Бережливое производство и его инструменты. Бережливое производство
Бережливое производство – это особая схема управления компанией. Основная идея состоит в постоянном стремлении исключить любые виды издержек. Бережливое производство – это концепция, предполагающая вовлечение в процедуру оптимизации каждого сотрудника. Такая схема направлена на максимальное ориентирование в сторону потребителя. Рассмотрим далее более подробно, что собой представляет система бережливого производства.

История возникновения
Внедрение бережливого производства в промышленность произошло в 1950-е годы в корпорации Toyota. Создателем такой схемы управления стал Тайити Оно. Большой вклад в дальнейшее развитие как теории, так и практики внес его коллега – Сигео Синго, который, кроме прочего, создал способ быстрой переналадки. Впоследствии американские специалисты исследовали систему и концептуализировали ее под названием lean manufacturing (lean production) – «тощее производство». В первое время концепция применялась в первую очередь в автомобилестроении. Спустя время схема была адаптирована и к процессному производству. Впоследствии инструменты бережливого производства стали использовать в здравоохранении, коммунальном хозяйстве, сфере услуг, торговле, вооруженных силах, секторе госуправления и прочих отраслях.
Главные аспекты
Бережливое производство на предприятии предполагает анализ ценности продукта, который выпускается для конечного потребителя, на каждой стадии создания. Основной задачей концепции выступает формирование непрерывного процесса устранения издержек. Другими словами, бережливое производство – это устранение любых действий, вследствие которых потребляются ресурсы, но в результате не создается никакой ценности для конечного потребителя. К примеру, ему не нужно, чтобы готовое изделие или его комплектующие были на складе. При традиционной системе все затраты, связанные с браком, переделкой, хранением, и прочие косвенные расходы перекладываются на потребителя. Бережливое производство – это схема, по которой вся деятельность компании разделена на процессы и операции, которые добавляют и не добавляют ценность продукту. В качестве основной задачи, таким образом, выступает планомерное уменьшение последних.
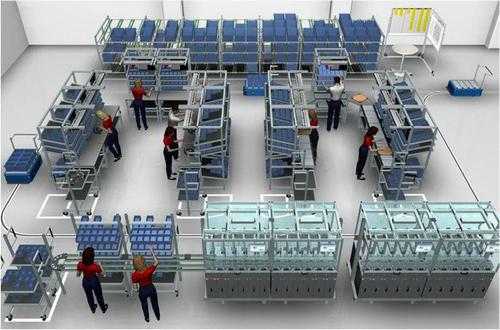
Бережливое производство: потери
В качестве синонима издержек в ряде случаев применяется термин muda. Это понятие означает различные расходы, мусор, отходы и так далее. Тайити Оно выделил семь видов издержек. Потери образуются вследствие:
- ожидания;
- перепроизводства;
- транспортировки;
- лишних стадий обработки;
- ненужных перемещений;
- выпуска дефектных товаров;
- лишних запасов.
Главным видом потерь Тайити Оно считал перепроизводство. Оно является фактором, вследствие которого возникают и остальные издержки. К приведенному выше списку был добавлен еще один пункт. Джеффри Лайкер, занимавшийся исследованием опыта Toyota, назвал в качестве потери нереализованный потенциал служащих. В качестве источников затрат называют перегрузку мощностей, сотрудников при осуществлении деятельности с повышенной интенсивностью, а также неравномерность исполнения операции (к примеру, прерывающийся график вследствие колебания спроса).
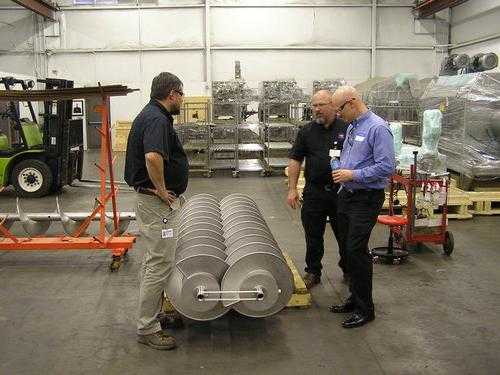
Принципы
Бережливое производство представляется в качестве процесса, разделенного на пять стадий:
- Определение ценности конкретного товара.
- Установление потока создания ценности данного продукта.
- Обеспечение непрерывного течения потока.
- Предоставление потребителю возможности вытягивать товар.
- Стремление к совершенству.
Среди прочих принципов, на которых основывается бережливое производство, следует выделить:
- Достижение отличного качества – сдача товара с первого предъявления, использование схемы «ноль дефектов», выявление и решение проблем на самых ранних стадиях их возникновения.
- Формирование долгосрочного взаимодействия с потребителем посредством деления информации, затрат и рисков.
- Гибкость.
Производственная система, используемая в Toyota, базируется на двух основных принципах: автономизации и «точно вовремя». Последний означает, что все необходимые элементы для сборки поступают на линию именно в тот момент, когда это нужно, строго в определенном для конкретного процесса количестве для сокращения складского запаса.
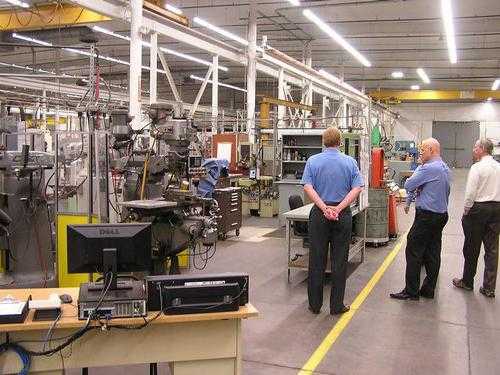
Составные элементы
В рамках рассматриваемой концепции выделены различные компоненты – методы бережливого производства. Некоторые из них могут и сами выступать в качестве схемы управления. К основным элементам относятся следующие:
- Поток единичных товаров.
- Общий уход за оборудованием.
- Система 5S.
- Кайдзен.
- Быстрая переналадка.
- Предотвращение ошибок.
Отраслевые варианты
Бережливое здравоохранение представляет собой концепцию сокращения временных затрат медперсонала, не связанных непосредственно с оказанием помощи людям. Лин-логистика является вытягивающей схемой, которая объединяет всех поставщиков, привлеченных к потоку создания ценности. В данной системе происходит частичное восполнение запасов небольшими объемами. В качестве основного показателя в этой схеме выступает логистическая совокупная стоимость. Инструменты бережливого производства используются почтовым ведомством Дании. В рамках концепции была осуществлена масштабная стандартизация предлагаемых услуг. Целями мероприятия выступали повышение производительности, ускорение пересылок. Были введены «карты поточного формирования ценности» для контроля и идентификации услуг. Также разработана и внедрена впоследствии система мотивации служащих ведомства. В строительстве сформирована особая стратегия, ориентированная на повышение эффективности процесса возведения сооружений на всех стадиях. Принципы лин-производства были адаптированы для разработки ПО. В городском, государственном управлении также используются элементы рассматриваемой схемы.
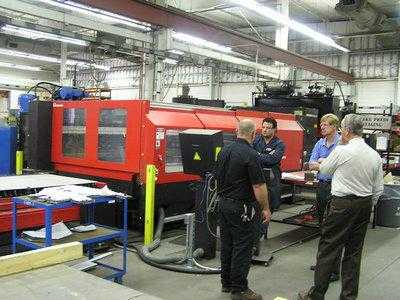
Кайдзен
Идея была сформулирована в 1950 году доктором Демингом. Внедрение этого принципа принесло большие доходы компаниям Японии. За это специалист был награжден императором медалью. Спустя время Союзом науки и техники Японии был объявлен приз им. Деминга за качество промышленных товаров.
Преимущества филосифии кайдзен
Достоинства этой системы были оценены в каждом промышленном секторе, где создавались условия для обеспечения наивысшей эффективности и производительности. Кайдзен считается японской философией. Она состоит в пропаганде непрерывных изменений. Школа мысли кайдзен настаивает на том, что постоянные преобразования выступают в качестве единственного пути к прогрессу. Основной упор система делает на повышение производительности посредством устранения ненужной и тяжелой работы. Само определение создано путем соединения двух слов: «кай» – «изменить» («преобразовать»), и «дзен» – «в сторону лучшего». Достоинства системы достаточно четко отражает успех экономики Японии. Это признают не только сами японцы, но и эксперты мира.
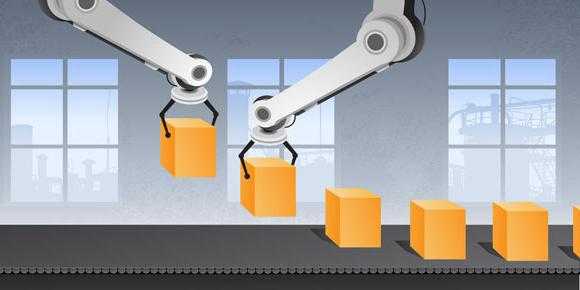
Цели концепции кайдзен
Выделяют пять основных направлений, по которым осуществляется развитие производства. К ним относят:
- Сокращение отходов.
- Незамедлительное устранение неисправностей.
- Оптимальное использование.
- Работа в команде.
- Наивысшее качество.
Следует сказать, что большая часть принципов основывается на здравом смысле. Основными компонентами системы выступают улучшение качества товара, привлечение к процессу каждого сотрудника, готовность к взаимодействию и переменам. Все эти мероприятия не требуют сложных математических расчетов или поиска научных подходов.
Сокращение отходов
Принципы философии кайдзен направлены на значительное снижение потерь на каждом этапе (операции, процессе). Одним из основных преимуществ схемы считается то, что она включает в себя каждого сотрудника. Это, в свою очередь, предполагает разработку и последующую реализацию предложений по совершенствованию на каждом уровне управления. Такая работа способствует минимизации потерь ресурсов.
Незамедлительное устранение неполадок
Каждый работник в соответствии с концепцией кайдзен должен противодействовать проблемам. Такое поведение способствует быстрому решению вопросов. При немедленном устранении неполадок время производственного цикла не увеличивается. Незамедлительное решение проблем позволяет направлять деятельность в эффективное русло.
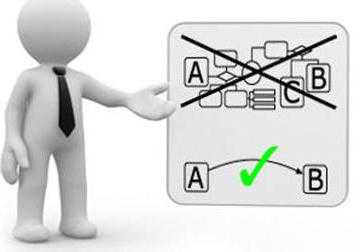
Оптимальное использование
При быстром решении проблем высвобождаются ресурсы. Они могут использоваться для усовершенствования и достижения иных целей. В комплексе эти меры позволяют наладить непрерывный процесс эффективного производства.
Работа в команде
Привлечение к решению проблем всех сотрудников позволяет найти выход быстрее. Успешное преодоление сложностей укрепляет дух и повышает самооценку сотрудников компании. Командная работа устраняет конфликтные ситуации, способствует формированию доверительных отношений между вышестоящими и нижестоящими служащими.
Лучшее качество
Быстрое и эффективное решение проблем способствует слаженной работе в команде, созданию большого объема ресурсов. Это, в свою очередь, обеспечит повышение качества выпускаемой продукции. Все это позволит компании выйти на новый уровень мощностей.
fb.ru
Что такое бережливое производство, LEAN и Toyota Production System
Иногда встречаешь человека, который ничего не слышал о бережливом производстве и просит вкратце рассказать, что это такое. Кроме того, есть люди, которые считают, что бережливое производство — это всё везде подписать и нанести напольную разметку.Оказывается, сложно в двух словах рассказать по теме, на которую можешь говорить неделю под ряд без остановки. Причем, умными словами (как в Википедии) объяснять может кто угодно, а я попробую простыми.
1. Ориентация на потребителя
В массовом производстве мы пытаемся угадать, что нужно рынку, производим это и надеемся распродать. В бережливом производстве мы сначала ожидаем заказов, и производим под них. Закупаем столько сырья, сколько нужно (только под конкретные заказы). Кроме того, очень внимательно относимся к обратной связи от клиентов.
Сейчас удастся встретить мало предприятий, загружающих склады, а не работающих под заказ. Но так работали General Motors, Chrysler, и, конечно же, Генри Форд.
2. Поток вытягивания
Бережливое производство — это вытягивающее производство. В массовом производстве стараются максимально загрузить оборудование, чтобы оно не простаивало, а производило как можно больше (пока есть из чего делать — делаем). Это создает огромные запасы как незавершенного производства, так и готовой продукции. Все эти запасы лежат без движения, ржавеют, теряются, устаревают морально и аккумулируют в себе деньги.
В вытягивающем производстве оборудование делает детали только тогда, когда с последующего этапа приходит информация что они там нужны.
Система оповещения называется «канбан».
Таким образом сокращаются запасы сырья, незавершенного производства и готовой продукции.
В бережливом производстве всё совершенствование выстраивается от потока, который перестраивается и балансируется. Делается всё возможное, чтобы он стал как можно более быстрым и оптимальным. Все остальные инструменты совершенствования крутятся вокруг потока и нужны для того, чтобы сделать совершенным именно поток создания ценности.
Совершенствование направляется узким местом. Концентрируется на нем. «Узкое место» — это некое ограничивающее общую производительность линии звено. После того, как узкое место улучшено, какое-то другое место становится узким.
«Lean» — это переводится не «бережливый». Это тощий, поджарый, стройный. Бережливо относиться можно к какой угодно системе производства. Но Lean именно поджарый, лишенный запасов. Когда про организм говорят, что он поджарый? Когда у него нет (жировых) запасов.
Визуально различие в потоках можно оценить здесь: Задача по производственному управлению
3. Организация производственных ячеек
Вживую выглядит так:
Цель: повысить производительность труда. Один человек может достигнуть такого совершенства, что сможет обслуживать сразу несколько единиц оборудования.
4. Сокращение длительности выпуска заказа
Все, чем мы занимаемся, — это следим за временем между размещением заказа потребителем и получением денег за выполненную работу. Мы сокращаем этот промежуток времени, устраняя потери, которые не добавляют ценности (Тайити Оно, 1988).
Нужно добиваться того, чтобы с того момента, как клиент подал заявку до момента, когда он получил свой заказ, проходило как можно меньше времени.
В этом процессе нужно ориентироваться на два понятия: время цикла и время такта.
Время цикла (длительность выпуска заказа) — это длительность прохождения изделия по всему потоку от начала до конца.
Время такта — это частота, с которой готовые изделия выходят с линии. Целевое время такта определяется рыночным спросом (например: нам нужно 2 автомобиля к сутки).
Массовое производство имеет очень короткое время такта (выпускает как из пулемета), но очень длительное время цикла (каждая из единиц производится долго). помимо замораживания материальных средств в виде незавершенного производства это также очень снижает скорость производства редких марок продукции.
5. Гибкость
В массовом производстве переналадка оборудования делается крайне редко — оборудование производит детали гигантскими партиями. В бережливом производстве следует изготавливать детали небольшими партиями, поэтому требуется часто переналаживать оборудование. Именно поэтому в нем очень развит инструмент SMED «Быстрая переналадка
6. Устранение потерь
Для того, чтобы сократить время цикла, устраняют потери. Потери — это всё, что не добавляет ценности конечному продукту. Прибыль повышается за счет устранения потерь на производстве.
Виды потерь:
- Перепроизводство;
- Излишние запасы;
- Ожидание;
- Транспортировка;
- Перемещения;
- Излишняя обработка;
- Дефекты;
- Нереализованный потенциал сотрудников.
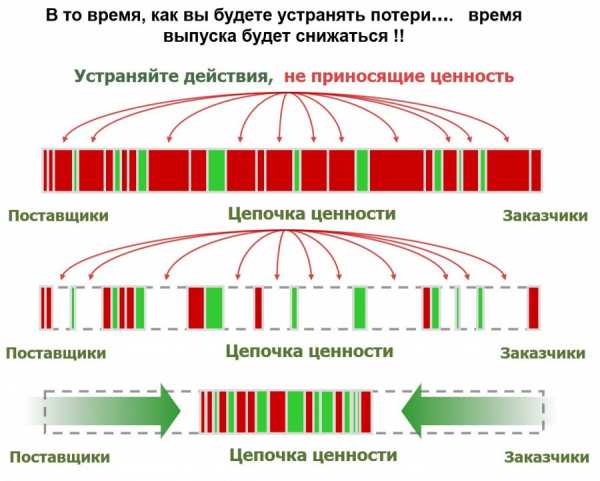
7. Внутрицеховая логистика
Поток создания ценности, а также потоки снабжения по возможности должны двигаться в едином направлении, исключая возвратные и пересекающиеся потоки. Длина путей перемещения также должна быть максимально сокращена. Для этого используется инструмент «Диаграмма спагетти», с помощью которой анализируем все перемещения, после чего решаем, как их оптимизировать.
8. Всеобщее вовлечение в процесс совершенствования
Для того, чтобы устранять 8 видов потерь, этим постоянно должны заниматься все сотрудники компании во главе с первым лицом. Вовлечение в этот процесс первого лица — это ключевое условие успеха.
Для вовлечения очень полезно вот это: Дайджест позитива. Замечания наоборот
Для этого потребуется отказ от культуры порицания в пользу открытого признания проблем. Отказ решать проблемы методом замены людей или методом «найти и наказать виновных».
Иначе ваш процесс совершенствования поломается о то, что ваши сотрудники будут упорно совершенствовать только свою незаменимость.
Как это выглядит на практике: «2-секундный Лин. Как вырастить персонал и весело создать Лин-культуру», Пол Эйкерс
Или так: «Пятнадцатый камень сада Рёандзи», 1986 г, Владимир Цветов — Про менталитет японцев
Ключевая особенность совершенствования — непрерывность. Нельзя перестроить предприятие, а потом к этому вопросу не возвращаться. Проект — это что-то имеющее начало и конец. А процесс совершенствования должен быть вектором.
Как часто нужно тренироваться чтобы быть спортсменом? Постоянно. Как часто нужно повышать свою квалификацию чтобы быть профессионалом? Постоянно.
Также и с производством. Японцы в этом плане впереди всей планеты и у них краеугольный камень: постоянное совершенствование. Нон-стопом десятилетиями.
Как японцы считают порочно: повседневная работа + совершенствование
Как японцы считают правильно: повседневная работа = совершенствование
Совершенствование должно быть неуклонным. Нельзя 1 раз сделать что-то здоровое и жить до 100 лет. Правильный образ жизни нужно поддерживать на протяжении всей жизни непрерывно.
Подробнее про совершенствование: «Кайдзен. Ключ к успеху японских компаний», 1985 г., Масааки Имаи
Совершенствование наращивает определенную рутину: Силы на поддержание системы
Если сделать преобразования и больше к этому вопросу не возвращаться, то произойдет вот что: Предотвращение деградации системы после того, как некий проект будет успешно завершен
Также: Организация рационализаторской деятельности на заводе
9. Иди в гембу (иди и смотри)
Важнейший принцип совершенствования и вовлечения. Он заключается в том, что начальники не должны заниматься развитием предприятия из кабинетов. Они должны идти в цех и смотреть, как выполняется работа. Или идти и смотреть по месту, где происходит брак. Искать причину его возникновения. Японский начальник всегда идет на передовую. Туда, где создается ценность.
Придя на место создания ценности (на гембу) нужно искать корневые причины появления проблем. Не дергать верхушки, а копать до самого корня. Для этого есть метод «5 Почему?». 5 раз или больше под ряд задав вопрос «почему?» рабочему на участке, можно выяснить, «откуда ноги растут». И принять действенные меры. Подробнее: Симптомы: устранить нельзя использовать
Это что касается потока создания ценности. А вообще, проблемы нужно искать не только в гемба, но и в администрации.
10. Ориентированность на процесс, а не на результат
У нас могут похвалить, если ты как-то обманул систему и выкрутился из сиюминутной проблемы. Потырил детали из какого-то другого заказа (который отгружать через 2 дня, а не сегодня), или руками влез в приоритет работы участка изготовления металлических деталей для повторного изготовления каких-то деталей, потерянных на твоем заказе, который сегодня отгружать.
Заказ с грехом пополам отгрузили, и все такие «фух!» выдохнули. Сейчас нужно разобраться, почему так произошло на этом заказе. Как потеряли изготовленные детали, и почему вовремя не приехали покупные. Но подождите-ка! Мы только что забрали детали из заказа, который отгружать послезавтра! Теперь нужно срочно думать, как его отгружать. Кроме того, мы вмешались в приоритет металлического участка, и он теперь работает с запозданием, и с этим тоже нужно что-то срочно делать! Поэтому некогда сейчас заниматься выяснениями, почему так произошло. Да и потом: всё же получилось. Результат же есть. А это — самое главное! (нет)В бережливом производстве нужно именно постоянно совершенствовать процесс, и тогда уже он будет давать стабильный результат.
Подробнее: Почему результата недостаточно [Принцип Деминга №10 — Избегать пустых лозунгов]
11. Система 5S
Для всеобщего вовлечения, а также для повышения производительности труда очень полезен 5S. Когда мы избавились от всего ненужного, разложили все предметы по местам, подписали их места хранения и следим за чистотой и порядком, это очень перестраивает сознание людей. Настраивает их на совершенствование. Также, становятся очень заметны люди, которые не хотят принимать в этом участия.
В Японии никто никогда не гнушался «совершенствованием ради совершенствования» без прямой денежной выгоды. Всё это создает философию, создает дух. Не всё измеряется деньгами. Есть еще и внутренняя энергия системы.
Подробнее:
denis-demakhin.livejournal.com
Принципы бережливого производства
Если ваша компания сталкивается на протяжении долгого периода времени с различными проблемами и не получает достаточный доход за приложенные усилия, то стоит подумать о внедрении бережливого производства на предприятии.
Бережливое производство на предприятии способно не просто изменить ситуацию, немного подкорректировав ее, а полностью поменять уклад, существующий в фирме. И дело не в том, что вы и ваши сотрудники работали плохо. Просто внедрение бережливого производства на предприятии позволит тратить меньше времени на изготовление, сократит брак и увеличит производительность.
- Базовым принципом мышления Бережливого Производства является создание Ценности. Ценность определяется как все те действия, за которые готов платить Потребитель.Действие, создающее ценность должно соответствовать трем следующим критериям:Первое – действие нужно Потребителю.
Второе – данное действие изменяет форму/функцию Продукта/Услуги, тем самым приближая его к финальному состоянию.
И последнее – действие должно быть выполнено без дефектов с первого раза.
Если одно из требований не выполняется, считается, что действие не создает Ценность.
- Следующим принципом Бережливого Производства является устранение потерь.
Муда – термин для потерь. Любое действие, не создающее Ценность, является потерей. Принято выделять 8 типов потерь:- Перепроизводство
- Излишние запасы
- Дефекты
- Действия не создающие ценности
- Ожидание
- Излишние передвижения
- Транспортировка
Неиспользованный потенциал сотрудников
Если рассматривать типичный процесс, можно обнаружить, что все действия, не направленные на создание Ценности, занимают 50% – 90% производственного цикла.
- Принцип непрерывного потока Процесса / движения Продукта и информации от НАЧАЛА до КОНЦА работы. Целью любого Процесса является организация непрерывного движения – Потока – Продукта или Информации от начала до конца.Сложности, препятствующие созданию потока:
- Мура или Неоднородность Потока. Все усилия должны быть сконцентрированы на контроле потока, при выявлении неоднородности, необходимо применить меры.
- Мури, Перезагруженность Потока. Это тот случай, когда Процесс выходит за пределы своих возможностей. Важным является то, чтобы специалисты, работающие с Процессом, осознавали его рамки. Выход Процесса за пределы рамок также повлечет за собой потери.
- Принцип «вытягивания» характеризуется точным представлением о необходимых объемах продукции, что позволяет, в соответствии с ними, предусмотреть необходимый объем сырья, и темп его пополнения; система “вытягивания” также характеризуется малым размером лотов и низким уровнем показателей Незавершенного Производства и Запасов.Система «вытягивания» формирует такой стиль управления, который характеризуется наличием оповещений и сигнальных систем, а также наличием развитой системы коммуникации.
- Высшей целью любого процесса является совершенная эффективность. Решение данной задачи Бережливое Производство видит в создании Невидимого и Безупречного Потока Производства без Потерь.
Основные инструменты Бережливого Производства включают:
- Метод 5 S (Отбор, Организация, Порядок, Стандартизация, Дисциплина, (+1) Безопасность).
- Устранение Муды или Потерь.
- Определение необходимого времени такта или темпа Процесса.
- Создание и использование системы Канбан (сигнальной системы) для сокращения Незавершенного Производства и Потерь.
- Использование метода Пока Йоке (Система “Защиты от Ошибок”) для выявления ошибок «на корню».
- Создание равномерного потока сырья/информации.
- Сокращение временных затрат на пересмены до нескольких минут (вместо часов).
- Использование метода Андон или визуальной сигнальной системы для обозначения того, что станок требует внимания
sixsigma.ru
Введение в Бережливое производство — Психология бизнеса и саморазвития
История бережливого производства
Развитие торговли, рынка капитала, формирование институтов частной собственности, повсеместный переход от подневольного к наемному труду, уменьшение религиозного диктата и многое другое, что происходило на рубеже 18–19 веков, сформовало благодатную почву для промышленной революции. Повсеместно отрывавшиеся новые производства разрушили монополии средневековых гильдий, разнообразных торговых ассоциаций и прочих почетных компаний. Множество ремесленных мастерских начали активно конкурировать между собой, что давало дополнительный толчок индустриальному развитию, но заставляло все больше задумываться о путях снижения себестоимости. Обостренная конкурентная борьба и растущий потребительский спрос определили, фактически, переход от кустарной ремесленной мастерской к массовому промышленному производству. В начале 20 века Генри Форд придумал прорывную, на тот момент, технологию — конвейер. В погоне за снижением себестоимости производства начали укрупняться, выпускаемые продукты — унифицироваться, обеспечение непрерывности работы конвейера вынуждало запасаться большими партиями сырья и материалов, в свою очередь готовая продукция также отгружалась огромными партиями на склады продавцов для последующей перепродажи.
На другой стороне земного шара, в послевоенной Японии, компания Тойота стала возобновлять производство грузовиков и легковых автомобилей. Тяжелые военные годы заставляли руководство экономить на всем. Компания выпускала сильно упрощенные модели, в целях экономии на некоторые модели ставилась всего одна фара. Культура бережливого подхода к производству получила свое развитие в послевоенный период становления компании. Молодой инженер компании Тайити Оно, в отличие от американских коллег, уделял большее внимание не экономии на масштабах, а на выявлении разнообразных непроизводственных потерь. Начиная с 1950 годов он разрабатывал и внедрял в компании Тойота системы организации производства «Канбан», принципы бережливого производства «Lean», концепцию «Точно в срок» (just-in-time). Все эти новшества дали существенные конкурентные преимущества компании. В 1960-ые годы компания Тойота активно завоевывала американский рынок, и новые производственные концепции оказались очень эффективны, даже там, где долгие годы балом правили принципы массового производства.
Конкуренты пристально наблюдали за Тойотой и ее производственной системой. Информация не была секретной, компания учила своих партнеров, местных поставщиков, розничных продавцов и т.д. Триумф японских производителей плохо отражался на бизнесе американских автомобильных гигантов. В начале 80 годов ассоциация американских производителей серьезно озадачилась проблемами отрасли и создала научный консорциум (PVMI) на базе Массачусетского технологического института, во главе которого стали Джеймс Вумек, Даниель Джонс и Даниэль Рус (J. Womack, D. Jones and D. Roos). Своими исследованиями они поделились не только в научной среде, но и опубликовали книгу — «Машина, которая изменила мир». Именно в этой книге впервые был использован термин Лин (Lean, в переводе постный, стройный) для описания принципов производства, разработанных в компании Тойота. Данный термин достаточно сложно перевести буквально на русский язык, и в русскоязычной литературе устоялся термин — Бережливое производство. Можно сказать, что эпоха Бережливого производства в том виде, каком мы его знаем сегодня, началась с этой книги, которая фактически стала чуть ли не библией Бережливого производства (Lean Production) сегодня.
Принципы Бережливого производства
Американские автомобильные производители начала 20 века применяли простой затратный метод ценообразования — метод полных издержек. Производитель суммировал все свои затраты на производство и добавлял к этому определенный процент — норму прибыли. Потребитель уже, в свою очередь, своим кошельком голосовал насколько цена соответствует потребительским качествам и привлекательна на фоне конкурентов. Для анализа потребительских предпочтений активно стали использовать социальные опросы, а для снижения цены — увеличение массовости производства. Японские производители, которые выходили на американский рынок, должны были предложить потребителю машину лучше и за меньшие деньги. Тойоте пришлось применять ценообразования по методу предельных издержек. Для определения предельной розничной стоимости бралась цена аналогичной американской машины, из этого вычиталась минимальная норма прибыли, а все что останется — должно было хватить на производство машины, которую потребитель оценит лучше американской. В таких условиях культура рационального подхода к издержкам оказалась более чем востребованной. Экономить нужно было буквально на всем.
Создатель системы бережливого производства Тайити Оно, иногда приходил цех, становился по центру, чертил вокруг себя круг и стоял так практически весь день наблюдая и записывая все идеи, где он видел растраты и потенциал для оптимизации. В системе Бережливого производства такие растраты традиционно называются японским словом «муда» (с японского потери). Под мудой подразумевается любая деятельность, не приносящая ценности для клиента. Непрерывная борьба по сокращению потерь — это, наверное, основа Бережливого производства. В традициях американского массового производства большие складские запасы считались рачительным ведением хозяйства: чем больше закупаемая партия — тем большую можно получить скидку, чем больше партия готовой продукции — тем лучше загружен конвейер, тем ниже себестоимость производства и т.д. Японцы проанализировали затраты на поддержания высоких складских запасов и посчитали, что это, наоборот, потери, а переход на регулярные маленькие закупки материалов, концепция «Точно во время», позволяет снизить затраты. Все растраты принято классифицировать на семь категорий, и помимо повышенных складских затрат, там есть еще брак, производственные простои, транспортировка, лишние движения, так и избыточная сложность продуктов и перепроизводство.
Для того, чтобы научиться различать затраты в концепции Бережливого производства, нужно научиться определять, что именно является ценным для клиента. В те времена автопроизводители уже активно использовали техники социальных опросов при разработке новых моделей. На потребителей обрушивались миллионы вопросов и они старались, как могли, отвечать, чтобы они хотели иметь в своей новой машине. Автопроизводители это реализовывали в новых версиях, а вот потребители не всегда потом покупали то, что отмечали в предыдущих опросах. Японцы использовали для разработки новых продуктов не принцип потребительских желаний, а концепцию потребительской ценности. Ценностью является только то, что клиент хотел бы видеть в своей машине и готов за это заплатить. Функциональность, которую хотелось бы иметь в машине, но в которой потребитель не видит никакой ценности — смело можно отнести к потерям, в концепции Lean это избыточное производство. Получается, что основа концепции Лин — это умение определять что именно добавляет потребительскую ценность в продукте, а что просто издержки.
Поняв потребительскую ценность, можно и нужно проанализировать весь поток ее создания. Таким образом, мы сможем выявить огромный пласт работ, которые мы делаем по каким-то причинам, но они никак не влияют на создание потребительской ценности. Многие из этих процессов вспомогательные, обслуживающие, от которых просто так не откажешься, но, регулярно переосмысливая и анализируя весь бизнес-процесс, можно всегда найти потенциал к улучшению. И только после того, как мы определили потребительские ценности, проанализировали поток их создания, мы можем вернуться к выявлению непроизводственных растрат. Понятно, что перевозка материалов, сама по себе, не создает ценности для клиента, но, взглянув на весь поток, можно попробовать найти решение, при котором материалы будут перевозиться с места на место 2–3 раза, а не 10 и более, как это было раньше. Оптимально расставленное оборудование, которое уменьшает время хождения сотрудников между станками, может сэкономить достаточно много времени и сил. Своевременное обслуживание оборудования может снизить вынужденный простой и т.д. Сейчас концепция Бережливого производства обросла множеством методов и техник, которые имеют свои названия, и для каждого типа растрат есть накопленный опыт и методики их сокращения.
Борьба со складскими запасами, переход на работу «точно во время», концепции быстрой перенастройки оборудования — все это нас подводит к одной из ключевых идей Лин продакшн — принципу вытягивания. Для того, чтобы не затоваривать склад готовой продукции, нужно стремиться к тому, чтобы производить товар максимально быстро тогда, когда он точно требуется клиенту. Для примера можно сравнить технологические процессы столовой и ресторана. Первые сначала наготовили сколько планируют продать в течении дня, если меньше, то часть клиентов уйдет в другую столовую, если больше — то в конце дня нужно будет излишки выкинуть. В случая же с рестораном — повар начинает готовить сразу, как только официант приносит заказ. Да, для ускорения времени приготовления, он может использовать полуготовые ингредиенты. В первом случае — это принцип «проталкивания». Произвести партию продукции, а потом «протолкнуть» ее на рынок. Во втором случае — «вытягивания», непосредственно заказ клиента инициирует процесс доставки, вытягивает требуемый продукт. Данный принцип может применяться и к производству, и к дистрибуции товаров. Не всегда возможно организовать по принципу «вытягивания», иногда эффективны какие-то комбинированные стратегии.
Ну, и заключительным принципом Бережливого производства будет то, что это не проект. У данного пути есть начало, но нет конца. Компания, вставшая на путь совершенствования своей деятельности, становится приверженцем данных принципов и продолжает развивать и совершенствовать их все время. В концепции Лин это называется японским словом Кайдзен, которое обозначает непрерывное совершенствование. Кайдзен является одной из техник Бережливого производства, но, помимо этого, внесло и вносит большой вклад в науку бизнес администрирования, а также бизнес-психологии.
Слайды можно скачать тут
orgdev.ru