Встроенное качество в бережливом производстве
Определение и необходимость встроенного качества
Определение 1
Встроенное качество — это так называемая система технических, организационных и логистических мер, которые направлены на дефицит некачественной с взгляда покупателя продукции.
Встроенное качество делает акцент не на контроль вырабатываемой продукции методом пост-фактум, а напротив на устранение происхождения дефектов. При действии концепции встроенного качества осуществляется последовательный анализ несоответствий, выявление их причин, обработка корректирующих действий и контроль последствий.
Определение 2
Встроенное качество – это все события, нацеленные на недопущение выпуска некачественной продукции.
Понимание потребности встроенного качества часто приходит к компаниям совместно с пониманием того, что число жалоб от недовольных клиентов растет с ростом числа сотрудников; что с увеличением усердности осмотра затраты на предотвращение брака и «регулирование» споров с клиентами не уменьшаются.
Из-за этого растет прессинг со стороны руководства и образуется ситуация (сожалению, неоднократно типичная) когда коллеги и начальство «действуют по разные стороны». Ясно, то, что в таких условиях развитие происходит весьма неторопливыми темпами, а в пучину разногласия постепенно втянутся ранее неизвестные подуровни управления — за рабочими последуют бригадиры, далее и мастера, и, что самое важное и плохое, новые сотрудники тоже начнут учиться неприемлемым техникам работы.
Готовые работы на аналогичную тему
Для удачного внедрения концепции встроенного качества нужно, чтобы операторы на рабочих местах осмысливали, то, что при возникновении дефекта, его в каждом случае необходимо будет устранять, но, тем не менее, есть разница в том, на каком этапе будет определен и устранен брак.
Принципы бережливого производства
Традиционно, к основным принципам бережливого производства относят:
- Выявление потоков создания ценности для конкретного продукта;
- Снабжение бесперебойного потока изготовления ценности продукта;
- Предоставление потребителю доступа к продуктам;
- Стремление к усовершенствованию.
Помимо данных принципов, выделяют следующие:
- Получение превосходного качества;
- Гибкость;
- Установление длительных отношений с потребителями.
Это достигается при помощи разделения рисков, затрат, а также информации. Основной бережливого производства является работа по устранению потерь.
Замечание 1
Потери включают в себя определенное действие, которое направлено на потребление ресурсов. Важно отметить, что потери не создают ни какой ценности для потребителя.
Основными задачами бережливого производства являются:
- Снижение затрат, к которым относятся и трудовые;
- Уменьшение сроков создания продукции;
- Уменьшение производственных и складских площадей;
- Обеспечение поставки продукции заказчику;
- Наибольшее качество при конкретной стоимости или наивысшая цена при конкретном качестве.
Принцип встроенного качества — Leanbase
Данный принцип представляет собой комплекс различных мероприятий
(по стандартизации работ, обеспечению обратной связи, проведению анализа и т.д.) для перемещения места обнаружения дефекта как можно ближе к месту его возникновения.Для начала необходимо понять различия таких понятий как место выявления дефекта (там, где его обнаружили) и место возникновения дефекта (там, где в процессе произошла ошибка, в результате которой был заложен дефект). Чем дальше по ходу технологической цепочки находятся эти места и чем дальше ушёл дефект от места возникновения, тем дороже он стоит (тем больше суммарные затраты). Понятно, что дефект, обнаруженный самим же работником, будет стоить в разы дешевле, чем дефект, прошедший дальше по потоку несколько операций и обнаруженный позднее. Дороже всего стоит дефект, обнаруженный Заказчиком. В таком случае его стоимость складывается не только из затрат на инструмент, материалы, рабочую силу, электроэнергию и т.п., это еще и потеря потенциальных или существующих клиентов (Заказчиков). Возрастание стоимости дефекта наглядно можно представить в виде рисунка (см. ниже).
Разумеется, лучший вариант – это дефект, остановленный на стадии проектирования конструкторской и технологической документации, однако на практике приходится работать с тем, что есть. Традиционным решением при выявлении дефекта является введение дополнительного контроля на различных этапах изготовления продукта. Как известно, контроль – потеря по определению, несмотря на то, что иногда он бывает необходим в качестве контрмеры, предотвращающей распространение бедствия. Но часто после решения проблемы контроль остаётся «на всякий случай». Хотя это уже тема отдельного разговора. Как с этим обстоят дела в вашей организации?
Говоря о контроле, принципиально можно выделить три вида:
- Приёмка контролёром, как правило, осуществляется между различными процессами (стадиями изготовления продукта, операциями и т.п.). Отбракованный продукт не попадает в следующий процесс.
- Проверка на следующей стадии, т.е. проверка внутри следующего процесса, когда продукт попал в следующий процесс.
- Самоконтроль, т.е. осуществление проверки в самом процессе, когда бракованный продукт не покидает его.
Принцип встраивания качества предполагает обеспечение возможностей наиболее раннего обнаружения дефекта, если отсутствует возможность вовсе его исключить. Ближе к этой идее третий вариант: самоконтроль. В традиционном понимании, самоконтроль – доплата работникам за определённое количество проверенных изделий, изготовленных ими. Но здесь существует несколько идеологических противоречий, препятствующих внедрению встроенного качества в традиционном мышлении.
- Во-первых, необходимо обратить внимание на заинтересованность самих работников. На что они мотивированы? Чтобы больше продукции проверить, чтобы больше дефектов выявить, чтобы выявлялось меньше дефектов или чтобы общий уровень брака по определённым показателям постоянно снижался? Как с этим обстоят дела у вас? Про необходимость определённых показателей, так или иначе характеризующих качество, мы уже говорили. Они существенно различаются в зависимости от специфики рассматриваемых процессов, поэтому мы не будем на них останавливаться. Подумайте, как объяснить людям необходимость самостоятельно контролировать и отвечать за качество своей работы. Визуализируйте основные показатели по качеству и проведите параллель между их динамикой и динамикой изменения заработанной платы работников.
Ещё раз проанализируйте, за что работники получают деньги.
- Во-вторых, необходимо обеспечить работников чёткими критериями, характеризующими годную продукцию и брак. На практике часто встречаются ситуации проявления нестабильности по выходу годных изделий, когда количество отбракованных единиц существенно различается в зависимости от работника, проводящего контроль. Так называемый субъективный фактор. Это происходит именно из-за отсутствия чётких параметров, отличающих годные изделия от бракованных. Сталкивались ли вы с такой проблемой? Как обстоят дела с этим в вашей организации? Данная проблема решается чётким обозначением параметров. В первую очередь должны быть чётко определены требования Заказчика, предъявляемые к тому или иному продукту. Наиболее распространённые решения — размещение визуализации или макетов продукта, показывающих границы между годным и бракованным изделием, обучение работников согласно этим требованиям.
- В-третьих, внедрение встроенного качества, как правило, основывается на чётких рабочих стандартах и внедряется вместе с методом стандартизованной работы.
Основная задача заключается в применении наилучшей последовательности выполнения работ в определённой операции, гарантирующей качество их выполнения. Определённые параметры, обозначающие границы между годным и бракованным изделиям в таком случае прописываются в стандартах выполнения операций работниками.
- В-четвёртых, необходимо сделать так, чтобы любое несоответствие было легко увидеть. Ни один дефект не должен остаться незамеченным. Это могут быть различные сигнальные системы, визуализация дефектов, определённое место для промежуточного хранения дефектов и т.п. Необходимо обеспечить быструю обратную связь из места обнаружения дефекта в место его возникновения. В таких случаях наиболее распространёнными являются системы андон, сигнализирующие об обнаружении дефекта. Быстрая обратная связь необходима для своевременной реакции, устранения причин, вызвавших появление дефекта и предотвращения дальнейшего их появления. Разумеется, на обратную связь должна быть соответствующая реакция: выяснение и устранение причин, исправление дефектов и т.
д.
- В-пятых, обязательное применение принципов «3НЕ» и «line stop». Работники принципиально не должны производить брак, при его выявлении они должны останавливаться, подавать сигнал и ожидать помощи.
- Последний момент, о котором необходимо сказать, но не последний в принципе, на котором следует акцентировать внимание – это систематическое проведение анализа. Для того чтобы понимать причины возникновения брака, вам придётся это делать. Возможно, брак выдаёт только один процесс, или несколько необученных человек, возможно, технология определённой операции не позволяет достичь лучшего качества. Анализ позволяет сузить фокус внимания для решения определённых проблем, сконцентрироваться на самом главном.
Для полного изучения принципов и подходов к встраиванию качества, рекомендуем прочитать книгу «Встроенное качество«.
Статья подготовлена на основании материала из книги «Бережливое производство для руководителей. Продвинутый уровень» , 2014 г. Ф.А. Семёнычев. Специально для LeanBase.ru
Вконтакте
Одноклассники
Google+
Встроенное качество. Сущность и методы системы встроенного качества. Метод 6σ
1. Встроенное качество. Сущность системы встроенного качества. Методы системы встроенного качества. Метод 6σ
Галямов Радмир Ахатович2. Встроенное качество
5S –Сортировка, Соблюдение порядка, Содержание в чистоте,
Стандартизация, Совершенствование
TPM –
Всеобщий уход за оборудованием
SMED –
Быстрая переналадка
Канбан –
Вытягивающее планирование на рабочем месте
Брак
– некачественное изготовление;
– недодел, передел;
– некомплектность.
3. Автономный контроль на рабочем месте – гарантия качества продукции
Контролером качества (КК) и одновременногарантией качества (ГК) является
разработка, проектирование, производство
и обслуживание такой продукции, которая
удовлетворяет требованиям потребителя
при минимальных издержках
4.

Основная задача инспекции: проверки независимыми
контролерами при помощи метода статистической выборки
II
Основная задача автономного контроля в процессе
производства: проверка всех заготовок на рабочем месте
Автономизация
(автономный контроль качества на рабочем месте)
Совершенствование системы принятия решения об остановке производственных
линий в случае возникновения неполадок
Решение только на
основе опыта и
визуального
наблюдения без
привлечения средств
контроля
Решение с помощью
механических
средств
Решение с помощью
простых систем
Средства визуального контроля
III
Основная задача служб контроля качества в подразделениях:
функциональное управление производством
Контроль качества
первоначально осуществлялся
независимыми контролерами
при помощи метода
статистической выборки. Но
затем стал применяться метод
автономного контроля всех
заготовок на рабочем месте,
состоящий в автономном
контроле дефектов
непосредственно в
производственном процессе
самими его участниками.
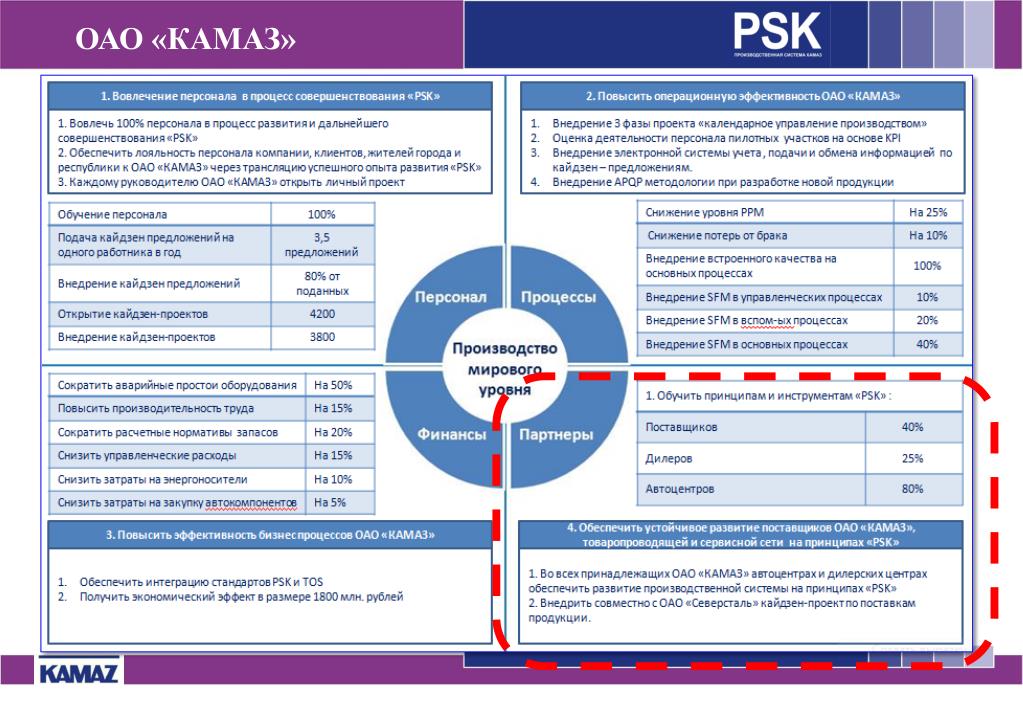
Теперь контроль качества стал
на «Тойоте» всеобъемлющим и
охватывает не только
производственную сферу, но и
все звенья функционального
управления
5. Условие производства 100%-ной качественной продукции и допустимые отклонения
Индекс стабильноститехнологического
процесса Ср=а/6σ;
Степень отклонения
β=в/(а/2)
Условия, при которых не
выпускаются
бракованные детали:
в+3σ
Или: Ср(1-β)>1
Toyota — Ср≥1,33
Уровень сигмы
6
5
4
3
2
1
Число дефектов на миллион
возможностей
3,4
233,0
6210,0
66807,0
308537,0
690000,0
Выход годных %
99,9997
99,977
99,379
93,32
69,2
31
Значения уровня сигм характеризуют воспроизводимость основного
бизнес-процесса предприятия, измеряемую числом дефектов на миллион
возможностей.
Воспроизводимость – статистический показатель, характеризующий
стабильность работы процесса.

процесса, тем меньше разброс показателя, характеризующего процесс.
7. Операция обрубки прутка
Распределение длин в начальный моментНГД – нижняя граница допуска; ВГД – верхняя граница допуска
8. Операция обрубки прутка
Распределение после переделки9. Операция обрубки прутка
Распределение после улучшений10. Схема достижения цели при автономном контроле качества на рабочем месте
Автономизация подразумевает вравной степени достижение
таких целей, как
снижение издержек на
производство продукции,
быстрая приспосабливаемость к
изменению спроса, а также
возрастание роли человека в
производственном процессе
Гибкое
производство
Снижение
издержек
производства
Реализация
процесса «точно
вовремя»
Сокращение
количества
рабочих
Гарантия
качества
Активизация
человеческого
фактора
Совершенствование рабочего процесса
Поставляется только
необходимое количество
деталей
Рабочий может обслуживать
несколько механизмов за
один временной цикл
Исследование основных
причин брака или
отклонений
Поставляются только
качественные изделия
Ручные опреции отделены
от механических
На табло включатся
сигнальные лампы
Механизм автоматически отключается,
если произведено необходимое
количество деталей или закончена
операция
Механизм автоматически отключается,
если появляется брак
Автономизация.

отклонение от стандарта
11. Автономный контроль качества
Снижение производственных издержек врезультате сокращения рабочей силы
Приспосабливаемость к изменениям
спроса
Возрастание роли человеческого фактора
12. Снижение производственных издержек в результате сокращения рабочей силы
Оборудование налажено таким образом, что оноавтоматически отключается после того, как произведено
необходимое количество продукции или при появлении
брака
Рабочему уже не нужно постоянно следить за работой
станков
Ручные операции можно отделить от механических, а
рабочий, закончив обслуживание станка А, может заняться
станком В, в то время как станок А продолжает
функционировать.
Рабочий может одновременно обслуживать более одного
станка, появляется возможность сократить число рабочих, а
следовательно, и себестоимость продукции.
13.
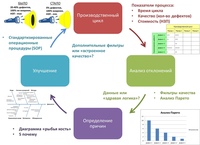
когда произведено заданное количество изделий
и поскольку выпускаются только изделия
требуемого качества, то автономизация
исключает перепроизводство
Тогда появляется возможность применить метод
«точно вовремя» и обеспечить быструю
приспосабливаемость производства к изменениям
спроса
14. Возрастание роли человеческого фактора
Контроль качества основан насамостоятельности работника и требует
оперативного принятия им решений, то это
побуждает работников к повышению
квалификации и таким образом ведет к
возрастанию роли человеческого фактора
15. Защитные системы останова линии
Контактный методДатчики — ограничители или фотоэлементы используются для того,
чтобы обнаруживать отличие в размере или в форме изделий и
таким образом выявлять определенные типы дефектов. Для того
чтобы можно было использовать метод контакта, иногда
практически аналогичным изделиям намеренно придают разные
размеры и форму.

другого, также являются составной частью контактного метода
Метод совокупности
Метод дополнительных действий
16. Защитные системы останова линии
Контактный методМетод совокупности
В отличие от контактного метода, который направлен главным
образом на то, чтобы установить наличие определенного признака
изделия, либо на то, чтобы удостовериться, что контролируемая
операция была правильно выполнена, метод совокупности
используется для того, чтобы обеспечить выполнение всех этапов
операции. Защитная система, основанная на этом методе,
используется, например, для того, чтобы гарантировать, что
рабочий вложил в упаковочную коробку все необходимые детали и
инструкцию
Метод дополнительных действий
17. Защитные системы останова линии
Контактный методМетод совокупности
Метод дополнительных действий
называется так потому, что в отличие от других простых методов
контроля он требует, чтобы рабочий произвел какое-то действие,
которое не является частью процесса обработки изделия.
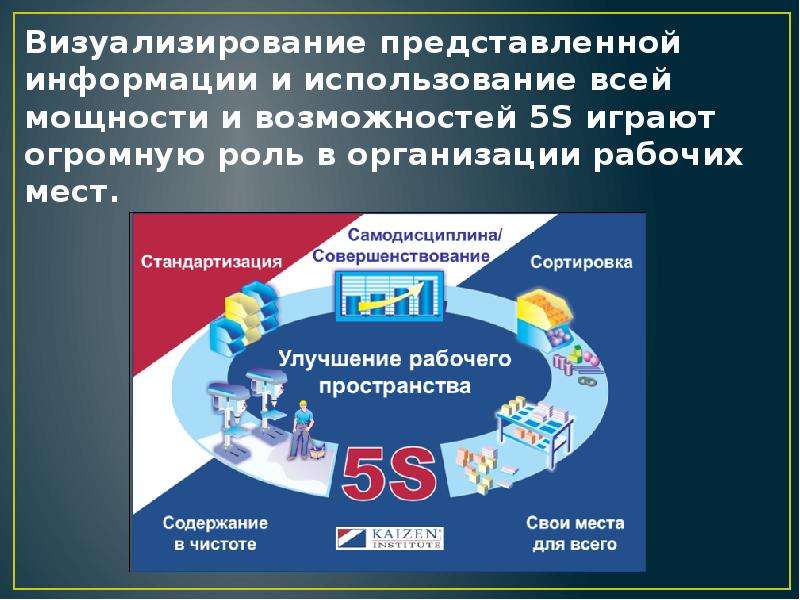
18. Средства визуального контроля
Электрические табло и сигнальные лампыЭлектрическое табло «Выход»
Электрическое табло «Обмен валюты»
19. Средства визуального контроля
Операционные карты и карточки канбанКанбан детали
Междурядная культивация
20. Средства визуального контроля
Цифровые дисплеи21. Средства визуального контроля
Указательные карточки складирования ипроизводственных запасов
22. Схема действия системы визуального контроля
Автономизация (автоматический контролькачества на рабочих местах)
Исправление неполадок
на линии или в
оборудовании
Простые
системы
Световое табло
(включая
сигнальные
лампы)
Наблюдение за
выполнением
нормируемых
операций
Операционная
карта
Производственная система «точно вовремя»
Выполнение
производственных
планов
Система
«канбан»
Цифровой
дисплей
Гарантия исправной
доставки и контроль за
производственными
запасами
Складская табличка
и табличка хранения
Системы визуального контроля эффективны в достижении автономизации,
но, как и другие методы контроля качества, они только фиксируют
неполадки
23.
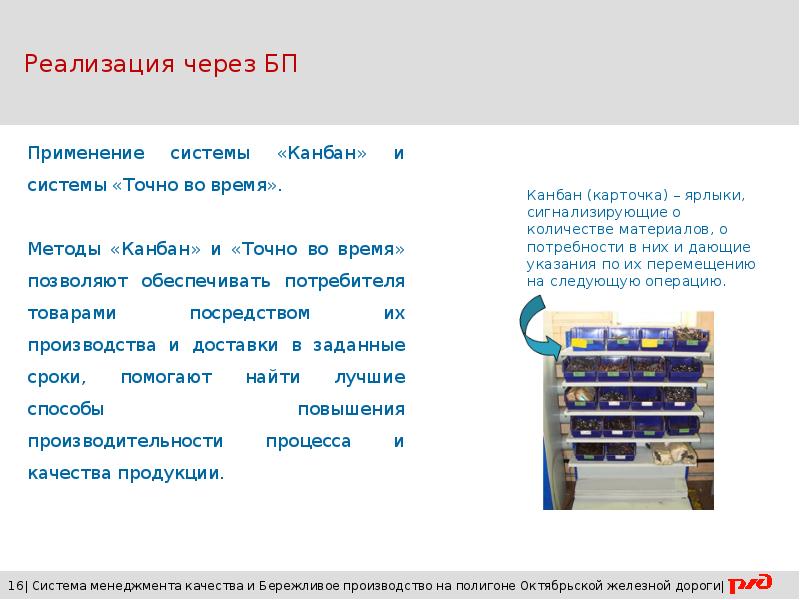
Невозможность заменить дефектные детали
или отремонтировать их во время простоя
Невозможность завершить все необходимые
операции в определенный временной цикл
Обнаружен брак
Останов на линии
Остановка линии и возвращение дефектных
деталей на предыдущие производственные
этапы
Усовершенствования с целью выполнения
всех операций в определенный временной
цикл
Усовершенствования с целью выполнения
всех операций в определенный временной
цикл
Гарантия качества
24. Обеспечение качества
«когда» — 8 этапов деятельности: планированиевыпуска изделия, конструирование изделия,
подготовка производства, производство,
производственный контроль, реализация и
обслуживание, проверка качества в эксплуатации;
«кем и где» — руководитель определенного
подразделения и название подразделения;
«что» — параметры и показатели , которые
должны быть гарантированны, и необходимые
для этого меры.
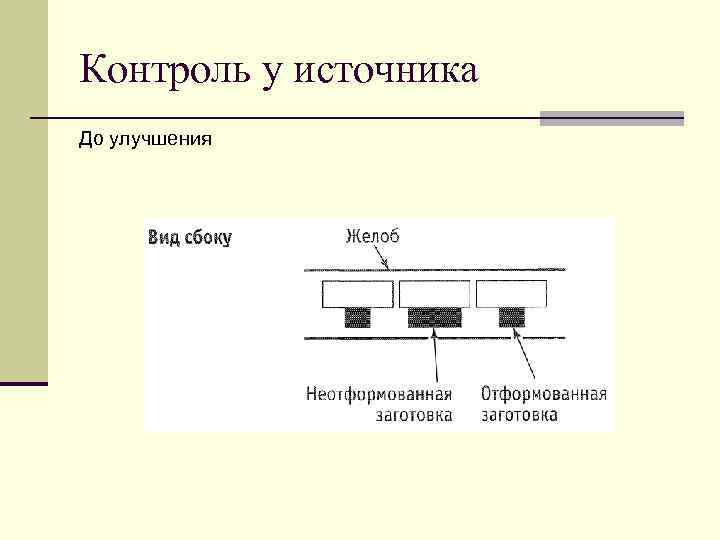
25. Применение устройств пока-ёкэ
26. Пример устройства пока-ёкэ, работающего по методу контакта
27. Пример устройства пока-ёкэ, работающего по методу фиксированного значения
28. Пример использования устройства пока-ёкэ, работающего по методу движений-этапов
29. Примеры сенсорных устройств различных видов
30. Образец использования ограничителя хода в качестве устройства пока-ёкэ
31. Образцы фотоэлектрических выключателей, фотодиодных датчиков и бесконтактных выключателей
32. Примеры использования датчиков различных видов
33. Примеры использования датчиков различных видов
34. Примеры использования датчиков различных видов
35. Примеры использования датчиков различных видов
36. Виды сенсорных устройств и их функции
37. Контроль у источника
До улучшения38. Контроль у источника
После улучшения39. Контроль у источника
До улучшения40. Контроль у источника
После улучшения41.

42. Контроль у источника
После улучшения43. Контроль у источника
До улучшения44. Контроль у источника
После улучшения45. Контроль у источника
До улучшения46. Контроль у источника
После улучшения47. Контроль у источника
До улучшения48. Контроль у источника
После улучшения49. Метод фиксированного значения
До улучшения50. Метод фиксированного значения
После улучшения51. Метод фиксированного значения
До улучшения52. Метод фиксированного значения
После улучшения53. Метод фиксированного значения
До улучшения54. Метод фиксированного значения
После улучшения55. Метод фиксированного значения
До улучшения56. Метод фиксированного значения
После улучшения57. Метод движений-этапов
До улучшения58. Канбан
Информация дляотдела снабжения
Название позиции
Описание позиции
Деталь № 12345
Используется в:
Мелкие детали
коробки приводов
Шифр сырья
Описание
Место хранения
Проволока Ø4
Хомут зажимной
Ячейка 5
Полка 3
Местонахождение
сырья
Количество
№ канбана/дата
120 шт.

№3-2/05-2011
Склад 56
А
B
C
D
E
59. Метод движений-этапов
После улучшения60. Метод движений-этапов
До улучшения61. Метод движений-этапов
После улучшения62. Метод движений-этапов
До улучшения63. Метод движений-этапов
После улучшения64. Метод движений-этапов
До улучшения65. Метод движений-этапов
После улучшения66. Метод движений-этапов
До улучшения67. Метод движений-этапов
После улучшения68. Метод движений-этапов
До улучшения69. Метод движений-этапов
После улучшения70. Метод движений-этапов
До улучшения71. Метод движений-этапов
После улучшения72. Заключение
Что может сделать работу лучше?Заинтересованность коллег
Спасибо за внимание!
Бережливое производство
Что такое бережливое производство? Существуют различные определения этого понятия, но если выразить очень коротко, то получится:
— это общеорганизационная система и стратегия достижения превосходства:
- созданием ценности (конечного результата)
- созданием культуры непрерывного роста производительности и мер по удалению ВСЕХ потерь ресурсов и времени
- созданием высококачественных, стабильных процессов и подчеркивания уважения к людям и их труду во всей организации.
Википедия говорит:
Бережливое производство (от англ. lean production, lean manufacturing — «стройное производство») — концепция управления производственным предприятием, основанная на постоянном стремлении к устранению всех видов потерь. Бережливое предприятие предполагает вовлечение в процесс оптимизации бизнеса каждого сотрудника и максимальную ориентацию на потребителя. Возникла как интерпретация идей производственной системы компании Toyota американскими исследователями её феномена.
Бережливость — это непрерывная методология совершенствования процесса.
Существует несколько ключевых принципов, необходимых в понимании для реализации бережливой системы. Неспособность понять и применить правила всеми участниками вашей организации, приведет к провалу попытки внедрения системы БП.
Без обязательства процесс становится неэффективен. Рассмотрим некоторые наиболее важные принципы, которые должны помочь вам в работе. Считайте, что это руководство к действию, поскольку существуют другие, которые не будут рассмотрены.
Устранение потерь при внедрении бережливого производстваСамым важным принципом бережливого производства, безусловно, становится ликвидация потерь. Многие нормы вращаются вокруг этой концепции. На предприятии имеется 7 основных видов потерь:
Потери перепроизводства
Потери перепроизводства считаются наихудшими из 7 потерь. Когда будут рассматриваться основные понятия своевременного предприятия, которые строят то, что необходимо, когда это необходимо, в количестве, необходимом, неудивительно, что трата перепроизводства считается наихудшей тратой.
Потери от ненужных движений
Потери движения предвечны в любой компании, будь то производственное предприятие, офис или розничный магазин. Чтобы уменьшить или устранить этот вид потерь, нужно рассмотреть такие области, как изгиб, подъем, подъем и избыточная ходьба, для улучшения методов. Ручка, оставленная на другой стороне стола считается ненужным движением, так как ее нужно было взять одной рукой и перенести на другую.
Потери от лишнего (ненужного) инвентаря
В условиях бережливости ненужный инвентарь считается одним из 7 основных видов потерь. Хотя уровень запасов может иметь хороший смысл, вы захотите избежать избыточных запасов. Инвентарь может вскрыть много проблем в компании. Лучший способ выявить эти проблемы — снизить ваш инвентарь.
Потери при сборке дефектов
Самой простой утратой для идентификации является изготовление дефектов. Этот вид потерь может привести к переработке, утилизации отходов в компании. Будет еще одна большая проблема, если дефекты вскроются позже. Из-за высокого риска потенциальные потери при выпуске дефектов могут быть наиболее дорогостоящими из всех потерь. Это может стоить вам клиента, что приведет к лишению будущих продаж.
Потери от ожидания
Отходы ожидания можно найти во многих формах. Это очевидно в некоторых ситуациях, но трудно увидеть в других. Наиболее очевидные формы ожидания будут видны, когда на производственной линии возникают нехватки компонентов или когда машина не работает. Потери ожидания могут быть сложнее заметнее в процессе, поскольку можно упустить из виду или считать НЕОБХОДИМЫМ. Эти отходы, как и все потери, должны быть идентифицированы и устранены.
Потери от транспортировки
Потери транспортировки могут включать необработанные компоненты, подузлы, пустые ящики или почти все, что требуется. Его можно будет найти не только в производственной зоне, но и в областях доставки материалов по всей цепочке поставок и даже в офисах. Транспортировка материала является необходимой деятельностью, но она не повышает ценность конечного продукта. Устранение или уменьшение этого типа потерь на вашем объекте (или в вашей цепочке поставок) может сократить общее время выполнения или время цикла.
Потери от переработки
Как и в случае большинства других видов неэффективности, некоторые потери от переработки будут легко идентифицироваться, в то время как других не будет. Углубленный взгляд на текущие процессы должен выявить, где существуют возможности улучшения, хотя их, возможно, не удастся устранить. Три основные вещи, которые нужно учитывать с точки зрения переработки, — это то, действительно ли работа необходима, если она добавляет ценность продукту и есть ли лучший способ, чтобы перестроить работу.
Хотя вышеупомянутые виды потерь первоначально были ориентированы на воспроизводство, они могут применяться и ко многим видам бизнеса. Идея удаления потерь заключается в том, чтобы проверить все области в вашей организации, определить, где работает не бережливость, чтобы уменьшить или устранить ее.
Постоянное качественное увеличение при внедрении бережливого производства на предприятии
Непрерывное совершенствование (обычно упоминаемое японским словом kaizen), возможно, оказывается самым критическим принципом бережливого производства. Это должно действительно стать основой вашей бережливой реализации. Без постоянного улучшения ваш прогресс будет прекращен. Как следует из названия, непрерывное совершенствование способствует постоянному, обязательному изменению к достижению желаемого состояния.
Изменения могут быть большими или малыми, но должны поддаваться улучшению (часто для достижения цели требуется много небольших изменений). Процесс действительно постоянный, так как всегда найдётся место для улучшения.
Непрерывное совершенствование должно быть разумным во всей организации. Не увлекайтесь, пытаясь улучшить всё и сразу, так не бывает. Маленькие дела часто могут привести к большим улучшениям.
Уважение к людям и к их труду — как инструмент бережливого производства в компаниях
Следующий принцип бережливого производства связан с людьми. Самым ценным ресурсом для любой компании — люди, которые работают на нее. Без этих людей бизнес или рабочий процесс не удастся. Когда люди не чувствуют себя уважаемыми, они склонны терять уважение к компании. Это может стать серьезной проблемой, когда вы пытаетесь реализовать бережливость.
Большинство людей хотят хорошо работать на работе. Рабочие идут на работу, чтобы зарабатывать на жизнь, они хотят развивать чувство ценности в своей работе. Хотят чувствовать, что внесли вклад в достижение целей компании, так как их работа и усилия что-то значили. Компания, поддерживающая уважение к философии человечества, будет ценить усилия рабочих и держать их на высоком уровне.
Попробуйте такие методы, чтобы люди знали, что их уважаете и цените: постоянное общение, похвала за хорошо выполненную работу, слушание их идей и помощь, когда это необходимо.
Выровненное производствоОснова бережливости — выровненное производство. Основа этого тезиса — то, что рабочая нагрузка одинакова всегда. Большинство компаний-производителей находятся во власти своих клиентов — заказчиков. Перед выпуском продукта они ждут получения заказов. Это приводит к увеличению времени на транспорт, которое может не удовлетворять требованиям клиентов.
На другом конце спектра некоторые компании будут производить, основываясь исключительно на прогнозе. Это может привести к избыточному продукту, который не требуется клиенту. Выравнивание созданий изделий учитывает как прогноз, так и историю. Ключевым элементом этого правила бережливого изготовления оказывается использование подтягивающей системы.
Своевременное производствоСледующим ключевым принципом является своевременное изготовление. Основой принципа является построение того, что требуется, когда требуется, и требуемого количества. Работая в сочетании с выровненным выпуском изделий, этот принцип хорошо работает с подтягивающей системой. Он позволяет перемещать и производить детали только при необходимости. Это означает, что компоненты не используются в продукте, который не требуется, и нет времени, затрачиваемого на строительство непродаваемого продукта.
Встроенное качество — обязательное условие бережливого производстваПоследним ключевым принципом бережливости, на который хотел обратить внимание, является встроенное качество. Идея принципа заключается в том, что качество встроено в производственный процесс. Качество встроено в конструкцию детали. Качество встроено в упаковку. Качество во всех областях продукта, от дизайна до доставки, является важным фактором качества.
Автоматизация с человеческим прикосновением входит в этот принцип. Прекрасным примером принципа являются машины, обнаруживающие дефекты и останавливать создание продукта.
Пять ключей бережливости
- Совершенствование системы с целью найти слабые места.
- Прогнозирование — система сбора информации о неисправностях оборудования и механизмов. Анализ проблем. Планирование технического обслуживания.
- Корректировка – устранение частых отказов, модернизация.
- Автономия — распределение обязанностей между персоналом.
- Постоянное улучшение — вовлечение работников в деятельность по поиску потерь (признаков БП). Предложение рабочими методов устранения.
«Встроенное Качество» в Фармацевтике
“Встроенное Качество” в Фармацевтике
December 4th, 2017Идея работы Джозефа Джурана «Встроенное Качество» содержится в том, что качество не может быть «проверено», а скорее «встроено» в процесс. Эта работа показывает, что большинство сбоев в обслуживании или создании новых продуктов являются результатом плохого планирования.
Качество фармацевтических продуктов
QbD (англ. Quality by design) – лучше всего определяется как систематический подход к развитию. Он начинается с определенных целей, которые сожержат в себе понимание процесса и его контроль. Этот подход основан на управлении рисками качества. QbD становится эффективным инструментом для совершенствования и поддержки фармацевтической практики.
Раньше качество почти полностью определялось послепроцессорной инспекцией, практически не имеющей основы для корректирующих действий или постоянного совершенствования. Это привело к созданию крупных глобальных регулирующих органов для фармацевтических компаний, ведущих инициативы QbD за последние десять лет, которые стали инициативами в самой отрасли. Практика QbD все чаще становится лучшей практикой во многих фармацевтических компаниях. Цели фармацевтического QbD могут включать следующее:
- Достижение значимых характеристик качества продукции, основанных на клинической эффективности
- Повышение возможности процесса и снижение вариативности качества продукта и его дефектов за счет улучшения дизайна продукта и процесса, понимания и контроля
- Повыщение продуктивности и эффективности производства
- Улучшение анализа основных причин и управления изменениями
В рамках QbD эти цели часто могут быть достигнуты путем связывания качества продукта с желаемой эффективностью, а затем разработки надежной рецептуры и производственного процесса для последовательного предоставления желаемого качества продукта.
Повысьте свои навыки путем обучения
Целями внедрения QbD в фармацевтике являются снижение вариативности качества продукта, что способствует повышению эффективности производства и эффективности производства и управлению изменениями после утверждения. Это достигается путем разработки надежной рецептуры и производственного процесса и установления клинически значимых спецификаций.
Если вы заинтересованы обучением по Лин Шесть Сигм и QbD в области фармацевтики – пишите нам [email protected]
Дзидока (jidoka) – методика системы встроенного качества | Бережливое производство (Lean)
Друзья, всем привет! В прежних статьях я затрагивал тему встроенной системы качества на производстве и привел пример одного из инструментов, который хорошо зарекомендовал себя в данном направлении (Poka Yoke). У меня на канале есть статья с подробным описанием данного инструмента. Сегодня предлагаю вам познакомиться ещё с одним инструментом системы встроенного качества — Дзидока (jidoka)
Дзидока (jidoka) – методика системы встроенного качества в производственный процесс с применением автоматизированных систем и инструментов. Основной целью данной методики является сокращение количества выпускаемых дефектов, тем самым снижение потерь в производстве. Простыми словами в основе метода Дзидока заложена задача по построению работы оборудования в производстве таким образом, чтобы оно могло само обнаружить отклонения продукции по качественным свойствам. Неоднократно слышал другое название данной методики – «Автономизация оборудования».
Своё начало методика берет с середины 20 века, как и большинство инструментов бережливого производства, в Японии (группа компаний «Тойота»). Где успешно работал с методикой и доказал её эффективность всем известный Тайити Оно. Но также известен тот факт, что методику Дзидока применили гораздо ранее. Примерно в конце 19 века основатель компании Тойота нашел применение инструменту в ткацкой промышленности, запустив автоматический ткацкий станок. Ключевой особенностью (инновацией) станка являлось то, что он выключался сразу после обрыва нити, не допуская тем самым выпуска дефектной продукции.
В наше время методика Дзидока хорошо себя зарекомендовала практически во всех производственных цепочках непрерывного цикла, где у операторов практически отсутствует возможность 100% контроля производственных операций. Лично я видел применение данного инструмента во многих секторах – металлургия, удобрения, продукты питания и т.д.
Эффективность от внедрения методики в производстве:
1. Повышение скорости обнаружения отклонений по качеству
2. Снижение затрат на переработку дефектной продукции и устранению потерь в производстве
3. Изменение подхода к решению проблем в производстве – повышение уровня вовлеченности у сотрудников
4. Повышение организационной эффективности, за счет снижения потребности в дополнительных ресурсах (сотрудников)
Пример.
Во время одного из аудитов на производство макаронных изделий я стал свидетелем того как производственная линия остановилась, когда встроенная в конвейер система взвешивания обнаружила отклонения по весу упаковки макаронных изделий. Система проинформировала о проблеме оператора и технолога, а они в свою очередь устранили причину проблемы и запустили линию в работу. Хочу отметить что отклонения по весу из-за которых была остановлена линия составляли 50 грамм (10% от веса упаковки), прежде чем оператор заметил бы данные отклонения линия смогла бы произвести более 500 кг продукции.
15 базовых инструментов для внедрения Бережливого производства.
Бережливое производство: цели, основные понятия, концепция и инструменты.
Как снизить затраты и себестоимость продукции, при этом повысить качество продукции и сократить сроки выполнения заказа или услуги? Технология внедрения бережливого производства, формирования и совершенствования производственной системы.
Как добиться снижения себестоимости продукции и повышения прибыли предприятия, не экономя на ФОТ, накладных расходах и цене закупного материала.
Обзор базовых инструментов и методов бережливого производства.
Анализ производственного процесса взглядом «орла» и «муравья» — учимся сначала определять процессы, а потом управлять ими.
Картирование потока создания ценности. Карта текущего состояния процесса — отличный инструмент для понимания существующих процессов в компании и поиска потерь. Создавая карту, вы сможете спланировать будущие изменения.
Оптимизация бизнес-процессов. С чего начать? Какие процессы оптимизировать в первую очередь?
7+1 видов поверхностных потерь. Видеопримеры – анализ, обсуждение выявленных потерь.
Практическая игра «Взлёт».
Практический кейс по интеграции действий членов команды для достижения общей командной цели.
Трехчасовая игра, в первом раунде участники моделируют — “проживают” существующий производственный процесс в компаниях. Во втором раунде, выявляют и анализируют потери, вырабатывают совместные решения по эффективному построению производственного процесса: организуют производственные ячейки с поточным единичным производством в соответствии со временем такта с минимальными необходимыми запасами, нацеленные на получение прибыли и снижение себестоимости продукции.
В результате игры участники отрабатывают навыки анализа производственного процесса, выявления потерь, планирования работы по повышению эффективности процессов.
Инструменты стандартизированной работы — документированные процедуры (инструкции), в которых зафиксирован наилучший способ выполнения операций.
Определение «узких мест» производства по месту — по факту. Узкое место (или так называемое “бутылочное горлышко”), которое находим в конкретном процессе, основываясь на фактических данных. “Бутылочное горлышко” не позволяет производить больше или быстрее. Устранение такого места влечет за собой улучшение производительности и сокращение времени выпуска продукции или оказания услуги.
Инструменты планирования, организации и управления производством в зависимости от типа производства.
8 отработанных на практике инструментов совершенствования заводской логистики.
Сессия вопросов-ответов.
Используя подход встроенного качества — FABTECH USA
Компания, начавшая путь с бережливого производства, понимает, что эффективная система бережливого производства направлена на добавление ценности продуктам и услугам, выявление и сокращение отходов, а также на улучшение поддержки сотрудников в организации.Ключевым элементом стратегии любой производственной организации также является достижение исключительного уровня качества продукции. Хорошо внедренная и управляемая система бережливого производства (LM) поможет достичь этой цели.
Критический принцип для получения высококачественных продуктов и услуг: не принимать; строить; или отправьте дефект. Но как организации достигают этой цели даже в среде LM? Остается ли полагаться на многоуровневую проверку, обнаружение и локализацию дефектов? Или акцент делается на наличии эффективных средств управления процессами и их соблюдении?
Самый действенный и действенный способ гарантировать высокое качество работы — это использование концепции под названием «Встроенное качество» (BIQ).BIQ — один из пяти принципов бережливого производства. Остальные четыре принципа:
- Вовлеченность сотрудников
- Стандартизация
- Короткое время выполнения
- Непрерывное совершенствование
BIQ, интегрированный с другими четырьмя принципами бережливого производства, определяет шаги, необходимые для обеспечения качества в производственном процессе. BIQ позволяет организации перейти от обнаружения и локализации дефектов к предотвращению их появления.Путем миграции через каждый этап процесса BIQ организация может повысить свою способность создавать качество на станции и снизить общие затраты на качество за счет уменьшения потребности в проверках и исправлениях.
Применяя концепции BIQ, производственная организация берет на себя все возрастающую ответственность за достижение качественных результатов на каждом этапе процесса BIQ. Кроме того, для достижения более высоких уровней производительности BIQ требуется более активное участие других функций внутри компании, таких как разработка продуктов, производство и закупки.Ответственность за BIQ становится «общекорпоративной». Built-In-Quality гарантирует, что каждый в организации вовлечен в достижение поставленных целей в области качества и удовлетворенности клиентов.
В моем выступлении на FABTECH 2016 в Лас-Вегасе 17 ноября я расскажу о концепции BIQ и о том, что необходимо для ее достижения в любой организации. И участники поймут:
- Основные принципы бережливого производства
- Как концепция качества сочетается с бережливым производством
- Как начать оценивать текущее положение компании в области качества
- Методы и инструменты, используемые с BIQ
- Как внедрить культуру бизнес-аналитики с лидерством на профессиональном уровне
[x_author title = ”Об авторе”]
Качество, заложенное в процессах
Экономичные производственные компании будут в максимальной степени стремиться к качеству своих процессов.Повышая качество вашего процесса, вы предотвращаете ненужные переделки и брак. Это означает, что ваши машины способны обнаруживать отклонения (дзидока), а ваши приспособления имеют защиту от ошибок, чтобы избежать неправильной сборки (poka yoke).
Обнаружение аномалий с помощью машин (дзидока)
При рассмотрении встроенного качества главный аспект, который следует вспомнить, — это «автоматизация с участием человека» или дзидока. Это один из основных столпов бережливого производства.
Автоматизация (дзидока) означает способность машины определять хорошие или плохие условия.При обнаружении ненормального состояния машина останавливается и срабатывает сигнал тревоги. Это должно заставить кого-нибудь снять детали и перезагрузить машину. В противном случае есть вероятность, что подозрительные части могут продолжить процесс.
Первоначальная концепция родилась, когда Toyota разработала ткацкий станок, который останавливался при обрыве нити. Это избавляет от необходимости стоять там и контролировать каждую машину. Отсюда и термин «автоматизация с участием человека».
Проверка ошибок (Poka-yoke)
В условиях бережливого производства концепция JIT не позволяет делать что-то второй раз.Вот почему так важно обеспечить качество, встроенное в ваш процесс. Идеи, необходимые для успеха, не всегда должны быть сложными или дорогими.
Профильные приспособления с датчиками присутствия — хороший пример poka-yoke. Он должен позволять вам вставлять только те компоненты, которые подходят, и будет сигнализировать, если машина будет работать без всех компонентов. Проведите пальцем по экрану для определения высоты, чтобы проверить, была ли сделана разбивка. Заблокируйте это до следующей операции, и вы фактически гарантируете хорошее качество деталей.
Независимо от того, что за идея, чем больше исправлений ошибок в процессе, тем лучше для вас. Это предотвращает дорогостоящие переделки, брак и потенциально пропущенные поставки.
Четыре столпа внутреннего качества
Quality Insider
Четыре столпа внутреннего качества
Хорошая основа важна для эффективной системы качества
Опубликовано: 29 ноября 2010 г. — 16:49
Схема дома Toyota Production System (TPS) часто строится с треугольной крышей, прямоугольным фундаментом и двумя прямоугольными колоннами между фундаментом и крышей.Пространство между столбцами заполнено выбранными вами системами, инструментами и принципами, подходящими для экономичного корпоративного приложения. Есть некоторые различия в том, что входит в основу, но немногие не согласны с тем, что кайдзен , стандартизированная работа и хейдзунка принадлежат именно этому. Колонны точно в срок и встроенного качества (также известные как дзидока ).
По сути, встроенная опора качества — это практика контроля переменных внутри процесса, обеспечения качества в собственном процессе, недопущения передачи плохого качества и проверки каждой детали.Это полная противоположность тому, что мы часто наблюдаем в традиционных организациях; благонамеренные люди передают сомнительное качество, беспорядочно проводят проверки на соответствие неадекватным или устаревшим стандартам, поднимают тревогу и во многих случаях встречают молчаливые взгляды и, в конце концов, тратят огромное количество времени на устранение дефектов, которые проскальзывают к заказчику. В отсутствие времени для принятия мер противодействия первопричинам цикл продолжается до тех пор, пока в результате преобразования бережливого производства или эквивалентного изменения культуры не будут внедрены системы для изменения такого поведения.
Войдите или создайте БЕСПЛАТНУЮ учетную запись, чтобы продолжить
Дайджест качества не взимает плату с читателей за его содержание. Мы считаем, что новости отрасли важны для вашей работы, и Quality Digest поддерживает предприятия любого типа.
Однако кто-то должен платить за этот контент. И именно здесь на помощь приходит реклама. Большинство людей считают рекламу неприятной, но она действительно выполняет полезную функцию, помимо того, что позволяет медиакомпаниям оставаться на плаву.Они информируют вас о новых продуктах и услугах, относящихся к вашей отрасли. Все объявления в Quality Digest относятся непосредственно к продуктам и услугам, которые нужны большинству наших читателей. Вы не увидите рекламу автомобилей или пищевых добавок.
Наше ОБЕЩАНИЕ: Дайджест качества отображает только статические объявления, которые никогда не перекрывают и не скрывают содержание. Они никогда не встанут у вас на пути. Они там для того, чтобы вы их читали, или нет.
Поэтому, пожалуйста, отключите блокировку рекламы на нашем сайте.
Спасибо,
Дайджест качества
In Quality — масштабируемая гибкая структура
Найти курс : Внедрение SAFeLeading SAFeSAFe для команд Практики встроенного качества гарантируют, что каждый элемент решения на каждом этапе разработки соответствует надлежащим стандартам качества на протяжении всего процесса разработки.Инспекция не улучшает качество и не гарантирует его качества. Осмотр поздно. Качество, хорошее или плохое, уже есть в продукте. Качество не может быть проверено в продукте или услуге; он должен быть встроен в него ».
—W. Эдвардс Деминг
Способность предприятия предоставлять новые функции в кратчайшие сроки и адаптироваться к быстро меняющимся бизнес-средам зависит от качества решения. Поэтому неудивительно, что встроенное качество является одной из основных ценностей SAFe, а также принципом Agile Manifesto: «Постоянное внимание к техническому совершенству и хорошему дизайну повышает гибкость» [1]. Встроенное качество также является основным принципом мышления Lean-Agile, помогая избежать затрат на задержки (CoD), связанных с отзывами, доработкой и исправлением дефектов.Встроенная философия качества SAFe применяет системное мышление для оптимизации всей системы, обеспечивая быстрый поток по всему потоку создания ценности, и делает качество работой каждого.
Все команды, включая программное обеспечение, оборудование, операции, маркетинг продукции, юридические вопросы, безопасность, соответствие и т. Д., Разделяют цели и принципы встроенного качества. Однако методы работы будут различаться в зависимости от дисциплины, потому что их рабочие продукты различаются.
Чтобы поддерживать гибкость бизнеса, предприятия должны постоянно реагировать на изменения рынка, и качество рабочих продуктов, которые повышают ценность бизнеса, напрямую определяет, насколько быстро команды могут работать.Рабочие продукты, которые управляют бизнесом, различаются в зависимости от домена, но включают программное обеспечение, конструкцию оборудования, сценарии, конфигурации, изображения, маркетинговые материалы, контракты и многое другое. Продукты, построенные на прочной технической основе и соответствующие стандартам, легче изменять и адаптировать. Это еще более важно для крупных решений, поскольку совокупный эффект даже незначительных дефектов и неправильных предположений может привести к неприемлемым последствиям.
Высокое качество строительства требует постоянного обучения и приверженности, но преимущества для бизнеса оправдывают вложения:
- Повышение удовлетворенности клиентов
- Повышенная скорость и предсказуемость доставки
- Лучшая производительность системы
- Улучшенная способность к инновациям, масштабированию и соблюдению нормативных требований
В оставшейся части этой статьи описываются пять аспектов встроенного качества SAFe для технологических групп и рабочих продуктов (рис. 1).Команды, ориентированные на бизнес, могут использовать их в качестве справочника при применении встроенных методов обеспечения качества к своим рабочим продуктам. Налаживание потока является основополагающим для всех команд, поскольку оно описывает, как удалить ошибки, переделать и другие потери, которые снижают производительность. Остальные четыре описывают методы обеспечения качества, которые можно адаптировать к различным областям, включая сначала тестирование, автоматизацию и изучение альтернатив с дизайном на основе наборов. Измерение встроенного качества для команды и технической гибкости также содержит руководство по качеству, которое обычно применимо ко всем командам — объединение в пары, коллективное владение, стандарты, автоматизация и определение готового.
Рис. 1. Пять измерений встроенного качестваДостижение потока с помощью Test-First и конвейера непрерывной доставки
Agile-команды работают в быстрой, основанной на потоках системе, чтобы быстро разрабатывать и реализовывать высококачественные бизнес-возможности. Вместо того, чтобы проводить большую часть тестирования в конце, Agile-команды определяют и выполняют множество тестов на ранних этапах, часто и на нескольких уровнях. Тесты определяются для изменений кода с использованием разработки, управляемой тестированием (TDD) [2], критериев приемлемости Story, Feature и Capability с использованием Behavior-Driven Development (BDD) [3] и гипотезы о преимуществах функций с использованием Lean-UX [4] ( Фигура 2).Повышение качества гарантирует, что частые изменения в гибкой разработке не приведут к новым ошибкам и обеспечат быстрое и надежное выполнение.
Рис. 2. Практика «сначала тестирование» ускоряет потокThink Test-First
Agile-команды создают тесты для всего — функций, историй и кода — в идеале до (или в то же время) создания элемента или сначала тестируют. Test-first применяется как к функциональным требованиям (Feature и Stories), так и к нефункциональным требованиям (NFR) в отношении производительности, надежности и т. Д.Подход «сначала тестирование» разрушает традиционную «V-модель», создавая тесты на более ранних этапах цикла разработки (рисунок 3).
Рис. 3. Тестирование сдвига BDD и TDD слеваДля поддержки быстрого потока тесты должны выполняться быстро, и команды стремятся их автоматизировать. Поскольку более крупные сквозные тесты на основе пользовательского интерфейса выполняются намного медленнее, чем небольшие автоматизированные тесты, нам нужен сбалансированный портфель тестов с большим количеством небольших быстрых тестов и меньшим количеством крупных медленных тестов. Мышление, ориентированное на тестирование, создает сбалансированную пирамиду тестирования (рис. 4).К сожалению, портфели тестирования многих организаций несбалансированы: слишком много больших, медленных, дорогих тестов и слишком мало маленьких, быстрых и дешевых тестов. Создавая большое количество кода и тестов на уровне истории, организации сокращают свою зависимость от более медленных, сквозных и дорогостоящих тестов.
Рис. 4. Уравновешивайте портфель тестов с множеством быстрых автоматических тестов.Создание конвейера непрерывной доставки
.Эти и другие встроенные методы обеспечения качества помогают создать конвейер непрерывной доставки (CDP) и возможность выпуска по запросу.На рис. 5 показана часть непрерывной интеграции CDP и показано, как изменения, встроенные в компоненты, тестируются в нескольких средах до того, как они поступят в производственную среду. «Тестирование удваивает» скорость тестирования путем замены медленных или дорогих компонентов (например, корпоративной базы данных) более быстрыми и дешевыми прокси (например, прокси-сервером базы данных в памяти).
Рис. 5. Непрерывная интеграция способствует повышению качества.Ускорение обратной связи с помощью сокращенных наборов тестов
Поскольку тесты могут расти со временем, они задерживают Agile-команды.Для настройки и выполнения полных наборов тестов может потребоваться значительное время. Команды могут создавать сокращенные наборы тестов и тестовые данные («дымовой тест»), чтобы гарантировать наиболее важные функции, прежде чем переходить к другим этапам конвейера. Они сотрудничают с системной группой, чтобы сбалансировать скорость и качество и помочь обеспечить поток (см. Рисунок 6).
Рис. 6. Уменьшенные наборы тестов ускоряют обратную связьДостижение качества архитектуры и дизайна
Архитектура и дизайн системы в конечном итоге определяют, насколько хорошо система может удовлетворить текущие и будущие потребности бизнеса.Качество в архитектуре и дизайне упрощает реализацию будущих требований, упрощает тестирование систем и помогает соответствовать требованиям NFR.
Поддержка будущих бизнес-потребностей
По мере того, как требования развиваются на основе изменений рынка, открытий в области развития и других причин, архитектуры и проекты также должны развиваться. Традиционные процессы, которые заставляют принимать решения на раннем этапе, могут привести к неоптимальному выбору, что приведет к неэффективности, которая замедлит поток и / или вызовет дальнейшую переработку. Для определения наилучшего решения требуются знания, полученные путем экспериментов, моделирования, моделирования, прототипирования и других учебных мероприятий.Для этого также требуется подход, основанный на наборах, который оценивает несколько альтернатив, чтобы прийти к наилучшему решению. После определения разработчики используют Подиум Архитектуры для реализации окончательного решения. Гибкая архитектура предоставляет целенаправленное руководство по синхронизации проектирования и реализации между командами.
Дизайн для качества
По мере развития требований к системе, ее дизайн также должен развиваться, чтобы поддерживать их. Низкокачественный дизайн сложно понять и изменить, что обычно приводит к более медленной доставке с большим количеством дефектов.Применение хорошей связи / сплоченности и соответствующей абстракции / инкапсуляции упрощает понимание и изменение реализаций. Принципы SOLID [5] делают системы гибкими, чтобы им было легче поддерживать новые требования.
Шаблоны проектирования[6] описывают хорошо известные способы поддержки этих принципов и предоставляют общий язык для облегчения понимания и удобочитаемости. Название элемента «Завод» или «Услуга» быстро указывает на его намерение в более широкой системе. Использование дизайна, основанного на наборах, исследует несколько решений, чтобы прийти к лучшему варианту дизайна, а не к первому варианту.Дополнительные сведения см. В разделе «Качество дизайна» в руководстве SAFe по встроенному качеству.
Проектирование и проектирование для облегчения тестирования
Архитектура и дизайн также определяют тестируемость системы . Модульные компоненты, которые обмениваются данными через четко определенные интерфейсы, создают стык [7], которые позволяют тестировщикам и разработчикам заменять дорогие или медленные компоненты тестовыми двойниками. В качестве примера на рисунке 7 показан компонент «Контроллер скорости», которому для регулировки скорости требуется текущее местоположение транспортного средства из компонента «Местоположение GPS».Для тестирования контроллера скорости с помощью GPS-местоположения требуется соответствующее оборудование GPS и генераторы сигналов для репликации спутников GPS. Замена этой сложности тестовым двойником сокращает время и усилия на разработку и тестирование контроллера скорости или любого другого компонента, который взаимодействует с GPS Location.
Рис. 7. Модульная архитектура на основе компонентов создает стыки, упрощающие тестирование.Применение качества проектирования в киберфизических системах
Эти принципы проектирования также применимы к киберфизическим системам.Инженеры во многих областях используют моделирование и симуляцию для получения знаний в области проектирования. Например, технологии проектирования интегральных схем (ИС) (VHDL, Verilog) подобны программному обеспечению и обладают теми же преимуществами, что и эти конструктивные характеристики и принципы SOLID [8]. При проектировании оборудования также применяется понятие тестовых двойников посредством моделирования и моделирования, или они предоставляют прототип дерева перед резкой металла.
Это часто требует изменения мышления. Как и программное обеспечение, оборудование также будет меняться в течение жизненного цикла системы.Вместо оптимизации для завершения проектирования с учетом текущих потребностей планирование будущих изменений за счет повышения качества обеспечивает лучшие долгосрочные результаты.
Достижение качества кода
Все возможности системы в конечном итоге реализуются кодом (или компонентами) системы. Скорость и легкость добавления новых возможностей зависит от того, насколько быстро и надежно разработчики смогут их изменить. Здесь перечислены несколько практик, отчасти вдохновленных экстремальным программированием (XP) [9].
Модульное тестирование и разработка через тестирование
Практика модульного тестирования разбивает код на части и обеспечивает автоматические тесты для каждой части.Эти тесты запускаются автоматически после каждого изменения и позволяют разработчикам быстро вносить изменения, будучи уверенными, что модификация не сломает другую часть системы. Тесты также служат в качестве документации и являются исполняемыми примерами взаимодействия с интерфейсом компонента, чтобы показать, как этот компонент следует использовать.
Test-Driven Development (TDD) направляет создание модульных тестов, указывая тест для изменения перед его созданием. Это заставляет разработчиков думать о проблеме шире, включая крайние случаи и граничные условия перед реализацией.Лучшее понимание приводит к более быстрой разработке с меньшим количеством ошибок и меньшим количеством переделок.
Работа в паре
Pairing позволяет двум разработчикам работать над одним изменением на одной рабочей станции. Один служит драйвером, пишущим код, а другой — навигатором, обеспечивающим обзор и обратную связь в режиме реального времени. Разработчики часто меняют роли. Сопряжение создает и поддерживает качество, поскольку код будет содержать общие знания, точки зрения и лучшие практики от каждого участника. Это также повышает и расширяет набор навыков для всей команды по мере того, как товарищи по команде учатся друг у друга.
Стандарты коллективной собственности и кодирования
Коллективное владение снижает зависимость между командами и гарантирует, что любой отдельный разработчик или команда не будет блокировать быстрый поток доставки ценности. Любой человек может добавить функциональность, исправить ошибки, улучшить дизайн или провести рефакторинг. Поскольку код не принадлежит одной команде или отдельному человеку, поддержка стандартов кодирования способствует согласованности, чтобы каждый мог понимать и поддерживать качество каждого компонента.
Применение качества кода в киберфизических системах
Хотя не все конструкции оборудования имеют «код», создание физических артефактов — это совместный процесс, и эти методы могут принести пользу.Инструменты автоматизированного проектирования (САПР), используемые при разработке оборудования, предоставляют «модульные тесты» в форме утверждений для электронного проектирования, а затем моделирования и анализа в механическом проектировании. Стандарты сопряжения, коллективного владения и кодирования могут дать аналогичные преимущества для создания проектов, которые легче поддерживать и изменять.
Некоторые технологии проектирования оборудования очень похожи на код (например, VHDL) с четко определенными входами и выходами, которые идеально подходят для таких практик, как TDD [8].
Достижение качества системы
В то время как качество кода и дизайна гарантирует, что системные артефакты можно легко понять и изменить, качество системы подтверждает, что системы работают, как ожидалось, и что все согласны с тем, какие изменения вносить. Советы по достижению качества системы выделены ниже.
Создание выравнивания для достижения быстрого потока
Согласованность и общее понимание сокращают задержки разработчиков и переделки, обеспечивая быстрый поток. Поведенческая разработка (BDD) определяет совместную практику, при которой владелец продукта и члены команды согласовывают точное поведение для истории или функции.Применение BDD помогает разработчикам с первого раза сформировать правильное поведение и сокращает количество переделок и ошибок. Модельно-ориентированная системная инженерия (MBSE) масштабирует это согласование на всю систему. Посредством процесса анализа и синтеза MBSE обеспечивает высокоуровневое и полное представление обо всех предлагаемых функциональных возможностях системы и о том, как их реализует проект системы.
Непрерывная интеграция комплексного решения
Гибкость масштабирования приводит к тому, что многие инженеры вносят множество мелких изменений, которые необходимо постоянно проверять на наличие конфликтов и ошибок.Практики непрерывной интеграции (CI) и непрерывной доставки (CD) обеспечивают разработчикам быструю обратную связь (рисунок 8). Каждое изменение быстро создается, затем интегрируется и тестируется на нескольких уровнях, включая среду развертывания. CI / CD автоматизирует процесс перемещения изменений на всех этапах и знает, как реагировать, когда тест не проходит. Проверки качества для NFR также автоматизированы. Хотя CI / CD стремится автоматизировать все тесты, некоторые функциональные (исследовательские) и NFR (юзабилити) тесты могут выполняться только вручную.
Рис. 8. Непрерывная интеграция (CI) и непрерывная доставка (CD) способствуют повышению качества в масштабе всей системыПрименение качества системы в киберфизических системах
Киберфизические системы также могут поддерживать быстрый подход CI / CD — даже с длительным сроком поставки физических компонентов. Как указывалось ранее, имитации, модели, предыдущие версии оборудования и другие прокси могут заменить окончательные компоненты системы. На рисунке 9 показано, как группа разработчиков системы предоставляет наглядную платформу для тестирования инкрементного поведения, подключая эти прокси-серверы компонентов.По мере созревания каждого компонента (проявляется увеличивающимся покраснением) платформа для сквозной интеграции также созревает. При таком подходе команды компонентов берут на себя ответственность как за поддержку своей части окончательного решения, так и за развитие платформы инкрементального сквозного тестирования.
Рисунок 9. Непрерывная интеграция (CI) для киберфизических системДостижение качества выпуска
Releasing позволяет компании измерить эффективность гипотезы о преимуществах функции. Чем быстрее организация выпускает релизы, тем быстрее она учится и тем больше пользы приносит.Модульные архитектуры, которые определяют стандартные интерфейсы между компонентами, позволяют выпускать небольшие изменения на уровне компонентов независимо. Небольшие изменения позволяют выпускать более быстрые, частые и менее рискованные выпуски, но требуют автоматизированного конвейера (показан на рисунке 2) для обеспечения качества.
В отличие от традиционной серверной инфраструктуры, «неизменяемая инфраструктура» не позволяет вносить изменения вручную и напрямую в рабочие серверы. Вместо этого изменения применяются к изображениям серверов, проверяются, а затем запускаются для замены работающих в данный момент серверов.Такой подход создает более последовательные и предсказуемые выпуски. Это также позволяет автоматическое восстановление. Если операционная среда обнаруживает производственную ошибку, она может откатить выпуск, просто запустив предыдущий образ для замены ошибочного.
Поддержка соответствия
Для систем, которые должны демонстрировать объективные свидетельства соответствия или аудита, выпуск имеет дополнительные условия. Эти организации должны доказать, что система соответствует своему прямому назначению и не имеет нежелательных, вредных последствий.Как описано в статье о соответствии, Lean Quality Management System (QMS) определяет утвержденные практики, политики и процедуры, которые поддерживают Lean-Agile, основанный на потоке, непрерывный процесс интеграции-развертывания-выпуска.
Масштабируемое определение «Готово»
Определение «Готово» — важный способ гарантировать, что прирост стоимости можно считать завершенным. Непрерывное развитие дополнительных функциональных возможностей системы требует масштабного определения «сделано», чтобы гарантировать, что нужная работа будет выполнена в нужное время, причем некоторые из них будут выполнены на ранней стадии, а некоторые — только для выпуска.Пример показан в таблице 1, но каждая команда, тренинг и предприятие должны создать собственное определение. Хотя они могут быть разными для каждого ART или команды, обычно у них есть общий набор элементов.
Таблица 1. Пример масштабируемого определения SAFe для DoneДостижение качества выпуска в киберфизических системах
Принято считать, что качество выпуска не должно позволять изменениям бездействовать в ожидании интеграции. Вместо этого интегрируйте изменения быстро и часто через последовательно увеличивающиеся части системы, пока изменение не поступит в среду для проверки.Некоторые киберфизические системы могут проходить валидацию в среде клиента (например, обновления по беспроводной сети в транспортных средствах). Другие проксируют эту среду с помощью одного или нескольких макетов, которые стремятся получить раннюю обратную связь, как показано ранее на рисунке 5. Сквозная платформа со временем созревает, обеспечивая более высокие уровни точности, которые также позволяют проводить более раннюю верификацию и валидацию (V&V). как усилия по соблюдению. Для многих систем эта ранняя обратная связь по проверке и верификации и соблюдению требований имеют решающее значение для понимания способности производить или выпускать продукцию.
Узнать больше
[1] Манифест для гибкой разработки программного обеспечения. www.AgileManifesto.org [2] Бек, Кент. Разработка через тестирование: пример . Аддисон-Уэсли, 2003. [3] Пью, Кен. Lean-Agile Разработка на основе приемочных тестов: лучшее программное обеспечение благодаря совместной работе . Аддисон-Уэсли, 2010. [4] Готельф, Джефф и Джош Сейден. Lean UX: создание отличных продуктов с помощью Agile-команд. O’Reilly Media, 2016 г. [5] Мартин, Роберт. Принципы OOD. http://butunclebob.com/ArticleS.UncleBob.PrinciplesOfOod [6] Гама, Эрих и др. Шаблоны проектирования: элементы объектно-ориентированного программного обеспечения многократного использования. Аддисон-Уэсли, 1994. [7] Перья, Майкл. Эффективное тестирование с использованием устаревшего кода . Прентис Холл, 2005. [8] Ясински, Риокардо. Эффективное кодирование с помощью VHDL, принципы и передовая практика . MIT Press, 2016. [9] Бек, Кент. Объяснение экстремального программирования: примите изменения . Аддисон-Уэсли, 1999.Последнее обновление: 10 февраля 2021 г.
Информация на этой странице принадлежит © 2010-2021 Scaled Agile, Inc.и защищена американскими и международными законами об авторских правах. Ни изображения, ни текст не могут быть скопированы с этого сайта без письменного разрешения правообладателя. Scaled Agile Framework и SAFe являются зарегистрированными товарными знаками Scaled Agile, Inc. Посетите раздел часто задаваемых вопросов о разрешениях и свяжитесь с нами для получения разрешений.Как повысить качество с помощью экономичного производства | Малый бизнес
Бережливое производство — это производственная теория, которая делает упор на устранение отходов во всех формах.Затраты ресурсов, которые не влияют на стоимость продукта, расточительны в среде бережливого производства. Когда целью является устранение отходов, результатом является улучшение обслуживания клиентов, повышение эффективности и качества продукции, производимой предприятием.
Ориентация на клиента и постоянное совершенствование
Бережливые организации сосредотачиваются на ценности для потребителя. Стремясь снизить затраты для конечных потребителей, предприятия, использующие принципы бережливого производства, будут стремиться устранять дефекты, чтобы снизить добавленную стоимость переделки деталей и компонентов.Первым шагом к внедрению системы бережливого производства является создание среды, ориентированной на клиента. Помимо ориентации на клиента, бережливое производство делает упор на постоянное совершенствование, которое представляет собой систему небольших постепенных изменений для повышения эффективности и устранения потерь. Некоторые компании используют кружки качества или группы по повышению качества для выявления, устранения и устранения потерь в компании.
Идентификация отходов
Для устранения отходов, например дефектов качества, необходимо их идентифицировать.Один из инструментов, который может использовать бережливый производственный бизнес, — это отображение потока создания ценности. Картирование потока создания ценности создает визуальный образ того, как материалы и информация проходят через организацию с момента размещения заказа покупателем до момента его отправки отделом отгрузки. Процесс картирования подчеркивает неэффективность производственного процесса и предоставляет возможности для проектов постоянного улучшения. Идентификация отходов влияет на качество продукта, показывая, где в процессе возникают дефекты.
Анализ первопричин
После того, как группа контроля качества выявляет дефект или неэффективность, ее члены могут приступить к анализу первопричин. В то время как некоторые предприятия внедряют процессы проверки для удаления дефектных материалов из производства, бережливые организации проводят анализ первопричин, чтобы решить проблему и предотвратить появление дефектов. Анализ первопричины позволяет проследить причину дефекта до его источника. Причины могут включать отказ оборудования, человеческий фактор, дефекты сырья или проблемы с рабочим процессом.Принципы бережливого производства включают политику отсутствия дефектов, которая поощряет работников создавать безошибочные продукты.
Внедрение решения
Когда у предприятия есть четко определенная проблема и выявлена первопричина, следующим шагом является внедрение решения. Использование командного подхода к решению проблемы позволяет предприятиям извлекать вклад от работников во всех сферах производственного процесса. Команды могут реализовать решение и собрать данные, чтобы убедиться, что проблема решена.
Ссылки
Биография писателя
Луанн Келчнер работает в Дейтона-Бич, штат Флорида, и с 2008 года пишет как фрилансер. Ее писательская работа охватывает множество тем, но в основном сосредоточена на статьях о здоровье и улучшении дома. Келхнер имеет степень по английскому языку и литературе в Университете Южного Нью-Гэмпшира.
9 принципов бережливого производства, чтобы избавиться от жаргона и получить качественные результаты | Процессная улица
Если вам нравятся следующие преимущества для вашего бизнеса, вам необходимо использовать принципы бережливого производства:
- 80% + сокращение отходов
- Снижение производственных затрат на 50%
- Снижение постоянных запасов на 80-90%
- Снижение затрат на качество на 90% (производство качественной продукции на 90% дешевле)
- Повышение производительности труда на 50%
Бережливое производство — это система, метод, школа мысли и даже образ жизни, направленные на сокращение потерь.Хотя он обычно применяется в производстве (отсюда «принципы бережливого производства и »), методы его достижения можно использовать для сокращения отходов при сохранении высокого качества независимо от того, какой производственный процесс вы выполняете.
Ключ в том, чтобы знать, что включает в себя каждый принцип и как его использовать, и именно это мы и собираемся рассказать сегодня!
Продолжайте читать, чтобы получить полное изложение следующих принципов бережливого производства (с двумя методами для хорошей оценки):
- Устранение отходов
- Кайдзен (постоянное совершенствование)
- Уважайте человеческий фактор
- Хейдзунка (уровень производства)
- JIT (Just In Time) производство
- Однокомпонентный поток
- Качество встроенное
- Poka-Yoke (защита от ошибок)
- Дзидока (автоматическое обнаружение дефектов)
Принципы бережливого производства
Ликвидация отходов
Устранение потерь является ключевым моментом в практике бережливого производства.Отсюда и название «бережливое производство», как «с минимальными потерями и / или излишками, насколько это возможно».
С этой целью один из основных принципов бережливого производства, которому следует следовать, — это обеспечение минимального количества отходов, создаваемых всем, что вы делаете. Чем больше отходов вы устраните, тем больше ваш бизнес будет экономить на каждом производимом продукте и каждом выполняемом процессе.
Сюда входят:
- Наличие постоянного инвентаря (пустая трата площадей и ресурсов)
- Выведение побочных продуктов, непригодных для использования
- Слишком большое количество рабочих станций, увеличивающее время в пути между ними
- Резервное копирование производственных очередей из-за узких мест
- Слишком много рабочих назначено на ограниченную задачу
- Отсутствие автоматизации процессов там, где это может быть использовано
Трудно охватить все возможные случаи, когда можно сократить отходы, поскольку есть возможности сделать это практически в каждой выполняемой задаче.Однако, если вы документируете рабочие процессы, которым вы следуете во всем, что делаете, становится намного легче увидеть, где образуются отходы и как их устранять.
Например, без управления бизнес-процессами вы не узнаете, как выполняются задачи. Вы можете знать, как должны выполняться , но вы не знаете, какие методы ваша команда использует на практике.
Если вы не знаете, как ваши задачи выполняются на практике, вы не сможете сократить потери, так как вы даже не будете знать, какая часть вашего процесса вызывает эти потери.
Хотя полностью исключить отходы практически невозможно, стремление сделать это приведет к постоянному совершенствованию ваших процессов и методов и повышению эффективности.
Проще говоря, если вы не сосредоточены на сокращении отходов, вы не используете принципы бережливого производства.
Кайдзен (постоянное совершенствование)
Сокращение отходов и постоянное совершенствование идут рука об руку с принципами бережливого производства. Продолжая улучшать свой бизнес и процессы, вы можете максимально сократить отходы, устранив все узкие места, которые могут возникнуть, и проанализировав, какие процессы неэффективны.
Кроме того, постоянное стремление к совершенствованию — сильный подход к любой повторяющейся задаче, поскольку любые внесенные вами улучшения принесут пользу всем будущим результатам.
Однако единственный способ постоянно улучшать вашу практику — это в первую очередь документировать и управлять своими процессами и процедурами. Как и в случае с сокращением отходов, это позволяет вам увидеть, где есть пробелы и недостатки в вашем бизнесе, и, следовательно, что можно легко улучшить (или какие улучшения будут иметь наибольший эффект).
Непрерывное совершенствование процессов не требует, чтобы вы начинали с хороших процессов . Черт возьми, вы могли бы возразить, что начало плохих процессов означает, что вам нужно больше улучшать и, следовательно, больше выгоды от постоянного улучшения.
Вместо этого сосредоточьтесь на том, чтобы убедиться, что процессы, которые вы задокументировали, точны. Нет смысла документировать идеализированный процесс того, как должен делать , потому что тогда вы не будете знать, где вы сейчас находитесь и какие улучшения можно сделать.
Это сложно, но не упустите возможность и точно задокументируйте свои процессы, поговорив с вовлеченными сотрудниками и узнав, что на самом деле происходит на передовой.
Лучше иметь точный и полный дыр процесс, чем идеальную модель, не вписывающуюся в реальность.
Уважайте свои человеческие начала
Когда мы говорим о бережливом производстве (или производственных принципах в целом), «уважение к человечеству» — не первое, что приходит на ум. Конечно, вы можете ценить своих сотрудников и желать, чтобы они были счастливы и увлечены своей работой, но сделать это основным принципом, пронизывающим каждый элемент вашего бизнеса, — это больше, чем большинство из них могло бы сделать.
Однако без уважения к человечеству и людям в вашей организации вы не сможете стабильно работать на высоком уровне.
Это также простой в теории принцип, так как нужно помнить лишь о нескольких ключевых элементах:
- Не перегружайте сотрудников
- Покажите им цель их работы (чего она достигает)
- Согласуйте эту цель со своими собственными целями
- Ответственность за успехи и неудачи
- Разберитесь в корне проблемы, поговорив с сотрудником и позволив ему рассказать вам своими словами
- Убедитесь, что их задачи имеют как можно меньшее трение (ничто не мешает им выполнять их)
- Бросьте вызов, не требуя
- Придают стабильности, но и разнообразия в задачах
На практике управлять каждым из них становится намного сложнее, поскольку вы имеете дело с людьми, а не с непредсказуемыми машинами.Во многом ваш успех в применении этого принципа будет зависеть от ваших коммуникативных навыков и динамики вашей команды и менеджеров — в такой же степени зависит от ваших сотрудников, которые поддерживают и поддерживают друг друга, как и от вас.
В свою очередь, если вы привлечете своих сотрудников и проявите к ним уважение, которого они заслуживают, они будут производить более стабильный результат, который зачастую также более высокого качества. Это связано с тем, что количество ошибок, связанных с человеческим фактором, естественным образом сокращается, поскольку сотрудники не все время отключаются из зоны, потому что ненавидят свои задачи или рабочую среду.
Heijunka (уровень производства)
Хейдзунка — японское слово, которое (применительно к бережливому производству) означает «выравнивание производства». В свою очередь, это означает, что что бы ни случилось, ваш результат останется неизменным каждый день.
Теория прочна — глядя на среднюю сумму заказа, вы можете поддерживать стабильное производство и не спешить с выполнением конкретного заказа. В дни, когда вы производите больше, чем продаете, избыток превращается в «запасы колебаний», тогда как в дни, когда продается больше, чем производится, происходит обратное.
Хотя наличие определенного количества колеблющегося (или «безопасного») запаса может показаться противоречащим идее сокращения отходов, таких как постоянные запасы, это не так расточительно, как наличие всего склада инвентаря, сидящего там, не зная, когда он может быть использован.
Чтобы гарантировать, что этот страховой запас будет продан, а не просто займет место и ресурсы, вам необходимо тщательно рассчитать (и скорректировать) производительность в соответствии со средней суммой заказа. Затем вы также можете рассчитать, насколько большим должен быть ваш страховой запас, посмотрев на отклонение номеров заказов от среднего.
Без сомнения, это потребует небольшого количества проб и ошибок, но выравнивание производства позволяет закрепить наиболее эффективные методы и упростить прогнозирование вашей работы и результатов.
Heijunka — это практика, лучше всего подходящая для производства, когда продукт, который вы создаете, либо сложный, либо требует много времени для создания, а спрос на ваши продукты достаточно предсказуем. Это связано с тем, что ваш страховой запас должен позволять вам всегда выполнять заказ (что не будет правдой, если ваш спрос резко возрастет), а постоянная производительность полезна, когда на ваши продукты уходит много работы.
JIT (Just In Time) производство
JIT («Just In Time») — одна из многих школ технологических инноваций, ориентированных на сокращение отходов. Как производственный принцип, он сосредоточен на работе над задачей или предметом, чтобы удовлетворить спрос, и не более того. Ничего лишнего не завершается, так как это считается расточительством (подумайте о постоянном инвентаре).
К сожалению, JIT невероятно сложно реализовать и на практике сопровождается таким количеством недостатков, что трудно даже понять, с чего начать.
Конечная цель состоит в том, чтобы не иметь абсолютно никаких запасов, будь то сырые ресурсы, изделия незавершенного производства или готовая продукция. Таким образом, применение JIT к существующей производственной операции требует от менеджеров переосмысления и реорганизации всего этого.
Не говоря уже о том, что если вы ошибаетесь в прогнозе заказа или что-то случится, что повлияет на ваш результат (например, сотрудник замедляется или машина ломается), нет никакой защиты, к которой можно было бы прибегать. Если вы напортачите, будьте готовы не выполнять приказы.
По этой причине JIT не является обязательным принципом бережливого производства. Если вы можете достичь этого, тогда отлично, но в противном случае подумайте о том, чтобы разбить вашу операцию на более мелкие наборы задач, к которым JIT может применяться индивидуально. Таким образом, вы можете извлечь выгоду из этой идеи без того же уровня опасности, который связан с широким распространением.
JIT не обязательно противоречит и Heijunka, но в большинстве ситуаций метод, который вы используете, будет зависеть от сложности вашего продукта и от того, насколько предсказуемы ваши потребности.Создание простых продуктов по запросу возможно, потому что вашим клиентам не придется ждать очень долго, что позволит JIT-потоку иметь меньше отрицательных моментов с точки зрения того, как долго им придется ждать.
Наличие крайне непредсказуемого спроса на продукцию также больше подходит для JIT, чем для Heijunka, поскольку вы не можете гарантировать, что любой созданный страховой запас будет израсходован, а не станет избыточным.
Поток одной детали
Однократный поток — это бережливый подход к производственным очередям и продуктам WIP (незавершенное производство / процесс).Ограничив вашу незавершенную работу одним элементом, вы можете значительно повысить эффективность и качество, связанное с конечным результатом.
Представьте себе производственную линию с несколькими рабочими станциями и оптовый заказ. Используя единый поток, один элемент перемещается на первую рабочую станцию, вся работа там завершается, а затем продукт перемещается на следующую станцию. Тем временем следующий продукт перемещается на первую рабочую станцию.
Над одним продуктом всегда работают на любой стадии процесса, и ничего не остается в ожидании освобождения станции.Время в пути между рабочими станциями максимально ограничено (обычно благодаря оптимизированной планировке этажа), а задачи сгруппированы таким образом, чтобы как можно более равномерно распределить работу между станциями.
Чтобы узнать больше, ознакомьтесь с нашей статьей по теме:
Качество встроенное
Концепция качества, встроенного в ваши производственные процессы, является ключом к ведению эффективного, но успешного бизнеса. Нет смысла быстро производить дешевую продукцию, если конечный результат полон дефектов и, в конце концов, не будет продаваться.
Качество обычно страдает либо из-за неправильных процессов, либо из-за человеческой ошибки, поэтому этот принцип бережливого производства достигается за счет использования двух методов, которые я расскажу по отдельности:
- Poka-yoke (защита ваших процессов от ошибок)
- Дзидока (автоматическое обнаружение отклонений)
Помимо этих принципов, качество является неотъемлемой частью ваших процессов, поскольку вы учитываете ценность и продукт, который вы предлагаете своим клиентам, а затем следите за тем, чтобы ваши методы экономии эффективности не влияли на качество, связанное с предоставлением этой ценности.
Poka-Yoke (защита от ошибок)
Poka-yoke (японский термин, обозначающий «защита от ошибок») — это один из методов, используемых для обеспечения качества в бережливых процессах, будь то производственные рабочие процессы или другие.
Идея состоит в том, что каждый процесс может быть спроектирован так, чтобы изначально предотвращать ошибки, либо путем реинжиниринга задач в соответствии со стандартным форматом, либо путем включения конкретных мер, обеспечивающих своевременное обнаружение и исправление ошибок.
Например, в производственном процессе у вас может быть задача прикрепить руки к игрушечному роботу.Скажем, это делается путем закрепления рук на теле, в то же время вставляя пружину в плечевой сустав, чтобы обеспечить движение.
Стандартный процесс, вероятно, просто включает инструкции по установке пружин на плечевые суставы, а затем закреплению рук на месте. Несмотря на то, что это исправно, это допускает человеческую ошибку, поскольку мало что может помешать кому-то забыть прикрепить пружину. Ошибка затем усугубляется тем, что ее трудно (если не невозможно) обнаружить с первого взгляда, а для ее последующего исправления требуется разобрать продукт.
Чтобы избавиться от этой проблемы, эквивалент poka-yoke просто добавил бы дополнительную ступеньку для предварительной подготовки двух пружин вместо того, чтобы брать их прямо со склада.
Это простое изменение позволит рабочему сразу увидеть, вставили ли они обе пружины, и таким образом предотвратить ошибку. По крайней мере, это позволит работнику заранее определить свою ошибку и исправить ее, прежде чем она станет более серьезной проблемой.
Чтобы узнать больше об этой технике, ознакомьтесь с нашим сообщением по теме:
Дзидока (обнаружение дефектов с помощью автоматизации)
Комплимент «пока» — это дзидока — принцип, согласно которому большинство дефектов может быть обнаружено автоматически, чтобы полностью исключить человеческую ошибку из уравнения.
Вместо того, чтобы заставлять сотрудника проверять каждый продукт на наличие дефектов или ошибок (например, обрыв нити на ткацком станке), машина настраивается со встроенными проверками для автоматического выполнения задачи. При обнаружении ошибки раздается звуковой сигнал, чтобы сотрудники знали, что что-то пошло не так.
Этот человеческий фактор также является причиной того, что дзидока называют «автоматизацией с человеческим прикосновением».
Бережливый производственный цикл
В заключение стоит выделить момент, чтобы взглянуть на цикл бережливого производства, поскольку он также может предоставить некоторые полезные принципы бережливого производства, которым нужно следовать.
Пять этапов цикла бережливого производства:
- Определить ценность (определить ценность для конечного потребителя)
- Составьте карту потока создания ценности (определите все этапы вашего процесса и исключите те, которые не создают ценности)
- Создайте поток (сделайте шаги создания ценности в тесной последовательности, чтобы как можно быстрее предоставить клиенту максимальную ценность)
- Установите притягивание (сделайте так, чтобы клиенты требовали или искали продукт, а не вы им навязывали)
- Стремиться к совершенству (стремиться к совершенству, используя постоянное совершенствование, устраняя отходы, создавая надежные процессы и в целом следуя принципам, которые мы рассмотрели ранее)
Как видите, хотя эффективность и надежность важны при применении принципов бережливого производства в производстве, не менее важно убедиться, что все, что вы делаете, приносит пользу для конечной цели.В конце концов, нет смысла делать что-то эффективно, если вы добьетесь этого, сделав конечный результат бесполезным.
Что вы думаете об использовании бережливого производства в производстве? Есть какие-нибудь советы или предостережения по теме? Я был бы рад услышать от вас в комментариях ниже!
Качество в организации бережливого производства
Качество? Что это значит?В наши дни «качество» в производственной организации имеет очень много значений; есть системы управления качеством, менеджеры по качеству, статистический контроль процессов, и некоторые из нас даже помнят старые добрые «Круги качества».Когда в производстве делается упор от качества к бережливому производству, где теперь качество?
Качество по-прежнему необходимо в любой производственной среде, и «Качество у источника» является основополагающим для непрерывной производственной системы. Качество у источника включает требования к качеству на каждом этапе процесса и имеет средства контроля, поэтому известные проблемы выделяются и не передаются дальше. Поскольку бережливое производство сокращает количество отходов в производственной системе, отходы материалов и времени из-за низкого качества требуют внимания.
Наличие инспекторов в конце линии больше не является приемлемым способом попытаться контролировать качество продукции, покидающей ваш завод. На каждом этапе процесса необходимо знать спецификации продукта и допуски и проверять их правильность, на каждом этапе «добавления стоимости» продукта, который меняет его форму, соответствие или функцию. эти проверки должны быть встроены в процесс, а требования к качеству должны быть четко определены: на этом этапе я проверяю длину секции, или качество сварки, или чистоту поверхности.Если это хорошо, то идет сюда, если нет, то, что происходит, тоже нужно четко определить.
Инструменты визуального управления и защиты от ошибок — отличные способы четко определить аспекты качества, которые важны на каждом этапе, и упростить определение того, является ли деталь приемлемой или требует внимания.