠ½Π΅ΠΌΡΡ? ΠΠΏΠ΅ΡΠ°ΡΠΈΠ²Π½ΠΎ ΠΈΠ·ΡΡΠΈΡΠ΅ Π·Π°ΡΡΠ°ΡΡ ΠΈ Π²ΡΠ³ΠΎΠ΄Ρ, Π² ΡΠΎΠΌ ΡΠΈΡΠ»Π΅ Π²ΠΎΠ·ΠΌΠΎΠΆΠ½ΡΠΉ ΠΏΠ»Π°Π½ Π²ΡΠΏΠΎΠ»Π½Π΅Π½ΠΈΡ ΠΏΡΠΎΠ΅ΠΊΡΠ°.
- ΠΠ»Ρ Π΄ΠΎΡΡΠΈΠΆΠ΅Π½ΠΈΡ ΡΡΠΏΠ΅Ρ Π° ΠΏΡΠΈ Π²ΡΠΏΠΎΠ»Π½Π΅Π½ΠΈΠΈ JIT ΠΎΡΠ΅Π½Ρ Π²Π°ΠΆΠ½Π° ΠΏΠΎΡΠ»Π΅Π΄ΠΎΠ²Π°ΡΠ΅Π»ΡΠ½ΠΎΡΡΡ Π²ΡΠΏΠΎΠ»Π½ΡΠ΅ΠΌΡΡ ΡΠ°Π³ΠΎΠ². Π‘Π½ΠΈΠΆΠ΅Π½ΠΈΠ΅ Π·Π°ΠΏΠ°ΡΠΎΠ² Π΄ΠΎ ΡΡΠΎΠ²Π½Ρ, ΠΎΠ±Π΅ΡΠΏΠ΅ΡΠΈΠ²Π°ΡΡΠ΅Π³ΠΎ Π³ΠΈΠ±ΠΊΠΎΡΡΡ ΠΏΡΠΎΠΈΠ·Π²ΠΎΠ΄ΡΡΠ²Π°, ΠΌΠΎΠΆΠ΅Ρ ΠΏΡΠΈΠ²Π΅ΡΡΠΈ ΠΊ ΡΠ΅Π·ΠΊΠΎΠΌΡ ΡΡ ΡΠ΄ΡΠ΅Π½ΠΈΡ ΠΏΠΎΠΊΠ°Π·Π°ΡΠ΅Π»Π΅ΠΉ Π΄ΠΎΡΡΠ°Π²ΠΊΠΈ ΠΏΡΠΎΠ΄ΡΠΊΡΠΈΠΈ ΠΏΠΎΡΡΠ΅Π±ΠΈΡΠ΅Π»ΡΠΌ. Π ΡΠ΅Π»ΠΎΠΌ, ΡΠ΅Π°Π»ΠΈΠ·Π°ΡΠΈΡ ΡΡΠΎΠ³ΠΎ ΠΏΠΎΠ΄Ρ ΠΎΠ΄Π° ΠΎΠΊΠ°Π·ΡΠ²Π°Π΅ΡΡΡ Π½Π°ΠΈΠ±ΠΎΠ»Π΅Π΅ ΡΡΠΏΠ΅ΡΠ½ΠΎΠΉ, Π΅ΡΠ»ΠΈ ΠΎΠ½ Π½Π°ΡΠΈΠ½Π°Π΅Ρ Π²ΡΠΏΠΎΠ»Π½ΡΡΡΡΡ Ρ ΡΠ°ΠΌΠΎΠ³ΠΎ ΠΊΠΎΠ½ΡΠ° ΠΏΡΠΎΠΈΠ·Π²ΠΎΠ΄ΡΡΠ²Π΅Π½Π½ΠΎΠ³ΠΎ ΠΏΡΠΎΡΠ΅ΡΡΠ°, Π° Π·Π°ΡΠ΅ΠΌ ΠΏΠΎΡΠ»Π΅Π΄ΠΎΠ²Π°ΡΠ΅Π»ΡΠ½ΠΎ ΠΈΠ΄Π΅Ρ ΠΊ Π΅Π³ΠΎ Π½Π°ΡΠ°Π»Ρ. ΠΠ΄Π½Π°ΠΊΠΎ ΡΠΎ, ΠΊΠ°ΠΊΠ°Ρ ΠΏΠΎΡΠ»Π΅Π΄ΠΎΠ²Π°ΡΠ΅Π»ΡΠ½ΠΎΡΡΡ ΡΠ²Π»ΡΠ΅ΡΡΡ Β«Π»ΡΡΡΠ΅ΠΉΒ», Π·Π°Π²ΠΈΡΠΈΡ ΠΎΡ ΠΊΠΎΠ½ΠΊΡΠ΅ΡΠ½ΠΎΠΉ ΡΠΈΡΡΠ°ΡΠΈΠΈ. Π§ΡΠΎΠ±Ρ Π³Π°ΡΠ°Π½ΡΠΈΡΠΎΠ²Π°ΡΡ Π½Π΅ΠΎΠ±Ρ ΠΎΠ΄ΠΈΠΌΡΠ΅ ΠΏΠΎΠΊΠ°Π·Π°ΡΠ΅Π»ΠΈ Π΄ΠΎΡΡΠ°Π²ΠΊΠΈ ΠΏΡΠΎΠ΄ΡΠΊΡΠΈΠΈ ΠΏΠΎΡΡΠ΅Π±ΠΈΡΠ΅Π»ΡΠΌ Π½Π° ΡΡΠ°ΠΏΠ΅ ΡΠ΅Π°Π»ΠΈΠ·Π°ΡΠΈΠΈ ΡΡΠΎΠ³ΠΎ ΠΏΠΎΠ΄Ρ ΠΎΠ΄Π°, ΡΠ»Π΅Π΄ΡΠ΅Ρ ΡΠ°ΡΡΠΌΠΎΡΡΠ΅ΡΡ Π²Π°ΡΠΈΠ°Π½Ρ Π²ΡΠ΅ΠΌΠ΅Π½Π½ΠΎΠ³ΠΎ ΠΏΠΎΠ²ΡΡΠ΅Π½ΠΈΡ ΡΡΠΎΠ²Π½Ρ Π·Π°ΠΏΠ°ΡΠΎΠ².
- ΠΠ΅ Π·Π°ΡΡΠ°Π²Π»ΡΠΉΡΠ΅ ΠΏΠΎΡΡΠ°Π²ΡΠΈΠΊΠΎΠ² ΡΡΠ°Π·Ρ ΠΏΠ΅ΡΠ΅ΠΉΡΠΈ Π½Π° Π²Π°ΡΠΈΠ°Π½Ρ JIT Π΄ΠΎ ΡΠ΅Ρ ΠΏΠΎΡ, ΠΏΠΎΠΊΠ° ΡΠ°ΠΌΠΈ Π½Π΅ Π·Π°ΠΊΠΎΠ½ΡΠΈΡΠ΅ ΠΏΠ΅ΡΠ΅Ρ ΠΎΠ΄ ΠΈΠ»ΠΈ Ρ ΠΎΡΡ Π±Ρ Π½Π΅ ΠΎΡΡΡΠ΅ΡΡΠ²ΠΈΡΠ΅ Π±ΠΎΠ»ΡΡΡΡ Π΅Π³ΠΎ ΡΠ°ΡΡΡ.
- ΠΠΏΡΠ΅Π΄Π΅Π»ΠΈΡΠ΅, ΠΏΠΎΠ΄Ρ ΠΎΠ΄ΠΈΡ Π»ΠΈ ΠΊΠΎΠ½ΡΡΡΡΠΊΡΠΈΡ ΠΏΡΠΎΠ΄ΡΠΊΡΠ° ΠΊ Π΅Π³ΠΎ ΠΏΡΠΎΠΈΠ·Π²ΠΎΠ΄ΡΡΠ²Ρ ΠΈΠ»ΠΈ Π΄ΠΎΡΡΠ°Π²ΠΊΠ΅ Π² Π²Π°ΡΠΈΠ°Π½ΡΠ΅ JIT. Π Π΅ΡΠΈΡΠ΅, Π½Π΅ ΡΠ»Π΅Π΄ΡΠ΅Ρ Π»ΠΈ Π²Π½Π΅ΡΡΠΈ Π² Π½Π΅Π΅ ΠΊΠ°ΠΊΠΈΠ΅-Π»ΠΈΠ±ΠΎ ΠΈΠ·ΠΌΠ΅Π½Π΅Π½ΠΈΡ.
- ΠΠΎΡΠ»Π΅ ΡΡΠΎΠ³ΠΎ ΠΈΠ·ΠΌΠ΅Π½ΠΈΡΠ΅ ΠΏΡΠΎΠΈΠ·Π²ΠΎΠ΄ΡΡΠ²Π΅Π½Π½ΡΠΉ ΠΏΡΠΎΡΠ΅ΡΡ ΡΠ°ΠΊ, ΡΡΠΎΠ±Ρ ΠΌΠΎΠΆΠ½ΠΎ Π±ΡΠ»ΠΎ ΠΏΠ΅ΡΠ΅ΠΉΡΠΈ Π½Π° Π²Π°ΡΠΈΠ°Π½Ρ JIT. ΠΠ° ΡΡΠΎΠΌ ΡΡΠ°ΠΏΠ΅ ΠΎΠ±ΡΡΠ½ΠΎ ΠΊΠΎΠΌΠΏΠ°Π½ΠΈΡ ΡΠΆΠ΅ Π΄ΠΎΠ±ΠΈΠ²Π°Π΅ΡΡΡ Π·Π½Π°ΡΠΈΡΠ΅Π»ΡΠ½ΡΡ ΡΠ»ΡΡΡΠ΅Π½ΠΈΠΉ ΠΈ ΠΏΠΎΠ²ΡΡΠ΅Π½ΠΈΡ ΡΡΡΠ΅ΠΊΡΠΈΠ²Π½ΠΎΡΡΠΈ.
- Π‘ΠΊΠΎΡΡΠ΅ΠΊΡΠΈΡΡΠΉΡΠ΅ ΡΠ°Π±ΠΎΡΡ ΠΈΠ½ΡΠΎΡΠΌΠ°ΡΠΈΠΎΠ½Π½ΡΡ ΡΠΈΡΡΠ΅ΠΌ ΡΠ°ΠΊ, ΡΡΠΎΠ±Ρ ΠΎΠ½ΠΈ ΠΎΠ±Π΅ΡΠΏΠ΅ΡΠΈΠ²Π°Π»ΠΈ Π·Π°ΠΏΡΠΎΡΡ ΠΏΠ΅ΡΠ²ΠΈΡΠ½ΡΡ ΠΏΡΠΎΡΠ΅ΡΡΠΎΠ².
- ΠΠΎΡΡΠ°ΡΠ°ΠΉΡΠ΅ΡΡ Π΄ΠΎΠ±ΠΈΡΡΡΡ ΡΠ»ΡΡΡΠ΅Π½ΠΈΡ Π²Π·Π°ΠΈΠΌΠΎΠ΄Π΅ΠΉΡΡΠ²ΠΈΡ Ρ ΠΏΠΎΡΡΠ°Π²ΡΠΈΠΊΠ°ΠΌΠΈ ΠΈ ΠΏΠΎΡΡΠ΅Π±ΠΈΡΠ΅Π»ΡΠΌΠΈ. ΠΠ»Π°Π³ΠΎΠ΄Π°ΡΡ ΡΡΠΎΠΌΡ ΡΠ΅Π·ΡΠ»ΡΡΠ°ΡΡ JIT ΡΡΠ°Π½ΡΡ Π΅ΡΠ΅ Π±ΠΎΠ»Π΅Π΅ Π²ΡΡΠΎΠΊΠΈΠΌΠΈ.
ΠΡΠ½ΠΎΠ²Π½Π°Ρ ΡΠ΅Π»Ρ Π±Π΅ΡΠ΅ΠΆΠ»ΠΈΠ²ΠΎΠ³ΠΎ ΠΏΠΎΠ΄Ρ ΠΎΠ΄Π° β ΡΠΎΠΊΡΠ°ΡΠ΅Π½ΠΈΠ΅ ΠΏΠΎΡΠ΅ΡΡ (ΠΎΡΠΎΠ±Π΅Π½Π½ΠΎ ΠΈΠ·-Π·Π° ΡΡΠ΅Π·ΠΌΠ΅ΡΠ½ΠΎ Π±ΠΎΠ»ΡΡΠΈΡ Π·Π°ΠΏΠ°ΡΠΎΠ²). Π’Π΅ΠΌ Π½Π΅ ΠΌΠ΅Π½Π΅Π΅ ΠΈΠ·Π±Π°Π²ΠΈΡΡΡΡ ΠΎΡ Π·Π°ΠΏΠ°ΡΠΎΠ² ΠΏΠΎΠ»Π½ΠΎΡΡΡΡ Π²Π°ΠΌ Π½Π΅ ΡΠ΄Π°ΡΡΡΡ, ΡΠ°ΠΊ ΠΊΠ°ΠΊ Π²ΡΠ΅ΠΌ ΡΠΈΡΡΠ΅ΠΌΠ°ΠΌ ΠΏΠΎΡΡΠ°Π²ΠΎΠΊ Π½ΡΠΆΠ½Ρ ΡΠ°Π±ΠΎΡΠΈΠ΅ Π·Π°ΠΏΠ°ΡΡ, ΡΡΠΎΠ±Ρ ΠΎΠ±Π΅ΡΠΏΠ΅ΡΠΈΡΡ Π½ΡΠΆΠ½ΠΎΠ΅ ΠΊΠΎΠ»ΠΈΡΠ΅ΡΡΠ²ΠΎ ΠΏΡΠΎΠ΄ΡΠΊΡΠΈΠΈ Π½Π° Π²ΡΡ ΠΎΠ΄Π΅. Π§Π΅ΠΌ Π±ΠΎΠ»Π΅Π΅ Π²ΡΡΠΎΠΊΠΎΠΉ ΡΠ²Π»ΡΠ΅ΡΡΡ Π²Π°ΡΠΈΠ°ΡΠΈΠ²Π½ΠΎΡΡΡ ΡΠ°Π±ΠΎΡΡ ΡΠΈΡΡΠ΅ΠΌΡ (Ρ. Π΅. Π²ΡΠΏΠΎΠ»Π½Π΅Π½ΠΈΠ΅ Π΅Ρ ΡΠ°Π·Π½ΡΡ Π·Π°ΠΊΠ°Π·ΠΎΠ², ΠΏΡΠΈΠΌΠ΅Π½Π΅Π½ΠΈΠ΅ ΡΠ°Π·Π½ΡΡ Π²ΠΈΠ΄ΠΎΠ² ΡΠ΅Ρ Π½ΠΎΠ»ΠΎΠ³ΠΈΠΉ), ΡΠ΅ΠΌ Π±ΠΎΠ»ΡΡΠΈΠ΅ Π±ΡΡΠ΅ΡΠ½ΡΠ΅ Π·Π°ΠΏΠ°ΡΡ Π½ΡΠΆΠ½Ρ Π΄Π»Ρ Π½Π΅Π΅, ΡΡΠΎΠ±Ρ ΡΡΠ΅ΡΡΡ ΡΠ°Π·Π½ΠΎΠΎΠ±ΡΠ°Π·ΠΈΠ΅ Π²ΡΠΏΠΎΠ»Π½ΡΠ΅ΠΌΡΡ Π΅Ρ Π΄Π΅ΠΉΡΡΠ²ΠΈΠΉ. ΠΠΎΡΡΠΎΠΌΡ, ΡΡΠΎΠ±Ρ ΡΠΈΡΡΠ΅ΠΌΠ° Π±Π΅ΡΠ΅ΠΆΠ»ΠΈΠ²ΠΎΠ³ΠΎ ΠΏΡΠΎΠΈΠ·Π²ΠΎΠ΄ΡΡΠ²Π° ΡΡΠ½ΠΊΡΠΈΠΎΠ½ΠΈΡΠΎΠ²Π°Π»Π° ΡΡΠΏΠ΅ΡΠ½ΠΎ, Π²Π°ΠΆΠ½ΠΎ ΠΈΠΌΠ΅ΡΡ Π½Π΅ ΡΠΎΠ»ΡΠΊΠΎ ΠΏΡΠΎΠΈΠ·Π²ΠΎΠ΄ΡΡΠ²Π΅Π½Π½ΡΡ ΡΠΈΡΡΠ΅ΠΌΡ, ΠΊΠΎΠ½ΡΡΠΎΠ»ΠΈΡΡΠ΅ΠΌΡΡ Π½Π° ΠΎΡΠ½ΠΎΠ²Π΅ Β«Π²ΡΡΡΠ³ΠΈΠ²Π°ΡΡΠ΅ΠΉΒ» ΡΠΈΡΡΠ΅ΠΌΡ, ΠΏΠ°ΡΡΠΈΠΈ Π½Π΅Π±ΠΎΠ»ΡΡΠΎΠ³ΠΎ ΡΠ°Π·ΠΌΠ΅ΡΠ° ΠΈ ΡΠΎΠΊΡΠ°ΡΠ΅Π½ΠΈΠ΅ Π²ΡΠ΅ΠΌΠ΅Π½ΠΈ Π΅Π΅ Π½Π°Π»Π°Π΄ΠΊΠΈ, Π½ΠΎ ΠΈ ΡΡΠ°Π±ΠΈΠ»ΡΠ½ΡΠΉ ΡΠΏΡΠΎΡ ΠΈ ΡΠΎΠΎΡΠ²Π΅ΡΡΡΠ²ΡΡΡΡΡ ΠΎΡΠ³Π°Π½ΠΈΠ·Π°ΡΠΈΡ ΠΎΠΏΠ΅ΡΠ°ΡΠΈΠΉ. Π ΡΠΎΠ²ΡΠ΅ΠΌΠ΅Π½Π½ΠΎΠΉ Π΄ΠΈΠ½Π°ΠΌΠΈΡΠ½ΠΎ ΡΠ°Π·Π²ΠΈΠ²Π°ΡΡΠ΅ΠΉΡΡ Π±ΠΈΠ·Π½Π΅Ρ-ΡΡΠ΅Π΄Π΅ Π±ΠΎΠ»Π΅Π΅ ΠΏΠΎΠ΄Ρ ΠΎΠ΄ΡΡΠΈΠΌΠΈ ΠΌΠΎΠ³ΡΡ ΠΎΠΊΠ°Π·Π°ΡΡΡΡ Π΄ΡΡΠ³ΠΈΠ΅ ΠΏΠΎΠ΄Ρ ΠΎΠ΄Ρ, Π² ΡΠ°ΡΡΠ½ΠΎΡΡΠΈ ΠΎΡΠ½ΠΎΠ²Π°Π½Π½ΡΠ΅ Π½Π° ΡΠ΅ΠΎΡΠΈΠΈ ΠΎΠ³ΡΠ°Π½ΠΈΡΠ΅Π½ΠΈΠΉ ΠΈΠ»ΠΈ ΠΏΡΠΎΠΈΠ·Π²ΠΎΠ΄ΡΡΠ²Π°, Π½Π°ΡΠ΅Π»Π΅Π½Π½ΠΎΠ³ΠΎ Π½Π° Π±ΡΡΡΡΠΎΠ΅ ΡΠ΅Π°Π³ΠΈΡΠΎΠ²Π°Π½ΠΈΠ΅.
- ΠΠ΅ ΡΠ°ΡΡΡΠΈΡΡΠ²Π°ΠΉΡΠ΅, ΡΡΠΎ Π²Ρ ΡΠΌΠΎΠΆΠ΅ΡΠ΅ Ρ ΠΏΠΎΠ»ΡΠ·ΠΎΠΉ ΠΏΡΠΈΠΌΠ΅Π½ΠΈΡΡ Π²ΡΠ΅ ΠΏΠΎΡΠ΅ΡΠΈ.
- ΠΠ΅ Π΄ΡΠΌΠ°ΠΉΡΠ΅, ΡΡΠΎ ΠΊΠΎΠ½ΡΡΠΎΠ»Ρ ΠΎΡΠ½ΠΎΡΠΈΡΡΡ Π»ΠΈΡΡ ΠΊ ΠΏΠΎΠΊΠ°Π·Π°ΡΠ΅Π»ΡΠΌ Π²ΡΠΏΡΡΠΊΠ°Π΅ΠΌΠΎΠΉ ΠΏΡΠΎΠ΄ΡΠΊΡΠΈΠΈ ΠΈ ΠΏΡΠΎΡΠ΅ΡΡΠ°ΠΌ.
- ΠΠ΅ ΡΡΠΎΠΈΡ Π½Π΅Π΄ΠΎΠΎΡΠ΅Π½ΠΈΠ²Π°ΡΡ ΠΌΠΎΡΡ Π΄ΠΎΠΌΠ° Π³Π΅ΠΌΠ±Ρ
- ΠΠ΅ ΡΡΠΎΠΈΡ Π½Π΅Π΄ΠΎΠΎΡΠ΅Π½ΠΈΠ²Π°ΡΡ ΠΊΡΠ»ΡΡΡΡΠ½ΡΠ΅ ΠΈ ΡΠΏΡΠ°Π²Π»Π΅Π½ΡΠ΅ΡΠΊΠΈΠ΅ Π°ΡΠΏΠ΅ΠΊΡΡ Π±Π΅ΡΠ΅ΠΆΠ»ΠΈΠ²ΠΎΠ³ΠΎ ΠΏΠΎΠ΄Ρ ΠΎΠ΄Π°. ΠΠ½ΠΈ ΡΡΠΎΠ»Ρ ΠΆΠ΅ Π²Π°ΠΆΠ½Ρ, Π° ΠΌΠΎΠΆΠ΅Ρ Π±ΡΡΡ Π΄Π°ΠΆΠ΅ ΠΈ Π±ΠΎΠ»ΡΡΠ΅, ΠΊΠ°ΠΊ ΠΈ ΠΏΡΠΈΠ΅ΠΌΡ ΠΈ ΠΈΠ½ΡΡΡΡΠΌΠ΅Π½ΡΡ Π±Π΅ΡΠ΅ΠΆΠ»ΠΈΠ²ΠΎΠ³ΠΎ ΠΏΡΠΎΠΈΠ·Π²ΠΎΠ΄ΡΡΠ²Π°. ΠΠΎΠΆΠ½ΠΎ ΠΏΡΠΈΠ²Π΅ΡΡΠΈ ΠΌΠ½ΠΎΠΆΠ΅ΡΡΠ²ΠΎ ΠΏΡΠΈΠΌΠ΅ΡΠΎΠ² ΠΏΡΠΎΠ΅ΠΊΡΠΎΠ² Π±Π΅ΡΠ΅ΠΆΠ»ΠΈΠ²ΠΎΠ³ΠΎ ΠΏΠΎΠ΄Ρ ΠΎΠ΄Π°, ΠΊΠΎΡΠΎΡΡΠ΅ ΠΎΠΊΠ°Π·Π°Π»ΠΈΡΡ Π½Π΅ΡΠ΄Π°ΡΠ½ΡΠΌΠΈ ΡΠΎΠ»ΡΠΊΠΎ ΠΈΠ·-Π·Π° ΡΠΎΠ³ΠΎ, ΡΡΠΎ Π»ΡΠ΄ΠΈ, ΠΊΠΎΡΠΎΡΡΠ΅ Π·Π°Π½ΠΈΠΌΠ°Π»ΠΈΡΡ ΠΈΡ ΡΠ΅Π°Π»ΠΈΠ·Π°ΡΠΈΠ΅ΠΉ, Π½Π΅ ΠΏΠΎΠ½ΠΈΠΌΠ°Π»ΠΈ Π²Π»ΠΈΡΠ½ΠΈΡ Π±Π΅ΡΠ΅ΠΆΠ»ΠΈΠ²ΠΎΠΉ ΡΠΈΠ»ΠΎΡΠΎΡΠΈΠΈ Π½Π° ΠΊΠΎΠΌΠΏΠ°Π½ΠΈΡ.
Π’Π°ΠΊΠΆΠ΅ ΠΠ°ΠΌ Π±ΡΠ΄Π΅Ρ ΠΈΠ½ΡΠ΅ΡΠ΅ΡΠ½ΠΎ:
chiefengineer.ru
Π‘ΠΈΡΡΠ΅ΠΌΡ ΡΠΎΡΠ½ΠΎ-Π²-ΡΡΠΎΠΊ (JIT: just-in-time): ΡΠ°Π·ΡΠ°Π±ΠΎΡΠΊΠ° ΠΈ Π²Π½Π΅Π΄ΡΠ΅Π½ΠΈΠ΅
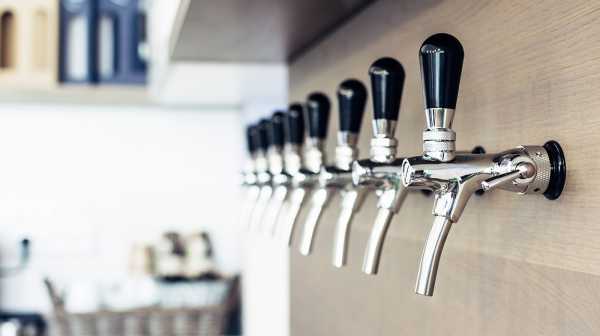
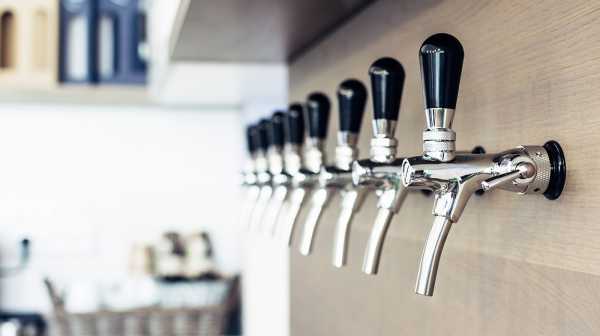
ΠΠ²ΡΠΎΡ: Π£ΠΈΠ»ΡΡΠΌ ΠΠΆ. Π‘ΡΠΈΠ²Π΅Π½ΡΠΎΠ½ (William J. Stevenson), ΠΏΡΠΎΡΠ΅ΡΡΠΎΡ Π ΠΎΡΠ΅ΡΡΠ΅ΡΡΠΊΠΎΠ³ΠΎ ΡΠ΅Ρ Π½ΠΎΠ»ΠΎΠ³ΠΈΡΠ΅ΡΠΊΠΎΠ³ΠΎ ΠΈΠ½ΡΡΠΈΡΡΡΠ° (ΠΡΡ-ΠΠΎΡΠΊ). ΠΠ°ΡΠ΅ΡΠΈΠ°Π» ΠΏΡΠ±Π»ΠΈΠΊΡΠ΅ΡΡΡ Π² Π°Π΄Π°ΠΏΡΠΈΡΠΎΠ²Π°Π½Π½ΠΎΠΌ ΠΏΠ΅ΡΠ΅Π²ΠΎΠ΄Π΅ Ρ Π°Π½Π³Π»ΠΈΠΉΡΠΊΠΎΠ³ΠΎ.
Β
Π’Π΅ΡΠΌΠΈΠ½ Β«ΡΠΎΡΠ½ΠΎ-Π²-ΡΡΠΎΠΊΒ» (just-in-time β JIT) ΠΈΡΠΏΠΎΠ»ΡΠ·ΡΠ΅ΡΡΡ ΠΏΠΎ ΠΎΡΠ½ΠΎΡΠ΅Π½ΠΈΡ ΠΊ ΠΏΡΠΎΠΌΡΡΠ»Π΅Π½Π½ΡΠΌ ΡΠΈΡΡΠ΅ΠΌΠ°ΠΌ, Π² ΠΊΠΎΡΠΎΡΡΡ ΠΏΠ΅ΡΠ΅ΠΌΠ΅ΡΠ΅Π½ΠΈΠ΅ ΠΈΠ·Π΄Π΅Π»ΠΈΠΉ Π² ΠΏΡΠΎΡΠ΅ΡΡΠ΅ ΠΏΡΠΎΠΈΠ·Π²ΠΎΠ΄ΡΡΠ²Π° ΠΈ ΠΏΠΎΡΡΠ°Π²ΠΊΠΈ ΠΎΡ ΠΏΠΎΡΡΠ°Π²ΡΠΈΠΊΠΎΠ² ΡΡΠ°ΡΠ΅Π»ΡΠ½ΠΎ ΡΠΏΠ»Π°Π½ΠΈΡΠΎΠ²Π°Π½Ρ Π²ΠΎ Π²ΡΠ΅ΠΌΠ΅Π½ΠΈ β ΡΠ°ΠΊ, ΡΡΠΎ Π½Π° ΠΊΠ°ΠΆΠ΄ΠΎΠΌ ΡΡΠ°ΠΏΠ΅ ΠΏΡΠΎΡΠ΅ΡΡΠ° ΡΠ»Π΅Π΄ΡΡΡΠ°Ρ (ΠΎΠ±ΡΡΠ½ΠΎ Π½Π΅Π±ΠΎΠ»ΡΡΠ°Ρ) ΠΏΠ°ΡΡΠΈΡ ΠΏΡΠΈΠ±ΡΠ²Π°Π΅Ρ Π΄Π»Ρ ΠΎΠ±ΡΠ°Π±ΠΎΡΠΊΠΈ ΡΠΎΡΠ½ΠΎ Π² ΡΠΎΡ ΠΌΠΎΠΌΠ΅Π½Ρ, ΠΊΠΎΠ³Π΄Π° ΠΏΡΠ΅Π΄ΡΠ΄ΡΡΠ°Ρ ΠΏΠ°ΡΡΠΈΡ Π·Π°Π²Π΅ΡΡΠ΅Π½Π°. ΠΡΡΡΠ΄Π° ΠΈ Π½Π°Π·Π²Π°Π½ΠΈΠ΅ just-in-time (ΡΠΎΡΠ½ΠΎ Π² ΡΡΠΎΠΊ, ΡΠΎΠ»ΡΠΊΠΎ Π²ΠΎΠ²ΡΠ΅ΠΌΡ). Π ΡΠ΅Π·ΡΠ»ΡΡΠ°ΡΠ΅ ΠΏΠΎΠ»ΡΡΠ°Π΅ΡΡΡ ΡΠΈΡΡΠ΅ΠΌΠ°, Π² ΠΊΠΎΡΠΎΡΠΎΠΉ ΠΎΡΡΡΡΡΡΠ²ΡΡΡ Π»ΡΠ±ΡΠ΅ ΠΏΠ°ΡΡΠΈΠ²Π½ΡΠ΅ Π΅Π΄ΠΈΠ½ΠΈΡΡ, ΠΎΠΆΠΈΠ΄Π°ΡΡΠΈΠ΅ ΠΎΠ±ΡΠ°Π±ΠΎΡΠΊΠΈ, Π° ΡΠ°ΠΊΠΆΠ΅ ΠΏΡΠΎΡΡΠ°ΠΈΠ²Π°ΡΡΠΈΠ΅ ΡΠ°Π±ΠΎΡΠΈΠ΅ ΠΈΠ»ΠΈ ΠΎΠ±ΠΎΡΡΠ΄ΠΎΠ²Π°Π½ΠΈΠ΅, ΠΎΠΆΠΈΠ΄Π°ΡΡΠΈΠ΅ ΠΈΠ·Π΄Π΅Π»ΠΈΡ Π΄Π»Ρ ΠΎΠ±ΡΠ°Π±ΠΎΡΠΊΠΈ.
Π―Π²Π»Π΅Π½ΠΈΠ΅ Β«ΡΠΎΡΠ½ΠΎ-Π²-ΡΡΠΎΠΊΒ» (JIT) Ρ Π°ΡΠ°ΠΊΡΠ΅ΡΠ½ΠΎ Π΄Π»Ρ ΠΏΡΠΎΠΈΠ·Π²ΠΎΠ΄ΡΡΠ²Π΅Π½Π½ΡΡ ΡΠΈΡΡΠ΅ΠΌ, ΠΊΠΎΡΠΎΡΡΠ΅ ΡΡΠ½ΠΊΡΠΈΠΎΠ½ΠΈΡΡΡΡ Ρ ΠΎΡΠ΅Π½Ρ Π½Π΅Π±ΠΎΠ»ΡΡΠΈΠΌ Β«ΠΆΠΈΡΠΎΠ²ΡΠΌ Π·Π°ΠΏΠ°ΡΠΎΠΌΒ» (Π½Π°ΠΏΡΠΈΠΌΠ΅Ρ, ΠΈΠ·Π»ΠΈΡΠ½ΠΈΠ΅ ΠΌΠ°ΡΠ΅ΡΠΈΠ°Π»ΡΠ½ΡΠ΅ Π·Π°ΠΏΠ°ΡΡ, ΠΈΠ·Π±ΡΡΠΎΠΊ ΡΠ°Π±ΠΎΡΠ΅ΠΉ ΡΠΈΠ»Ρ, ΠΈΠ·Π»ΠΈΡΠ½ΠΈΠ΅ ΠΏΡΠΎΠΈΠ·Π²ΠΎΠ΄ΡΡΠ²Π΅Π½Π½ΡΠ΅ ΠΏΠ»ΠΎΡΠ°Π΄ΠΈ). JIT ΠΎΡΠ½ΠΎΡΠΈΡΡΡ ΠΊ ΡΠ°ΡΠΏΡΠ΅Π΄Π΅Π»Π΅Π½ΠΈΡ Π²ΠΎ Π²ΡΠ΅ΠΌΠ΅Π½ΠΈ Π΄Π²ΠΈΠΆΠ΅Π½ΠΈΡ ΡΠ΅ΡΠ΅Π· ΡΠΈΡΡΠ΅ΠΌΡ Π΄Π΅ΡΠ°Π»Π΅ΠΉ ΠΈ ΠΌΠ°ΡΠ΅ΡΠΈΠ°Π»ΠΎΠ², Π° ΡΠ°ΠΊΠΆΠ΅ ΡΡΠ»ΡΠ³.
ΠΠΎΠΌΠΏΠ°Π½ΠΈΠΈ, ΠΈΡΠΏΠΎΠ»ΡΠ·ΡΡΡΠΈΠ΅ ΠΏΠΎΠ΄Ρ ΠΎΠ΄ JIT ΠΎΠ±ΡΡΠ½ΠΎ ΠΈΠΌΠ΅ΡΡ Π·Π½Π°ΡΠΈΡΠ΅Π»ΡΠ½ΠΎΠ΅ ΠΏΡΠ΅ΠΈΠΌΡΡΠ΅ΡΡΠ²ΠΎ ΠΏΠ΅ΡΠ΅Π΄ ΡΠ²ΠΎΠΈΠΌΠΈ ΠΊΠΎΠ½ΠΊΡΡΠ΅Π½ΡΠ°ΠΌΠΈ, ΠΊΠΎΡΠΎΡΡΠ΅ ΠΈΡΠΏΠΎΠ»ΡΠ·ΡΡΡ Π±ΠΎΠ»Π΅Π΅ ΡΡΠ°Π΄ΠΈΡΠΈΠΎΠ½Π½ΡΠΉ ΠΏΠΎΠ΄Ρ ΠΎΠ΄. Π£ Π½ΠΈΡ Π½ΠΈΠΆΠ΅ ΡΡΠΎΠΈΠΌΠΎΡΡΡ ΠΏΡΠΎΠΈΠ·Π²ΠΎΠ΄ΡΡΠ²Π°, ΠΌΠ΅Π½ΡΡΠ΅ Π±ΡΠ°ΠΊΠ°, Π²ΡΡΠ΅ Π³ΠΈΠ±ΠΊΠΎΡΡΡ ΠΈ ΡΠΏΠΎΡΠΎΠ±Π½ΠΎΡΡΡ Π±ΡΡΡΡΠΎ ΠΏΡΠ΅Π΄ΠΎΡΡΠ°Π²Π»ΡΡΡ Π½Π° ΡΡΠ½ΠΎΠΊ Π½ΠΎΠ²ΡΠ΅ ΠΈΠ»ΠΈ ΡΡΠΎΠ²Π΅ΡΡΠ΅Π½ΡΡΠ²ΠΎΠ²Π°Π½Π½ΡΠ΅ ΡΠΎΠ²Π°ΡΡ.
Π Π΄Π°Π½Π½ΠΎΠΉ ΠΏΡΠ±Π»ΠΈΠΊΠ°ΡΠΈΠΈ ΠΌΡ ΡΠ°ΡΡΠΌΠΎΡΡΠΈΠΌ ΡΠΈΡΡΠ΅ΠΌΡ Β«ΡΠΎΡΠ½ΠΎ-Π²-ΡΡΠΎΠΊΒ» (JIT), Π²ΠΊΠ»ΡΡΠ°Ρ Π΅Π΅ ΠΎΡΠ½ΠΎΠ²Π½ΡΠ΅ ΡΠ»Π΅ΠΌΠ΅Π½ΡΡ ΠΈ ΡΠ°ΠΊΡΠΎΡΡ, ΠΊΠΎΡΠΎΡΡΠ΅ ΡΡΠ΅Π±ΡΡΡΡΡ Π΄Π»Ρ ΡΡΡΠ΅ΠΊΡΠΈΠ²Π½ΠΎΠΉ ΡΠ°Π±ΠΎΡΡ.
Β
ΠΠΎΠ΄Ρ ΠΎΠ΄ Β«ΡΠΎΡΠ½ΠΎ-Π²-ΡΡΠΎΠΊΒ» Π±ΡΠ» ΡΠ°Π·ΡΠ°Π±ΠΎΡΠ°Π½ Π² ΡΠΏΠΎΠ½ΡΠΊΠΎΠΉ Π°Π²ΡΠΎΠΌΠΎΠ±ΠΈΠ»ΡΠ½ΠΎΠΉ ΠΊΠΎΠΌΠΏΠ°Π½ΠΈΠΈ Toyota. ΠΠ³ΠΎ Π°Π²ΡΠΎΡ β Π’Π°ΠΉΠΈΡΠΈ ΠΠ½ΠΎ (ΠΊΠΎΡΠΎΡΡΠΉ Π² ΠΊΠΎΠ½Π΅ΡΠ½ΠΎΠΌ ΡΡΠ΅ΡΠ΅ ΡΡΠ°Π» Π²ΠΈΡΠ΅-ΠΏΡΠ΅Π·ΠΈΠ΄Π΅Π½ΡΠΎΠΌ ΠΊΠΎΠΌΠΏΠ°Π½ΠΈΠΈ ΠΏΠΎ ΠΏΡΠΎΠΈΠ·Π²ΠΎΠ΄ΡΡΠ²Ρ) ΠΈ Π½Π΅ΡΠΊΠΎΠ»ΡΠΊΠΎ Π΅Π³ΠΎ ΠΊΠΎΠ»Π»Π΅Π³. ΠΠ° ΡΠΎ, ΡΡΠΎ JIT Π±ΡΠ»Π° ΡΠ°Π·ΡΠ°Π±ΠΎΡΠ°Π½Π° ΠΈΠΌΠ΅Π½Π½ΠΎ Π² Π―ΠΏΠΎΠ½ΠΈΠΈ, Π²Π΅ΡΠΎΡΡΠ½ΠΎ, ΠΏΠΎΠ²Π»ΠΈΡΠ» ΡΠ°ΠΊΡ, ΡΡΠΎ Π―ΠΏΠΎΠ½ΠΈΡ ΡΠ²Π»ΡΠ΅ΡΡΡ ΠΏΠ΅ΡΠ΅Π½Π°ΡΠ΅Π»Π΅Π½Π½ΠΎΠΉ ΡΡΡΠ°Π½ΠΎΠΉ Ρ ΠΎΡΠ΅Π½Ρ ΠΎΠ³ΡΠ°Π½ΠΈΡΠ΅Π½Π½ΡΠΌΠΈ ΠΏΡΠΈΡΠΎΠ΄Π½ΡΠΌΠΈ ΡΠ΅ΡΡΡΡΠ°ΠΌΠΈ. ΠΠ΅ΡΠ΄ΠΈΠ²ΠΈΡΠ΅Π»ΡΠ½ΠΎ ΠΏΠΎΡΡΠΎΠΌΡ, ΡΡΠΎ ΡΠΏΠΎΠ½ΡΡ ΠΎΡΠ΅Π½Ρ ΡΡΠ²ΡΡΠ²ΠΈΡΠ΅Π»ΡΠ½Ρ ΠΊ ΠΏΡΡΡΡΠΌ ΡΡΠ°ΡΠ°ΠΌ ΠΌΠ°ΡΠ΅ΡΠΈΠ°Π»ΠΎΠ², Π²ΡΠ΅ΠΌΠ΅Π½ΠΈ ΠΈ ΡΡΠ΅Π΄ΡΡΠ², ΠΈ ΠΊ Π½Π΅ΡΡΡΠ΅ΠΊΡΠΈΠ²Π½ΠΎΡΡΠΈ ΡΡΡΠ΄Π°. ΠΠ½ΠΈ ΡΠ°ΡΡΠ΅Π½ΠΈΠ²Π°ΡΡ Π±ΡΠ°ΠΊ ΠΈ ΠΈΡΠΏΡΠ°Π²Π»Π΅Π½ΠΈΡ Π΄Π΅ΡΠ΅ΠΊΡΠΎΠ² ΠΊΠ°ΠΊ Π½Π΅ΠΎΠ±ΠΎΡΠ½ΠΎΠ²Π°Π½Π½ΡΠ΅ Π·Π°ΡΡΠ°ΡΡ, Π° Π·Π°ΠΏΠ°ΡΡ β ΠΊΠ°ΠΊ Π·Π»ΠΎ, ΠΏΠΎΡΠΎΠΌΡ ΡΡΠΎ ΠΎΠ½ΠΈ Π·Π°Π½ΠΈΠΌΠ°ΡΡ ΠΏΡΠΎΡΡΡΠ°Π½ΡΡΠ²ΠΎ ΠΈ ΡΠ²ΡΠ·ΡΠ²Π°ΡΡ ΡΠ΅ΡΡΡΡΡ.
Π¨ΠΈΡΠΎΠΊΠΎ ΡΠ°ΡΠΏΡΠΎΡΡΡΠ°Π½Π΅Π½ΠΎ ΠΌΠ½Π΅Π½ΠΈΠ΅, ΡΡΠΎ ΡΠΈΡΡΠ΅ΠΌΠ° JIT β ΡΡΠΎ ΠΏΡΠΎΡΡΠΎ ΡΠΎΠΎΡΠ²Π΅ΡΡΡΠ²ΡΡΡΠ΅Π΅ ΠΏΠ»Π°Π½ΠΈΡΠΎΠ²Π°Π½ΠΈΠ΅ ΠΏΡΠΎΠΈΠ·Π²ΠΎΠ΄ΡΡΠ²Π°, ΡΠ΅Π·ΡΠ»ΡΡΠ°ΡΠΎΠΌ ΠΊΠΎΡΠΎΡΠΎΠ³ΠΎ ΡΠ²Π»ΡΠ΅ΡΡΡ ΠΌΠΈΠ½ΠΈΠΌΠ°Π»ΡΠ½ΡΠΉ ΡΡΠΎΠ²Π΅Π½Ρ Π½Π΅Π·Π°Π²Π΅ΡΡΠ΅Π½Π½ΠΎΠ³ΠΎ ΠΏΡΠΎΠΈΠ·Π²ΠΎΠ΄ΡΡΠ²Π° ΠΈ ΠΌΠ°ΡΠ΅ΡΠΈΠ°Π»ΡΠ½ΡΡ Π·Π°ΠΏΠ°ΡΠΎΠ². ΠΠΎ Π² ΡΡΡΠ½ΠΎΡΡΠΈ, JIT ΠΏΡΠ΅Π΄ΡΡΠ°Π²Π»ΡΠ΅Ρ ΡΠΎΠ±ΠΎΠΉ ΠΎΠΏΡΠ΅Π΄Π΅Π»Π΅Π½Π½ΡΡ ΡΠΈΠ»ΠΎΡΠΎΡΠΈΡ, ΠΊΠΎΡΠΎΡΠ°Ρ ΠΎΡ Π²Π°ΡΡΠ²Π°Π΅Ρ ΠΊΠ°ΠΆΠ΄ΡΠΉ Π°ΡΠΏΠ΅ΠΊΡ ΠΏΡΠΎΠΈΠ·Π²ΠΎΠ΄ΡΡΠ²Π΅Π½Π½ΠΎΠ³ΠΎ ΠΏΡΠΎΡΠ΅ΡΡΠ°, ΠΎΡ ΡΠ°Π·ΡΠ°Π±ΠΎΡΠΊΠΈ Π΄ΠΎ ΠΏΡΠΎΠ΄Π°ΠΆΠΈ ΠΈΠ·Π΄Π΅Π»ΠΈΡ ΠΈ ΠΏΠΎΡΠ»Π΅ΠΏΡΠΎΠ΄Π°ΠΆΠ½ΠΎΠ³ΠΎ ΠΎΠ±ΡΠ»ΡΠΆΠΈΠ²Π°Π½ΠΈΡ.
ΠΡΠ° ΡΠΈΠ»ΠΎΡΠΎΡΠΈΡ ΡΡΡΠ΅ΠΌΠΈΡΡΡ ΠΊ ΡΠΎΠ·Π΄Π°Π½ΠΈΡ ΡΠΈΡΡΠ΅ΠΌΡ, ΠΊΠΎΡΠΎΡΠ°Ρ Ρ ΠΎΡΠΎΡΠΎ ΡΡΠ½ΠΊΡΠΈΠΎΠ½ΠΈΡΡΠ΅Ρ Ρ ΠΌΠΈΠ½ΠΈΠΌΠ°Π»ΡΠ½ΡΠΌ ΡΡΠΎΠ²Π½Π΅ΠΌ ΠΌΠ°ΡΠ΅ΡΠΈΠ°Π»ΡΠ½ΡΡ Π·Π°ΠΏΠ°ΡΠΎΠ², ΠΌΠΈΠ½ΠΈΠΌΠ°Π»ΡΠ½ΡΠΌ ΠΏΡΠΎΡΡΡΠ°Π½ΡΡΠ²ΠΎΠΌ ΠΈ ΠΌΠΈΠ½ΠΈΠΌΠ°Π»ΡΠ½ΡΠΌ Π΄Π΅Π»ΠΎΠΏΡΠΎΠΈΠ·Π²ΠΎΠ΄ΡΡΠ²ΠΎΠΌ. ΠΡΠΎ Π΄ΠΎΠ»ΠΆΠ½Π° Π±ΡΡΡ ΡΠΈΡΡΠ΅ΠΌΠ°, ΠΊΠΎΡΠΎΡΠ°Ρ Π½Π΅ ΠΏΠΎΠ΄Π΄Π°Π΅ΡΡΡ ΡΠ±ΠΎΡΠΌ ΠΈ Π½Π°ΡΡΡΠ΅Π½ΠΈΡΠΌ ΠΈ ΡΠ²Π»ΡΠ΅ΡΡΡ Π³ΠΈΠ±ΠΊΠΎΠΉ (Π² ΡΠΎΠΌ ΡΡΠΎ ΠΊΠ°ΡΠ°Π΅ΡΡΡ ΠΈΠ·ΠΌΠ΅Π½Π΅Π½ΠΈΠΉ Π°ΡΡΠΎΡΡΠΈΠΌΠ΅Π½ΡΠ° ΠΈΠ·Π΄Π΅Π»ΠΈΠΉ ΠΈ ΠΎΠ±ΡΠ΅ΠΌΠ° ΠΏΡΠΎΠΈΠ·Π²ΠΎΠ΄ΡΡΠ²Π°). ΠΠΎΠ½Π΅ΡΠ½Π°Ρ ΡΠ΅Π»Ρ ΡΠΎΡΡΠΎΠΈΡ Π² ΡΠΎΠΌ, ΡΡΠΎΠ±Ρ ΠΏΠΎΠ»ΡΡΠΈΡΡ ΡΠ±Π°Π»Π°Π½ΡΠΈΡΠΎΠ²Π°Π½Π½ΡΡ ΡΠΈΡΡΠ΅ΠΌΡ Ρ ΠΏΠ»Π°Π²Π½ΡΠΌ ΠΈ Π±ΡΡΡΡΡΠΌ ΠΏΠΎΡΠΎΠΊΠΎΠΌ ΠΌΠ°ΡΠ΅ΡΠΈΠ°Π»ΠΎΠ² ΡΠ΅ΡΠ΅Π· ΡΠΈΡΡΠ΅ΠΌΡ.
Π ΡΠΈΡΡΠ΅ΠΌΠ°Ρ JIT ΠΊΠ°ΡΠ΅ΡΡΠ²ΠΎ Β«Π²ΡΡΡΠΎΠ΅Π½ΠΎΒ» ΠΊΠ°ΠΊ Π² ΠΈΠ·Π΄Π΅Π»ΠΈΠ΅, ΡΠ°ΠΊ ΠΈ Π² ΠΏΡΠΎΠΈΠ·Π²ΠΎΠ΄ΡΡΠ²Π΅Π½Π½ΡΠΉ ΠΏΡΠΎΡΠ΅ΡΡ. ΠΠΎΠΌΠΏΠ°Π½ΠΈΠΈ, ΠΊΠΎΡΠΎΡΡΠ΅ ΠΈΡΠΏΠΎΠ»ΡΠ·ΡΡΡ ΡΠΈΡΡΠ΅ΠΌΡ JIT, Π΄ΠΎΡΡΠΈΠ³Π»ΠΈ ΡΠ°ΠΊΠΎΠ³ΠΎ ΡΡΠΎΠ²Π½Ρ ΠΊΠ°ΡΠ΅ΡΡΠ²Π°, ΠΊΠΎΡΠΎΡΠΎΠ΅ ΠΏΠΎΠ·Π²ΠΎΠ»ΡΠ΅Ρ ΠΈΠΌ ΡΠ°Π±ΠΎΡΠ°ΡΡ Ρ Π½Π΅Π±ΠΎΠ»ΡΡΠΈΠΌΠΈ ΠΏΡΠΎΠΈΠ·Π²ΠΎΠ΄ΡΡΠ²Π΅Π½Π½ΡΠΌΠΈ ΠΏΠ°ΡΡΠΈΡΠΌΠΈ ΠΈ ΠΏΠ»ΠΎΡΠ½ΡΠΌ Π³ΡΠ°ΡΠΈΠΊΠΎΠΌ. ΠΡΠΈ ΡΠΈΡΡΠ΅ΠΌΡ ΠΈΠΌΠ΅ΡΡ Π²ΡΡΠΎΠΊΡΡ Π½Π°Π΄Π΅ΠΆΠ½ΠΎΡΡΡ, ΠΈΡΠΊΠ»ΡΡΠ΅Π½Ρ Π³Π»Π°Π²Π½ΡΠ΅ ΠΈΡΡΠΎΡΠ½ΠΈΠΊΠΈ Π½Π΅ΡΡΡΠ΅ΠΊΡΠΈΠ²Π½ΠΎΡΡΠΈ ΠΈ ΡΡΡΠ²ΠΎΠ², Π° ΡΠ°Π±ΠΎΡΠΈΠ΅ ΠΎΠ±ΡΡΠ΅Π½Ρ Π½Π΅ ΡΠΎΠ»ΡΠΊΠΎ ΡΡΡΠ΄ΠΈΡΡΡΡ Π² ΡΠΈΡΡΠ΅ΠΌΠ΅, Π½ΠΎ ΠΈ Π½Π΅ΠΏΡΠ΅ΡΡΠ²Π½ΠΎ Π΅Π΅ ΡΠΎΠ²Π΅ΡΡΠ΅Π½ΡΡΠ²ΠΎΠ²Π°ΡΡ.
Β
ΠΠΎΠ½Π΅ΡΠ½Π°Ρ ΡΠ΅Π»Ρ ΡΠΈΡΡΠ΅ΠΌΡ JIT β ΡΡΠΎ ΡΠ±Π°Π»Π°Π½ΡΠΈΡΠΎΠ²Π°Π½Π½Π°Ρ ΡΠΈΡΡΠ΅ΠΌΠ°; ΡΠΎ Π΅ΡΡΡ ΡΠ°ΠΊΠ°Ρ, ΠΊΠΎΡΠΎΡΠ°Ρ ΠΎΠ±Π΅ΡΠΏΠ΅ΡΠΈΠ²Π°Π΅Ρ ΠΏΠ»Π°Π²Π½ΡΠΉ ΠΈ Π±ΡΡΡΡΡΠΉ ΠΏΠΎΡΠΎΠΊ ΠΌΠ°ΡΠ΅ΡΠΈΠ°Π»ΠΎΠ² ΡΠ΅ΡΠ΅Π· ΡΠΈΡΡΠ΅ΠΌΡ. ΠΡΠ½ΠΎΠ²Π½Π°Ρ ΠΈΠ΄Π΅Ρ ΡΠΎΡΡΠΎΠΈΡ Π² ΡΠΎΠΌ, ΡΡΠΎΠ±Ρ ΡΠ΄Π΅Π»Π°ΡΡ ΠΏΡΠΎΡΠ΅ΡΡ ΠΊΠ°ΠΊ ΠΌΠΎΠΆΠ½ΠΎ ΠΊΠΎΡΠΎΡΠ΅, ΠΈΡΠΏΠΎΠ»ΡΠ·ΡΡ ΡΠ΅ΡΡΡΡΡ ΠΎΠΏΡΠΈΠΌΠ°Π»ΡΠ½ΡΠΌ ΡΠΏΠΎΡΠΎΠ±ΠΎΠΌ. Π‘ΡΠ΅ΠΏΠ΅Π½Ρ Π΄ΠΎΡΡΠΈΠΆΠ΅Π½ΠΈΡ ΡΡΠΎΠΉ ΡΠ΅Π»ΠΈ Π·Π°Π²ΠΈΡΠΈΡ ΠΎΡ ΡΠΎΠ³ΠΎ, Π½Π°ΡΠΊΠΎΠ»ΡΠΊΠΎ Π΄ΠΎΡΡΠΈΠ³Π½ΡΡΡ Π΄ΠΎΠΏΠΎΠ»Π½ΠΈΡΠ΅Π»ΡΠ½ΡΠ΅ (Π²ΡΠΏΠΎΠΌΠΎΠ³Π°ΡΠ΅Π»ΡΠ½ΡΠ΅) ΡΠ΅Π»ΠΈ, ΡΠ°ΠΊΠΈΠ΅ ΠΊΠ°ΠΊ:
- ΠΡΠΊΠ»ΡΡΠΈΡΡ ΡΠ±ΠΎΠΈ ΠΈ Π½Π°ΡΡΡΠ΅Π½ΠΈΡ ΠΏΡΠΎΡΠ΅ΡΡΠ° ΠΏΡΠΎΠΈΠ·Π²ΠΎΠ΄ΡΡΠ²Π°.
- Π‘Π΄Π΅Π»Π°ΡΡ ΡΠΈΡΡΠ΅ΠΌΡ Π³ΠΈΠ±ΠΊΠΎΠΉ.
- Π‘ΠΎΠΊΡΠ°ΡΠΈΡΡ Π²ΡΠ΅ΠΌΡ ΠΏΠΎΠ΄Π³ΠΎΡΠΎΠ²ΠΊΠΈ ΠΊ ΠΏΡΠΎΡΠ΅ΡΡΡ ΠΈ Π²ΡΠ΅ ΠΏΡΠΎΠΈΠ·Π²ΠΎΠ΄ΡΡΠ²Π΅Π½Π½ΡΠ΅ ΡΡΠΎΠΊΠΈ.
- Π‘Π²Π΅ΡΡΠΈ ΠΊ ΠΌΠΈΠ½ΠΈΠΌΡΠΌΡ ΠΌΠ°ΡΠ΅ΡΠΈΠ°Π»ΡΠ½ΡΠ΅ Π·Π°ΠΏΠ°ΡΡ.
- Π£ΡΡΡΠ°Π½ΠΈΡΡ Π½Π΅ΠΎΠ±ΠΎΡΠ½ΠΎΠ²Π°Π½Π½ΡΠ΅ Π·Π°ΡΡΠ°ΡΡ.
Β
Π‘Π±ΠΎΠΈ ΠΈ Π½Π°ΡΡΡΠ΅Π½ΠΈΡ ΠΏΡΠΎΡΠ΅ΡΡΠ° ΠΎΠΊΠ°Π·ΡΠ²Π°ΡΡ ΠΎΡΡΠΈΡΠ°ΡΠ΅Π»ΡΠ½ΠΎΠ΅ Π²ΠΎΠ·Π΄Π΅ΠΉΡΡΠ²ΠΈΠ΅ Π½Π° ΡΠΈΡΡΠ΅ΠΌΡ, Π½Π°ΡΡΡΠ°Ρ ΠΏΠ»Π°Π²Π½ΡΠΉ ΠΏΠΎΡΠΎΠΊ ΠΈΠ·Π΄Π΅Π»ΠΈΠΉ, ΠΏΠΎΡΡΠΎΠΌΡ ΠΈΡ Π½Π΅ΠΎΠ±Ρ ΠΎΠ΄ΠΈΠΌΠΎ ΠΈΡΠΊΠ»ΡΡΠΈΡΡ. Π‘ΡΡΠ²Ρ Π²ΡΠ·ΡΠ²Π°ΡΡΡΡ ΡΠ°ΠΌΡΠΌΠΈ ΡΠ°Π·Π½ΠΎΠΎΠ±ΡΠ°Π·Π½ΡΠΌΠΈ ΡΠ°ΠΊΡΠΎΡΠ°ΠΌΠΈ: Π½ΠΈΠ·ΠΊΠΈΠΌ ΠΊΠ°ΡΠ΅ΡΡΠ²ΠΎΠΌ, Π½Π΅ΠΈΡΠΏΡΠ°Π²Π½ΠΎΡΡΡΡ ΠΎΠ±ΠΎΡΡΠ΄ΠΎΠ²Π°Π½ΠΈΡ, ΠΈΠ·ΠΌΠ΅Π½Π΅Π½ΠΈΡΠΌΠΈ Π² Π³ΡΠ°ΡΠΈΠΊΠ°Ρ , ΠΎΠΏΠΎΠ·Π΄Π°Π½ΠΈΠ΅ΠΌ ΠΏΠΎΡΡΠ°Π²ΠΎΠΊ. ΠΡΠ΅ ΡΡΠΈ ΡΠ°ΠΊΡΠΎΡΡ ΡΠ»Π΅Π΄ΡΠ΅Ρ ΠΏΠΎ Π²ΠΎΠ·ΠΌΠΎΠΆΠ½ΠΎΡΡΠΈ ΠΈΡΠΊΠ»ΡΡΠΈΡΡ.
ΠΡΠ΅ΠΌΡ ΠΏΠΎΠ΄Π³ΠΎΡΠΎΠ²ΠΊΠΈ ΠΈ ΠΏΡΠΎΠΈΠ·Π²ΠΎΠ΄ΡΡΠ²Π΅Π½Π½ΡΠ΅ ΡΡΠΎΠΊΠΈ ΡΠ΄Π»ΠΈΠ½ΡΡΡ ΠΏΡΠΎΡΠ΅ΡΡ, Π½ΠΈΡΠ΅Π³ΠΎ Π½Π΅ Π΄ΠΎΠ±Π°Π²Π»ΡΡ ΠΏΡΠΈ ΡΡΠΎΠΌ ΠΊ ΡΡΠΎΠΈΠΌΠΎΡΡΠΈ ΠΈΠ·Π΄Π΅Π»ΠΈΡ. ΠΡΠΎΠΌΠ΅ ΡΠΎΠ³ΠΎ, ΠΏΡΠΎΠ΄ΠΎΠ»ΠΆΠΈΡΠ΅Π»ΡΠ½ΠΎΡΡΡ ΡΡΠΈΡ ΡΡΠΎΠΊΠΎΠ² ΠΎΡΡΠΈΡΠ°ΡΠ΅Π»ΡΠ½ΠΎ Π²ΠΎΠ·Π΄Π΅ΠΉΡΡΠ²ΡΠ΅Ρ Π½Π° Π³ΠΈΠ±ΠΊΠΎΡΡΡ ΡΠΈΡΡΠ΅ΠΌΡ. Π‘Π»Π΅Π΄ΠΎΠ²Π°ΡΠ΅Π»ΡΠ½ΠΎ, ΠΈΡ ΡΠΎΠΊΡΠ°ΡΠ΅Π½ΠΈΠ΅ ΠΎΡΠ΅Π½Ρ Π²Π°ΠΆΠ½ΠΎ ΠΈ ΡΠ²Π»ΡΠ΅ΡΡΡ ΠΎΠ΄Π½ΠΎΠΉ ΠΈΠ· ΡΠ΅Π»Π΅ΠΉ Π½Π΅ΠΏΡΠ΅ΡΡΠ²Π½ΠΎΠ³ΠΎ ΡΡΠΎΠ²Π΅ΡΡΠ΅Π½ΡΡΠ²ΠΎΠ²Π°Π½ΠΈΡ.
ΠΠ°ΡΠ΅ΡΠΈΠ°Π»ΡΠ½ΡΠ΅ Π·Π°ΠΏΠ°ΡΡ β ΡΡΠΎ Π½Π΅Π·Π°Π΄Π΅ΠΉΡΡΠ²ΠΎΠ²Π°Π½Π½ΡΠ΅ ΡΠ΅ΡΡΡΡΡ, ΠΊΠΎΡΠΎΡΡΠ΅ Π·Π°Π½ΠΈΠΌΠ°ΡΡ ΠΌΠ΅ΡΡΠΎ ΠΈ ΠΏΠΎΠ²ΡΡΠ°ΡΡ ΡΡΠΎΠΈΠΌΠΎΡΡΡ ΠΏΡΠΎΠΈΠ·Π²ΠΎΠ΄ΡΡΠ²Π°. ΠΡ ΡΠ»Π΅Π΄ΡΠ΅Ρ ΡΠ²Π΅ΡΡΠΈ ΠΊ ΠΌΠΈΠ½ΠΈΠΌΡΠΌΡ ΠΈΠ»ΠΈ ΠΏΠΎ Π²ΠΎΠ·ΠΌΠΎΠΆΠ½ΠΎΡΡΠΈ Π²ΠΎΠΎΠ±ΡΠ΅ ΡΡΡΡΠ°Π½ΠΈΡΡ.
ΠΠ΅ΠΎΠ±ΠΎΡΠ½ΠΎΠ²Π°Π½Π½ΡΠ΅ ΡΠ°ΡΡ ΠΎΠ΄Ρ ΠΏΡΠ΅Π΄ΡΡΠ°Π²Π»ΡΡΡ ΡΠΎΠ±ΠΎΠΉ Π½Π΅ΠΏΡΠΎΠΈΠ·Π²ΠΎΠ΄ΠΈΡΠ΅Π»ΡΠ½ΡΠ΅ ΡΠ΅ΡΡΡΡΡ; ΠΈΡ ΡΡΡΡΠ°Π½Π΅Π½ΠΈΠ΅ ΠΌΠΎΠΆΠ΅Ρ ΠΎΡΠ²ΠΎΠ±ΠΎΠ΄ΠΈΡΡ ΡΠ΅ΡΡΡΡΡ ΠΈ ΡΠ°ΡΡΠΈΡΠΈΡΡ ΠΏΡΠΎΠΈΠ·Π²ΠΎΠ΄ΡΡΠ²ΠΎ. Π ΡΠΈΠ»ΠΎΡΠΎΡΠΈΠΈ JIT Π½Π΅ΠΎΠ±ΠΎΡΠ½ΠΎΠ²Π°Π½Π½ΡΠ΅ ΡΠ°ΡΡ ΠΎΠ΄Ρ Π²ΠΊΠ»ΡΡΠ°ΡΡ:
- ΠΠ΅ΡΠ΅ΠΏΡΠΎΠΈΠ·Π²ΠΎΠ΄ΡΡΠ²ΠΎ
- ΠΡΠ΅ΠΌΡ ΠΎΠΆΠΈΠ΄Π°Π½ΠΈΡ
- ΠΠ΅Π½ΡΠΆΠ½ΡΠ΅ ΠΏΠ΅ΡΠ΅Π²ΠΎΠ·ΠΊΠΈ
- Π₯ΡΠ°Π½Π΅Π½ΠΈΠ΅ ΠΌΠ°ΡΠ΅ΡΠΈΠ°Π»ΡΠ½ΡΡ Π·Π°ΠΏΠ°ΡΠΎΠ²
- ΠΡΠ°ΠΊ ΠΈ ΠΎΡΡ ΠΎΠ΄Ρ
- ΠΠ΅ΡΡΡΠ΅ΠΊΡΠΈΠ²Π½ΡΠ΅ ΠΌΠ΅ΡΠΎΠ΄Ρ ΡΠ°Π±ΠΎΡΡ
- ΠΠ΅ΡΠ΅ΠΊΡΡ ΠΈΠ·Π΄Π΅Π»ΠΈΠΉ
Β
ΠΠ°Π»ΠΈΡΠΈΠ΅ ΠΏΠΎΠ΄ΠΎΠ±Π½ΡΡ Π½Π΅ΠΎΠ±ΠΎΡΠ½ΠΎΠ²Π°Π½Π½ΡΡ ΡΠ°ΡΡ ΠΎΠ΄ΠΎΠ² Π³ΠΎΠ²ΠΎΡΠΈΡ ΠΎ Π²ΠΎΠ·ΠΌΠΎΠΆΠ½ΠΎΡΡΠΈ ΡΡΠΎΠ²Π΅ΡΡΠ΅Π½ΡΡΠ²ΠΎΠ²Π°Π½ΠΈΡ ΠΈΠ»ΠΈ ΡΠΏΠΈΡΠΎΠΊ Π½Π΅ΠΎΠ±ΠΎΡΠ½ΠΎΠ²Π°Π½Π½ΡΡ ΡΠ°ΡΡ ΠΎΠ΄ΠΎΠ² ΠΎΠΏΡΠ΅Π΄Π΅Π»ΡΠ΅Ρ ΠΏΠΎΡΠ΅Π½ΡΠΈΠ°Π»ΡΠ½ΡΠ΅ ΡΠ΅Π»ΠΈ Π½Π΅ΠΏΡΠ΅ΡΡΠ²Π½ΠΎΠ³ΠΎ ΡΡΠΎΠ²Π΅ΡΡΠ΅Π½ΡΡΠ²ΠΎΠ²Π°Π½ΠΈΡ.
Β
ΠΡΠΎΠ΅ΠΊΡΠΈΡΠΎΠ²Π°Π½ΠΈΠ΅ ΠΈ ΠΏΡΠΎΠΈΠ·Π²ΠΎΠ΄ΡΡΠ²ΠΎ Π² ΡΠΈΡΡΠ΅ΠΌΠ΅ JIT ΠΏΡΠ΅Π΄ΡΡΠ°Π²Π»ΡΡΡ ΡΠΎΠ±ΠΎΠΉ ΠΎΡΠ½ΠΎΠ²Ρ Π΄Π»Ρ Π²ΡΠΏΠΎΠ»Π½Π΅Π½ΠΈΡ ΠΏΠ΅ΡΠ΅ΡΠΈΡΠ»Π΅Π½Π½ΡΡ Π²ΡΡΠ΅ ΡΠ΅Π»Π΅ΠΉ. ΠΡΠ° ΠΎΡΠ½ΠΎΠ²Π° ΡΠΎΡΡΠΎΠΈΡ ΠΈΠ· ΡΠ΅ΡΡΡΠ΅Ρ ΡΠΎΡΠΌΠΈΡΡΡΡΠΈΡ Π±Π»ΠΎΠΊΠΎΠ²:
- Π Π°Π·ΡΠ°Π±ΠΎΡΠΊΠ° ΠΈΠ·Π΄Π΅Π»ΠΈΡ.
- Π Π°Π·ΡΠ°Π±ΠΎΡΠΊΠ° ΠΏΡΠΎΡΠ΅ΡΡΠ°.
- ΠΠ°Π΄ΡΠΎΠ²ΡΠ΅/ΠΎΡΠ³Π°Π½ΠΈΠ·Π°ΡΠΈΠΎΠ½Π½ΡΠ΅ ΡΠ»Π΅ΠΌΠ΅Π½ΡΡ.
- ΠΠ»Π°Π½ΠΈΡΠΎΠ²Π°Π½ΠΈΠ΅ ΠΈ ΡΠΏΡΠ°Π²Π»Π΅Π½ΠΈΠ΅ ΠΏΡΠΎΠΈΠ·Π²ΠΎΠ΄ΡΡΠ²ΠΎΠΌ.
Β
Π‘ΠΊΠΎΡΠΎΡΡΡ ΠΈ ΠΏΡΠΎΡΡΠΎΡΠ° β Π΄Π²Π° ΠΎΠ±ΡΠΈΡ ΡΠ»Π΅ΠΌΠ΅Π½ΡΠ°, ΠΊΠΎΡΠΎΡΡΠ΅ ΠΏΡΠΎΡ ΠΎΠ΄ΡΡ ΡΠ΅ΡΠ΅Π· ΡΡΠΈ ΡΠΎΡΠΌΠΈΡΡΡΡΠΈΠ΅ Π±Π»ΠΎΠΊΠΈ.
Β
1. Π Π°Π·ΡΠ°Π±ΠΎΡΠΊΠ° ΠΈΠ·Π΄Π΅Π»ΠΈΡ
Π’ΡΠΈ ΡΠ»Π΅ΠΌΠ΅Π½ΡΠ° ΠΏΡΠΎΠ΅ΠΊΡΠ° ΠΈΠ·Π΄Π΅Π»ΠΈΡ ΡΠ²Π»ΡΡΡΡΡ ΠΊΠ»ΡΡΠ΅Π²ΡΠΌΠΈ Π΄Π»Ρ ΡΠΈΡΡΠ΅ΠΌΡ Β«ΡΠΎΡΠ½ΠΎ-Π²-ΡΡΠΎΠΊΒ»:
- Π‘ΡΠ°Π½Π΄Π°ΡΡΠ½ΡΠ΅ ΠΊΠΎΠΌΠΏΠ»Π΅ΠΊΡΡΡΡΠΈΠ΅
- ΠΠΎΠ΄ΡΠ»ΡΠ½ΠΎΠ΅ ΠΏΡΠΎΠ΅ΠΊΡΠΈΡΠΎΠ²Π°Π½ΠΈΠ΅
- ΠΠ°ΡΠ΅ΡΡΠ²ΠΎ
Β
ΠΠ΅ΡΠ²ΡΠ΅ Π΄Π²Π° ΡΠ»Π΅ΠΌΠ΅Π½ΡΠ° ΡΠ²ΡΠ·Π°Π½Ρ ΡΠΎ ΡΠΊΠΎΡΠΎΡΡΡΡ ΠΈ ΠΏΡΠΎΡΡΠΎΡΠΎΠΉ.
ΠΡΠΏΠΎΠ»ΡΠ·ΠΎΠ²Π°Π½ΠΈΠ΅ ΡΡΠ°Π½Π΄Π°ΡΡΠ½ΡΡ ΠΊΠΎΠΌΠΏΠ»Π΅ΠΊΡΡΡΡΠΈΡ ΠΎΠ·Π½Π°ΡΠ°Π΅Ρ, ΡΡΠΎ ΡΠ°Π±ΠΎΡΠΈΠ΅ ΠΈΠΌΠ΅ΡΡ Π΄Π΅Π»ΠΎ Ρ ΠΌΠ΅Π½ΡΡΠΈΠΌ ΠΊΠΎΠ»ΠΈΡΠ΅ΡΡΠ²ΠΎΠΌ Π΄Π΅ΡΠ°Π»Π΅ΠΉ, Π° ΡΡΠΎ ΡΠΎΠΊΡΠ°ΡΠ°Π΅Ρ Π²ΡΠ΅ΠΌΡ ΠΈ Π·Π°ΡΡΠ°ΡΡ Π½Π° ΠΎΠ±ΡΡΠ΅Π½ΠΈΠ΅. ΠΠ°ΠΊΡΠΏΠΊΠ°, ΠΎΠ±ΡΠ°Π±ΠΎΡΠΊΠ° ΠΈ ΠΏΡΠΎΠ²Π΅ΡΠΊΠ° ΠΊΠ°ΡΠ΅ΡΡΠ²Π° ΠΏΡΠΈ ΡΡΠΎΠΌ Π±ΠΎΠ»Π΅Π΅ ΡΡΠ°Π½Π΄Π°ΡΡΠ½Ρ ΠΈ Π΄Π°ΡΡ Π²ΠΎΠ·ΠΌΠΎΠΆΠ½ΠΎΡΡΡ Π½Π΅ΠΏΡΠ΅ΡΡΠ²Π½ΠΎΠ³ΠΎ ΡΡΠΎΠ²Π΅ΡΡΠ΅Π½ΡΡΠ²ΠΎΠ²Π°Π½ΠΈΡ. ΠΡΡΠ³ΠΎΠ΅ Π²Π°ΠΆΠ½ΠΎΠ΅ ΠΏΡΠ΅ΠΈΠΌΡΡΠ΅ΡΡΠ²ΠΎ Π·Π°ΠΊΠ»ΡΡΠ°Π΅ΡΡΡ Π² ΠΈΡΠΏΠΎΠ»ΡΠ·ΠΎΠ²Π°Π½ΠΈΠΈ ΡΡΠ°Π½Π΄Π°ΡΡΠ½ΠΎΠΉ ΠΏΡΠΎΡΠ΅Π΄ΡΡΡ ΠΎΠ±ΡΠ°Π±ΠΎΡΠΊΠΈ.
ΠΠΎΠ΄ΡΠ»ΡΠ½ΠΎΠ΅ ΠΏΡΠΎΠ΅ΠΊΡΠΈΡΠΎΠ²Π°Π½ΠΈΠ΅ β ΡΡΠΎ ΡΠ²ΠΎΠ΅Π³ΠΎ ΡΠΎΠ΄Π° ΡΠ°ΡΡΠΈΡΠ΅Π½ΠΈΠ΅ ΠΏΠΎΠ½ΡΡΠΈΡ ΡΡΠ°Π½Π΄Π°ΡΡΠ½ΡΡ ΠΊΠΎΠΌΠΏΠ»Π΅ΠΊΡΡΡΡΠΈΡ . ΠΠΎΠ΄ΡΠ»ΠΈ β Π³ΡΡΠΏΠΏΡ Π΄Π΅ΡΠ°Π»Π΅ΠΉ, ΡΠΎΠ±ΡΠ°Π½Π½ΡΠ΅ Π² Π΅Π΄ΠΈΠ½ΡΠΉ ΡΠ·Π΅Π» (ΠΈ ΠΏΡΠ΅Π΄ΡΡΠ°Π²Π»ΡΡΡΠΈΠ΅ ΡΠΎΠ±ΠΎΠΉ ΠΏΠΎΡΡΠΎΠΌΡ ΠΎΡΠ΄Π΅Π»ΡΠ½ΡΡ Π΅Π΄ΠΈΠ½ΠΈΡΡ). ΠΡΠΎ Π·Π½Π°ΡΠΈΡΠ΅Π»ΡΠ½ΠΎ ΡΠΎΠΊΡΠ°ΡΠ°Π΅Ρ ΡΠΈΡΠ»ΠΎ Π΄Π΅ΡΠ°Π»Π΅ΠΉ, Ρ ΠΊΠΎΡΠΎΡΡΠΌΠΈ ΠΏΡΠΈΡ ΠΎΠ΄ΠΈΡΡΡ ΡΠ°Π±ΠΎΡΠ°ΡΡ, ΡΠΏΡΠΎΡΠ°Π΅Ρ ΡΠ±ΠΎΡΠΊΡ, Π·Π°ΠΊΡΠΏΠΊΡ, ΠΎΠ±ΡΠ°Π±ΠΎΡΠΊΡ, ΠΎΠ±ΡΡΠ΅Π½ΠΈΠ΅, ΠΈ ΡΠ°ΠΊ Π΄Π°Π»Π΅Π΅. Π‘ΡΠ°Π½Π΄Π°ΡΡΠΈΠ·Π°ΡΠΈΡ ΠΈΠΌΠ΅Π΅Ρ Π΄ΠΎΠΏΠΎΠ»Π½ΠΈΡΠ΅Π»ΡΠ½ΡΡ ΠΏΠΎΠ»ΡΠ·Ρ, ΡΠΌΠ΅Π½ΡΡΠ°Ρ Π΄Π»ΠΈΠ½Ρ ΡΠΏΠΈΡΠΊΠ° ΠΌΠ°ΡΠ΅ΡΠΈΠ°Π»ΠΎΠ² Π΄Π»Ρ ΡΠ°Π·Π»ΠΈΡΠ½ΡΡ ΠΈΠ·Π΄Π΅Π»ΠΈΠΉ, Ρ.Π΅. ΡΠΏΡΠΎΡΠ°Ρ ΡΡΠΎΡ ΡΠΏΠΈΡΠΎΠΊ.
ΠΠ΅Π΄ΠΎΡΡΠ°ΡΠΊΠΈ ΡΡΠ°Π½Π΄Π°ΡΡΠΈΠ·Π°ΡΠΈΠΈ Π·Π°ΠΊΠ»ΡΡΠ°ΡΡΡΡ Π² ΡΠΎΠΌ, ΡΡΠΎ ΠΈΠ·Π΄Π΅Π»ΠΈΡ ΠΌΠ΅Π½Π΅Π΅ ΡΠ°Π·Π½ΠΎΠΎΠ±ΡΠ°Π·Π½Ρ ΠΈ ΡΠΎΠΏΡΠΎΡΠΈΠ²Π»ΡΡΡΡΡ ΠΈΠ·ΠΌΠ΅Π½Π΅Π½ΠΈΡΠΌ ΡΠ²ΠΎΠΈΡ ΡΡΠ°Π½Π΄Π°ΡΡΠ½ΡΡ ΠΏΡΠΎΠ΅ΠΊΡΠΎΠ². ΠΡΠΈ Π½Π΅ΡΠ΄ΠΎΠ±ΡΡΠ²Π° Π½Π΅ΡΠΊΠΎΠ»ΡΠΊΠΎ ΡΠΌΠ΅Π½ΡΡΠ°ΡΡΡΡ ΡΠ°ΠΌ, Π³Π΄Π΅ ΡΠ°Π·Π»ΠΈΡΠ½ΡΠ΅ ΠΈΠ·Π΄Π΅Π»ΠΈΡ ΠΈΠΌΠ΅ΡΡ ΠΎΠ±ΡΠΈΠ΅ ΡΠ°ΡΡΠΈ ΠΈΠ»ΠΈ ΠΌΠΎΠ΄ΡΠ»ΠΈ. Π‘ΡΡΠ΅ΡΡΠ²ΡΠ΅Ρ ΡΠ°ΠΊΡΠΈΠΊΠ°, ΠΊΠΎΡΠΎΡΡΡ ΠΈΠ½ΠΎΠ³Π΄Π° Π½Π°Π·ΡΠ²Π°ΡΡ Β«ΠΎΡΡΡΠΎΡΠ΅Π½Π½Π°Ρ Π΄ΠΈΡΡΠ΅ΡΠ΅Π½ΡΠΈΠ°ΡΠΈΡΒ»: ΡΠ΅ΡΠ΅Π½ΠΈΡ ΠΎΡΠ½ΠΎΡΠΈΡΠ΅Π»ΡΠ½ΠΎ ΡΠΎΠ³ΠΎ, ΠΊΠ°ΠΊΠΈΠ΅ ΠΈΠΌΠ΅Π½Π½ΠΎ ΠΈΠ·Π΄Π΅Π»ΠΈΡ Π±ΡΠ΄ΡΡ Π·Π°ΠΏΡΡΠ΅Π½Ρ Π² ΠΏΡΠΎΠΈΠ·Π²ΠΎΠ΄ΡΡΠ²ΠΎ, ΠΎΡΠΊΠ»Π°Π΄ΡΠ²Π°ΡΡΡΡ Π½Π° ΡΠΎ Π²ΡΠ΅ΠΌΡ, ΠΏΠΎΠΊΠ° ΠΏΡΠΎΠΈΠ·Π²ΠΎΠ΄ΡΡΡΡ ΡΡΠ°Π½Π΄Π°ΡΡΠ½ΡΠ΅ Π΄Π΅ΡΠ°Π»ΠΈ.
ΠΠΎΠ³Π΄Π° ΡΡΠ°Π½ΠΎΠ²ΠΈΡΡΡ ΠΎΡΠ΅Π²ΠΈΠ΄Π½ΡΠΌ, ΠΊΠ°ΠΊΠΈΠ΅ ΠΈΠΌΠ΅Π½Π½ΠΎ ΠΈΠ·Π΄Π΅Π»ΠΈΡ Π½Π΅ΠΎΠ±Ρ ΠΎΠ΄ΠΈΠΌΡ, ΡΠΈΡΡΠ΅ΠΌΠ° Π±ΡΡΡΡΠΎ ΡΠ΅Π°Π³ΠΈΡΡΠ΅Ρ, ΠΏΡΠΎΠΈΠ·Π²ΠΎΠ΄Ρ ΠΎΡΡΠ°Π²ΡΠΈΠ΅ΡΡ Π½Π΅ΡΡΠ°Π½Π΄Π°ΡΡΠ½ΡΠ΅ Π΄Π΅ΡΠ°Π»ΠΈ ΡΡΠΈΡ ΠΈΠ·Π΄Π΅Π»ΠΈΠΉ. ΠΠ°ΡΠ΅ΡΡΠ²ΠΎ β ΡΡΠΎ ΠΎΡΠ½ΠΎΠ²Π½ΠΎΠ΅ Π½Π΅ΠΎΠ±Ρ ΠΎΠ΄ΠΈΠΌΠΎΠ΅ ΡΡΠ»ΠΎΠ²ΠΈΠ΅ ΡΠΈΡΡΠ΅ΠΌΡ Β«ΡΠΎΡΠ½ΠΎ-Π²-ΡΡΠΎΠΊΒ». ΠΠ½ΠΎ ΠΆΠΈΠ·Π½Π΅Π½Π½ΠΎ Π²Π°ΠΆΠ½ΠΎ Π΄Π»Ρ ΡΠΈΡΡΠ΅ΠΌ JIT, ΠΏΠΎΡΠΊΠΎΠ»ΡΠΊΡ Π½ΠΈΠ·ΠΊΠΎΠ΅ ΠΊΠ°ΡΠ΅ΡΡΠ²ΠΎ ΠΌΠΎΠΆΠ΅Ρ Π²ΡΠ·Π²Π°ΡΡ ΡΠ΅ΡΡΠ΅Π·Π½ΡΠ΅ ΡΡΡΠ²Ρ Π² ΠΏΡΠΎΡΠ΅ΡΡΠ΅ ΠΏΡΠΎΠΈΠ·Π²ΠΎΠ΄ΡΡΠ²Π°. Π‘ΠΈΡΡΠ΅ΠΌΠ° Π½Π°ΡΠ΅Π»Π΅Π½Π° Π½Π° ΠΏΠ»Π°Π²Π½ΡΠΉ ΠΏΠΎΡΠΎΠΊ ΡΠ°Π±ΠΎΡΡ; ΠΏΠΎΡΠ²Π»Π΅Π½ΠΈΠ΅ ΠΏΡΠΎΠ±Π»Π΅ΠΌ ΠΈΠ·-Π·Π° Π½ΠΈΠ·ΠΊΠΎΠ³ΠΎ ΠΊΠ°ΡΠ΅ΡΡΠ²Π° Π²ΡΠ·ΡΠ²Π°Π΅Ρ ΡΠ±ΠΎΠΈ Π² ΡΡΠΎΠΌ ΠΏΠΎΡΠΎΠΊΠ΅.
ΠΠΎΡΠΊΠΎΠ»ΡΠΊΡ Π½Π΅Π±ΠΎΠ»ΡΡΠΈΠ΅ ΡΠ°Π·ΠΌΠ΅ΡΡ ΠΏΡΠΎΠΈΠ·Π²ΠΎΠ΄ΡΡΠ²Π΅Π½Π½ΠΎΠΉ ΠΏΠ°ΡΡΠΈΠΈ ΠΈ ΠΎΡΡΡΡΡΡΠ²ΠΈΠ΅ ΡΠ΅Π·Π΅ΡΠ²Π½ΡΡ Π·Π°ΠΏΠ°ΡΠΎΠ² Π΄Π°ΡΡ Π² ΡΠ΅Π·ΡΠ»ΡΡΠ°ΡΠ΅ ΠΌΠΈΠ½ΠΈΠΌΠ°Π»ΡΠ½ΡΠΉ ΠΎΠ±ΡΠ΅ΠΌ Π½Π΅Π·Π°Π²Π΅ΡΡΠ΅Π½Π½ΠΎΠ³ΠΎ ΠΏΡΠΎΠΈΠ·Π²ΠΎΠ΄ΡΡΠ²Π°, ΠΏΡΠΎΠΈΠ·Π²ΠΎΠ΄ΡΡΠ²Π΅Π½Π½ΡΠΉ ΠΏΡΠΎΡΠ΅ΡΡ Π²ΡΠ½ΡΠΆΠ΄Π΅Π½ ΠΎΡΡΠ°Π½Π°Π²Π»ΠΈΠ²Π°ΡΡΡΡ, ΠΊΠΎΠ³Π΄Π° Π²ΠΎΠ·Π½ΠΈΠΊΠ°Π΅Ρ ΠΏΡΠΎΠ±Π»Π΅ΠΌΠ°. ΠΡΠΈ ΡΡΠΎΠΌ ΠΎΠ½ Π½Π΅ ΠΌΠΎΠΆΠ΅Ρ Π²ΠΎΠ·ΠΎΠ±Π½ΠΎΠ²ΠΈΡΡΡΡ Π΄ΠΎ ΡΠ΅Ρ ΠΏΠΎΡ, ΠΏΠΎΠΊΠ° ΠΏΡΠΎΠ±Π»Π΅ΠΌΠ° Π½Π΅ Π±ΡΠ΄Π΅Ρ ΡΠ΅ΡΠ΅Π½Π°. Π‘ΠΎΠ²Π΅ΡΡΠ΅Π½Π½ΠΎ ΠΎΡΠ΅Π²ΠΈΠ΄Π½ΠΎ, ΡΡΠΎ ΠΎΡΡΠ°Π½ΠΎΠ²ΠΊΠ° Π²ΡΠ΅Π³ΠΎ ΠΏΡΠΎΡΠ΅ΡΡΠ° ΠΎΠ±Ρ ΠΎΠ΄ΠΈΡΡΡ ΠΎΡΠ΅Π½Ρ Π΄ΠΎΡΠΎΠ³ΠΎ ΠΈ ΡΠ½ΠΈΠΆΠ°Π΅Ρ ΠΏΠ»Π°Π½ΠΎΠ²ΡΠΉ ΡΡΠΎΠ²Π΅Π½Ρ Π²ΡΠΏΡΡΠΊΠ°, ΠΏΠΎΡΡΠΎΠΌΡ Π°Π±ΡΠΎΠ»ΡΡΠ½ΠΎ Π½Π΅ΠΎΠ±Ρ ΠΎΠ΄ΠΈΠΌΠΎ ΠΏΠΎ Π²ΠΎΠ·ΠΌΠΎΠΆΠ½ΠΎΡΡΠΈ ΠΈΠ·Π±Π΅Π³Π°ΡΡ ΠΎΡΡΠ°Π½ΠΎΠ²ΠΊΠΈ ΡΠΈΡΡΠ΅ΠΌΡ ΠΈ Π±ΡΡΡΡΠΎ ΡΠ΅ΡΠ°ΡΡ ΠΏΡΠΎΠ±Π»Π΅ΠΌΡ Π² ΡΠ»ΡΡΠ°Π΅ ΠΈΡ ΠΏΠΎΡΠ²Π»Π΅Π½ΠΈΡ.
Π‘ΠΈΡΡΠ΅ΠΌΡ JIT ΠΈΡΠΏΠΎΠ»ΡΠ·ΡΡΡ ΡΡΠ΅Ρ ΡΡΠ°ΠΏΠ½ΡΠΉ ΠΏΠΎΠ΄Ρ ΠΎΠ΄ ΠΊ ΠΊΠ°ΡΠ΅ΡΡΠ²Ρ. ΠΠ΅ΡΠ²Π°Ρ ΡΠ°ΡΡΡ β Π²Π½Π΅Π΄ΡΠΈΡΡ ΠΊΠ°ΡΠ΅ΡΡΠ²ΠΎ Π² ΠΈΠ·Π΄Π΅Π»ΠΈΠ΅ ΠΈ Π² ΠΏΡΠΎΠΈΠ·Π²ΠΎΠ΄ΡΡΠ²Π΅Π½Π½ΡΠΉ ΠΏΡΠΎΡΠ΅ΡΡ. ΠΡΡΠΎΠΊΠΈΠΉ ΡΡΠΎΠ²Π΅Π½Ρ ΠΊΠ°ΡΠ΅ΡΡΠ²Π° Π΄ΠΎΡΡΠΈΠΆΠΈΠΌ ΠΏΠΎΡΠΎΠΌΡ, ΡΡΠΎ Β«ΡΠΎΡΠ½ΠΎΡΡΠΎΡΠ½ΡΠ΅Β» ΡΠΈΡΡΠ΅ΠΌΡ ΠΏΡΠΎΠΈΠ·Π²ΠΎΠ΄ΡΡ ΡΡΠ°Π½Π΄Π°ΡΡΠ½ΡΠ΅ ΠΈΠ·Π΄Π΅Π»ΠΈΡ, Ρ ΠΈΡΠΏΠΎΠ»ΡΠ·ΠΎΠ²Π°Π½ΠΈΠ΅ΠΌ ΡΠΎΠΎΡΠ²Π΅ΡΡΡΠ²Π΅Π½Π½ΠΎ ΡΡΠ°Π½Π΄Π°ΡΡΠ½ΡΡ ΠΌΠ΅ΡΠΎΠ΄ΠΎΠ² ΡΠ°Π±ΠΎΡΡ ΠΈ ΡΡΠ°Π½Π΄Π°ΡΡΠ½ΠΎΠ³ΠΎ ΠΎΠ±ΠΎΡΡΠ΄ΠΎΠ²Π°Π½ΠΈΡ, ΡΠ°Π±ΠΎΡΠΈΠ΅ ΠΏΡΠΈΠ²ΡΠΊΠ»ΠΈ ΠΊ ΡΠ²ΠΎΠΈΠΌ ΠΏΡΠΎΠΈΠ·Π²ΠΎΠ΄ΡΡΠ²Π΅Π½Π½ΡΠΌ ΠΎΠΏΠ΅ΡΠ°ΡΠΈΡΠΌ ΠΈ Ρ ΠΎΡΠΎΡΠΎ ΠΈΡ Π·Π½Π°ΡΡ.
ΠΡΠΎΠΌΠ΅ ΡΠΎΠ³ΠΎ, Π²ΡΠ΅ ΡΠ°ΡΡ ΠΎΠ΄Ρ Π½Π° ΠΊΠ°ΡΠ΅ΡΡΠ²ΠΎ ΠΏΡΠΎΠ΅ΠΊΡΠ° (Ρ.Π΅. ΡΠΎΡΠΌΠΈΡΠΎΠ²Π°Π½ΠΈΠ΅ ΠΊΠ°ΡΠ΅ΡΡΠ²Π° ΠΈΠ·Π΄Π΅Π»ΠΈΡ Π΅ΡΠ΅ Π½Π° ΡΡΠ°Π΄ΠΈΠΈ ΠΏΡΠΎΠ΅ΠΊΡΠ°) ΠΌΠΎΠΆΠ½ΠΎ ΡΠ°ΡΠΏΡΠ΅Π΄Π΅Π»ΠΈΡΡ Π½Π° ΠΌΠ½ΠΎΠ³ΠΈΠ΅ ΠΈΠ·Π΄Π΅Π»ΠΈΡ, ΠΏΠΎΠ»ΡΡΠ°Ρ ΠΏΡΠΈ ΡΡΠΎΠΌ Π½Π΅Π±ΠΎΠ»ΡΡΡΡ ΡΡΠΎΠΈΠΌΠΎΡΡΡ Π΅Π΄ΠΈΠ½ΠΈΡΡ ΠΈΠ·Π΄Π΅Π»ΠΈΡ. ΠΡΠ΅Π½Ρ Π²Π°ΠΆΠ½ΠΎ Π²ΡΠ±ΡΠ°ΡΡ ΡΠΎΠΎΡΠ²Π΅ΡΡΡΠ²ΡΡΡΠΈΠΉ ΡΡΠΎΠ²Π΅Π½Ρ ΠΊΠ°ΡΠ΅ΡΡΠ²Π° Ρ ΡΠΎΡΠΊΠΈ Π·ΡΠ΅Π½ΠΈΡ ΠΊΠΎΠ½Π΅ΡΠ½ΠΎΠ³ΠΎ ΠΏΠΎΡΡΠ΅Π±ΠΈΡΠ΅Π»Ρ ΠΈ Π²ΠΎΠ·ΠΌΠΎΠΆΠ½ΠΎΡΡΠ΅ΠΉ ΠΏΡΠΎΠΈΠ·Π²ΠΎΠ΄ΡΡΠ²Π°. Π’Π°ΠΊΠΈΠΌ ΠΎΠ±ΡΠ°Π·ΠΎΠΌ, ΠΏΡΠΎΠ΅ΠΊΡΠΈΡΠΎΠ²Π°Π½ΠΈΠ΅ ΠΈΠ·Π΄Π΅Π»ΠΈΡ ΠΈ ΡΠ°Π·ΡΠ°Π±ΠΎΡΠΊΠ° ΠΏΡΠΎΡΠ΅ΡΡΠ° Π΄ΠΎΠ»ΠΆΠ½Ρ ΠΈΠ΄ΡΠΈ ΡΡΠΊΠ° ΠΎΠ± ΡΡΠΊΡ.
Β
2. Π Π°Π·ΡΠ°Π±ΠΎΡΠΊΠ° ΠΏΡΠΎΡΠ΅ΡΡΠ°
ΠΠ»Ρ Β«ΡΠΎΡΠ½ΠΎΡΡΠΎΡΠ½ΡΡ Β» ΡΠΈΡΡΠ΅ΠΌ ΠΎΡΠΎΠ±ΠΎ Π²Π°ΠΆΠ½Ρ ΡΠ΅ΠΌΡ Π°ΡΠΏΠ΅ΠΊΡΠΎΠ² ΡΠ°Π·ΡΠ°Π±ΠΎΡΠΊΠΈ ΠΈΠ·Π΄Π΅Π»ΠΈΡ:
- ΠΡΠΎΠΈΠ·Π²ΠΎΠ΄ΡΡΠ²Π΅Π½Π½ΡΠ΅ ΠΏΠ°ΡΡΠΈΠΈ Π½Π΅Π±ΠΎΠ»ΡΡΠΎΠ³ΠΎ ΠΎΠ±ΡΠ΅ΠΌΠ°
- Π‘ΠΎΠΊΡΠ°ΡΠ΅Π½ΠΈΠ΅ Π²ΡΠ΅ΠΌΠ΅Π½ΠΈ ΠΏΠΎΠ΄Π³ΠΎΡΠΎΠ²ΠΊΠΈ ΠΊ ΠΏΡΠΎΠΈΠ·Π²ΠΎΠ΄ΡΡΠ²Ρ
- ΠΡΠΎΠΈΠ·Π²ΠΎΠ΄ΡΡΠ²Π΅Π½Π½ΡΠ΅ ΡΡΠ΅ΠΉΠΊΠΈ
- ΠΠ³ΡΠ°Π½ΠΈΡΠ΅Π½ΠΈΠ΅ ΠΎΠ±ΡΠ΅ΠΌΠ° Π½Π΅Π·Π°Π²Π΅ΡΡΠ΅Π½Π½ΠΎΠ³ΠΎ ΠΏΡΠΎΠΈΠ·Π²ΠΎΠ΄ΡΡΠ²Π°
- ΠΠΎΠ²ΡΡΠ΅Π½ΠΈΠ΅ ΠΊΠ°ΡΠ΅ΡΡΠ²Π°
- ΠΠΈΠ±ΠΊΠΎΡΡΡ ΠΏΡΠΎΠΈΠ·Π²ΠΎΠ΄ΡΡΠ²Π°
- ΠΠ΅Π±ΠΎΠ»ΡΡΠΈΠ΅ ΠΌΠ°ΡΠ΅ΡΠΈΠ°Π»ΡΠ½ΠΎ-ΠΏΡΠΎΠΈΠ·Π²ΠΎΠ΄ΡΡΠ²Π΅Π½Π½ΡΠ΅ Π·Π°ΠΏΠ°ΡΡ
Β
ΠΠ΅Π±ΠΎΠ»ΡΡΠΎΠΉ ΠΎΠ±ΡΠ΅ΠΌ ΠΏΡΠΎΠΈΠ·Π²ΠΎΠ΄ΡΡΠ²Π΅Π½Π½ΠΎΠΉ ΠΏΠ°ΡΡΠΈΠΈ ΠΈ Π·Π°ΠΊΡΠΏΠΎΡΠ½ΠΎΠΉ ΠΏΠ°ΡΡΠΈΠΈ Π΄Π°Π΅Ρ ΡΡΠ΄ ΠΏΡΠ΅ΠΈΠΌΡΡΠ΅ΡΡΠ², ΠΊΠΎΡΠΎΡΡΠ΅ ΠΏΠΎΠ·Π²ΠΎΠ»ΡΡΡ ΡΠΈΡΡΠ΅ΠΌΠ°ΠΌ JIT ΡΡΡΠ΅ΠΊΡΠΈΠ²Π½ΠΎ ΡΡΠ½ΠΊΡΠΈΠΎΠ½ΠΈΡΠΎΠ²Π°ΡΡ. ΠΠΎ-ΠΏΠ΅ΡΠ²ΡΡ , ΠΊΠΎΠ³Π΄Π° ΡΠ΅ΡΠ΅Π· ΡΠΈΡΡΠ΅ΠΌΡ ΠΏΠ΅ΡΠ΅ΠΌΠ΅ΡΠ°ΡΡΡΡ Π½Π΅Π±ΠΎΠ»ΡΡΠΈΠ΅ ΠΏΡΠΎΠΈΠ·Π²ΠΎΠ΄ΡΡΠ²Π΅Π½Π½ΡΠ΅ ΠΏΠ°ΡΡΠΈΠΈ, ΡΠΎ ΠΈ ΠΎΠ±ΡΠ΅ΠΌ Π½Π΅Π·Π°Π²Π΅ΡΡΠ΅Π½Π½ΠΎΠ³ΠΎ ΠΏΡΠΎΠΈΠ·Π²ΠΎΠ΄ΡΡΠ²Π° (Ρ.Π΅. ΠΌΠ°ΡΠ΅ΡΠΈΠ°Π»ΠΎΠ², Π½Π°Ρ ΠΎΠ΄ΡΡΠΈΡ ΡΡ Π² ΠΏΡΠΎΡΠ΅ΡΡΠ΅ ΠΎΠ±ΡΠ°Π±ΠΎΡΠΊΠΈ) Π·Π½Π°ΡΠΈΡΠ΅Π»ΡΠ½ΠΎ ΠΌΠ΅Π½ΡΡΠ΅, ΡΠ΅ΠΌ ΠΏΡΠΈ ΠΊΡΡΠΏΠ½ΡΡ ΠΏΠ°ΡΡΠΈΡΡ .
ΠΡΠΎ ΡΠΌΠ΅Π½ΡΡΠ°Π΅Ρ ΡΡΠΎΠΈΠΌΠΎΡΡΡ Ρ ΡΠ°Π½Π΅Π½ΠΈΡ, ΡΡΠ΅Π±ΡΠ΅Ρ ΠΌΠ΅Π½ΡΡΠ΅Π³ΠΎ ΠΌΠ΅ΡΡΠ° Π΄Π»Ρ Ρ ΡΠ°Π½Π΅Π½ΠΈΡ, ΠΈ Π½Π΅ ΡΠΎΠ·Π΄Π°Π΅Ρ ΠΈΠ·Π»ΠΈΡΠ½Π΅ΠΉ Π·Π°Π³ΡΡΠΆΠ΅Π½Π½ΠΎΡΡΠΈ ΠΏΡΠΎΡΡΡΠ°Π½ΡΡΠ²Π° Π½Π° ΡΠ°Π±ΠΎΡΠ΅ΠΌ ΠΌΠ΅ΡΡΠ΅. ΠΠΎ-Π²ΡΠΎΡΡΡ , ΠΊΠΎΠ³Π΄Π° Π²ΠΎΠ·Π½ΠΈΠΊΠ°ΡΡ ΠΏΡΠΎΠ±Π»Π΅ΠΌΡ Ρ ΠΊΠ°ΡΠ΅ΡΡΠ²ΠΎΠΌ, Π·Π°ΡΡΠ°ΡΡ Π½Π° ΠΏΡΠΎΠ²Π΅ΡΠΊΡ ΠΈ ΠΏΠ΅ΡΠ΅Π΄Π΅Π»ΠΊΡ ΠΌΠ΅Π½ΡΡΠ΅, ΠΏΠΎΡΠΊΠΎΠ»ΡΠΊΡ Π² ΠΊΠ°ΠΆΠ΄ΠΎΠΉ ΠΏΠ°ΡΡΠΈΠΈ ΠΌΠ΅Π½ΡΡΠ΅ Π΅Π΄ΠΈΠ½ΠΈΡ, ΡΡΠ΅Π±ΡΡΡΠΈΡ ΠΏΡΠΎΠ²Π΅ΡΠΊΠΈ ΠΈ ΠΏΠ΅ΡΠ΅ΡΠ°Π±ΠΎΡΠΊΠΈ. ΠΡΠΎΠΌΠ΅ ΡΠΎΠ³ΠΎ, Π½Π΅Π±ΠΎΠ»ΡΡΠΈΠ΅ ΠΏΠ°ΡΡΠΈΠΈ ΠΎΠ±Π΅ΡΠΏΠ΅ΡΠΈΠ²Π°ΡΡ Π±ΠΎΠ»ΡΡΡΡ Π³ΠΈΠ±ΠΊΠΎΡΡΡ ΠΏΡΠΈ ΠΏΠ»Π°Π½ΠΈΡΠΎΠ²Π°Π½ΠΈΠΈ.
ΠΠ΅Π±ΠΎΠ»ΡΡΠΎΠΉ ΠΎΠ±ΡΠ΅ΠΌ ΠΏΡΠΎΠΈΠ·Π²ΠΎΠ΄ΡΡΠ²Π΅Π½Π½ΠΎΠΉ ΠΏΠ°ΡΡΠΈΠΈ ΠΈ ΠΌΠ΅Π½ΡΡΡΠΈΠΉΡΡ Π°ΡΡΠΎΡΡΠΈΠΌΠ΅Π½Ρ ΠΈΠ·Π΄Π΅Π»ΠΈΠΉ ΡΡΠ΅Π±ΡΡΡ ΡΠ°ΡΡΡΡ ΠΏΠ΅ΡΠ΅ΠΎΡΠ½Π°ΡΠ΅Π½ΠΈΠΉ ΠΈ ΠΏΠ΅ΡΠ΅Π½Π°Π»Π°Π΄ΠΊΠΈ ΠΎΠ±ΠΎΡΡΠ΄ΠΎΠ²Π°Π½ΠΈΡ (Ρ.Π΅. ΠΏΠΎΠ΄Π³ΠΎΡΠΎΠ²ΠΊΠΈ ΠΊ ΠΏΡΠΎΠΈΠ·Π²ΠΎΠ΄ΡΡΠ²Ρ). ΠΡΠ»ΠΈ ΡΠ°ΠΊΡΡ ΠΏΠΎΠ΄Π³ΠΎΡΠΎΠ²ΠΊΡ Π½Π΅Π²ΠΎΠ·ΠΌΠΎΠΆΠ½ΠΎ ΠΏΡΠΎΠΈΠ·Π²Π΅ΡΡΠΈ Π±ΡΡΡΡΠΎ ΠΈ ΠΎΡΠ½ΠΎΡΠΈΡΠ΅Π»ΡΠ½ΠΎ Π½Π΅Π΄ΠΎΡΠΎΠ³ΠΎ, Π²ΡΠ΅ΠΌΡ ΠΈ Π·Π°ΡΡΠ°ΡΡ ΡΡΠ°Π½ΡΡ ΡΠΎΡΠΌΠΎΠ·ΡΡΠΈΠΌΠΈ ΡΠ°ΠΊΡΠΎΡΠ°ΠΌΠΈ. Π§Π°ΡΡΠΎ ΡΠ°Π±ΠΎΡΠΈΡ ΠΎΠ±ΡΡΠ°ΡΡ ΡΠ°ΠΌΠΈΠΌ ΠΏΡΠΎΠ²ΠΎΠ΄ΠΈΡΡ ΠΏΠΎΠ΄Π³ΠΎΡΠΎΠ²ΠΊΡ ΡΠ²ΠΎΠ΅Π³ΠΎ ΠΎΠ±ΠΎΡΡΠ΄ΠΎΠ²Π°Π½ΠΈΡ ΠΊ ΠΏΡΠΎΠΈΠ·Π²ΠΎΠ΄ΡΡΠ²Π΅Π½Π½ΠΎΠΌΡ ΠΏΡΠΎΡΠ΅ΡΡΡ ΠΡΠΎΠΌΠ΅ ΡΠΎΠ³ΠΎ, ΠΈΡΠΏΠΎΠ»ΡΠ·ΡΡΡΡΡ ΡΠΏΠ΅ΡΠΈΠ°Π»ΡΠ½ΡΠ΅ ΠΏΡΠΎΠ³ΡΠ°ΠΌΠΌΡ ΠΏΠΎ ΡΠΎΠΊΡΠ°ΡΠ΅Π½ΠΈΡ ΡΡΠΎΠΊΠΎΠ² ΠΈ ΡΠ°ΡΡ ΠΎΠ΄ΠΎΠ² Π½Π° ΠΏΠΎΠ΄Π³ΠΎΡΠΎΠ²ΠΊΡ ΠΊ ΠΏΡΠΎΠΈΠ·Π²ΠΎΠ΄ΡΡΠ²Ρ; ΠΏΡΠΈ ΡΡΠΎΠΌ ΡΠ°Π±ΠΎΡΠΈΠ΅ ΡΡΠ°Π½ΠΎΠ²ΡΡΡΡ ΡΠ΅Π½Π½ΠΎΠΉ ΡΠ°ΡΡΡΡ ΠΏΡΠΎΡΠ΅ΡΡΠ°.
ΠΡΠΎΠΌΠ΅ ΡΠΎΠ³ΠΎ, Π΄Π»Ρ ΡΠΎΠΊΡΠ°ΡΠ΅Π½ΠΈΡ Π²ΡΠ΅ΠΌΠ΅Π½ΠΈ ΠΈ ΡΡΠΎΠΈΠΌΠΎΡΡΠΈ ΠΏΠΎΠ΄Π³ΠΎΡΠΎΠ²ΠΊΠΈ ΠΌΠΎΠΆΠ½ΠΎ ΠΈΡΠΏΠΎΠ»ΡΠ·ΠΎΠ²Π°ΡΡ Π³ΡΡΠΏΠΏΠΈΡΠΎΠ²ΠΊΡ ΡΠ΅Ρ Π½ΠΎΠ»ΠΎΠ³ΠΈΠΉ β ΠΎΠ±ΡΠ΅Π΄ΠΈΠ½Π΅Π½ΠΈΠ΅ ΡΡ ΠΎΠ΄Π½ΡΡ ΠΎΠΏΠ΅ΡΠ°ΡΠΈΠΉ. ΠΠ°ΠΏΡΠΈΠΌΠ΅Ρ, ΠΏΡΠΎΠΈΠ·Π²ΠΎΠ΄ΡΡΠ²ΠΎ ΡΠ°Π·Π»ΠΈΡΠ½ΡΡ Π΄Π΅ΡΠ°Π»Π΅ΠΉ, ΠΊΠΎΡΠΎΡΡΠ΅ ΡΡ ΠΎΠ΄Π½Ρ ΠΏΠΎ ΡΠΎΡΠΌΠ΅, ΠΌΠ°ΡΠ΅ΡΠΈΠ°Π»Ρ ΠΈ Ρ.ΠΏ., ΠΌΠΎΠΆΠ΅Ρ ΠΏΠΎΡΡΠ΅Π±ΠΎΠ²Π°ΡΡ ΠΎΠ΄Π½ΠΎΡΠΈΠΏΠ½ΠΎΠΉ (ΡΡ ΠΎΠΆΠ΅ΠΉ) ΠΏΠΎΠ΄Π³ΠΎΡΠΎΠ²ΠΊΠΈ. ΠΡ ΠΏΠΎΡΠ»Π΅Π΄ΠΎΠ²Π°ΡΠ΅Π»ΡΠ½Π°Ρ ΠΎΠ±ΡΠ°Π±ΠΎΡΠΊΠ° Π½Π° ΠΎΠ΄Π½ΠΎΠΌ ΠΈ ΡΠΎΠΌ ΠΆΠ΅ ΠΎΠ±ΠΎΡΡΠ΄ΠΎΠ²Π°Π½ΠΈΠΈ ΠΌΠΎΠΆΠ΅Ρ ΡΠΎΠΊΡΠ°ΡΠΈΡΡ Π½Π΅ΠΎΠ±Ρ ΠΎΠ΄ΠΈΠΌΡΠ΅ ΠΈΠ·ΠΌΠ΅Π½Π΅Π½ΠΈΡ; ΠΏΠΎΡΡΠ΅Π±ΡΠ΅ΡΡΡ ΡΠΎΠ»ΡΠΊΠΎ Π½Π΅Π·Π½Π°ΡΠΈΡΠ΅Π»ΡΠ½Π°Ρ ΡΠ΅Π³ΡΠ»ΠΈΡΠΎΠ²ΠΊΠ°.
ΠΠ±ΡΠ°Ρ ΡΠ΅ΡΡΠ° Β«ΡΠΎΡΠ½ΠΎΡΡΠΎΡΠ½ΡΡ Β» ΡΠΈΡΡΠ΅ΠΌ β ΠΌΠ½ΠΎΠΆΠ΅ΡΡΠ²ΠΎ ΠΏΡΠΎΠΈΠ·Π²ΠΎΠ΄ΡΡΠ²Π΅Π½Π½ΡΡ ΡΡΠ΅Π΅ΠΊ. ΠΠ½ΠΈ ΠΎΠ±ΡΠ΅Π΄ΠΈΠ½ΡΡΡ ΠΎΠ±ΠΎΡΡΠ΄ΠΎΠ²Π°Π½ΠΈΠ΅ ΠΈ ΠΈΠ½ΡΡΡΡΠΌΠ΅Π½ΡΡ Π΄Π»Ρ ΠΎΠ±ΡΠ°Π±ΠΎΡΠΊΠΈ Π³ΡΡΠΏΠΏΡ Π΄Π΅ΡΠ°Π»Π΅ΠΉ ΡΠΎ ΡΡ ΠΎΠ΄Π½ΡΠΌΠΈ ΡΠ΅Ρ Π½ΠΎΠ»ΠΎΠ³ΠΈΡΠ΅ΡΠΊΠΈΠΌΠΈ ΡΡΠ΅Π±ΠΎΠ²Π°Π½ΠΈΡΠΌΠΈ. ΠΠΎ ΡΠ²ΠΎΠ΅ΠΉ ΡΡΡΠΈ, ΡΡΠ΅ΠΉΠΊΠΈ β ΡΡΠΎ Π²ΡΡΠΎΠΊΠΎΡΠΏΠ΅ΡΠΈΠ°Π»ΠΈΠ·ΠΈΡΠΎΠ²Π°Π½Π½ΡΠ΅ ΠΈ ΡΡΡΠ΅ΠΊΡΠΈΠ²Π½ΡΠ΅ ΠΏΡΠΎΠΈΠ·Π²ΠΎΠ΄ΡΡΠ²Π΅Π½Π½ΡΠ΅ ΡΠ΅Π½ΡΡΡ. Π‘ΡΠ΅Π΄ΠΈ Π²Π°ΠΆΠ½Π΅ΠΉΡΠΈΡ ΠΏΡΠ΅ΠΈΠΌΡΡΠ΅ΡΡΠ² ΠΏΡΠΎΠΈΠ·Π²ΠΎΠ΄ΡΡΠ²Π΅Π½Π½ΡΡ ΡΡΠ΅Π΅ΠΊ: ΡΠΎΠΊΡΠ°ΡΠ°Π΅ΡΡΡ Π²ΡΠ΅ΠΌΡ ΠΏΠ΅ΡΠ΅Ρ ΠΎΠ΄Π° ΠΊ Π½ΠΎΠ²ΠΎΠΌΡ Π²ΠΈΠ΄Ρ ΠΈΠ·Π΄Π΅Π»ΠΈΡ, ΡΡΡΠ΅ΠΊΡΠΈΠ²Π½ΠΎ ΠΈΡΠΏΠΎΠ»ΡΠ·ΡΠ΅ΡΡΡ ΠΎΠ±ΠΎΡΡΠ΄ΠΎΠ²Π°Π½ΠΈΠ΅, ΡΠ°Π±ΠΎΡΠΈΠΌ Π»Π΅Π³ΡΠ΅ ΠΎΠ²Π»Π°Π΄Π΅ΡΡ ΡΠΌΠ΅ΠΆΠ½ΡΠΌΠΈ ΡΠΏΠ΅ΡΠΈΠ°Π»ΡΠ½ΠΎΡΡΡΠΌΠΈ. Π‘ΠΎΡΠ΅ΡΠ°Π½ΠΈΠ΅ Π²ΡΡΠΎΠΊΠΎΠΉ ΡΡΡΠ΅ΠΊΡΠΈΠ²Π½ΠΎΡΡΠΈ ΡΠ°Π±ΠΎΡΡ ΡΡΠ΅Π΅ΠΊ Ρ ΠΌΠ°Π»ΡΠΌΠΈ ΡΠ°Π·ΠΌΠ΅ΡΠ°ΠΌΠΈ ΠΏΡΠΎΠΈΠ·Π²ΠΎΠ΄ΡΡΠ²Π΅Π½Π½ΡΡ ΠΏΠ°ΡΡΠΈΠΉ ΠΏΡΠΈΠ²ΠΎΠ΄ΠΈΡ ΠΊ ΠΌΠΈΠ½ΠΈΠΌΠ°Π»ΡΠ½ΠΎΠΌΡ ΠΎΠ±ΡΠ΅ΠΌΡ Π½Π΅Π·Π°Π²Π΅ΡΡΠ΅Π½Π½ΠΎΠ³ΠΎ ΠΏΡΠΎΠΈΠ·Π²ΠΎΠ΄ΡΡΠ²Π°.
ΠΠΎΡΡΠΎΡΠ½Π½ΠΎΠ΅ ΡΠΎΠ²Π΅ΡΡΠ΅Π½ΡΡΠ²ΠΎΠ²Π°Π½ΠΈΠ΅ ΠΊΠ°ΡΠ΅ΡΡΠ²Π° ΡΠ°ΡΡΠΎ Π½Π°ΠΏΡΠ°Π²Π»Π΅Π½ΠΎ Π½Π° ΠΏΠΎΠΈΡΠΊ ΠΈ ΡΡΡΡΠ°Π½Π΅Π½ΠΈΠ΅ Π²ΡΠ΅Ρ ΠΏΡΠΈΡΠΈΠ½, Π²ΡΠ·ΡΠ²Π°ΡΡΠΈΡ ΠΏΡΠΎΠ±Π»Π΅ΠΌΡ.
Π‘ΠΈΡΡΠ΅ΠΌΡ Β«ΡΠΎΡΠ½ΠΎ-Π²-ΡΡΠΎΠΊΒ» ΡΠΎΠ·Π΄Π°Π½Ρ Π΄Π»Ρ ΡΠ²Π΅Π΄Π΅Π½ΠΈΡ ΠΊ ΠΌΠΈΠ½ΠΈΠΌΡΠΌΡ ΠΌΠ°ΡΠ΅ΡΠΈΠ°Π»ΡΠ½ΡΡ Π·Π°ΠΏΠ°ΡΠΎΠ² ΠΏΡΠΎΠΈΠ·Π²ΠΎΠ΄ΡΡΠ²Π°. Π‘ΠΎΠ³Π»Π°ΡΠ½ΠΎ ΡΠΈΠ»ΠΎΡΠΎΡΠΈΠΈ JIT, Ρ ΡΠ°Π½Π΅Π½ΠΈΠ΅ Π·Π°ΠΏΠ°ΡΠΎΠ² β Π±Π΅ΡΡΠΌΡΡΠ»Π΅Π½Π½ΡΠ΅ ΡΠ°ΡΡ ΠΎΠ΄Ρ. ΠΠ°ΠΏΠ°ΡΡ β ΡΡΠΎ ΡΠ²ΠΎΠ΅Π³ΠΎ ΡΠΎΠ΄Π° Π±ΡΡΠ΅ΡΡ, ΠΊΠΎΡΠΎΡΡΠ΅ ΡΠΊΡΡΠ²Π°ΡΡ ΠΏΠΎΠ²ΡΠΎΡΡΡΡΠΈΠ΅ΡΡ ΠΏΡΠΎΠ±Π»Π΅ΠΌΡ. ΠΡΠΈ ΠΏΡΠΎΠ±Π»Π΅ΠΌΡ Π½Π΅ ΡΠ΅ΡΠ°ΡΡΡΡ β ΡΠ°ΡΡΠΈΡΠ½ΠΎ ΠΈΠΌΠ΅Π½Π½ΠΎ ΠΏΠΎ ΡΠΎΠΉ ΠΏΡΠΈΡΠΈΠ½Π΅, ΡΡΠΎ ΠΎΠ½ΠΈ ΡΠΊΡΡΡΡ, Π° ΡΠ°ΡΡΠΈΡΠ½ΠΎ ΠΏΠΎΡΠΎΠΌΡ, ΡΡΠΎ Π½Π°Π»ΠΈΡΠΈΠ΅ ΡΠ΅Π·Π΅ΡΠ²Π½ΠΎΠ³ΠΎ Π·Π°ΠΏΠ°ΡΠ° Π΄Π΅Π»Π°Π΅Ρ ΠΈΡ ΠΌΠ΅Π½Π΅Π΅ ΡΠ΅ΡΡΠ΅Π·Π½ΡΠΌΠΈ.
ΠΡΠΏΠΎΠ»ΡΠ·ΡΡ ΠΏΠΎΠ΄Ρ ΠΎΠ΄ JIT, ΠΏΠΎΡΡΠ΅ΠΏΠ΅Π½Π½ΠΎ ΠΏΠΎΠ½ΠΈΠΆΠ°ΡΡ ΡΡΠΎΠ²Π΅Π½Ρ Π·Π°ΠΏΠ°ΡΠΎΠ², ΡΡΠΎΠ±Ρ ΠΎΡΠΊΡΡΡΡ ΠΏΡΠΎΠ±Π»Π΅ΠΌΡ. ΠΠΎΠ³Π΄Π° ΠΏΡΠΎΠ±Π»Π΅ΠΌΡ ΠΎΠ±Π½Π°ΡΡΠΆΠ΅Π½Ρ ΠΈ ΡΠ΅ΡΠ΅Π½Ρ, ΡΡΠΎΠ²Π΅Π½Ρ Π·Π°ΠΏΠ°ΡΠΎΠ² Π΅ΡΠ΅ ΡΠ°Π· ΠΏΠΎΠ½ΠΈΠΆΠ°ΡΡ, Π½Π°Ρ ΠΎΠ΄ΡΡ ΠΈ ΡΠ΅ΡΠ°ΡΡ ΡΠ»Π΅Π΄ΡΡΡΠΈΠΉ ΠΏΠ»Π°ΡΡ ΠΏΡΠΎΠ±Π»Π΅ΠΌ ΠΈ Ρ.Π΄.
Β
3. ΠΠ°Π΄ΡΠΎΠ²ΡΠ΅/ΠΎΡΠ³Π°Π½ΠΈΠ·Π°ΡΠΈΠΎΠ½Π½ΡΠ΅ ΡΠ»Π΅ΠΌΠ΅Π½ΡΡ
Π‘ΡΡΠ΅ΡΡΠ²ΡΠ΅Ρ ΠΏΡΡΡ ΠΊΠ°Π΄ΡΠΎΠ²ΡΡ ΠΈ ΠΎΡΠ³Π°Π½ΠΈΠ·Π°ΡΠΈΠΎΠ½Π½ΡΡ ΡΠ»Π΅ΠΌΠ΅Π½ΡΠΎΠ², ΠΎΡΠΎΠ±Π΅Π½Π½ΠΎ Π²Π°ΠΆΠ½ΡΡ Π΄Π»Ρ ΡΠΈΡΡΠ΅ΠΌ JIT:
- Π Π°Π±ΠΎΡΠΈΠ΅ ΠΊΠ°ΠΊ Π°ΠΊΡΠΈΠ²
- ΠΠ±ΡΡΠ΅Π½ΠΈΠ΅ ΡΠ°Π±ΠΎΡΠΈΡ ΡΠΌΠ΅ΠΆΠ½ΡΠΌ ΡΠΏΠ΅ΡΠΈΠ°Π»ΡΠ½ΠΎΡΡΡΠΌ
- ΠΠ΅ΠΏΡΠ΅ΡΡΠ²Π½ΠΎΠ΅ ΡΡΠΎΠ²Π΅ΡΡΠ΅Π½ΡΡΠ²ΠΎΠ²Π°Π½ΠΈΠ΅
- ΠΡΡ Π³Π°Π»ΡΠ΅ΡΡΠΊΠΈΠΉ ΡΡΠ΅Ρ
- Π ΡΠΊΠΎΠ²ΠΎΠ΄ΡΡΠ²ΠΎ ΠΏΡΠ΅Π΄ΠΏΡΠΈΡΡΠΈΠ΅ΠΌ/ΠΏΡΠΎΠ΅ΠΊΡΠΎΠΌ
Β
Π€ΡΠ½Π΄Π°ΠΌΠ΅Π½ΡΠ°Π»ΡΠ½ΡΠΉ ΠΏΡΠΈΠ½ΡΠΈΠΏ ΡΠΈΠ»ΠΎΡΠΎΡΠΈΠΈ JIT β ΡΡΠΈΡΠ°ΡΡ ΡΠ°Π±ΠΎΡΠΈΡ Π°ΠΊΡΠΈΠ²Π½ΡΠΌ ΠΊΠ°ΠΏΠΈΡΠ°Π»ΠΎΠΌ ΠΏΡΠ΅Π΄ΠΏΡΠΈΡΡΠΈΡ. Π₯ΠΎΡΠΎΡΠΎ ΠΎΠ±ΡΡΠ΅Π½Π½ΡΠ΅ ΠΈ ΠΌΠΎΡΠΈΠ²ΠΈΡΠΎΠ²Π°Π½Π½ΡΠ΅ ΡΠ°Π±ΠΎΡΠΈΠ΅ ΡΠ²Π»ΡΡΡΡΡ ΡΠ΅ΡΠ΄ΡΠ΅ΠΌ ΡΠΈΡΡΠ΅ΠΌΡ. ΠΠ½ΠΈ ΠΈΠΌΠ΅ΡΡ Π±ΠΎΠ»ΡΡΠ΅ ΠΏΠΎΠ»Π½ΠΎΠΌΠΎΡΠΈΠΉ Π² ΠΏΡΠΈΠ½ΡΡΠΈΠΈ ΡΠ΅ΡΠ΅Π½ΠΈΠΉ, ΡΠ΅ΠΌ ΠΈΡ ΠΊΠΎΠ»Π»Π΅Π³ΠΈ Π² ΡΡΠ°Π΄ΠΈΡΠΈΠΎΠ½Π½ΡΡ ΡΠΈΡΡΠ΅ΠΌΠ°Ρ , Π½ΠΎ ΠΎΡ Π½ΠΈΡ ΡΠΎΠΎΡΠ²Π΅ΡΡΡΠ²Π΅Π½Π½ΠΎ ΠΈ ΠΆΠ΄ΡΡ Π±ΠΎΠ»ΡΡΠ΅Π³ΠΎ.
Π Π°Π±ΠΎΡΠΈΠ΅ ΠΎΠ±ΡΡΠ°ΡΡΡΡ ΡΠΌΠ΅ΠΆΠ½ΡΠΌ ΡΠΏΠ΅ΡΠΈΠ°Π»ΡΠ½ΠΎΡΡΡΠΌ Π΄Π»Ρ Π²ΡΠΏΠΎΠ»Π½Π΅Π½ΠΈΡ Π½Π΅ΡΠΊΠΎΠ»ΡΠΊΠΈΡ ΡΠ»Π΅ΠΌΠ΅Π½ΡΠΎΠ² ΠΏΡΠΎΡΠ΅ΡΡΠ° ΠΈ ΡΠ°Π±ΠΎΡΡ Π½Π° ΡΠ°Π·Π½ΠΎΠΎΠ±ΡΠ°Π·Π½ΠΎΠΌ ΠΎΠ±ΠΎΡΡΠ΄ΠΎΠ²Π°Π½ΠΈΠΈ. ΠΡΠΎ ΠΏΡΠΈΠ΄Π°Π΅Ρ ΡΠΈΡΡΠ΅ΠΌΠ΅ Π΄ΠΎΠΏΠΎΠ»Π½ΠΈΡΠ΅Π»ΡΠ½ΡΡ Π³ΠΈΠ±ΠΊΠΎΡΡΡ, ΠΏΠΎΡΠΎΠΌΡ ΡΡΠΎ ΡΠ°Π±ΠΎΡΠΈΠ΅ ΠΌΠΎΠ³ΡΡ ΠΎΠΊΠ°Π·Π°ΡΡ Π΄ΡΡΠ³ Π΄ΡΡΠ³Ρ ΠΏΠΎΠΌΠΎΡΡ ΠΏΡΠΈ ΠΏΠΎΡΠ²Π»Π΅Π½ΠΈΠΈ Β«Π·Π°ΡΠΎΡΠΎΠ²Β» Π² ΠΏΡΠΎΠΈΠ·Π²ΠΎΠ΄ΡΡΠ²Π΅Π½Π½ΠΎΠΌ ΠΏΡΠΎΡΠ΅ΡΡΠ΅ ΠΈΠ»ΠΈ Π·Π°ΠΌΠ΅Π½ΠΈΡΡ ΠΎΡΡΡΡΡΡΠ²ΡΡΡΠ΅Π³ΠΎ ΠΊΠΎΠ»Π»Π΅Π³Ρ.
Π Π°Π±ΠΎΡΠΈΠ΅ Π² ΡΠΈΡΡΠ΅ΠΌΠ΅ JIT Π½Π΅ΡΡΡ Π±ΠΎΠ»ΡΡΡΡ ΠΎΡΠ²Π΅ΡΡΡΠ²Π΅Π½Π½ΠΎΡΡΡ Π·Π° ΠΊΠ°ΡΠ΅ΡΡΠ²ΠΎ, ΡΠ΅ΠΌ ΡΠ°Π±ΠΎΡΠΈΠ΅ Π² ΡΡΠ°Π΄ΠΈΡΠΈΠΎΠ½Π½ΡΡ ΡΠΈΡΡΠ΅ΠΌΠ°Ρ . ΠΡ Π½ΠΈΡ ΠΆΠ΄ΡΡ ΡΡΠ°ΡΡΠΈΡ Π² ΡΠ΅ΡΠ΅Π½ΠΈΠΈ ΠΏΡΠΎΠ±Π»Π΅ΠΌ Π² ΠΏΡΠΎΡΠ΅ΡΡΠ΅ Π½Π΅ΠΏΡΠ΅ΡΡΠ²Π½ΠΎΠ³ΠΎ ΡΡΠΎΠ²Π΅ΡΡΠ΅Π½ΡΡΠ²ΠΎΠ²Π°Π½ΠΈΡ. Π Π°Π±ΠΎΡΠΈΠ΅ Π² ΡΠΈΡΡΠ΅ΠΌΠ°Ρ JIT ΠΎΠ±ΡΡΠ½ΠΎ ΠΏΡΠΎΡ ΠΎΠ΄ΡΡ ΡΠ΅ΡΡΠ΅Π·Π½ΡΡ ΠΏΠΎΠ΄Π³ΠΎΡΠΎΠ²ΠΊΡ Π² ΠΎΠ±Π»Π°ΡΡΠΈ ΡΡΠ°ΡΠΈΡΡΠΈΡΠ΅ΡΠΊΠΎΠ³ΠΎ ΡΠΏΡΠ°Π²Π»Π΅Π½ΠΈΡ ΠΏΡΠΎΡΠ΅ΡΡΠΎΠΌ, ΡΠ»ΡΡΡΠ΅Π½ΠΈΡ ΠΊΠ°ΡΠ΅ΡΡΠ²Π° ΠΈ ΡΠ΅ΡΠ΅Π½ΠΈΡ ΠΏΡΠΎΠ±Π»Π΅ΠΌ.
ΠΡΡΠ³Π°Ρ Ρ Π°ΡΠ°ΠΊΡΠ΅ΡΠ½Π°Ρ ΡΠ΅ΡΡΠ° Β«ΡΠΎΡΠ½ΠΎΡΡΠΎΡΠ½ΡΡ ΡΠΈΡΡΠ΅ΠΌΒ» β ΡΠΏΠΎΡΠΎΠ± ΡΠ°ΡΠΏΡΠ΅Π΄Π΅Π»Π΅Π½ΠΈΡ Π½Π°ΠΊΠ»Π°Π΄Π½ΡΡ ΡΠ°ΡΡ ΠΎΠ΄ΠΎΠ². Π’ΡΠ°Π΄ΠΈΡΠΈΠΎΠ½Π½ΡΠ΅ ΠΌΠ΅ΡΠΎΠ΄Ρ ΡΡΠ΅ΡΠ° ΠΈΠ½ΠΎΠ³Π΄Π° ΠΈΡΠΊΠ°ΠΆΠ°ΡΡ ΡΠ°ΡΠΏΡΠ΅Π΄Π΅Π»Π΅Π½ΠΈΠ΅ ΡΠ°ΡΡ ΠΎΠ΄ΠΎΠ², ΠΏΠΎΡΠΎΠΌΡ ΡΡΠΎ ΡΠ°ΡΠΏΡΠ΅Π΄Π΅Π»ΡΡΡ ΠΈΡ Π½Π° ΠΎΡΠ½ΠΎΠ²Π΅ Π½Π΅ΠΏΠΎΡΡΠ΅Π΄ΡΡΠ²Π΅Π½Π½ΠΎ ΠΎΡΡΠ°Π±ΠΎΡΠ°Π½Π½ΡΡ ΡΠ°ΡΠΎΠ².
ΠΡΠ΅ ΠΎΠ΄Π½ΠΎ ΡΠ²ΠΎΠΉΡΡΠ²ΠΎ ΡΠΈΡΡΠ΅ΠΌ Β«ΡΠΎΡΠ½ΠΎ-Π²-ΡΡΠΎΠΊΒ» ΡΠ²ΡΠ·Π°Π½ΠΎ Ρ ΡΡΠΊΠΎΠ²ΠΎΠ΄ΡΡΠ²ΠΎΠΌ. ΠΡ ΠΌΠ΅Π½Π΅Π΄ΠΆΠ΅ΡΠ° ΡΡΠ΅Π±ΡΠ΅ΡΡΡ Π±ΡΡΡ Π»ΠΈΠ΄Π΅ΡΠΎΠΌ ΠΈ ΠΏΠΎΠΌΠΎΡΠ½ΠΈΠΊΠΎΠΌ, Π° Π½Π΅ ΠΏΡΠΎΡΡΠΎ ΠΎΡΠ΄Π°Π²Π°ΡΡ ΠΏΡΠΈΠΊΠ°Π·Ρ. ΠΡΡΡΠ΅ΡΠΊΠΈ ΠΏΠΎΠΎΡΡΡΡΡΡΡ Π΄Π²ΡΡΡΠΎΡΠΎΠ½Π½ΠΈΠ΅ ΡΠ²ΡΠ·ΠΈ ΠΌΠ΅ΠΆΠ΄Ρ ΠΌΠ΅Π½Π΅Π΄ΠΆΠ΅ΡΠ°ΠΌΠΈ ΠΈ ΡΠ°Π±ΠΎΡΠΈΠΌΠΈ.
Β
4. ΠΠ»Π°Π½ΠΈΡΠΎΠ²Π°Π½ΠΈΠ΅ ΠΈ ΡΠΏΡΠ°Π²Π»Π΅Π½ΠΈΠ΅ ΠΏΡΠΎΠΈΠ·Π²ΠΎΠ΄ΡΡΠ²ΠΎΠΌ
5 ΡΠ»Π΅ΠΌΠ΅Π½ΡΠΎΠ² ΠΏΡΠΎΠΈΠ·Π²ΠΎΠ΄ΡΡΠ²Π΅Π½Π½ΠΎΠ³ΠΎ ΡΠΏΡΠ°Π²Π»Π΅Π½ΠΈΡ ΠΈ ΠΏΠ»Π°Π½ΠΈΡΠΎΠ²Π°Π½ΠΈΡ ΠΎΡΠΎΠ±Π΅Π½Π½ΠΎ Π²Π°ΠΆΠ½Ρ Π΄Π»Ρ ΡΠΈΡΡΠ΅ΠΌ JIT:
- Π Π°Π²Π½ΠΎΠΌΠ΅ΡΠ½Π°Ρ Π·Π°Π³ΡΡΠ·ΠΊΠ° ΡΠΈΡΡΠ΅ΠΌΡ.
- Π‘ΠΈΡΡΠ΅ΠΌΠ° ΠΏΠ΅ΡΠ΅ΠΌΠ΅ΡΠ΅Π½ΠΈΡ ΡΠ°Π±ΠΎΡΡ.
- ΠΠΈΠ·ΡΠ°Π»ΡΠ½ΡΠ΅ ΡΠΈΡΡΠ΅ΠΌΡ.
- Π’Π΅ΡΠ½ΡΠ΅ Π²Π·Π°ΠΈΠΌΠΎΡΠ²ΡΠ·ΠΈ Ρ ΠΏΠΎΡΡΠ°Π²ΡΠΈΠΊΠ°ΠΌΠΈ.
- Π‘ΠΎΠΊΡΠ°ΡΠ΅Π½ΠΈΠ΅ ΡΠΈΡΠ»Π° ΠΎΠΏΠ΅ΡΠ°ΡΠΈΠΉ ΠΈ ΠΎΠ±ΡΠ΅ΠΌΠ° Π΄Π΅Π»ΠΎΠΏΡΠΎΠΈΠ·Π²ΠΎΠ΄ΡΡΠ²Π°.
Β
ΠΡΠ½ΠΎΠ²Π½ΠΎΠΉ ΡΠΏΠΎΡ Π² ΡΠΈΡΡΠ΅ΠΌΠ°Ρ JIT ΡΠ΄Π΅Π»Π°Π½ Π½Π° Π΄ΠΎΡΡΠΈΠΆΠ΅Π½ΠΈΠ΅ ΡΡΠ°Π±ΠΈΠ»ΡΠ½ΡΡ , ΡΡΠ°Π²Π½ΠΎΠ²Π΅ΡΠ΅Π½Π½ΡΡ ΡΠ°Π±ΠΎΡΠΈΡ Π³ΡΠ°ΡΠΈΠΊΠΎΠ². Π‘ ΡΡΠΎΠΉ ΡΠ΅Π»ΡΡ, ΠΎΡΠ½ΠΎΠ²Π½ΡΠ΅ ΠΏΡΠΎΠΈΠ·Π²ΠΎΠ΄ΡΡΠ²Π΅Π½Π½ΡΠ΅ Π³ΡΠ°ΡΠΈΠΊΠΈ ΡΠ°Π·ΡΠ°Π±Π°ΡΡΠ²Π°ΡΡΡΡ ΡΠ°ΠΊ, ΡΡΠΎΠ±Ρ ΠΎΠ±Π΅ΡΠΏΠ΅ΡΠΈΡΡ ΡΠ°Π²Π½ΠΎΠΌΠ΅ΡΠ½ΡΡ ΡΠ°Π±ΠΎΡΡΡ Π·Π°Π³ΡΡΠ·ΠΊΡ ΠΏΡΠΎΠΈΠ·Π²ΠΎΠ΄ΡΡΠ²Π΅Π½Π½ΡΡ ΠΌΠΎΡΠ½ΠΎΡΡΠ΅ΠΉ.
ΠΠΎΠ½ΡΡΠΈΡ Β«ΡΡΠ½ΡΡΡΒ» ΠΈ Β«ΡΠΎΠ»ΠΊΠ°ΡΡΒ» ΠΈΡΠΏΠΎΠ»ΡΠ·ΡΡΡ Π΄Π»Ρ ΠΎΠΏΠΈΡΠ°Π½ΠΈΡ Π΄Π²ΡΡ ΡΠ°Π·Π»ΠΈΡΠ½ΡΡ ΡΠΏΠΎΡΠΎΠ±ΠΎΠ² ΠΏΠ΅ΡΠ΅ΠΌΠ΅ΡΠ΅Π½ΠΈΡ ΡΠ°Π±ΠΎΡΡ ΡΠ΅ΡΠ΅Π· ΠΏΡΠΎΠΈΠ·Π²ΠΎΠ΄ΡΡΠ²Π΅Π½Π½ΡΡ ΡΠΈΡΡΠ΅ΠΌΡ. Π Β«ΡΠΎΠ»ΠΊΠ°ΡΡΠΈΡ Β» ΡΠΈΡΡΠ΅ΠΌΠ°Ρ (push system), ΠΏΠΎ ΠΎΠΊΠΎΠ½ΡΠ°Π½ΠΈΠΈ ΡΠ°Π±ΠΎΡΡ Π½Π° ΠΏΡΠΎΠΈΠ·Π²ΠΎΠ΄ΡΡΠ²Π΅Π½Π½ΠΎΠΌ ΡΡΠ°ΡΡΠΊΠ΅, ΠΏΡΠΎΠ΄ΡΠΊΡΠΈΡ ΡΠΎΠ»ΠΊΠ°ΡΡ Π½Π° ΡΠ»Π΅Π΄ΡΡΡΠΈΠΉ ΡΡΠ°ΡΡΠΎΠΊ; ΠΈΠ»ΠΈ ΠΆΠ΅, Π΅ΡΠ»ΠΈ Π΄Π°Π½Π½Π°Ρ ΠΎΠΏΠ΅ΡΠ°ΡΠΈΡ Π±ΡΠ»Π° Π·Π°Π²Π΅ΡΡΠ°ΡΡΠ΅ΠΉ, Π³ΠΎΡΠΎΠ²ΡΠ΅ ΠΈΠ·Π΄Π΅Π»ΠΈΡ Π²ΡΡΠ°Π»ΠΊΠΈΠ²Π°ΡΡΡΡ Π½Π° ΡΠΊΠ»Π°Π΄ ΠΊΠΎΠ½Π΅ΡΠ½ΠΎΠΉ ΠΏΡΠΎΠ΄ΡΠΊΡΠΈΠΈ.
Π Β«ΡΡΠ½ΡΡΠΈΡ Β» ΡΠΈΡΡΠ΅ΠΌΠ°Ρ (pull system) ΡΠΏΡΠ°Π²Π»Π΅Π½ΠΈΠ΅ ΠΏΠ΅ΡΠ΅ΠΌΠ΅ΡΠ΅Π½ΠΈΠ΅ΠΌ ΡΠ°Π±ΠΎΡΡ Π·Π°ΠΊΡΠ΅ΠΏΠ»Π΅Π½ΠΎ Π·Π° ΠΏΠΎΡΠ»Π΅Π΄ΡΡΡΠ΅ΠΉ ΠΎΠΏΠ΅ΡΠ°ΡΠΈΠ΅ΠΉ: ΠΊΠ°ΠΆΠ΄ΡΠΉ ΡΠ°Π±ΠΎΡΠΈΠΉ ΡΡΠ°ΡΡΠΎΠΊ ΠΏΠΎ ΠΌΠ΅ΡΠ΅ Π½Π΅ΠΎΠ±Ρ ΠΎΠ΄ΠΈΠΌΠΎΡΡΠΈ Β«ΠΏΡΠΈΡΡΠ³ΠΈΠ²Π°Π΅ΡΒ» ΡΠ΅Π±Π΅ ΠΏΡΠΎΠ΄ΡΠΊΡΠΈΡ Ρ ΠΏΡΠ΅Π΄ΡΠ΄ΡΡΠ΅Π³ΠΎ ΡΡΠ°ΡΡΠΊΠ°; ΠΏΡΠΎΠ΄ΡΠΊΡΠΈΡ Ρ ΠΊΠΎΠ½Π΅ΡΠ½ΠΎΠΉ ΠΎΠΏΠ΅ΡΠ°ΡΠΈΠΈ Β«Π²ΡΡΡΠ³ΠΈΠ²Π°Π΅ΡΡΡΒ» Π·Π°ΠΏΡΠΎΡΠΎΠΌ ΠΏΠΎΡΡΠ΅Π±ΠΈΡΠ΅Π»Ρ ΠΈΠ»ΠΈ ΠΊΠΎΠ½ΡΡΠΎΠ»ΡΠ½ΡΠΌ Π³ΡΠ°ΡΠΈΠΊΠΎΠΌ. Β«Π’ΠΎΡΠ½ΠΎΡΡΠΎΡΠ½ΡΠ΅ ΡΠΈΡΡΠ΅ΠΌΡΒ» ΠΈΡΠΏΠΎΠ»ΡΠ·ΡΡΡ Β«ΡΡΠ½ΡΡΠΈΠΉΒ» ΠΏΠΎΠ΄Ρ ΠΎΠ΄ Π΄Π»Ρ ΡΠΏΡΠ°Π²Π»Π΅Π½ΠΈΡ ΠΏΠΎΡΠΎΠΊΠΎΠΌ ΡΠ°Π±ΠΎΡΡ ΠΊΠΎΠ³Π΄Π° ΠΊΠ°ΠΆΠ΄ΡΠΉ ΡΠ°Π±ΠΎΡΠΈΠΉ ΡΡΠ°ΡΡΠΎΠΊ Π²ΡΠΏΡΡΠΊΠ°Π΅Ρ ΠΏΡΠΎΠ΄ΡΠΊΡΠΈΡ Π² ΡΠΎΠΎΡΠ²Π΅ΡΡΡΠ²ΠΈΠΈ Ρ Π·Π°ΠΏΡΠΎΡΠΎΠΌ ΠΏΠΎΡΠ»Π΅Π΄ΡΡΡΠ΅Π³ΠΎ ΡΠ°Π±ΠΎΡΠ΅Π³ΠΎ ΡΡΠ°ΡΡΠΊΠ°. Π’ΡΠ°Π΄ΠΈΡΠΈΠΎΠ½Π½ΡΠ΅ ΠΏΡΠΎΠΈΠ·Π²ΠΎΠ΄ΡΡΠ²Π΅Π½Π½ΡΠ΅ ΡΠΈΡΡΠ΅ΠΌΡ ΠΈΡΠΏΠΎΠ»ΡΠ·ΡΡΡ Β«ΡΠΎΠ»ΠΊΠ°ΡΡΠΈΠΉΒ» ΠΏΠΎΠ΄Ρ ΠΎΠ΄ Π΄Π»Ρ ΠΏΡΠΎΠ΄Π²ΠΈΠΆΠ΅Π½ΠΈΡ ΡΠ°Π±ΠΎΡ ΡΠ΅ΡΠ΅Π· ΡΠΈΡΡΠ΅ΠΌΡ.
ΠΠ°ΠΊ ΠΏΡΠ°Π²ΠΈΠ»ΠΎ, Π² ΡΠΈΡΡΠ΅ΠΌΠ°Ρ Β«ΡΠΎΡΠ½ΠΎ-Π²-ΡΡΠΎΠΊΒ» Π΄Π΅ΠΉΡΡΠ²ΡΡΡ ΠΎΡΠ΅Π½Ρ ΡΠ΅ΡΠ½ΡΠ΅ ΡΠ²ΡΠ·ΠΈ Ρ ΠΏΠΎΡΡΠ°Π²ΡΠΈΠΊΠ°ΠΌΠΈ, ΠΊΠΎΡΠΎΡΡΠ΅ Π΄ΠΎΠ»ΠΆΠ½Ρ ΠΎΠ±Π΅ΡΠΏΠ΅ΡΠΈΡΡ ΡΠ°ΡΡΡΠ΅ ΠΏΠΎΡΡΠ°Π²ΠΊΠΈ Π½Π΅Π±ΠΎΠ»ΡΡΠΈΡ ΠΏΠ°ΡΡΠΈΠΉ Π²ΡΡΠΎΠΊΠΎΠΊΠ°ΡΠ΅ΡΡΠ²Π΅Π½Π½ΡΡ ΠΈΠ·Π΄Π΅Π»ΠΈΠΉ. Π ΡΡΠ°Π΄ΠΈΡΠΈΠΎΠ½Π½ΠΎΠΉ ΠΏΡΠΎΠΈΠ·Π²ΠΎΠ΄ΡΡΠ²Π΅Π½Π½ΠΎΠΉ ΡΠΈΡΡΠ΅ΠΌΠ΅, ΠΏΠΎΠΊΡΠΏΠ°ΡΠ΅Π»ΠΈ ΡΠ°ΠΌΠΈ ΡΠ»Π΅Π΄ΡΡ Π·Π° ΠΊΠ°ΡΠ΅ΡΡΠ²ΠΎΠΌ Π·Π°ΠΊΡΠΏΠ»Π΅Π½Π½ΠΎΠΉ ΠΏΡΠΎΠ΄ΡΠΊΡΠΈΠΈ, ΠΏΡΠΎΠ²Π΅ΡΡΡ ΠΏΠ°ΡΡΠΈΠΈ ΠΏΠΎΡΡΠ°Π²ΠΎΠΊ Π½Π° ΠΊΠ°ΡΠ΅ΡΡΠ²ΠΎ ΠΈ ΠΊΠΎΠ»ΠΈΡΠ΅ΡΡΠ²ΠΎ, ΠΈ Π²ΠΎΠ·Π²ΡΠ°ΡΠ°Ρ Π½Π΅ΠΊΠ°ΡΠ΅ΡΡΠ²Π΅Π½Π½ΡΠΉ ΡΠΎΠ²Π°Ρ ΠΎΠ±ΡΠ°ΡΠ½ΠΎ ΠΏΠΎΡΡΠ°Π²ΡΠΈΠΊΡ Π΄Π»Ρ Π΄ΠΎΡΠ°Π±ΠΎΡΠΊΠΈ ΠΈ Π·Π°ΠΌΠ΅Π½Ρ.
Π Β«ΡΠΎΡΠ½ΠΎΡΡΠΎΡΠ½ΡΡ Β» ΡΠΈΡΡΠ΅ΠΌΠ°Ρ ΡΠ΅Π·Π΅ΡΠ²Π½ΠΎΠ³ΠΎ Π²ΡΠ΅ΠΌΠ΅Π½ΠΈ ΠΏΡΠ°ΠΊΡΠΈΡΠ΅ΡΠΊΠΈ Π½Π΅Ρ, ΠΏΠΎΡΡΠΎΠΌΡ Π½Π΅ΠΊΠ°ΡΠ΅ΡΡΠ²Π΅Π½Π½ΡΠ΅ ΠΈΠ·Π΄Π΅Π»ΠΈΡ Π½Π°ΡΡΡΠ°ΡΡ ΠΏΠ»Π°Π²Π½ΠΎΠ΅ Π΄Π²ΠΈΠΆΠ΅Π½ΠΈΠ΅ ΡΠ°Π±ΠΎΡΡ ΡΠ΅ΡΠ΅Π· ΡΠΈΡΡΠ΅ΠΌΡ. ΠΠΎΠ»Π΅Π΅ ΡΠΎΠ³ΠΎ, ΠΏΡΠΎΠ²Π΅ΡΠΊΠ° ΠΏΠΎΡΡΡΠΏΠ°ΡΡΠΈΡ Π·Π°ΠΊΡΠΏΠΎΠΊ ΡΡΠΈΡΠ°Π΅ΡΡΡ Π½Π΅ΠΏΡΠΎΠΈΠ·Π²ΠΎΠ΄ΠΈΡΠ΅Π»ΡΠ½ΠΎΠΉ ΡΡΠ°ΡΠΎΠΉ Π²ΡΠ΅ΠΌΠ΅Π½ΠΈ, ΠΏΠΎΡΠΎΠΌΡ ΡΡΠΎ ΠΎΠ½Π° Π½ΠΈΡΠ΅Π³ΠΎ Π½Π΅ Π΄ΠΎΠ±Π°Π²Π»ΡΠ΅Ρ ΠΊ ΡΡΠΎΠΈΠΌΠΎΡΡΠΈ ΠΈΠ·Π΄Π΅Π»ΠΈΡ. ΠΠΎ ΡΡΠΎΠΉ ΠΏΡΠΈΡΠΈΠ½Π΅ ΠΎΠ±ΡΠ·Π°Π½Π½ΠΎΡΡΡ Π³Π°ΡΠ°Π½ΡΠΈΠΈ ΠΊΠ°ΡΠ΅ΡΡΠ²Π° ΠΏΠ΅ΡΠ΅Π΄Π°Π΅ΡΡΡ ΠΏΠΎΡΡΠ°Π²ΡΠΈΠΊΠ°ΠΌ.
ΠΠΎΠΊΡΠΏΠ°ΡΠ΅Π»ΠΈ ΡΠ°Π±ΠΎΡΠ°ΡΡ Ρ ΠΏΠΎΡΡΠ°Π²ΡΠΈΠΊΠ°ΠΌΠΈ, ΠΏΠΎΠΌΠΎΠ³Π°Ρ ΠΈΠΌ Π΄ΠΎΠ±ΠΈΡΡΡΡ Π½Π΅ΠΎΠ±Ρ ΠΎΠ΄ΠΈΠΌΠΎΠ³ΠΎ ΡΡΠΎΠ²Π½Ρ ΠΊΠ°ΡΠ΅ΡΡΠ²Π° ΠΈ ΠΎΡΠΎΠ·Π½Π°ΡΡ Π²ΡΡ Π²Π°ΠΆΠ½ΠΎΡΡΡ ΠΏΡΠΎΠΈΠ·Π²ΠΎΠ΄ΡΡΠ²Π° ΡΠΎΠ²Π°ΡΠΎΠ² ΠΏΠΎΡΡΠΎΡΠ½Π½ΠΎΠ³ΠΎ Π²ΡΡΠΎΠΊΠΎΠ³ΠΎ ΠΊΠ°ΡΠ΅ΡΡΠ²Π°. ΠΠΎΠ½Π΅ΡΠ½Π°Ρ ΡΠ΅Π»Ρ ΠΏΠΎΠΊΡΠΏΠ°ΡΠ΅Π»Ρ β Π·Π°ΠΊΡΠ΅ΠΏΠΈΡΡ Π·Π° ΠΏΠΎΡΡΠ°Π²ΡΠΈΠΊΠΎΠΌ ΡΠ΅ΡΡΠΈΡΠΈΠΊΠ°Ρ ΡΠΎΠΎΡΠ²Π΅ΡΡΡΠ²ΠΈΡ, ΠΊΠ°ΠΊ Π·Π° ΠΏΡΠΎΠΈΠ·Π²ΠΎΠ΄ΠΈΡΠ΅Π»Π΅ΠΌ ΡΠΎΠ²Π°ΡΠΎΠ² Π²ΡΡΠΎΠΊΠΎΠ³ΠΎ ΠΊΠ°ΡΠ΅ΡΡΠ²Π°. Π‘ΡΡΡ Π² ΡΠΎΠΌ, ΡΡΠΎΠ±Ρ Π½Π° ΠΏΠΎΡΡΠ°Π²ΡΠΈΠΊΠ° ΠΌΠΎΠΆΠ½ΠΎ Π±ΡΠ»ΠΎ ΠΏΠΎΠ»Π½ΠΎΡΡΡΡ ΠΏΠΎΠ»Π°Π³Π°ΡΡΡΡ, Π½Π΅ ΡΠΎΠΌΠ½Π΅Π²Π°ΡΡΡ, ΡΡΠΎ Π΅Π³ΠΎ ΠΏΠΎΡΡΠ°Π²ΠΊΠΈ Π±ΡΠ΄ΡΡ ΡΠΎΠΎΡΠ²Π΅ΡΡΡΠ²ΠΎΠ²Π°ΡΡ ΠΎΠΏΡΠ΅Π΄Π΅Π»Π΅Π½Π½ΠΎΠΌΡ ΡΡΠΎΠ²Π½Ρ ΠΊΠ°ΡΠ΅ΡΡΠ²Π° ΠΈ Π½Π΅ Π½ΡΠΆΠ΄Π°ΡΡΡΡ Π² ΠΏΡΠΎΠ²Π΅ΡΠΊΠ°Ρ ΡΠΎ ΡΡΠΎΡΠΎΠ½Ρ ΠΏΠΎΠΊΡΠΏΠ°ΡΠ΅Π»Ρ.
Π’Π΅Ρ Π½ΠΎΠ»ΠΎΠ³ΠΈΡΠ΅ΡΠΊΠΈΠ΅ ΠΈΠ·ΠΌΠ΅Π½Π΅Π½ΠΈΡ ΡΠ²Π»ΡΡΡΡΡ ΡΠ°ΠΌΡΠΌΠΈ Π΄ΠΎΡΠΎΠ³ΠΎΡΡΠΎΡΡΠΈΠΌΠΈ ΡΡΠ΅Π΄ΠΈ Π²ΡΠ΅Ρ ΠΏΠ΅ΡΠ΅ΡΠΈΡΠ»Π΅Π½Π½ΡΡ ΠΎΠΏΠ΅ΡΠ°ΡΠΈΠΉ. Π‘ΠΈΡΡΠ΅ΠΌΡ JIT ΡΠΎΠΊΡΠ°ΡΠ°ΡΡ ΡΠ°ΡΡ ΠΎΠ΄Ρ, ΡΠΌΠ΅Π½ΡΡΠΈΠ² ΡΠΈΡΠ»ΠΎ ΠΈ ΡΠ°ΡΡΠΎΡΡ ΠΏΡΠΎΠ²Π΅Π΄Π΅Π½ΠΈΡ ΠΏΠΎΠ΄ΠΎΠ±Π½ΡΡ ΠΎΠΏΠ΅ΡΠ°ΡΠΈΠΉ. ΠΠ°ΠΏΡΠΈΠΌΠ΅Ρ, ΠΏΠΎΡΡΠ°Π²ΡΠΈΠΊ Π΄ΠΎΡΡΠ°Π²Π»ΡΠ΅Ρ ΠΈΠ·Π΄Π΅Π»ΠΈΡ Π½Π΅ΠΏΠΎΡΡΠ΅Π΄ΡΡΠ²Π΅Π½Π½ΠΎ Π½Π° ΠΏΡΠΎΠΈΠ·Π²ΠΎΠ΄ΡΡΠ²ΠΎ, ΠΏΠΎΠ»Π½ΠΎΡΡΡΡ ΠΌΠΈΠ½ΡΡ ΡΠΊΠ»Π°Π΄Ρ, β ΡΠ΅ΠΌ ΡΠ°ΠΌΡΠΌ ΡΠΏΡΠ°Π·Π΄Π½ΡΠ΅ΡΡΡ Π΄Π΅ΡΡΠ΅Π»ΡΠ½ΠΎΡΡΡ, ΡΠ²ΡΠ·Π°Π½Π½Π°Ρ Ρ ΠΏΠΎΠΌΠ΅ΡΠ΅Π½ΠΈΠ΅ΠΌ ΠΌΠ°ΡΠ΅ΡΠΈΠ°Π»ΠΎΠ² Π½Π° ΡΠΊΠ»Π°Π΄ ΠΈ ΠΏΠΎΡΠ»Π΅Π΄ΡΡΡΠΈΠΌ ΠΏΠ΅ΡΠ΅ΠΌΠ΅ΡΠ΅Π½ΠΈΠ΅ΠΌ ΠΈΡ Π½Π° ΠΏΡΠΎΠΈΠ·Π²ΠΎΠ΄ΡΡΠ²Π΅Π½Π½ΡΠ΅ ΡΡΠ°ΡΡΠΊΠΈ.
ΠΠ΅ΡΠΊΠΎΠ½Π΅ΡΠ½ΡΠ΅ ΠΏΠΎΠΈΡΠΊΠΈ ΠΏΡΡΠ΅ΠΉ ΠΏΠΎΠ²ΡΡΠ΅Π½ΠΈΡ ΠΊΠ°ΡΠ΅ΡΡΠ²Π°, ΠΏΡΠΎΠ½ΠΈΠ·ΡΠ²Π°ΡΡΠΈΠ΅ Π²ΡΡ ΡΠΈΡΡΠ΅ΠΌΡ JIT, ΡΠΏΡΠ°Π·Π΄Π½ΡΡΡ ΠΌΠ½ΠΎΠ³ΠΈΠ΅ Π²ΠΈΠ΄Ρ Π΄Π΅ΡΡΠ΅Π»ΡΠ½ΠΎΡΡΠΈ, ΡΠ²ΡΠ·Π°Π½Π½ΡΠ΅ Ρ ΠΊΠ°ΡΠ΅ΡΡΠ²ΠΎΠΌ ΠΈΠ·Π΄Π΅Π»ΠΈΡ β ΠΈ ΡΠΎΠΎΡΠ²Π΅ΡΡΡΠ²ΡΡΡΠΈΠ΅ Π·Π°ΡΡΠ°ΡΡ. ΠΡΠΏΠΎΠ»ΡΠ·ΠΎΠ²Π°Π½ΠΈΠ΅ ΡΡΡΠΈΡ ΠΎΠ²ΠΎΠ³ΠΎ ΠΊΠΎΠ΄ΠΈΡΠΎΠ²Π°Π½ΠΈΡ (Π½Π΅ ΡΠΎΠ»ΡΠΊΠΎ Π² Β«ΡΠΎΡΠ½ΠΎΡΡΠΎΡΠ½ΡΡ Β» ΡΠΈΡΡΠ΅ΠΌΠ°Ρ ) ΠΏΠΎΠΌΠΎΠ³Π°Π΅Ρ ΡΠΎΠΊΡΠ°ΡΠΈΡΡ ΠΎΠΏΠ΅ΡΠ°ΡΠΈΠΈ ΠΏΠΎ Π²Π²ΠΎΠ΄Ρ Π΄Π°Π½Π½ΡΡ ΠΈ ΡΠ²Π΅Π»ΠΈΡΠΈΠ²Π°Π΅Ρ ΡΠΎΡΠ½ΠΎΡΡΡ Π΄Π°Π½Π½ΡΡ .
Β
Β«Π’ΠΎΡΠ½ΠΎΡΡΠΎΡΠ½ΡΠ΅Β» ΡΠΈΡΡΠ΅ΠΌΡ ΠΈΠΌΠ΅ΡΡ ΡΡΠ΄ Π²Π°ΠΆΠ½ΡΡ ΠΏΡΠ΅ΠΈΠΌΡΡΠ΅ΡΡΠ², ΠΊΠΎΡΠΎΡΡΠ΅ ΠΏΡΠΈΠ²Π»Π΅ΠΊΠ°ΡΡ Π²Π½ΠΈΠΌΠ°Π½ΠΈΠ΅ ΠΊΠΎΠΌΠΏΠ°Π½ΠΈΠΉ Ρ ΡΡΠ°Π΄ΠΈΡΠΈΠΎΠ½Π½ΡΠΌ ΠΏΠΎΠ΄Ρ ΠΎΠ΄ΠΎΠΌ ΠΊ ΠΏΡΠΎΠΈΠ·Π²ΠΎΠ΄ΡΡΠ²Ρ ΠΡΠ½ΠΎΠ²Π½ΡΠΌΠΈ ΠΏΡΠ΅ΠΈΠΌΡΡΠ΅ΡΡΠ²Π°ΠΌΠΈ ΡΠ²Π»ΡΡΡΡΡ:
- ΠΠΎΠ½ΠΈΠΆΠ΅Π½Π½ΡΠΉ ΡΡΠΎΠ²Π΅Π½Ρ ΠΌΠ°ΡΠ΅ΡΠΈΠ°Π»ΡΠ½ΡΡ Π·Π°ΠΏΠ°ΡΠΎΠ² Π² ΠΏΡΠΎΡΠ΅ΡΡΠ΅ ΠΏΡΠΎΠΈΠ·Π²ΠΎΠ΄ΡΡΠ²Π° (Π½Π΅Π·Π°Π²Π΅ΡΡΠ΅Π½Π½ΠΎΠ³ΠΎ ΠΏΡΠΎΠΈΠ·Π²ΠΎΠ΄ΡΡΠ²Π°), Π·Π°ΠΊΡΠΏΠΎΠΊ ΠΈ Π³ΠΎΡΠΎΠ²ΡΡ ΠΈΠ·Π΄Π΅Π»ΠΈΠΉ.
- ΠΠ΅Π½ΡΡΠΈΠ΅ ΡΡΠ΅Π±ΠΎΠ²Π°Π½ΠΈΡ ΠΊ ΡΠ°Π·ΠΌΠ΅ΡΠ°ΠΌ ΠΏΡΠΎΠΈΠ·Π²ΠΎΠ΄ΡΡΠ²Π΅Π½Π½ΡΡ ΠΏΠ»ΠΎΡΠ°Π΄Π΅ΠΉ.
- ΠΠΎΠ²ΡΡΠ΅Π½ΠΈΠ΅ ΠΊΠ°ΡΠ΅ΡΡΠ²Π° ΠΈΠ·Π΄Π΅Π»ΠΈΠΉ, ΡΠΌΠ΅Π½ΡΡΠ΅Π½ΠΈΠ΅ Π±ΡΠ°ΠΊΠ° ΠΈ ΠΏΠ΅ΡΠ΅Π΄Π΅Π»ΠΎΠΊ.
- Π‘ΠΎΠΊΡΠ°ΡΠ΅Π½ΠΈΠ΅ ΡΡΠΎΠΊΠΎΠ² ΠΏΡΠΎΠΈΠ·Π²ΠΎΠ΄ΡΡΠ²Π°.
- ΠΠΎΠ»ΡΡΠ°Ρ Π³ΠΈΠ±ΠΊΠΎΡΡΡ ΠΏΡΠΈ ΠΈΠ·ΠΌΠ΅Π½Π΅Π½ΠΈΠΈ Π°ΡΡΠΎΡΡΠΈΠΌΠ΅Π½ΡΠ° ΠΈΠ·Π΄Π΅Π»ΠΈΠΉ.
- ΠΠΎΠ»Π΅Π΅ ΠΏΠ»Π°Π²Π½ΡΠΉ ΠΏΠΎΡΠΎΠΊ ΠΏΡΠΎΠΈΠ·Π²ΠΎΠ΄ΡΡΠ²Π° Ρ ΠΎΡΠ΅Π½Ρ ΡΠ΅Π΄ΠΊΠΈΠΌΠΈ ΡΠ±ΠΎΡΠΌΠΈ, ΠΏΡΠΈΡΠΈΠ½Π°ΠΌΠΈ ΠΊΠΎΡΠΎΡΡΡ ΡΠ²Π»ΡΠ»ΠΈΡΡ Π±Ρ ΠΏΡΠΎΠ±Π»Π΅ΠΌΡ ΠΊΠ°ΡΠ΅ΡΡΠ²Π°, ΠΊΠΎΡΠΎΡΠ΅ ΡΡΠΎΠΊΠΈ ΠΏΠΎΠ΄Π³ΠΎΡΠΎΠ²ΠΊΠΈ ΠΊ ΠΏΡΠΎΠΈΠ·Π²ΠΎΠ΄ΡΡΠ²Π΅Π½Π½ΠΎΠΌΡ ΠΏΡΠΎΡΠ΅ΡΡΡ; ΡΠ°Π±ΠΎΡΠΈΠ΅ Ρ ΠΌΠ½ΠΎΠ³ΠΎΠΏΡΠΎΡΠΈΠ»ΡΠ½ΠΎΠΉ ΠΊΠ²Π°Π»ΠΈΡΠΈΠΊΠ°ΡΠΈΠ΅ΠΉ, ΠΊΠΎΡΠΎΡΡΠ΅ ΠΌΠΎΠ³ΡΡ ΠΏΠΎΠΌΠΎΡΡ ΠΈΠ»ΠΈ Π·Π°ΠΌΠ΅Π½ΠΈΡΡ Π΄ΡΡΠ³ Π΄ΡΡΠ³Π°.
- ΠΠΎΠ²ΡΡΠ΅Π½Π½ΡΠΉ ΡΡΠΎΠ²Π΅Π½Ρ ΠΏΡΠΎΠΈΠ·Π²ΠΎΠ΄ΠΈΡΠ΅Π»ΡΠ½ΠΎΡΡΠΈ ΠΈ ΠΈΡΠΏΠΎΠ»ΡΠ·ΠΎΠ²Π°Π½ΠΈΡ ΠΎΠ±ΠΎΡΡΠ΄ΠΎΠ²Π°Π½ΠΈΡ.
- Π£ΡΠ°ΡΡΠΈΠ΅ ΡΠ°Π±ΠΎΡΠΈΡ Π² ΡΠ΅ΡΠ΅Π½ΠΈΠΈ ΠΏΡΠΎΠ±Π»Π΅ΠΌ.
- ΠΠ΅ΠΎΠ±Ρ ΠΎΠ΄ΠΈΠΌΠΎΡΡΡ Ρ ΠΎΡΠΎΡΠΈΡ ΠΎΡΠ½ΠΎΡΠ΅Π½ΠΈΠΉ Ρ ΠΏΠΎΡΡΠ°Π²ΡΠΈΠΊΠ°ΠΌΠΈ.
- ΠΠ΅Π½ΡΡΠ΅ Π½Π΅ΠΎΠ±Ρ ΠΎΠ΄ΠΈΠΌΠΎΡΡΠΈ Π² Π½Π΅ΠΏΡΠΎΠΈΠ·Π²ΠΎΠ΄ΡΡΠ²Π΅Π½Π½ΡΡ ΡΠ°Π±ΠΎΡΠ°Ρ , Π½Π°ΠΏΡΠΈΠΌΠ΅Ρ, ΡΠΊΠ»Π°Π΄ΠΈΡΠΎΠ²Π°Π½ΠΈΠΈ ΠΈ ΠΏΠ΅ΡΠ΅ΠΌΠ΅ΡΠ΅Π½ΠΈΠΈ ΠΌΠ°ΡΠ΅ΡΠΈΠ°Π»ΠΎΠ².
Β
Π‘ΠΈΡΡΠ΅ΠΌΠ° Β«ΡΠΎΡΠ½ΠΎ-Π²-ΡΡΠΎΠΊΒ» β ΡΡΠΎ ΡΠΈΡΡΠ΅ΠΌΠ°, ΠΊΠΎΡΠΎΡΠ°Ρ ΠΏΡΠΈΠΌΠ΅Π½ΡΠ΅ΡΡΡ ΠΏΡΠ΅ΠΈΠΌΡΡΠ΅ΡΡΠ²Π΅Π½Π½ΠΎ Π² ΡΠ΅ΡΠΈΠΉΠ½ΠΎΠΌ ΠΏΡΠΎΠΈΠ·Π²ΠΎΠ΄ΡΡΠ²Π΅. Π ΡΠ°ΠΊΠΎΠΉ ΡΠΈΡΡΠ΅ΠΌΠ΅ ΡΠΎΠ²Π°ΡΡ ΠΏΠ΅ΡΠ΅ΠΌΠ΅ΡΠ°ΡΡΡΡ ΡΠ΅ΡΠ΅Π· ΡΠΈΡΡΠ΅ΠΌΡ ΠΈ Π·Π°Π΄Π°Π½ΠΈΠ΅ Π²ΡΠΏΠΎΠ»Π½ΡΠ΅ΡΡΡ Π² ΡΠΎΡΠ½ΠΎΠΌ ΡΠΎΠΎΡΠ²Π΅ΡΡΡΠ²ΠΈΠΈ Ρ Π³ΡΠ°ΡΠΈΠΊΠΎΠΌ. Β«Π’ΠΎΡΠ½ΠΎΡΡΠΎΡΠ½ΡΠ΅Β» ΡΠΈΡΡΠ΅ΠΌΡ ΡΡΠ΅Π±ΡΡΡ ΠΎΡΠ΅Π½Ρ Π½Π΅Π±ΠΎΠ»ΡΡΠΈΡ ΠΌΠ°ΡΠ΅ΡΠΈΠ°Π»ΡΠ½ΡΡ Π·Π°ΠΏΠ°ΡΠΎΠ², ΠΏΠΎΡΠΊΠΎΠ»ΡΠΊΡ ΠΏΠΎΡΠ»Π΅Π΄ΠΎΠ²Π°ΡΠ΅Π»ΡΠ½ΡΠ΅ ΠΎΠΏΠ΅ΡΠ°ΡΠΈΠΈ ΠΆΠ΅ΡΡΠΊΠΎ ΡΠΊΠΎΠΎΡΠ΄ΠΈΠ½ΠΈΡΠΎΠ²Π°Π½Ρ.
ΠΠΎΠ½Π΅ΡΠ½ΠΎΠΉ ΡΠ΅Π»ΡΡ JIT ΡΠ²Π»ΡΠ΅ΡΡΡ ΡΠ±Π°Π»Π°Π½ΡΠΈΡΠΎΠ²Π°Π½Π½ΡΠΉ, ΠΏΠ»Π°Π²Π½ΡΠΉ ΠΏΠΎΡΠΎΠΊ ΠΏΡΠΎΠΈΠ·Π²ΠΎΠ΄ΡΡΠ²Π°. ΠΡΠΏΠΎΠΌΠΎΠ³Π°ΡΠ΅Π»ΡΠ½ΡΠ΅ ΡΠ΅Π»ΠΈ: ΡΡΡΡΠ°Π½Π΅Π½ΠΈΠ΅ Π½Π°ΡΡΡΠ΅Π½ΠΈΠΉ Π² ΡΠΈΡΡΠ΅ΠΌΠ΅, ΠΎΠ±Π΅ΡΠΏΠ΅ΡΠ΅Π½ΠΈΠ΅ Π³ΠΈΠ±ΠΊΠΎΡΡΠΈ ΡΠΈΡΡΠ΅ΠΌΡ, ΡΠΎΠΊΡΠ°ΡΠ΅Π½ΠΈΠ΅ Π²ΡΠ΅ΠΌΠ΅Π½ΠΈ ΠΎΡΠ½Π°ΡΠ΅Π½ΠΈΡ ΠΈ ΡΡΠΎΠΊΠΎΠ² ΠΏΡΠΎΠΈΠ·Π²ΠΎΠ΄ΡΡΠ²Π°, ΠΈΡΠΊΠ»ΡΡΠ΅Π½ΠΈΠ΅ Π½Π΅ΠΏΡΠΎΠΈΠ·Π²ΠΎΠ΄ΠΈΡΠ΅Π»ΡΠ½ΡΡ ΡΠ°ΡΡ ΠΎΠ΄ΠΎΠ², ΠΈ ΠΌΠΈΠ½ΠΈΠΌΠΈΠ·Π°ΡΠΈΡ ΠΌΠ°ΡΠ΅ΡΠΈΠ°Π»ΡΠ½ΡΡ Π·Π°ΠΏΠ°ΡΠΎΠ². Π€ΠΎΡΠΌΠΈΡΡΡΡΠΈΠ΅ Π±Π»ΠΎΠΊΠΈ Β«ΡΠΎΡΠ½ΠΎΡΡΠΎΡΠ½ΠΎΠΉΒ» ΡΠΈΡΡΠ΅ΠΌΡ β ΡΠ°Π·ΡΠ°Π±ΠΎΡΠΊΠ° ΠΈΠ·Π΄Π΅Π»ΠΈΡ, ΡΠ°Π·ΡΠ°Π±ΠΎΡΠΊΠ° ΠΏΡΠΎΡΠ΅ΡΡΠ°, ΠΊΠ°Π΄ΡΠΎΠ²ΡΠ΅ ΠΈ ΠΎΡΠ³Π°Π½ΠΈΠ·Π°ΡΠΈΠΎΠ½Π½ΡΠ΅ Π²ΠΎΠΏΡΠΎΡΡ, ΠΏΠ»Π°Π½ΠΈΡΠΎΠ²Π°Π½ΠΈΠ΅ ΠΈ ΡΠΏΡΠ°Π²Π»Π΅Π½ΠΈΠ΅ ΠΏΡΠΎΠΈΠ·Π²ΠΎΠ΄ΡΡΠ²ΠΎΠΌ.
Π’Π°ΠΊΠΎΠ΅ ΠΏΡΠΎΠΈΠ·Π²ΠΎΠ΄ΡΡΠ²ΠΎ ΡΡΠ΅Π±ΡΠ΅Ρ ΠΈΡΠΊΠ»ΡΡΠ΅Π½ΠΈΡ Π²ΡΠ΅Ρ Π²ΠΎΠ·ΠΌΠΎΠΆΠ½ΡΡ ΠΈΡΡΠΎΡΠ½ΠΈΠΊΠΎΠ² Π½Π°ΡΡΡΠ΅Π½ΠΈΡ ΠΏΠ»Π°Π²Π½ΠΎΠ³ΠΎ ΠΏΠΎΡΠΎΠΊΠ° ΡΠ°Π±ΠΎΡ. ΠΡΡΠΎΠΊΠΎΠ΅ ΠΊΠ°ΡΠ΅ΡΡΠ²ΠΎ Π½Π΅ΠΎΠ±Ρ ΠΎΠ΄ΠΈΠΌΠΎ, ΠΏΠΎΡΠΎΠΌΡ ΡΡΠΎ ΠΏΡΠΎΠ±Π»Π΅ΠΌΡ Ρ ΠΊΠ°ΡΠ΅ΡΡΠ²ΠΎΠΌ ΠΌΠΎΠ³ΡΡ Π½Π°ΡΡΡΠΈΡΡ ΠΏΡΠΎΡΠ΅ΡΡ. ΠΡΠΎΠΌΠ΅ ΡΠΎΠ³ΠΎ, ΡΠ΅ΡΠ΅Π½ΠΈΠ΅ ΠΏΡΠΎΠ±Π»Π΅ΠΌ Π½Π°ΡΠ΅Π»Π΅Π½ΠΎ Π½Π° ΡΡΡΡΠ°Π½Π΅Π½ΠΈΠ΅ Π²ΡΠ΅Ρ Π½Π°ΡΡΡΠ΅Π½ΠΈΠΉ ΠΏΡΠΎΠΈΠ·Π²ΠΎΠ΄ΡΡΠ²Π΅Π½Π½ΠΎΠ³ΠΎ ΠΏΡΠΎΡΠ΅ΡΡΠ° ΠΈ ΠΏΡΠΈΠ΄Π°Π½ΠΈΠ΅ ΡΠΈΡΡΠ΅ΠΌΠ΅ Π±ΠΎΠ»ΡΡΠ΅ΠΉ ΡΡΡΠ΅ΠΊΡΠΈΠ²Π½ΠΎΡΡΠΈ ΠΈ Π½Π΅ΠΏΡΠ΅ΡΡΠ²Π½ΠΎΠ³ΠΎ ΡΡΠΎΠ²Π΅ΡΡΠ΅Π½ΡΡΠ²ΠΎΠ²Π°Π½ΠΈΡ.
ΠΠ»ΡΡΠ΅Π²ΠΎΠ΅ ΠΏΡΠ΅ΠΈΠΌΡΡΠ΅ΡΡΠ²ΠΎ Β«ΡΠΎΡΠ½ΠΎΡΡΠΎΡΠ½ΡΡ Β» ΡΠΈΡΡΠ΅ΠΌ β ΠΏΠΎΠ½ΠΈΠΆΠ΅Π½Π½ΡΠΉ ΡΡΠΎΠ²Π΅Π½Ρ Π·Π°ΠΏΠ°ΡΠΎΠ², Π²ΡΡΠΎΠΊΠΎΠ΅ ΠΊΠ°ΡΠ΅ΡΡΠ²ΠΎ, Π³ΠΈΠ±ΠΊΠΎΡΡΡ, ΡΠΎΠΊΡΠ°ΡΠ΅Π½ΠΈΠ΅ ΡΡΠΎΠΊΠΎΠ² ΠΏΡΠΎΠΈΠ·Π²ΠΎΠ΄ΡΡΠ²Π°, ΠΏΠΎΠ²ΡΡΠ΅Π½ΠΈΠ΅ ΠΏΡΠΎΠΈΠ·Π²ΠΎΠ΄ΠΈΡΠ΅Π»ΡΠ½ΠΎΡΡΠΈ ΠΈ ΡΡΡΠ΅ΠΊΡΠΈΠ²Π½ΠΎΡΡΠΈ ΠΈΡΠΏΠΎΠ»ΡΠ·ΠΎΠ²Π°Π½ΠΈΡ ΠΎΠ±ΠΎΡΡΠ΄ΠΎΠ²Π°Π½ΠΈΡ, ΡΠ½ΠΈΠΆΠ΅Π½ΠΈΠ΅ ΠΎΠ±ΡΠ΅ΠΌΠ° Π±ΡΠ°ΠΊΠ° ΠΈ ΠΏΠ΅ΡΠ΅ΡΠ°Π±ΠΎΡΠΎΠΊ, Π° ΡΠ°ΠΊΠΆΠ΅ ΡΠΌΠ΅Π½ΡΡΠ΅Π½Π½ΡΠ΅ ΡΡΠ΅Π±ΠΎΠ²Π°Π½ΠΈΡ ΠΊ ΠΏΠ»ΠΎΡΠ°Π΄ΡΠΌ.
Β
Π’ΠΎΠ»ΡΠΊΠΎ ΠΏΡΠ°ΠΊΡΠΈΡΠ΅ΡΠΊΠΈΠ΅ ΡΠΎΠ²ΡΠ΅ΠΌΠ΅Π½Π½ΡΠ΅ Π·Π½Π°Π½ΠΈΡ ΠΈ Π½Π°Π²ΡΠΊΠΈ. ΠΠ·ΡΡΠΈΡΠ΅ ΡΡΠΈ ΠΏΡΠ°ΠΊΡΠΈΡΠ΅ΡΠΊΠΈΠ΅ ΠΊΡΡΡΡ ΠΏΠΎ ΠΌΠ΅Π½Π΅Π΄ΠΆΠΌΠ΅Π½ΡΡ ΠΈ ΡΠΏΡΠ°Π²Π»Π΅Π½ΠΈΡ ΠΈΠ»ΠΈ ΡΡΠΈΡΠ΅ΡΡ ΠΏΠΎ Π°Π±ΠΎΠ½Π΅ΠΌΠ΅Π½ΡΡ, ΡΠΎ ΡΠΊΠΈΠ΄ΠΊΠΎΠΉ.
www.elitarium.ru
ΠΠ²Π΅Π΄Π΅Π½ΠΈΠ΅ Π² Π±Π΅ΡΠ΅ΠΆΠ»ΠΈΠ²ΠΎΠ΅ ΠΏΡΠΎΠΈΠ·Π²ΠΎΠ΄ΡΡΠ²ΠΎ
ΠΠ²Π΅Π΄Π΅Π½ΠΈΠ΅
Lean Production — ΠΏΡΠΎΠΈΠ·Π²ΠΎΠ΄ΡΡΠ²ΠΎ Π±Π΅Π· ΠΏΠΎΡΠ΅ΡΡ.
ΠΡΠΎΠΈΠ·Π²ΠΎΠ΄ΡΡΠ²Π΅Π½Π½Π°Ρ ΡΠΈΡΡΠ΅ΠΌΠ° Π’ΠΎΠΉΠΎΡΡ
(Toyota Production System, TPS)
ΠΡΠ΅Π΄ΡΠ΅ΡΡΠ²Π΅Π½Π½ΠΈΡΠ΅ΠΉ Lean Π±ΡΠ»Π° ΠΡΠΎΠΈΠ·Π²ΠΎΠ΄ΡΡΠ²Π΅Π½Π½Π°Ρ ΡΠΈΡΡΠ΅ΠΌΠ° Π’ΠΎΠΉΠΎΡΡ, ΠΏΡΠΈΡΠ΅Π΄ΡΠ°Ρ Π½Π° ΡΠΌΠ΅Π½Ρ ΠΌΠ°ΡΡΠΎΠ²ΠΎΠΌΡ ΠΏΡΠΎΠΈΠ·Π²ΠΎΠ΄ΡΡΠ²Ρ.
ΠΠ°Π·ΠΎΠ²ΡΠ΅ ΠΏΡΠΈΠ½ΡΠΈΠΏΡ TPS
- Π’ΠΎΡΠ½ΠΎ Π²ΠΎΠ²ΡΠ΅ΠΌΡ (Just-in-time, JIT) ΠΠ΅Π»Π°ΡΡ ΡΠΎΠ»ΡΠΊΠΎ ΡΠΎ, ΡΡΠΎ Π½ΡΠΆΠ½ΠΎ, ΠΊΠΎΠ³Π΄Π° Π½ΡΠΆΠ½ΠΎ ΠΈ ΡΠΊΠΎΠ»ΡΠΊΠΎ Π½ΡΠΆΠ½ΠΎ.
- ΠΠ·ΠΈΠ΄ΠΎΠΊΠ° (Jidoka) ΠΈΠ»ΠΈ ΠΠ²ΡΠΎΠ½ΠΎΠΌΠΈΠ·Π°ΡΠΈΡ (Autonomation) ΠΠ½ΡΠ΅Π»Π»Π΅ΠΊΡΡΠ°Π»ΡΠ½Π°Ρ Π°Π²ΡΠΎΠΌΠ°ΡΠΈΠ·Π°ΡΠΈΡ: ΠΌΠ°ΡΠΈΠ½Π° Π°Π²ΡΠΎΠΌΠ°ΡΠΈΡΠ΅ΡΠΊΠΈ ΠΎΡΠΊΠ»ΡΡΠ°Π΅ΡΡΡ, Π΅ΡΠ»ΠΈ ΠΏΠΎΠ½ΠΈΠΌΠ°Π΅Ρ, ΡΡΠΎ Π½Π°ΡΠΈΠ½Π°Π΅Ρ Π³Π½Π°ΡΡ Π±ΡΠ°ΠΊ.
ΠΠ΄Π½ΠΈΠΌ ΠΈΠ· ΡΠ»Π΅ΠΌΠ΅Π½ΡΠΎΠ² ΠΠ²ΡΠΎΠ½ΠΎΠΌΠΈΠ·Π°ΡΠΈΠΈ ΡΠ²Π»ΡΠ΅ΡΡΡ ΠΠ½Π΄ΠΎΠ½ (Andon) β ΡΠΈΡΡΠ΅ΠΌΠ° Π²ΠΈΠ·ΡΠ°Π»ΡΠ½ΠΎΠ³ΠΎ ΠΈ Π·Π²ΡΠΊΠΎΠ²ΠΎΠ³ΠΎ ΠΎΠΏΠΎΠ²Π΅ΡΠ΅Π½ΠΈΡ ΠΏΠ΅ΡΡΠΎΠ½Π°Π»Π° ΠΎ ΠΏΡΠΎΠ±Π»Π΅ΠΌΠ°Ρ Ρ ΠΊΠ°ΡΠ΅ΡΡΠ²ΠΎΠΌ ΠΈ Π½Π΅ΠΈΡΠΏΡΠ°Π²Π½ΠΎΡΡΡΡ ΠΎΠ±ΠΎΡΡΠ΄ΠΎΠ²Π°Π½ΠΈΡ.
ΠΠΎΡΠ΅ΡΠΈ
ΠΠΎΡΠ΅ΡΠΈ (Muda) β ΡΡΠΎ Π΄Π΅ΠΉΡΡΠ²ΠΈΡ, ΠΊΠΎΡΠΎΡΡΠ΅ ΠΏΡΠΈΠ²ΠΎΠ΄ΡΡ ΠΊ ΡΠ²Π΅Π»ΠΈΡΠ΅Π½ΠΈΡ ΡΠ΅Π±Π΅ΡΡΠΎΠΈΠΌΠΎΡΡΠΈ ΠΏΡΠΎΠ΄ΡΠΊΡΠΈΠΈ, Π½ΠΎ Π½Π΅ ΡΠ²Π΅Π»ΠΈΡΠΈΠ²Π°ΡΡ Π΅Ρ ΡΠ΅Π½Π½ΠΎΡΡΡ Π² Π³Π»Π°Π·Π°Ρ ΠΏΠΎΡΡΠ΅Π±ΠΈΡΠ΅Π»Ρ.
ΠΠ²Π° ΡΠΈΠΏΠ° ΠΏΠΎΡΠ΅ΡΡ
- ΠΠΎΡΠ΅ΡΠΈ, ΠΊΠΎΡΠΎΡΡΠ΅ Π½Π΅ΠΈΠ·Π±Π΅ΠΆΠ½Ρ ΠΈ Π½Π΅ΠΎΠ±Ρ ΠΎΠ΄ΠΈΠΌΡ Π΄Π»Ρ ΠΏΡΠΎΠΈΠ·Π²ΠΎΠ΄ΡΡΠ²Π΅Π½Π½ΠΎΠ³ΠΎ ΠΏΡΠΎΡΠ΅ΡΡΠ°.
- ΠΠΎΡΠ΅ΡΠΈ, ΠΎΡ ΠΊΠΎΡΠΎΡΡΡ ΠΌΠΎΠΆΠ½ΠΎ ΠΈ Π½ΡΠΆΠ½ΠΎ ΠΈΠ·Π±Π°Π²ΠΈΡΡΡΡ.
ΠΡΡΠΎΡΠ½ΠΈΠΊΠΈ ΠΏΠΎΡΠ΅ΡΡ
- Π’ΡΠ°Π½ΡΠΏΠΎΡΡΠΈΡΠΎΠ²ΠΊΠ° (ΡΠΈΡΠΊΠΈ ΠΏΠΎΠ²ΡΠ΅ΠΆΠ΄Π΅Π½ΠΈΡ, ΡΡΠ΅ΡΠΈ, Π·Π°Π΄Π΅ΡΠΆΠΊΠΈ)
- ΠΠ΅ΡΠ΅ΠΏΡΠΎΠΈΠ·Π²ΠΎΠ΄ΡΡΠ²ΠΎ (ΠΏΡΠΎΠΈΠ·Π²ΠΎΠ΄ΡΡΠ²ΠΎ ΠΎΠΏΠ΅ΡΠ΅ΠΆΠ°Π΅Ρ ΡΠΏΡΠΎΡ)
- ΠΠΆΠΈΠ΄Π°Π½ΠΈΠ΅ ΡΠ»Π΅Π΄ΡΡΡΠ΅Π³ΠΎ ΡΡΠ°ΠΏΠ° ΠΎΠ±ΡΠ°Π±ΠΎΡΠΊΠΈ ΠΈΠ»ΠΈ ΡΡΠ°Π½ΡΠΏΠΎΡΡΠΈΡΠΎΠ²ΠΊΠΈ
- ΠΠ²ΠΈΠΆΠ΅Π½ΠΈΠ΅ (ΠΏΠΎΠ²ΡΠ΅ΠΆΠ΄Π΅Π½ΠΈΠ΅ ΠΈ ΠΈΠ·Π½ΠΎΡ ΠΎΠ±ΠΎΡΡΠ΄ΠΎΠ²Π°Π½ΠΈΡ, ΡΡΠ°Π²ΠΌΠΈΡΠΎΠ²Π°Π½ΠΈΠ΅ ΠΏΠ΅ΡΡΠΎΠ½Π°Π»Π°)
- ΠΠ΅Π½ΡΠΆΠ½Π°Ρ ΠΎΠ±ΡΠ°Π±ΠΎΡΠΊΠ° (ΠΊΠΎΠ³Π΄Π° ΠΏΠΎΠΊΡΠΏΠ°ΡΠ΅Π»Ρ Π½Π΅ Ρ ΠΎΡΠ΅Ρ ΠΏΠ»Π°ΡΠΈΡΡ Π·Π° Π½Π°Π²ΠΎΡΠΎΡΡ)
- ΠΠ°ΠΏΠ°ΡΡ ΡΡΡΡΡ, Π½Π΅Π·Π°Π²Π΅ΡΡΡΠ½Π½ΠΎΠ³ΠΎ ΠΏΡΠΎΠΈΠ·Π²ΠΎΠ΄ΡΡΠ²Π° ΠΈ Π³ΠΎΡΠΎΠ²ΠΎΠΉ ΠΏΡΠΎΠ΄ΡΠΊΡΠΈΠΈ (Π·Π°ΠΌΠΎΡΠ°ΠΆΠΈΠ²Π°Π½ΠΈΠ΅ ΠΊΠ°ΠΏΠΈΡΠ°Π»Π°)
- ΠΡΠ°ΠΊ, ΠΎΡΡ ΠΎΠ΄Ρ
- ΠΠ΅ΡΠ°Π²Π½ΠΎΠΌΠ΅ΡΠ½ΠΎΡΡΡ Π·Π°Π³ΡΡΠ·ΠΊΠΈ ΠΎΠ±ΠΎΡΡΠ΄ΠΎΠ²Π°Π½ΠΈΡ ΠΈΠ»ΠΈ ΡΠ°Π±ΠΎΡΠΈΡ Π² ΡΠ΅ΡΠ΅Π½ΠΈΠ΅ ΡΠΌΠ΅Π½Ρ.
- ΠΠ΅ΡΠ΅Π³ΡΡΠ·ΠΊΠ° ΠΎΠ±ΠΎΡΡΠ΄ΠΎΠ²Π°Π½ΠΈΡ ΠΈΠ»ΠΈ ΡΠ°Π±ΠΎΡΠΈΡ .
ΠΠ°ΠΉΠΊΠ°ΠΊΡ
ΠΠΎΠ½ΡΠ΅ΠΏΡΠΈΡ ΡΠ°Π΄ΠΈΠΊΠ°Π»ΡΠ½ΠΎΠ³ΠΎ ΡΡΠΎΠ²Π΅ΡΡΠ΅Π½ΡΡΠ²ΠΎΠ²Π°Π½ΠΈΡ ΠΠ°ΠΉΠΊΠ°ΠΊΡ (Kaikaku) ΠΏΠΎΠΌΠΎΠ³Π°Π΅Ρ ΠΈΠ΄Π΅Π½ΡΠΈΡΠΈΡΠΈΡΠΎΠ²Π°ΡΡ Π΄Π΅ΠΉΡΡΠ²ΠΈΡ, ΠΊΠΎΡΠΎΡΡΠ΅ ΠΏΡΠΈΠ²ΠΎΠ΄ΡΡ ΠΊ ΠΏΠΎΡΠ΅ΡΡΠΌ Π²ΡΠΎΡΠΎΠ³ΠΎ ΡΠΈΠΏΠ°, ΠΈ ΠΈΠ·Π±Π°Π²ΠΈΡΡΡΡ ΠΎΡ Π½ΠΈΡ .
ΠΠ°ΠΉΠ΄Π·Π΅Π½
ΠΠΎΠ½ΡΠ΅ΠΏΡΠΈΡ ΡΠ²ΠΎΠ»ΡΡΠΈΠΎΠ½Π½ΠΎΠ³ΠΎ ΡΠ»ΡΡΡΠ΅Π½ΠΈΡ Π±ΠΈΠ·Π½Π΅Ρ-ΠΎΠΏΠ΅ΡΠ°ΡΠΈΠΉ ΠΠ°ΠΉΠ΄Π·Π΅Π½ (Kaizen) ΠΏΠΎΠΌΠΎΠ³Π°Π΅Ρ Π½Π΅ΠΏΡΠ΅ΡΡΠ²Π½ΠΎ ΡΠΎΠ²Π΅ΡΡΠ΅Π½ΡΡΠ²ΠΎΠ²Π°ΡΡ ΡΠ΅ΠΏΠΎΡΠΊΠΈ ΡΠΎΠ·Π΄Π°Π½ΠΈΡ ΡΠ΅Π½Π½ΠΎΡΡΠΈ.
5S
Π‘ΠΈΡΡΠ΅ΠΌΠ° 5S ΠΏΠΎΠΌΠΎΠ³Π°Π΅Ρ Π½Π°Π²Π΅ΡΡΠΈ ΠΏΠΎΡΡΠ΄ΠΎΠΊ Π½Π° ΡΠ°Π±ΠΎΡΠΈΡ ΠΌΠ΅ΡΡΠ°Ρ , ΠΏΠΎΠ²ΡΡΠΈΡΡ ΠΏΡΠΎΠΈΠ·Π²ΠΎΠ΄ΠΈΡΠ΅Π»ΡΠ½ΠΎΡΡΡ ΠΈ Π±Π΅Π·ΠΎΠΏΠ°ΡΠ½ΠΎΡΡΡ ΡΡΡΠ΄Π°.
1 | Sort | ΠΡΡΠΎΡΡΠΈΡΡΠΉΡΠ΅ Π²ΡΠ΅ ΠΏΡΠ΅Π΄ΠΌΠ΅ΡΡ ΠΏΠΎ Π½Π°Π·Π½Π°ΡΠ΅Π½ΠΈΡ, Π²ΡΠ±ΡΠΎΡΡΡΠ΅ Π²ΡΡ Π»ΠΈΡΠ½Π΅Π΅ |
2 | Set in Order | ΠΠ°ΠΆΠ΄ΡΠΉ ΠΏΡΠ΅Π΄ΠΌΠ΅Ρ Π΄ΠΎΠ»ΠΆΠ΅Π½ Ρ ΡΠ°Π½ΠΈΡΡΡΡ Π½Π° ΡΠ²ΠΎΡΠΌ ΠΌΠ΅ΡΡΠ΅, ΡΡΠΎΠ±Ρ Π΅Π³ΠΎ Π»Π΅Π³ΠΊΠΎ ΠΌΠΎΠΆΠ½ΠΎ Π±ΡΠ»ΠΎ Π½Π°ΠΉΡΠΈ |
3 | Shine | Π‘ΠΎΠ΄Π΅ΡΠΆΠΈΡΠ΅ Π² ΡΠΈΡΡΠΎΡΠ΅ ΠΈΠ½ΡΡΡΡΠΌΠ΅Π½Ρ ΠΈ ΡΠ°Π±ΠΎΡΠ΅Π΅ ΠΏΡΠΎΡΡΡΠ°Π½ΡΡΠ²ΠΎ |
4 | Standardize | Π‘ΡΠ°Π½Π΄Π°ΡΡΠΈΠ·ΠΈΡΡΠΉΡΠ΅ ΠΏΡΠΎΡΠ΅ΡΡ ΠΏΠΎΠ΄Π΄Π΅ΡΠΆΠ°Π½ΠΈΡ ΠΏΠΎΡΡΠ΄ΠΊΠ° ΠΈ ΡΠΈΡΡΠΎΡΡ |
5 | Sustain | Π‘ΠΎΠ²Π΅ΡΡΠ΅Π½ΡΡΠ²ΡΠΉΡΠ΅ ΡΠΈΡΡΠ΅ΠΌΡ. |
ΠΡΡΡΠ³ΠΈΠ²Π°Π½ΠΈΠ΅ Π²ΠΌΠ΅ΡΡΠΎ ΠΏΡΠΎΡΠ°Π»ΠΊΠΈΠ²Π°Π½ΠΈΡ
Π Π°Π±ΠΎΡΠ° Π½Π° ΠΊΠ°ΠΆΠ΄ΠΎΠΌ ΡΡΠ°ΠΏΠ΅ Π½Π°ΡΠΈΠ½Π°Π΅ΡΡΡ ΡΠΎΠ»ΡΠΊΠΎ ΠΏΠΎ ΡΠΈΠ³Π½Π°Π»Ρ ΠΎΡ ΡΠ»Π΅Π΄ΡΡΡΠ΅Π³ΠΎ ΡΡΠ°ΠΏΠ° Π² ΡΠ΅ΠΏΠΎΡΠΊΠ΅ ΡΠΎΠ·Π΄Π°Π½ΠΈΡ ΡΠ΅Π½Π½ΠΎΡΡΠΈ. ΠΠ΅ΡΠ²ΡΠΌ ΡΠ°ΠΊΠΈΠΌ ΡΠΈΠ³Π½Π°Π»ΠΎΠΌ ΡΠ²Π»ΡΠ΅ΡΡΡ ΡΠ΅Π°Π»ΡΠ½ΡΠΉ Π·Π°ΠΊΠ°Π· ΠΏΠΎΠΊΡΠΏΠ°ΡΠ΅Π»Ρ β ΠΈΠΌΠ΅Π½Π½ΠΎ ΡΠΏΡΠΎΡ ΡΠΏΡΠ°Π²Π»ΡΠ΅Ρ Π±Π΅ΡΠ΅ΠΆΠ»ΠΈΠ²ΡΠΌ ΠΏΡΠΎΠΈΠ·Π²ΠΎΠ΄ΡΡΠ²ΠΎΠΌ.
Π ΠΌΠ°ΡΡΠΎΠ²ΠΎΠΌ ΠΏΡΠΎΠΈΠ·Π²ΠΎΠ΄ΡΡΠ²Π΅ ΠΏΡΠΎΠ΄ΡΠΊΡΠΈΡ ΠΏΡΠΎΡΠ°Π»ΠΊΠΈΠ²Π°Π΅ΡΡΡ ΠΊ ΠΏΠΎΡΡΠ΅Π±ΠΈΡΠ΅Π»Ρ, ΠΏΡΠΎΠΈΠ·Π²ΠΎΠ΄ΡΡΠ²ΠΎ ΡΠ°Π±ΠΎΡΠ°Π΅Ρ Π½Π° ΡΠΊΠ»Π°Π΄.
ΠΠ΅ΡΠΎΠ΄ ΠΠ°Π½Π±Π°Π½ (Kanban) ΠΏΡΠΈΠΌΠ΅Π½ΡΡΡ Π΄Π»Ρ ΡΠ΅Π°Π»ΠΈΠ·Π°ΡΠΈΠΈ ΠΊΠΎΠ½ΡΠ΅ΠΏΡΠΈΠΈ Π²ΡΡΡΠ³ΠΈΠ²Π°Π½ΠΈΡ. Π‘ΠΈΠ³Π½Π°Π»ΠΎΠΌ Π΄Π»Ρ Π½Π°ΡΠ°Π»Π° ΡΠ°Π±ΠΎΡΡ ΡΠ°Π±ΠΎΡΠ΅Π³ΠΎ ΡΠ΅Π½ΡΡΠ° ΡΠ»ΡΠΆΠΈΡ ΡΠ»Π΅ΠΊΡΡΠΎΠ½Π½ΠΎΠ΅ ΡΠΎΠΎΠ±ΡΠ΅Π½ΠΈΠ΅, ΠΊΠ°ΡΡΠΎΡΠΊΠ° ΠΈΠ»ΠΈ ΠΏΡΡΡΠΎΠΉ ΡΡΠΈΠΊ, ΠΊΠΎΡΠΎΡΡΠΉ Π²Π΅ΡΠ½ΡΠ»ΡΡ ΠΎΡ ΡΠ»Π΅Π΄ΡΡΡΠ΅Π³ΠΎ ΠΏΠΎ ΡΠ΅ΠΏΠΎΡΠΊΠ΅ ΡΠ°Π±ΠΎΡΠ΅Π³ΠΎ ΡΠ΅Π½ΡΡΠ°.
Π‘ΠΈΡΡΠ΅ΠΌΠ° Π±ΡΡΡΡΠΎΠΉ ΠΏΠ΅ΡΠ΅Π½Π°Π»Π°Π΄ΠΊΠΈ (Single-Minute Exchange of Dies, SMED) ΠΏΠΎΠ·Π²ΠΎΠ»ΡΠ΅Ρ Π±Π΅Π· Π·Π°Π΄Π΅ΡΠΆΠ΅ΠΊ Π°Π΄Π°ΠΏΡΠΈΡΠΎΠ²Π°ΡΡ Π»ΠΈΠ½ΠΈΡ Π½Π° Π²ΡΠΏΡΡΠΊ Π΄ΡΡΠ³ΠΎΠ³ΠΎ Π²ΠΈΠ΄Π° ΠΏΡΠΎΠ΄ΡΠΊΡΠΈΠΈ, Ρ.Β Π΅. ΠΎΡΠ³Π°Π½ΠΈΠ·ΠΎΠ²Π°ΡΡ ΠΏΡΠΎΠΈΠ·Π²ΠΎΠ΄ΡΡΠ²ΠΎ ΠΌΠ΅Π»ΠΊΠΈΠΌΠΈ ΠΏΠ°ΡΡΠΈΡΠΌΠΈ.
ΠΡΡΠ°Π²Π½ΠΈΠ²Π°Π½ΠΈΠ΅ ΠΏΠΎΡΠΎΡΠ½ΠΎΠ³ΠΎ ΠΏΡΠΎΠΈΠ·Π²ΠΎΠ΄ΡΡΠ²Π°
ΠΡΠ΅ΠΌΡ ΡΠ°ΠΊΡΠ° Ρ Π°ΡΠ°ΠΊΡΠ΅ΡΠΈΠ·ΡΠ΅Ρ ΡΠΊΠΎΡΠΎΡΡΡ ΡΠ°Π±ΠΎΡΡ ΠΏΡΠΎΠΈΠ·Π²ΠΎΠ΄ΡΡΠ²Π°. ΠΠ° ΠΎΠ΄ΠΈΠ½ ΡΠ°ΠΊΡ Π²ΡΠΏΡΡΠΊΠ°Π΅ΡΡΡ ΠΎΠ΄Π½ΠΎ ΠΈΠ·Π΄Π΅Π»ΠΈΠ΅. ΠΡΠ»ΠΈ Π²ΡΠ΅ΠΌΡ ΡΠΈΠΊΠ»Π° ΠΎΠ΄Π½ΠΎΠΉ ΠΎΠΏΠ΅ΡΠ°ΡΠΈΠΈ ΡΠ°Π²Π½ΠΎ Π²ΡΠ΅ΠΌΠ΅Π½ΠΈ ΡΠ°ΠΊΡΠ°, ΡΠΎ Π²ΠΎΠ·Π½ΠΈΠΊΠ°Π΅Ρ ΠΏΠΎΡΠΎΠΊ Π΅Π΄ΠΈΠ½ΠΈΡΠ½ΡΡ ΠΈΠ·Π΄Π΅Π»ΠΈΠΉ.
Π Π°Π·ΠΌΠ΅ΡΠ΅Π½ΠΈΠ΅ ΡΠ΅Ρ Π½ΠΎΠ»ΠΎΠ³ΠΈΡΠ΅ΡΠΊΠΎΠ³ΠΎ ΠΎΠ±ΠΎΡΡΠ΄ΠΎΠ²Π°Π½ΠΈΡ Π² Π»ΠΈΠ½ΠΈΡ, Π° Π½Π΅ ΠΏΠΎ ΡΡΠ½ΠΊΡΠΈΠΎΠ½Π°Π»ΡΠ½ΠΎΠΌΡ ΠΏΡΠΈΠ·Π½Π°ΠΊΡ (ΡΠΎΠΊΠ°ΡΠ½ΡΠΉ ΡΡΠ°ΡΡΠΎΠΊ, ΡΡΠ΅Π·Π΅ΡΠ½ΡΠΉ ΡΡΠ°ΡΡΠΎΠΊ ΠΈ Ρ.Β ΠΏ.) ΠΏΠΎΠ·Π²ΠΎΠ»ΡΠ΅Ρ ΡΠΎΠΊΡΠ°ΡΠΈΡΡ ΠΏΠΎΡΠ΅ΡΠΈ Π½Π° ΠΎΠΆΠΈΠ΄Π°Π½ΠΈΠ΅ ΠΈ ΡΡΠ°Π½ΡΠΏΠΎΡΡΠΈΡΠΎΠ²ΠΊΡ ΠΌΠ°ΡΠ΅ΡΠΈΠ°Π»ΠΎΠ² ΠΈ ΠΈΠ·Π΄Π΅Π»ΠΈΠΉ ΠΌΠ΅ΠΆΠ΄Ρ ΡΠ°Π±ΠΎΡΠΈΠΌΠΈ ΡΠ΅Π½ΡΡΠ°ΠΌΠΈ.
ΠΡΠ΅ΠΎΠ±ΡΠ΅Π΅ ΡΠΏΡΠ°Π²Π»Π΅Π½ΠΈΠ΅ ΠΊΠ°ΡΠ΅ΡΡΠ²ΠΎΠΌ
(Total Quality Management , TQM)
ΠΠΎΠ½ΡΠ΅ΠΏΡΠΈΡ Π²ΡΠ΅ΠΎΠ±ΡΠ΅ΠΉ Π²ΠΎΠ²Π»Π΅ΡΡΠ½Π½ΠΎΡΡΠΈ Π² ΡΠΏΡΠ°Π²Π»Π΅Π½ΠΈΠ΅ ΠΊΠ°ΡΠ΅ΡΡΠ²ΠΎΠΌ Π½Π° Π²ΡΠ΅Ρ
ΡΡΠ°ΠΏΠ°Ρ
ΠΆΠΈΠ·Π½Π΅Π½Π½ΠΎΠ³ΠΎ ΡΠΈΠΊΠ»Π° ΠΏΡΠΎΠ΄ΡΠΊΡΠ° ΠΎΡ ΡΠ°Π·ΡΠ°Π±ΠΎΡΠΊΠΈ Π΄ΠΎ ΡΡΠΈΠ»ΠΈΠ·Π°ΡΠΈΠΈ.
ΠΠ΅ ΡΠΎΠ²ΠΌΠ΅ΡΡΠΈΠΌΠ° Ρ Π°Π²ΡΠΎΡΠΈΡΠ°ΡΠ½ΡΠΌ ΡΡΠΈΠ»Π΅ΠΌ ΡΠΏΡΠ°Π²Π»Π΅Π½ΠΈΡ, ΠΎΡΠ½ΠΎΠ²ΡΠ²Π°Π΅ΡΡΡ Π½Π° Π΄ΠΎΠ²Π΅ΡΠΈΠΈ, Π΄Π΅Π»Π΅Π³ΠΈΡΠΎΠ²Π°Π½ΠΈΠΈ ΠΏΠΎΠ»Π½ΠΎΠΌΠΎΡΠΈΠΉ, Π½ΠΎΠ²Π°ΡΠΎΡΡΡΠ²Π΅ ΠΈ ΡΠ²ΠΎΡΡΠ΅ΡΠΊΠΎΠΌ ΠΏΠΎΠ΄Ρ
ΠΎΠ΄Π΅.
ΠΠ΅ΡΠΎΠ΄Ρ TQM
- Π‘ΡΠ°ΡΠΈΡΡΠΈΡΠ΅ΡΠΊΠΎΠ΅ ΡΠΏΡΠ°Π²Π»Π΅Π½ΠΈΠ΅ ΠΏΡΠΎΡΠ΅ΡΡΠΎΠΌ (Statistical Process Control, SPC)
- ΠΡΠ°Π²ΠΎ Π½Π° ΠΎΡΡΠ°Π½ΠΎΠ²ΠΊΡ Π»ΠΈΠ½ΠΈΠΈ — ΠΏΠΎΠ·Π²ΠΎΠ»ΡΠ΅Ρ ΡΠ°Π±ΠΎΡΠ΅ΠΌΡ ΠΎΡΡΠ°Π½ΠΎΠ²ΠΈΡΡ ΠΏΡΠΎΠΈΠ·Π²ΠΎΠ΄ΡΡΠ²ΠΎ ΠΏΡΠΈ ΠΎΡΠΊΠ»ΠΎΠ½Π΅Π½ΠΈΠΈ ΠΊΠ°ΡΠ΅ΡΡΠ²Π° ΠΎΡ Π·Π°Π΄Π°Π½Π½ΠΎΠ³ΠΎ ΡΡΠΎΠ²Π½Ρ.
- Π‘ΠΈΡΡΠ΅ΠΌΠ° Π·Π°ΡΠΈΡΡ ΠΎΡ Π΄ΡΡΠ°ΠΊΠ° (Poka-yoke) — ΠΏΠΎΠΌΠΎΠ³Π°Π΅Ρ ΠΈΠ·Π±Π°Π²ΠΈΡΡΡ ΠΎΡ ΠΎΡΠΈΠ±ΠΎΠΊ Ρ ΠΏΠΎΠΌΠΎΡΡΡ Π²ΡΡΡΠΎΠ΅Π½Π½ΡΡ ΡΠ΅Ρ Π½ΠΈΡΠ΅ΡΠΊΠΈΡ ΡΠ΅ΡΠ΅Π½ΠΈΠΉ.
- ΠΠΈΠ°Π³ΡΠ°ΠΌΠΌΡ ΠΡΠΈΠΊΠ°Π²Ρ β ΠΏΠΎΠ·Π²ΠΎΠ»ΡΡΡ ΠΈΡΡΠ»Π΅Π΄ΠΎΠ²Π°ΡΡ ΠΏΡΠΈΡΠΈΠ½Π½ΠΎ-ΡΠ»Π΅Π΄ΡΡΠ²Π΅Π½Π½ΡΠ΅ ΡΠ²ΡΠ·ΠΈ ΡΠ°ΠΊΡΠΎΡΠΎΠ², Π²Π»ΠΈΡΡΡΠΈΡ Π½Π° ΠΊΠ°ΡΠ΅ΡΡΠ²ΠΎ.
ΠΡΠ΅ΠΎΠ±ΡΠ΅Π΅ ΠΎΠ±ΡΠ»ΡΠΆΠΈΠ²Π°Π½ΠΈΠ΅ ΠΎΠ±ΠΎΡΡΠ΄ΠΎΠ²Π°Π½ΠΈΡ
(Total Productive Maintenance , TPM)
ΠΠΎΠ½ΡΠ΅ΠΏΡΠΈΡ Π²ΡΠ΅ΠΎΠ±ΡΠ΅ΠΉ Π²ΠΎΠ²Π»Π΅ΡΡΠ½Π½ΠΎΡΡΠΈ Π² ΠΎΠ±ΡΠ»ΡΠΆΠΈΠ²Π°Π½ΠΈΠ΅ ΠΎΠ±ΠΎΡΡΠ΄ΠΎΠ²Π°Π½ΠΈΡ Ρ ΡΠ΅Π»ΡΡ ΡΠ½ΠΈΠΆΠ΅Π½ΠΈΡ ΠΏΠΎΡΠ΅ΡΡ, ΡΠ²ΡΠ·Π°Π½Π½ΡΡ
Ρ ΠΏΡΠΎΡΡΠΎΡΠΌΠΈ, ΠΎΡΠΊΠ°Π·Π°ΠΌΠΈ, Π½ΠΈΠ·ΠΊΠΎΠΉ ΠΏΡΠΎΠΈΠ·Π²ΠΎΠ΄ΠΈΡΠ΅Π»ΡΠ½ΠΎΡΡΡΡ, Π±ΡΠ°ΠΊΠΎΠΌ.
ΠΠΎΠΊΠ°Π·Π°ΡΠ΅Π»Ρ ΠΎΠ±ΡΠ΅ΠΉ ΡΡΡΠ΅ΠΊΡΠΈΠ²Π½ΠΎΡΡΠΈ ΠΎΠ±ΠΎΡΡΠ΄ΠΎΠ²Π°Π½ΠΈΡ
(Overall Equipment Effectiveness, OEE)
OEE β ΠΈΠ½ΡΠ΅Π³ΡΠ°Π»ΡΠ½ΡΠΉ ΠΏΠΎΠΊΠ°Π·Π°ΡΠ΅Π»Ρ, ΡΡΠΈΡΡΠ²Π°ΡΡΠΈΠΉ ΠΏΠΎΡΠ΅ΡΠΈ ΡΠ²ΡΠ·Π°Π½Π½ΡΠ΅ Ρ ΠΏΡΠΎΡΡΠΎΡΠΌΠΈ, ΡΠ½ΠΈΠΆΠ΅Π½ΠΈΠ΅ΠΌ ΠΏΡΠΎΠΈΠ·Π²ΠΎΠ΄ΠΈΡΠ΅Π»ΡΠ½ΠΎΡΡΠΈ ΠΈ ΠΊΠ°ΡΠ΅ΡΡΠ²Π°.
OEE = ΠΠΎΡΠΎΠ²Π½ΠΎΡΡΡ * ΠΡΠΎΠΈΠ·Π²ΠΎΠ΄ΠΈΡΠ΅Π»ΡΠ½ΠΎΡΡΡ * ΠΠ°ΡΠ΅ΡΡΠ²ΠΎ
ΠΠΎΡΠΎΠ²Π½ΠΎΡΡΡ = Π€Π°ΠΊΡΠΈΡΠ΅ΡΠΊΠΎΠ΅ Π²ΡΠ΅ΠΌΡ ΡΠ°Π±ΠΎΡΡΒ / ΠΠ»Π°Π½ΠΎΠ²ΠΎΠ΅ Π²ΡΠ΅ΠΌΡ ΡΠ°Π±ΠΎΡΡ
Π€Π°ΠΊΡΠΈΡΠ΅ΡΠΊΠΎΠ΅ Π²ΡΠ΅ΠΌΡ ΡΠ°Π±ΠΎΡΡΒ = ΠΠ»Π°Π½ΠΎΠ²ΠΎΠ΅Β Π²ΡΠ΅ΠΌΡΒ ΡΠ°Π±ΠΎΡΡΒ β ΠΡΠ΅ΠΌΡΒ Π½Π΅Π·Π°ΠΏΠ»Π°Π½ΠΈΡΠΎΠ²Π°Π½Π½ΠΎΠ³ΠΎΒ ΠΏΡΠΎΡΡΠΎΡ
ΠΡΠΎΠΈΠ·Π²ΠΎΠ΄ΠΈΡΠ΅Π»ΡΠ½ΠΎΡΡΡ = (ΠΠΎΠ»-Π²ΠΎΒ ΠΏΡΠΎΠΈΠ·Π²Π΅Π΄ΡΠ½Π½ΡΡ Β ΠΈΠ·Π΄Π΅Π»ΠΈΠΉΒ * ΠΠΈΠ½ΠΈΠΌΠ°Π»ΡΠ½ΠΎΠ΅Β Π²ΡΠ΅ΠΌΡΒ ΡΠΈΠΊΠ»Π°)Β / Π€Π°ΠΊΡΠΈΡΠ΅ΡΠΊΠΎΠ΅Β Π²ΡΠ΅ΠΌΡΒ ΡΠ°Π±ΠΎΡΡ.
ΠΠΈΠ½ΠΈΠΌΠ°Π»ΡΠ½ΠΎΠ΅ Π²ΡΠ΅ΠΌΡ ΡΠΈΠΊΠ»Π° β ΠΌΠΈΠ½ΠΈΠΌΠ°Π»ΡΠ½ΠΎΠ΅ Π²ΡΠ΅ΠΌΡ, Π½Π΅ΠΎΠ±Ρ ΠΎΠ΄ΠΈΠΌΠΎΠ΅ Π΄Π»Ρ Π²ΡΠΏΡΡΠΊΠ° ΠΎΠ΄Π½ΠΎΠ³ΠΎ ΠΈΠ·Π΄Π΅Π»ΠΈΡ.
ΠΠ°ΡΠ΅ΡΡΠ²ΠΎ = ΠΠΎΠ»-Π²ΠΎΒ ΠΏΡΠΎΠΈΠ·Π²Π΅Π΄ΡΠ½Π½ΡΡ Β Π³ΠΎΠ΄Π½ΡΡ ΠΈΠ·Π΄Π΅Π»ΠΈΠΉΒ / ΠΠΎΠ»-Π²ΠΎΒ ΠΏΡΠΎΠΈΠ·Π²Π΅Π΄ΡΠ½Π½ΡΡ Β ΠΈΠ·Π΄Π΅Π»ΠΈΠΉ.
ΠΠΈΡΠ΅ΡΠ°ΡΡΡΠ°
ΠΡΠ½ΠΈΡΠ» ΠΠΆΠΎΠ½Ρ, ΠΠΆΠ΅ΠΉΠΌΡ ΠΡΠΌΠ΅ΠΊ. ΠΠ΅ΡΠ΅ΠΆΠ»ΠΈΠ²ΠΎΠ΅ ΠΏΡΠΎΠΈΠ·Π²ΠΎΠ΄ΡΡΠ²ΠΎ: ΠΠ°ΠΊ ΠΈΠ·Π±Π°Π²ΠΈΡΡΡΡ ΠΎΡ ΠΏΠΎΡΠ΅ΡΡ ΠΈ Π΄ΠΎΠ±ΠΈΡΡΡΡ ΠΏΡΠΎΡΠ²Π΅ΡΠ°Π½ΠΈΡ Π²Π°ΡΠ΅ΠΉ ΠΊΠΎΠΌΠΏΠ°Π½ΠΈΠΈ. Β —Β Π.:Β ΠΠ»ΡΠΏΠΈΠ½Π°Β ΠΠ°Π±Π»ΠΈΡΠ΅ΡΒ 2013.
ΠΠΈΡΠ΅ΡΠΊΠΈΠ½ Π‘.Π., ΠΠ»Π°Π΄ΠΎΠ² Π.Π., ΠΡΠ°Π΅Π² Π.Π. Π’ΠΎΡΠ½ΠΎ Π²ΠΎΠ²ΡΠ΅ΠΌΡ Π΄Π»Ρ Π ΠΎΡΡΠΈΠΈ. ΠΡΠ°ΠΊΡΠΈΠΊΠ° ΠΏΡΠΈΠΌΠ΅Π½Π΅Π½ΠΈΡ ERP-ΡΠΈΡΡΠ΅ΠΌ. Β —Β Π.:Β ΠΠ½ΡΡΠΈΡΡΡΒ ΠΊΠΎΠΌΠΏΠ»Π΅ΠΊΡΠ½ΡΡ Β ΡΡΡΠ°ΡΠ΅Π³ΠΈΡΠ΅ΡΠΊΠΈΡ Β ΠΈΡΡΠ»Π΅Π΄ΠΎΠ²Π°Π½ΠΈΠΉ,Β 2013.
Π’Π°ΠΉΠΈΡΠΈ ΠΠ½ΠΎ. ΠΡΠΎΠΈΠ·Π²ΠΎΠ΄ΡΡΠ²Π΅Π½Π½Π°Ρ ΡΠΈΡΡΠ΅ΠΌΠ° Π’ΠΎΠΉΠΎΡΡ. Π£Ρ ΠΎΠ΄Ρ ΠΎΡ ΠΌΠ°ΡΡΠΎΠ²ΠΎΠ³ΠΎ ΠΏΡΠΎΠΈΠ·Π²ΠΎΠ΄ΡΡΠ²Π°. Β —Β Π.:Β ΠΠ»ΡΠΏΠΈΠ½Π°Β ΠΠ°Π±Π»ΠΈΡΠ΅ΡΒ 2002.
ΠΠ²Π΅Π΄Π΅Π½ΠΈΠ΅ Π² ΡΠΈΡΡΠ΅ΠΌΡ ΡΠ±Π°Π»Π°Π½ΡΠΈΡΠΎΠ²Π°Π½Π½ΡΡ ΠΏΠΎΠΊΠ°Π·Π°ΡΠ΅Π»Π΅ΠΉ
www.maxplant.ru
ΠΠ΅ΡΠ΅ΠΆΠ»ΠΈΠ²ΠΎΠ΅ ΠΏΡΠΎΠΈΠ·Π²ΠΎΠ΄ΡΡΠ²ΠΎ: Π΅Π³ΠΎ ΡΡΡΡ, ΠΊΠΎΠ½ΡΠ΅ΠΏΡΠΈΡ ΠΈ ΠΎΡΠ½ΠΎΠ²Π½ΡΠ΅ ΠΈΠ½ΡΡΡΡΠΌΠ΅Π½ΡΡ
5 ΠΠΎΡΠ΅ΠΌΡ? (5 Why?) β ΠΈΠ½ΡΡΡΡΠΌΠ΅Π½Ρ Π²ΡΡΠ²Π»Π΅Π½ΠΈΡ ΠΏΠ΅ΡΠ²ΠΎΠΏΡΠΈΡΠΈΠ½ ΡΠ°ΡΡΠΌΠ°ΡΡΠΈΠ²Π°Π΅ΠΌΠΎΠΉ ΠΏΡΠΎΠ±Π»Π΅ΠΌΡ. ΠΡΠ½ΠΎΠ²Π°Π½ Π½Π° Π΄ΠΎΠΏΡΡΠ΅Π½ΠΈΠΈ, ΡΡΠΎ ΠΎΡΠ²Π΅ΡΠ°Ρ Π½Π° Π²ΠΎΠΏΡΠΎΡ ΠΠΎΡΠ΅ΠΌΡ ΠΏΡΡΡ ΡΠ°Π·, ΠΊΠΎΡΠ΅Π½Ρ ΠΏΡΠΎΠ±Π»Π΅ΠΌΡ, ΡΠ°ΠΊΠΆΠ΅ ΠΊΠ°ΠΊ ΠΈ ΡΠ΅ΡΠ΅Π½ΠΈΠ΅, ΡΡΠ°Π½ΠΎΠ²ΡΡΡΡ ΡΠ²Π½ΡΠΌΠΈ.
5W 2H β ΠΌΠ΅ΡΠΎΠ΄ Π΄Π»Ρ ΠΎΠΏΡΠ΅Π΄Π΅Π»Π΅Π½ΠΈΡ ΠΏΡΠΎΠ±Π»Π΅ΠΌΡ ΠΈΠ»ΠΈ Π·Π°Π΄Π°ΡΠΈ. ΠΠΎΠ΄ΡΠ°Π·ΡΠΌΠ΅Π²Π°Π΅Ρ ΠΎΡΠ²Π΅ΡΡ Π½Π° 7 Π²ΠΎΠΏΡΠΎΡΠΎΠ² ΡΠΎΠ΄Π΅ΡΠΆΠ°ΡΠΈΡ ΡΡ Π² ΠΌΠ½Π΅ΠΌΠΎΠ½ΠΈΡΠ΅ΡΠΊΠΎΠΌ ΠΊΠΎΠ΄Π΅ 5W2H β What, Who, Where, When, Why, How, How Much (Π§ΡΠΎ, ΠΡΠΎ, ΠΠ΄Π΅, ΠΠΎΠ³Π΄Π°, ΠΠΎΡΠ΅ΠΌΡ, ΠΠ°ΠΊ, Π‘ΠΊΠΎΠ»ΡΠΊΠΎ). ΠΡΠ²Π΅ΡΡ Π½Π° ΠΏΠ΅ΡΠ΅ΡΠΈΡΠ»Π΅Π½Π½ΡΠ΅ Π²ΠΎΠΏΡΠΎΡΡ ΠΏΠΎΠ·Π²ΠΎΠ»ΡΡΡ ΠΏΠΎΠ»ΡΡΠΈΡΡ ΡΠ΅Π»ΠΎΡΡΠ½ΠΎΠ΅ ΠΏΡΠ΅Π΄ΡΡΠ°Π²Π»Π΅Π½ΠΈΠ΅ ΠΎ ΠΏΡΠΎΠ±Π»Π΅ΠΌΠ΅ ΠΈΠ»ΠΈ Π·Π°Π΄Π°ΡΠ΅ Π΄Π»Ρ Π½Π°ΡΠ°Π»Π° Π΅Π΅ ΡΠ΅ΡΠ΅Π½ΠΈΡ.
7 Π²ΠΈΠ΄ΠΎΠ² ΠΏΠΎΡΠ΅ΡΡ β ΠΊΠ»Π°ΡΡΠΈΡΠ΅ΡΠΊΠΈΠ΅ Π²ΠΈΠ΄Ρ ΠΏΠΎΡΠ΅ΡΡ, ΠΎΠΏΡΠ΅Π΄Π΅Π»Π΅Π½Π½ΡΠ΅ Π½Π° Π’ΠΎΠΉΠΎΡΠ΅: ΠΠ΅ΡΠ΅ΠΏΡΠΎΠΈΠ·Π²ΠΎΠ΄ΡΡΠ²ΠΎ, ΠΠ°ΡΠ΅ΡΠΈΠ°Π» ΠΎΠΆΠΈΠ΄Π°Π΅Ρ, Π§Π΅Π»ΠΎΠ²Π΅ΠΊ ΠΎΠΆΠΈΠ΄Π°Π΅Ρ, ΠΠ·Π»ΠΈΡΠ½ΡΡ ΠΎΠ±ΡΠ°Π±ΠΎΡΠΊΠ°, ΠΠ²ΠΈΠΆΠ΅Π½ΠΈΠ΅ ΠΌΠ°ΡΠ΅ΡΠΈΠ°Π»Π°, ΠΠ²ΠΈΠΆΠ΅Π½ΠΈΠ΅ Π»ΡΠ΄Π΅ΠΉ, ΠΠ΅ΡΠ΅ΠΊΡΡ.
8 Π²ΠΈΠ΄ΠΎΠ² ΠΏΠΎΡΠ΅ΡΡ β ΠΊ ΡΠ΅ΠΌΠΈ Β«ΠΊΠ»Π°ΡΡΠΈΡΠ΅ΡΠΊΠΈΠΌΒ» Π²ΠΈΠ΄Π°ΠΌ ΠΏΠΎΡΠ΅ΡΡ Π΄ΠΎΠ±Π°Π²Π»Π΅Π½ Π²ΠΎΡΡΠΌΠΎΠΉ Π²ΠΈΠ΄ — ΠΠ΅ΠΈΡΠΏΠΎΠ»ΡΠ·ΠΎΠ²Π°Π½ΠΈΠ΅ ΠΈΠ΄Π΅ΠΉ.
DMAIC (define, measure, analyze, improve, control) β Π Π°Π·Π½ΠΎΠ²ΠΈΠ΄Π½ΠΎΡΡΡ ΠΏΡΠΈΠ½ΡΠΈΠΏΠ° ΡΠΎΠ²Π΅ΡΡΠ΅Π½ΡΡΠ²ΠΎΠ²Π°Π½ΠΈΡ ΠΏΡΠΎΡΠ΅ΡΡΠΎΠ² ΠΈ ΠΎΠΏΠ΅ΡΠ°ΡΠΈΠΉ ΠΏΡΠΈΠ½ΡΡΠ°Ρ Π² Π¨Π΅ΡΡΡ ΡΠΈΠ³ΠΌΠ°. ΠΠ·Π°ΠΈΠΌΠ½ΠΎΠ΅ ΡΠΎΠΎΡΠ²Π΅ΡΡΡΠ²ΠΈΠ΅ ΡΠΈΠΊΠ»Π° DMAIC ΠΈ PDCA: DMA β P, I-D, C- C,A. ΠΠΏΡΠ΅Π΄Π΅Π»ΠΈ ΡΠ΅Π»Ρ, ΡΠΎΠ±Π΅ΡΠΈ Π΄Π°Π½Π½ΡΠ΅, ΠΏΡΠΎΠ°Π½Π°Π»ΠΈΠ·ΠΈΡΡΠΉ ΠΈΡ ΠΈ ΡΠΏΠ»Π°Π½ΠΈΡΡΠΉ ΡΠ»ΡΡΡΠ΅Π½ΠΈΠ΅, ΡΠ΅Π°Π»ΠΈΠ·ΡΠΉ ΡΠ»ΡΡΡΠ΅Π½ΠΈΠ΅, ΠΏΡΠΎΠΊΠΎΠ½ΡΡΠΎΠ»ΠΈΡΡΠΉ ΠΏΠΎΠ»ΡΡΠ΅Π½Π½ΡΠΉ ΡΠ΅Π·ΡΠ»ΡΡΠ°Ρ.
SIPOC ΠΠΈΠ°Π³ΡΠ°ΠΌΠΌΠ° (Suppliers Inputs Process Outputs Customers, SIPOC) β ΠΈΠ½ΡΡΡΡΠΌΠ΅Π½Ρ Π΄Π»Ρ ΡΡΠΎΡΠ½Π΅Π½ΠΈΡ Π³ΡΠ°Π½ΠΈΡ ΡΠ°ΡΡΠΌΠ°ΡΡΠΈΠ²Π°Π΅ΠΌΠΎΠ³ΠΎ ΠΏΡΠΎΡΠ΅ΡΡΠ°. ΠΠΊΠ»ΡΡΠ°Π΅Ρ ΠΎΠΏΡΠ΅Π΄Π΅Π»Π΅Π½ΠΈΠ΅ ΠΏΠΎΡΡΠ°Π²ΡΠΈΠΊΠΎΠ² ΠΈ ΡΠΎΠΎΡΠ²Π΅ΡΡΡΠ²ΡΡΡΠΈΡ Π²Ρ ΠΎΠ΄ΠΎΠ², ΠΎΡΠ½ΠΎΠ²Π½ΡΡ ΡΠ°Π³ΠΎΠ² ΡΠ°ΡΡΠΌΠ°ΡΡΠΈΠ²Π°Π΅ΠΌΠΎΠ³ΠΎ ΠΏΡΠΎΡΠ΅ΡΡΠ°, Π²ΡΡ ΠΎΠ΄ΠΎΠ² ΠΈ ΡΠΎΠΎΡΠ²Π΅ΡΡΡΠ²ΡΡΡΠΈΡ ΠΏΠΎΠ»ΡΡΠ°ΡΠ΅Π»Π΅ΠΉ.
ΠΠ²ΡΠΎΠ½ΠΎΠΌΠ½ΠΎΠ΅ ΠΎΠ±ΡΠ»ΡΠΆΠΈΠ²Π°Π½ΠΈΠ΅ ΠΎΠ±ΠΎΡΡΠ΄ΠΎΠ²Π°Π½ΠΈΡ (Autonomous Maintenance, TPM AM) β ΠΏΠΎΠ΄Ρ ΠΎΠ΄ ΠΊ ΠΎΠ±ΡΠ»ΡΠΆΠΈΠ²Π°Π½ΠΈΡ ΠΎΠ±ΠΎΡΡΠ΄ΠΎΠ²Π°Π½ΠΈΡ, Π³Π΄Π΅ ΡΠ°ΡΡΡ ΡΡΠ½ΠΊΡΠΈΠΉ ΠΏΠΎ ΠΎΠ±ΡΠ»ΡΠΆΠΈΠ²Π°Π½ΠΈΡ (ΡΠΈΡΡΠΊΠ°, ΡΠΌΠ°Π·ΠΊΠ°, Π·Π°ΠΌΠ΅Π½Π° ΡΠ°ΡΡ ΠΎΠ΄Π½ΡΡ ΠΌΠ°ΡΠ΅ΡΠΈΠ°Π»ΠΎΠ² ΠΈ ΠΏΡΠΎΡΠΈΠ΅ ΠΏΡΠΎΡΡΡΠ΅ ΡΠ΅ΡΠ²ΠΈΡΠ½ΡΠ΅ ΠΎΠΏΠ΅ΡΠ°ΡΠΈΠΈ) Π²ΡΠΏΠΎΠ»Π½ΡΠ΅ΡΡΡ ΡΠΈΠ»Π°ΠΌΠΈ ΡΠ°ΠΌΠΈΡ ΠΎΠΏΠ΅ΡΠ°ΡΠΎΡΠΎΠ², Π² ΡΠΎ Π²ΡΠ΅ΠΌΡ ΠΊΠ°ΠΊ ΡΠ΅Ρ Π½ΠΈΡΠ΅ΡΠΊΠ°Ρ ΡΠ»ΡΠΆΠ±Π° ΡΠΎΡΡΠ΅Π΄ΠΎΡΠ°ΡΠΈΠ²Π°Π΅ΡΡΡ Π½Π° ΡΠ΅ΡΠ΅Π½ΠΈΠΈ Π±ΠΎΠ»Π΅Π΅ ΡΠ»ΠΎΠΆΠ½ΡΡ Π·Π°Π΄Π°Ρ (ΡΠ΅ΠΌΠΎΠ½ΡΡ, ΡΠ»ΠΎΠΆΠ½ΡΠ΅ Π’Π ΡΡΠ΅Π±ΡΡΡΠΈΠ΅ Π²ΡΡΠΎΠΊΠΎΠΉ ΠΊΠ²Π°Π»ΠΈΡΠΈΠΊΠ°ΡΠΈΠΈ).
ΠΠ½Π°Π»ΠΈΠ· Π²ΠΈΠ΄ΠΎΠ² ΠΈ ΠΏΠΎΡΠ»Π΅Π΄ΡΡΠ²ΠΈΠΉ ΠΎΡΠΊΠ°Π·ΠΎΠ² (Failure Mode and Effect Analysis, FMEA) β ΠΌΠ΅ΡΠΎΠ΄ Π²ΡΡΠ²Π»Π΅Π½ΠΈΡ Π²ΠΎΠ·ΠΌΠΎΠΆΠ½ΡΡ ΠΏΡΠΈΡΠΈΠ½ ΠΈ ΠΎΡΠ΅Π½ΠΊΠΈ ΡΠΈΡΠΊΠΎΠ² ΡΠ±ΠΎΡ Π² ΠΏΡΠΎΡΠ΅ΡΡΠ΅, ΠΏΡΠΎΠ΄ΡΠΊΡΠ΅, ΠΊΠΎΠ½ΡΡΡΡΠΊΡΠΈΠΈ, ΡΠΈΡΡΠ΅ΠΌΠ΅ ΠΈ ΠΏΡ. ΠΡΠ½ΠΎΡΠΈΡΡΡ ΠΊ ΠΏΡΠ΅Π²Π΅Π½ΡΠΈΠ²Π½ΡΠΌ ΠΌΠ΅ΡΠΎΠ΄Π°ΠΌ ΡΠ΅ΡΠ΅Π½ΠΈΡ ΠΏΡΠΎΠ±Π»Π΅ΠΌ. ΠΡΠ΅Π½ΠΊΠ° ΡΠΈΡΠΊΠΎΠ² ΠΏΠΎΠ·Π²ΠΎΠ»ΡΠ΅Ρ ΠΎΠΏΡΠ΅Π΄Π΅Π»ΠΈΡΡ ΠΏΡΠΈΠΎΡΠΈΡΠ΅Ρ Π·Π°Π΄Π°ΡΠΈ.
ΠΠ΅ΡΠ΅ΠΆΠ»ΠΈΠ²ΠΎΠ΅ ΠΏΡΠ΅Π΄ΠΏΡΠΈΡΡΠΈΠ΅ (ΠΠΈΠ½ ΠΏΡΠ΅Π΄ΠΏΡΠΈΡΡΠΈΠ΅, Lean Company) β ΡΡΠ°ΡΡΡ ΠΏΡΠΎΠΈΠ·Π²ΠΎΠ΄ΡΡΠ²Π΅Π½Π½ΠΎΠΉ ΡΠΈΡΡΠ΅ΠΌΡ ΠΎΡΠ³Π°Π½ΠΈΠ·Π°ΡΠΈΠΈ, Π΄ΠΎΡΡΠΈΠ³ΡΠ΅ΠΉ Π»ΡΡΡΠΈΡ ΠΏΠΎΠΊΠ°Π·Π°ΡΠ΅Π»Π΅ΠΉ ΡΡΡΠ΅ΠΊΡΠΈΠ²Π½ΠΎΡΡΠΈ Π² ΠΎΡΡΠ°ΡΠ»ΠΈ. Π§ΡΠΎ ΠΎΠ·Π½Π°ΡΠ°Π΅Ρ ΠΌΠΈΠ½ΠΈΠΌΠ°Π»ΡΠ½ΡΠ΅ ΠΈΠ·Π΄Π΅ΡΠΆΠΊΠΈ, ΠΌΠΈΠ½ΠΈΠΌΡΠΌ Π±ΡΠ°ΠΊΠ°, ΠΌΠΈΠ½ΠΈΠΌΠ°Π»ΡΠ½ΡΠΉ ΠΏΡΠΎΠΈΠ·Π²ΠΎΠ΄ΡΡΠ²Π΅Π½Π½ΡΠΉ ΡΠΈΠΊΠ». ΠΠ»Ρ ΠΏΠΎΠ΄ΠΎΠ±Π½ΠΎΠΉ Ρ Π°ΡΠ°ΠΊΡΠ΅ΡΠΈΡΡΠΈΠΊΠΈ ΡΠ°ΠΊΠΆΠ΅ ΠΈΡΠΏΠΎΠ»ΡΠ·ΡΠ΅ΡΡΡ ΡΠ΅ΡΠΌΠΈΠ½ ΠΡΠΎΠΈΠ·Π²ΠΎΠ΄ΠΈΡΠ΅Π»ΡΠ½ΠΎΡΡΡ ΠΌΠΈΡΠΎΠ²ΠΎΠ³ΠΎ ΠΊΠ»Π°ΡΡΠ° (World Class Performance) ΠΈΠ»ΠΈ ΠΠΏΠ΅ΡΠ°ΡΠΈΠΎΠ½Π½ΠΎΠ΅ Π‘ΠΎΠ²Π΅ΡΡΠ΅Π½ΡΡΠ²ΠΎ (Operational Excellence).
ΠΠ΅ΡΠ΅ΠΆΠ»ΠΈΠ²ΠΎΠ΅ ΠΏΡΠΎΠΈΠ·Π²ΠΎΠ΄ΡΡΠ²ΠΎ, ΠΠΈΠ½ (Lean, Lean Manufacturing, Lean Production, Lean Management) β ΠΏΡΠΎΠΈΠ·Π²ΠΎΠ΄ΡΡΠ²Π΅Π½Π½Π°Ρ ΠΊΠΎΠ½ΡΠ΅ΠΏΡΠΈΡ, ΡΠΎΠΆΠ΄Π΅Π½Π½Π°Ρ Π² ΡΠ΅Π·ΡΠ»ΡΡΠ°ΡΠ΅ ΡΠΈΡΡΠ΅ΠΌΠ°ΡΠΈΠ·Π°ΡΠΈΠΈ ΠΎΠΏΡΡΠ° ΡΠΏΠΎΠ½ΡΠΊΠΎΠΉ ΠΊΠΎΠΌΠΏΠ°Π½ΠΈΠΈ TOYOTA (ΠΡΠΎΠΈΠ·Π²ΠΎΠ΄ΡΡΠ²Π΅Π½Π½Π°Ρ ΡΠΈΡΡΠ΅ΠΌΠ° Π’ΠΎΠΉΠΎΡΡ, Toyota Production System, TPS). ΠΠ΅ΡΠ΅ΠΆΠ»ΠΈΠ²ΠΎΠ΅ ΠΏΡΠΎΠΈΠ·Π²ΠΎΠ΄ΡΡΠ²ΠΎ Π½Π°ΠΏΡΠ°Π²Π»Π΅Π½ΠΎ Π½Π° ΡΠΎΠΊΡΠ°ΡΠ΅Π½ΠΈΠ΅ Π²ΡΠ΅ΠΌΠ΅Π½ΠΈ ΠΎΡ Π·Π°ΠΊΠ°Π·Π° Π΄ΠΎ ΠΏΠΎΡΡΠ°Π²ΠΊΠΈ ΠΊΠ»ΠΈΠ΅Π½ΡΡ ΠΏΡΡΠ΅ΠΌ ΡΡΡΡΠ°Π½Π΅Π½ΠΈΠ΅ ΡΠ΅ΠΌΠΈ Π²ΠΈΠ΄ΠΎΠ² ΠΏΠΎΡΠ΅ΡΡ, ΠΈΡΠΏΠΎΠ»ΡΠ·ΡΡ Π²ΠΎΠ²Π»Π΅ΡΠ΅Π½ΠΈΠ΅ Π²ΡΠ΅Π³ΠΎ ΠΏΠ΅ΡΡΠΎΠ½Π°Π»Π° ΠΎΡΠ³Π°Π½ΠΈΠ·Π°ΡΠΈΠΈ.
ΠΠ΅ΡΠ΅ΠΆΠ»ΠΈΠ²ΡΠΉ ΡΠΊΠ»Π°Π΄ β ΠΎΠΏΡΠΈΠΌΠΈΠ·Π°ΡΠΈΡ ΡΠΊΠ»Π°Π΄Π° Ρ ΠΈΡΠΏΠΎΠ»ΡΠ·ΠΎΠ²Π°Π½ΠΈΠ΅ΠΌ ΠΈΠ½ΡΡΡΡΠΌΠ΅Π½ΡΠΎΠ² ΠΈ ΠΏΡΠΈΠ½ΡΠΈΠΏΠΎΠ² Π±Π΅ΡΠ΅ΠΆΠ»ΠΈΠ²ΠΎΠ³ΠΎ ΠΏΡΠΎΠΈΠ·Π²ΠΎΠ΄ΡΡΠ²Π°: 5Π‘, Π°Π΄ΡΠ΅ΡΠ½ΠΎΠ΅ Ρ ΡΠ°Π½Π΅Π½ΠΈΠ΅, ΡΠ΅Π·Π΅ΡΠ²Π½ΡΠ΅ ΡΡΠ΅ΠΉΠΊΠΈ, ΡΡΠ°Π½Π΄Π°ΡΡΠ½Π°Ρ ΡΠ°Π±ΠΎΡΠ° ΡΠΊΠ»Π°Π΄Π° ΠΈ ΠΏΡΠΎΡΠΈΠ΅.
ΠΡΡΡΡΠ°Ρ ΠΏΠ΅ΡΠ΅Π½Π°Π»Π°Π΄ΠΊΠ° ΠΎΠ±ΠΎΡΡΠ΄ΠΎΠ²Π°Π½ΠΈΡ (Quick Changeover, Single Minute Exchange of Die, SMED) β ΠΌΠ΅ΡΠΎΠ΄ ΡΠΎΠΊΡΠ°ΡΠ΅Π½ΠΈΡ Π²ΡΠ΅ΠΌΠ΅Π½ΠΈ ΠΏΠ΅ΡΠ΅Ρ ΠΎΠ΄Π° Ρ ΠΎΠ΄Π½ΠΎΠ³ΠΎ Π²ΠΈΠ΄Π° ΠΏΡΠΎΠ΄ΡΠΊΡΠΈΠΈ Π½Π° Π΄ΡΡΠ³ΠΎΠΉ Π·Π° ΠΌΠΈΠ½ΠΈΠΌΠ°Π»ΡΠ½ΠΎΠ΅ Π²ΡΠ΅ΠΌΡ. ΠΠ΅ΡΠΎΠ΄ ΠΎΡΠ½ΠΎΠ²Π°Π½ Π½Π° ΡΠ°Π·Π΄Π΅Π»Π΅Π½ΠΈΠΈ Π²Π½ΡΡΡΠ΅Π½Π½ΠΈΡ ΠΈ Π²Π½Π΅ΡΠ½ΠΈΡ ΠΎΠΏΠ΅ΡΠ°ΡΠΈΠΉ, Ρ.Π΅. ΡΡΠ΅Π±ΡΡΡΠΈΡ ΠΈ Π½Π΅ ΡΡΠ΅Π±ΡΡΡΠΈΡ ΠΎΡΡΠ°Π½ΠΎΠ²ΠΊΠΈ ΡΡΠ°Π½ΠΊΠ°, ΡΠΎΠΎΡΠ²Π΅ΡΡΡΠ²Π΅Π½Π½ΠΎ. ΠΠ±Π΅ΡΠΏΠ΅ΡΠΈΠ²Π°Π΅Ρ Π½Π΅ΠΎΠ±Ρ ΠΎΠ΄ΠΈΠΌΡΡ Π³ΠΈΠ±ΠΊΠΎΡΡΡ ΡΡΠ°ΡΡΠΊΠΎΠ² Π΄Π»Ρ ΠΏΠ΅ΡΠ΅Ρ ΠΎΠ΄Π° Π½Π° Π²ΡΡΡΠ³ΠΈΠ²Π°ΡΡΡΡ ΡΠΈΡΡΠ΅ΠΌΡ ΠΏΡΠΎΠΈΠ·Π²ΠΎΠ΄ΡΡΠ²Π°.
ΠΡΠ΅ΠΌΡ Π΄ΠΎΠ±Π°Π²Π»ΡΡΡΠ΅Π΅ ΡΠ΅Π½Π½ΠΎΡΡΡ (Value Added Time, VAT) β ΠΏΠΎΠΊΠ°Π·Π°ΡΠ΅Π»Ρ Ρ Π°ΡΠ°ΠΊΡΠ΅ΡΠΈΠ·ΡΡΡΠΈΠΉ Π΄ΠΎΠ»Ρ ΠΏΠΎΠ»Π΅Π·Π½ΠΎΠ³ΠΎ Π²ΡΠ΅ΠΌΠ΅Π½ΠΈ Π² ΡΡΠ°Π²Π½Π΅Π½ΠΈΠΈ Ρ ΠΎΠ±ΡΠ΅ΠΉ ΠΏΡΠΎΠ΄ΠΎΠ»ΠΆΠΈΡΠ΅Π»ΡΠ½ΠΎΡΡΡΡ ΠΏΡΠΎΡΠ΅ΡΡΠ° (Lead Time, LT).
ΠΡΠ΅ΠΌΡ ΡΠ°ΠΊΡΠ° (Tact time) β ΡΠΈΡΠΌ ΡΠ°Π±ΠΎΡΡ ΠΏΡΠΎΠΈΠ·Π²ΠΎΠ΄ΡΡΠ²Π° Π΄Π»Ρ ΠΎΠ±Π΅ΡΠΏΠ΅ΡΠ΅Π½ΠΈΡ ΠΏΡΠΎΠ΄ΡΠΊΡΠΈΠ΅ΠΉ ΠΊΠ»ΠΈΠ΅Π½ΡΠΎΠ² Π² ΡΠΎΠΎΡΠ²Π΅ΡΡΡΠ²ΠΈΠΈ ΡΠΎ ΡΠΏΡΠΎΡΠΎΠΌ. Π Π°ΡΡΡΠΈΡΡΠ²Π°Π΅ΡΡΡ ΠΊΠ°ΠΊ ΠΎΡΠ½ΠΎΡΠ΅Π½ΠΈΠ΅ Π΄ΠΎΡΡΡΠΏΠ½ΠΎΠ³ΠΎ Π²ΡΠ΅ΠΌΠ΅Π½ΠΈ ΠΊ ΠΏΡΠΎΠ³Π½ΠΎΠ·ΠΈΡΡΠ΅ΠΌΠΎΠΌΡ ΡΠΏΡΠΎΡΡ. Π’Π°ΠΊΠΈΠΌ ΠΎΠ±ΡΠ°Π·ΠΎΠΌ, ΠΎΠΏΡΠ΅Π΄Π΅Π»ΡΠ΅ΡΡΡ ΠΏΠ΅ΡΠΈΠΎΠ΄ΠΈΡΠ½ΠΎΡΡΡ Π²ΡΠΏΡΡΠΊΠ° Π³ΠΎΡΠΎΠ²ΠΎΠΉ ΠΏΡΠΎΠ΄ΡΠΊΡΠΈΠΈ. ΠΠΌΠ΅Ρ ΡΠ°ΠΊΠΎΠΉ ΠΏΡΠΎΠ³Π½ΠΎΠ·Π½ΡΠΉ ΠΏΠΎΠΊΠ°Π·Π°ΡΠ΅Π»Ρ ΠΌΠΎΠΆΠ½ΠΎ Π²ΡΠΏΠΎΠ»Π½ΡΡΡ Π±Π°Π»Π°Π½ΡΠΈΡΠΎΠ²ΠΊΡ ΡΡΠ°ΡΡΠΊΠΎΠ², ΡΠΎ Π΅ΡΡΡ ΡΡΡΡΠ°Π½ΠΈΡΡ Β«ΡΠ·ΠΊΠΈΠ΅ ΠΌΠ΅ΡΡΠ°Β» ΠΈ Π½Π΅ΡΡΡΠ΅ΠΊΡΠΈΠ²Π½ΡΡ Π·Π°Π³ΡΡΠ·ΠΊΡ. ΠΠΎΡΠ»Π΅ ΡΡΠ²Π΅ΡΠΆΠ΄Π΅Π½ΠΈΡ ΠΏΠΎΠΊΠ°Π·Π°ΡΠ΅Π»Ρ ΠΡΠ΅ΠΌΡ ΡΠ°ΠΊΡΠ° ΡΠΈΠ½Ρ ΡΠΎΠ½ΠΈΠ·ΠΈΡΡΠ΅Ρ ΡΠ°Π±ΠΎΡΡ Π²ΡΠ΅Π³ΠΎ ΠΏΠΎΡΠΎΠΊΠ° ΡΠΎΠ·Π΄Π°Π½ΠΈΡ ΡΠ΅Π½Π½ΠΎΡΡΠΈ, ΠΈ Π½Π΅ Π΄Π°Π΅Ρ ΡΠ°ΡΡΠΈ Π·Π°ΠΏΠ°ΡΠ°ΠΌ, ΠΌΠΈΠ½ΠΈΠΌΠΈΠ·ΠΈΡΡΠ΅Ρ ΠΏΡΠΎΡΡΠΎΠΈ Π»ΡΠ΄Π΅ΠΉ ΠΈ ΠΌΠ°ΡΠΈΠ½.
ΠΡΠ΅ΠΎΠ±ΡΠ΅Π΅ ΠΎΠ±ΡΠ»ΡΠΆΠΈΠ²Π°Π½ΠΈΠ΅ ΠΎΠ±ΠΎΡΡΠ΄ΠΎΠ²Π°Π½ΠΈΡ (Total Productive Maintenance, TPM) β ΠΏΡΠΎΠΈΠ·Π²ΠΎΠ΄ΡΡΠ²Π΅Π½Π½Π°Ρ ΠΊΠΎΠ½ΡΠ΅ΠΏΡΠΈΡ, ΠΎΡΠΈΠ΅Π½ΡΠΈΡΠΎΠ²Π°Π½Π½Π°Ρ Π½Π° ΠΎΠ±Π΅ΡΠΏΠ΅ΡΠ΅Π½ΠΈΠ΅ Π½Π°Π΄Π΅ΠΆΠ½ΠΎΡΡΠΈ ΠΎΠ±ΠΎΡΡΠ΄ΠΎΠ²Π°Π½ΠΈΡ, ΠΈΡΠΊΠ»ΡΡΠ΅Π½ΠΈΡ Π΄Π΅ΡΠ΅ΠΊΡΠΎΠ² ΠΈ Π½Π΅ΡΡΠ°ΡΡΠ½ΡΡ ΡΠ»ΡΡΠ°Π΅Π².
ΠΡΠ΅ΠΎΠ±ΡΠ΅Π΅ ΡΠΏΡΠ°Π²Π»Π΅Π½ΠΈΠ΅ ΠΊΠ°ΡΠ΅ΡΡΠ²ΠΎΠΌ (Total Quality Management, TQM) β ΠΏΠΎΠ΄Ρ ΠΎΠ΄ ΠΊ ΠΌΠ΅Π½Π΅Π΄ΠΆΠΌΠ΅Π½ΡΡ, Π² ΠΊΠΎΡΠΎΡΠΎΠΌ Π²ΡΠ΅ ΠΊΠΎΠΌΠΏΠΎΠ½Π΅Π½ΡΡ ΠΎΡΠ³Π°Π½ΠΈΠ·Π°ΡΠΈΠΈ ΡΠ°ΡΡΠΌΠ°ΡΡΠΈΠ²Π°ΡΡΡΡ ΡΠ΅ΡΠ΅Π· ΠΏΡΠΈΠ·ΠΌΡ ΠΊΠ°ΡΠ΅ΡΡΠ²Π°. ΠΡΠΏΠΎΠ»ΡΠ·ΡΠ΅Ρ ΡΠ΅Π·ΠΈΡ: Π Π΅Π·ΡΠ»ΡΡΠ°Ρ ΠΎΠΏΡΠ΅Π΄Π΅Π»ΡΠ΅ΡΡΡ ΠΊΠ°ΡΠ΅ΡΡΠ²ΠΎΠΌ ΡΠ°ΠΌΠΎΠ³ΠΎ ΠΏΡΠΎΡΠ΅ΡΡΠ°. Π Π΄ΠΎΠ»Π³ΠΎΡΡΠΎΡΠ½ΠΎΠΉ ΠΏΠ΅ΡΡΠΏΠ΅ΠΊΡΠΈΠ²Π΅ TQM ΠΏΠΎΠ·Π²ΠΎΠ»ΡΠ΅Ρ Π΄ΠΎΡΡΠΈΠ³Π°ΡΡ ΡΡΠ°Π±ΠΈΠ»ΡΠ½ΠΎΠ³ΠΎ ΠΊΠ°ΡΠ΅ΡΡΠ²Π° ΠΏΡΠΎΠ΄ΡΠΊΡΠΈΠΈ, Π²ΡΡΠΎΠΊΠΎΠΉ ΠΏΡΠΎΠΈΠ·Π²ΠΎΠ΄ΡΡΠ²Π΅Π½Π½ΠΎΠΉ ΠΊΡΠ»ΡΡΡΡΡ ΠΎΡΠ³Π°Π½ΠΈΠ·Π°ΡΠΈΠΈ, ΡΠΎΡΠ΅ΡΠ°ΡΡΠ΅ΠΉ Π°ΡΠΌΠΎΡΡΠ΅ΡΡ ΡΠ²ΠΎΡΡΠ΅ΡΡΠ²Π° ΠΈ Π΄ΠΈΡΡΠΈΠΏΠ»ΠΈΠ½Ρ.
ΠΡΡΡΠΎΠ΅Π½Π½ΠΎΠ΅ ΠΊΠ°ΡΠ΅ΡΡΠ²ΠΎ (Π°Π²ΡΠΎΠΊΠ°ΡΠ΅ΡΡΠ²ΠΎ, built in quality) β ΠΎΡΠ³Π°Π½ΠΈΠ·Π°ΡΠΈΠΎΠ½Π½ΠΎ-ΡΠ΅Ρ Π½ΠΈΡΠ΅ΡΠΊΠΈΠ΅ ΠΌΠ΅ΡΡ, Π½Π°ΠΏΡΠ°Π²Π»Π΅Π½Π½ΡΠ΅ Π½Π° ΠΈΡΠΊΠ»ΡΡΠ΅Π½ΠΈΠ΅ ΠΎΡΠΈΠ±ΠΎΠΊ Π½Π΅ ΠΏΡΡΠ΅ΠΌ ΠΊΠΎΠ½ΡΡΠΎΠ»Ρ, Π° ΠΌΠ΅ΡΠΎΠ΄ΠΎΠΌ Π²ΡΡΡΠ°ΠΈΠ²Π°Π½ΠΈΡ ΠΊΠ°ΡΠ΅ΡΡΠ²Π° Π² ΡΠ°ΠΌ ΠΏΡΠΎΡΠ΅ΡΡ. ΠΡΠ»ΠΈ ΠΎΡΠΈΠ±ΠΊΠ° Π²ΡΠ΅ ΠΆΠ΅ ΠΏΡΠΎΠΈΠ·ΠΎΡΠ»Π°, ΠΈΠ½ΡΡΡΡΠΌΠ΅Π½ΡΠ°ΡΠΈΠΉ Π²ΡΡΡΠΎΠ΅Π½Π½ΠΎΠ³ΠΎ ΠΊΠ°ΡΠ΅ΡΡΠ²Π° ΠΏΡΠΈΠ·Π²Π°Π½ ΠΏΡΠΈΠ±Π»ΠΈΠ·ΠΈΡΡ ΠΌΠ΅ΡΡΠΎ ΠΎΠ±Π½Π°ΡΡΠΆΠ΅Π½ΠΈΡ ΠΊ ΠΌΠ΅ΡΡΡ Π²ΠΎΠ·Π½ΠΈΠΊΠ½ΠΎΠ²Π΅Π½ΠΈΡ ΠΎΡΠΈΠ±ΠΊΠΈ (Π΄Π»Ρ Π²ΠΈΠ·ΡΠ°Π»ΠΈΠ·Π°ΡΠΈΠΈ ΠΈΡΠΏΠΎΠ»ΡΠ·ΡΠ΅ΡΡΡ ΠΌΠ°ΡΡΠΈΡΠ° Π°Π²ΡΠΎΠΊΠ°ΡΠ΅ΡΡΠ²Π°). ΠΡΡΡΠΎΠ΅Π½Π½ΠΎΠ΅ ΠΊΠ°ΡΠ΅ΡΡΠ²ΠΎ ΡΠ΅Π°Π»ΠΈΠ·ΡΠ΅Ρ ΠΏΡΠΈΠ½ΡΠΈΠΏ Β«Π½Π΅ ΠΏΡΠΈΠ½ΠΈΠΌΠ°ΠΉ, Π½Π΅ ΠΏΡΠΎΠΈΠ·Π²ΠΎΠ΄ΠΈ, Π½Π΅ ΠΏΠ΅ΡΠ΅Π΄Π°Π²Π°ΠΉ Π±ΡΠ°ΠΊΒ».
ΠΡΡΡΠ³ΠΈΠ²Π°ΡΡΠ°Ρ ΡΠΈΡΡΠ΅ΠΌΠ° ΠΏΡΠΎΠΈΠ·Π²ΠΎΠ΄ΡΡΠ²Π°, Π’ΡΠ½ΡΡΠ°Ρ ΡΠΈΡΡΠ΅ΠΌΠ° (PULL System) β ΠΏΡΠΎΠΈΠ·Π²ΠΎΠ΄ΡΡΠ²Π΅Π½Π½Π°Ρ ΡΠΈΡΡΠ΅ΠΌΠ°, ΠΎΡΠ½ΠΎΠ²Π°Π½Π½Π°Ρ Π½Π° ΠΏΡΠΈΠ½ΡΠΈΠΏΠ΅ Π²ΡΡΡΠ³ΠΈΠ²Π°Π½ΠΈΡ. ΠΠ°ΡΠ΅ΡΠΈΠ°Π»ΡΠ½ΡΠ΅ ΠΏΠΎΡΠΎΠΊΠΈ ΡΠ΅Π³ΡΠ»ΠΈΡΡΡΡΡΡ ΠΏΠΎΡΡΠ΅Π±ΠΈΡΠ΅Π»Π΅ΠΌ (Π²Π½Π΅ΡΠ½ΠΈΠΌ ΠΈ/ΠΈΠ»ΠΈ Π²Π½ΡΡΡΠ΅Π½Π½ΠΈΠΌ ΠΊΠ»ΠΈΠ΅Π½ΡΠΎΠΌ), Π° Π½Π΅ ΠΆΠ΅ΡΡΠΊΠΎΠΉ ΡΠΈΡΡΠ΅ΠΌΠΎΠΉ ΠΏΠ»Π°Π½ΠΈΡΠΎΠ²Π°Π½ΠΈΡ. ΠΠ½ΡΠΎΡΠΌΠ°ΡΠΈΠΎΠ½Π½Π°Ρ ΡΠΈΡΡΠ΅ΠΌΠ°, ΡΠΎΠΎΠ±ΡΠ°ΡΡΠ°Ρ ΠΎ ΠΏΠΎΡΡΠ΅Π±Π½ΠΎΡΡΠΈ, ΠΎΡΠ½ΠΎΠ²Π°Π½Π° Π½Π° Π³ΠΎΡΠΈΠ·ΠΎΠ½ΡΠ°Π»ΡΠ½ΠΎΠΌ Π²Π·Π°ΠΈΠΌΠΎΠ΄Π΅ΠΉΡΡΠ²ΠΈΠΈ ΡΡΠ°ΡΡΠΊΠΎΠ² Β«ΠΏΠΎΡΡΠ΅Π±ΠΈΡΠ΅Π»Ρ — ΠΏΠΎΡΡΠ°Π²ΡΠΈΠΊΒ» ΠΈ ΡΠ΅Π°Π»ΠΈΠ·ΡΠ΅ΡΡΡ Ρ ΠΈΡΠΏΠΎΠ»ΡΠ·ΠΎΠ²Π°Π½ΠΈΠ΅ΠΌ ΠΊΠ°ΡΡΠΎΡΠ΅ΠΊ ΠΠ°Π½Π±Π°Π½ (ΡΠΏ. Kamban, Kanban) ΠΈΠ»ΠΈ ΠΏΡΠΈΠ½ΡΠΈΠΏΠ° ΡΡΠΏΠ΅ΡΠΌΠ°ΡΠΊΠ΅ΡΠ°.
ΠΠ΅ΠΌΠ±Π° (ΡΠΏ. Gemba) β ΠΌΠ΅ΡΡΠΎ, Π³Π΄Π΅ ΡΠΎΠ·Π΄Π°Π΅ΡΡΡ ΡΠ΅Π½Π½ΠΎΡΡΡ. ΠΠ±ΡΡΠ½ΠΎ, ΡΠ΅Ρ , ΡΡΠΎΠΉΠΊΠ° ΠΎΠ±ΡΠ»ΡΠΆΠΈΠ²Π°Π½ΠΈΡ, ΠΌΠ΅ΡΡΠΎ, Π³Π΄Π΅ ΠΏΡΠΎΠΈΡΡ ΠΎΠ΄ΠΈΡ Π΄ΠΎΠ±Π°Π²Π»Π΅Π½ΠΈΠ΅ ΠΏΠΎΡΡΠ΅Π±ΠΈΡΠ΅Π»ΡΡΠΊΠΈΡ ΡΠ²ΠΎΠΉΡΡΠ² ΠΏΡΠΎΠ΄ΡΠΊΡΡ ΠΈΠ»ΠΈ ΡΡΠ»ΡΠ³Π΅.
ΠΠΈΡΡΠΎΠ³ΡΠ°ΠΌΠΌΠ° β ΡΠ°Π·Π½ΠΎΠ²ΠΈΠ΄Π½ΠΎΡΡΡ ΡΡΠΎΠ»Π±ΠΈΠΊΠΎΠ²ΠΎΠΉ Π΄ΠΈΠ°Π³ΡΠ°ΠΌΠΌΡ. ΠΡΠΏΠΎΠ»ΡΠ·ΡΠ΅ΡΡΡ Π΄Π»Ρ ΠΏΠΎΠ½ΠΈΠΌΠ°Π½ΠΈΡ Π·Π°ΠΊΠΎΠ½Π° ΡΠ°ΡΠΏΡΠ΅Π΄Π΅Π»Π΅Π½ΠΈΡ ΡΡΠ°ΡΠΈΡΡΠΈΡΠ΅ΡΠΊΠΈΡ Π΄Π°Π½Π½ΡΡ ΠΈ Π²Π΅Π»ΠΈΡΠΈΠ½Ρ ΠΈΡ ΡΠ°Π·Π±ΡΠΎΡΠ°. ΠΠΈΡΡΠΎΠ³ΡΠ°ΠΌΠΌΠ° ΠΏΠΎΠΌΠΎΠ³Π°Π΅Ρ ΠΏΠΎΠ½ΡΡΡ Π½Π° ΡΠ΅ΠΌ ΡΠ»Π΅Π΄ΡΠ΅Ρ ΡΡΠΎΠΊΡΡΠΈΡΠΎΠ²Π°ΡΡ Π²Π½ΠΈΠΌΠ°Π½ΠΈΠ΅ Π΄Π»Ρ ΡΠ΅Π»Π΅ΠΉ ΡΠ»ΡΡΡΠ΅Π½ΠΈΡ ΠΏΡΠΎΡΠ΅ΡΡΠ°.
ΠΠΎΠ»ΠΎΡ ΠΊΠ»ΠΈΠ΅Π½ΡΠ° (Voice Of the Customer, VoC) β ΠΌΠ΅ΡΠΎΠ΄ ΠΎΠΏΠΈΡΡΠ²Π°ΡΡΠΈΠΉ ΠΏΠΎΡΡΠ΅Π±Π½ΠΎΡΡΠΈ Π½Π°ΡΠΈΡ ΠΊΠ»ΠΈΠ΅Π½ΡΠΎΠ², ΠΈ ΡΠΎ, ΠΊΠ°ΠΊ ΠΎΠ½ΠΈ Π²ΠΎΡΠΏΡΠΈΠ½ΠΈΠΌΠ°ΡΡ Π½Π°ΡΠΈ ΠΏΡΠΎΠ΄ΡΠΊΡΡ ΠΈ ΡΡΠ»ΡΠ³ΠΈ. ΠΠ΅ΡΠΎΠ΄ ΠΈΡΠΏΠΎΠ»ΡΠ·ΡΠ΅ΡΡΡ Π΄Π»Ρ ΡΠΎΠΏΠΎΡΡΠ°Π²Π»Π΅Π½ΠΈΡ ΠΏΡΠΎΡΠ΅ΡΡΠ° Ρ ΠΈΠ·ΠΌΠ΅ΡΡΠ΅ΠΌΡΠΌΠΈ ΡΡΠ΅Π±ΠΎΠ²Π°Π½ΠΈΡΠΌΠΈ ΠΊΠ»ΠΈΠ΅Π½ΡΠΎΠ².
ΠΠΆΠΈΠ΄ΠΎΠΊΠ°, ΠΠ·ΠΈΠ΄ΠΎΠΊΠ° (ΡΠΏ. Jidoka) — ΡΡΡΡΠΎΠΉΡΡΠ²ΠΎ, ΠΊΠΎΡΠΎΡΠΎΠ΅ Π°Π²ΡΠΎΠΌΠ°ΡΠΈΡΠ΅ΡΠΊΠΈ Π²ΡΠΊΠ»ΡΡΠ°Π΅Ρ ΠΌΠ°ΡΠΈΠ½Ρ ΠΏΡΠΈ ΠΈΠ·Π³ΠΎΡΠΎΠ²Π»Π΅Π½ΠΈΠΈ ΠΎΡΠΈΠ±ΠΎΡΠ½ΠΎΠΉ Π΄Π΅ΡΠ°Π»ΠΈ.
ΠΠΈΠ°Π³ΡΠ°ΠΌΠΌΠ° ΠΡΠΈΠΊΠ°Π²Ρ, ΠΠΈΠ°Π³ΡΠ°ΠΌΠΌΠ° ΠΡΠΈΠΊΠ°Π²Ρ, ΠΠΈΠ°Π³ΡΠ°ΠΌΠΌΠ° Β«Π ΡΠ±ΡΡ ΠΊΠΎΡΡΡΒ», ΠΠΈΠ°Π³ΡΠ°ΠΌΠΌΠ° ΠΏΡΠΈΡΠΈΠ½Π½ΠΎ-ΡΠ»Π΅Π΄ΡΡΠ²Π΅Π½Π½ΡΡ ΡΠ²ΡΠ·Π΅ΠΉ (Fishbone Diagram, Ishikawa Diagram) β ΠΌΠ΅ΡΠΎΠ΄ Π²ΡΡΠ²Π»Π΅Π½ΠΈΡ ΡΠ°ΠΊΡΠΎΡΠΎΠ², Π²Π»ΠΈΡΡΡΠΈΡ Π½Π° ΡΠ°ΡΡΠΌΠ°ΡΡΠΈΠ²Π°Π΅ΠΌΡΡ ΠΏΡΠΎΠ±Π»Π΅ΠΌΡ. ΠΠΎΠΈΡΠΊ ΡΠ°ΠΊΡΠΎΡΠΎΠ² ΠΏΡΠΎΠΈΠ·Π²ΠΎΠ΄ΠΈΡΡΡ ΠΏΠΎ Π½Π΅ΡΠΊΠΎΠ»ΡΠΊΠΈΠΌ Π½Π°ΠΏΡΠ°Π²Π»Π΅Π½ΠΈΡΠΌ: ΠΡΠ΄ΠΈ, ΠΠ±ΠΎΡΡΠ΄ΠΎΠ²Π°Π½ΠΈΠ΅, ΠΠ΅ΡΠΎΠ΄, ΠΠ½Π΅ΡΠ½ΡΡ ΡΡΠ΅Π΄Π°, ΠΠ·ΠΌΠ΅ΡΠ΅Π½ΠΈΡ, ΠΠ°ΡΠ΅ΡΠΈΠ°Π».
ΠΠΈΠ°Π³ΡΠ°ΠΌΠΌΠ° ΠΠ°ΡΠ΅ΡΠΎ (ΠΡΠ°Π²ΠΈΠ»ΠΎ 80/20, ΠΏΡΠ°Π²ΠΈΠ»ΠΎ ΠΠ°ΡΠ΅ΡΠΎ) β ΡΠ°Π·Π½ΠΎΠ²ΠΈΠ΄Π½ΠΎΡΡΡ ΡΡΠΎΠ»Π±ΠΈΠΊΠΎΠ²ΠΎΠΉ Π΄ΠΈΠ°Π³ΡΠ°ΠΌΠΌΡ ΠΎΡΡΠΎΡΡΠΈΡΠΎΠ²Π°Π½Π½ΠΎΠΉ ΠΏΠΎ ΡΠ±ΡΠ²Π°Π½ΠΈΡ. ΠΡΠΏΠΎΠ»ΡΠ·ΡΠ΅ΡΡΡ Π΄Π»Ρ Π½Π°Π³Π»ΡΠ΄Π½ΠΎΠ³ΠΎ ΠΏΡΠ΅Π΄ΡΡΠ°Π²Π»Π΅Π½ΠΈΡ Π°ΡΡΠΈΠ±ΡΡΠΈΠ²Π½ΡΡ Π΄Π°Π½Π½ΡΡ , Π΄Π»Ρ ΠΎΠΏΡΠ΅Π΄Π΅Π»Π΅Π½ΠΈΡ ΠΏΡΠΈΠΎΡΠΈΡΠ΅ΡΠΎΠ² Π²ΠΎΠ·Π΄Π΅ΠΉΡΡΠ²ΠΈΡ Π½Π° ΠΏΡΠΎΠ±Π»Π΅ΠΌΡ. ΠΡΠΏΠΎΠ»ΡΠ·ΡΠ΅Ρ ΠΏΡΠΈΠ½ΡΠΈΠΏ ΠΠ°ΡΠ΅ΡΠΎ, ΠΊΠΎΡΠΎΡΡΠΉ ΠΏΡΠΈΠΌΠ΅Π½ΠΈΡΠ΅Π»ΡΠ½ΠΎ ΠΊ ΠΏΡΠΎΠ±Π»Π΅ΠΌΠ°ΠΌ ΠΏΡΠΎΠΈΠ·Π²ΠΎΠ΄ΡΡΠ²Π° ΡΡΠ°ΠΊΡΡΠ΅ΡΡΡ ΡΠ»Π΅Π΄ΡΡΡΠΈΠΌ ΠΎΠ±ΡΠ°Π·ΠΎΠΌ: 80% Π²ΡΠ΅Π³ΠΎ Π±ΡΠ°ΠΊΠ° ΡΠ²Π»ΡΠ΅ΡΡΡ ΡΠ»Π΅Π΄ΡΡΠ²ΠΈΠ΅ΠΌ 20% Π²ΡΠ΅Ρ ΠΏΡΠΈΡΠΈΠ½. Π ΠΊΠ»Π°ΡΡΠΈΡΠ΅ΡΠΊΠΎΠΌ Π²ΠΈΠ΄Π΅ ΡΠΎΠ΄Π΅ΡΠΆΠΈΡ ΠΊΡΠΈΠ²ΡΡ ΠΠΎΡΠ΅Π½ΡΠ°, ΠΊΠΎΡΠΎΡΠ°Ρ ΠΈΠ»Π»ΡΡΡΡΠΈΡΡΠ΅Ρ ΠΏΡΠΎΡΠ΅Π½ΡΠ½ΡΠΉ Π²ΠΊΠ»Π°Π΄ ΠΊΠ°ΠΆΠ΄ΠΎΠ³ΠΎ ΡΠ»Π΅ΠΌΠ΅Π½ΡΠ° Π΄ΠΈΠ°Π³ΡΠ°ΠΌΠΌΡ ΠΠ°ΡΠ΅ΡΠΎ.
ΠΠ°ΠΉΠ΄Π·Π΅Π½, ΠΠ°ΠΉΠ·Π΅Π½, ΠΠ΅ΠΏΡΠ΅ΡΡΠ²Π½ΠΎΠ΅ ΡΠΎΠ²Π΅ΡΡΠ΅Π½ΡΡΠ²ΠΎΠ²Π°Π½ΠΈΠ΅ (Kaizen, Continuous Improvement) β Π½Π΅ΠΏΡΠ΅ΡΡΠ²Π½ΠΎΠ΅ ΡΠΎΠ²Π΅ΡΡΠ΅Π½ΡΡΠ²ΠΎΠ²Π°Π½ΠΈΠ΅, Π² ΠΊΠΎΡΠΎΡΠΎΠΌ Π·Π°Π΄Π΅ΠΉΡΡΠ²ΠΎΠ²Π°Π½ Π²Π΅ΡΡ ΠΏΠ΅ΡΡΠΎΠ½Π°Π», ΠΈ ΠΊΠΎΡΠΎΡΠΎΠ΅ Π½Π°ΠΏΡΠ°Π²Π»Π΅Π½ΠΎ Π½Π° ΡΠ»ΡΡΡΠ΅Π½ΠΈΠ΅ Π²ΡΠ΅Ρ Π½Π°ΠΏΡΠ°Π²Π»Π΅Π½ΠΈΠΉ ΡΠ°Π±ΠΎΡΡ ΠΏΡΠ΅Π΄ΠΏΡΠΈΡΡΠΈΡ. ΠΠ°ΠΉΠ΄Π·Π΅Π½ β ΡΡΠΎ ΠΏΡΡΡ Π΄ΠΎΡΡΠΈΠΆΠ΅Π½ΠΈΡ ΡΡΠ°ΡΡΡΠ° ΠΠ΅ΡΠ΅ΠΆΠ»ΠΈΠ²ΠΎΠ΅ ΠΏΡΠ΅Π΄ΠΏΡΠΈΡΡΠΈΠ΅.
ΠΠ°Π½Π±Π°Π½ (Kanban, Kamban β ΡΠΏ. ΠΊΠ°ΡΡΠΎΡΠΊΠ°) β ΠΈΠ½ΡΠΎΡΠΌΠ°ΡΠΈΠΎΠ½Π½Π°Ρ ΡΠΈΡΡΠ΅ΠΌΠ° Π΄Π»Ρ ΠΈΠ·Π²Π΅ΡΠ΅Π½ΠΈΡ ΠΎ ΠΏΠΎΡΡΠ΅Π±Π½ΠΎΡΡΠΈ ΡΡΠ°ΡΡΠΊΠ°. Π Π°Π·Π»ΠΈΡΠ°ΡΡ Π΄ΠΎ ΡΠ΅ΡΡΠΈ Π²ΠΈΠ΄ΠΎΠ² ΠΊΠ°Π½Π±Π°Π½ Ρ ΡΡΠ΅ΡΠΎΠΌ ΠΎΡΠΎΠ±Π΅Π½Π½ΠΎΡΡΠ΅ΠΉ ΠΏΠΎΠ»ΡΡΠ°ΡΠ΅Π»Ρ ΠΈ ΠΏΠΎΡΡΠ°Π²ΡΠΈΠΊΠ° (Π²Π½Π΅ΡΠ½ΠΈΠΉ, Π²Π½ΡΡΡΠ΅Π½Π½ΠΈΠΉ, Ρ ΠΏΠ΅ΡΠ΅Π½Π°Π»Π°Π΄ΠΊΠΎΠΉ, Π±Π΅Π· ΠΏΠ΅ΡΠ΅Π½Π°Π»Π°Π΄ΠΊΠΈ, ΠΈ ΠΏΡ.). ΠΡΠΈΠΌΠ΅Π½ΡΠ΅ΡΡΡ Π΄Π»Ρ ΡΠ΅Π°Π»ΠΈΠ·Π°ΡΠΈΠΈ ΠΏΡΠΈΠ½ΡΠΈΠΏΠ° Β«Π’ΠΎΡΠ½ΠΎ Π²ΠΎΠ²ΡΠ΅ΠΌΡΒ»
ΠΠ°ΡΡΠΈΡΠΎΠ²Π°Π½ΠΈΠ΅ ΠΏΠΎΡΠΎΠΊΠ° ΡΠ΅Π½Π½ΠΎΡΡΠΈ (Value Stream Mapping, VSM) β Π²ΠΈΠ·ΡΠ°Π»ΡΠ½ΡΠΉ ΠΌΠ΅ΡΠΎΠ΄ ΠΏΠΎΠ½ΠΈΠΌΠ°Π½ΠΈΡ ΠΏΠΎΡΠ΅Π½ΡΠΈΠ°Π»Π° ΡΡΡΠ΅ΠΊΡΠΈΠ²Π½ΠΎΡΡΠΈ ΠΏΡΠΎΠΈΠ·Π²ΠΎΠ΄ΡΡΠ²Π° ΠΏΡΠΎΠ΄ΡΠΊΡΠΈΠΈ ΠΈΠ»ΠΈ ΡΡΠ»ΡΠ³. ΠΠ°ΡΡΠΈΡΠΎΠ²Π°Π½ΠΈΠ΅ ΠΌΠΎΠΆΠ΅Ρ ΠΏΡΠΎΠΈΠ·Π²ΠΎΠ΄ΠΈΡΡΡΡ Π²Π΅Π·Π΄Π΅, Π³Π΄Π΅ Π΅ΡΡΡ ΠΏΠΎΡΠΎΠΊ ΡΠΎΠ·Π΄Π°Π½ΠΈΡ ΡΠ΅Π½Π½ΠΎΡΡΠΈ: ΡΠ±ΠΎΡΠΊΠ° ΡΠ·Π»Π°, ΠΏΡΠΎΠΈΠ·Π²ΠΎΠ΄ΡΡΠ²ΠΎ Π·Π°ΠΊΠΎΠ½ΡΠ΅Π½Π½ΠΎΠ³ΠΎ ΠΏΡΠΎΠ΄ΡΠΊΡΠ°, ΡΠ΅ΠΏΡ ΠΏΠΎΡΡΠ°Π²ΠΎΠΊ.
ΠΠΎΠ±Π΅ΡΡ ΠΠ°ΠΉΠ·Π΅Π½ (ΡΠΏ. Kobetsu Kaizen) β ΠΎΠ΄ΠΈΠ½ ΠΈΠ· ΠΌΠ΅ΡΠΎΠ΄ΠΎΠ² ΡΠΎΠΊΡΡΠΈΡΠΎΠ²Π°Π½Π½ΠΎΠ³ΠΎ ΡΠ΅ΡΠ΅Π½ΠΈΡ ΠΏΡΠΎΠ±Π»Π΅ΠΌ. ΠΡ ΠΎΠ΄ΠΈΡ Π² ΡΠΎΡΡΠ°Π² TPM.
ΠΠΎΠ½ΡΡΠΎΠ»ΡΠ½ΡΠ΅ ΠΊΠ°ΡΡΡ Π¨ΡΡ Π°ΡΡΠ° (Control Charts) — ΡΡΠΎ ΠΏΡΠ΅Π΄ΡΡΠ°Π²Π»Π΅Π½ΠΈΠ΅ ΠΏΠΎΠ»ΡΡΠ΅Π½Π½ΡΡ Π² Ρ ΠΎΠ΄Π΅ ΡΠ΅Ρ Π½ΠΎΠ»ΠΎΠ³ΠΈΡΠ΅ΡΠΊΠΎΠ³ΠΎ ΠΏΡΠΎΡΠ΅ΡΡΠ° Π΄Π°Π½Π½ΡΡ Π² Π²ΠΈΠ΄Π΅ Π³ΡΠ°ΡΠΈΠΊΠ° Π² ΠΏΠΎΡΡΠ΄ΠΊΠ΅ ΠΈΡ ΠΏΠΎΡΡΡΠΏΠ»Π΅Π½ΠΈΡ Π²ΠΎ Π²ΡΠ΅ΠΌΠ΅Π½ΠΈ. ΠΠ½ΠΈ ΠΏΠΎΠ·Π²ΠΎΠ»ΡΡΡ ΠΊΠΎΠ½ΡΡΠΎΠ»ΠΈΡΠΎΠ²Π°ΡΡ Ρ Π°ΡΠ°ΠΊΡΠ΅ΡΠΈΡΡΠΈΠΊΠΈ ΠΏΡΠΎΡΠ΅ΡΡΠ° ΠΈ ΠΏΠΎΠΊΠ°Π·ΡΠ²Π°ΡΡ ΠΎΡΠΊΠ»ΠΎΠ½Π΅Π½ΠΈΡ ΠΎΡ ΡΠ΅Π»Π΅Π²ΠΎΠ³ΠΎ Π·Π½Π°ΡΠ΅Π½ΠΈΡ, Π° ΡΠ°ΠΊΠΆΠ΅ ΠΎΡΡΠ°ΠΆΠ°ΡΡ ΡΡΠΎΠ²Π΅Π½Ρ ΡΠΏΡΠ°Π²Π»ΡΠ΅ΠΌΠΎΡΡΠΈ ΠΏΡΠΎΡΠ΅ΡΡΠ°. ΠΡΡΠ³ΠΈΠΌΠΈ ΡΠ»ΠΎΠ²Π°ΠΌΠΈ, ΠΊΠΎΠ½ΡΡΠΎΠ»ΡΠ½ΡΠ΅ ΠΊΠ°ΡΡΡ ΠΏΠΎΠ·Π²ΠΎΠ»ΡΡΡ Π²ΡΡΠ²ΠΈΡΡ Π½Π΅ΡΠ»ΡΡΠ°ΠΉΠ½ΠΎΠ΅ Π²ΠΎΠ·Π΄Π΅ΠΉΡΡΠ²ΠΈΠ΅ Π½Π° ΠΏΡΠΎΡΠ΅ΡΡ, ΠΊΠΎΠ³Π΄Π° ΠΎΠ½ Π΅ΡΠ΅ Π½Π°Ρ ΠΎΠ΄ΠΈΡΡΡ Π² Π³ΡΠ°Π½ΠΈΡΠ°Ρ Π΄ΠΎΠΏΡΡΠΊΠ°.
ΠΠΈΠ½ Π¨Π΅ΡΡΡ Π‘ΠΈΠ³ΠΌΠ° (Lean Six Sigma) β ΠΎΠ±ΡΠ΅Π΄ΠΈΠ½Π΅Π½ΠΈΠ΅ ΠΊΠΎΠ½ΡΠ΅ΠΏΡΠΈΠΉ ΠΠ΅ΡΠ΅ΠΆΠ»ΠΈΠ²ΠΎΠ΅ ΠΏΡΠΎΠΈΠ·Π²ΠΎΠ΄ΡΡΠ²ΠΎ ΠΈ Π¨Π΅ΡΡΡ ΡΠΈΠ³ΠΌΠ°. ΠΠΊΠ»Π°Π΄ ΠΠΈΠ½ β ΡΠΊΠΎΡΠΎΡΡΡ, Π¨Π΅ΡΡΡ Π‘ΠΈΠ³ΠΌΠ° ΡΠΏΠ΅ΡΠΈΠ°Π»ΠΈΠ·ΠΈΡΡΠ΅ΡΡΡ Π½Π° ΡΡΠ°Π±ΠΈΠ»ΠΈΠ·Π°ΡΠΈΠΈ, Ρ.Π΅. ΡΡΡΡΠ°Π½Π΅Π½ΠΈΠΈ Π²Π°ΡΠΈΠ°ΡΠΈΠΈ.
ΠΠΎΠ³ΠΈΡΡΠΈΡΠ΅ΡΠΊΠΈΠΉ ΠΏΠΎΠ΅Π·Π΄, ΠΠΈΡΡΡΡΠΌΠ°ΡΠΈ (Logistic Train, Mizusumashi) β ΡΠΏΠΎΡΠΎΠ± ΠΎΡΠ³Π°Π½ΠΈΠ·Π°ΡΠΈΠΈ ΡΠ½Π°Π±ΠΆΠ΅Π½ΠΈΡ ΡΡΠ°ΡΡΠΊΠΎΠ² ΡΡΡΡΠ΅ΠΌ ΠΈ Π²ΡΠ²ΠΎΠ·Π° Π³ΠΎΡΠΎΠ²ΠΎΠΉ ΠΏΡΠΎΠ΄ΡΠΊΡΠΈΠΈ, Ρ ΠΈΡΠΏΠΎΠ»ΡΠ·ΠΎΠ²Π°Π½ΠΈΠ΅ΠΌ ΡΡΠ°Π½ΡΠΏΠΎΡΡΠ°, ΡΠ°Π±ΠΎΡΠ°ΡΡΠ΅Π³ΠΎ ΠΏΠΎ ΡΡΠ°Π½Π΄Π°ΡΡΠ½ΠΎΠΌΡ Π³ΡΠ°ΡΠΈΠΊΡ.
ΠΠ΅ΡΠΎΠ΄Ρ Π°Π½Π°Π»ΠΈΠ·Π° ΠΈ ΡΠ΅ΡΠ΅Π½ΠΈΡ ΠΏΡΠΎΠ±Π»Π΅ΠΌ (Problem Solving Tools) β ΠΈΠ½ΡΡΡΡΠΌΠ΅Π½ΡΡ ΠΏΠΎΠ΄Π΄Π΅ΡΠΆΠΊΠΈ ΡΠΈΠΊΠ»Π° PDCA/ DMAIC. ΠΠ΅ΡΠ΅ΡΠ΅Π½Ρ ΠΎΡΠ΅Π½Ρ Π·Π½Π°ΡΠΈΡΠ΅Π»Π΅Π½ ΠΈ Π²ΠΊΠ»ΡΡΠ°Π΅Ρ ΠΈΠ½ΡΡΡΡΠΌΠ΅Π½ΡΡ ΠΎΠΏΡΠ΅Π΄Π΅Π»Π΅Π½ΠΈΡ ΠΏΡΠΎΠ±Π»Π΅ΠΌ (5W2H, SIPOC, VoC), ΠΈΠ·ΠΌΠ΅ΡΠ΅Π½ΠΈΡ (ΠΠΎΠ½ΡΡΠΎΠ»ΡΠ½ΡΠΉ Π»ΠΈΡΡΠΎΠΊ), Π°Π½Π°Π»ΠΈΠ·Π° (ΠΠΈΠ°Π³ΡΠ°ΠΌΠΌΠ° ΠΠ°ΡΠ΅ΡΠΎ, ΠΠΈΠ°Π³ΡΠ°ΠΌΠΌΠ° ΠΡΠΈΠΊΠ°Π²Ρ, FMEA), ΡΠ΅Π°Π»ΠΈΠ·Π°ΡΠΈΠΈ ΡΠ»ΡΡΡΠ΅Π½ΠΈΠΉ (ΠΠ»Π°Π½ Π΄Π΅ΠΉΡΡΠ²ΠΈΠΉ) ΠΈ ΠΌΠΎΠ½ΠΈΡΠΎΡΠΈΠ½Π³Π° (ΠΠΎΠ½ΡΡΠΎΠ»ΡΠ½ΡΠ΅ ΠΊΠ°ΡΡΡ Π¨ΡΡ Π°ΡΡΠ°, ΠΠΈΡΡΠΎΠ³ΡΠ°ΠΌΠΌΠ°, ΠΠΎΠ½ΠΈΡΠΎΡ ΠΏΠΎΠΊΠ°Π·Π°ΡΠ΅Π»Ρ).
ΠΠΎΠ»ΠΎΠΊΠΎΠ²ΠΎΠ·, ΠΠΈΠ»ΠΊΡΠ°Π½ (Milkrun) β ΠΏΡΠΈΠ½ΡΠΈΠΏ ΠΎΡΠ³Π°Π½ΠΈΠ·Π°ΡΠΈΠΈ ΡΠ°Π±ΠΎΡΡ ΡΡΠ°Π½ΡΠΏΠΎΡΡΠ° ΠΏΡΠ΅Π΄ΡΡΠΌΠ°ΡΡΠΈΠ²Π°ΡΡΠΈΠΉ ΡΡΠ°Π½Π΄Π°ΡΡΠ½ΡΠ΅ ΠΌΠ°ΡΡΡΡΡΡ, ΠΏΠΎΠ΄ΠΎΠ±Π½ΠΎ ΠΌΠΎΠ»ΠΎΠΊΠΎΠ²ΠΎΠ·Ρ. ΠΡΠΏΠΎΠ»ΡΠ·ΡΠ΅ΡΡΡ Π΄Π»Ρ ΡΠ½ΠΈΠΆΠ΅Π½ΠΈΡ ΠΏΠΎΡΠ΅ΡΡ ΠΏΡΠΈ ΠΎΡΡΡΠ΅ΡΡΠ²Π»Π΅Π½ΠΈΠΈ ΠΏΠ΅ΡΠ΅Π²ΠΎΠ·ΠΎΠΊ ΡΡΡΡΡ ΠΈ Π³ΠΎΡΠΎΠ²ΠΎΠΉ ΠΏΡΠΎΠ΄ΡΠΊΡΠΈΠΈ ΡΠΎΠ±ΡΡΠ²Π΅Π½Π½ΡΠΌ ΡΡΠ°Π½ΡΠΏΠΎΡΡΠΎΠΌ.
ΠΠ°Π±ΠΎΡ ΠΠΆΡΠ½Π΄ΠΆΠΎ (Junjo) β ΠΈΠ½ΡΠΎΡΠΌΠ°ΡΠΈΠΎΠ½Π½Π°Ρ ΡΠΈΡΡΠ΅ΠΌΠ°, ΠΏΡΠ΅Π΄ΡΡΠΌΠ°ΡΡΠΈΠ²Π°ΡΡΠ°Ρ ΡΠ½Π°Π±ΠΆΠ΅Π½ΠΈΠ΅ Π½Π°Π±ΠΎΡΠ°ΠΌΠΈ Π΄Π΅ΡΠ°Π»Π΅ΠΉ Ρ ΡΠ°Π·Π»ΠΈΡΠ½ΡΡ ΡΡΠ°ΡΡΠΊΠΎΠ² ΠΏΠΎ ΠΏΡΠΈΠ½ΡΠΈΠΏΡ Β«Π’ΠΎΡΠ½ΠΎ Π²ΠΎΠ²ΡΠ΅ΠΌΡΒ».
ΠΠ±ΡΡΠ΅Π½ΠΈΠ΅ Π½Π° ΡΠ°Π±ΠΎΡΠ΅ΠΌ ΠΌΠ΅ΡΡΠ΅ (Training Within Industry, TWI) β ΠΌΠ΅ΡΠΎΠ΄ΠΈΠΊΠ° ΠΏΠΎΠ΄Π³ΠΎΡΠΎΠ²ΠΊΠΈ ΠΏΠ΅ΡΡΠΎΠ½Π°Π»Π°, Π²ΠΊΠ»ΡΡΠ°ΡΡΠ°Ρ ΠΏΠΎΠ΄Ρ ΠΎΠ΄Ρ ΠΊ ΠΎΠ±ΡΡΠ΅Π½ΠΈΡ ΠΏΠ΅ΡΡΠΎΠ½Π°Π»Π°, ΡΠ»ΡΡΡΠ΅Π½ΠΈΡ ΠΌΠ΅ΡΠΎΠ΄ΠΎΠ² ΡΠ°Π±ΠΎΡΡ, ΠΏΠΎΠ΄Π΄Π΅ΡΠΆΠΊΠΈ Ρ ΠΎΡΠΎΡΠ΅ΠΉ Π°ΡΠΌΠΎΡΡΠ΅ΡΡ Π² ΠΊΠΎΠ»Π»Π΅ΠΊΡΠΈΠ²Π΅. Π¨ΠΈΡΠΎΠΊΠΎ ΠΈΡΠΏΠΎΠ»ΡΠ·ΠΎΠ²Π°Π»Π°ΡΡ Π² Π‘Π¨Π Π²ΠΎ Π²ΡΠ΅ΠΌΡ ΠΡΠΎΡΠΎΠΉ ΠΠΈΡΠΎΠ²ΠΎΠΉ Π²ΠΎΠΉΠ½Ρ. ΠΠ½ΠΎΠ³ΠΈΠ΅ ΡΠΊΡΠΏΠ΅ΡΡΡ ΡΡΠΈΡΠ°ΡΡ TWI Π±Π°Π·ΠΎΠΉ Π΄Π»Ρ ΡΠΎΡΠΌΠΈΡΠΎΠ²Π°Π½ΠΈΡ ΠΏΡΠΎΠΈΠ·Π²ΠΎΠ΄ΡΡΠ²Π΅Π½Π½ΠΎΠΉ ΡΠΈΡΡΠ΅ΠΌΡ Π’ΠΎΠΉΠΎΡΡ.
ΠΠ±ΡΠ°Ρ ΡΡΡΠ΅ΠΊΡΠΈΠ²Π½ΠΎΡΡΡ ΠΎΠ±ΠΎΡΡΠ΄ΠΎΠ²Π°Π½ΠΈΡ (Overall Equipment Efficiency, OEE) β ΠΈΠ½ΡΠ΅Π³ΡΠ°Π»ΡΠ½ΡΠΉ ΠΏΠΎΠΊΠ°Π·Π°ΡΠ΅Π»Ρ, Ρ Π°ΡΠ°ΠΊΡΠ΅ΡΠΈΠ·ΡΡΡΠΈΠΉ ΡΡΡΠ΅ΠΊΡΠΈΠ²Π½ΠΎΡΡΡ ΠΈΡΠΏΠΎΠ»ΡΠ·ΠΎΠ²Π°Π½ΠΈΡ ΠΎΠ±ΠΎΡΡΠ΄ΠΎΠ²Π°Π½ΠΈΡ. ΠΡΡΠ°ΠΆΠ°Π΅Ρ Π΄ΠΎΡΡΡΠΏΠ½ΠΎΡΡΡ ΠΎΠ±ΠΎΡΡΠ΄ΠΎΠ²Π°Π½ΠΈΡ, Π΅Π³ΠΎ ΠΏΡΠΎΠΈΠ·Π²ΠΎΠ΄ΠΈΡΠ΅Π»ΡΠ½ΠΎΡΡΡ, Π° ΡΠ°ΠΊΠΆΠ΅ ΠΊΠ°ΡΠ΅ΡΡΠ²ΠΎ ΠΏΡΠΎΠΈΠ·Π²Π΅Π΄Π΅Π½Π½ΠΎΠΉ ΠΏΡΠΎΠ΄ΡΠΊΡΠΈΠΈ. ΠΠΠ ΡΠ²Π»ΡΠ΅ΡΡΡ Π½Π°ΠΈΠ±ΠΎΠ»Π΅Π΅ ΡΠ°ΡΠΏΡΠΎΡΡΡΠ°Π½Π΅Π½Π½ΡΠΌ ΠΏΠΎΠΊΠ°Π·Π°ΡΠ΅Π»Π΅ΠΌ ΠΊΠΎΠΌΠΏΠ»Π΅ΠΊΡΠ½ΠΎΠΉ ΠΎΡΠ΅Π½ΠΊΠΈ ΡΡΡΠ΅ΠΊΡΠΈΠ²Π½ΠΎΡΡΠΈ ΠΈΡΠΏΠΎΠ»ΡΠ·ΡΠ΅ΠΌΠΎΠ³ΠΎ ΠΎΠ±ΠΎΡΡΠ΄ΠΎΠ²Π°Π½ΠΈΡ.
ΠΠ»Π°Π½ΠΎΠ²ΠΎΠ΅ ΠΎΠ±ΡΠ»ΡΠΆΠΈΠ²Π°Π½ΠΈΠ΅ ΠΎΠ±ΠΎΡΡΠ΄ΠΎΠ²Π°Π½ΠΈΡ (Planned Maintenance, TPM PM) β ΠΊΠΎΠΌΠΏΠ»Π΅ΠΊΡ ΠΏΠ»Π°Π½ΠΎΠ²ΡΡ ΠΌΠ΅ΡΠΎΠΏΡΠΈΡΡΠΈΠΉ Π½Π°ΠΏΡΠ°Π²Π»Π΅Π½Π½ΡΡ Π½Π° ΠΎΠ±Π΅ΡΠΏΠ΅ΡΠ΅Π½ΠΈΠ΅ Π½Π°Π΄Π΅ΠΆΠ½ΠΎΡΡΠΈ ΠΎΠ±ΠΎΡΡΠ΄ΠΎΠ²Π°Π½ΠΈΡ. ΠΡΠΎΡΠ΅Π΄ΡΡΡ ΠΏΠ»Π°Π½ΠΎΠ²ΠΎ-ΠΏΡΠ΅Π΄ΡΠΏΡΠ΅Π΄ΠΈΡΠ΅Π»ΡΠ½ΡΡ ΡΠ΅ΠΌΠΎΠ½ΡΠΎΠ² Π½Π°ΠΏΡΠ°Π²Π»Π΅Π½Π½Ρ Π½Π° ΠΏΠΎΠ²ΡΡΠ΅Π½ΠΈΠ΅ MTBF ΠΈ ΡΠΎΠΊΡΠ°ΡΠ΅Π½ΠΈΠ΅ MTTR.
ΠΠΎΡΠ΅ΡΠΈ, ΠΏΡΠΎΠΈΠ·Π²ΠΎΠ΄ΡΡΠ²Π΅Π½Π½ΡΠ΅ ΠΏΠΎΡΠ΅ΡΠΈ (Waste, Muda) β ΡΡΠΎ Π΄Π΅ΠΉΡΡΠ²ΠΈΡ, ΠΊΠΎΡΠΎΡΡΠ΅ ΡΡΠ΅Π±ΡΡΡ Π·Π°ΡΡΠ°Ρ ΡΠ΅ΡΡΡΡΠΎΠ², Π½ΠΎ Π½Π΅ Π΄ΠΎΠ±Π°Π²Π»ΡΡΡ ΠΈΠ·Π΄Π΅Π»ΠΈΡ ΠΏΠΎΡΡΠ΅Π±ΠΈΡΠ΅Π»ΡΡΠΊΠΈΡ ΡΠ²ΠΎΠΉΡΡΠ². ΠΡΠΎΡΠΈΠ²ΠΎΠΏΠΎΠ»ΠΎΠΆΠ½ΠΎΠ΅ ΠΏΠΎΠ½ΡΡΠΈΠ΅ β ΡΠ΅Π½Π½ΠΎΡΡΡ, ΡΡΠΎ ΡΠ΅ Π΄Π΅ΠΉΡΡΠ²ΠΈΡ, ΠΊΠΎΡΠΎΡΡΠ΅ ΠΏΡΠΈΠ±Π»ΠΈΠΆΠ°ΡΡ ΠΈΠ·Π΄Π΅Π»ΠΈΠ΅ ΠΊ ΠΊΠ»ΠΈΠ΅Π½ΡΡ. Π Π°Π·Π»ΠΈΡΠ°ΡΡ Π΅ΡΠ΅ Π΄Π²Π° Π²ΠΈΠ΄Π° ΠΏΠΎΡΠ΅ΡΡ. ΠΠ΅ΡΠ°Π²Π½ΠΎΠΌΠ΅ΡΠ½ΠΎΡΡΡ (ΠΡΡΠ°, Mura), ΠΈΠ·ΠΌΠ΅Π½ΡΠΈΠ²ΠΎΡΡΡ Π² ΠΌΠ΅ΡΠΎΠ΄Π°Ρ ΡΠ°Π±ΠΎΡΡ ΠΈ ΡΠ΅Π·ΡΠ»ΡΡΠ°ΡΠ°Ρ ΠΏΡΠΎΡΠ΅ΡΡΠ°. ΠΠ·Π»ΠΈΡΠ΅ΠΊ (ΠΡΡΠΈ, Muri), ΠΏΠ΅ΡΠ΅Π³ΡΡΠ·ΠΊΠ° ΡΠ΅Π»ΠΎΠ²Π΅ΠΊΠ° ΠΈΠ»ΠΈ ΠΎΠ±ΠΎΡΡΠ΄ΠΎΠ²Π°Π½ΠΈΡ, Π½Π΅ΡΠ°Π·ΡΠΌΠ½ΠΎΡΡΡ.
ΠΡΠΈΠ½ΡΠΈΠΏ Π‘ΡΠΏΠ΅ΡΠΌΠ°ΡΠΊΠ΅ΡΠ° (Supermarket) β ΡΠΏΠΎΡΠΎΠ± ΠΎΡΠ³Π°Π½ΠΈΠ·Π°ΡΠΈΠΈ ΡΠ½Π°Π±ΠΆΠ΅Π½ΠΈΡ ΠΏΡΠΎΠΈΠ·Π²ΠΎΠ΄ΡΡΠ²Π΅Π½Π½ΡΡ ΡΡΠ°ΡΡΠΊΠΎΠ² Ρ ΡΡΠ΅ΡΠΎΠΌ ΠΈΡ ΡΠ΅Π°Π»ΡΠ½ΠΎΠΉ ΠΏΠΎΡΡΠ΅Π±Π½ΠΎΡΡΠΈ. ΠΡΠΈΠΌΠ΅Π½ΡΠ΅ΡΡΡ Π΄Π»Ρ ΡΠ΅Π°Π»ΠΈΠ·Π°ΡΠΈΠΈ Π²ΡΡΡΠ³ΠΈΠ²Π°ΡΡΠ΅ΠΉ ΡΠΈΡΡΠ΅ΠΌΡ ΠΏΡΠΎΠΈΠ·Π²ΠΎΠ΄ΡΡΠ²Π°.
ΠΡΠΎΠ΅ΠΊΡΠΈΡΠΎΠ²Π°Π½ΠΈΠ΅ ΠΏΡΠΎΠΈΠ·Π²ΠΎΠ΄ΡΡΠ²Π΅Π½Π½ΡΡ Π»ΠΈΠ½ΠΈΠΉ (Layout Design) β ΡΠΏΠΎΡΠΎΠ± ΠΏΡΠΎΠ΅ΠΊΡΠΈΡΠΎΠ²Π°Π½ΠΈΡ ΠΏΡΠΎΠΈΠ·Π²ΠΎΠ΄ΡΡΠ²Π΅Π½Π½ΡΡ Π»ΠΈΠ½ΠΈΠΉ Π΄Π»Ρ ΠΌΠΈΠ½ΠΈΠΌΠΈΠ·Π°ΡΠΈΠΈ ΠΏΠΎΡΠ΅ΡΡ ΠΏΡΠΈ ΠΈΡ ΠΏΡΠΎΠΌΡΡΠ»Π΅Π½Π½ΠΎΠΉ ΡΠΊΡΠΏΠ»ΡΠ°ΡΠ°ΡΠΈΠΈ.
ΠΡΠΎΠ΅ΠΊΡΠΈΡΠΎΠ²Π°Π½ΠΈΠ΅ ΡΠΊΠ»Π°Π΄Π° (Warehouse Design) β ΡΠ°ΡΡΠ΅Ρ ΠΏΠ°ΡΠ°ΠΌΠ΅ΡΡΠΎΠ² ΡΠΊΠ»Π°Π΄Π° Π΄Π»Ρ ΠΎΠΏΡΠΈΠΌΠΈΠ·Π°ΡΠΈΠΈ Π²Π·Π°ΠΈΠΌΠΎΠ΄Π΅ΠΉΡΡΠ²ΠΈΡ Ρ Π²Π½Π΅ΡΠ½ΠΈΠΌΠΈ ΠΈ Π²Π½ΡΡΡΠ΅Π½Π½ΠΈΠΌΠΈ ΠΊΠΎΠ½ΡΡΠ°Π³Π΅Π½ΡΠ°ΠΌΠΈ, Π²ΡΠΏΠΎΠ»Π½Π΅Π½ΠΈΡ ΡΠΊΠ»Π°Π΄ΡΠΊΠΈΡ ΠΎΠΏΠ΅ΡΠ°ΡΠΈΠΉ ΠΈ ΠΎΠ±Π΅ΡΠΏΠ΅ΡΠ΅Π½ΠΈΡ Π±Π΅Π·ΠΎΠΏΠ°ΡΠ½ΠΎΡΡΠΈ.
ΠΡΠΎΠ΅ΠΊΡΠΈΡΠΎΠ²Π°Π½ΠΈΠ΅ ΡΠ΅ΠΏΠΎΡΠ΅ΠΊ ΠΏΠΎΡΡΠ°Π²ΠΎΠΊ (Supply Chain Design) β ΠΈΠ½ΡΠ΅Π³ΡΠΈΡΠΎΠ²Π°Π½Π½ΡΠΉ ΠΏΠΎΠ΄Ρ ΠΎΠ΄ ΠΊ ΡΠ°ΡΡΠ΅ΡΡ ΠΏΠ°ΡΠ°ΠΌΠ΅ΡΡΠΎΠ² Π²ΡΠ΅Π³ΠΎ ΠΏΠΎΡΠΎΠΊΠ° ΡΠΎΠ·Π΄Π°Π½ΠΈΡ ΡΠ΅Π½Π½ΠΎΡΡΠΈ, Π²ΠΊΠ»ΡΡΠ°Ρ ΠΌΠ°ΡΠ΅ΡΠΈΠ°Π»ΡΠ½ΡΠΉ ΠΏΠΎΡΠΎΠΊΠΈ ΠΈ ΠΏΡΠΎΠΈΠ·Π²ΠΎΠ΄ΡΡΠ²Π΅Π½Π½ΡΠ΅ ΠΌΠΎΡΠ½ΠΎΡΡΠΈ Π²ΡΠ΅Ρ Π·Π½Π°ΡΠΈΠΌΡΡ ΡΡΠ°ΡΡΠ½ΠΈΠΊΠΎΠ² ΡΠ΅ΠΏΠΎΡΠΊΠΈ.
ΠΡΠΎΠΈΠ·Π²ΠΎΠ΄ΡΡΠ²Π΅Π½Π½Π°Ρ ΡΡΠ΅ΠΉΠΊΠ° (Cell) β ΡΠΏΠΎΡΠΎΠ± ΠΊΠΎΠΌΠΏΠΎΠ½ΠΎΠ²ΠΊΠΈ ΡΠ°Π±ΠΎΡΠΈΡ ΠΌΠ΅ΡΡ Ρ ΡΡΠ΅ΡΠΎΠΌ ΠΌΠΈΠ½ΠΈΠΌΠΈΠ·Π°ΡΠΈΠΈ ΠΏΠΎΡΠ΅ΡΡ Π² ΠΏΠΎΡΠΎΠΊΠ΅ ΡΠΎΠ·Π΄Π°Π½ΠΈΡ ΡΠ΅Π½Π½ΠΎΡΡΠΈ.
ΠΡΠΎΡΡΠ°Ρ Π°Π²ΡΠΎΠΌΠ°ΡΠΈΠ·Π°ΡΠΈΡ (Low Cost Automation, LCA) β ΠΏΡΠΈΠΌΠ΅Π½Π΅Π½ΠΈΠ΅ Π² ΡΠ°Π±ΠΎΡΠ΅ ΠΏΡΠΎΡΡΡΡ ΠΏΡΠΈΡΠΏΠΎΡΠΎΠ±Π»Π΅Π½ΠΈΠΉ Π΄Π»Ρ ΠΎΠ±Π»Π΅Π³ΡΠ΅Π½ΠΈΡ ΡΡΡΠ΄Π°, ΠΏΠΎΠ²ΡΡΠ΅Π½ΠΈΡ ΠΏΡΠΎΠΈΠ·Π²ΠΎΠ΄ΠΈΡΠ΅Π»ΡΠ½ΠΎΡΡΠΈ, ΡΠΎΠΎΡΠ²Π΅ΡΡΡΠ²ΠΈΡ Π²ΡΠ΅ΠΌΠ΅Π½ΠΈ ΡΠ°ΠΊΡΠ° ΠΏΡΠΎΠΈΠ·Π²ΠΎΠ΄ΡΡΠ²Π°.
Π Π°Π½Π½Π΅Π΅ ΠΎΠ±ΡΠ»ΡΠΆΠΈΠ²Π°Π½ΠΈΠ΅ ΠΎΠ±ΠΎΡΡΠ΄ΠΎΠ²Π°Π½ΠΈΡ (Early Management) β ΠΏΠΎΠ΄Ρ ΠΎΠ΄ ΠΊ Π·Π°ΠΏΡΡΠΊΡ ΠΎΠ±ΠΎΡΡΠ΄ΠΎΠ²Π°Π½ΠΈΡ Π² ΠΏΡΠΎΠΌΡΡΠ»Π΅Π½Π½ΡΡ ΡΠΊΡΠΏΠ»ΡΠ°ΡΠ°ΡΠΈΡ, ΠΎΠ±Π΅ΡΠΏΠ΅ΡΠΈΠ²Π°ΡΡΠΈΠΉ Β«Π²Π΅ΡΡΠΈΠΊΠ°Π»ΡΠ½ΡΠΉ ΡΡΠ°ΡΡΒ», Ρ.Π΅. ΠΌΠΈΠ½ΠΈΠΌΠ°Π»ΡΠ½ΠΎΠ΅ Π²ΡΠ΅ΠΌΡ Π²ΡΡ ΠΎΠ΄Π° Π½Π° ΠΏΡΠΎΠ΅ΠΊΡΠ½ΡΡ ΠΌΠΎΡΠ½ΠΎΡΡΡ. Π Π°Π½Π½Π΅Π΅ ΠΎΠ±ΡΠ»ΡΠΆΠΈΠ²Π°Π½ΠΈΠ΅ ΠΎΡΠΈΠ΅Π½ΡΠΈΡΠΎΠ²Π°Π½ΠΎ Π½Π° Π²ΡΡΠ²Π»Π΅Π½ΠΈΠ΅ Π²ΡΠ΅Ρ Π²ΠΎΠ·ΠΌΠΎΠΆΠ½ΡΡ ΠΏΡΠΎΠ±Π»Π΅ΠΌ Ρ ΡΠΊΡΠΏΠ»ΡΠ°ΡΠ°ΡΠΈΠ΅ΠΉ ΠΈ ΠΎΠ±ΡΠ»ΡΠΆΠΈΠ²Π°Π½ΠΈΠ΅ΠΌ ΠΎΠ±ΠΎΡΡΠ΄ΠΎΠ²Π°Π½ΠΈΡ Π½Π° ΡΡΠ°Π΄ΠΈΠΈ ΠΏΡΠΎΠ΅ΠΊΡΠΈΡΠΎΠ²Π°Π½ΠΈΡ.
Π‘Π°ΠΌΠΎΠΊΠΎΠ½ΡΡΠΎΠ»Ρ β ΡΡΠ΅Π΄ΡΡΠ²Π° ΠΈ ΠΌΠ΅ΡΠΎΠ΄Ρ Π΄Π»Ρ ΠΎΠΏΡΠ΅Π΄Π΅Π»Π΅Π½ΠΈΡ Π΄Π΅ΡΠ΅ΠΊΡΠ°, Π΅Π³ΠΎ ΠΈΡΠΏΡΠ°Π²Π»Π΅Π½ΠΈΡ ΠΈΠ»ΠΈ ΠΈΠ·ΠΎΠ»ΡΡΠΈΠΈ, ΠΊΠΎΡΠΎΡΡΠ΅ ΠΈΡΠΏΠΎΠ»ΡΠ·ΡΡΡΡΡ ΡΠ°ΠΌΠΈΠΌ ΠΎΠΏΠ΅ΡΠ°ΡΠΎΡΠΎΠΌ.
Π‘Π΅ΠΊΠ²Π΅Π½ΡΠΎΡ Π½Π° ΠΏΡΠΎΠΈΠ·Π²ΠΎΠ΄ΡΡΠ²Π΅Π½Π½ΠΎΠΉ Π»ΠΈΠ½ΠΈΠΈ β ΡΠΈΠ·ΠΈΡΠ΅ΡΠΊΠΎΠ΅ ΡΡΡΡΠΎΠΉΡΡΠ²ΠΎ Π½Π° ΠΏΡΠΎΠΈΠ·Π²ΠΎΠ΄ΡΡΠ²Π΅Π½Π½ΠΎΠΌ ΡΡΠ°ΡΡΠΊΠ΅ Π΄Π»Ρ ΠΎΡΠ³Π°Π½ΠΈΠ·Π°ΡΠΈΠΈ ΠΎΡΠ΅ΡΠ΅Π΄ΠΈ Π·Π°ΠΊΠ°Π·ΠΎΠ² Π² ΡΠΎΠΎΡΠ²Π΅ΡΡΡΠ²ΠΈΠΈ Ρ ΠΏΡΠΈΠ½ΡΠΈΠΏΠΎΠΌ FIFO.
Π‘ΠΈΡΡΠ΅ΠΌΠ° 5Π‘ (5Π‘, 5S system) β ΠΏΡΡΡ ΡΠ°Π³ΠΎΠ² ΠΏΠΎ ΠΎΡΠ³Π°Π½ΠΈΠ·Π°ΡΠΈΠΈ ΡΡΡΠ΅ΠΊΡΠΈΠ²Π½ΠΎΠ³ΠΎ ΠΈ Π±Π΅Π·ΠΎΠΏΠ°ΡΠ½ΠΎΠ³ΠΎ ΡΠ°Π±ΠΎΡΠ΅Π³ΠΎ ΠΏΡΠΎΡΡΡΠ°Π½ΡΡΠ²Π°. 5S β ΡΡΠΎ ΠΌΠ½Π΅ΠΌΠΎΠ½ΠΈΡΠ΅ΡΠΊΠΈΠΉ ΠΊΠΎΠ΄, ΡΠΎΠ΄Π΅ΡΠΆΠ°ΡΠΈΠΉ ΠΏΡΡΡ ΡΠ»ΠΎΠ² Π½Π°ΡΠΈΠ½Π°ΡΡΠΈΡ ΡΡ Π½Π° S (Π² ΠΎΡΠΈΠ³ΠΈΠ½Π°Π»Π΅, ΠΏΡΡΡ ΡΠΏΠΎΠ½ΡΠΊΠΈΡ ΡΠ»ΠΎΠ²: ΡΠ΅ΠΉΡΠΈ, ΡΠ΅ΠΉΡΠΎΠ½, ΡΠ΅ΠΉΡΠΎ, ΡΠ°ΠΉΠΊΠ΅ΡΡ, ΡΠΈΡΡΠΊΠ΅). Π ΡΡΡΡΠΊΠΎΠΉ Π²Π΅ΡΡΠΈΠΈ 5Π‘ ΠΎΠ·Π½Π°ΡΠ°Π΅Ρ ΠΏΡΡΡ ΡΠ°Π³ΠΎΠ²: Π‘ΠΎΡΡΠΈΡΠΎΠ²ΠΊΠ°, Π‘Π²ΠΎΠΈ ΠΌΠ΅ΡΡΠ° Π΄Π»Ρ Π²ΡΠ΅Π³ΠΎ, Π‘ΠΎΠ΄Π΅ΡΠΆΠ°Π½ΠΈΠ΅ Π² ΡΠΈΡΡΠΎΡΠ΅, Π‘ΡΠ°Π½Π΄Π°ΡΡΠΈΠ·Π°ΡΠΈΡ, Π‘Π°ΠΌΠΎΠ΄ΠΈΡΡΠΈΠΏΠ»ΠΈΠ½Π° ΠΈ Π‘ΠΎΠ²Π΅ΡΡΠ΅Π½ΡΡΠ²ΠΎΠ²Π°Π½ΠΈΠ΅.
Π‘ΡΠ΅Π΄Π½Π΅Π΅ Π²ΡΠ΅ΠΌΡ Π²ΠΎΡΡΡΠ°Π½ΠΎΠ²Π»Π΅Π½ΠΈΡ ΠΏΠΎΡΠ»Π΅ ΠΎΡΠΊΠ°Π·ΠΎΠ²(Mean Time To Repair, MTTR) — Π½Π°ΡΡΠ΄Ρ Ρ MTBF, ΠΎΡΠ½ΠΎΡΠΈΡΡΡ ΠΊ ΠΎΡΠ½ΠΎΠ²Π½ΡΠΌ ΠΏΠΎΠΊΠ°Π·Π°ΡΠ΅Π»ΡΠΌ, Ρ Π°ΡΠ°ΠΊΡΠ΅ΡΠΈΠ·ΡΡΡΠΈΠΌ ΡΡΡΠ΅ΠΊΡΠΈΠ²Π½ΠΎΡΡΡ ΡΠ°Π±ΠΎΡΡ ΡΠ΅ΠΌΠΎΠ½ΡΠ½ΠΎΠΉ ΡΠ»ΡΠΆΠ±Ρ ΠΎΡΠ³Π°Π½ΠΈΠ·Π°ΡΠΈΠΈ.
Π‘ΡΠ΅Π΄Π½Π΅Π΅ Π²ΡΠ΅ΠΌΡ ΠΌΠ΅ΠΆΠ΄Ρ ΠΎΡΠΊΠ°Π·Π°ΠΌΠΈ (Mean Time Between Failures, MTBF) β Π½Π°ΡΡΠ΄Ρ Ρ MTTR, ΠΎΡΠ½ΠΎΡΠΈΡΡΡ ΠΊ ΠΎΡΠ½ΠΎΠ²Π½ΡΠΌ ΠΏΠΎΠΊΠ°Π·Π°ΡΠ΅Π»ΡΠΌ, Ρ Π°ΡΠ°ΠΊΡΠ΅ΡΠΈΠ·ΡΡΡΠΈΠΌ ΡΡΡΠ΅ΠΊΡΠΈΠ²Π½ΠΎΡΡΡ ΡΠ°Π±ΠΎΡΡ ΡΠ΅ΠΌΠΎΠ½ΡΠ½ΠΎΠΉ ΡΠ»ΡΠΆΠ±Ρ ΠΎΡΠ³Π°Π½ΠΈΠ·Π°ΡΠΈΠΈ.
Π‘ΡΠ°Π½Π΄Π°ΡΡΠΈΠ·Π°ΡΠΈΡ β Π±Π°Π·ΠΎΠ²ΡΠΉ ΠΈΠ½ΡΡΡΡΠΌΠ΅Π½Ρ ΠΎΠ±Π΅ΡΠΏΠ΅ΡΠ΅Π½ΠΈΡ ΠΊΠ°ΡΠ΅ΡΡΠ²Π°. Π‘ΡΠ°Π½Π΄Π°ΡΡ β ΡΡΠΎ ΡΠ°ΠΌΡΠΉ ΠΏΡΠΎΡΡΠΎΠΉ, ΡΡΡΠ΅ΠΊΡΠΈΠ²Π½ΡΠΉ ΠΈ Π±Π΅Π·ΠΎΠΏΠ°ΡΠ½ΡΠΉ ΡΠΏΠΎΡΠΎΠ± Π²ΡΠΏΠΎΠ»Π½Π΅Π½ΠΈΡ ΡΠ°Π±ΠΎΡΡ ΠΈΠ·Π²Π΅ΡΡΠ½ΡΠΉ Π½Π° ΡΠ΅Π³ΠΎΠ΄Π½ΡΡΠ½ΠΈΠΉ Π΄Π΅Π½Ρ.
Π‘ΡΠ°Π½Π΄Π°ΡΡΠΈΠ·ΠΈΡΠΎΠ²Π°Π½Π½Π°Ρ ΡΠ°Π±ΠΎΡΠ° β ΡΠΏΠΎΡΠΎΠ± Π°Π½Π°Π»ΠΈΠ·Π° ΠΈ ΠΎΠΏΡΠΈΠΌΠΈΠ·Π°ΡΠΈΠΈ ΡΠ°Π±ΠΎΡΡ ΠΏΠ΅ΡΡΠΎΠ½Π°Π»Π° ΡΡΠ°ΡΡΠΊΠ° Π² ΡΠΎΠΎΡΠ²Π΅ΡΡΡΠ²ΠΈΠΈ Ρ ΠΈΠ·ΠΌΠ΅Π½ΡΡΡΠΈΠΌΡΡ Π²ΡΠ΅ΠΌΠ΅Π½Π΅ΠΌ ΡΠ°ΠΊΡΠ° ΠΈΠ»ΠΈ ΠΏΡΠΈ ΠΏΠΎΠΈΡΠΊΠ΅ ΡΠ»ΡΡΡΠ΅Π½ΠΈΡ.
Π‘ΡΠ°ΡΠΈΡΡΠΈΡΠ΅ΡΠΊΠΈΠΉ ΠΊΠΎΠ½ΡΡΠΎΠ»Ρ ΠΏΡΠΎΡΠ΅ΡΡΠ° (Statistical Process Control) — ΠΌΠ΅ΡΠΎΠ΄Ρ ΡΡΠ°ΡΠΈΡΡΠΈΡΠ΅ΡΠΊΠΎΠ³ΠΎ ΡΠ΅Π³ΡΠ»ΠΈΡΠΎΠ²Π°Π½ΠΈΡ ΠΏΡΠΎΡΠ΅ΡΡΠΎΠ².
Π’ΠΎΡΠ½ΠΎ ΠΠΎΠ²ΡΠ΅ΠΌΡ (Just in Time) β ΠΏΡΠΈΠ½ΡΠΈΠΏ ΡΠ΅Π³ΡΠ»ΠΈΡΠΎΠ²Π°Π½ΠΈΡ Π²Π½ΡΡΡΠ΅Π½Π½ΠΈΡ ΠΈ Π²Π½Π΅ΡΠ½ΠΈΡ ΠΌΠ°ΡΠ΅ΡΠΈΠ°Π»ΡΠ½ΡΡ ΠΏΠΎΡΠΎΠΊΠΎΠ² Π½Π°ΠΏΡΠ°Π²Π»Π΅Π½Π½ΡΠΉ Π½Π° ΡΠ½ΠΈΠΆΠ΅Π½ΠΈΠ΅ Π·Π°ΠΏΠ°ΡΠΎΠ² ΡΡΡΡΡ, Π½Π΅Π·Π°Π²Π΅ΡΡΠ΅Π½Π½ΠΎΠ³ΠΎ ΠΏΡΠΎΠΈΠ·Π²ΠΎΠ΄ΡΡΠ²Π° ΠΈ Π³ΠΎΡΠΎΠ²ΠΎΠΉ ΠΏΡΠΎΠ΄ΡΠΊΡΠΈΠΈ ΠΈ, ΠΊΠ°ΠΊ ΡΠ»Π΅Π΄ΡΡΠ²ΠΈΠ΅, Π½Π° Π²ΡΡΠ²ΠΎΠ±ΠΎΠΆΠ΄Π΅Π½ΠΈΠ΅ ΠΎΠ±ΠΎΡΠΎΡΠ½ΡΡ ΡΡΠ΅Π΄ΡΡΠ². ΠΡΠ»ΠΈΡΠΈΡΠ΅Π»ΡΠ½ΠΎΠΉ ΠΎΡΠΎΠ±Π΅Π½Π½ΠΎΡΡΡΡ ΡΠ°ΠΊΠΎΠΉ ΡΠΈΡΡΠ΅ΠΌΡ ΡΠ²Π»ΡΠ΅ΡΡΡ ΠΏΠΎΡΠΎΠΊ Π΅Π΄ΠΈΠ½ΠΈΡΠ½ΡΡ ΠΈΠ·Π΄Π΅Π»ΠΈΠΉ (One Piece Flow), ΡΠ²ΠΈΠ΄Π΅ΡΠ΅Π»ΡΡΡΠ²ΡΡΡΠΈΠΉ ΠΎΠ± ΠΎΡΡΡΡΡΡΠ²ΠΈΠΈ Π΄ΠΈΡΠ±Π°Π»Π°Π½ΡΠ° ΠΌΠ΅ΠΆΠ΄Ρ ΡΡΠ°ΡΡΠΊΠ°ΠΌΠΈ, ΠΎΡΡΡΡΡΡΠ²ΠΈΠΈ Π²Π½Π΅ΠΏΠ»Π°Π½ΠΎΠ²ΡΡ ΠΎΡΡΠ°Π½ΠΎΠ²ΠΎΠ², ΡΡΠ°Π±ΠΈΠ»ΡΠ½ΠΎΠΌ ΠΊΠ°ΡΠ΅ΡΡΠ²Π΅. ΠΠ»Ρ Π±Π°Π»Π°Π½ΡΠΈΡΠΎΠ²ΠΊΠΈ ΡΠ°Π±ΠΎΡΡ ΡΡΠ°ΡΡΠΊΠΎΠ² ΠΈΡΠΏΠΎΠ»ΡΠ·ΡΠ΅ΡΡΡ Π²ΡΠ΅ΠΌΡ ΡΠ°ΠΊΡΠ°, ΠΎΠΏΡΠ΅Π΄Π΅Π»ΡΡΡΠ΅Π΅ ΡΠΈΡΠΌ ΡΠ°Π±ΠΎΡΡ ΡΠΎΠΎΡΠ²Π΅ΡΡΡΠ²ΡΡΡΠΈΠΉ ΠΏΠΎΡΡΠ΅Π±Π½ΠΎΡΡΡΠΌ Π²Π½Π΅ΡΠ½ΠΈΡ ΠΏΠΎΡΡΠ΅Π±ΠΈΡΠ΅Π»Π΅ΠΉ.
Π€ΠΎΠΊΡΡΠΈΡΠΎΠ²Π°Π½Π½ΠΎΠ΅ ΡΠ΅ΡΠ΅Π½ΠΈΠ΅ ΠΏΡΠΎΠ±Π»Π΅ΠΌ (Focused Problem Solving) β ΠΏΡΠΈΠ½ΡΠΈΠΏ Π°ΠΊΡΠ΅Π½ΡΠΈΡΠΎΠ²Π°Π½Π½ΠΎΠ³ΠΎ ΡΠ΅ΡΠ΅Π½ΠΈΡ ΡΡΡΠ΅ΡΡΠ²Π΅Π½Π½ΡΡ ΠΏΡΠΎΠ±Π»Π΅ΠΌ Ρ ΠΊΠ°ΡΠ΅ΡΡΠ²ΠΎΠΌ, ΠΎΠ±ΠΎΡΡΠ΄ΠΎΠ²Π°Π½ΠΈΠ΅ΠΌ, Π±Π΅Π·ΠΎΠΏΠ°ΡΠ½ΠΎΡΡΡΡ ΠΈ ΠΏΡ. Π Π΅ΡΠ΅Π½ΠΈΠ΅ ΠΏΡΠΎΠ±Π»Π΅ΠΌ ΠΏΡΠΎΠΈΡΡ ΠΎΠ΄ΠΈΡ ΠΏΡΡΠ΅ΠΌ ΡΡΡΡΠ°Π½Π΅Π½ΠΈΡ ΠΊΠΎΡΠ΅Π½Π½ΡΡ ΠΏΡΠΈΡΠΈΠ½ ΠΏΡΠΎΠ±Π»Π΅ΠΌΡ (ΠΏΠ΅ΡΠ²ΠΎΠΏΡΠΈΡΠΈΠ½). Π ΠΌΠ΅ΡΠΎΠ΄ΠΈΠΊΠ°ΠΌ, ΠΈΡΠΏΠΎΠ»ΡΠ·ΡΡΡΠΈΠΌ ΠΏΡΠΈΠ½ΡΠΈΠΏ ΡΠΎΠΊΡΡΠΈΡΠΎΠ²Π°Π½Π½ΠΎΠ³ΠΎ ΡΠ΅ΡΠ΅Π½ΠΈΡ ΠΏΡΠΎΠ±Π»Π΅ΠΌ, ΠΎΡΠ½ΠΎΡΡΡΡΡ: 8D (8 Do), ΠΠ½Π°Π»ΠΈΠ· ΠΊΠΎΡΠ΅Π½Π½ΡΡ ΠΏΡΠΈΡΠΈΠ½ ΠΎΡΠΊΠ°Π·ΠΎΠ² ΠΎΠ±ΠΎΡΡΠ΄ΠΎΠ²Π°Π½ΠΈΡ (Root Cause Failure Analysis, RCFA), ΠΠΎΠ±Π΅ΡΡ ΠΠ°ΠΉΠ΄Π·Π΅Π½ (ΠΠΎΠ±Π΅ΡΡ ΠΠ°ΠΉΠ΄Π·Π΅Π½ β ΡΠ»Π΅ΠΌΠ΅Π½Ρ TPM). ΠΠ΅ΡΠ΅ΡΠΈΡΠ»Π΅Π½Π½ΡΠ΅ ΠΌΠ΅ΡΠΎΠ΄Ρ ΠΈΡΠΏΠΎΠ»ΡΠ·ΡΡΡ ΡΠΈΠΊΠ» PDCA ΠΈ ΡΠ°Π·Π»ΠΈΡΠ°ΡΡΡΡ Π΄Π΅ΡΠ°Π»ΡΠΌΠΈ, ΡΠ²ΠΎΠΉΡΡΠ²Π΅Π½Π½ΡΠΌΠΈ ΡΠ°Π±ΠΎΡΠ΅ Ρ ΠΏΡΠΎΠ±Π»Π΅ΠΌΠ°ΠΌΠΈ ΠΊΠ°ΡΠ΅ΡΡΠ²Π°, ΠΎΠ±ΡΠ»ΡΠΆΠΈΠ²Π°Π½ΠΈΡ ΠΎΠ±ΠΎΡΡΠ΄ΠΎΠ²Π°Π½ΠΈΡ, ΠΈ ΠΏΡ.
Π¦ΠΈΠΊΠ» PDCA, Π¦ΠΈΠΊΠ» ΠΠ»Π°Π½ΠΈΡΡΠΉ-ΠΠ΅Π»Π°ΠΉ-ΠΡΠΎΠ²Π΅ΡΡΠΉ-ΠΠΎΠ·Π΄Π΅ΠΉΡΡΠ²ΡΠΉ (Π¦ΠΈΠΊΠ» ΠΠ΅ΠΌΠΈΠ½Π³Π°-Π¨ΡΡ Π°ΡΡΠ°, Plan Do Check Act) β ΠΏΡΠΈΠ½ΡΠΈΠΏ ΡΠΎΠ²Π΅ΡΡΠ΅Π½ΡΡΠ²ΠΎΠ²Π°Π½ΠΈΡ ΠΏΡΠΎΡΠ΅ΡΡΠΎΠ² ΠΈ ΠΎΠΏΠ΅ΡΠ°ΡΠΈΠΉ. Π ΡΠΎΠΎΡΠ²Π΅ΡΡΡΠ²ΠΈΠΈ Ρ Π΄Π°Π½Π½ΡΠΌ ΠΏΠΎΠ΄Ρ ΠΎΠ΄ΠΎΠΌ Π»ΡΠ±ΠΎΠ΅ ΡΠ»ΡΡΡΠ΅Π½ΠΈΠ΅ Π΄ΠΎΠ»ΠΆΠ½ΠΎ ΠΏΡΠΎΠΉΡΠΈ ΡΠ΅ΡΡΡΠ΅ ΡΡΠ°Π΄ΠΈΠΈ. ΠΠΎ-ΠΏΠ΅ΡΠ²ΡΡ , ΡΠΏΠ»Π°Π½ΠΈΡΡΠΉ ΡΠ»ΡΡΡΠ΅Π½ΠΈΠ΅, Π²ΠΎ-Π²ΡΠΎΡΡΡ , ΡΠ΅Π°Π»ΠΈΠ·ΡΠΉ Π΅Π³ΠΎ Π² ΠΏΠΈΠ»ΠΎΡΠ½ΠΎΠΌ ΡΠΎΡΠΌΠ°ΡΠ΅, Π²-ΡΡΠ΅ΡΡΠΈΡ , ΠΏΠΎΠΉΠΌΠΈ ΡΠ΅Π·ΡΠ»ΡΡΠ°Ρ, Π²-ΡΠ΅ΡΠ²Π΅ΡΡΡΡ , Π² Π·Π°Π²ΠΈΡΠΈΠΌΠΎΡΡΠΈ ΠΎΡ ΡΠ΅Π·ΡΠ»ΡΡΠ°ΡΠ° ΠΏΡΠΈΠΌΠΈ ΡΠ΅ΡΠ΅Π½ΠΈΠ΅, Π²Π½Π΅Π΄ΡΠΈΡΡ ΠΈΠ»ΠΈ ΠΏΠΎΠ²ΡΠΎΡΠΈΡΡ ΡΠΈΠΊΠ» ΠΈΠ»ΠΈ ΠΎΡΠΊΠ°Π·Π°ΡΡΡΡ ΠΎΡ ΠΈΠ΄Π΅ΠΈ.
Π¨Π΅ΡΡΡ ΡΠΈΠ³ΠΌΠ°, Π¨Π΅ΡΡΡ ΡΠΈΠ³ΠΌ, 6 Π‘ΠΈΠ³ΠΌ (Six Sigma, 6s) β ΠΏΡΠΎΠΈΠ·Π²ΠΎΠ΄ΡΡΠ²Π΅Π½Π½Π°Ρ ΠΊΠΎΠ½ΡΠ΅ΠΏΡΠΈΡ, ΡΠ°Π·ΡΠ°Π±ΠΎΡΠ°Π½Π½Π°Ρ Π² ΠΊΠΎΠΌΠΏΠ°Π½ΠΈΠΈ Motorola ΠΈ ΠΏΠΎΠ»ΡΡΠΈΠ²ΡΠ°Ρ ΡΠΈΡΠΎΠΊΠΎΠ΅ ΡΠ°ΡΠΏΡΠΎΡΡΡΠ°Π½Π΅Π½ΠΈΠ΅ Π² ΠΌΠΈΡΠ΅ ΠΏΠΎΡΠ»Π΅ Π²Π½Π΅Π΄ΡΠ΅Π½ΠΈΡ Π² General Electric. Π¨Π΅ΡΡΡ ΡΠΈΠ³ΠΌΠ° ΠΎΡΠΈΠ΅Π½ΡΠΈΡΠΎΠ²Π°Π½Π° Π½Π° ΡΡΡΡΠ°Π½Π΅Π½ΠΈΠ΅ Π²Π°ΡΠΈΠ°ΡΠΈΠ²Π½ΠΎΡΡΠΈ Π²ΡΠ΅Ρ ΠΏΡΠΎΡΠ΅ΡΡΠΎΠ² Π² ΠΎΡΠ³Π°Π½ΠΈΠ·Π°ΡΠΈΠΈ Ρ ΠΈΡΠΏΠΎΠ»ΡΠ·ΠΎΠ²Π°Π½ΠΈΠ΅ΠΌ ΠΈΠ½ΡΡΡΡΠΌΠ΅Π½ΡΠΎΠ² ΡΠΏΡΠ°Π²Π»Π΅Π½ΠΈΡ ΠΊΠ°ΡΠ΅ΡΡΠ²ΠΎΠΌ, Π² ΡΠΎΠΌ ΡΠΈΡΠ»Π΅ ΡΡΠ°ΡΠΈΡΡΠΈΡΠ΅ΡΠΊΠΈΡ . ΠΠ°Π·Π²Π°Π½ΠΈΠ΅ ΠΊΠΎΠ½ΡΠ΅ΠΏΡΠΈΠΈ ΠΏΡΠΎΠΈΡΡ ΠΎΠ΄ΠΈΡ ΠΎΡ ΡΡΠ°ΡΠΈΡΡΠΈΡΠ΅ΡΠΊΠΎΠ³ΠΎ ΠΏΠΎΠ½ΡΡΠΈΡ ΡΡΠ΅Π΄Π½Π΅Π³ΠΎ ΠΊΠ²Π°Π΄ΡΠ°ΡΠΈΡΠ½ΠΎΠ³ΠΎ ΠΎΡΠΊΠ»ΠΎΠ½Π΅Π½ΠΈΡ ΠΎΠ±ΠΎΠ·Π½Π°ΡΠ°Π΅ΠΌΠΎΠ³ΠΎ ΡΠΈΠΌΠ²ΠΎΠ»ΠΎΠΌ Π³ΡΠ΅ΡΠ΅ΡΠΊΠΎΠ³ΠΎ Π°Π»ΡΠ°Π²ΠΈΡΠ° s (ΡΠΈΠ³ΠΌΠ°). Π£ΡΠΎΠ²Π΅Π½Ρ ΠΊΠ°ΡΠ΅ΡΡΠ²Π° 6s ΠΎΠ·Π½Π°ΡΠ°Π΅Ρ 3,4 Π΄Π΅ΡΠ΅ΠΊΡΠ½ΡΡ ΠΈΠ·Π΄Π΅Π»ΠΈΠΉ Π½Π° ΠΌΠΈΠ»Π»ΠΈΠΎΠ½ ΠΏΡΠΎΠΈΠ·Π²Π΅Π΄Π΅Π½Π½ΡΡ .
Π―ΡΠΈΠΊ Π²ΡΡΠ°Π²Π½ΠΈΠ²Π°Π½ΠΈΡ (Leveling Box) β ΡΠΈΠ·ΠΈΡΠ΅ΡΠΊΠΎΠ΅ ΡΡΡΡΠΎΠΉΡΡΠ²ΠΎ Π΄Π»Ρ Π±Π°Π»Π°Π½ΡΠΈΡΠΎΠ²ΠΊΠΈ Π·Π°Π³ΡΡΠ·ΠΊΠΈ ΠΏΡΠΎΠΈΠ·Π²ΠΎΠ΄ΡΡΠ²Π΅Π½Π½ΡΡ ΡΡΠ°ΡΡΠΊΠΎΠ² Π½Π° ΠΎΡΠ½ΠΎΠ²Π΅ ΠΠ°Π½Π±Π°Π½.
lean-consulting.ru
ΠΠ΅ΡΠ΅ΠΆΠ»ΠΈΠ²ΠΎΠ΅ ΠΏΡΠΎΠΈΠ·Π²ΠΎΠ΄ΡΡΠ²ΠΎ
Β Β Β Β ΠΠ»Ρ ΠΏΡΠ°ΠΊΡΠΈΡΠ΅ΡΠΊΠΎΠ³ΠΎ Π²Π½Π΅Π΄ΡΠ΅Π½ΠΈΡ Π±Π΅ΡΠ΅ΠΆΠ»ΠΈΠ²ΠΎΠ³ΠΎ ΠΏΡΠΎΠΈΠ·Π²ΠΎΠ΄ΡΡΠ²Π° ΠΈΡΠΏΠΎΠ»ΡΠ·ΡΡΡΡΡ ΡΠ°Π·Π»ΠΈΡΠ½ΡΠ΅ ΠΈΠ½ΡΡΡΡΠΌΠ΅Π½ΡΡ:Β Β Π ΠΏΠ΅ΡΠ²ΠΎΠΉ ΡΠ°ΡΡΠΈ ΡΡΠ°ΡΡΠΈ ΡΠ°ΡΡΠΌΠΎΡΡΠΈΠΌ Π½Π΅ΠΊΠΎΡΠΎΡΡΠ΅ ΠΈΠ· Π½ΠΈΡ :
Β
Β Β ΠΠ°ΡΡΠ° ΠΏΠΎΡΠΎΠΊΠ° ΡΠΎΠ·Π΄Π°Π½ΠΈΡ ΡΠ΅Π½Π½ΠΎΡΡΠΈ ΠΏΡΠΎΠ΄ΡΠΊΡΠ°/ΡΡΠ»ΡΠ³ΠΈ.
Β
Β Β ΠΠ°ΡΡΠ° ΠΏΠΎΡΠΎΠΊΠ° ΡΠΎΠ·Π΄Π°Π½ΠΈΡ ΡΠ΅Π½Π½ΠΎΡΡΠΈ ΠΏΡΠΎΠ΄ΡΠΊΡΠ°/ΡΡΠ»ΡΠ³ΠΈ — ΡΡΠΎ ΠΊΠ°ΡΡΠ° ΡΠ°ΠΊΡΠΈΡΠ΅ΡΠΊΠΎΠ³ΠΎ ΡΠΎΡΡΠΎΡΠ½ΠΈΡ. ΠΠ½Π° ΠΎΡ
Π²Π°ΡΡΠ²Π°Π΅Ρ Π²ΡΠ΅ ΠΏΡΠΎΡΠ΅ΡΡΡ — ΠΎΡ Π½Π°ΡΠ°Π»Π° Π΄ΠΎ ΠΊΠΎΠ½ΡΠ° ΡΠΎΠ·Π΄Π°Π½ΠΈΡ ΠΏΡΠΎΠ΄ΡΠΊΡΠ° ΠΈΠ»ΠΈ ΠΎΠΊΠ°Π·Π°Π½ΠΈΡ ΡΡΠ»ΡΠ³ΠΈ. ΠΠ°ΡΡΠ° ΠΏΠΎΠ·Π²ΠΎΠ»ΡΠ΅Ρ ΠΎΠ±Π½Π°ΡΡΠΆΠΈΡΡ Π½Π΅ ΡΠΎΠ»ΡΠΊΠΎ ΠΏΠΎΡΠ΅ΡΠΈ, Π½ΠΈ ΠΈ ΠΈΡ
ΠΈΡΡΠΎΡΠ½ΠΈΠΊΠΈ, ΠΈ ΡΠ»Π΅Π΄ΠΎΠ²Π°ΡΠ΅Π»ΡΠ½ΠΎ, ΠΎΠΏΡΠ΅Π΄Π΅Π»ΠΈΡΡ ΠΎΠ±Π»Π°ΡΡΠΈ, Π½Π° ΠΊΠΎΡΠΎΡΡΠ΅ ΡΡΠΎΠΈΡ Π½Π°ΠΏΡΠ°Π²Π»ΡΡΡ ΡΡΠΈΠ»ΠΈΡ.Β
Β ΠΡΠ°ΠΏΡ ΡΠΎΡΡΠ°Π²Π»Π΅Π½ΠΈΡ ΠΊΠ°ΡΡΡ:
1)Β Β Β Β Β ΠΠΏΡΠ΅Π΄Π΅Π»Π΅Π½ΠΈΠ΅ Π²ΡΠ΅Ρ ΠΏΡΠΎΠΈΠ·Π²ΠΎΠ΄ΡΡΠ²Π΅Π½Π½ΡΡ ΠΏΡΠΎΡΠ΅ΡΡΠΎΠ² ΠΎΡ ΠΏΠΎΡΡΡΠΏΠ»Π΅Π½ΠΈΡ Π·Π°ΠΏΡΠΎΡΠ° Π½Π° ΠΈΠ·Π³ΠΎΡΠΎΠ²Π»Π΅Π½ΠΈΠ΅ ΠΏΡΠΎΠ΄ΡΠΊΡΠ° Π΄ΠΎ ΠΏΠΎΡΡΠ°Π²ΠΊΠΈ Π΅Π³ΠΎ ΠΏΠΎΡΡΠ΅Π±ΠΈΡΠ΅Π»Ρ (ΠΎΡ ΠΏΠΎΡΡΡΠΏΠ»Π΅Π½ΠΈΡ Π·Π°ΠΏΡΠΎΡΠ° Π½Π° ΡΡΠ»ΡΠ³Ρ Π΄ΠΎ ΠΌΠΎΠΌΠ΅Π½ΡΠ° Π΅Π΅ ΠΎΠΊΠ°Π·Π°Π½ΠΈΡ)
2)Β Β Β Β Β Π Π°ΡΡΠ΅Ρ Π²ΡΠ΅ΠΌΠ΅Π½ΠΈ ΠΊΠ°ΠΆΠ΄ΠΎΠΉ ΠΎΡΠ΄Π΅Π»ΡΠ½ΠΎΠΉ ΠΎΠΏΠ΅ΡΠ°ΡΠΈΠΈ, Π²ΡΠ΅ΠΌΠ΅Π½ΠΈ Π½Π° ΡΡΠ°Π½ΡΠΏΠΎΡΡΠΈΡΠΎΠ²ΠΊΡ ΠΈ ΠΏΠ΅ΡΠ΅ΠΌΠ΅ΡΠ΅Π½ΠΈΠ΅
3)Β Β Β Β Β ΠΠ·ΠΎΠ±ΡΠ°ΠΆΠ΅Π½ΠΈΠ΅ Π²ΡΠ΅Ρ ΡΠ»Π΅ΠΌΠ΅Π½ΡΠΎΠ² ΠΊΠ°ΡΡΡ ΡΠ΅ΠΊΡΡΠ΅Π³ΠΎ ΡΠΎΡΡΠΎΡΠ½ΠΈΡ Π½Π° ΠΎΠ΄Π½ΠΎΠΌ Π»ΠΈΡΡΠ΅
4)Β Β Β Β Β Π€ΠΎΡΠΌΠΈΡΠΎΠ²Π°Π½ΠΈΠ΅ ΡΠ²ΠΎΠ΅Π³ΠΎ Π²ΠΈΠ΄Π΅Π½ΠΈΡ ΠΏΡΠΎΠ²Π΅Π΄Π΅Π½ΠΈΡ ΠΎΠΏΠ΅ΡΠ°ΡΠΈΠΈ ΡΠΎΡΡΡΠ΄Π½ΠΈΠΊΠ°ΠΌΠΈ, ΡΡΠ°ΡΡΠ²ΡΡΡΠΈΠΌΠΈ Π² Π²ΡΠΏΠΎΠ»Π½Π΅Π½ΠΈΠΈ ΡΠΎΠΉ ΠΈΠ»ΠΈ ΠΈΠ½ΠΎΠΉ ΠΎΠΏΠ΅ΡΠ°ΡΠΈΠΈ
5)Β Β Β Β Β ΠΠ±ΡΠ΅Π΄ΠΈΠ½Π΅Π½ΠΈΠ΅ Π²ΡΠ΅Ρ ΠΎΠΏΠ΅ΡΠ°ΡΠΈΠΉ, ΠΏΡΠ΅Π΄ΡΡΠ°Π²Π»Π΅Π½Π½ΡΡ ΡΠΎΡΡΡΠ΄Π½ΠΈΠΊΠ°ΠΌΠΈ ΠΏΡΠ΅Π΄ΠΏΡΠΈΡΡΠΈΡ, ΠΎΠ±ΡΡΠΆΠ΄Π΅Π½ΠΈΠ΅ ΡΡΠ΅ΠΏΠ΅Π½ΠΈ ΠΈΡ Π΄Π΅ΡΠ°Π»ΠΈΠ·Π°ΡΠΈΠΈ, ΠΈ ΠΏΠΎΠ»ΡΡΠ΅Π½ΠΈΠ΅ ΠΊΠ°ΡΡΡ Π±ΡΠ΄ΡΡΠ΅Π³ΠΎ ΡΠΎΡΡΠΎΡΠ½ΠΈΡ
6)Β Β Β Β Β Π‘ΠΎΠΏΠΎΡΡΠ°Π²Π»Π΅Π½ΠΈΠ΅ ΠΊΠ°ΡΡ ΡΠ΅ΠΊΡΡΠ΅Π³ΠΎ ΠΈ Π±ΡΠ΄ΡΡΠ΅Π³ΠΎ ΡΠΎΡΡΠΎΡΠ½ΠΈΡ
7)Β Β Β Β Β Π Π°Π·ΡΠ°Π±ΠΎΡΠΊΠ° ΠΏΠ»Π°Π½Π° ΠΏΠΎ ΡΠ»ΡΡΡΠ΅Π½ΠΈΡ ΠΊΠ°ΡΠ΅ΡΡΠ²Π° ΠΏΡΠΎΠΈΠ·Π²ΠΎΠ΄ΡΡΠ²Π΅Π½Π½ΡΡ ΠΏΡΠΎΡΠ΅ΡΡΠΎΠ²
Β Β ΠΠ°ΡΡΠ° ΠΏΠΎΡΠΎΠΊΠ° ΡΠΎΠ·Π΄Π°Π½ΠΈΡ ΡΠ΅Π½Π½ΠΎΡΡΠΈ Π΄Π°Π΅Ρ ΡΠ»Π΅Π΄ΡΡΡΠΈΠ΅ ΠΏΡΠ΅ΠΈΠΌΡΡΠ΅ΡΡΠ²Π°:
- ΠΊΠ°ΡΡΠ° — ΡΡΠΎ Π΅Π΄ΠΈΠ½ΡΠΉ ΡΠ·ΡΠΊ, Π½Π° ΠΊΠΎΡΠΎΡΠΎΠΌ ΠΌΠΎΠΆΠ½ΠΎ ΠΎΠ±ΡΡΠΆΠ΄Π°ΡΡ ΠΏΡΠΎΠΈΠ·Π²ΠΎΠ΄ΡΡΠ²Π΅Π½Π½ΡΠ΅ ΠΏΡΠΎΡΠ΅ΡΡΡ;
- Π²ΡΡΠ²Π»Π΅Π½ΠΈΠ΅ ΡΠ²ΡΠ·Π΅ΠΉ ΠΌΠ΅ΠΆΠ΄Ρ ΠΈΠ½ΡΠΎΡΠΌΠ°ΡΠΈΠΎΠ½Π½ΡΠΌ ΠΈ ΠΌΠ°ΡΠ΅ΡΠΈΠ°Π»ΡΠ½ΡΠΌ ΠΏΠΎΡΠΎΠΊΠ°ΠΌΠΈ;
- Π²ΠΎΠ·ΠΌΠΎΠΆΠ½ΠΎΡΡΡ ΡΠ²ΠΈΠ΄Π΅ΡΡ Π½Π΅ ΡΠΎΠ»ΡΠΊΠΎ ΠΎΡΠ΄Π΅Π»ΡΠ½ΡΠΉ ΠΏΡΠΎΠΈΠ·Π²ΠΎΠ΄ΡΡΠ²Π΅Π½Π½ΡΠΉ ΠΏΡΠΎΡΠ΅ΡΡ, Π½ΠΎ ΠΈ Π²Π΅ΡΡ ΠΏΠΎΡΠΎΠΊ;
- ΠΎΠΏΡΠ΅Π΄Π΅Π»Π΅Π½ΠΈΠ΅ ΡΠΊΡΡΡΡΡ ΠΏΡΠΎΠΈΠ·Π²ΠΎΠ΄ΡΡΠ²Π΅Π½Π½ΡΡ ΠΏΠΎΡΠ΅ΡΡ, Π·Π°ΡΠ°ΡΡΡΡ ΡΠΎΡΡΠ°Π²Π»ΡΡΡΠΈΠ΅ Π±ΠΎΠ»ΡΡΡΡ ΡΠ°ΡΡΡ ΡΠ΅Π±Π΅ΡΡΠΎΠΈΠΌΠΎΡΡΠΈ ΠΏΡΠΎΠ΄ΡΠΊΡΠ° ΠΈΠ»ΠΈ ΡΡΠ»ΡΠ³ΠΈ, ΠΈ ΠΈΡΡΠΎΡΠ½ΠΈΠΊΠΎΠ² ΡΡΠΈΡ ΠΏΠΎΡΠ΅ΡΡ;
- ΠΎΠΏΡΠ΅Π΄Π΅Π»Π΅Π½ΠΈΠ΅ ΠΎΠΏΠ΅ΡΠ°ΡΠΈΠΉ, ΡΠΎΠ·Π΄Π°ΡΡΠΈΡ ΠΈ Π½Π΅ ΡΠΎΠ·Π΄Π°ΡΡΠΈΡ Π΄ΠΎΠ±Π°Π²Π»Π΅Π½Π½ΡΡ ΡΠ΅Π½Π½ΠΎΡΡΡ;
- ΠΎΠ±Π΅ΡΠΏΠ΅ΡΠ΅Π½ΠΈΠ΅ ΡΡΠ½ΠΎΡΡΠΈ ΠΈ ΠΏΡΠΎΡΡΠΎΡΡ ΠΎΠ±ΡΡΠΆΠ΄Π΅Π½ΠΈΡ ΠΏΡΠΎΡΠ΅ΡΡΠΎΠ².
Β Β ΠΠ°ΡΡΠΈΡΠΎΠ²Π°Π½ΠΈΠ΅ β Π²ΠΈΠ·ΡΠ°Π»ΠΈΠ·ΠΈΡΠΎΠ²Π°Π½Π½ΠΎΠ΅ ΠΎΠΏΠΈΡΠ°Π½ΠΈΠ΅ Π² ΠΎΠΏΡΠ΅Π΄Π΅Π»ΡΠ½Π½ΠΎΠΉ ΡΠΎΡΠΌΠ΅ ΠΏΠΎΡΠΎΠΊΠ° (ΠΌΠ°ΡΠ΅ΡΠΈΠ°Π»ΡΠ½ΠΎΠ³ΠΎ, ΠΈΠ½ΡΠΎΡΠΌΠ°ΡΠΈΠΎΠ½Π½ΠΎΠ³ΠΎ) ΡΠΎΠ·Π΄Π°Π½ΠΈΡ ΡΠ΅Π½Π½ΠΎΡΡΠΈ Π±ΠΈΠ·Π½Π΅Ρ-ΠΏΡΠΎΡΠ΅ΡΡΠ°. ΠΠ°ΡΡΠΈΡΠΎΠ²Π°Π½ΠΈΠ΅ ΠΏΡΠΎΠΈΠ·Π²ΠΎΠ΄ΠΈΡΡΡ Π² ΡΡΠ»ΠΎΠ²ΠΈΡΡ
Β«ΠΊΠ°ΠΊ Π΅ΡΡΡΒ», Β«ΠΊΠ°ΠΊ Π΄ΠΎΠ»ΠΆΠ½ΠΎ Π±ΡΡΡΒ» ΠΈ Β«ΠΊΠ°ΠΊ Π±ΡΠ΄Π΅ΡΒ».
ΠΡΠΈ ΠΏΠΎΠΌΠΎΡΠΈ ΡΡΠΎΠ³ΠΎ ΠΈΠ½ΡΡΡΡΠΌΠ΅Π½ΡΠ° ΡΠΎΠ·Π΄Π°ΡΡΡΡ ΠΊΠ°ΡΡΠ° ΠΏΠΎΡΠΎΠΊΠ° ΡΠΎΠ·Π΄Π°Π½ΠΈΡ ΡΠ΅Π½Π½ΠΎΡΡΠΈ, ΠΊΠΎΡΠΎΡΠ°Ρ ΠΏΠΎΠ·Π²ΠΎΠ»ΠΈΡ ΡΡΡΠΊΠΎ ΠΎΠΏΡΠ΅Π΄Π΅Π»ΠΈΡΡ Π²ΡΠ΅ΠΌΡ ΡΠΎΠ·Π΄Π°Π½ΠΈΡ ΡΠ΅Π½Π½ΠΎΡΡΠΈ ΠΈ ΠΏΠΎΡΠ΅ΡΠΈ, ΡΡΡΠ΅ΡΡΠ²ΡΡΡΠΈΠ΅ Π² ΠΏΠΎΡΠΎΠΊΠ΅ ΡΠΎΠ·Π΄Π°Π½ΠΈΡ ΡΠ΅Π½Π½ΠΎΡΡΠΈ.
Β Β ΠΠ°ΡΡΠ° ΠΏΠΎΡΠΎΠΊΠ° ΡΠΎΠ·Π΄Π°Π½ΠΈΡ β ΡΡΠΎ ΠΈΠ½ΡΡΡΡΠΌΠ΅Π½Ρ, Ρ ΠΏΠΎΠΌΠΎΡΡΡ ΠΊΠΎΡΠΎΡΠΎΠ³ΠΎ ΠΌΠΎΠΆΠ½ΠΎ ΠΎΡΠΎΠ±ΡΠ°Π·ΠΈΡΡ ΠΌΠ°ΡΠ΅ΡΠΈΠ°Π»ΡΠ½ΡΠ΅ ΠΈ ΠΈΠ½ΡΠΎΡΠΌΠ°ΡΠΈΠΎΠ½Π½ΡΠ΅ ΠΏΠΎΡΠΎΠΊΠΈ Π² Ρ ΠΎΠ΄Π΅ ΡΠΎΠ·Π΄Π°Π½ΠΈΡ ΡΠ΅Π½Π½ΠΎΡΡΠΈ. ΠΡΠ΅ΠΌΠ΅Π½Π΅ΠΌ ΡΠΎΠ·Π΄Π°Π½ΠΈΡ ΡΠ΅Π½Π½ΠΎΡΡΠΈ ΠΏΡΠΈΠ½ΡΡΠΎ ΡΡΠΈΡΠ°ΡΡ Π²ΡΠ΅ΠΌΡ Π²ΡΠΏΠΎΠ»Π½Π΅Π½ΠΈΡ ΡΠ°Π±ΠΎΡ, ΠΊΠΎΡΠΎΡΡΠ΅ ΠΏΡΠ΅ΠΎΠ±ΡΠ°Π·ΡΡΡ ΠΏΡΠΎΠ΄ΡΠΊΡ ΡΠ°ΠΊ, ΡΡΠΎΠ±Ρ ΠΏΠΎΡΡΠ΅Π±ΠΈΡΠ΅Π»ΠΈ Π±ΡΠ»ΠΈ Π³ΠΎΡΠΎΠ²Ρ ΠΏΠ»Π°ΡΠΈΡΡ Π·Π° Π½Π΅Π³ΠΎ. ΠΠΎΡΠΎΠΊ ΡΠΎΠ·Π΄Π°Π½ΠΈΡ ΡΠ΅Π½Π½ΠΎΡΡΠΈ β Π²ΡΠ΅ Π΄Π΅ΠΉΡΡΠ²ΠΈΡ (Π΄ΠΎΠ±Π°Π²Π»ΡΡΡΠΈΠ΅ ΠΈ Π½Π΅ Π΄ΠΎΠ±Π°Π²Π»ΡΡΡΠΈΠ΅ ΡΠ΅Π½Π½ΠΎΡΡΡ), Π½ΡΠΆΠ½ΡΠ΅, ΡΡΠΎΠ±Ρ ΠΏΡΠΎΠΈΠ·Π²Π΅ΡΡΠΈ ΠΏΡΠΎΠ΄ΡΠΊΡ.
Β Β Π ΡΠΎΠΆΠ°Π»Π΅Π½ΠΈΡ, ΠΏΡΠ°ΠΊΡΠΈΠΊΠ° ΠΏΠΎΠΊΠ°Π·ΡΠ²Π°Π΅Ρ, ΡΡΠΎ ΠΏΠΎΡΠ΅ΡΠΈ Ρ Π½Π°Ρ ΡΠΎΡΡΠ°Π²Π»ΡΡΡ Π»ΡΠ²ΠΈΠ½ΡΡ Π΄ΠΎΠ»Ρ ΠΏΡΠΎΡΠ΅ΡΡΠ°, ΠΈΡ ΡΠ°Π·ΠΌΠ΅Ρ Π΄ΠΎΡ ΠΎΠ΄ΠΈΡ Π΄ΠΎ 80 % β ΡΡΠΎ ΠΈ Π΅ΡΡΡ ΠΏΠΎΠ»Π΅ Π΄Π΅ΡΡΠ΅Π»ΡΠ½ΠΎΡΡΠΈ Π΄Π»Ρ ΡΠΈΡΡΠ΅ΠΌΡ ΠΠ°ΠΉΠ·Π΅Π½: Π½Π΅ΠΏΡΠ΅ΡΡΠ²Π½ΠΎΠ΅ ΡΠ»ΡΡΡΠ΅Π½ΠΈΠ΅; ΡΠΏΠΎΡΠΎΠ± ΡΡΡΠ΅ΠΌΠ»Π΅Π½ΠΈΡ ΠΊ ΡΠΎΠ²Π΅ΡΡΠ΅Π½ΡΡΠ²Ρ ΡΠ΅ΡΠ΅Π· ΡΡΡΡΠ°Π½Π΅Π½ΠΈΠ΅ ΠΏΠΎΡΠ΅ΡΡ; ΠΏΡΠ΅Π΄Π»ΠΎΠΆΠ΅Π½ΠΈΡ ΠΏΠΎ ΡΡΡΡΠ°Π½Π΅Π½ΠΈΡ ΠΏΠΎΡΠ΅ΡΡ.
Β Β ΠΡΠ΅ΠΌ ΠΈΠ·Π²Π΅ΡΡΠ½ΠΎ, ΡΡΠΎ Π½ΡΠΆΠ΄Ρ ΠΏΠΎΡΡΠ΅Π±ΠΈΡΠ΅Π»Ρ Π½Π΅ΠΏΡΠ΅ΡΡΠ²Π½ΠΎ ΡΠ°ΡΡΡΡ, Π° Π·Π½Π°ΡΠΈΡ, ΠΈ ΠΏΡΠΎΡΠ΅ΡΡ ΡΠ»ΡΡΡΠ΅Π½ΠΈΠΉ ΡΠΎΠΆΠ΅ Π½Π΅ΠΏΡΠ΅ΡΡΠ²Π΅Π½, ΡΠ°ΠΊ ΠΊΠ°ΠΊ ΠΎΠ½ Π½Π°ΠΏΡΠ°Π²Π»Π΅Π½ Π½Π° ΡΡΠ°Π½ΡΡΠΎΡΠΌΠ°ΡΠΈΡ Π½ΡΠΆΠ΄ ΠΏΠΎΡΡΠ΅Π±ΠΈΡΠ΅Π»Ρ Π² ΠΊΠΎΠ½ΠΊΡΠ΅ΡΠ½ΡΡ ΠΏΡΠΎΠ΄ΡΠΊΡΠΈΡ.
Β
Β Β Β Β Π‘ΠΈΡΡΠ΅ΠΌΠ° 5S.
Β Β Β ΠΠ½ΡΡΡΡΠΌΠ΅Π½Ρ 5S — ΡΠ°ΡΠΈΠΎΠ½Π°Π»ΡΠ½ΠΎΠ΅ ΠΈΡΠΏΠΎΠ»ΡΠ·ΠΎΠ²Π°Π½ΠΈΡ ΡΠ°Π±ΠΎΡΠ΅Π³ΠΎ ΠΌΠ΅ΡΡΠ°. ΠΠΊΠ»ΡΡΠ°Π΅Ρ Π² ΡΠ΅Π±Ρ 5 ΠΏΡΠΎΡΡΡΡ ΡΠΎΡΡΠ°Π²Π»ΡΡΡΠΈΡ :
ΠΡΠΈΠ½ΡΠΈΠΏ | Π‘ΠΎΠ΄Π΅ΡΠΆΠ°Π½ΠΈΠ΅ ΡΠ°Π±ΠΎΡΡΒ |
1.Π‘Π΅ΠΉΡΠΈ — ΡΠΎΡΡΠΈΡΠΎΠ²ΠΊΠ°. Π£Π΄Π°Π»Π΅Π½ΠΈΠ΅ Π½Π΅Π½ΡΠΆΠ½ΠΎΠ³ΠΎ. Β | ΠΡΠ΅ ΠΏΡΠ΅Π΄ΠΌΠ΅ΡΡ Π² ΡΠ°ΠΌΠΊΠ°Ρ ΠΊΠΎΠΌΠΏΠ°Π½ΠΈΠΈ ΠΈ Π΅Ρ ΠΏΠΎΠ΄ΡΠ°Π·Π΄Π΅Π»Π΅Π½ΠΈΠΉ ΡΠ°Π·Π΄Π΅Π»ΡΡΡΡΡ Π½Π° ΡΡΠΈ ΠΊΠ°ΡΠ΅Π³ΠΎΡΠΈΠΈ (Π½Π΅Π½ΡΠΆΠ½ΡΠ΅, Π½Π΅Π½ΡΠΆΠ½ΡΠ΅ ΡΡΠΎΡΠ½ΠΎ ΠΈ Π½ΡΠΆΠ½ΡΠ΅):
ΠΠ° ΠΊΠ°ΠΆΠ΄ΡΠΌ ΡΠ°Π±ΠΎΡΠ½ΠΈΠΊΠΎΠΌ Π·Π°ΠΊΡΠ΅ΠΏΠ»ΡΡΡΡΡ ΡΡΠ΅ΡΡ Π΅Π³ΠΎ ΠΎΡΠ²Π΅ΡΡΡΠ²Π΅Π½Π½ΠΎΡΡΠΈ. |
2.Π‘Π΅ΠΉΡΠΎΠ½ — ΡΠ°ΡΠΈΠΎΠ½Π°Π»ΡΠ½ΠΎΠ΅ ΠΈΡΠΏΠΎΠ»ΡΠ·ΠΎΠ²Π°Π½ΠΈΠ΅. Π Π°ΡΠΈΠΎΠ½Π°Π»ΡΠ½ΠΎΠ΅ ΡΠ°Π·ΠΌΠ΅ΡΠ΅Π½ΠΈΠ΅ ΠΏΡΠ΅Π΄ΠΌΠ΅ΡΠΎΠ². | ΠΠΎ ΠΎΡΠ½ΠΎΡΠ΅Π½ΠΈΡ ΠΊ Π½ΡΠΆΠ½ΡΠΌ ΠΏΡΠ΅Π΄ΠΌΠ΅ΡΠ°ΠΌ ΠΈ ΠΏΡΠ΅Π΄ΠΌΠ΅ΡΠ°ΠΌ, Π½Π΅ Π½ΡΠΆΠ½ΡΠΌ ΡΡΠΎΡΠ½ΠΎ, Π²ΡΡΠ°Π±Π°ΡΡΠ²Π°ΡΡΡΡ ΠΈ ΡΠ΅Π°Π»ΠΈΠ·ΡΡΡΡΡ ΡΠ΅ΡΠ΅Π½ΠΈΡ, ΠΊΠΎΡΠΎΡΡΠ΅ ΠΎΠ±Π΅ΡΠΏΠ΅ΡΠΈΠ²Π°ΡΡ:
|
3. Π‘Π΅ΠΉΡΠΎ — ΡΠ±ΠΎΡΠΊΠ°. Π£Π±ΠΎΡΠΊΠ°, ΠΏΡΠΎΠ²Π΅ΡΠΊΠ°, ΡΡΡΡΠ°Π½Π΅Π½ΠΈΠ΅ Π½Π΅ΠΈΡΠΏΡΠ°Π²Π½ΠΎΡΡΠ΅ΠΉ. | ΠΠ΅Π½Π΅ΡΠ°Π»ΡΠ½Π°Ρ ΡΠ±ΠΎΡΠΊΠ° ΠΏΠΎΠΌΠ΅ΡΠ΅Π½ΠΈΠΉ (ΠΏΡΠΈ Π½Π΅ΠΎΠ±Ρ ΠΎΠ΄ΠΈΠΌΠΎΡΡΠΈ):
|
4.Π‘Π΅ΠΉΠΊΠ΅ΡΡΡ — ΡΡΠ°Π½Π΄Π°ΡΡΠΈΠ·Π°ΡΠΈΡ. Π‘ΡΠ°Π½Π΄Π°ΡΡΠΈΠ·Π°ΡΠΈΡ ΠΏΡΠ°Π²ΠΈΠ». | Π€ΠΈΠΊΡΠ°ΡΠΈΡ Π² ΠΏΠΈΡΡΠΌΠ΅Π½Π½ΠΎΠΌ Π²ΠΈΠ΄Π΅ ΠΏΡΠ°Π²ΠΈΠ»:
|
5.Π‘Π΅ΠΉΡΡΠΊΠ΅ — ΡΠΎΠ²Π΅ΡΡΠ΅Π½ΡΡΠ²ΠΎΠ²Π°Π½ΠΈΠ΅.Β ΠΠΈΡΡΠΈΠΏΠ»ΠΈΠ½ΠΈΡΠΎΠ²Π°Π½Π½ΠΎΡΡΡ ΠΈ ΠΎΡΠ²Π΅ΡΡΡΠ²Π΅Π½Π½ΠΎΡΡΡ. | ΠΠ°ΠΊΡΠ΅ΠΏΠ»Π΅Π½ΠΈΠ΅ ΡΡΠ΅Ρ ΠΎΡΠ²Π΅ΡΡΡΠ²Π΅Π½Π½ΠΎΡΡΠΈ ΠΊΠ°ΠΆΠ΄ΠΎΠ³ΠΎ ΡΠ°Π±ΠΎΡΠ½ΠΈΠΊΠ° (ΠΎΠ±ΡΠ΅ΠΊΡΡ Π²Π½ΠΈΠΌΠ°Π½ΠΈΡ ΠΈ ΠΎΡΠ½ΠΎΠ²Π½ΡΠ΅ ΠΎΠ±ΡΠ·Π°Π½Π½ΠΎΡΡΠΈ ΠΏΠΎ ΠΈΡ ΠΏΠΎΠ΄Π΄Π΅ΡΠΆΠ°Π½ΠΈΡ Π² Π½ΠΎΡΠΌΠ°Π»ΡΠ½ΠΎΠΌ ΡΠΎΡΡΠΎΡΠ½ΠΈΠΈ):
|
Β Β Β ΠΡΠ½ΠΎΠ²Π½ΡΠ΅ ΠΏΡΠ΅ΠΈΠΌΡΡΠ΅ΡΡΠ²Π° ΠΈΠ½ΡΡΡΡΠΌΠ΅Π½ΡΠ°:
- ΡΠ½ΠΈΠΆΠ΅Π½ΠΈΠ΅ ΡΠΈΡΠ»Π° ΠΎΡΠΈΠ±ΠΎΠΊ Π² Π΄ΠΎΠΊΡΠΌΠ΅Π½ΡΠ°Ρ ;
- ΡΠΎΠ·Π΄Π°Π½ΠΈΠ΅ ΠΊΠΎΠΌΡΠΎΡΡΠ½ΠΎΠ³ΠΎ ΠΏΡΠΈΡ ΠΎΠ»ΠΎΠ³ΠΈΡΠ΅ΡΠΊΠΎΠ³ΠΎ ΠΊΠ»ΠΈΠΌΠ°ΡΠ°, ΡΡΠΈΠΌΡΠ»ΠΈΡΠΎΠ²Π°Π½ΠΈΠ΅ ΠΆΠ΅Π»Π°Π½ΠΈΡ ΡΠ°Π±ΠΎΡΠ°ΡΡ;
- ΠΏΠΎΠ²ΡΡΠ΅Π½ΠΈΠ΅ ΠΏΡΠΎΠΈΠ·Π²ΠΎΠ΄ΠΈΡΠ΅Π»ΡΠ½ΠΎΡΡΠΈ ΡΡΡΠ΄Π°;
- ΠΏΠΎΠ²ΡΡΠ΅Π½ΠΈΠ΅ ΠΏΡΠΈΠ±ΡΠ»ΠΈ ΠΏΡΠ΅Π΄ΠΏΡΠΈΡΡΠΈΡ ΠΈ ΡΠΎΠΎΡΠ²Π΅ΡΡΡΠ²Π΅Π½Π½ΠΎ ΠΏΠΎΠ²ΡΡΠ΅Π½ΠΈΠ΅ ΡΡΠΎΠ²Π½Ρ Π΄ΠΎΡ ΠΎΠ΄Π° ΡΠ°Π±ΠΎΡΠΈΡ ;
- ΠΈΠ½ΡΡΡΡΠΌΠ΅Π½Ρ Π½Π΅ ΡΡΠ΅Π±ΡΠ΅Ρ ΠΏΡΠΈΠΌΠ΅Π½Π΅Π½ΠΈΡ Π½ΠΎΠ²ΡΡ ΡΠΏΡΠ°Π²Π»Π΅Π½ΡΠ΅ΡΠΊΠΈΡ ΡΠ΅Ρ Π½ΠΎΠ»ΠΎΠ³ΠΈΠΉ ΠΈ ΡΠ΅ΠΎΡΠΈΠΉ.
Β
Β Β Β Β ΠΠΈΠ·ΡΠ°Π»ΠΈΠ·Π°ΡΠΈΡ.
Β Β ΠΠΈΠ·ΡΠ°Π»ΠΈΠ·Π°ΡΠΈΡ — ΡΡΠΎ Π»ΡΠ±ΠΎΠ΅ ΡΡΠ΅Π΄ΡΡΠ²ΠΎ, ΠΈΠ½ΡΠΎΡΠΌΠΈΡΡΡΡΠ΅Π΅ ΠΎ ΡΠΎΠΌ, ΠΊΠ°ΠΊ Π΄ΠΎΠ»ΠΆΠ½Π° Π²ΡΠΏΠΎΠ»Π½ΡΡΡΡΡ ΡΠ°Π±ΠΎΡΠ°. ΠΡΠΎ ΡΠ°ΠΊΠΎΠ΅ ΡΠ°Π·ΠΌΠ΅ΡΠ΅Π½ΠΈΠ΅ ΠΈΠ½ΡΡΡΡΠΌΠ΅Π½ΡΠΎΠ², Π΄Π΅ΡΠ°Π»Π΅ΠΉ, ΡΠ°ΡΡ ΠΈ Π΄ΡΡΠ³ΠΈΡ ΠΈΠ½Π΄ΠΈΠΊΠ°ΡΠΎΡΠΎΠ² ΡΠΎΡΡΠΎΡΠ½ΠΈΡ ΠΏΡΠΎΠΈΠ·Π²ΠΎΠ΄ΡΡΠ²Π°, ΠΏΡΠΈ ΠΊΠΎΡΠΎΡΠΎΠΌ ΠΊΠ°ΠΆΠ΄ΡΠΉ Ρ ΠΏΠ΅ΡΠ²ΠΎΠ³ΠΎ Π²Π·Π³Π»ΡΠ΄Π° ΠΌΠΎΠΆΠ΅Ρ ΠΏΠΎΠ½ΡΡΡ ΡΠΎΡΡΠΎΡΠ½ΠΈΠ΅ ΡΠΈΡΡΠ΅ΠΌΡ — Π½ΠΎΡΠΌΠ° ΠΈΠ»ΠΈ ΠΎΡΠΊΠ»ΠΎΠ½Π΅Π½ΠΈΠ΅.
ΠΠ°ΠΈΠ±ΠΎΠ»Π΅Π΅ ΡΠ°ΡΡΠΎ ΠΈΡΠΏΠΎΠ»ΡΠ·ΡΠ΅ΠΌΡΠ΅ ΠΌΠ΅ΡΠΎΠ΄Ρ Π²ΠΈΠ·ΡΠ°Π»ΠΈΠ·Π°ΡΠΈΠΈ:
1)Β Β Β Β Β ΠΠΊΠΎΠ½ΡΡΡΠΈΠ²Π°Π½ΠΈΠ΅
2)Β Β Β Β Β Π¦Π²Π΅ΡΠΎΠ²Π°Ρ ΠΌΠ°ΡΠΊΠΈΡΠΎΠ²ΠΊΠ°
3)Β Β Β Β Β ΠΠ΅ΡΠΎΠ΄ Π΄ΠΎΡΠΎΠΆΠ½ΡΡ Π·Π½Π°ΠΊΠΎΠ²
4)Β Β Β Β Β ΠΠ°ΡΠΊΠΈΡΠΎΠ²ΠΊΠ° ΠΊΡΠ°ΡΠΊΠΎΠΉ
5)Β Β Β Β Β Β«ΠΡΠ»ΠΎΒ»-Β«ΡΡΠ°Π»ΠΎΒ»
6)Β Β Β Β Β ΠΡΠ°ΡΠΈΡΠ΅ΡΠΊΠΈΠ΅ ΡΠ°Π±ΠΎΡΠΈΠ΅ ΠΈΠ½ΡΡΡΡΠΊΡΠΈΠΈ
7)Β Β Β Β Β ΠΠΎΡΠΊΠ° ΠΏΠΎΡΠ΅ΡΠ° ΠΎΡΠ»ΠΈΡΠΈΠ²ΡΠΈΡ ΡΡ ΡΠΎΡΡΡΠ΄Π½ΠΈΠΊΠΎΠ²
Β Β Π’ΡΠ΅Π±ΠΎΠ²Π°Π½ΠΈΡ ΠΊ ΡΡΠ΅Π΄ΡΡΠ²Π°ΠΌ Π²ΠΈΠ·ΡΠ°Π»ΡΠ½ΠΎΠ³ΠΎ ΠΊΠΎΠ½ΡΡΠΎΠ»Ρ:
- ΠΎΠΏΠΈΡΡΠ²Π°ΡΡ ΠΏΠΎΡΠ΅Π½ΡΠΈΠ°Π»ΡΠ½ΡΠ΅ Π½Π΅ΠΈΡΠΏΡΠ°Π²Π½ΠΎΡΡΠΈ ΠΈ Π²ΠΎΠ·ΠΌΠΎΠΆΠ½ΡΠ΅ ΠΎΡΡΠ°Π½ΠΎΠ²ΠΊΠΈ Π² ΡΠ°Π±ΠΎΡΠ΅;
- ΠΏΡΠΎΡΡΡ Π΄Π»Ρ ΠΏΠΎΠ½ΠΈΠΌΠ°Π½ΠΈΡ, ΡΡΠΈΡΡΠ²Π°ΡΡ ΡΠ°Π·Π½ΡΠΉ ΡΡΠΎΠ²Π΅Π½Ρ ΠΎΠ±ΡΠ°Π·ΠΎΠ²Π°Π½Π½ΠΎΡΡΠΈ ΠΈ Π²Π»Π°Π΄Π΅Π½ΠΈΡ ΡΠ·ΡΠΊΠ°ΠΌΠΈ;
- Π²ΠΈΠ΄Π½Ρ ΠΈΠ·Π΄Π°Π»Π΅ΠΊΠ°;
- ΡΠΎΠ΄Π΅ΡΠΆΠ°Ρ Π°ΠΊΡΡΠ°Π»ΡΠ½ΡΡ ΠΈΠ½ΡΠΎΡΠΌΠ°ΡΠΈΡ, ΠΎΠ±Π½ΠΎΠ²Π»ΡΡΡΡΡ ΠΏΠ΅ΡΠΈΠΎΠ΄ΠΈΡΠ΅ΡΠΊΠΈ ΠΈ ΡΠ²ΠΎΠ΅Π²ΡΠ΅ΠΌΠ΅Π½Π½ΠΎ;
- ΠΏΠΎΠ½ΡΡΠ½Ρ Ρ ΠΏΠ΅ΡΠ²ΠΎΠ³ΠΎ ΡΠ°Π·Π°.
Β Β ΠΠ°ΠΏΡΠ°Π²Π»Π΅Π½ΠΈΡ ΡΠ°Π·Π²Π΅ΡΡΡΠ²Π°Π½ΠΈΡ:
- ΠΠΈΠ·ΡΠ°Π»ΠΈΠ·Π°ΡΠΈΡ ΠΌΠ΅ΡΡ Ρ
ΡΠ°Π½Π΅Π½ΠΈΡ, ΠΌΠ°ΡΠΊΠΈΡΠΎΠ²ΠΊΠΈ, ΡΠΊΠ°Π·Π°ΡΠ΅Π»Π΅ΠΉ
- ΠΠΈΠ·ΡΠ°Π»ΠΈΠ·Π°ΡΠΈΡ ΡΡΠ°Π½Π΄Π°ΡΡΠΎΠ² ΡΠ°Π±ΠΎΡ, ΠΏΡΠ°Π²ΠΈΠ», ΠΏΠΎΠ΄ΡΠΊΠ°Π·ΠΎΠΊ
- ΠΠΈΠ·ΡΠ°Π»ΠΈΠ·Π°ΡΠΈΡ ΡΠ΅Ρ Π½ΠΈΠΊΠΈ Π±Π΅Π·ΠΎΠΏΠ°ΡΠ½ΠΎΡΡΠΈ
- ΠΠΈΠ·ΡΠ°Π»ΠΈΠ·Π°ΡΠΈΡ ΡΠ΅Ρ Π½ΠΈΡΠ΅ΡΠΊΠΈΡ ΠΏΡΠΎΠ±Π»Π΅ΠΌ, ΠΎΡΡΠ°Π½ΠΎΠ²ΠΊΠΈ ΠΎΠ±ΠΎΡΡΠ΄ΠΎΠ²Π°Π½ΠΈΡ, Π½Π΅ΠΎΠ±Ρ ΠΎΠ΄ΠΈΠΌΠΎΡΡΠΈ ΠΏΠΎΠΌΠΎΡΠΈ
- ΠΠΈΠ·ΡΠ°Π»ΠΈΠ·Π°ΡΠΈΡ Π·Π°Π΄Π°Π½ΠΈΠΉ, ΠΏΠ»Π°Π½ΠΎΠ² ΡΠ°Π±ΠΎΡ, Π³ΡΠ°ΡΠΈΠΊΠΎΠ²
- ΠΠΈΠ·ΡΠ°Π»ΠΈΠ·Π°ΡΠΈΡ ΡΠ΅Π»Π΅Π²ΡΡ ΠΏΠΎΠΊΠ°Π·Π°ΡΠ΅Π»Π΅ΠΉ, ΡΠ΅ΠΊΡΡΠ΅Π³ΠΎ ΡΠΎΡΡΠΎΡΠ½ΠΈΡ
- ΠΠΈΠ·ΡΠ°Π»ΠΈΠ·Π°ΡΠΈΡ Ρ ΠΎΠ΄Π° ΠΎΡΠ΄Π΅Π»ΡΠ½ΡΡ ΠΏΡΠΎΠ΅ΠΊΡΠΎΠ², ΠΌΠ΅ΡΠΎΠΏΡΠΈΡΡΠΈΠΉ
Β Β ΠΡΠ½ΠΎΠ²Π½ΡΠ΅ ΠΏΡΠ΅ΠΈΠΌΡΡΠ΅ΡΡΠ²Π° ΠΈΠ½ΡΡΡΡΠΌΠ΅Π½ΡΠ°:
- Π²ΠΎΠ·ΠΌΠΎΠΆΠ½ΠΎΡΡΡ Π·Π½Π°ΡΠΈΡΠ΅Π»ΡΠ½ΠΎ ΡΠΏΡΠΎΡΡΠΈΡΡ ΡΠ°Π±ΠΎΡΡ, ΡΡΠΊΠΎΠ½ΠΎΠΌΠΈΡΡ Π²ΡΠ΅ΠΌΡ, ΡΠ½Π΅ΡΠ³ΠΈΡ ΠΈ Π΄Π΅Π½ΡΠ³ΠΈ;
- ΠΏΡΠ΅Π΄ΠΎΡΡΠ°Π²Π»Π΅Π½ΠΈΠ΅ ΠΈΠ½ΡΠΎΡΠΌΠ°ΡΠΈΠΈ ΠΎ ΠΏΠ»Π°Π½ΠΎΠ²ΡΡ ΠΏΠΎΠΊΠ°Π·Π°ΡΠ΅Π»ΡΡ , ΠΊΠΎΡΠΎΡΡΡ Π½ΡΠΆΠ½ΠΎ Π΄ΠΎΡΡΠΈΡΡ, Π½Π°Π»ΠΈΡΠΈΠΈ Π½Π΅ΠΎΠ±Ρ ΠΎΠ΄ΠΈΠΌΡΡ Π² ΡΠ°Π±ΠΎΡΠ΅ ΠΌΠ°ΡΠ΅ΡΠΈΠ°Π»ΠΎΠ² ΠΈ ΠΌΠ΅ΡΡΠ΅ Π²ΡΠΏΠΎΠ»Π½Π΅Π½ΠΈΡ ΡΠ΅Ρ ΠΈΠ»ΠΈ ΠΈΠ½ΡΡ ΡΠ°Π±ΠΎΡ;
- ΡΠ²Π΅Π»ΠΈΡΠ΅Π½ΠΈΠ΅ ΠΏΡΠΎΠΈΠ·Π²ΠΎΠ΄ΠΈΡΠ΅Π»ΡΠ½ΠΎΡΡΠΈ;
- ΠΏΠΎΠΌΠΎΡΡ ΡΡΠΊΠΎΠ²ΠΎΠ΄ΠΈΡΠ΅Π»Ρ Π² ΠΎΠΏΡΠ΅Π΄Π΅Π»Π΅Π½ΠΈΠΈ ΡΠΎΡΡΠΎΡΠ½ΠΈΡ ΠΏΡΠΎΡΠ΅ΡΡΠ°, Π² Π²ΡΡΠ²Π»Π΅Π½ΠΈΠΈ ΡΠ·ΠΊΠΈΡ ΠΌΠ΅ΡΡ Π² ΠΏΡΠΎΠΈΠ·Π²ΠΎΠ΄ΡΡΠ²Π΅Π½Π½ΡΡ ΠΏΡΠΎΡΠ΅ΡΡΠ°Ρ ΠΈ ΠΎΠΏΠ΅ΡΠ°ΡΠΈΡΡ , Π²ΠΎΠ·ΠΌΠΎΠΆΠ½ΠΎΡΡΠΈ ΠΎΠΏΠ΅ΡΠ°ΡΠΈΠ²Π½ΠΎ ΠΏΡΠΈΠ½ΠΈΠΌΠ°ΡΡ ΠΊΠΎΡΡΠ΅ΠΊΡΠΈΡΡΡΡΠΈΠ΅ ΠΌΠ΅ΡΡ;
- ΠΏΠΎΠ΄Π½ΡΡΠΈΠ΅ ΠΊΠΎΠ»Π»Π΅ΠΊΡΠΈΠ²Π½ΠΎΠ³ΠΎ Π΄ΡΡ Π° ΠΈ ΠΌΠΎΡΠ°Π»ΡΠ½ΠΎΠ΅ ΡΡΠΈΠΌΡΠ»ΠΈΡΠΎΠ²Π°Π½ΠΈΠ΅ ΡΠ°Π±ΠΎΡΠ½ΠΈΠΊΠΎΠ².
ΠΡΠΈΠΌΠ΅Π½Π΅Π½ΠΈΠ΅ ΠΈΠ½ΡΡΡΡΠΌΠ΅Π½ΡΠΎΠ² ΠΈ ΠΌΠ΅ΡΠΎΠ΄ΠΎΠ² Π±Π΅ΡΠ΅ΠΆΠ»ΠΈΠ²ΠΎΠ³ΠΎ ΠΏΡΠΎΠΈΠ·Π²ΠΎΠ΄ΡΡΠ²Π° ΠΏΠΎΠ·Π²ΠΎΠ»ΡΠ΅Ρ Π΄ΠΎΠ±ΠΈΡΡΡΡ Π·Π½Π°ΡΠΈΡΠ΅Π»ΡΠ½ΠΎΠ³ΠΎ ΠΏΠΎΠ²ΡΡΠ΅Π½ΠΈΡ ΡΡΡΠ΅ΠΊΡΠΈΠ²Π½ΠΎΡΡΠΈ Π΄Π΅ΡΡΠ΅Π»ΡΠ½ΠΎΡΡΠΈ ΠΏΡΠ΅Π΄ΠΏΡΠΈΡΡΠΈΡ, ΠΏΡΠΎΠΈΠ·Π²ΠΎΠ΄ΠΈΡΠ΅Π»ΡΠ½ΠΎΡΡΠΈ ΡΡΡΠ΄Π°, ΡΠ»ΡΡΡΠ΅Π½ΠΈΡ ΠΊΠ°ΡΠ΅ΡΡΠ²Π° Π²ΡΠΏΡΡΠΊΠ°Π΅ΠΌΠΎΠΉ ΠΏΡΠΎΠ΄ΡΠΊΡΠΈΠΈ ΠΈ ΡΠΎΡΡΠ° ΠΊΠΎΠ½ΠΊΡΡΠ΅Π½ΡΠΎΡΠΏΠΎΡΠΎΠ±Π½ΠΎΡΡΠΈ Π±Π΅Π· Π·Π½Π°ΡΠΈΡΠ΅Π»ΡΠ½ΡΡ ΠΊΠ°ΠΏΠΈΡΠ°Π»ΡΠ½ΡΡ Π²Π»ΠΎΠΆΠ΅Π½ΠΈΠΉ.
Β
Β Β Β Β Π‘ΡΠ°Π½Π΄Π°ΡΡΠΈΠ·Π°ΡΠΈΡ β ΡΡΠΎ ΡΡΡΠ΅ΠΌΠ»Π΅Π½ΠΈΠ΅ ΠΊ Π²ΡΠΏΠΎΠ»Π½Π΅Π½ΠΈΡ ΡΠ°Π±ΠΎΡΡ ΠΏΠΎ ΠΏΡΠ°Π²ΠΈΠ»Π°ΠΌ, ΠΏΡΡΠ΅ΠΌ ΡΠ°Π·ΡΠ°Π±ΠΎΡΠΊΠΈ Π΄ΠΎΠΊΡΠΌΠ΅Π½ΡΠΎΠ² ΠΎΠΏΡΠ΅Π΄Π΅Π»ΡΡΡΠΈΡ ΡΠ°Π³ Π·Π° ΡΠ°Π³ΠΎΠΌ ΠΏΡΠΎΠΈΠ·Π²ΠΎΠ΄ΡΡΠ²Π΅Π½Π½ΡΠΉ ΠΏΡΠΎΡΠ΅ΡΡ.
Β Β Π’ΡΠ΅Π±ΠΎΠ²Π°Π½ΠΈΡ ΠΊ ΡΡΠ°Π½Π΄Π°ΡΡΠ°ΠΌ:
- Π»Π΅Π³ΠΊΠΎ ΡΠΈΡΠ°Π΅ΠΌΡ;
- Π²ΠΈΠ·ΡΠ°Π»ΡΠ½ΠΎ ΠΏΠΎΠ½ΡΡΠ½Ρ;
- Π²ΠΊΠ»ΡΡΠ°ΡΡΠΈΠ΅ ΡΠΎΠ»ΡΠΊΠΎ ΠΈΠΌΠ΅ΡΡΠΈΠ΅ΡΡ ΠΈΠ½ΡΡΡΡΠΌΠ΅Π½ΡΡ ΠΈ ΠΌΠ°ΡΠ΅ΡΠΈΠ°Π»Ρ;
- ΠΏΡΠΎΠ²Π΅ΡΠ΅Π½Ρ ΠΈ ΠΎΠ΄ΠΎΠ±ΡΠ΅Π½Ρ ΡΡΠΊΠΎΠ²ΠΎΠ΄ΡΡΠ²ΠΎΠΌ.
Β Β ΠΠ°ΠΏΡΠ°Π²Π»Π΅Π½ΠΈΡ ΡΠ°Π·Π²Π΅ΡΡΡΠ²Π°Π½ΠΈΡ:
- Π Π°Π·ΡΠ°Π±ΠΎΡΠΊΠ° ΠΎΡΠ³Π°Π½ΠΈΠ·Π°ΡΠΈΠΎΠ½Π½ΡΡ ΡΡΠ°Π½Π΄Π°ΡΡΠΎΠ² (ΠΠΎΠ»ΠΈΡΠΈΠΊ, ΠΏΡΠ°Π²ΠΈΠ», ΠΈΠ½ΡΡΡΡΠΊΡΠΈΠΉ, Π½ΠΎΡΠΌ, ΡΠΊΠ°Π·Π°Π½ΠΈΠΉ).
Π Π°Π·ΡΠ°Π±ΠΎΡΠΊΠ° ΠΎΠΏΠ΅ΡΠ°ΡΠΈΠΎΠ½Π½ΡΡ ΡΡΠ°Π½Π΄Π°ΡΡΠΎΠ² (ΠΠΏΠΈΡΠ°Π½ΠΈΠΉ Π²ΡΠΏΠΎΠ»Π½Π΅Π½ΠΈΡ ΡΠ°Π±ΠΎΡΡ, ΠΏΡΠΎΡΠ΅ΡΡΠΎΠ²).
Β
Β Β Β ΠΡΠ΅ΠΎΠ±ΡΠ°Ρ ΡΠΊΡΠΏΠ»ΡΠ°ΡΠ°ΡΠΈΠΎΠ½Π½Π°Ρ ΡΠΈΡΡΠ΅ΠΌΠ° (Total Productive Maintenance, TPM) β ΡΡΠΎ ΠΎΠ±Π΅ΡΠΏΠ΅ΡΠ΅Π½ΠΈΠ΅ Π±Π΅ΡΠΏΠ΅ΡΠ΅Π±ΠΎΠΉΠ½ΠΎΡΡΠΈ ΡΠ°Π±ΠΎΡΡ ΠΎΠ±ΠΎΡΡΠ΄ΠΎΠ²Π°Π½ΠΈΡ Ρ Π·Π°Π΄Π°Π½Π½ΡΠΌΠΈ ΠΏΠ°ΡΠ°ΠΌΠ΅ΡΡΠ°ΠΌΠΈ.
Β Β Π¦Π΅Π»ΠΈ TPM β ΡΠ½ΠΈΠΆΠ΅Π½ΠΈΠ΅ ΡΠ΅ΡΡΠΈ Π²ΠΈΠ΄ΠΎΠ² ΠΏΠΎΡΠ΅ΡΡ, ΡΡ ΡΠ΄ΡΠ°ΡΡΠΈΡ ΡΡΡΠ΅ΠΊΡΠΈΠ²Π½ΠΎΡΡΡ ΠΈΡΠΏΠΎΠ»ΡΠ·ΠΎΠ²Π°Π½ΠΈΡ ΠΎΠ±ΠΎΡΡΠ΄ΠΎΠ²Π°Π½ΠΈΡ:
β Β | ΠΠ°ΠΈΠΌΠ΅Π½ΠΎΠ²Π°Π½ΠΈΠ΅ ΠΏΠΎΡΠ΅ΡΡΒ | Π¦Π΅Π»ΡΒ | ΠΠΎΡΡΠ½Π΅Π½ΠΈΠ΅Β |
1 | ΠΠΎΡΠ΅ΡΠΈ ΠΈΠ·-Π·Π° ΠΏΠΎΠ»ΠΎΠΌΠΎΠΊ ΠΎΠ±ΠΎΡΡΠ΄ΠΎΠ²Π°Π½ΠΈΡ | 0 | ΠΠΎΡΠ΅ΡΠΈ ΠΈΠ·-Π·Π° ΠΏΠΎΠ»ΠΎΠΌΠΎΠΊ ΠΏΠΎ Π²ΡΠ΅ΠΌΡ ΠΎΠ±ΠΎΡΡΠ΄ΠΎΠ²Π°Π½ΠΈΡ Π΄ΠΎΠ»ΠΆΠ½Ρ Π±ΡΡΡ Π΄ΠΎΠ²Π΅Π΄Π΅Π½Ρ Π΄ΠΎ Π½ΡΠ»Ρ |
2 | ΠΠΎΡΠ΅ΡΠΈ ΠΈΠ·-Π·Π° ΠΏΠ΅ΡΠ΅Π½Π°Π»Π°Π΄ΠΎΠΊ ΠΈ ΡΠ΅Π³ΡΠ»ΠΈΡΠΎΠ²ΠΎΠΊ ΠΎΠ±ΠΎΡΡΠ΄ΠΎΠ²Π°Π½ΠΈΡ | ΠΠΈΠ½ΠΈΠΌΠΈΠ·Π°ΡΠΈΡ | ΠΠΈΠ½ΠΈΠΌΠΈΠ·Π°ΡΠΈΡ ΠΏΡΠΎΠ΄ΠΎΠ»ΠΆΠΈΡΠ΅Π»ΡΠ½ΠΎΡΡΡ ΠΏΠ΅ΡΠ΅Π½Π°Π»Π°Π΄ΠΊΠΈ ΠΎΠ±ΠΎΡΡΠ΄ΠΎΠ²Π°Π½ΠΈΡ, Π² ΡΠ°ΡΡΠ½ΠΎΡΡΠΈ Π΄ΠΎΠ²Π΅ΡΡΠΈ ΠΏΠ΅ΡΠ΅Π½Π°Π»Π°Π΄ΠΊΠΈ Π΄ΠΎ ΡΡΠΎΠ²Π½Ρ Β«Π΅Π΄ΠΈΠ½ΠΈΡΠ½ΠΎΠΉ ΠΏΠ΅ΡΠ΅Π½Π°Π»Π°Π΄ΠΊΠΈΒ» (ΠΏΡΠΎΠ΄ΠΎΠ»ΠΆΠΈΡΠ΅Π»ΡΠ½ΠΎΡΡΡΡ ΠΌΠ΅Π½Π΅Π΅ 10 ΠΌΠΈΠ½), Π° ΡΠ°Π±ΠΎΡΡ ΠΏΠΎ ΡΠ΅Π³ΡΠ»ΠΈΡΠΎΠ²ΠΊΠ΅ ΠΎΠ±ΠΎΡΡΠ΄ΠΎΠ²Π°Π½ΠΈΡ ΡΠ²Π΅ΡΡΠΈ ΠΊ Π½ΡΠ»Ρ |
3 | ΠΠΎΡΠ΅ΡΠΈ ΠΈΠ·-Π·Π° ΡΠ½ΠΈΠΆΠ΅Π½ΠΈΡ ΡΠΊΠΎΡΠΎΡΡΠΈ ΡΠ°Π±ΠΎΡΡ ΠΎΠ±ΠΎΡΡΠ΄ΠΎΠ²Π°Π½ΠΈΡ | 0 | Π Π°Π·ΡΡΠ² ΠΌΠ΅ΠΆΠ΄Ρ ΠΏΠ°ΡΠΏΠΎΡΡΠ½ΡΠΌΠΈ ΡΠ΅Ρ Π½ΠΈΡΠ΅ΡΠΊΠΈΠΌΠΈ Ρ Π°ΡΠ°ΠΊΡΠ΅ΡΠΈΡΡΠΈΠΊΠ°ΠΌΠΈ ΠΎΠ±ΠΎΡΡΠ΄ΠΎΠ²Π°Π½ΠΈΡ ΠΈ ΡΠ΅Π°Π»ΡΠ½ΡΠΌΠΈ Ρ Π°ΡΠ°ΠΊΡΠ΅ΡΠΈΡΡΠΈΠΊΠ°ΠΌΠΈ Π΅Π³ΠΎ ΡΠ°Π±ΠΎΡΡ Π΄ΠΎΠ²Π΅ΡΡΠΈ Π΄ΠΎ Π½ΡΠ»Ρ. ΠΠ° ΡΡΠ΅Ρ ΠΌΠΎΠ΄Π΅ΡΠ½ΠΈΠ·Π°ΡΠΈΠΈ ΠΎΠ±ΠΎΡΡΠ΄ΠΎΠ²Π°Π½ΠΈΡ ΠΏΡΠ΅Π²ΡΡΠΈΡΡ ΠΏΠ°ΡΠΏΠΎΡΡΠ½ΡΡ ΡΠΊΠΎΡΠΎΡΡΡ Π΅Π³ΠΎ ΡΠ°Π±ΠΎΡΡ |
4 | ΠΠΎΡΠ΅ΡΠΈ ΠΈΠ·-Π·Π° ΠΌΠ΅Π»ΠΊΠΈΡ ΠΎΡΡΠ°Π½ΠΎΠ²ΠΎΠΊ ΠΎΠ±ΠΎΡΡΠ΄ΠΎΠ²Π°Π½ΠΈΡ | 0 | ΠΠΎΡΠ΅ΡΠΈ ΠΈΠ·-Π·Π° ΠΌΠ΅Π»ΠΊΠΈΡ ΠΎΡΡΠ°Π½ΠΎΠ²ΠΎΠΊ ΠΏΠΎ Π²ΡΠ΅ΠΌΡ ΠΎΠ±ΠΎΡΡΠ΄ΠΎΠ²Π°Π½ΠΈΡ Π΄ΠΎΠ»ΠΆΠ½Ρ Π±ΡΡΡ Π΄ΠΎΠ²Π΅Π΄Π΅Π½Ρ Π΄ΠΎ Π½ΡΠ»Ρ |
5 | ΠΠΎΡΠ΅ΡΠΈ ΠΈΠ·-Π·Π° Π±ΡΠ°ΠΊΠ° ΠΈ ΠΏΠ΅ΡΠ΅Π΄Π΅Π»ΠΎΠΊ | 0 | ΠΠΎΡΠ΅ΡΠΈ ΠΈΠ·-Π·Π° Π±ΡΠ°ΠΊΠ° ΠΈ ΠΏΠ΅ΡΠ΅Π΄Π΅Π»ΠΎΠΊ ΠΏΠΎ ΠΏΡΠΈΡΠΈΠ½Π΅ ΠΎΠ±ΠΎΡΡΠ΄ΠΎΠ²Π°Π½ΠΈΡ Π΄ΠΎΠ»ΠΆΠ½Ρ Π±ΡΡΡ ΡΠΌΠ΅Π½ΡΡΠ΅Π½Ρ ΠΏΡΠ°ΠΊΡΠΈΡΠ΅ΡΠΊΠΈ Π΄ΠΎ Π½ΡΠ»Ρ |
6 | ΠΠΎΡΠ΅ΡΠΈ ΠΏΡΠΈ Π·Π°ΠΏΡΡΠΊΠ΅ ΠΎΠ±ΠΎΡΡΠ΄ΠΎΠ²Π°Π½ΠΈΡ | ΠΠΈΠ½ΠΈΠΌΠΈΠ·Π°ΡΠΈΡ | ΠΠΈΠ½ΠΈΠΌΠΈΠ·ΠΈΡΠΎΠ²Π°ΡΡ ΠΏΠΎΡΠ΅ΡΠΈ ΠΏΡΠΈ Π·Π°ΠΏΡΡΠΊΠ΅ ΠΎΠ±ΠΎΡΡΠ΄ΠΎΠ²Π°Π½ΠΈΡ |
Β
Β Β ΠΠ°ΠΏΡΠ°Π²Π»Π΅Π½ΠΈΡ ΡΠ°Π·Π²Π΅ΡΡΡΠ²Π°Π½ΠΈΡ:
1. Π‘Π°ΠΌΠΎΡΡΠΎΡΡΠ΅Π»ΡΠ½ΠΎΠ΅ ΠΎΠ±ΡΠ»ΡΠΆΠΈΠ²Π°Π½ΠΈΠ΅ ΠΎΠ±ΠΎΡΡΠ΄ΠΎΠ²Π°Π½ΠΈΡ:
- Π°Π²ΡΠΎΠ½ΠΎΠΌΠ½ΠΎΠ΅ ΠΎΠ±ΡΠ»ΡΠΆΠΈΠ²Π°Π½ΠΈΠ΅ (ΠΎΠΏΠ΅ΡΠ°ΡΠΎΡ)
- ΠΎΠ±ΡΡΠ΅Π½ΠΈΠ΅ ΠΏΠΎ ΠΎΠ±ΡΠ»ΡΠΆΠΈΠ²Π°Π½ΠΈΡ ΠΈ ΡΠ΅ΠΌΠΎΠ½ΡΡ ΠΎΠ±ΠΎΡΡΠ΄ΠΎΠ²Π°Π½ΠΈΡ Π΄Π»Ρ ΠΎΠΏΠ΅ΡΠ°ΡΠΎΡΠΎΠ² ΠΈ ΡΠ΅ΠΌΠΎΠ½ΡΠ½ΠΈΠΊΠΎΠ².
2. ΠΠΎΠ΄Π΄Π΅ΡΠΆΠΊΠ° Π½ΠΎΡΠΌΠ°Π»ΡΠ½ΠΎΠ³ΠΎ ΡΡΠ½ΠΊΡΠΈΠΎΠ½ΠΈΡΠΎΠ²Π°Π½ΠΈΡ ΠΎΠ±ΠΎΡΡΠ΄ΠΎΠ²Π°Π½ΠΈΡ Π½Π° ΠΏΡΠΎΡΡΠΆΠ΅Π½ΠΈΠΈ Π΅Π³ΠΎ ΠΆΠΈΠ·Π½Π΅Π½Π½ΠΎΠ³ΠΎ ΡΠΈΠΊΠ»Π°:
- ΠΏΡΠ΅Π΄ΠΎΡΠ²ΡΠ°ΡΠ΅Π½ΠΈΠ΅ ΠΈ ΡΠ°Π½Π΅Π΅ ΠΎΠ±Π½Π°ΡΡΠΆΠ΅Π½ΠΈΠ΅ Π½Π΅ΠΈΡΠΏΡΠ°Π²Π½ΠΎΡΡΠΈ ΠΎΠ±ΠΎΡΡΠ΄ΠΎΠ²Π°Π½ΠΈΡ
- ΠΏΠ»Π°Π½ΠΎΠ²ΠΎΠ΅ ΠΎΠ±ΡΠ»ΡΠΆΠΈΠ²Π°Π½ΠΈΠ΅
- Π±ΡΡΡΡΠΎΠ΅ ΡΠ΅Π°Π³ΠΈΡΠΎΠ²Π°Π½ΠΈΠ΅ Π½Π° Π²ΠΎΠ·Π½ΠΈΠΊΡΠΈΠ΅ ΠΏΡΠΎΠ±Π»Π΅ΠΌΡ Ρ ΠΎΠ±ΠΎΡΡΠ΄ΠΎΠ²Π°Π½ΠΈΠ΅ΠΌ
3. ΠΡΠΎΠ²Π΅Π΄Π΅Π½ΠΈΠ΅ ΠΎΡΠ΄Π΅Π»ΡΠ½ΡΡ ΡΠ»ΡΡΡΠ΅Π½ΠΈΠΉ, ΠΊΠΎΡΠ²Π΅Π½Π½ΠΎ ΡΠ²ΡΠ·Π°Π½Π½ΡΡ Ρ ΠΎΠ±ΡΠ»ΡΠΆΠΈΠ²Π°Π½ΠΈΠ΅ΠΌ ΠΎΠ±ΠΎΡΡΠ΄ΠΎΠ²Π°Π½ΠΈΡ:
- ΡΠ°Π·Π²ΠΈΡΠΈΠ΅ Π΄Π΅ΡΡΠ΅Π»ΡΠ½ΠΎΡΡΠΈ ΠΏΠΎ ΡΠ»ΡΡΡΠ΅Π½ΠΈΡ ΠΊΠ°ΡΠ΅ΡΡΠ²Π°
- ΡΠΎΠ·Π΄Π°Π½ΠΈΠ΅ ΡΠΈΡΡΠ΅ΠΌΡ ΡΠΏΡΠ°Π²Π»Π΅Π½ΠΈΡ ΡΠ°Π·ΡΠ°Π±ΠΎΡΠΊΠΎΠΉ ΠΈ Π²Π½Π΅Π΄ΡΠ΅Π½ΠΈΠ΅ΠΌ Π½ΠΎΠ²ΠΎΠ³ΠΎ ΠΎΠ±ΠΎΡΡΠ΄ΠΎΠ²Π°Π½ΠΈΡ
- ΡΠΎΠ²Π΅ΡΡΠ΅Π½ΡΡΠ²ΠΎΠ²Π°Π½ΠΈΠ΅ ΡΠΈΡΡΠ΅ΠΌΡ ΠΎΡ ΡΠ°Π½Ρ ΡΡΡΠ΄Π° ΠΈ ΠΎΠΊΡΡΠΆΠ°ΡΡΠ΅ΠΉ ΡΡΠ΅Π΄Ρ
Β
Β Β Β Β Π’ΠΎΡΠ½ΠΎ Π²ΠΎΠ²ΡΠ΅ΠΌΡ β ΡΡΠΎ ΠΏΠΎΡΡΡΠΏΠ»Π΅Π½ΠΈΠ΅ Π½Π° ΠΊΠ°ΠΆΠ΄ΡΠΉ ΠΏΠΎΡΠ»Π΅Π΄ΡΡΡΠΈΠΉ ΠΏΡΠΎΡΠ΅ΡΡ Π² ΠΏΠΎΡΠΎΠΊΠ΅ ΡΠ΅Π½Π½ΠΎΡΡΠ΅ΠΉ:
- ΡΠΎΠ»ΡΠΊΠΎ ΡΠ΅Ρ ΡΠ»Π΅ΠΌΠ΅Π½ΡΠΎΠ² ΡΠ°Π±ΠΎΡ, ΠΊΠΎΡΠΎΡΡΠ΅ Π½Π΅ΠΎΠ±Ρ ΠΎΠ΄ΠΈΠΌΡ;
- ΠΈΠΌΠ΅Π½Π½ΠΎ Π² ΡΠΎΡ ΠΌΠΎΠΌΠ΅Π½Ρ, ΠΊΠΎΠ³Π΄Π° ΡΡΠΎ ΡΡΠ΅Π±ΡΠ΅ΡΡΡ;
- ΡΠΎΡΠ½ΠΎ Π² ΡΠ΅Ρ ΠΊΠΎΠ»ΠΈΡΠ΅ΡΡΠ²Π°Ρ , ΠΊΠΎΡΠΎΡΡΠ΅ Π² ΡΡΠΎΡ ΠΌΠΎΠΌΠ΅Π½Ρ Π½Π΅ΠΎΠ±Ρ ΠΎΠ΄ΠΈΠΌΡ.
Β Β ΠΠ°ΠΏΡΠ°Π²Π»Π΅Π½ΠΈΡ ΡΠ°Π·Π²Π΅ΡΡΡΠ²Π°Π½ΠΈΡ:
- ΠΠ΅ΡΠ΅Ρ ΠΎΠ΄ ΠΎΡ Π²ΡΡΠ°Π»ΠΊΠΈΠ²Π°Π½ΠΈΡ ΠΊ Π²ΡΡΡΠ³ΠΈΠ²Π°Π½ΠΈΡ.
- Π‘ΠΎΠΊΡΠ°ΡΠ΅Π½ΠΈΠ΅ Π²ΡΠ΅Ρ Π²ΠΈΠ΄ΠΎΠ² Π·Π°ΠΏΠ°ΡΠΎΠ².
- Π‘ΠΎΠΊΡΠ°ΡΠ΅Π½ΠΈΠ΅ Π²ΡΠ΅ΠΌΠ΅Π½ΠΈ ΠΏΡΠΎΠΈΠ·Π²ΠΎΠ΄ΡΡΠ²Π΅Π½Π½ΡΡ ΡΠΈΠΊΠ»ΠΎΠ².
Β Β ΠΠΎΠ·ΠΌΠΎΠΆΠ½ΡΠ΅ ΠΈΠ½ΡΡΡΡΠΌΠ΅Π½ΡΡ:
- ΠΠ°Π½Π±Π°Π½
- Π‘ΡΠΏΠ΅ΡΠΌΠ°ΡΠΊΠ΅ΡΡ
- Π‘ΡΠ°Π½Π΄Π°ΡΡΠΈΠ·Π°ΡΠΈΡ
Β
Β Β Β Β Β Β«ΠΠΎΠΊΠ°-ΡΠΊΠ°Β» — ΠΌΠ΅ΡΠΎΠ΄ ΠΏΡΠ΅Π΄ΠΎΡΠ²ΡΠ°ΡΠ΅Π½ΠΈΡ.
Β Β ΠΠ°Π·Π½Π°ΡΠ΅Π½ΠΈΠ΅ ΠΌΠ΅ΡΠΎΠ΄Π°.
Π Π°Π·Π»ΠΈΡΠ½ΡΠ΅ ΠΏΡΠΈΠ΅ΠΌΡ Π·Π°ΡΠΈΡΡ ΠΎΡ ΠΎΡΠΈΠ±ΠΎΠΊ ΡΠ»Π΅Π΄ΡΠ΅Ρ ΠΏΡΠΈΠΌΠ΅Π½ΡΡΡ ΠΊΠ°ΠΊ ΠΏΡΠΈ Π²Ρ ΠΎΠ΄Π½ΠΎΠΌ ΠΊΠΎΠ½ΡΡΠΎΠ»Π΅, ΡΠ°ΠΊ ΠΈ Π² Ρ ΠΎΠ΄Π΅ Π²ΡΠ΅Π³ΠΎ ΠΏΡΠΎΡΠ΅ΡΡΠ° ΠΈΠ·Π³ΠΎΡΠΎΠ²Π»Π΅Π½ΠΈΡ ΠΏΡΠΎΠ΄ΡΠΊΡΠΈΠΈ.
Β Β Π¦Π΅Π»Ρ ΠΌΠ΅ΡΠΎΠ΄Π°.
ΠΠΎΠ²ΡΡΠ΅Π½ΠΈΠ΅ ΠΏΠΎΡΡΠ΅Π±ΠΈΡΠ΅Π»ΡΠ½ΠΎΠΉ ΡΡΠΎΠΈΠΌΠΎΡΡΠΈ ΠΏΡΠΎΠ΄ΡΠΊΡΠΈΠΈ ΠΏΡΡΠ΅ΠΌ ΠΏΡΠ΅Π΄ΠΎΡΠ²ΡΠ°ΡΠ΅Π½ΠΈΡ ΠΎΡΠΈΠ±ΠΎΠΊ Π½Π° Π΄Π΅ΠΉΡΡΠ²ΡΡΡΠ΅ΠΌ ΠΏΡΠΎΠΈΠ·Π²ΠΎΠ΄ΡΡΠ²Π΅.
Β Β Π‘ΡΡΡ ΠΌΠ΅ΡΠΎΠ΄Π°.
ΠΠ°ΡΠΈΡΠ° ΠΎΡ ΠΎΡΠΈΠ±ΠΎΠΊ Π»Π΅ΠΆΠΈΡ Π² ΠΎΡΠ½ΠΎΠ²Π΅ Π±Π΅Π·Π΄Π΅ΡΠ΅ΠΊΡΠ½ΠΎΠ³ΠΎ ΠΏΡΠΎΠΈΠ·Π²ΠΎΠ΄ΡΡΠ²Π°.
ΠΠΎΠ½ΡΠ΅ΠΏΡΠΈΡ ΠΏΡΠ΅Π΄ΡΠΏΡΠ΅ΠΆΠ΄Π΅Π½ΠΈΡ Π½Π΅ΠΆΠ΅Π»Π°ΡΠ΅Π»ΡΠ½ΡΡ ΡΠΎΠ±ΡΡΠΈΠΉ, Π²ΡΠ·Π²Π°Π½Π½ΡΡ ΠΎΡΠΈΠ±ΠΊΠ°ΠΌΠΈ ΡΠ΅Π»ΠΎΠ²Π΅ΠΊΠ°, ΠΏΡΠΎΡΡΠ°. ΠΡΠ»ΠΈ Π½Π΅ Π΄ΠΎΠΏΡΡΠΊΠ°ΡΡ ΠΈΡ Π²ΠΎΠ·Π½ΠΈΠΊΠ½ΠΎΠ²Π΅Π½ΠΈΡ Π½Π° Π΄Π΅ΠΉΡΡΠ²ΡΡΡΠ΅ΠΌ ΠΏΡΠΎΠΈΠ·Π²ΠΎΠ΄ΡΡΠ²Π΅, ΡΠΎ ΠΊΠ°ΡΠ΅ΡΡΠ²ΠΎ Π±ΡΠ΄Π΅Ρ Π²ΡΡΠΎΠΊΠΈΠΌ, Π° Π΄ΠΎΡΠ°Π±ΠΎΡΠΊΠΈ — Π½Π΅Π±ΠΎΠ»ΡΡΠΈΠΌΠΈ. ΠΡΠΎ ΠΏΡΠΈΠ²ΠΎΠ΄ΠΈΡ ΠΊ ΡΠ°ΡΡΡΡΠ΅ΠΉ ΡΠ΄ΠΎΠ²Π»Π΅ΡΠ²ΠΎΡΠ΅Π½Π½ΠΎΡΡΠΈ ΠΏΠΎΡΡΠ΅Π±ΠΈΡΠ΅Π»Ρ ΠΈ ΠΎΠ΄Π½ΠΎΠ²ΡΠ΅ΠΌΠ΅Π½Π½ΠΎ ΠΊ ΡΠ½ΠΈΠΆΠ΅Π½ΠΈΡ ΠΈΠ·Π΄Π΅ΡΠΆΠ΅ΠΊ ΠΏΡΠΎΠΈΠ·Π²ΠΎΠ΄ΡΡΠ²Π°.
Β Β ΠΠ»Π°Π½ Π΄Π΅ΠΉΡΡΠ²ΠΈΠΉ.
Π‘ΡΠΎΡΠΌΠΈΡΠΎΠ²Π°ΡΡ ΠΊΠΎΠΌΠ°Π½Π΄Ρ ΠΈΠ· ΡΠΏΠ΅ΡΠΈΠ°Π»ΠΈΡΡΠΎΠ²: ΠΏΡΠ΅Π΄ΡΡΠ°Π²ΠΈΡΠ΅Π»Π΅ΠΉ ΡΡΠΊΠΎΠ²ΠΎΠ΄ΡΡΠ²Π°, ΡΠ»ΡΠΆΠ±Ρ ΠΊΠ°ΡΠ΅ΡΡΠ²Π°, ΡΠ΅Ρ Π½ΠΈΡΠ΅ΡΠΊΠΎΠΉ ΡΠ»ΡΠΆΠ±Ρ ΠΈ ΠΏΡΠΎΠΈΠ·Π²ΠΎΠ΄ΡΡΠ²Π°.
ΠΡΡΠ²ΠΈΡΡ ΠΏΡΠΎΠ±Π»Π΅ΠΌΡ, ΡΡΠ΅Π±ΡΡΡΠΈΠ΅ ΡΠ΅ΡΠ΅Π½ΠΈΡ, ΠΈ ΠΏΡΠΈΡΠΈΠ½Ρ ΠΈΡ ΡΡΡΠ΅ΡΡΠ²ΠΎΠ²Π°Π½ΠΈΡ.
Π Π°Π·ΡΠ°Π±ΠΎΡΠ°ΡΡ ΠΌΠ΅ΡΡ ΠΏΠΎ ΡΠΎΠ²Π΅ΡΡΠ΅Π½ΡΡΠ²ΠΎΠ²Π°Π½ΠΈΡ ΠΏΡΠΎΠΈΠ·Π²ΠΎΠ΄ΡΡΠ²Π° ΠΈ ΠΏΡΠ΅Π΄ΠΎΡΠ²ΡΠ°ΡΠ΅Π½ΠΈΡ Π²ΠΎΠ·ΠΌΠΎΠΆΠ½ΠΎΡΡΠΈ Π²ΠΎΠ·Π½ΠΈΠΊΠ½ΠΎΠ²Π΅Π½ΠΈΡ ΠΎ ΡΠΈΠ±ΠΎΠΊ, ΡΡΠΊΠΎΠ²ΠΎΠ΄ΡΡΠ²ΡΡΡΡ ΠΏΡΠ°Π²ΠΈΠ»Π°ΠΌΠΈ ΠΏΡΠΈΠΌΠ΅Π½Π΅Π½ΠΈΡ ΠΌΠ΅ΡΠΎΠ΄Π° ΠΏΠΎΠΊΠ°-ΡΠΊΡ.
Π£ΡΡΡΠ°Π½ΠΈΡΡ ΠΏΠΎΡΠ΅Π½ΡΠΈΠ°Π»ΡΠ½ΡΠ΅ ΠΎΡΠΈΠ±ΠΊΠΈ, ΠΈΡΠΏΠΎΠ»ΡΠ·ΡΡ Π² ΠΏΡΠΎΡΠ΅ΡΡΠ΅ ΠΏΡΠΎΠΈΠ·Π²ΠΎΠ΄ΡΡΠ²Π° ΡΡΠΎΠ²Π΅ΡΡΠ΅Π½ΡΡΠ²ΠΎΠ²Π°Π½Π½ΡΠ΅ ΠΏΡΠΈΡΠΏΠΎΡΠΎΠ±Π»Π΅Π½ΠΈΡ, ΠΏΡΠΈΠ±ΠΎΡΡ ΠΈ ΠΎΠ±ΠΎΡΡΠ΄ΠΎΠ²Π°Π½ΠΈΠ΅.
Β Β ΠΡΠΎΠ±Π΅Π½Π½ΠΎΡΡΠΈ ΠΌΠ΅ΡΠΎΠ΄Π°.
Β Β Π‘ΠΎΠ²ΡΠ΅ΠΌΠ΅Π½Π½Π°Ρ Π²Π΅ΡΡΠΈΡ Π·Π°ΡΠΈΡΡ ΠΎΡ ΠΎΡΠΈΠ±ΠΎΠΊ, ΠΈΠ·Π²Π΅ΡΡΠ½Π°Ρ ΠΏΠΎΠ΄ Π½Π°Π·Π²Π°Π½ΠΈΠ΅ΠΌ ΠΏΠΎΠΊΠ°-ΡΠΊΡ (poka-yoke1), ΠΏΠΎΡΠ²ΠΈΠ»Π°ΡΡ Π² Π―ΠΏΠΎΠ½ΠΈΠΈ, ΡΡΠΎΠ±Ρ ΠΏΠΎΠ²ΡΡΠ°ΡΡ ΠΊΠ°ΡΠ΅ΡΡΠ²ΠΎ ΠΏΡΠΎΠ΄ΡΠΊΡΠΈΠΈ, ΠΏΡΠ΅Π΄ΠΎΡΠ²ΡΠ°ΡΠ°Ρ ΠΎΡΠΈΠ±ΠΊΠΈ Π½Π° Π΄Π΅ΠΉΡΡΠ²ΡΡΡΠ΅ΠΌ ΠΏΡΠΎΠΈΠ·Π²ΠΎΠ΄ΡΡΠ²Π΅. Π Π°Π½Π΅Π΅ ΡΠΏΠΎΠ½ΡΠΊΠΈΠΌΠΈ ΡΠΏΠ΅ΡΠΈΠ°Π»ΠΈΡΡΠ°ΠΌΠΈ ΠΏΡΠΈΠΌΠ΅Π½ΡΠ»ΡΡ ΡΠ΅ΡΠΌΠΈΠ½ Π±Π°ΠΊΠ°-ΡΠΊΡ (baka-yoke). ΠΠΎΡΠ»ΠΎΠ²Π½ΡΠΉ ΠΏΠ΅ΡΠ΅Π²ΠΎΠ΄ ΡΠ΅ΡΠΌΠΈΠ½Π° «Π±Π°ΠΊΠ°-ΡΠΊΡ» — «Π·Π°ΡΠΈΡΠ° ΠΎΡ Π³Π»ΡΠΏΠΎΡΡΠΈ», ΠΈΠ½ΡΠΌΠΈ ΡΠ»ΠΎΠ²Π°ΠΌΠΈ, — ΡΡΠΎ Π·Π°ΡΠΈΡΠ½ΠΎΠ΅ ΡΡΡΡΠΎΠΉΡΡΠ²ΠΎ, Π±Π»Π°Π³ΠΎΠ΄Π°ΡΡ ΠΊΠΎΡΠΎΡΠΎΠΌΡ Π΄Π΅ΡΠ΅ΠΊΡΡ ΠΏΡΠΎΡΡΠΎ Π½Π΅ ΠΎΠ±ΡΠ°Π·ΡΡΡΡΡ. Π‘Π»Π΅Π΄ΡΠ΅Ρ ΠΎΡΠΌΠ΅ΡΠΈΡΡ, ΡΡΠΎ ΠΎΡΠ½ΠΎΠ²Π½ΡΠ΅ ΠΏΠΎΠ»ΠΎΠΆΠ΅Π½ΠΈΡ ΡΡΠΎΠΉ ΠΊΠΎΠ½ΡΠ΅ΠΏΡΠΈΠΈ ΡΠΈΡΠΎΠΊΠΎ ΠΏΡΠΈΠΌΠ΅Π½ΡΠ»ΠΈΡΡ ΠΊΠΎΠΌΠΏΠ°Π½ΠΈΠ΅ΠΉ Ford Π΅ΡΠ΅ Π² 1908 Π³.
Β Β ΠΠ·Π²Π΅ΡΡΠ½ΠΎ ΠΌΠ½ΠΎΠΆΠ΅ΡΡΠ²ΠΎ ΡΠΏΠΎΡΠΎΠ±ΠΎΠ² ΠΈ ΠΏΡΠΈΠ΅ΠΌΠΎΠ² ΠΏΡΠ΅Π΄ΡΠΏΡΠ΅ΠΆΠ΄Π΅Π½ΠΈΡ ΠΎΡΠΈΠ±ΠΎΠΊ, Π½Π°ΡΠΈΠ½Π°Ρ Ρ ΠΏΡΠΎΡΡΡΡ ΠΏΠ΅ΡΠ΅Π΄Π΅Π»ΠΎΠΊ ΠΈ ΠΈΠ·ΠΌΠ΅Π½Π΅Π½ΠΈΠΉ, Π²Π½ΠΎΡΠΈΠΌΡΡ Π² ΠΎΠ±ΠΎΡΡΠ΄ΠΎΠ²Π°Π½ΠΈΠ΅ ΠΈ ΠΏΡΠΎΡΠ΅ΡΡΡ ΠΈΠ·Π³ΠΎΡΠΎΠ²Π»Π΅Π½ΠΈΡ ΠΏΡΠΎΠ΄ΡΠΊΡΠΈΠΈ, ΠΈ Π·Π°ΠΊΠ°Π½ΡΠΈΠ²Π°Ρ ΡΠ΅ΡΡΠ΅Π·Π½ΠΎΠΉ ΠΌΠΎΠ΄Π΅ΡΠ½ΠΈΠ·Π°ΡΠΈΠ΅ΠΉ ΠΊΠΎΠ½ΡΡΡΡΠΊΡΠΈΠΈ ΠΈΠ·Π΄Π΅Π»ΠΈΠΉ. ΠΠ°ΠΏΡΠΈΠΌΠ΅Ρ, Π½Π°ΠΏΠΈΡΠ°Π½ΠΈΠ΅ ΠΈΠ½ΡΡΡΡΠΊΡΠΈΠΉ Π΄Π»Ρ ΠΈΡΠΏΠΎΠ»Π½ΠΈΡΠ΅Π»Π΅ΠΉ, ΠΊ ΠΊΠΎΡΠΎΡΡΠΌ ΠΎΠ½ΠΈ ΡΠΌΠΎΠ³ΡΡ ΠΎΠ±ΡΠ°ΡΠ°ΡΡΡΡ Π² Π±ΡΠ΄ΡΡΠ΅ΠΌ; ΠΏΡΠ΅Π΄ΡΠΏΡΠ΅Π΄ΠΈΡΠ΅Π»ΡΠ½ΡΠ΅ Π½Π°Π΄ΠΏΠΈΡΠΈ ΠΈ ΠΏΡΠ΅Π΄ΡΠΏΡΠ΅ΠΆΠ΄Π°ΡΡΠΈΠ΅ ΡΠΈΠ³Π½Π°Π»Ρ; ΠΏΠΎΠ²ΡΠΎΡΠ΅Π½ΠΈΠ΅ ΠΏΠΎΠ΄ΡΠΈΠ½Π΅Π½Π½ΡΠΌΠΈ ΠΏΠΎΠ»ΡΡΠ΅Π½Π½ΡΡ Π·Π°Π΄Π°Π½ΠΈΠΉ Π΄Π»Ρ ΠΎΠ±Π΅ΡΠΏΠ΅ΡΠ΅Π½ΠΈΡ ΠΈΡ ΠΏΡΠ°Π²ΠΈΠ»ΡΠ½ΠΎΠ³ΠΎ ΠΏΠΎΠ½ΠΈΠΌΠ°Π½ΠΈΡ ΠΈ Ρ. Π΄.
Β Β ΠΡΠΈΠΌΠ΅Ρ ΠΈΡΠΏΠΎΠ»ΡΠ·ΠΎΠ²Π°Π½ΠΈΡ ΠΏΡΠΎΡΡΠΎΠ³ΠΎ ΠΏΡΠΈΠ΅ΠΌΠ° Π·Π°ΡΠΈΡΡ ΠΎΡ ΠΎΡΠΈΠ±ΠΎΠΊ.
Β Β Β Β Β Β Β Β Β Β Π ΡΠ΅Ρ Π΅, Π½Π΅ΡΠΌΠΎΡΡΡ Π½Π° Π²ΡΡ ΡΡΠ°ΡΠΈΡΡΠΈΠΊΡ, ΠΌΠ°ΡΠΊΠΈΡΠΎΠ²ΠΊΡ ΠΈ ΠΊΠΎΠ½ΡΡΠΎΠ»Ρ, ΠΏΠΎΡΡΠΎΡΠ½Π½ΠΎ ΠΏΠΎΠ²ΡΠΎΡΡΡΡΡΡ Π΄Π²Π΅ ΠΎΠ΄ΠΈΠ½Π°ΠΊΠΎΠ²ΡΠ΅ ΠΎΡΠΈΠ±ΠΊΠΈ: Π΄Π΅ΡΠ°Π»Ρ Π ΠΏΡΠΈ ΠΌΠΎΠ½ΡΠ°ΠΆΠ΅ Π±Π»ΠΎΠΊΠ° ΡΠ°ΡΡΠΎ ΠΎΠΊΠ°Π·ΡΠ²Π°Π΅ΡΡΡ Π² ΠΎΠΊΠΎΡΠΊΠ΅ 2, ΠΈ Π½Π°ΠΎΠ±ΠΎΡΠΎΡ, Π΄Π΅ΡΠ°Π»Ρ Π ΠΎΠΊΠ°Π·ΡΠ²Π°Π΅ΡΡΡ Π² ΠΎΠΊΠΎΡΠΊΠ΅ 1.
Β Β ΠΡΠΎΡΡΠΎΠΉ ΠΏΡΠΈΠ΅ΠΌ Π·Π°ΡΠΈΡΡ ΠΎΡ ΠΎΡΠΈΠ±ΠΎΠΊ — ΠΏΠΎΠΊΠ°-ΡΠΊΡ — ΠΏΠΎΠ·Π²ΠΎΠ»ΡΠ΅Ρ Π½Π°ΠΉΡΠΈ ΡΠ΅ΡΠ΅Π½ΠΈΠ΅, Π΄Π΅Π»Π°ΡΡΠ΅Π΅ Π½Π΅Π²ΠΎΠ·ΠΌΠΎΠΆΠ½ΠΎΠΉ Π»ΡΠ±ΡΡ ΠΎΡΠΈΠ±ΠΊΡ. ΠΠΎΠ½ΡΠΈΠ³ΡΡΠ°ΡΠΈΠΈ ΠΎΠΊΠΎΡΠΊΠ° 1 ΠΈ ΠΌΠΎΠ½ΡΠ°ΠΆΠ½ΠΎΠ³ΠΎ ΡΠ»Π΅ΠΌΠ΅Π½ΡΠ° Π ΡΠ°ΠΊ ΠΈΠ·ΠΌΠ΅Π½Π΅Π½Ρ, ΡΡΠΎ Π·Π°ΠΌΠ΅Π½Π° ΠΏΡΠΈ ΠΌΠΎΠ½ΡΠ°ΠΆΠ΅ Π΄Π°ΠΆΠ΅ ΡΠ΅ΠΎΡΠ΅ΡΠΈΡΠ΅ΡΠΊΠΈ Π½Π΅Π²ΠΎΠ·ΠΌΠΎΠΆΠ½Π°.
Β Β ΠΡΠ°Π²ΠΈΠ»Π° ΠΏΡΠΈΠΌΠ΅Π½Π΅Π½ΠΈΡ ΠΏΡΠΈΠ΅ΠΌΠΎΠ² Π·Π°ΡΠΈΡΡ ΠΎΡ ΠΎΡΠΈΠ±ΠΎΠΊ.
ΠΠ°ΠΊ ΠΌΠΎΠΆΠ½ΠΎ Π±Π»ΠΈΠΆΠ΅ ΠΏΠΎΠ΄ΠΎΠΉΡΠΈ ΠΊ ΠΈΡΡΠΎΡΠ½ΠΈΠΊΡ ΠΏΡΠΎΠ±Π»Π΅ΠΌΡ, ΡΡΠ΄Π°, Π³Π΄Π΅ ΠΏΡΠΎΠ±Π»Π΅ΠΌΠ° Π΄Π΅ΠΉΡΡΠ²ΠΈΡΠ΅Π»ΡΠ½ΠΎ Π²ΠΎΠ·Π½ΠΈΠΊΠ»Π° ΠΈ Π³Π΄Π΅ ΠΎΠ½Π° ΡΠ½ΠΎΠ²Π° ΠΌΠΎΠΆΠ΅Ρ ΠΏΠΎΡΠ²ΠΈΡΡΡΡ.
ΠΠ²Π΅ΡΡΠΈ ΡΡΠ°Π·Ρ Π²ΡΠ΅ Π½Π΅ΠΎΠ±Ρ ΠΎΠ΄ΠΈΠΌΡΠ΅ Π²ΠΈΠ΄Ρ ΠΊΠΎΠ½ΡΡΠΎΠ»Ρ ΠΈ ΠΌΠ΅ΡΡ ΠΏΡΠ΅Π΄ΠΎΡΠ²ΡΠ°ΡΠ΅Π½ΠΈΡ ΠΏΠΎΠ²ΡΠΎΡΠ½ΠΎΠ³ΠΎ ΠΏΠΎΡΠ²Π»Π΅Π½ΠΈΡ ΠΏΡΠΎΠ±Π»Π΅ΠΌΡ.
ΠΡΠΈ ΡΠ°Π·ΡΠ°Π±ΠΎΡΠΊΠ΅ ΠΈ ΠΊΠΎΠ½ΡΡΡΡΠΈΡΠΎΠ²Π°Π½ΠΈΠΈ ΠΈΡΠΏΠΎΠ»ΡΠ·ΠΎΠ²Π°ΡΡ ΡΠ»ΠΎΠΆΠ½ΡΠ΅ ΠΌΠ΅ΡΠΎΠ΄Ρ ΠΈ ΡΠ΅Ρ Π½ΠΈΠΊΠΈ ΡΡΡΡΠ°Π½Π΅Π½ΠΈΡ ΠΏΡΠΎΠ±Π»Π΅ΠΌΡ, Π° Π² ΠΏΡΠΎΠΈΠ·Π²ΠΎΠ΄ΡΡΠ²Π΅ ΠΏΡΠΈΠΌΠ΅Π½ΡΡΡ ΠΏΡΠΎΡΡΡΠ΅ ΠΈ Π±ΡΡΡΡΡΠ΅ ΡΠ΅ΡΠ΅Π½ΠΈΡ.
Π£Π»ΡΡΡΠ΅Π½ΠΈΡ Π² ΠΏΡΠΎΠΈΠ·Π²ΠΎΠ΄ΡΡΠ²Π΅ ΠΏΡΠΎΠ²ΠΎΠ΄ΠΈΡΡ Π±ΡΡΡΡΠΎ, Π±Π΅Π· ΡΠ»ΠΎΠΆΠ½ΡΡ Π°Π½Π°Π»ΠΈΠ·ΠΎΠ² ΠΈ ΡΠ°ΠΊΠΈΠΌ ΠΎΠ±ΡΠ°Π·ΠΎΠΌ, ΡΡΠΎΠ±Ρ Π²ΡΠ΅ Π»ΡΠ΄ΠΈ Π±ΡΠ»ΠΈ Π²ΠΊΠ»ΡΡΠ΅Π½Ρ Π² ΡΠ΅ΡΠ΅Π½ΠΈΠ΅ ΠΎΠ±ΡΠΈΡ ΠΏΡΠΎΠ±Π»Π΅ΠΌ ΠΈ ΡΡΡΡΠ°Π½Π΅Π½ΠΈΠ΅ Π½Π΅ΡΠΎΠΎΡΠ²Π΅ΡΡΡΠ²ΠΈΠΉ.
Β Β ΠΠΎΠΏΠΎΠ»Π½ΠΈΡΠ΅Π»ΡΠ½Π°Ρ ΠΈΠ½ΡΠΎΡΠΌΠ°ΡΠΈΡ:
ΠΠΎΠ»ΡΡΠΈΠ½ΡΡΠ²ΠΎ ΡΡΡΡΠΎΠΉΡΡΠ² ΠΏΠΎ Π·Π°ΡΠΈΡΠ΅ ΠΎΡ ΠΎΡΠΈΠ±ΠΎΠΊ ΡΠ²Π»ΡΡΡΡΡ ΠΏΡΠΎΡΡΡΠΌΠΈ ΠΈ Π½Π΅Π΄ΠΎΡΠΎΠ³ΠΈΠΌΠΈ.
ΠΡΠΎΠ³ΡΠ°ΠΌΠΌΠ° ΠΏΠΎ ΡΠ»ΡΡΡΠ΅Π½ΠΈΡ ΡΠΎΠ»ΡΠΊΠΎ ΡΠΎΠ³Π΄Π° ΠΌΠΎΠΆΠ΅Ρ Π±ΡΡΡ ΡΡΠΏΠ΅ΡΠ½ΠΎΠΉ, ΠΊΠΎΠ³Π΄Π° Π²ΡΠ΅ ΡΠΎΡΡΡΠ΄Π½ΠΈΠΊΠΈ — ΠΎΡ ΠΎΠΏΠ΅ΡΠ°ΡΠΎΡΠΎΠ² Π΄ΠΎ ΡΡΠ°ΡΡΠΈΡ ΠΌΠ΅Π½Π΅Π΄ΠΆΠ΅ΡΠΎΠ² — ΠΏΡΠΎΠΉΠ΄ΡΡ ΠΎΠ±ΡΡΠ΅Π½ΠΈΠ΅ ΠΌΠ΅ΡΠΎΠ΄Π°ΠΌ Π·Π°ΡΠΈΡΡ ΠΎΡ ΠΎΡΠΈΠ±ΠΎΠΊ ΠΈ Π±ΡΠ΄ΡΡ Π½Π°ΠΏΡΡΠΌΡΡ ΡΡΠ°ΡΡΠ²ΠΎΠ²Π°ΡΡ Π² ΠΈΡ Π²Π½Π΅Π΄ΡΠ΅Π½ΠΈΠΈ.
ΠΡΠΈΠΌΠ΅Π½Π΅Π½ΠΈΠ΅ ΠΊΠΎΠΌΠ°Π½Π΄Π½ΠΎΠ³ΠΎ ΠΏΠΎΠ΄Ρ ΠΎΠ΄Π° ΠΊ Π²Π½Π΅Π΄ΡΠ΅Π½ΠΈΡ ΡΠΏΠΎΡΠΎΠ±ΠΎΠ² Π·Π°ΡΠΈΡΡ ΠΎΡ ΠΎΡΠΈΠ±ΠΎΠΊ ΠΏΠΎΠ·Π²ΠΎΠ»ΡΠ΅Ρ ΡΡΠΈΡΡΠ²Π°ΡΡ ΠΈΠ½ΡΠ΅ΡΠ΅ΡΡ, ΠΊΠ°ΠΊ ΠΏΡΠΎΠΈΠ·Π²ΠΎΠ΄ΡΡΠ²Π΅Π½Π½ΡΡ ΠΏΠΎΠ΄ΡΠ°Π·Π΄Π΅Π»Π΅Π½ΠΈΠΉ, ΡΠ°ΠΊ ΠΈ ΠΏΠΎΡΡΠ΅Π±ΠΈΡΠ΅Π»Ρ.
Β Β ΠΠΎΡΡΠΎΠΈΠ½ΡΡΠ²Π° ΠΌΠ΅ΡΠΎΠ΄Π°.
ΠΠΎΡΠ»Π΅Π΄ΠΎΠ²Π°ΡΠ΅Π»ΡΠ½ΠΎΠ΅ ΠΏΡΠΈΠΌΠ΅Π½Π΅Π½ΠΈΠ΅ ΡΠ°Π·Π»ΠΈΡΠ½ΡΡ ΡΠΏΠΎΡΠΎΠ±ΠΎΠ² ΠΈ ΠΏΡΠΈΠ΅ΠΌΠΎΠ² ΠΏΡΠ΅Π΄ΡΠΏΡΠ΅ΠΆΠ΄Π΅Π½ΠΈΡ ΠΎΡΠΈΠ±ΠΎΠΊ ΠΏΠΎΠ·Π²ΠΎΠ»ΡΠ΅Ρ Π·Π½Π°ΡΠΈΡΠ΅Π»ΡΠ½ΠΎ ΡΠΎΠΊΡΠ°ΡΠΈΡΡ ΠΈΡ ΡΠΈΡΠ»ΠΎ, ΡΡΠΎ ΡΠΏΠΎΡΠΎΠ±ΡΡΠ²ΡΠ΅Ρ ΡΠ½ΠΈΠΆΠ΅Π½ΠΈΡ Π·Π°ΡΡΠ°Ρ ΠΈ ΠΏΠΎΠ²ΡΡΠ΅Π½ΠΈΡ ΡΠ΄ΠΎΠ²Π»Π΅ΡΠ²ΠΎΡΠ΅Π½Π½ΠΎΡΡΠΈ ΠΏΠΎΡΡΠ΅Π±ΠΈΡΠ΅Π»Π΅ΠΉ.
Β Β ΠΠ΅Π΄ΠΎΡΡΠ°ΡΠΊΠΈ ΠΌΠ΅ΡΠΎΠ΄Π°.
ΠΡΡΡΠ΅ΡΠ°ΡΡΠ΅Π΅ΡΡ ΡΠΎΠΏΡΠΎΡΠΈΠ²Π»Π΅Π½ΠΈΠ΅ ΠΏΡΠΈ ΠΏΡΠΈΠ½ΡΠ΄ΠΈΡΠ΅Π»ΡΠ½ΠΎΠΌ Π²Π½Π΅Π΄ΡΠ΅Π½ΠΈΠΈ Π² Π΄Π΅ΠΉΡΡΠ²ΡΡΡΠ΅Π΅ ΠΏΡΠΎΠΈΠ·Π²ΠΎΠ΄ΡΡΠ²ΠΎ ΡΡΡΡΠΎΠΉΡΡΠ² ΠΏΠΎ Π·Π°ΡΠΈΡΠ΅ ΠΎΡ ΠΎΡΠΈΠ±ΠΎΠΊ ΡΠ°ΡΡΠΎ Ρ Π²ΠΎΠ΄ΠΈΡ Π½Π° Π½Π΅Ρ ΡΡΠΈΠ»ΠΈΡ ΠΏΠΎ ΡΠ»ΡΡΡΠ΅Π½ΠΈΡ ΠΏΡΠΎΡΠ΅ΡΡΠ° .
Β Β ΠΠΆΠΈΠ΄Π°Π΅ΠΌΡΠΉ ΡΠ΅Π·ΡΠ»ΡΡΠ°Ρ.
ΠΡΡΠΎΠΊΠ°Ρ ΠΏΠΎΡΡΠ΅Π±ΠΈΡΠ΅Π»ΡΠ½Π°Ρ ΡΡΠΎΠΈΠΌΠΎΡΡΡ ΠΏΡΠΎΠ΄ΡΠΊΡΠΈΠΈ.
Β
Β Β Β Β ΠΡΡΡΡΠ°Ρ ΠΏΠ΅ΡΠ΅Π½Π°Π»Π°Π΄ΠΊΠ°.
Β Β ΠΡΡΡΡΠ°Ρ ΠΏΠ΅ΡΠ΅Π½Π°Π»Π°Π΄ΠΊΠ° (Single-Minute Exchange of DiesΒ (SMED)Β β Π±ΡΡΡΡΠ°Ρ ΡΠΌΠ΅Π½Π° ΠΏΡΠ΅ΡΡ-ΡΠΎΡΠΌ)Β β ΠΏΠ΅ΡΠ΅Π½Π°Π»Π°Π΄ΠΊΠ° ΠΈΠ»ΠΈ ΠΏΠ΅ΡΠ΅ΠΎΡΠ½Π°ΡΡΠΊΠ° ΠΎΠ±ΠΎΡΡΠ΄ΠΎΠ²Π°Π½ΠΈΡ ΠΌΠ΅Π½Π΅Π΅ ΡΠ΅ΠΌ Π·Π° 10 ΠΌΠΈΠ½ΡΡ. ΠΡΠ΅Π΄ΡΡΠ°Π²Π»ΡΠ΅Ρ ΡΠΎΠ±ΠΎΠΉ Π½Π°Π±ΠΎΡ ΡΠ΅ΠΎΡΠ΅ΡΠΈΡΠ΅ΡΠΊΠΈΡ ΠΈ ΠΏΡΠ°ΠΊΡΠΈΡΠ΅ΡΠΊΠΈΡ ΠΌΠ΅ΡΠΎΠ΄ΠΎΠ², ΠΊΠΎΡΠΎΡΡΠ΅ ΠΏΠΎΠ·Π²ΠΎΠ»ΡΡΡ ΡΠΎΠΊΡΠ°ΡΠΈΡΡ Π²ΡΠ΅ΠΌΡ ΠΎΠΏΠ΅ΡΠ°ΡΠΈΠΉ Π½Π°Π»Π°Π΄ΠΊΠΈ ΠΈ ΠΏΠ΅ΡΠ΅Π½Π°Π»Π°Π΄ΠΊΠΈ ΠΎΠ±ΠΎΡΡΠ΄ΠΎΠ²Π°Π½ΠΈΡ. ΠΠ·Π½Π°ΡΠ°Π»ΡΠ½ΠΎ ΡΡΠ° ΡΠΈΡΡΠ΅ΠΌΠ° Π±ΡΠ»Π° ΡΠ°Π·ΡΠ°Π±ΠΎΡΠ°Π½Π° Π΄Π»Ρ ΡΠΎΠ³ΠΎ, ΡΡΠΎΠ±Ρ ΠΎΠΏΡΠΈΠΌΠΈΠ·ΠΈΡΠΎΠ²Π°ΡΡ ΠΎΠΏΠ΅ΡΠ°ΡΠΈΠΈ Π·Π°ΠΌΠ΅Π½Ρ ΡΡΠ°ΠΌΠΏΠΎΠ² ΠΈ ΠΏΠ΅ΡΠ΅Π½Π°Π»Π°Π΄ΠΊΠΈ ΡΠΎΠΎΡΠ²Π΅ΡΡΡΠ²ΡΡΡΠ΅Π³ΠΎ ΠΎΠ±ΠΎΡΡΠ΄ΠΎΠ²Π°Π½ΠΈΡ, ΠΎΠ΄Π½Π°ΠΊΠΎ ΠΏΡΠΈΠ½ΡΠΈΠΏΡ Β«Π±ΡΡΡΡΠΎΠΉ ΠΏΠ΅ΡΠ΅Π½Π°Π»Π°Π΄ΠΊΠΈΒ» ΠΌΠΎΠΆΠ½ΠΎ ΠΏΡΠΈΠΌΠ΅Π½ΡΡΡ ΠΊΠΎ Π²ΡΠ΅ΠΌ ΡΠΈΠΏΠ°ΠΌ ΠΏΡΠΎΡΠ΅ΡΡΠΎΠ².
Β Β Π‘ΠΈΠ³Π΅ΠΎ Π‘ΠΈΠ½Π³ΠΎ ΠΏΠΎΠ½Π°Π΄ΠΎΠ±ΠΈΠ»ΠΎΡΡ Π΄Π΅Π²ΡΡΠ½Π°Π΄ΡΠ°ΡΡ Π»Π΅Ρ, ΡΡΠΎΠ±Ρ ΡΠ°Π·ΡΠ°Π±ΠΎΡΠ°ΡΡ ΡΠΈΡΡΠ΅ΠΌΡ SMED. ΠΠ·ΡΡΠ°Ρ ΠΎΠΏΠ΅ΡΠ°ΡΠΈΠΈ ΠΏΠ΅ΡΠ΅Π½Π°Π»Π°Π΄ΠΊΠΈ ΠΎΠ±ΠΎΡΡΠ΄ΠΎΠ²Π°Π½ΠΈΡ Π½Π° ΠΌΠ½ΠΎΠ³ΠΈΡ Π·Π°Π²ΠΎΠ΄Π°Ρ , ΠΎΠ½ ΠΎΠ±Π½Π°ΡΡΠΆΠΈΠ» Π΄Π²Π΅ Π²Π°ΠΆΠ½ΡΠ΅ Π²Π΅ΡΠΈ, ΠΊΠΎΡΠΎΡΡΠ΅ ΠΈ Π»Π΅Π³Π»ΠΈ Π² ΠΎΡΠ½ΠΎΠ²Ρ SMED:
- ΠΠΏΠ΅ΡΠ°ΡΠΈΠΈ ΠΏΠ΅ΡΠ΅Π½Π°Π»Π°Π΄ΠΊΠΈ ΠΌΠΎΠΆΠ½ΠΎ ΡΠ°Π·Π΄Π΅Π»ΠΈΡΡ Π½Π° Π΄Π²Π΅ ΠΊΠ°ΡΠ΅Π³ΠΎΡΠΈΠΈ:
- ΠΠ½ΡΡΡΠ΅Π½Π½ΠΈΠ΅ Π΄Π΅ΠΉΡΡΠ²ΠΈΡ ΠΏΠΎ ΠΏΠ΅ΡΠ΅Π½Π°Π»Π°Π΄ΠΊΠ΅, ΡΠΎ Π΅ΡΡΡ ΠΎΠΏΠ΅ΡΠ°ΡΠΈΠΈ, ΠΊΠΎΡΠΎΡΡΠ΅ Π²ΡΠΏΠΎΠ»Π½ΡΡΡΡΡ ΠΏΠΎΡΠ»Π΅ ΠΎΡΡΠ°Π½ΠΎΠ²ΠΊΠΈ ΠΎΠ±ΠΎΡΡΠ΄ΠΎΠ²Π°Π½ΠΈΡ. ΠΠ°ΠΏΡΠΈΠΌΠ΅Ρ, ΠΏΡΠ΅ΡΡ-ΡΠΎΡΠΌΡ ΠΌΠΎΠΆΠ½ΠΎ Π·Π°ΠΌΠ΅Π½ΠΈΡΡ ΡΠΎΠ»ΡΠΊΠΎ ΠΏΡΠΈ ΠΎΡΡΠ°Π½ΠΎΠ²Π»Π΅Π½Π½ΠΎΠΌ ΠΏΡΠ΅ΡΡΠ΅.
- ΠΠ½Π΅ΡΠ½ΠΈΠ΅ Π΄Π΅ΠΉΡΡΠ²ΠΈΡ ΠΏΠΎ ΠΏΠ΅ΡΠ΅Π½Π°Π»Π°Π΄ΠΊΠ΅, ΡΠΎ Π΅ΡΡΡ ΠΎΠΏΠ΅ΡΠ°ΡΠΈΠΈ, ΠΊΠΎΡΠΎΡΡΠ΅ ΠΌΠΎΠ³ΡΡ Π±ΡΡΡ Π²ΡΠΏΠΎΠ»Π½Π΅Π½Ρ Π²ΠΎ Π²ΡΠ΅ΠΌΡ ΡΠ°Π±ΠΎΡΡ ΠΎΠ±ΠΎΡΡΠ΄ΠΎΠ²Π°Π½ΠΈΡ. ΠΠ°ΠΏΡΠΈΠΌΠ΅Ρ, Π±ΠΎΠ»ΡΡ ΠΊΡΠ΅ΠΏΠ»Π΅Π½ΠΈΡ ΠΏΡΠ΅ΡΡ-ΡΠΎΡΠΌΡ ΠΌΠΎΠΆΠ½ΠΎ ΠΏΠΎΠ΄ΠΎΠ±ΡΠ°ΡΡ ΠΈ ΠΎΡΡΠΎΡΡΠΈΡΠΎΠ²Π°ΡΡ ΠΈ ΠΏΡΠΈ ΡΠ°Π±ΠΎΡΠ°ΡΡΠ΅ΠΌ ΠΏΡΠ΅ΡΡΠ΅.
- ΠΡΠ΅ΠΎΠ±ΡΠ°Π·ΠΎΠ²Π°Π½ΠΈΠ΅ ΠΊΠ°ΠΊ ΠΌΠΎΠΆΠ½ΠΎ Π±ΠΎΠ»ΡΡΠ΅Π³ΠΎ ΡΠΈΡΠ»Π° Π²Π½ΡΡΡΠ΅Π½Π½ΠΈΡ ΠΎΠΏΠ΅ΡΠ°ΡΠΈΠΉ ΠΏΠ΅ΡΠ΅Π½Π°Π»Π°Π΄ΠΊΠΈ Π²ΠΎ Π²Π½Π΅ΡΠ½ΠΈΠ΅ ΠΏΠΎΠ·Π²ΠΎΠ»ΡΠ΅Ρ Π² Π½Π΅ΡΠΊΠΎΠ»ΡΠΊΠΎ ΡΠ°Π· ΡΠΎΠΊΡΠ°ΡΠΈΡΡ Π²ΡΠ΅ΠΌΡ ΠΏΠ΅ΡΠ΅Π½Π°Π»Π°Π΄ΠΊΠΈ ΠΎΠ±ΠΎΡΡΠ΄ΠΎΠ²Π°Π½ΠΈΡ.
ΠΠ΅ΡΠ΅Π½Π°Π»Π°Π΄ΠΊΠ° Π² ΠΎΠ΄Π½ΠΎ ΠΊΠ°ΡΠ°Π½ΠΈΠ΅ (One-touch setup ΠΈΠ»ΠΈ One-Touch Exchange of Die)Β β Π²Π°ΡΠΈΠ°Π½Ρ SMED, Π³Π΄Π΅ Π²ΡΠ΅ΠΌΡ ΠΏΠ΅ΡΠ΅Π½Π°Π»Π°Π΄ΠΊΠΈ ΠΈΠ·ΠΌΠ΅ΡΡΠ΅ΡΡΡ Π΅Π΄ΠΈΠ½ΠΈΡΠ°ΠΌΠΈ ΠΌΠΈΠ½ΡΡ (Π½Π΅ Π±ΠΎΠ»ΡΡΠ΅ 9).
Β
ΠΡΠ»ΠΈ Π²Π°ΠΌ ΠΈΠ·Π²Π΅ΡΡΠ½Ρ Π΄ΡΡΠ³ΠΈΠ΅ ΠΈΠ½ΡΡΡΡΠΌΠ΅Π½ΡΡ Π±Π΅ΡΠ΅ΠΆΠ»ΠΈΠ²ΠΎΠ³ΠΎ ΠΏΡΠΎΠΈΠ·Π²ΠΎΠ΄ΡΡΠ²Π°, ΠΏΠΎΠΆΠ°Π»ΡΠΉΡΡΠ°, ΡΠΎΠΎΠ±ΡΠΈΡΠ΅ ΠΌΠ½Π΅ ΡΠ΅ΡΠ΅Π· ΡΠΎΡΠΌΡ ΠΎΠ±ΡΠ°ΡΠ½ΠΎΠΉ ΡΠ²ΡΠ·ΠΈ.
producm.ru