В данный реестр включены
более 30 предприятий России и Белоруссии, которые изготавливают твердые
древесноволокнистые плиты мокрого и сухого способа производства. Если
вы не нашли свой завод, или хотите внести изменения в каталог
— напишите письмо. Изоплит, ОАО, г. Обоянь, Курской обл Древесноволокнистые плиты мокрого способа производства, ГОСТ 4598-86, твердые, вентиляторы пылевые и стружечные, крыльчатки к станкам ДС-7 и ДС 7-а сайт http://www.izoplit.ru Жешартский фанерный комбинат, ооо, п. Жешарт, Республика Коми Древесноволокнистая плита средней плотности сайт http://zfk11.ru КДП Новая Вятка, ооо (Вятка-Лес-Инвест) 610013, Кировская обл., Нововятский р-н, г. Киров, ул. Коммуны, 1 тел.: (8332) 31-78-23, 31-78-51, 31-77-06, Факс: (8332) 31-77-06, 31-73-48 сайт Княжпогостский
завод ДВП (Woodway Group)
Кроностар, г. Шарья Костромской
обл. Лесплитинвест, Ленинградская область, г. Приозерск толщины 8, 10, 12, 14, 16, 18, 22, 24, 25, 30 мм, шлифованные и ламинированные сайт http://lplit.ru Марийский целлюлозно-бумажный комбинат, г.Волжск, ОАО республика Марий Эл Древесноволокнистые плиты мокрого способа производства ГОСТ 4598-86 сайт http://www.marbum.ru Нелидовский ДОК , ОАО Древесноволокнистые плиты мокрого способа производства ГОСТ 4598—86, твердые 3,2 мм, и мягкие 12 мм сайт http://www.neldok.ru Нововятский лесоперерабатывающий комбинат, ОАО, г.Киров Древесноволокнистая плита, в т.ч. отделанная, МДФ сайт http://www.lpk.ru Новоенисейский лесохимический комплекс Древесноволокнистые плиты сухого способа производства (ТУ 133-31-07-99) и мокрого способ производства ГОСТ 4598-86 сайт http:// www.nlhk.ru Орглит, г. Пермь Древесноволокнистые плиты ТУ 5536-02-43047621-2000 толщиной 3, 2 мм и 6 мм , основной формат 1700 х 2745 мм сайтОтрадновский комплексный лесопромышленный комбинат 624870, Свердловская обл., Серовский р-н, пгт. Восточный (34315) 2-22-22 (коммут) Партнер-Томск,
г. Томск Плиты древесноволокнистые сухого непрерывного способа производства, плиты древесноволокнистые средней плотности сайт http://www.pspcom.ru Полеко,
Подосиновский лесопромышленный к-т, ОАО, пос.
Демьяново, Подосиновского р-на Кировской обл. тел (83351)1-13-90, 5-21-00 сайт
Римбунан Хиджау МДФ, ооо Древесноволокнистые
плиты МДФ/ТХДФ различной толщины ТУ 5536-001-98102991-2012,
форматы 1220 х 2440, 1830 х 2440 мм (по заказу до 2750 х 2070 мм),
толщины от 1,5 до 38 мм 680000, Россия, Хабаровский край, Хабаровск, ул.Фрунзе,22, офис 9-12 Тел. (4212) 75- 55-66, Факс: (4212) 75-55-70 Плиты древесноволокнистые мокрого способа производства, ГОСТ 4598-86. твердые сайт http://suhona.com Туринский целлюлозно -
бумажный завод, ЗАО, г.Туринск,
Свердловская обл сайт http://www.tcbz.ru Уфимский фанерно-плитный
комбинат, ОАО (подразделение холдинга Башлес) сайт http://bashles.ru/holding/ufpk Шекснинский КДП, г. Шексна Вологодской обл. Древесноволокнистая плита средней плотности (ПСП) согласно ТУ 5536-026-00273643-98 выпускается размером 2440х1830, толщины 10,16,18,24 мм, класс эмиссии Е2. По качеству поверхности подразделяется на 1,2 и 3 сорта сайт http://www.skdp.ru Юг, ОАО,
п. Мостовской, Краснодарский край Б е л о р у с с и я Борисовский ДОК, ОАО , г. Борисов, Минская обл. Плиты древесноволокнистые сухого непрерывного способа производства. Основные форматы: 2440х1220; 2440х1830; 2440х1845; 2440х2050; 2500х1230 мм, толщины: 2,5; 3,0; 3,2; 3,6 сайт http://www.borisovdok.by Борисовдрев, ОАО, г. Борисов, Минской обл сайт http://www.borisovdrev.by Бобруйский завод ДВП сайт http://bzdvp-by.all.biz Мостовдрев, Белоруссия, Гродненская обл., г. Мосты Плита МДФ/ХДФ длиной 2620, 2800, 3660мм, шириной 1830, 2070 мм и толщиной 2,5-40 мм, шлифованная и ламинированная. сайт http://mostovdrev.by Витбскдрев, ОАО, г. Витебск, Белоруссия Древесноволокнистые плиты ГОСТ 4598-86 марки ТС, формат 2745х1700 мм, толщина 3.2 мм сайт http://www.vitebskdrev.com Китайско-итальянские линии для пропитки декоративных и технических бумаг для ламинирования составил Абушенко Александр Викторович, |
www.c-a-m.narod.ru
Производство и производители ДВП в России
Производство ДВП и ДСП – материалоемкая отрасль, поэтому производственный цикл начинается с подготовки основных компонентов. В качестве наполнителя для двп используются всевозможные древесные отходы и некондиционный лес. Помимо этого, для составления смеси может применяться бумажная макулатура, конопляная и льняная костра, стебли кукурузы, а также хлопчатника, и даже бамбука. Естественно, что для заводов, построенных в России, последние два компонента являются экзотикой и практически не используются.
После промывки в чанах со специальными барабанами, необходимыми для отделения посторонних минеральный примесей (песок, гравий, глина и пр.) и магнитной сепарации, сырье проходит несколько стадий измельчения:
- Сначала проводится обработка на специальных рубильных станках, где крупные фрагменты превращаются в щепу.
- Полученная стружка поступает на вибросепаратор для разделение на фракции.
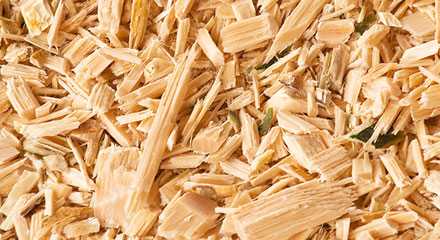
Затем смеси предстоит дальнейшее размалывание на дефибрерах и рафинерах. Конечной целью этого процесса является получение однородной волокнистой массы, которая подсушивается до оптимальной (предусмотренной рецептурой) степени содержания влаги.
Составление рецептурной смеси
Подготовленное сырье шнековыми направляющими отправляется в бункер, где соединяется со связующим веществом. В качестве последнего могут выступать как фенолформальдегидные смолы, так и менее токсичные карбамидоформальдегидные смолы, а также природный лигнин.
Помимо клея, в массу на данной стадии могут добавляться иные ингредиенты, улучшающие некоторые свойства конечного продукта.
Производство водостойкого ДВП подразумевает добавки парафиновых эмульсий, канифоли или церезиновых композиций, которые обволакивая древесные волокна, придают плитам гидрофобность.
Кроме того, введение парафина придает готовым листам ДВП и дсп блеск и предотвращает излишнее налипание массы на оборудование для производства ДВП при прессовании.
Чтобы повысить сопротивляемость готового материала гниению, производители добавляют в состав для прессования различные антисептики, препятствующие развитию микроорганизмов. Также могут добавляться и антипирены – средства, повышающие огнестойкость древесно-волокнистой плиты.
Формирование ковра и прессование
Технология производства ДВП может предусматривать мокрое и сухое прессование, при этом в дальнейшей обработке полученной массы имеются значительные различия.
Мокрый способ прессования
Производство ДВП мокрым способом подразумевает выработку суспензии древесноволокнистой массы определенной концентрации. Для этого волокно после размола разбавляется водой и собирается в бассейн, создавая рабочий запас пульпы. Влажная масса подается на отливочные машины, которые формируют на сетке так называемый ковер, разравнивая сформированный пласт прижимным роликом. После формирования часть воды отсасывается вакуумом и ковер поступает на подпрессовку.
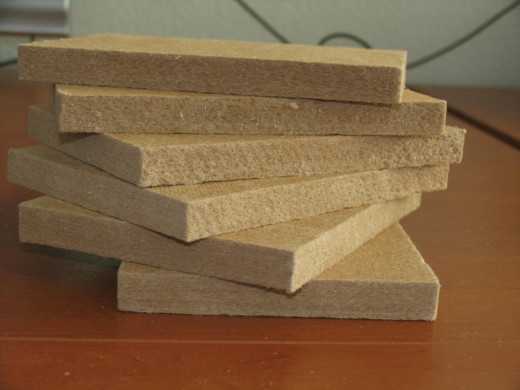
Прессование плит – ответственная операция, от которой значительно зависит качество готовой продукции. Оборудование для производства ДВП – многоэтажный пресс, который позволяет выполнить трехфазный цикл прессования при температуре плит 180-200°С:
- отжим воды под давлением 2÷4 мПа;
- сушка под давлением 0,8÷1мПа;
- закалка под давлением 2÷4 мПа.
Именно от производительности пресса зависит мощность завода, а его стоимость составляет около 30% от всех затрат на оборудование для производства ДВП.
Для улучшения прочностных свойств полученных плит их можно дополнительно пропитывать талловым маслом, помещая в камеры с циркулирующим горячим воздухом.
Большинство заводов в России работает по методу мокрого прессования. Отличительная особенность такого ДВП – сетчатая оборотная сторона листа.
Сухой способ прессования
При сухом способе древесные волокна, смешанные с клеем, настилаются на сетку, через которую в вакуумных установках отсасывается воздух и масса уплотняется. Свойлоченный ковер поступает на прессование. Благодаря отсутствию воды, продолжительность стадии прессования сокращается более чем в два раза. По этому методу можно вырабатывать ДВП толщиной до 30 мм, а также профилированные листы ДВП.
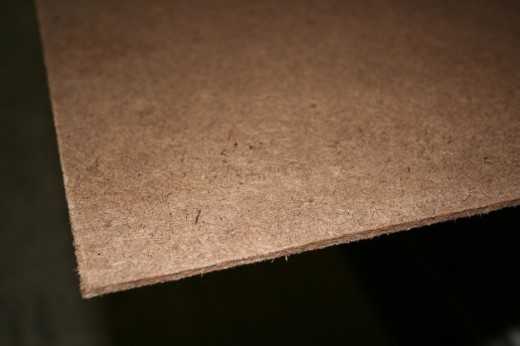
Этот способ в России менее распространен, так как сухое производство имеет весьма существенные недостатки, а именно:
- высокую пожароопасность предприятий;
- образование большого количества древесной пыли и, как следствие этого, производство требует приобретения дорогостоящих циклонов для ее улавливания.
Основные производители ДВП
К сожалению, благодаря тому, что в последнее время появилось множество кустарных мини-заводов, на которых производство ДВП выполняется без надлежащего лабораторного контроля за качеством готовой продукции, рынок заполнен второсортным ДВП.
В России можно назвать несколько предприятий, обладающих значительным опытом в производстве древесных плит:
- ЗАО “Изоплит” (Курская область) уже более 45 лет занимается производством листов и деталей ДВП.
- Одним из крупнейших производителей является также Княжепогостский завод ДВП (республика КОМИ).
- ЛПК “Полеко” (Кировская область) производит продукцию на лигнине, отвечающую жестким требованиям западноевропейских стандартов, благодаря чему она реализуется не только в России, но и импортируется за рубеж.
- ДВП “SteelBoard” позиционируются производителем, как материал, имеющий уникальный среди древесных плит коэффициент водопоглащения и разбухания.
drevplity.ru
Технология производства ДВП (древесноволокнистых плит)
Читатель знает, что в настоящее время изготовляются плиты из измельченной древесины разных типов, наибольшее значение из которых имеют древесностружечные и древесноволокнистые плиты. Древесноволокнистые плиты выпускают нескольких видов: твердые и сверхтвердые мокрым способом, твердые сухим способом, мягкие. У них есть общие операции, но имеются и принципиальные различия в технологии, которые автор будет отмечать.
Как правило, сырьем для древесноволокнистых плит служит щепа, которую можно изготовлять непосредственно в цехе или привозить со стороны. До подачи в производство щепу промывают для удаления минеральных «примесей (песка, камней, глины), а также производят магнитную сепарацию для извлечения из нее металла. Щепу хранят в бункерах, откуда она поступает в машины для размола на волокно. Известны и применяются машины для первой, грубой) ступени размола, так называемые дефибраторы, и для второй ступени, где производится более тонкий помол, рафинаторы.
Волокнистая масса при необходимости более тонкого измельчения непосредственно из дефибратора или из бассейна поступает в рафинатор, у которого в отличие от дефибратора нет камеры прогрева. Размольная его часть примерно такая же, как у дефибратора. Часто при размоле в волокно вводят добавки: парафин для увеличения водостойкости плит, синтетические смолы для получения нужной их прочности. Введение смолы практикуется при производстве древесноволокнистых плит сухим способом. Здесь нужно обратить внимание на то, что далее процессы производства плит сухим и мокрым способом расходятся.
При мокром способе волокнистая масса низкой концентрации поступает в бассейн, где создается запас массы и происходит ее проклеивание водоотталкивающими веществами. Из бассейна масса подается на отлив ковра. Это важнейшая операция. Главная функция операции отлива — формирование ковра равномерной плотности. Для ее выполнения необходимо подавать на отлив волокнистую массу равномерной концентрации (это делается с помощью специальных регуляторов). Количество подаваемой массы в единицу времени должно быть постоянным. Для этого имеются специальные напорные баки. В современном производстве древесноволокнистых плит на большинстве предприятий применяются отливные машины непрерывного действия (рис. 32).
Рис. 32. Схема отливной машины:
I — напускной ящик; II — регистровая часть; III —отсасывающая часть; IV — прессовая часть; V — обрезка ковра; 1 — сетки; 2 — пила; 3 — направляющие ролики; 4 — приводные барабаны; 5 — древесноволокнистый ковер
Окончательное формирование плиты происходит при прессовании. Пресс — сложная, громоздкая и дорогостоящая машина. В производстве древесноволокнистых плит используются, как правило, многоэтажные прессы периодического действия. Обогреваются плиты горячей водой (температурой до 230°С), приготовляемой в аккумуляторе. Высота его до 10 м и диаметр до 2,5 м. Современные прессы с усилием 70000—75000 кН имеют до 10 плунжеров диаметром по 700—800 мм каждый. В прессах имеется 20—30 рабочих промежутков, в которые заталкиваются поддоны с мокрыми коврами (рис. 33). Прессование происходит при давлении 3—5 МПа и температуре 210—230° С. Продолжительность цикла прессования 8—11 мин (в зависимости от толщины плиты, влажности ковра, наличия в ковре смолы и т. п.).
Ввиду того, что производительность пресса определяет производительность завода, а стоимость его доходит до 20% стоимости всего оборудования, были проведены разработки с целью резкого сокращения продолжительности прессования и тем самым увеличения производительности пресса. Так появился сухой способ производства древесноволокнистых плит. Он во многом отличен от мокрого способа. При сухом способе волокно после размола не разбавляется водой, а наоборот, высушивается и настилается в сухом виде тоже на сетку. Отсасывается не вода, а воздух, благодаря чему ковер уплотняется. Затем он подпрессовывается, обрезается, раскраивается на отдельные форматы, которые поступают в пресс. Для повышения качества плит в волокно вводится смола (как правило, фенольная), а также водостойкие и другие добавки. Здесь это выгодно делать, потому что смола и добавки водой не вымываются, и это относится к достоинствам сухого способа. Благодаря тому, что волокно сухое, продолжительность прессования уменьшается в 2—3 раза, соответственно увеличивается и производительность завода в целом. Максимальная производительность заводов, работающих по мокрому способу, достигает 15 млн. м2 плит в год, а по сухому способу — 25 и даже 30 млн. м2 в год. При сухом способе можно делать плиты толщиной даже 12— 15 мм, а также изменять плотность плит. При мокром способе плотность твердых плит равна 1000—1100 кг/м3, при сухом 900—1100 кг/м3 и меньше указанной величины, а при необходимости и больше.
Рис. 33. Общий вид гидравлического пресса с околопрессовой механизацией:
1 — пресс; 2 — загрузчик; 3 — разгрузчик; 4 — конвейер возврата транспортных листов с сетками; S — конвейер для готовых плит; 6 — пила для резки ковра
Читателю будет, очевидно, интересно узнать, что сухим способом можно делать древесноволокнистые плиты толщиной до 20—30 мм средней плотности (700—800 кг/м3). Это крупное достижение технологии деревообработки: такие плиты, изготовленные из волокна, имеют очень хорошую поверхность, высокую прочность, легко обрабатываются и поэтому из них можно изготавливать высококачественную мебель.
Сухой способ имеет два крупных недостатка, ограничивающие его распространение, — повышенную запыленность окружающей среды и высокую пожарную опасность. Для улавливания пыли, образующейся при производстве плит, приходится строить дорогостоящие установки, которые сложней и дороже сооружений для очистки сточных вод в производстве плит мокрым способом. Для предотвращения возгорания волокна необходимы специальные сложные автоматически действующие устройства.
Итак, после прессования (обоими способами — мокрым и сухим) получаются твердые плиты, которые обрезают с четырех сторон. При этом легко узнать, каким способом изготовлена плита. При сухом способе обе стороны плиты гладкие, при мокром способе на одной стороне плиты остается отпечаток сетки. Это и понятно, поскольку при прессовании сухого ковра нет нужды в сетке, через которую отжимается вода при прессовании мокрого ковра.
После обрезки твердые древесноволокнистые плиты проходят операцию закалки. Назначение ее в завершении начатых в прессе процессов термохимических превращений компонентов древесного волокна. Закалка повышает прочность плит и уменьшает водопоглощение. Температура закалки 160—170° С. Скорость воздуха, омывающего плиты, 4—5 м/с, продолжительность закалки — до 4 ч. Проводят закалку в специальных камерах.
Из камеры закалки плиты выходят практически с нулевой влажностью. Они активно впитывают влагу из воздуха. При укладке в пакет края плит поглощают намного больше влаги, чем середина, что приводит к их короблению. Поэтому проводится специальная операция увлажнения плит в камерах непрерывного действия или барабанного типа. Плиты в камерах находятся 6— 7 ч при 65°С и влажности воздуха 95%.
В заключение — несколько цифр. В СССР действуют, заводы по производству древесноволокнистых плит мокрым способом в основном мощностью 10 и 15 млн. м2 плит в год, или 30 и 50 тыс. т в год. На 1 т плит (примерно 300—350 м2) расходуется до 3 м3 древесины и до 20 т воды. На одном заводе работает до 500 человек разных профессий. Сложность оборудования диктует необходимость в рабочих высокой квалификации. Выделяются рабочие, обслуживающие рубительные машины, размольное оборудование, отливную машину, пресс, камеры закалки, а также рабочие по техническому надзору за оборудованием и его ремонту.
www.stroitelstvo-new.ru
Древесноволокнистые плиты (Производители ДВП) — общая информация
Производители ДВП на сегодняшний день занимают всё большую нишу на рынке строительных и отделочных материалов.
Производители ДВП изготавливают широкий спектр товаров, начиная со строительных материалов, заканчивая бытовыми нуждами. В строительном комплексе ДВП наиболее востребованы. Их используют как для жилищного, так и для промышленного строительства.
Среди сфер применения материала производители ДВП выделяют следующее:
1. Теплоизоляция и звукоизоляция кровли;
2. Изготовление междуэтажных перекрытий;
3. Непосредственная отделка стен, потолков и в целом отделочные работы помещений;
4. Укладка паркета и паркетной доски;
5. Изготовление дверей;
6. Производство внутренних деталей мебели и проч.
В основном, производители ДВП создают продукт из отходов деревообрабатывающего и лесопильного комплекса. Остатки древесного пиломатериала расщепляют и специальным прессом прессуют их в плиты. После процесса прессования производится сушка уже готового материала. Кроме того, сегодня получил распространение способ изготовления листов ДВП непосредственно из бумажной макулатуры. Благодаря имеющимся технологиям производители ДВП способны сделать прочный и стойкий материал, который может качественно прослужить длительный срок. Средний срок эксплуатации ДВП составляет от 30 до 35 лет, в зависимости от эксплуатационных условий.
Если рассматривать процесс изготовления плит более подробно, то производители ДВП действуют следующим образом:
В уже готовую волокнистую массу вводятся специальные растворы, осадители и эмульсии. Сразу же после этого волокнистая масса попадает в отливочные машины, где производится отливка материала. После этой процедуры волокнистая масса имеет очень большую влажность — от 70%. Полутвердые и твердые плиты ДВП попадают на горячие пресса. Температура прессования варьируется в диапазоне от 135 до 180 градусов по Цельсию. Прессуются только твердые плиты ДВП. Если речь идет об изоляционном листе ДВП, то он проходит непосредственную сушку в специальных сушильных камерах с пониженным процентом влажности. Твердые листы ДВП после прессования необходимо увлажнить приблизительно на 5 или 7%, в зависимости от массы.
Средняя толщина листа ДВП от 3 до 8 миллиметров. Размеры могут варьироваться: от 1200 до 3600 миллиметров по длине, и от 1000 до 1800 соответственно по ширине.
Листы древесноволокнистые производятся путем горячего прессования плиты или сушки, в зависимости от предназначения материала. При необходимости производители ДВП в волокнистую массу вводят специальные связующие элементы в виде смол и специфических добавок. Это могут быть вещества для улучшения эксплуатационных свойств и характеристик. К таким веществам можно отнести парафин, канифоль (гидрофобизующие вещества для увеличения прочностных характеристик). Используют некоторые виды синтетических смол и антисептиков непосредственно для увеличения прочности материала.
Производят ДВП двумя способами. Если производится сухой сбор древесины, то при непосредственном измельчении в состав вводится от 4 до 8% специальной синтетической смолы. Это обеспечивает достаточную плотность и прочность материалу. При сухом сборе, перед попаданием под пресс волокнистую массу тщательно высушивают. При мокром сборе смолу не используют.
На сегодняшний день на территории России производители плит ДВП работают более чем на 50 линиях.
Производители ДВП в Перми
permdsk.ru
ДВП — «Сибирь ТД» — Фанера, ЛДСП, МДФ, ДВП
ДВП (Древесно- волокнистая плита ) – листовой материал, который изготавливается путем горячего прессования или сушки древесных волокон с добавлением связующих веществ и специальных добавок в зависимости от требуемых параметров.
Существует 2 способа производства ДВП:
- сухой – требующий введения в измельченную древесину синтетической смолы
- мокрый – без добавки связующего вещества.
Преимущества:
- Высокое качество, широкое практическое применение, однородные состав и плотность.
- Идеальные характеристики при механической обработке и возможность получения различных профилей.
- Заменитель натурального дерева, альтернатива в отношении фанеры и столярных плит.
- Легко режется, сверлится, фрезеруется, имеет гладкую поверхность.
Древесно-волокнистые плиты, ДВП | ||||||||||||
наименование | формат | листов в м3 | S листа, м2 | поверхность | цена | |||||||
ДВП | 2,5*1700*2750 | 85,72 | 4,667 | 1ст | 260 | |||||||
ДВП | 2,5*1220*2440 | 137,37 | 2,977 | 2ст | 210 | |||||||
ДВП | 3,2*2050*2440 | 62,48 | 5,002 | 2ст | 340 | |||||||
ДВП | 5,0*1220*2710 | 50,23 | 3,318 | 2ст | 350 |
Остались вопросы? Звоните!
тел.: 242-18-20
Область применения:
- в строительстве для звуко- и теплоизоляции
- производство мебели
- отделка помещений
- изготовление междуэтажных перекрытий, стен
- при укладке линолеума, паркета, паркетной доски
www.xn--90afmb4bcf0g.xn--p1ai
Производство ДВП (древесноволокнистых плит)
Началом организации в Советском Союзе производства древесноволокнистых плит (двп) следует считать 1936—1937 гг., когда были сданы в эксплуатацию Ново-Белицкий завод (БССР) и Московский завод, однако дальнейшее развитие производство древесноволокнистых плит (двп) в СССР получило в послевоенный период.
Дальнейшее увеличение производства, намечаемое к 1970 г. до объема 300 млн. м2 плит в год, будет осуществляться за счет строительства крупных предприятий, для чего в настоящее время разрабатываются типовые проекты на строительство предприятий по производству древесноволокнистых плит (двп) как мокрым, так и сухим способом мощностью 10, 20 и 40 млн. м2 в год.
Действующие и проектируемые предприятия, как правило, будут в составе крупных лесопильно-деревообрабатывающих или целлюлозно-бумажных комбинатов.
Являясь индустриальным, эффективным, плитным материалом, производство которого не требует деловой древесины и таким образом способствует максимальному использованию заготовляемой неделовой древесины и отходов лесопильно-деревообрабатывающего производства, древесноволокнистые плиты (двп) нашли широкое распространение во всех отраслях промышленности и строительства за рубежом.
Изоляционные ДВП применяют в строительстве для утепления наружных стен в малоэтажном сборном домостроении и для звукоизоляции; полутвердые и твердые — как отделочный материал для внутренней обшивки стен, перегородок и потолков, а также для устройства полов, отделки санитарно-технических узлов, изготовления дверей щитовой конструкции, встроенной и кухонной мебели и пр. В зависимости от назначения плиты пропитывают синтетическими смолами и отделывают эмалями.
Малый объемный вес, большие размеры плит и отсутствие линейных усадок делают изоляционные плиты первоклассным материалом для утепления стандартных щитовых домов.
Эффективность применения твердых плит для внутренней отделки зданий взамен обычной штукатурки исключает сезонность этих работ, значительно увеличивает производительность труда (в 10—15 раз) и снижает стоимость этих работ (в 2—2,5 раза). Использование плит, покрытых эмалями, взамен керамических для отделки кухонь и санитарных узлов в 3—3,5 раза снижает стоимость и в 5 раз трудоемкость этих работ.
При изготовлении щитовых дверей с облицовкой твердой древесноволокнистой плитой отпадет надобность в высококачественном хвойном пиломатериале, расход которого при изготовлении филенчатых дверей составляет 0,07—0,08 м3/м2.
ГОСТ 4598—60 предусматривается выпуск древесноволокнистых плит пяти видов в зависимости от объемного веса:
Виды ДВП | с объемным весом (кг/м3) |
---|---|
изоляционные | до 250 |
изоляционно-отделочные | от 250 до 350 |
полутвердые | не менее 400 |
твердые | 850 |
сверхтвердые | 950 |
Для производства двп могут быть использованы тонкомерная древесина и отходы лесопильно-деревообрабатывающего производства как хвойных, так и лиственных пород.
Кроме древесины сырьем для производства древесноволокнистых плит могут служить стебли однолетних растений (камыш, солома, кенаф, костра и др.).
Опилки могут использоваться как добавка к щепе в объеме 15—20% — Технология производства на отечественных заводах Организована по мокрому способу и заключается в следующем.
Древесина в круглом виде или отходы производства (горбыль, срезки и др.) на рубильных машинах измельчаются в щепу, которая сортируется и при помощи ленточных и скребковых транспортеров подается в бункера.
Далее щепа (влажность 40—50%) размалывается на дефибраторах с одновременной пропаркой под давлением 8—12 ат со степенью помола массы 6—8° ШР и разбавляется водой до концентрации 4—6%. Вторичный размол производится в рафинаторах до 10—12° ШР, после чего щепа направляется в массные бассейны. Из бассейнов масса насосами подается в ящик для непрерывной проклейки канифольно-парафиновой эмульсией при изготовлении изоляционных плит и парафиновой эмульсией или смолой при изготовлении твердых плит.
Формовка плит производится на длинносеточной или круглосеточной отливочной машине.
При изготовлении изоляционных плит дальнейшей операцией является сушка плит в роликовых сушилках до влажности 1—3% и раскрой на заданные размеры.
При изготовлении полутвердых и твердых плит массный ковер разрезается на размеры плит пресса (1200X5400), которые подаются на загрузочную этажерку пресса. Прессование производится при температуре плит 180—190° и давлении 50— 55 кгс/см2. Готовые плиты после выхода из пресса обрезаются и подвергаются термообработке и увлажнению.
Отделка древесноволокнистых плит (ДВП) производится путем:
покрытия лицевой поверхности плит слоем пигментированной массы методом налива на сырое полотно в процессе производства;
облицовки плит бумагой, синтетическими пленками и бумажно-слоистыми пластиками;
покрытия лаками, красками и синтетическими эмалями;
покрытия текстильными материалами и металлической фольгой.
К технике отделки древесноволокнистых плит следует отнести также перфорирование плит, нанесение на лицевую сторону бороздок и рисунков, имитирующих кожу, текстуру ценных пород древесины и др.
Древесноволокнистые плиты (двп), имеющие высококачественную отделку бумагой, пленками, эмалями и лаками, найдут широкое применение не только в строительстве и мебельной промышленности. Они с успехом будут применяться в автостроении, вагоностроении, судостроении, заменяя дорогостоящую фанеру и другие дефицитные отделочные материалы.
Целесообразно рассказать еще об одном типе древесных материалов. В них древесные частицы связываются не синтетическим клеем, а цементом. Известно много видов таких материалов, но наиболее распространенные и перспективные из древесно-цементных материалов — фибролит, арболит и цементно-стружечные плиты.
www.stroitelstvo-new.ru
Новый раздел
сверхтвердые: СТ-500, плотностью более 900 кг.В зависимости от плотности находится и предназначение указанных марок. Мягкие ДВП в силу малой плотности обладают высокими звукоизоляционными свойствами, что позволяет использовать их для облицовки стен и потолков внутри зданий с нормальной и пониженной влажностью воздуха, а так же, при возведении внутренних перегородок. Кроме того, большие габаритные размеры листов ДВП удобны для устройства выравнивающих слоев пола перед покрытием линолеумом или ламинатом.
В мебельной промышленности мягкие ДВП используются для изготовления задних стенок мебельных шкафов, не имеющих выхода на лицевую поверхность, а так же, в качестве дна ящиков. Для повышения декоративных свойств, они могут быть подвергнуты отделке прозрачными лаками или пигментированными эмалями.
— Твердые ДВП, в силу повышенной плотности и устойчивости к кратковременному воздействию водосодержащих клеевых и грунтовочных смесей, с успехом применяются при оборудовании внутренних помещений жилых и общественных зданий. Ими обшиваются каркасные перегородки помещений, производится выравнивание стен и потолков. При производстве мебели твердые ДВП используются в качестве деталей ящиков, полок и задних стенок шкафов. А при оборудовании ниш и встроенных шкафов могут быть применены как для облицовывания стенок по установленному каркасу, так и для изготовления заполнения рамочных дверей и для малогабаритных полок.Сверхтвердые виды в процессе изготовления дополнительно пропитываются синтетическими смолами, поэтому они отличаются не только высокой плотностью, но и влагостойкостью и применяются для устройства чистовых полов. Как вариант производства – плиты с лакокрасочным покрытием, защищенные водостойкими эмалями или слоем напрессованной полимерной пленки (однотонной или с рисунком, имитирующим природные материалы). Данный вид продукции применяется для внутренней отделки пассажирских вагонов, трамваев, служебных помещений и для изготовления мебели.
Размеры
Листы ДВП при небольшой толщине имеют большие габаритные размеры по длине и ширине, сохраняя в то же время все достоинства древесных материалов: низкую теплопроводность, высокие звукоизоляционные свойства и биологическую безвредность. А еще к достоинствам ДВП следует добавить очень низкую по сравнению с массивом древесины стоимость в пересчете на 1 м3.
Размеры листов определены ГОСТ 4598-86 «Плиты древесноволокнистые. Технические условия» и составляют: — для всех видов мягких плит: длина 3000 + 5мм, 2700, 2500, 1800, 1600 и 1220 мм, ширина 1700 + 5мм и 1220 мм. Толщина у марок М-4 и М-12 составляет 12, 16 и 25 мм, а у М-20 – 8 и 12 мм, — полутвердые плиты представляют собой листовой материал типа толстого картона толщиной 6, 8 и 12 мм, — твердые и сверхтвердые плиты имеют толщину 2,5 мм, 3,2 мм, 4,5 мм и 6 мм, Полутвердые, твердые и сверхтвердые виды имеют следующие габаритные размеры: длина – 3660, 3350, 3050, 2745, 2440, 2140 мм ширина – 2140, 1830, 1525, 1220 мм максимальный размер выпускаемых плит 6100 х 2140 мм
Хранение
На складах компании хранение соответствует ГОСТ 4598-86.
Хранение плит осуществляется в закрытых помещения с влажностью воздуха в пределах 70%.
Пачки плит одинакового размера, марки и предназначения укладываются в штабеля высотой не более 4,5 м. Для защиты от повреждений складочные места оборудуются поддонами и брусками-прокладками для разделения стоп и удобства их транспортировки.
Каждая пачка опровождается биркой, содержащей следующую информацию: наименование продукции, наименование предприятия-производителя и его юридический адрес, ТУ на продукцию, марка плиты, размеры, количество плит в шт. и в м2, дата выработки, номер смены и личный штамп приемщика.
Материалы по теме
fanera-bazar.ru