описание, особенности, принципы и отзывы
Руководитель любого предприятия, независимо от сферы деятельности, мечтает, чтобы прибыль росла, а производственные затраты оставались неизменными. Добиться такого результата помогает система «5С» на производстве (в английском варианте 5S), основывающаяся только на рациональном использовании внутренних резервов.
Создавалась эта система не с чистого листа. Нечто подобное еще в конце XIX века предлагал американец Фредерик Тейлор. У нас в России этим занимался ученый, революционер, философ и идеолог А.А. Богданов, издавший в 1911 году книгу о принципах научного менеджмента. На основе изложенных в ней положений в СССР внедряли НОТ, то есть научную организацию труда. Но наиболее совершенной стала предложенная японским инженером Тайити Оно и внедренная им на заводе Toyota Motor система «5С» на производстве. Что это такое, и почему японская система стала такой популярной?
Дело в том, что в ее основе лежит простой принцип, не требующий затрат. Он заключается в следующем — каждый работник, от уборщицы до директора, должен максимально оптимизировать свою часть в общем рабочем процессе. Это приводит к увеличению прибыли производства в целом и к росту доходов всех его сотрудников. Сейчас эстафету внедрения системы «5С» подхватили предприятия во всем мире, включая Россию. В этой статье мы попытаемся убедить скептиков в том, что японское ноу-хау действительно работает, причем абсолютно в любой сфере деятельности.
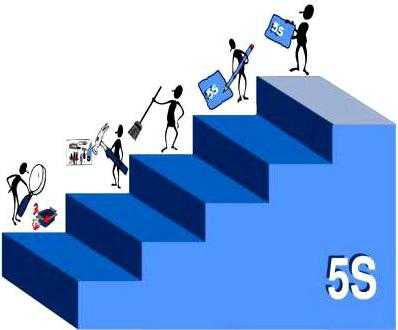
Система «5С» на производстве, что это такое
Международное 5S расшифровывается, как пять шагов («шаг» по-английски step). Некоторые экономисты и пропагандисты нового отношения к труду объясняют название пятью японскими постулатами, последовательно внедряемыми в системе 5S: сэири, сэитон, сэисо, сэикэцу и сицукэ. Для нас ближе и понятнее наши родные «5С» — пять последовательных шагов, которые нужно выполнить, чтобы добиться процветания своего производства. Это:
1. Сортировка.
2. Соблюдение порядка.
3. Содержание в чистоте.
4. Стандартизация.
5. Совершенствование.
Как видим, ничего сверхъестественного система «5С» на производстве не требует. Возможно, именно поэтому к ней пока можно встретить недоверие и несерьезное отношение.

Этапы создания системы
Мудрый японец Тайити Оно, который, благодаря внедрению на заводе по производству «Тойот» своих методик, сумел дослужиться от инженера до генерального директора, обратил внимание, как много потерь происходит из-за различных неувязок и накладок. Например, на конвейер не поставили вовремя какие-нибудь мелкие винтики, и в результате встало все производство. Или наоборот, деталей подали с запасом, они оказались лишними, и в результате кому-то из сотрудников пришлось везти их обратно на склад, а значит, тратить на пустую работу свое время. Тайити Оно разработал концепцию, которую назвал «точно в срок». То есть на конвейер теперь поставлялось ровно столько деталей, сколько нужно.
Можно привести и другие примеры. Система «5С» на производстве также включала в себя концепцию «канбан», что по-японски значит «рекламная вывеска». Тайити Оно предложил на каждую деталь или каждый инструмент цеплять так называемую бирку «канбан», в которой давалась вся необходимая информация по детали или инструменту. В принципе, она применима к чему угодно. Например, к товарам, медикаментам, папкам в офисе. Третьей концепцией, на которой основывается система «5С» на производстве, стало понятие «кайдзен», означающее непрерывное совершенствование. Придумывались и другие концепции, которые подошли лишь для узкоспециализированных производственных процессов. В этой статье мы их рассматривать не будем. В итоге всех опробованных на практике нововведений и сформировалось 5 шагов, применимых к любому производству. Разберем их подробно.
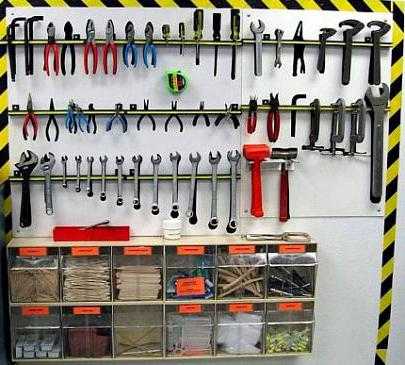
Сортировка
У многих из нас на рабочих столах скапливаются предметы, которые, в принципе, не нужны. Например, старые формуляры, не используемые файлы, черновики расчетов, салфетка, на которой стояла чашка кофе. А среди этого хаоса могут находиться нужные файлы или документы. Основные принципы системы «5С» подразумевают оптимизировать свой рабочий процесс, то есть сделать так, чтобы не тратилось время на поиск нужных вещей среди завалов ненужного. Это и есть сортировка. То есть на рабочем месте (возле станка, на столе, в мастерской – где угодно) все предметы раскладываются на две стопки – нужное и ненужное, от которого необходимо избавиться. Далее все нужное раскладывается на следующие стопки: «используется часто и постоянно», «используется редко», «почти не используется». На этом сортировка закончена.
Соблюдение порядка
Если просто разобрать предметы, толку не будет. Нужно эти предметы (инструменты, документы) разложить в таком порядке, чтобы используемое постоянно и часто очутилось на виду или так, чтобы его можно было быстро взять и легко положить назад. То, что используется редко, можно отправить куда-нибудь в ящик, но к нему нужно прикрепить бирку «канбан», с тем, чтобы через время можно было легко и безошибочно его найти. Как видим, система «5С» на рабочем месте начинается с самых простых шагов, но на деле она оказывается очень эффективной. А кроме того, она повышает настроение и желание трудиться.
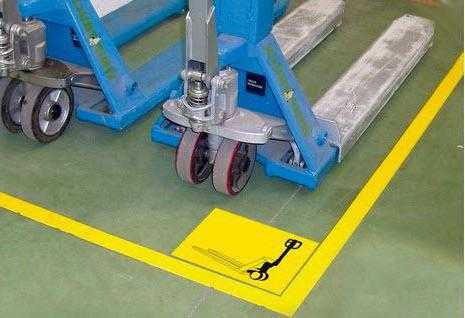
Содержание в чистоте
Этот третий шаг является для многих самым логичным. Соблюдать чистоту нас учат с детства. На производстве она тоже необходима, причем, чистыми должны быть не только столы офисных работников или шкафы в учреждениях общепита, но и станки, подсобные помещения уборщиц. В Японии сотрудники бережно относятся к своим рабочим местам, трижды в день их убирают – с утра перед работой, в обеденный перерыв и вечером, по окончании трудового дня. Кроме того, у них на предприятиях введена специальная маркировка участков, позволяющих соблюдать на производстве порядок, то есть разными цветами отмечены участки готовой продукции, складирования определенных деталей и так далее.
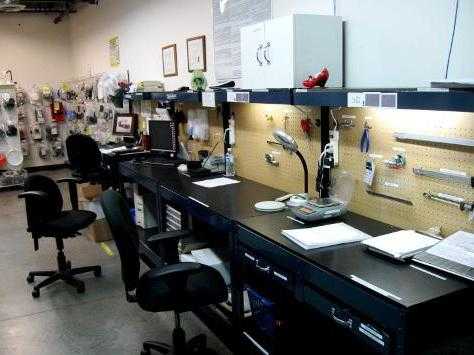
Стандартизация
Принципы стандартизации придумал еще Тайити Оно. Широко использует их и современная система 5S. Управление производством, благодаря стандартизации, получает замечательный инструмент контроля за всеми процессами. В результате быстро устраняются причины отставания от графика и исправляются ошибки, приводящие к выпуску некачественной продукции. На заводе Toyota Motor стандартизация выглядела так: мастера составляли ежедневные планы работ, на рабочих местах вывешивались точные инструкции, в конце трудового будня специальные работники проверяли, какие за день произошли отступления от плана и почему. Это и есть основное правило стандартизации, то есть точные инструкции, планы работ и контроль за их выполнением. Сейчас на многих предприятиях, например, на заводах ENSTO в Эстонии, вводится премиальная система работников, четко выполняющих положения системы «5С» и на основе этого повышающих свою производительность, что является отличным стимулом принять эту систему, как образ жизни.
Совершенствование
Пятый шаг, на котором завершается система «5С» на производстве, основан на концепции кайдзен. Она означает, что все работники, независимо от занимаемой должности, должны стремиться усовершенствовать процесс работы на вверенном им участке. Философская суть кайдзен заключается в том, что вся наша жизнь каждый день становится лучше, а коль работа – это часть жизни, она тоже не должна оставаться в стороне от улучшений.
Поле деятельности тут широкое, ведь пределов у совершенства не существует. Согласно понятиям японцев, работники сами должны хотеть улучшить свой производственный процесс, без указаний и принуждений. Сейчас во многих организациях создаются команды рабочих, следящих за качеством продукции, обучающих своему положительному опыту других, помогающих добиваться совершенства.
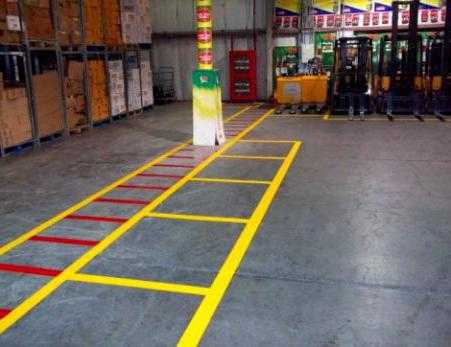
Основные ошибки
Чтобы система «5С» начала работать, мало ее организовать или взять на работу сотрудников, которые будут заставлять своих коллег ее внедрять. Тут важно, чтобы люди осознали полезность этого новшества и приняли его как стиль жизни. Внедрение системы «5С» в России на производстве сталкивается с трудностями именно по причине того, что наш русский менталитет отличается от японского. Для многих наших производств характерно следующее:
1. Работники, особенно если для них нет поощрительных стимулов, не стремятся увеличить прибыль предприятия. Они спрашивают, зачем стараться сделать начальника еще богаче, если у него и так все есть.
2. Сами руководители не заинтересованы во внедрении системы «5С», потому что не видят в ней целесообразности.
3. Многие директивы, «спускаемые сверху», привыкли выполнять только для «галочки». В Японии наблюдается совсем другое отношение к своему труду. Например, тот же Тайити Оно, внедряя систему «5С», думал не о личной выгоде, а о выгоде компании, в которой он был всего лишь инженером.
4. На многих предприятиях внедряется насильно система «5С». Бережливое производство, подразумевающее устранение потерь всех видов (рабочего времени, сырья, хороших работников, мотивации и прочих показателей) при этом не получается, так как работники начинают на подсознательном уровне противиться нововведениям, что в итоге сводит все старания к нулю.
5. Руководители, внедряющие систему, не полностью понимают ее суть, из-за чего возникают сбои в налаженных процессах производства.
6. Стандартизация часто перерастает в бюрократию, хорошее дело обрастает указаниями и директивами, которые только мешают работе.
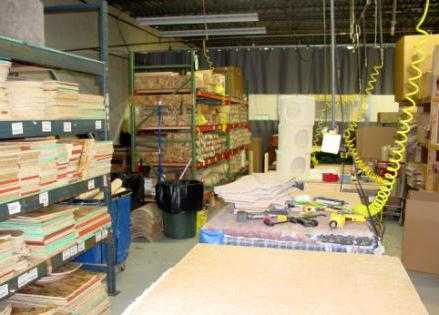
Отзывы
Россияне, у кого введена система «5С» на производстве, отзывы об этом новшестве оставляют весьма неоднозначные. Отмечаемые плюсы:
- приятнее находиться на рабочем месте;
- не отвлекают от работы ненужные мелочи;
- более четко идет рабочий процесс;
- снизилась усталость в конце смены;
- немного возросла зарплата за счет увеличения производительности труда;
- снизился производственный травматизм.
Отмечаемые минусы:
- проводя сортировку, заставляют выбрасывать все подряд;
- стандартизация привела к увеличению бюрократии;
- введение системы «5С» не на всех участках предприятия усугубило проблемы;
- постановка на первое место системы «5С» отодвинула на второй план такие важные вопросы, как нехватка запчастей.
fb.ru
Принципы и инструменты бережливого производства системы 5S
Система 5S – один из ключевых инструментов бережливого производства, направленный на повышение безопасности, эффективности и производительности труда на рабочем месте (рабочем пространстве). Благодаря своей простоте и эффективности часто является начальным этапом совершенствования производственной системы. При этом реализация данной методики формирует новую культуру производства, позволяющую качественно изменить организацию.
Название метода происходит от 5 шагов, каждый из которых начинается на “С”. Так как систему придумали в Японии, оригинальные названия читаются примерно так: Seiri, Seiton, Seiso, Seiketsu, Shitsuke. Позже 5 этапов внедрения были переведены на английский: Sort, Straighten, Sweep, Standardize, Self-discipline, – и русский. Один из вариантов русского перевода: Сортировка, Самоорганизация, Сияние, Стандартизация, Совершенствование. Из-за наличия русского перевода этапов название системы можно встретить как в латыни (5S), так и русскоязычном варианте (5С).
Примечателен тот факт, что схожая система – CANDO (Clearing, Arrangement, Neatness, Discipline, Organization), – появившаяся в США намного раньше, чем 5S, в наши дни менее известна и распространена. По некоторым источникам, CANDO – один из тех принципов бережливого производства, которые основатель производственной системы Toyota позаимствовал во время визита на завод Ford.
Первый шаг системы 5S – Сортировка
На данном этапе все мероприятия сводятся к определению необходимых для работы инструментов и удалению всех ненужных, неисправных или неиспользуемых предметов. Для чего это делается? Для повышения безопасности на рабочем месте, стандартизации выполняемой работы – соответственно, повышения продуктивности и качества.
Практики бережливого производства называют этот шаг самым сложным, так как признавать ненужность предметов, которые долгое время находились под рукой, для большинства людей не так просто. В психологическом плане это требует отказа от привычного порядка, сформировавшегося за годы работы, и принятия нового, неизвестного, часто насаждаемого извне.
Для того, чтобы преодолеть сопротивление на этом этапе, чаще всего прибегают к трем приемам:
- Проводят обучение принципам бережливого производства и системы 5S.
- Вовлекают сотрудников в процесс реализации системы 5S на их непосредственных рабочих местах.
- Создают зону “красных меток” (Red Tag Area) – карантин для предметов, которые не используются на рабочем месте ежедневно, однако по тем или иным причинам не могут быть удалены немедленно.
Второй шаг системы 5S – Самоорганизация или систематизация
Как говорят практики бережливого производства: “всему свое место, и все на своих местах”. Данный этап нацелен на максимально рациональное размещение необходимых для работы предметов в рабочем пространстве. Чем чаще используется предмет, тем ближе и доступнее он должен быть расположен. Чем реже – тем больше шансов найти его за пределами рабочего места, например, в шкафу или на общем стенде.
Зачем это делается? Опять же, безопасность, продуктивность и качество. Удобно расположенный предмет обеспечит эргономику рабочего места и целевое применение. Те же инструменты, которые используются реже, следует разместить в поле общего доступа, что существенно сократит их необходимое количество.
Основные приемы данного этапа системы 5С – различные варианты визуализации: маркировка, зонирование, оконтуривание, метод “теней” и т.д.
Третий шаг системы 5S – Сияние или содержание в чистоте
Данный этап направлен на создание условий для поддержания чистоты рабочего пространства. Разумеется, это подразумевает уборку и чистку. Но на этом третий шаг внедрения системы 5С не завершается. Необходимо установить источники загрязнения – понять причины и разработать план мероприятий по их устранению.
Также на данном этапе разрабатываются графики и стандарты уборки (кто, как часто и чем проводит уборку?), а также обеспечивается необходимых для этих целей инвентарь.
Четвертый шаг системы 5S – Стандартизация
Стандартизация предполагает меры по закреплению и удержанию достигнутых результатов. Для этих целей разрабатываются организационные стандарты, которые в лаконичной и визуализированной форме закрепляют правила относительно обустройства, визуализации, уборки, зонирования и других параметров рабочих мест.
Кроме того, настоящий этап предусматривает создание системы контрольных механизмов, чаще всего аудитов 5С. Для чего это делается? Чтобы предотвратить постепенное “скатывание” системы к первоначальному состоянию.
Пятый шаг системы 5S – Совершенствование
Как проще всего обеспечить удержание полученных результатов? Только непрерывно совершенствуя рабочее пространство усилиями всех сотрудников: каждый сотрудник, каждый день, всюду!
На данном этапе применяют следующее:
- Обеспечивают информирование персонала о состоянии процесса развертывания системы 5S, результатах аудитов, выявленных проблемах и т.д.
- Обеспечивают интеграцию системы 5S и системы подачи предложений по улучшениям.
- Обеспечивают интеграцию системы аудитов 5S и премирования сотрудников.
sixsigmaonline.ru
Методика внедрения инструмента бережливого производства 5S
Библиографическое описание:
Васильева С. Е., Данилова С. Ю. Методика внедрения инструмента бережливого производства 5S // Молодой ученый. 2016. №13. С. 388-393. URL https://moluch.ru/archive/117/31280/ (дата обращения: 17.08.2019).
Ключевой целью системы 5S является создание организованного и чистого рабочего места, которое предусматривает безопасное и стабильное кружение, более лёгкое определение потерь и отклонений [1].
Предлагаемая методика 5S основана на пятиуровневой последовательности (таблица 1).
Таблица 1
Описание системы 5S
Уровень | Название | Описание |
1 | Сортировка | Хранение исключительно необходимого |
2 | Создание порядка | Свое место для каждой вещи и каждая вещь на своем месте |
3 | Соблюдение чистоты | Приведение зоны к первоначальному виду и поддержание аккуратного рабочего места |
4 | Стандартизация | Стандарты, кто что и когда делает во всех зонах |
5 | Совершенствование | Поддержание системы и измерение ее эффективности |
Рассмотрим каждый уровень более подробно.
Уровень 1. 1S. Сортировка
Сортировка — это хранение только того, что необходимо для создания ценности для клиента, когда ничего больше нельзя убрать. Необходимые на рабочем месте предметы отделены от ненужных предметов, которые затем удаляются. Это относится не только к дополнительным материалам (например, инструменты, оборудование, стеллажи), но и к прямым материалам. Для прямых материалов требуется установить максимальные и минимальные уровни всех запасов. Минимальный уровень устанавливается на основе Клиентского спроса при сохранении стабильного производства. Максимальный уровень запасов — это минимальное количество, необходимое для поддержания стабильного производства и, соответственно, поддержания нетерпимости к потерям. Сортировка тесно связана с Принципами управления материалами на предприятии. Она требует хорошего баланса рабочей нагрузки смежных процессов, которые стандартизированы таким образом, что производство является стабильным. Сортировка — один из самых важных инструментов предприятия для достижения уровня 3 ключевых концепций предприятия.
Уровень 2. 2S. Создание порядка
На этом уровне определяется место для каждого необходимого предмета и расположение этих предметов в зоне, так что в основном у всего есть своё место, и всё находится на своих местах. Кроме того, в качестве ключевого элемента этого уровня, важно выявление источников загрязнения и устранение основных причин этого для обеспечения требуемых условий и избежания нежелательных элементов или нежелательных ситуаций.
Уровень 3. 3S. Соблюдение чистоты
Уровень 4. 4S. Стандартизация
Стандартизация — это включение практик первых трёх S в ежедневную работу, это определение стандарта, кто, что, когда и как делает на всех участках. Стандарты 5S для всех зон завода устанавливаются и поддерживаются с помощью визуальных изображений стандартного состояния. Для поддержания хорошего состояния 5S каждый должен знать, что он несёт ответственность за выполнение, а также что, почему, когда, где и как делать.
Ниже на рисунке 1 представлены ключевые факторы успеха от внедрения системы 5S. На рисунке 2 представим более подробно последовательность операций процесса на примере предприятия по производству автокомпонентов.
Рис. 1. Развернутое описание ключевых факторов успеха
Рис. 2. Последовательность операций процесса
На этой фазе целью является поддержание системы 5S и создание системы оценки для обеспечения эффективности. Обеспечьте дисциплинированное соблюдение правил и процедур 5S для предотвращения нарушений. Придерживайтесь правил для поддержания стандарта и продолжайте совершенствоваться каждый день.
В результате предложенное мероприятие позволит:
– 5S тесно связана с безопасностью труда
– Рабочая среда влияет на вовлеченность сотрудников
– На чистом и организованном предприятии легче определить потери
– 5S влияет на восприятие нас клиентами и инвесторами
– 5S и наглядное управление предусматривают безопасную и стабильную среду, более легкое определение потерь и ненормальных состояний [2].
После внедрения процедуры 5S необходимо разработать оценочный лист (таблица 2) и один раз в месяц оценивать уровень применения данной процедуры.
Таблица 2
Оценочный лист по 5S апримере предприятия по производству автокомпонентов
5S | AREA | Участок | 1 | Очень плохо — Нет контроля | |||||||
AUDITED BY | 5S | 2 | Плохо — Некоторый контроль | ||||||||
Date | 12.02.2014 | 3 | Ср уровень — Частично под контролем | ||||||||
Пошив | 4 | Хорошо — Приемлемо | |||||||||
5 | Очень хорошо- Под контролем | ||||||||||
5S | No | Чек лист | Описание | 1 | 2 | 3 | 4 | 5 | Comments | ||
Seiri Separate Селекция | 1 | Все машины и части оборудования постоянно используются | Нужно нам или нет? Ненужные отметить красной лэйблом 5S. | 5 | |||||||
2 | Нет посторонних предметов на рабочих площадях | Нужно нам или нет? Проверить. Ненужные отметить красной лэйблом 5S. | 5 | ||||||||
3 | Все ненужные части четко обозначены | Все ненужные предметы (помеченные красной лэйблом 5S) убраны | 5 | ||||||||
4 | Все контейнеры, рабочие области, стеллажи и инструменты четко обозначены | Проверить | 5 | ||||||||
25 | 5 | Доски отчетов обновлены и хорошо представлены | Все графики и отчеты действительны и презентабельны | 5 | |||||||
Seiton Straighten Сортировка | 6 | Все площади четко обозначены? | Все участки и материалы четко обозначены? | 5 | |||||||
7 | Все документы и файлы промаркированы и аккуратно размещены | Документы и файлы промаркированы и правильно размещены | 5 | ||||||||
8 | Места хранения на рабочих местах и рабочие места разработаны с целью простоты использования | Все расположено в пределах вытянутой руки | 5 | ||||||||
9 | Весь запас храниться в спец месте | Места для всего и все на своих четко обозначенных местах | 4 | Не укрыты часть стеллажей банка кроя | |||||||
24 | 10 | Зоны досок контроля чистые и проход к ним не затруднен | Нет загромождений в проходах к доскам контроля | 5 | |||||||
Seiso Scrub Уборка | 11 | Проверяемая площадь всегда чистая и свободная от лишних предметов | Стараться удалить грязь повторно не повредит | 5 | |||||||
12 | Машины чистые? | Все машины очищены от грязи пыли и масла | 5 | ||||||||
13 | Действует система по уборке (часть ODS) — отображена и актуальна | Операторы поддерживают чистоту в течение смены | 5 | ||||||||
14 | Нет кабелей, проводки, воздухоотводов, лежащих на полу или плохо закрепленных | Всё закрепляется четко на месте | 5 | ||||||||
25 | 15 | Уборочное оборудование | Хранение оборудования рядом с рабочей зоной | 5 | |||||||
Seiketsu Standardise Стандартизация | 16 | Показаны основные процедуры и стандартные операции отображены | Четко видны и актуальны | 5 | |||||||
17 | Операторы прошли тренинг и знают 5S | Операторы знают 5S | 5 | ||||||||
18 | Показать стандарты 5S | Стандарты 5S показаны | 5 | ||||||||
19 | Аудиты 5S регулярны и результаты представлены | Проверить отчет по аудитам | 5 | ||||||||
25 | 20 | Вывоз отходов | Есть мусорные ведра и они регулярно опустошаются | 5 | |||||||
Shitsuke Sytemise Систематизация | 21 | Спецодежда | Все операторы носят спецодежду и защитные приспособления | 5 | |||||||
22 | Ознакомление с 5S и ОТиТБ | Все операторы ознакомлены с 5S и требованиями ОТиТБ | 5 | ||||||||
23 | Мастерские 5S в случае необходимости | Проверять отчеты 5S после каждого изменения layout или запуска новой модели/проекта | 5 | ||||||||
24 | Все ознакомлены с планом эвакуации, техникой безопасности и сборки | Спросить оператор о местоположении | 5 | ||||||||
25 | 25 | Информация по качеству представлена для мотивации персонала (IPPM и т. д.) | Данные показаны и операторы ознакомлены? | 5 | |||||||
Необходимые условия для успешной реализации процедуры:
Определенное лидерство по предприятию, выполнение обходов 5S
– Ресурсы, определенные по участкам
– Выбор показательной области для создания концепции, которая может использоваться для
– распространения на остальную часть предприятия
– Выполнение перекрёстных проверок и закрытие вопросов
– Выполнение графика уборки
– Видение будущего состояния и чёткий план действий по его достижению
Таким образом, предложенная методика позволит эффективно организовать рабочее место.
Литература:
- Агеева И. М., Данилова С. Ю. Оптимизация производственного процесса за счет внедрения инструментов бережливого производства 5S / И. М. Агеева, С.Ю, Данилова // «Современные подходы к трансформации концепций государственного регулирования и управления в социально-экономических системах»Материалы 2-й Международной научно-практической конференции Курск, 19 февраля 2013 г. в 2-х томах: Изд-во ЗАО «Университетская книга, 2013. — Ч.1. — С. — 25–31.
- Степина, С. Е., Чернова Д. В. Методика анализа логистических процессов автосервисного предприятия в рамках концепции бережливого производства / С. Е. Степина, Д. В. Чернова // Вестник Самарского государственного экономического университета. — 2011. С.100–106.
- Womack, J. Seeing the Whole: Mapping the Extended Value Stream [Text] / J. Womack, D. Jones. — Brookline: Lean Enterprise Institute, 2002. — 152 р.
Основные термины (генерируются автоматически): место, уровень, IPPM, AUDITED, AREA, стабильное производство, рабочее место, оценочный лист, аккуратное рабочее место, ODS.
moluch.ru
Бережливое производство и система 5S
Целью любого процесса является создание продукта от начала до конца процесса. Должны быть предприняты усилия для контроля потока, и если погрешности обнаружены, они должны быть немедленно устранены, когда знают бережливое производство, что это такое. Это происходит, когда процесс выходит за пределы своих возможностей. Важно, чтобы специалисты понимали процесс. Несоблюдение параметров процесса приведет к лишним расходам. Совершенство во всех процессах продукт является конечной целью. Бережливое производство подразумевает непрерывный безупречный поток продукции без отходов.
Основные инструменты системы бережливого производства:
- определение правильного тактового времени или темпа процесса;
- создание и использование системы для предотвращения появления отходов;
- использование устройств для обнаружения ошибок в процессе;
- создание четного потока или материала;
- стремление к совершенству.
Руководство ищет возможности улучшения в каждой части потока создания ценных изделий. Выявление и устранение основных причин проблем в производственных процессах для достижения совершенства. Бережливое производство исключает методы, которые не повышают ценность для клиентов. Принципы и концепции в области бережливого производства чрезвычайно полезны и обеспечивают глубокое понимание процесса бережливого производства. Бережливые производственные принципы являются ключевыми для работы. Устранить отходы производственного процесса довольно сложно, но это не невозможно. Многие руководители проектов на производственных объектах испытывают ту же борьбу, но считают экономичным производство жизнеспособным вариантом.
Внедрение бережливого производства подразумевает:
- определение участков, которые не считаются ценными для потребителя;
- исключение этих участков для снижения издержек производства.
Таким образом, можно постепенно разрешить производственной операции производить только то, что абсолютно необходимо, в конечном итоге избавляя фабрику от ненужного производства. В дальнейшем на продукцию потребуется получение разрешительных документов, таких как декларация таможенного союза или добровольный сертификат.
Система 5s бережливое производство.
Система 5s – комплексная методика улучшения производственного процесса путём оптимизации пяти связанных между собой этапов, собранная как цельная система в Японии в конце 20-го века. Наименование каждого из этапов в японском языке начинается на букву «s».
Но в русском языке на букву «с» подобраны соответствующие этим наименованиям аналоги, поэтому нередко в литературе используется адаптированное «русское» название метода бережливого производства – Система 5С, где:
- 1С – Сортируй – Seiri (Сейри).
- 2С – Соблюдай порядок – Seiton (Сейтон).
- 3С – Содержи в чистоте – Seisō (Сейсо).
- 4С – Стандартизируй – Seiketsu (Сейкецу).
- 5С – Совершенствуй (или Самодисциплина) – Shitsuke (Сицуке).
Существует адаптация и под английский язык, где наименование каждого этапа начинается уже на английскую букву «s»: Sorting, Set in Order, Sweeping, Standardizing, Sustaining the discipline.
Принципы бережливого производства.
1)Идентификация ценности — определение ценности клиента является наиболее важным аспектом бережливого производства. Определение ценности может быть чем-то, что потребитель считает абсолютно необходимым.
2) Сопоставление потока создания ценности. После определения значения настало время перейти к сопоставлению потока создания ценности. Этот процесс включает в себя определение каждого аспекта процесса, с самого начала, где собирается сырье, до доставки продукта. Этот принцип помогает найти другие этапы производства отходов, что в конечном итоге позволяет операции разработать план по его устранению. Создание потока — после того, как принят план для устранения отходов.
3) Следующим шагом является наблюдение за оставшимися действиями в рамках операции. Это делается для того, чтобы в процессе не было проблемных мест, прерываний или любых других проблем.
После того, как недочеты внутри процесса выяснены, производственный поток становится намного быстрее и эффективнее. Это связано с устранением бесценных шагов. Это позволяет потребителям извлечь продукты по мере необходимости. Для реализации продукции на торгах организации потребуется сертификат РПО или сертификат деловой репутации.
В поисках совершенства — внедрение этих шагов само по себе значительно улучшит производственные мощности, но бережливое производство требует значительных усилий и изменения мышления. Вместо того, чтобы рассматривать это как просто метод производства, важно рассматривать его как культуру, требующую нахождения всех специалистов на рабочих местах. Несколько раз пройдя процесс по методологии бережливого производства, можно приблизиться к полной реализации своего производственного объекта. Наряду с бережливыми принципами, надо знать об общих отходах в процессе производства.
sltiu.ru
5S на транспорте — 1 шаг 5С и введение
Рис. 1. Лестница создания эффективного рабочего места.
Система устанавливает пять шагов, выполнение которых направлено на создание условий для стабильного оптимального выполнения операций, поддержание порядка, чистоты, аккуратности, экономии времени и энергии для повышения производительности, предотвращения несчастных случаев, снижения загрязнения окружающей среды.
Таблица 1
Основные принципы системы 5С
Принцип |
Содержание работы |
1. Сортировка: оставьте только нужное (ККЯ) |
Все предметы разделяются на три категории: нужные, не нужные срочно и ненужные. Нужные сохраняются на рабочем месте. Не нужные срочно располагаются на определенном удалении от рабочего места или хранятся централизованно Ненужные удаляются. |
2. Свои места для всего: каждой вещи свое место |
По отношению к нужным предметам и предметам не нужным срочно вырабатываются и реализуются решения, которые обеспечивают: ·быстроту, легкость и безопасность доступа к ним; ·визуализацию способа размещения и контроля наличия, отсутствия или местонахождения нужного предмета; ·свободу перемещения предметов и эстетичность рабочего места (автомобиля). |
3. Содержание в чистоте: рабочее место в исправном, подготовленном к работе состоянии |
Тщательная уборка и очистка рабочего места (автомобиля) и оборудования. Фиксация и устранение неисправностей. Выявление источников загрязнения, труднодоступных и проблемных мест. Выработка и реализация мер по уборке труднодоступных мест, ликвидации источников проблем и загрязнений. Выработка правил проведения уборки-проверки, чистки оборудования, смазки. |
4. Стандартизация процедур поддержания чистоты и порядка |
Фиксация в письменном виде правил и стандартов выполнения рабочих операций, направленных на: удаление ненужного, рациональное размещение предметов, уборку, смазку, проверку. |
5. Самодисциплина: стимулируйте поддержание порядка |
Закрепление сфер ответственности за каждым водителем (объекты внимания и основные обязанности по их поддержанию в нормальном состоянии). Выработка у водителей правильных привычек, закрепление навыков соблюдения правил. Применение эффективных методов контроля – чек-лист. |
В целом применение системы 5С позволяет создавать эффективные рабочие места, что в дальнейшем дает экономию средств, улучшает качество, поднимает эффективность перевозки товара, повышает уровень производительности и безопасности труда.
Система 5С направлена на следующие объекты:
— Внешний вид водителя;
— Рабочие зоны:
— Салон автомобиля
— Кузов автомобиля
— Внешнее состояние автомобиля
— Техническое состояние автомобиля
— Предметы у водителя и в зоне:
— Спецодежда, документы, электронные устройства.
— Предметы и оборудование, необходимые для выполнения работы (ККМ, сейф, погрузочно-разгрузочное оборудование, стяжные ремни, противооткатное устройство)
— Предметы, необходимые по правилам дорожного движения (аптечка, огнетушитель, знак аварийной остановки и т.д.)
— Средства для ремонта автомобиля (запасное колесо, домкрат, балонный ключ)
4. ОРГАНИЗАЦИЯ РАБОТ ПО ВНЕДРЕНИЮ СИСТЕМЫ 5С
4.1 Перед началом работы необходимо определить:
— Цель работы
— Руководителя работ
— Состав рабочих групп
— План-график проведения встреч рабочих групп
4.2 Ответственность за внедрение системы 5С в филиале возлагается на Заместителя директора филиала. Ответственность за проведение и поддержание системы 5С на грузовых автомобилях возлагается на сотрудника, ответственного за выпуск автомобиля на линию.
4.3 Рекомендуемый состав рабочей группы:
— Заместитель директора филиала;
— сотрудник, ответственный за выпуск автомобиля на линию;
— водитель/водители.
Примечание: состав группы может быть иным, в зависимости от организационной структуры подразделения.
5. ШАГ №1 СИСТЕМЫ 5С: СОРТИРУЙТЕ: ОСТАВЬТЕ ТОЛЬКО НУЖНОЕ
5.1. Цель первого этапа 1С – определить необходимые для рабочей деятельности предметы, освободить рабочее пространство от ненужных предметов, создать предпосылки для организации визуального управления и стабилизации процесса.
5.2. В случае, если чистота и санитарное состояние автомобиля находятся на невысоком уровне, целесообразно начать с генеральной уборки, которая позволит быстро освободиться от существующей части грязи и мусора, неприятных запахов. Кроме того, самому водителю необходимо привести себя в порядок и свой внешний вид. Затем приступать к реализации первого шага системы 5С.
Схема проведения 1С представлена в таб. 2.
Таблица 2
№ этапа |
Этап |
Название этапа |
1.1 |
Подготовительный |
Определение графика проведения Сортировки |
Определение перечня работ |
||
1.2 |
Определение критериев необходимости предметов в автомобиле и у водителя |
|
1.3 |
Фотографирование водителя и автомобиля |
|
2.1 |
Реализация |
Идентификация предметов у водителя и в автомобиле |
2.2 |
Оценка степени необходимости каждого предмета, принятие решений |
|
2.3 |
Документирование результатов 1С, фиксирование списка необходимых предметов в контрольный листок |
|
2.4 |
Удаление предметов, по которым принято соответствующее решение, из автомобиля и у водителя |
|
Перемещение предметов, по которым принято соответствующее решение |
5.3.1. Подготовительный этап.
5.3.1.1. Рабочая группа проводит организационное совещание, на котором:
— разрабатывает график проведения 1С;
— участниками рабочей группы изучаются теоретические и методические материалы. При необходимости для проведения обучения руководитель группы приглашает кайдзен-менеджера если таковой сотрудник имеется в компании или на предприятии.
— Определяются способы и порядок удаления предметов.
Примечание: рекомендуемые способы удаления предметов:
• Выбросить (самое последнее)
• Передать другим водителям
• Продать
• Передать другому подразделению
Также рабочая группа перед началом шага 1С разъясняет водителям цели и задачи 1С и системы 5С в целом.
5.3.1.2. Рабочая группа определяет критерии необходимости предметов в автомобиле и у водителя. Рекомендуется за основу взять следующие три критерия:
— Необходимость предмета при выполнении текущей деятельности. Это могут быть как предметы, используемые непосредственно в работе водителя (стяжные ремни, документы на груз, перчатки, ручка, мобильный телефон и т.д.), так и предметы первой необходимости (аптечка, огнетушитель, знак аварийной остановки). Если предмет не нужен, он должен быть удален из рабочей зоны (кабина или кузов) и удален у водителя;
— Частота использования. Если предметом пользуются редко, то его можно хранить вне рабочего места;
— Количество предметов, необходимых для текущей деятельности. Если нужно ограниченное количество предметов, излишки можно удалить или хранить вне рабочего места. К примеру, если положено 4 стяжных ремня, то должно быть 4 (максимум 6 – на случай дополнительного крепежа, поломки или повреждения) стяжных ремня. Также и с пишущей ручкой. Нет необходимости хранить несколько ручек в разных частях салона (двери, бардачок, панель приборов, подлокотник и др.). Достаточно 1-2 ручек для оформления документов.
5.3.1.3. Рабочая группа фотографирует текущую ситуацию в автомобиле и самого водителя. Фотографирование автомобиля должно проходить со всех сторон, включая рабочие зоны (салон и кузов). Также фотографируется водитель спереди и сзади во весь рост. Фотографии сохранены в папку с указанием даты фотосъемки.
5.3.2. Этап реализации
5.3.2.1. Рабочая группа проводит идентификацию предметов в автомобиле и у водителя, а также определяет степень необходимости этих предметов и в соответствии с этим принимает решение об их дальнейшей судьбе:
— оставить предмет там, где он находится
— изменить количество
— переместить предмет на новое место в пределах автомобиля;
— утилизировать;
В результате должен быть сформирован список необходимых предметов всех рабочих зон и у водителя, который используется для формирования Контрольного листка (см. п. 5.4.3)
5.3.2.2. Удаление ненужных предметов.
— Выявленные лишние предметы должны быть удалены из автомобиля сразу же после принятия решения о способе удаления.
Примечание: Возможные рекомендуемые способы удаления предметов:
• Выбросить – для выявленных лишних предметов, не представляющих ценности.
• Передать другим подразделениям или водителям – для выявленных лишних предметов, представляющих ценность, и необходимых на других участках.
• Продать – для выявленных лишних предметов, представляющих ценность, но не нужных для выполнения рабочих операций.
5.3.3. Контроль эффективности первого шага системы 5С
Контроль эффективности внедрения первого шага системы 5С осуществляется при помощи «Контрольного листа по проверке эффективности внедрения первого шага системы 5С». Контрольный лист 1-го уровня (аудит выполняется самим водителем) должен храниться в салоне автомобиля в лотке или папке.
Эффективность внедрения первого шага оценивается по автомобилю и водителю в целом. Наличие правил отнесения предметов к нужным, кол-во предметов и место их нахождения.
iambuilding.ru
Система 5s на производстве что это такое
Система 5s – это система рационализации труда на производстве, которая пришла к нам из Японии. Читайте об основных принципах системы и о том, можно ли ее внедрить в России и стоит ли это делать.
В этой статье вы узнаете:
В послевоенный период, когда японский автопром жестко конкурировал с американским, инженер завода по производству «Тойот» Тайити Оно сумел внедрить принципы порядка, дисциплины и рационализации на предприятии, которые позволили резко увеличить производительность без существенных затрат.
Концепция 5S стала продолжением научных трудов и экспериментов Фредерика Тейлора по внедрению нормирования и рационализации труда на производстве, которые он проводил в США в конце 19-ого века. Однако 5S основана на Японских традициях и культуре бережливого производства.
В России научной организацией труда начал заниматься революционер, писатель-фантаст А. А. Богданов. Но в России, где русский крестьянин полгода вынужден бездействовать во время морозов, а потом за несколько теплых месяцев все быстро делать («битва за урожай») система 5s так и осталась научной фантастикой. Внедрение «бережливого производства» в России идет с крайним трудом и сопротивлением.
Скачайте дополнительные материалы к статье:
Система 5с на производстве: что это такое
Рассмотрим все принципы системы 5s в офисе.
Сэири (整理) – Сортировка
Сортировка предполагает, что все вещи и предметы, лежащие на рабочем месте, разделяются на 4 вида по частоте использования: постоянно, часто, редко и никогда. Соответственно, те которые не используются убираются на склад, те которые постоянно – лежат «прямо под рукой», часто используемые – поблизости в ящике и редко нужные – где-нибудь подальше в тумбе.
Вроде все просто и понятно. Наверное, каждый по себе знает, как сложно найти нужную вещь, когда все свалено в одну кучу. Или когда, скажем, кухня на первом этаже, а накрывают на третьем — бегать туда-сюда очень утомительно. Поэтому принцип, чтобы «все нужное лежало под рукой» очень сильно экономит время и производительность (см. также, как рассчитать и анализировать производительность труда).
Сэитон (整頓) – Соблюдение порядка
Это метод 5S, согласно которому «все имеет свое место», то есть это прямое продолжение Сэири. Когда вещи отсортированы, каждому предмету должно быть назначено конкретное место. Это место должно быть подписано и обозначено, а сам предмет маркируется красной биркой с соответствующей записью. По-японски такие бирки называются «Канбан» (читайте подробнее про систему Канбан). Иногда, предметы обводят, чтобы точно знать их расположение.
Пометить каждый предмет, да еще и обвести его – это уже в наш российский менталитет слабо вписывается. Хотя теоретически очевидно, что тогда сразу все легко найти и потом положить на место.
Как внедрить систему 5s: опыт российской компании
5S – это один из методов бережливого производства. Российской компании удалось преодолеть сопротивление персонала и внедрить у себя систему бережливого производства. Ее уникальный опыт может пригодиться тем предприятиям, которые тоже планируют перейти на бережливые рейсы.
Внедрить 5S
Сэисо (清掃) – Содержание в чистоте рабочего места
Здесь все понятно. В чистоте приятно работать и т. д. Вот только я вспоминаю, как на производственной практике мастер заставлял буквально «вылизывать» станки в цеху и не отпускал домой по 1–2 часа сверх рабочего дня.
При использовании принципов бережливого производства 5s зачастую возникают вопросы, кто должен убирать: сам работник или уборщица. Представьте себе, что уборщица начинает влажной тряпкой протирать открытый компьютер у сотрудников IT-отдела, которые могут находиться в спящем режиме. Короткое замыкание гарантировано. Поэтому правило Сэисо гласит, что сотрудник сам должен убирать за собой рабочее место.
Гость, уже успели прочесть в свежем номере?
Сэикэцу (清潔) – Стандартизация
Стандартизация включает в себя правила, инструкции по выполнению тех или иных работ, нормативы по их выполнению, используемые средства и т. д. Суть состоит в том, что нормировщики, например, уже высчитали, сколько деталей на определенном станке за определенный период должен изготовить рабочий. Если он будет работать по-своему, то:
- либо сделает быстрее, чем нужно (в Японии система «Точно в срок» этого не поощряет), и будет «прохлаждаться», мешая остальным
- либо сделает быстрее за счет качества (ведь качество и скорость взаимопротивоположные понятия),
- либо сделает медленнее и затормозит работу остальных, либо с большими издержками и т. д.
Система организации и рационализации рабочего места 5S предполагает описание и контроль за исполнением первых трех пунктов: сортировка, порядок и чистота. Периодически начальство делает контрольный обход, и все данные по рабочим местам заносит в контрольный лист:
КОНТРОЛЬНЫЙ ЛИСТ ПРОВЕРКИ (фргагмент)
(наименование подразделения)
за м-ц 20 г.
Шаг |
Критерий |
Дата проведения проверки |
|||
1. Сортировка и удаление лишнего (определить, что есть, что из этого необходимо, от остального избавиться) |
На рабочем месте имеется ненужный и не в требуемом количестве инвентарь, инструмент, тара. пр. |
|
|
|
|
Итого проблем по 1C |
|
|
|
|
|
Оценка |
|
|
|
|
|
2. Соблюдение порядка, создание места для того, что необходимо (определить места для того, что осталось) |
Постоянные места для вещей не очевидны с первого раза (нет или не просматривается разметка) |
|
|
|
|
Общее количество проблем выявленных предыдущей проверкой |
|
|
|
|
|
% текущих проблем к предыдущим |
|
|
|
|
|
ФИО проверяющего |
|
|
|
|
|
Подпись проверяющего |
|
|
|
|
Сицукэ (躾) – Самодисциплина и совершенствование
Совершенно очевидно, что вся система из пяти S не будет работать, если сами сотрудники предприятия не желают ею пользоваться. Для убеждения работников в Японии, прежде всего, используются доски почета персонала, сравнительные фотографии и другая наглядная агитация.
Кроме того использование системы 5s для организации и рационализации рабочего места, также процессов необходим творческий подход. Сотрудники должны предлагать соответствующие улучшения. И руководство в целом должны постоянно оптимизировать процесс. Поэтому японцы часто собираются после работы и обсуждают, как им что-нибудь улучшить.
Например, для оптимизации рабочего пространства часто используют диаграмму «Спагетти» (название из-за схожести с макаронами). На рисунке отмечают маршруты, которые проходят сотрудники или клиенты, или инструменты, или документы и т.д. и видят, как можно по-другому расположить рабочие места, чтобы сократить рабочее время на ненужную беготню.
Рисунок. Диаграмма «Спагетти»
На диаграмме видно, что до изменений товар проходил гораздо более длинный путь, чем после расположения отделов и склада по пути следования товара из цеха. Соответственно, это сокращает время на логистику.
Проблемы внедрения стандартов 5s в России
Однажды директор издательства, где я работал руководителем отдела продаж, предупредил, что завтра у всех сотрудников заберут все ненужные вещи и положат на склад до особого распоряжения. Никто не придал этому особого значения, так как под словом «ненужные» каждый понимал что-то свое.
На следующий день директор с двумя помощниками из отдела охраны стал проходить по отделам и забирать у сотрудников все, что находилось на столах, в ящиках и на полках. Народ возмущался, но бойцы из службы безопасности были непреклонны. После этого директор объявил, что если кому действительно что-то очень нужно, то он должен написать письменную заявку, пойти на склад и там поискать свои вещи.
Больше всех не повезло сотрудникам бэк-офиса. Если бухгалтерию директор обошел стороной, то «делопроизводители» были вынуждены несколько дней ковыряться в мешках и папках на складе с книгами, чтобы найти свои рабочие документы. Что касается канцелярии, то народ не пошел за ней на склад, а заказал все по новой секретарю. Несколько человек не выдержали и уволились.
Результат очень простой. Несколько месяцев сотрудники все старательно прятали от глаз директора, а он радовался чистым столам. А производительность труда не выросла никак.
В чем же сложность внедрения 5s на производстве и в офисах в России?
1) Это российский менталитет. В учебниках по международному менеджменту различают три типа культуры свойственные разным народам: моноактивные, полиактивные и реактивные. Моноактивные и реактивные культуры, к которым относятся японцы, немцы, американцы и другие, живут строго по планам, правилам и инструкциям, четко соблюдая все сроки и графики работ. В один промежуток времени они, как правило, делают только одно дело.
Носители полиактивной культуры делают множество дел одновременно, не придерживаясь четких правил, планов и графиков, адаптируя их под текущий момент. Делают не то, что должно, а то, что нравится. К этим культурам относятся: итальянцы, арабы, мексиканцы, африканцы, русские и т. д.
Для представителей этих культур понятия порядок, дисциплина, инструкция, технология и т. д. являются весьма относительными. Они могут поддерживаться на высоком уровне только в авторитарной иерархической структуре, например, армии.
Поскольку для представителей западных культур главным стимулом является вознаграждение, для восточных – наслаждение процессом, а для русских – зуботычина и грозный окрик начальства, то система внедрения «порядка и дисциплины» на рабочем месте на российском предприятии возможно только через силовое давление начальства: ругань, штрафы и т. д.
2) Отсутствие мотивации у руководителей. Причина, по которой начальство вдруг решает внедрять 5s, заключается не в желании увеличить производительность труда, а в необходимости что-либо делать по развитию фирмы в принципе. Или собственник прочитал очередную умную статью про западный менеджмент и говорит директору: «давай, внедряй». В общем ни четкого понимания, зачем все это, ни особой мотивации у руководства нет, а потому проводится внедрение чисто формально. Все делают вид, что почистили пару раз рабочие места и на этом все заканчивается.
3) Даже если руководство поставило себе цель: во чтобы то ни стало, то подчиненным все это не понятно. Для них это «лишний геморрой и тараканы в голове у начальства». Менеджеры не могут толком объяснить: зачем это нужно самим сотрудникам. Например, вот лежал всю жизнь гаечный ключ на «17» у механика под рукой, а теперь он должен висеть на стенде с красным флажком и обведенный по контуру! Механику что, больше заняться нечем?!
Здесь можно задаться вопросом: а что же тогда делать? Во-первых, не надо внедрять то, что вы и сами себе не можете толком объяснить зачем это и что это даст. 5S – «это не догма, а руководство к действию».
4) Отсутствие стимулов. Да, матом и штрафами можно добиться определенных результатов. Будет идеально чистое место, но только производительность упадет, так как за недостающими деталями рабочему нужно будет постоянно ходить на склад, например. Руководство не хочет признавать тот факт, что сортировка, «разложение по полочкам», уборка рабочего места, стандартизация и самодисциплина – это тяжкий труд для российского работника. И он должен быть оплачен! Иными словами, на время внедрения 5s должны быть предусмотрены соответствующие премии сотрудникам!
Подготовлено по материалам
«Системы Финансовый директор»
www.fd.ru
КОНЦЕПЦИЯ БЕРЕЖЛИВОГО ПРОИЗВОДСТВА: ИСПОЛЬЗОВАНИЕ СИСТЕМЫ 5С НА ПРЕДПРИЯТИИ
Концепция бережливого производства заключается в максимальной минимизации издержек или потерь.
Потери — это издержки, которое несет организация в процессе производства товаров или услуг.
Тайиши Оно, основатель производственной системы Тайота, выделил 8 видов потерь на предприятии рисунок 1 [4].
Рисунок 1. Виды потерь на производстве
Необходимо подчеркнуть, что концепция бережливого производства предусматривает участие всей организации в целом, как руководства предприятия, так остальных сотрудников организации.
Основная задача концепции бережливого производства заключается в постоянном совершенствовании организации.
Концепция бережливого производства включает в свою систему множество инструментов, однако каждый из них предполагает в своей сущности некоторые усилия и траты, самым наименее затратным инструментом бережливого производства является система «5С»[2].
Рисунок 2. Инструменты бережливого производства
Рассмотрим данный инструмент бережливого производства более подробно в этой статье.
Инструмент «5С» — это система, которая обеспечивает наиболее рациональную организацию рабочего места работника. Данная система направлена на увеличение производительности труда, а так же увеличивает эффективность управления рабочим пространством на предприятии и экономии времени [3].
Основная цель системы «5С» создание комфортной среды для работника любого подразделения, для того, что бы работник точно знал, где находится инструмент или документ [1].
Как и в любой системе бережливого производства в 5С предусматривается участие всех работников организации, т.е. каждый работник без исключения должен оптимизировать свое рабочее место на максимальном уровне
Система «5С» включает в себя следующие 5 основополагающих принципов (рисунок 3)[3].
Данная система не включает никаких особенных или очень сложных методов, вероятно по этой причине она получила такую популярность в других странах.
Рисунок 3. Принципы системы 5С
1С – Сортировка. Подразумевает осмотр рабочего места, устранение неиспользуемых предметов и уборку.
2С — Соблюдение порядка. Включает в себя закрепление за каждым предметом определенное место в соответствии с частотой использования, каждый предмет должен быть готовым к применению.
3С — Содержание в чистоте. Данные принцип заключается в содержании своего рабочего места в чистоте посредством либо устранения источника грязи, либо периодичной уборку рабочего места.
4С – Стандартизация. Подразумевает письменное закрепление правил, инструкций использования рабочего места или инструмента. К стандартизации может относиться «Паспорт рабочего места». В данном паспорте указывается, в каком виде необходимо содержать рабочем место, а так же правила и частоту уборки рабочего места.
5С – Совершенствование. Постоянное поддержание порядка на рабочем месте, и стремление к усовершенствованию.
Если работник придерживается данной системы — это позволит содержать рабочее место в абсолютной чистоте, все необходимые документы будут находиться в готовности к использованию, и поиск не будет занимать продолжительное время[1].
Рисунок 4. Рабочее место до и после использования системы 5С
Применение системы 5С на предприятии поможет руководителю добиться следующего результата[1]:
- Сократить время простояв из-за неисправности того или иного оборудования;
- Обеспечить надлежащее состояние и санитарно-гигиенические условия рабочего места;
- Сократить потери связанные с загрязнение производимой продукции;
- Увеличение производительности труда за счет психологического настроя работников;
- Соблюдение правил охраны труда, а следовательно сокращение травматизма на рабочем месте;
- Быстрый поиск инструментов или документов на рабочем месте.
Необходимо заметить, что данная система «5С» сокращает срок адаптации вновь принятых сотрудников на предприятие. Данная система поможет быстрее ориентироваться на рабочем месте и приспособиться к темпу работы предприятия.
Однако, необходимо заметить, что данную систему «»5С так же можно применять не только на физическом рабочем месте, но так и виртуальном.
На предприятиях часто сталкиваются с тем, что при отсутствии работника необходимо найти какой либо документ на его персональном компьютере, что часто вызывает затруднение.
Часто наши ПК загружены устаревшей или давно не используемой информацией, среди которой очень сложно найти необходимый документ, в особенности, если названы они абсолютно неприменимыми или не связанными названиями.
Так, если внедряя систему 5С на ПК и общих серверах, мы увеличиваем эффективность использования оперативной памяти ПК, сокращаем время поиска, увеличиваем оперативность выполнения работ.
Для начальной стадии внедрения бережливого производства на предприятии система «5С» является весьма эффективной и удобной как фундамент, на котором стоиться все концепций. Данная система легка и не требует в своей сущности больших усилий со стороны работников или руководства предприятия. На основе системы «5С» предприятие без затруднений может внедрять другой более сложный и затратный инструмент концепции бережливого производства.
Главную роль, естественно, при внедрении любой системы бережливого производства является психология персонала предприятия. Каждому работнику необходимо понимать, что все выполняют задачу для достижения одной единой цели и добиваться положительного результата.
Список литературы:
- Шехватов А.В., Сверчков П.А. БЕРЕЖЛИВОЕ ПРОИЗВОДСТВО, СИСТЕМА 5С // Молодежный научный форум: Общественные и экономические науки: электр. сб. ст. по мат. XXI междунар. студ. науч.-практ. конф. № 2(21). URL: https://nauchforum.ru/archive/MNF_social/2(21).pdf
- Менеджмент качества [Электронный ресурс] : С чего начинается качество на рабочем месте — Электрон. дан. — 2011.
- Кротенко В.С. «БЕРЕЖЛИВОЕ ПРОИЗВОДСТВО (LEAN PRODUCTION). — Квалиметрия и управление качеством. Москва-2015, выпуск 27
- Тайити Оно. Производственная система Тойоты: уходя от массового производства. – М: Издательство ИКСИ, 2012.
sibac.info