Производство печатных плат, как бизнес: с чего начать?
Производство печатных плат– бизнес, который имеет рентабельность в абсолютно любой стране, так как в создании электронного оборудования без данного компонента никак не обойтись.
Народные умельцы могут производить такие элементы даже в домашних условиях! Технология производства плат не состоит из непосильных для простого человека этапов, а большинство компонентов легко найти на радиорынках или специализированных площадках в интернете.
Платы заводского образца имеют больший спрос, но для их производства необходимо соответствующее оборудование и соблюдение четкой инструкции по сборке.
В сегодняшней статье мы расскажем подробнее о домашнем и заводском производстве, а также и поможем вам сориентироваться в приблизительной стоимости такого бизнеса вообще.
Что такое печатные платы?
Современные гаджеты не представляют своего существования без такого компонента, как печатная плата. Заготовка представляет из себя пластинку с диэлектрического материала, которая содержит цепи, проводящие электрический ток.
Располагаться такие «жилки» могут либо на самой поверхности диэлектрика, либо же бывают внедрены во внутреннюю часть основы печатной платы.
Назначение плат – объединение компонентов электронных устройств в единую сеть. Они проводят электричество и соединяют элементы гаджета в цельную механическую структуру. Выводы на концах плат крепятся один к одному при помощи пайки.
Из чего состоит печатная плата:
• диэлектрический материал, лежащий в основании; |
• рисунок из фольги, выполняющий функцию электрического проводника; |
• специальные отверстия для монтажа; |
• контактные площадки, объединяющие планарные элементы печатной платы; |
• паяльная маска, выполняющая роль защитного покрытия; |
• маркировка (в промышленном производстве). |
Если производство платы происходило на домашнем оборудовании для личных целей, некоторые компоненты конструкции могут быть из этого списка изъяты.
Классификация плат для печати зависит от таких факторов, как температурный порог использования и отрасль применения.
Классификация печатных плат по количеству слоев:
- Односторонняя – покрытие из фольги для диэлектрика наносится лишь на одну сторону.
- Двухсторонние – покрытие из фольги для диэлектрика наносится на две стороны печатной платы.
- Многослойные – диэлектрическая основа имеет несколько слоев, на каждом из которых располагается покрытие из фольги.
При производстве различных электронных устройств могут возникать проблемы с функциональностью самой основы. Слишком хрупкий диэлектрик становится проблемой в смартфонах с гибким дисплеем, а работа типичной платы в условиях повышенных температур приводит к ее плавке и, соответственно, выходу из строя.
Увеличивающейся ассортимент продукции повлек за собой появление новых решений по реализации компонентов. Это заставило производство печатных плат внедрить еще одну классификацию на основании свойств материала диэлектрической основы. В технической литературе появились такие термины, как жесткие и гибкие платы для печати.
Существуют также отдельные технологические решения, учитывающие особенности применения плат для печати (высокая/низкая частота, температура и тому подобное).
Официальная документация по производству печатных плат состоит из 5 нормативных документов, перечень которых можете увидеть на рисунке:
Пошаговое производство печатных плат
Сразу оговорим, что массовое производство печатных плат в домашних условиях организовать практически нереально, да и оборудование для этого варианта, как таковое, не существует.
Если у вас в голове зародилась мысль заняться серьезным бизнесом в этой отрасли, будьте готовы к масштабному производству и выходу на рынок всей страны. Именно страны, так как найти достаточное количество заказчиков даже в крупном городе России нельзя – дело будет попросту нерентабельным.
1. Технология производства печатных плат.
Технологический процесс производства печатных плат содержит в себе четыре основных этапа, каждый из которых подразделяется на более локальные задачи, требующие дорогостоящего оборудования и подготовленного места.
Перед началом производства стоит побеспокоиться о подготовке материалов и оборудования. Список всех необходимого «сырья» для производства печатных плат подан в таблице ниже. В расчет бралась классификация на основании количества слоев.
Материалы для производства печатных плат:
1) Материалы для изготовления одно и двусторонних печатных плат | ||
---|---|---|
Название | Марка | Толщина |
Гетинакс фольгированный | ГФ-1-35; ГФ-1-50; ГФ-2-35; ГФ-2-50; ГФ-1-35Г; ГФ-1-50Г; ГФ-2-35Г; ГФ-2-50Г | 1…3 |
Фольгированный гетинакс общего назначения | ГОФ-1-35Г; ГОФ-2-35Г; ГОФВ-1-35Г; ГОФВ-2-35Г | 1…3 |
Фольгированный стеклотекстолит | СФ-1-35; СФ-2-35; СФ-1-50; СФ-2-50; СФ-1-35Г; СФ-2-35Г; СФ-1-50Г; СФ-2-50Г; СФ-1Н-35; СФ-2Н-35; СФ-1Н-50; СФ-2Н-50; СФ-1Н-35Г; СФ-2Н-35Г; СФ-1Н-50Г; СФ-2Н-50Г; | 0.5…3 |
Стеклотекстолит фольгированный повышенной нагрев стойкости | СФПН-1-50; СФПН-2-50 | 0.5…3 |
Диэлектрик фольгированный гальвано стойкий | ФДГ-1; ФДГ-2 | 0.5…3 |
2) Материалы для изготовления печатных плат повышенной плотности монтажа | ||
Название | Марка | Толщина |
Материалы для полу аддитивной технологии | СТЭФ-1-2ЛК | 1.0; 2.0 |
Стеклотекстолит листовой с адгезивным слоем | СТЭК | 1.0; 1.5; 2.0 |
Диэлектрик фольгированный для уплотненного монтажа | СЛОФАДИТ | 0.5; 0.8; 1.0; 1.5; 2.0; 2.5; 3.0 |
Стеклотекстолит теплостойкий с алюминиевым протектором | СТПА-5-1; СТПА-5-2 | 0.1; 0,12; 0.13; 0.16; 0.2; 0.25; 0.3; 0.35; 0,5; 0,8; 1.0; 1.5; 2.0 |
3) Материалы для изготовления многослойных печатных плат | ||
Название | Марка | Толщина |
Стеклотекстолит фольгированный травящийся | ФТС-1-20АО; ФТС-2-20АО; ФТС-1-20А; ФТС-2-20А; ФТС-1-20Б; ФТС-2-20Б | 0.08; 0.15; 0.16; 0.27; 0.5 |
ФТС-1-35Б; ФТС-2-35Б | 0.1; 0.12; 0.14; 0.23; 0.25 | |
ФТС-1-35АО; ФТС-2-35АО; ФТС-1-35А; ФТС-2-35А; | 0.1; 0.19; 0.14; 0.23; 0.1; 0.12; 0.14; 0.23 | |
Стеклотекстолит теплостойкий фольгированный | СТФ-1 | 0.1; 0.12; 0.13; 0.15; 0.2; 0.25; 0.35; 0.5; 0.8; 1.0; 1.5; 2.0; 2.5 |
СТФ-2 | 0.25; 0.35; 0.5; 0.8; 1.0; 1.5; 2.0; 3.0 | |
Диэлектрики фольгированные серии «Д» | ДФС-1; ДФС-2 | 0.06; 0.08; 0.01; 0.13; 0.15; 0.2; 0.25; 0.3; 0.4; 0.5 |
Стеклотекстолит, фольгированный гальвано стойкий и теплостойкий | СФ-200-1; СФ-200-2; СФГ-200-1; СФГ-200-2 | 0.8; 1.0; 1.5; 2.0 |
Диэлектрик фольгированный гальвано стойкий и теплостойкий | СФГ- 230-1-35; СФГ-230-2-35; | 0.13; 0.2; 0.25; 0.5; 0.8; 1.0 |
СФГ-230-1-150; СФГ-230-2-50 | 0.25; 0.5; 0.8; 1.0; 1.5; 2.0; 2.5 | |
Стеклотекстолит общего назначения | СОФ-1 | 0.8; 1.0; 1.5; 2.0; 2.5; 3.0 |
СОФ-2 | 0.2; 0.25; 0.8; 1.0; 1.5; 2.0; 2.5 | |
Стеклотекстолит общего назначения негорючий | СОНФ-1 | 1.5; 2.0; 2.5; 3.0 |
СОНФ-2 | 0.35; 0.5; 0.8; 1.0; 1.5; 2.0; 3.0 |
Поданный список наиболее полный и подойдет на любой комплект оборудования.
Когда все необходимое закуплено, можно начинать сам процесс производства.
Существует два метода изготовления плат – субтрактивный и аддитивный. В первом случае, рисунок основы формируется через удаление излишек фольги, а во втором – меднением сквозь предварительно подготовленную маску (химический метод).
При промышленном производстве использование аддитивного подхода менее целесообразно с финансовой точки зрения – оборудование и сырье обойдутся предпринимателю в разы дороже. Потому 90% точек изготовления специализируются исключительно на субтрактивном методе производства печатных плат.
А теперь давайте более детально рассмотрим все этапы производства печатных плат – нюансы изготовления + оборудование, на котором компонент приобретает свой товарный вид.
2. Формирование заготовки платы для печати.
Заготовка формируется из фольгированного диэлектрического материала. Диэлектриком в промышленном производстве выступает стеклотекстолит (90% случаев) или текстолит с основой из ткани или бумаги.
Подбор толщины заготовки исходит из самих требований в заказе – чем выше прочность и электрическая проводимость, тем толще основа. При нецелевом производстве используется усредненный показатель толщины – оборудование настраивается на 13-14 миллиметров.
Схема формирования заготовки:
- Вырезать на оборудовании необходимую форму.
- Подготовить листы алюминиевой фольги.
- Нанести на вырезанную заготовку фольгу. Толщина нанесения зависит от целей, в которых будет использоваться плата.
Отдельную производственную группу составляют алюминиевые платы для печати – применяются они в осветительном оборудовании, когда для функционирования компонента необходимо получить проводимость через всю поверхность платы.
Алюминиевые платы делятся на два типа:
- С внешним оксидированием – сплошной оксидированный алюминиевый лист, по периметру которого располагается фольга из меди. Могут применяться и другие металлы, но для их использования требуется предварительное нанесение тонкого слоя диэлектрика.
- Полное оксидирование – рисунок оборудованием внедряется в саму основу материала, потому обработка приходится на большую часть глубины заготовки. Точное значение рассчитывается оборудованием по заданному системой шаблону.
На практике, к более экономному типу производства относится первый метод. Предприниматель сокращает затраты времени на 50-70% + не покупает дополнительные модули на оборудование.
3. Нанесение рисунка проводников платы.
Самый трудоемкий этап производства, требующий больших капиталовложений во вспомогательное сырье и оборудование.
Чтобы получить рисунок печатной платы, используют один из 3-х способов, либо их комбинацию.
Способы нанесения рисунка для проведения тока:
Химический.
Включает в себя два этапа – добавление маски на заготовку с фольгированным слоем и удаление излишков путем бомбардирования химическими частичками. Из оборудования вам здесь понадобится фоторезист, фотошаблон и источник ультрафиолетового излучения.
Фоторезистом (жидким или пленочным) заполняют всю поверхность заготовки, а потом через шаблон просвечивают ультрафиолетом дорожки электрического проводника.
Незащищенную площадь промывают химическим раствором (хлорное железо или медный купорос), после чего слой фольги снимается и остается лишь электропроводящий рисунок.
Механический.
Для реализации требуется специальное оборудование механического воздействия, которое сможет по шаблону удалить ненужные площади фольги на поверхности заготовки.
Лазерный.
Ранее, данный способ практически не использовался из-за повышенных отражающих свойств меди и алюминия. Но прогресс не стоит на месте, и в 2018 году лазерное оборудование может более тонко настраивать длину волны, что позволяет применять установки даже на поверхностях с высокими параметрами отражения.
В промышленном производстве наиболее популярным был и остается способ нанесения рисунка с использованием механического оборудования. Предпринимателю не нужно беспокоиться о массе дополнительных средств, которые требуются при химической гравировке, а использование лазерного оборудования – слишком дорогое удовольствие.
Нанесение рисунка – это только первый шаг в обработке заготовки печатной платы. Далее, элемент проходит еще четыре промежуточных технологических этапа, пока не приобретает необходимый вид.
Этап №1. Металлизация отверстий печатных плат.
Отверстия пробиваются специальным механическим или лазерным оборудованием. Второй вариант используется для более тонкой работы, когда реализовать действие при помощи механической обработки нереально с физической точки зрения.
Сама металлизация может проходит двумя путями:
Механически.
Для реализации необходимо высокоточное оборудование (для промышленного производства) и материал (электропроводящий клей или заклепки).
Данный метод очень дорогой в использовании, потому применяется лишь выборочно – для высокоточных печатных плат, либо при металлизации в домашних условиях.
Химически.
Отверстия металлизируются путем осадочного накопления на заготовке меди. Данный процесс предшествует непосредственному нанесению рисунка на саму форму.
Второй метод легко реализовать в промышленном производстве, но для домашнего использования он применяется крайне редко из-за обилия технологических нюансов и длительности.
Этап №2. Прессование плат для печати.
Используется лишь для многослойных печатных плат, которые содержат в себе более одного слоя.
Данный процесс предшествует металлизации отверстий, так как прессование уже готовых заготовок может повредить внешний слой изоляции и самих кроплений меди.
Схема прессования плат для печати в промышленном производстве:
1. Подготовка слоев, которые будут располагаться в середине и нанесение рисунка. |
2. Прессование плат в печи под давлением – в качестве прокладок используются так называемые препреги. |
3. Сверление отверстий. |
4. Металлизация. |
5. Травление фольги внешних слоев. |
Переходные отверстия могут формироваться и до прессования. Тогда, функционал печатных плат расширяется, но и стоимость производства увеличивается на 30-40%.
Использование «заглушек» требует от предпринимателя поиска разумного компромисса между рентабельностью производства и стоимостью самого процесса изготовления, включая стоимость оборудования.
Этап №3. Нанесение покрытия.
Необходимый технологический этап производства, без которого печатные платы могут с легкостью поддаваться механическим повреждениям.
Вариации покрытия плат для печати:
- Лаковые. Имеют не только защитную функцию, но и декоративную. Зеленое покрытие платы– это привычный цвет этого компонента электроники для большинства людей.
- Маркировка. Совмещает в себе декоративную функцию с информационной. Используется при производстве в больших промышленных масштабах и наносится при помощи шелкографии. Иногда может использоваться лазерное или струйное оборудование.
- Лужение проводников. Дополнительный слой, наносящийся поверх основного слоя меди на поверхности заготовки. Реализация происходит химическим методом – через ванну с припоем. Достоинство – высокая степень защиты. Недостаток – толщина заготовки, снижающая ее монтажные свойства.
- Покрытие инертными металлами. В качестве материала используется олово, палладий, реже платина и золото.
- Лакировка токопроводящим раствором. Увеличивает проводящие свойства заготовки печатной платы.
Когда платы уже монтированы, производство может дополняться еще одним защитным слоем, уменьшающим влияние внешней среды на функционал печатной платы.
Этап №4. Механическая обработка заготовки платы для печати.
Промышленное производство подразумевает изготовление множество копий печатных плат на едином листе диэлектрика.
Все описанные выше этапы лист проходит, как единое целое. Разделение на отдельные элементы происходит в самом конце процесса, с помощью специального механического оборудования.
Схема механической обработки плат для печати:
- Частичная или полная фрезеровка, в зависимости от формы платы. Для плат правильных форм (прямоугольник, квадрат) фреза делает небольшие канавки, облегчающие разламывание элементов в дальнейшем, а при неправильных формах оборудование делает сквозные линии, оставляя небольшие соединительные мосты для скрепления плат.
- Просверливание отверстий для крепежа печатной платы – количество и диаметр отверстий зависит от шаблона, по которому работает оборудование на производстве.
- Окончательное разделение плат на отдельные элементы.
Все тонкости по механической обработке печатных плат на производстве можно найти в ГОСТ 23665-79, где описаны основные рекомендации и требования к механической обработке контура и не только.
На этом производство заготовки печатной платы окончено. Однако, товар еще нельзя считать готовым. Впереди его ожидает оснащение вспомогательными микросхемами и тестирование на работоспособность.
4. Монтаж компонентов.
В основном, к «телу» все детали платы крепятся при помощи пайки. При массовом производстве используется специализированное оборудование, которое применяет групповой способ пайки.
На автоматизированном производстве ручное крепление не встречается вообще, так как использование сотрудников вместо оборудования не является оптимальным подходом к производству. Платить зарплату одному оператору автоматизированной установке намного проще, нежели целому цеху работников.
Выделяют два метода пайки:
Волновой. | Используется для выводных элементов печатных плат. Инструментом служат активаторы на механической основе, создающие одну сплошную полосу для пайки. Оборудование проводит группу плат над волной нижней стороной – пайка схватывается моментально благодаря нанесенному заранее флюсу. |
Пайка через печь. | Планарный метод пайки, при котором изначально на поверхность платы наносится специальная паяльная паста. Затем устанавливается сам компонент, и заготовка отправляется в печь, где порошок в пасте активизируется и намертво припаивается к самому элементу. Если компонент тяжелый, его садят на пару капель паяльного клея. |
По завершению пайки для очистки остатков паяльных веществ и других сопутствующих производству загрязнений на поверхность наносят растворители.
Финальный шаг – плата покрывается защитными растворами, что быстро схватываются – лак, гидрофобизаторы и тому подобное. Если планируется ее эксплуатация в условиях с повышенной вибрацией, заготовку заливают компаундом высокой вязкости.
5. Тестирование продукта.
В производстве существует несколько методик тестирования функциональности плат. Среди основных – электрические и оптические тесты.
В первом случае прослеживается наличие замыканий в системе и общая целостность электрической цепи. Оптические тесты же указывают на механические недочеты, которые могли быть допущены на различных этапах сборки.
Для оптического тестирования камеры с высоким разрешением размещают:
- при формировании рисунка на заготовке и нанесении самого контура с отверстиями;
- при пайке, а именно – на этапах дозировки паяльной пасты;
- при монтаже вспомогательных компонентов на саму заготовку;
- на выходе с паяльного оборудования – осуществляется проверка на правильность крепления элементов.
При оптическом исследовании выявляются такие дефекты, как смещение, коробление, избыток или недостаток паяльного материала, из-за чего крепление может оторваться при перенесении повышенных нагрузок.
И, как в каждом бизнесе, если вы новичок и не в курсе всех технологических особенностей производства печатных плат, то можете с легкостью допустить ошибки. Тем более, учитывая сложность самого производства, их количество может быть достаточно велико.
Типичные технологические ошибки при производстве:
- Неточный подбор диаметров отверстий для крепления компонентов. При расчетах теряется такой сопутствующий фактор производства, как металлизация. Из-за ее применения просвет уменьшится на 5-7%, потому будущий монтаж навесных компонентов будет либо сильно усложнён, либо невозможен вообще.
- Отсутствие припуска на контур. На окончательном этапе производства при обработке на механическом оборудовании габариты элемента могут уменьшаться на 2-3% (канавки для разрезания листа и другие операции). Если данный параметр вычислить неточно, размер вашей платы будет отличаться от желаемого в большую или меньшую сторону.
- Отклонения при распределении дорожек и точек для пайки. Такие отклонения могут увеличить вероятность коробления после температурной обработки в печах.
- Перенасыщение меди в точке пайки может привести к плохой заливке контакта, так как данный металл обладает хорошими теплоотводимыми свойствами. Чтобы избежать такой проблемы, вокруг точек монтажа следует оставлять небольшой термический зазор.
- Платы, которые будут лакироваться, должны заранее предоставлять информацию о компонентах, которые данной обработке не подлежат. При попадании лака на разъемы и другие чувствительные компоненты, плата становится непригодной к использованию, тем самым увеличивая процент брака с производства.
Представленные ошибки типичны, но не единственные в своем роде. Перед началом бизнеса в данной сфере вам следует очень детально изучите технологию изготовления, и определиться с направлениями в производстве.
Для каждой отрасли есть свои особенности, без учета которых количество брака продукции будет выходить за рамки 10-15%, что очень сильно ударит по карману предпринимателя.
6. Оборудование для производства печатных плат.
В 2018 году выбор оборудования по производству печатных плат очень широкий. Начинающие предприниматели могут пойти двумя путями – купить новое оборудование или поддержанное.
В первом случае, вам придется выложить кругленькую сумму, но вы получите производственные гарантии на 1-2 года + бесплатное техническое обслуживание и настройку. Новый комплект оборудования способен проработать в две смены до 10 лет с минимальными перебоями.
Второй вариант позволяет сэкономить на оборудовании до 150% от требуемого капитала, но всегда есть риск нарваться на производственное оснащение, которое на вид вроде и новое, но при постоянной нагрузке не протянет более 1 месяца.
Затраты на ремонт могут превышать половину стоимости подержанного оборудования, потому относиться к варианту закупки подержанной техники стоит с особой осторожностью.
Как минимум, требуйте от продавца предоставление гарантий на 6-10 месяцев – этого времени хватит, чтобы отбить его стоимость и накопить на новое, если с подержанным что-либо случится.
Полный список оборудования для производства плат мы подали в виде таблицы. Все цены усредненные и могут колебаться с порогом 10-15% от указанных.
Технологический процесс | Оборудование для производства печатных плат | Кол-во | Цена |
---|---|---|---|
Итого: | 64 000$ | ||
1) Участок механической обработки | |||
Нарезание заготовок из листов | Установка нарезания | 1 | 10 000$ |
Расштифтование пакета | Расштифтование | 1 | |
Сверлильный станок с ЧПУ, одно шпиндельный | Станок с ЧПУ | 1 | |
Оконтуривание/фрезерование, одно шпиндельный станок с ЧПУ | Станок с ЧПУ | 1 | |
2) Участок мокрых процессов | |||
Подготовка поверхности заготовки | Установка химической очистки | 1 | 12 000$ |
Оксидное покрытие поверхности | Установка оксидирования | 1 | |
Удаление засмаливания в отверстиях | Линия DeSmear | 1 | |
Щеточная зачистка + прочистка отверстий под давлением | Установка щеточной зачистки | 1 | |
Химическое меднение | Линия химического меднения | 1 | |
Проявление сухого пленочного фоторезиста | Установка проявления | 1 | |
Гальваническое покрытие медь/олово | Гальваническая линия | 1 | |
Снятие сухого пленочного фоторезиста | Линия снятия СПФ | 1 | |
Удаление металлорезиста (олова) | Линия удаления олова | 1 | |
Проявление | Линия проявления | 1 | |
3) Жёлтая комната | |||
Ламинирование сухим плёночным резистом. | Вальцованный ламинатор | 1 | 2 000$ |
Экспонирование сухого плёночного фоторезиста | Уст-ка УФ эксперт 8 кВт | 1 | |
4) Участок трафаретной печати | |||
Трафаретная печать | Трафаретный принтер | 1 | 6 000$ |
Нанесение надписей на плату | Трафаретный принтер | 1 | |
Промывание трафаретов | Установка промывки | 1 | |
Сушка трафаретов | Шкаф сушки | 1 | |
Заточка ракелей | Заточная установка | 1 | |
Натяжение трафарета | Установка натяжения | 1 | |
Сушка трафаретов | Сушильный шкаф | 1 | |
5) Участок контроля качества | |||
Автоматическая оптическая инспекция-АОИ | Установка АОИ | 1 | 2 000$ |
Электрическая проверка платы | Тестер «летающий зонд» | 1 | |
6) Нанесение финишного покрытия | |||
Предварительная очистка платы | Установка очистки | 1 | 8 000$ |
Покрытие оловом – горячее лужение | Установка горячего лужения | 1 | |
Отмывка платы после лужения | Установка отмывки | 1 | |
Покрытие хим. никель/золото | Погружная линия | 1 | |
Очистка ультразвуком | Установка очистки | ||
7) Участок прессования | |||
Пробивка координатных отверстий в слоях | Станок для пробивки | 1 | 24 000$ |
Сушка внутренних слоёв | Сушильный шкаф | 1 | |
Пакетирование/штифтование | Установка пакетирования | 1 | |
Прессование слоёв | Пресс | 1 | |
Водяное охлаждение | Система охлаждения воды | 1 |
Поданный комплект оборудования является наиболее полным и направлен на долгосрочное производство плат для печати. Если вы планируете постепенно расширять свой бизнес, то минимальная сумма, на которую стоит рассчитывать, – от 30 000$.
Изготовление печатных плат промышленным способом.
Что такое печатная плата? Предназначение устройства.
7. Помещение, персонал, вложения и окупаемость.
Оборудование – не единственная статья расходов, которую понесёт предприниматель, работая в сфере производства электронных компонентов. Немаловажным условием успеха является аренда помещения, соответствующего ГОСТам и общепринятым стандартам в этой отрасли.
Далеко не каждое помещение может быть использовано для производства.
Сам цех будет состоять из 2-х отделов – складского и производственного. Объем первого зависит от выработки вашего производства, а во втором случае минимальная площадь составляет не менее 75 кв. м.
Другие требования к помещению для производства:
- Качественная линия электрического питания, поддерживающая проводимость в 220 и 380 вольт.
- Вытяжка промышленной конструкции. Если обработка деталей происходит, преимущественно, химическими методами, отводящих труб может понадобиться более одной штуки.
- Оборудование для развода и поступления воздуха в сжатом виде.
- Водопровод может подойти и общего пользования. Для деминерализации жидкости устанавливается отдельное оборудование. Приготовление растворов на основании водопроводной воды не будет соответствовать технологическим нормам.
Не забывайте также, что производство печатных плат подразумевает использование химических растворов, для которых просто необходим отдельный сток.
Чтобы наладить производство в две смены при условии полной автоматизации оборудования, вам будет достаточно иметь в своем штате сотрудников четырёх операторов-универсалов, которые станут прослеживать и контролировать автоматизированный процесс производства плат для печати.
В список временного персонала входят секретарь, грузчик, маркетолог и другие специальности, услуги которых на постоянной основе частному предпринимателю попросту не пригодятся. Их наем происходит время от времени и оплачивается, как подработка.
Если дела идут в гору и у вас появляется возможность наладить производство печатных плат через дочерние отделения, стоимость таких объектов обойдется вам даже выше, нежели центрального. Всё потому, что помимо оборудования и помещения придется нанимать большее количество персонала, и делать это на постоянной основе.
Куда можно сбывать продукцию:
- электронная начинка в автомобильном производстве;
- начинка медицинского оборудования;
- отрасли, связанные с компьютерной техникой;
- крупная и мелкая бытовая техника + измерительные приборы.
Общая стоимость открытия бизнеса – не менее 75 000$. Сюда входят расходы на материалы, зарплата сотрудникам, оборудование, аренда помещений, маркетинговая кампания и дополнительные затраты при реализации.
Средняя окупаемость одной линии производства печатных плат находится на уровне 24-30 месяцев, при условии, что в вашем финансовом плане предусмотрены дополнительные статьи расходов (ремонт, обслуживание оборудования и тому подобное).
Производство печатных плат – бизнес с высокой рентабельностью, но с длительным сроком окупаемости. Не каждый готов ждать более 2-х лет, чтобы отбить собственные деньги. Однако, если дело будет иметь успех + потенциал к расширению, вы сможете сократить данный срок вдвое, а дальнейшая прибыль будет расти ежемесячно.
Полезная статья? Не пропустите новые!
Введите e-mail и получайте новые статьи на почту
biznesprost.com
Делаем настольное устройство для изготовления печатных плат в один клик / Habr
В очередной раз отмывая раковину от рыжих пятен хлорного железа, после травления платы, я подумал, что пришло время автоматизировать этот процесс. Так я начал делать устройство для изготовления плат, которое уже сейчас можно использовать для создания простейшей электроники.Ниже я расскажу о том, как делал этот девайс.
Базовый процесс изготовления печатной платы субтрактивным методом заключается в том, что на фольгированном материале удаляются ненужные участки фольги.
Сегодня большинство электронщиков используют технологии типа лазерно-утюжной для домашнего производства плат. Этот метод предполагает удаление ненужных участков фольги с использованием химического раствора, который разъедает фольгу в ненужных местах. Первые эксперименты с ЛУТом несколько лет назад показали мне, что в этой технологии полно мелочей, порой напрочь мешающих достижению приемлемого результата. Тут и подготовка поверхности платы, и выбор бумаги или иного материала для печати, и температура в совокупности со временем нагрева, а также особенности смывки остатков глянцевого слоя. Также приходится работать с химией, а это не всегда удобно и полезно в домашних условиях.
Мне хотелось поставить на стол некоторое устройство, в которое как в принтер можно отправить исходник платы, нажать кнопку и через какое-то время получить готовую плату.
Немного погуглив можно узнать, что люди, начиная с 70х годов прошлого века, начали разрабатывать настольные устройства для изготовления печатных плат. Первым делом появились фрезерные станки для печатных плат, которые вырезали дорожки на фольгированном текстолите специальной фрезой. Суть технологии заключается в том, что на высоких оборотах фреза, закрепленная на жёстком и точном координатном столе с ЧПУ срезает слой фольги в нужных местах.
Желание немедленно купить специализированный станок прошло после изучения цен от поставщика. Выкладывать такие деньги за устройство я, как и большинство хоббийщиков, не готов. Поэтому решено было сделать станок самостоятельно.
Понятно, что устройство должно состоять из координатного стола, перемещающего режущий инструмент в нужную точку и самого режущего устройства.
В интернете достаточно примеров того, как сделать координатный стол на любой вкус. Например те же RepRap справляются с этой задачей (с поправками на точность).
С одного из моих предыдущих хобби-проектов по созданию плоттера у меня остался самодельный координатный стол. Поэтому основная задача заключалась в создании режущего инструмента.
Вполне логичным шагом могло стать оснащение плоттера миниатюрным гравером вроде Dremel. Но проблема в том, что плоттер, который можно дешево собрать в домашних условиях сложно сделать с необходимой жесткостью, параллельностью его плоскости к плоскости текстолита (при этом даже текстолит сам по себе может быть изогнутым). В итоге вырезать на нём платы более менее хорошего качества не представлялось бы возможным. К тому же не в пользу использования фрезерной обработки говорил тот факт, что фреза тупится со временем и утрачивает свои режущие свойства. Вот было бы здорово, если бы медь с поверхности текстолита можно было удалять бесконтактным способом.
Уже существуют лазерные станки немецкого производителя LPKF, в которых фольга просто испаряется мощным полупроводниковым лазером инфракрасного диапазона. Станки отличаются точностью и скоростью обработки, но их цена ещё выше чем у фрезерных, а собрать из доступных всем материалов такую вещь и как-то её удешевить пока не представляется простой задачей.
Из всего вышесказанного я сформировал некоторые требования к желаемому устройству:
- Цена сопоставимая со стоимостью среднего домашнего 3д-принтера
- Бесконтактное удаление меди
- Возможность собрать устройство из доступных компонентов самостоятельно в домашних условиях
Так я начал размышлять о возможной альтернативе лазеру в области бесконтактного удаления меди с текстолита. И наткнулся на метод электроискровой обработки, который давно применяется в металлообработке для изготовления точных металлических деталей.
При таком методе металл удаляется электрическими разрядами, которые испаряют и разбрызгивают его с поверхности заготовки. Таким образом образуются кратеры, размер которых зависит от энергии разряда, его длительности и, конечно же, типа материала заготовки. В простейшем виде электрическую эрозию стали использовать в 40-х года XX века для пробивания отверстий в металлических деталях. В отличие от традиционной механической обработки отверстия можно было получить практически любой формы. В настоящее время данный метод активно применяется в металлообработке и породил целую серию видов станков.
Обязательной частью таких станков является генератор импульсов тока, система подачи и перемещения электрода — именно электрод (обычно медный, латунный или графитовый) является рабочим инструментом такого станка. Простейший генератор импульсов тока представляет собой простой конденсатор нужного номинала, подключенный к источнику постоянного напряжения через токоограничивающий резистор. При этом емкость и напряжение определяют энергию разряда, которая в свою очередь определяет размеры кратеров, а значит и чистоту обработки. Правда есть один существенный нюанс — напряжение на конденсаторе в рабочем режиме определяется напряжением пробоя. Последнее же практически линейно зависит от зазора между электродом и заготовкой.
За вечер был изготовлен прототип эрозионного инструмента, представляющий собой соленоид, к якорю которого прикреплена медная проволочка. Соленоид обеспечивал вибрацию проволоки и прерывание контакта. В качестве источника питания был использован ЛАТР: выпрямленный ток заряжал конденсатор, а переменный питал соленоид. Эта конструкция была также закреплена в держателе ручки плоттера. В целом, результат оправдал ожидания, и головка оставляла на фольге сплошные полосы со рваными краями.
Способ явно имел право на жизнь, но требовалось решить одну задачу — компенсировать расход проволоки, которая расходуется при работе. Для этого требовалось создать механизм подачи и блок управления для него.
После этого, всё свободное время я начал проводить в одном из хакспейсов нашего города, где есть станки для металлообработки. Начались продолжительные попытки сделать приемлемое режущее устройство. Эрозионная головка состояла из пары шток-втулка, обеспечивающих вертикальную вибрацию, возвратной пружины и протяжного механизма. Для управления соленоидом потребовалось изготовить несложную схему состоящую из генератора импульса заданной длины на NE555, MOSFET-транзистора и индуктивного датчика тока. Первоначально предполагалось использовать режим автоколебаний, то есть подавать импульс на ключ сразу после импульса тока. При этом частота колебаний зависит от величины зазора и управление приводом производится согласно измерению периода автоколебаний. Однако стабильный автоколебательный режим оказался возможен в диапазоне амплитуд колебания головки, который составлял меньше половины максимального. Поэтому я принял решение использовать фиксированную частоту колебаний, генерируемых аппаратным ШИМом. При этом о состоянии зазора между проволокой и платой можно судить по времени между окончанием открывающего импульса и первым импульсом тока. Для большей стабильности при работе и улучшении частотных характеристик соленоид был закреплен над механизмом протяжки проволоки, а якорь размещен на дюралевой скобе. После этих доработок удалось добиться устойчивой работы на частотах до 35 Гц.
Закрепив режущую головку на плоттере, я начал опыты по прорезанию изолирующих дорожек на печатных платах. Первый результат достигнут и головка более-менее устойчиво обеспечивает непрерывный рез. Вот видео, демонстрирующее что получилось:
Принципиальная возможность изготавливать платы при помощи электроискровой обработки подтверждена. В ближайших планах повысить точность, увеличить скорость обработки и чистоту реза, а также выложить часть наработок в открытый доступ. Также планирую адаптировать модуль под использование с RepRap. Буду рад идеям и замечаниям в комментариях.
habr.com
Изготовление печатных плат на ЧПУ станке*
ЧПУ станок очень удобно использовать в домашней радиолюбительской мастерской для изготовления печатных плат как макетов изделий, так и малых партий изделий. Наличие гравировально – фрезерного ЧПУ в домашней мастерской или малом предприятии позволяет как сократить время необходимое на изготовление печатной платы при изготовлении макетов, прототипов малых партий продукции, так и повысить качество изготавливаемых печатных плат по сравнению с другими способами изготовления. Использование станка с числовым программным управлением позволяет выполнять полный спектр операций по изготовлению печатной платы — фрезеровку проводящего рисунка (дорожек), сверление отверстий как для установки компонентов так и для межслойных переходов, обрезки и платы по контуру.
Для начала необходимо создать проект печатной платы. Для этого очень удобно использовать очень популярную в среде радиолюбителей программу Sprint Layout 6. При разработке нужно учитывать технологические особенности обработки фольгированного текстолита на станке с чпу, то есть производить трассировку достаточно широкими дорожками, оставляя необходимые зазоры для прохождения гравера/фрезы и т.д. Точкой начала отсчета координат необходимо выбрать ЛЕВЫЙ НИЖНИЙ УГОЛ, рисунок 1.
рисунок1
На слое О рисуем контур (границы) печатной платы по которым будет производиться обрезка готовой платы. Толщину линий указываем в зависимости от диаметра используемой для обрезки платы фрезы. Контролируем, зазор между краем платы и дорожками, чтобы контур не пересекалися с дорожками. Для того, чтобы плата после вырезки по не была выброшена из заготовки и не повредилась фрезой, оставляем перемычки, на которых плата будет держаться в заготовке. Их легко можно будет потом перекусить бокорезами при извлечении готовой платы. Выключаем лишние слои и предварительно осматриваем плату, рисунок 2.
рисунок 2
Открываем окно настройки «стратегий» фрезеровки, рисуноки 3 и 4.
рисунок 3
рисунок 4
В оконе «ширина дорожки» (рисунок 4) указываем толщину нашего режущего инструмента. Например гравер с режущим кончиком 0,6мм. Для удобства дальнейшей обработки ставим галочку «наметить отверстия». Нажимаем «Ок». Сохраняем в удобном для нас месте рисунок 5.
рисунок 5
После вычисления траектории обработки плата будет выглядеть следующим образом , рисунок 6:
рисунок 6
Наглядно можно отследить путь прохождения фрезы и количество меди, которое она снимет. Для удобства отображения траектории движения фрезы тонкой линией можно нажать выделенную кнопку, рисунок 7:
рисунок 7
На данном этапе необходимо внимательно отследить траекторию движения фрезы — проконтролировать отсутствие замыкания между проводящими дорожеками не принадлежащими к одоимённой цепи . При выявлении ошибки – исправить и пересохранить файл.
Далее необходимо подготовить управляющую программу, для станка. С помощью утилиты Step Cam 1.79 (скачать можно в интернете) открываем наш файл фрезеровки, производим настройку рабочей подачи и глубины резания (зависит от использумого станка, инструмента и материала) и конвертируем в G-code, нажав клавишу Make G-code. Программа на основе файла фрезеровки сгенерирует G-код обработки. Увидеть результат генерации G-кода можно с помощью вкладки Action -> Draw G-code. Если ничего не отобразится – нужно кликнуть мышью в окошке, рисунок 8.
Опытным путем подбиаем глубину фрезеровки, стараясь настроить станок так, чтобы фреза/гравер снимал только слой меди, с небольшим перерезанием. Данный параметр зависит от толщины медной фольги фольги используемого текстолита.
рисунок 8
Нажимаем Save G-code. Файл готов.
Загружаем файл в Mach4,проводим визуальный контроль загруженного файла. Выставляем нули на станке, запускаем обработку.
Для сверлнения отверстий в плате и вырезания по контуру настройка и подготовка файлов аналогична. Примерные настройки указаны на рисунках 9 и 10.
Сверление рисунок 9:
рисунок 9
Фрезеровка платы по контуру, рисунок 10:
рисунок 10
Сохраняем настройки для сверления и фрезеровки контура отдельно. Загружаем в Step Cam. Указываем глубину обработки, в зависимости от толщины используемого текстолита, с небольшим перерезанием. К примеру при толщине текстолита 1,5 мм выставляем для сверления 1,6-1,7 мм. Фрезеровку по контуру желательно выполнять в 2 – 4 прохода, в зависимоти от характеристик режущего инструмента. Для этого задаем в Step Cam глубину погружения при фрезеровке 0,5 мм, а затем после каждого прохода на станке вручную опускаем по оси «Z» инструмент и обнуляем.
Некоторые нюансы работы на станке при изготовлении печатной платы:
1. Поверхность рабочего стола должна быть максимально плоской и ровной. Один из вариантов добиться этого – сделать «жертвенный стол» из фанеры и отторцевать его. Для этого к основному рабочему столу станка крепится лист фанеры, а затем с помощью крупной фрезы фрезеруется «ложе» под плату на небольшую глубину (1-2мм).
2. Стеклотекстолит не всегда идеально ровный материал, и толщина его тоже может варьироваться. Поэтому резать необходимо с небольшим перерезанием. Некоторые опытные люди специально составляют карты высот, для более точной обработки. Степень перерезания определяется опытным путем.
3. Для фрезеровки можно использовать гравер типа «пирамидка» с кончиком от 0,4 до 1мм. Для сверления существуют сверла на 0,8-1,5мм с хвостовиком под стандартную цангу 3,175мм. Вырезать по контуру лучше всего фрезой «кукуруза» 2-3мм.
4. Инструмент каждый раз меняется вручную. Для этого после выполнения, например фрезеровки дорожек, останавливаем шпиндель, станок оставляем в режиме удержания. Поднимаем режущий инструмент на удобную для замены высоту, меняем. После этого производим выставление нуля по оси «Z». И так при каждой смене инструмента. Координаты X и Y не обнуляем.
5. Не забываем, что стеклотекстолит не самый полезный материал для организма. Особенно вредна пыль текстолита для дыхательных путей. Поэтому желательно организовать вытяжку или иным другим способом удалять лишнюю пыль из области резки. Можно например периодически смачивать печатную плату водой или друой подходящей жидкостью, с помощью медицинского шприца. Неплохо с задачей защиты дыхательных путей справится влажная повязка на нос/рот или респиратор.
!Статья носит ознакомительный характер, основана на личном опыте автора и не является единственно верным и возможным решением.
Фрезеровка проводников печатных плат
cncmodelist.ru
Станок для изготовления печатных плат
Оборудование для производства печатных плат
ВАЖНО! Изготовление печатных плат на станках серии HIGH-Z — весьма точный и быстрый процесс. CNC станки HIGH-Z — это лучшее на сегодня оборудование для производства печатных плат. Наши станки могут одновременно фрезеровать проводящую полосу и сверлить отверстия! Технология изготовления печатных плат на cnc станках HIGH-Z позволяет добиваться весьма высокой точности фрезерования — 0,02 миллиметра. Оснащение для производства печатных плат имеет небольшие размеры.
Главная / Области применения /
|
|
ООО «Си-Эн-Си Машин» поставляет лучшее немецкое оборудование для производства печатных плат — станки с ЧПУ серии HIGH-Z и Raptor. Мы — официальный дистрибьтор этих станков в России.
Технология изготовления печатных плат на cnc станке HIGH-Z
Вы проектируете свою печатную плату, например, в PCAD, сохраняете файл как .plt-файл (HPGL). Далее нужно запустить программу PCNC (поставляется в комплекте).
Для опытных образцов или маленьких серий очень существенно иметь возможность фрезеровки печатных плат. Гравировально-фрезерные cnc станки HIGH-Z имеют возможность фрезеровать проводящую полосу с точностью приблизительно 0,1 — 0,15 мм.
Возможно, Вы знаете на личном опыте, как неудобно отсутствие возможности фрезерования и какое дополнительное оборудование необходимо, чтобы фрезеровать печатные платы самостоятельно.
Оборудование для прототипирования печатных плат
На фрезерных станках с ЧПУ серии HIGH-Z можно изготавливать прототипы печатных плат для мелкосерийных производств из таких материалов как алюминий, текстолит, стеклотекстолит, лавсан и др. волокнистых материалов.
Возможность изготавливать двусторонние печатные платы. Это видео пермской компании ООО «Уралинтелком» демонстрирует процесс производства двусторонней печатной платы со всеми необходимыми операциями: фрезеровка дорожек, сверловка отверстий, обрезка печатной платы на станке HIGH-ZS-400. Также возможно, при необходимости, наносить на плату клеевые составы.
Для производства печатных плат обязательной опцией является механический регулятор глубины, подпружиненный механизм которого считывает неровность поверхности, тем самым, обработка материала производится на четко заданную глубину.
Преимущество cnc станка HIGH-Z:
Станок фрезерует проводящую полосу и сверлит отверстия в одно и тоже время! Посмотрите результат фрезеровки печатной платы на фотографиях и видео.
Фрезеровка проводящей полосы на 0,2 мм глубиной
Фрезеровка печатной платы в сложном материале
Для производства печатных плат и других изделий со сложной конфигурацией, для фрезеровки любых материалов. Используются фрезерно-гравировальные cnc-станки High-Z. Результат, главным образом, зависит от выбора материала и сокращения геометрии используемого инструмента.
Печатная плата с медью
Фрезеровка: алюминиевый сайдинг
Для фрезеровки алюминиевого сайдинга со вспененным материалом внутри есть специальная фреза.
Фрезеровка и сверление печатных плат — это всего лишь одна из многих отраслей применения наших станков.
Купить оборудование для производства печатных плат
Компаниям г. Санкт-Петербурга: предлагаем станки для изготовления печатных плат.
Заказать фрезерно-гравировальные станки для производства печатных плат с доставкой в любой город России или СНГ можно по телефонам: +(351) 220-09-50, +7 (912) 772-60-57. Предварительный заказ on-line: купить станок с чпу
Процесс прототипирования и изготовления печатной платы на немецком станке HIGH-Z или Raptor — это действительно профессиональный подход к производству. Качество немецкого оборудования обеспечит надёжную и бесперебойную эксплуатацию. Наши специалисты проконсультируют Вас по работе станка, обеспечат всей необходимой документацией. Мы также разрабатываем управляющие программы для CNC станков и осуществляем поставку дополнительного оборудования.
www.cnc-machine.ru
Изготовление печатных плат на чпу станке
ЧПУ станок очень удобно использовать в домашней радиолюбительской мастерской для изготовления печатных плат как макетов изделий, так и малых партий изделий. Наличие гравировально – фрезерного ЧПУ в домашней мастерской или малом предприятии позволяет как сократить время необходимое на изготовление печатной платы при изготовлении макетов, прототипов малых партий продукции, так и повысить качество изготавливаемых печатных плат по сравнению с другими способами изготовления. Использование станка с числовым программным управлением позволяет выполнять полный спектр операций по изготовлению печатной платы — фрезеровку проводящего рисунка (дорожек), сверление отверстий как для установки компонентов так и для межслойных переходов, обрезки и платы по контуру.
Для начала необходимо создать проект печатной платы. Для этого очень удобно использовать очень популярную в среде радиолюбителей программу Sprint Layout 6. При разработке нужно учитывать технологические особенности обработки фольгированного текстолита на станке с чпу, то есть производить трассировку достаточно широкими дорожками, оставляя необходимые зазоры для прохождения гравера/фрезы и т.д. Точкой начала отсчета координат необходимо выбрать ЛЕВЫЙ НИЖНИЙ УГОЛ, рисунок 1.
рисунок1
На слое О рисуем контур (границы) печатной платы по которым будет производиться обрезка готовой платы. Толщину линий указываем в зависимости от диаметра используемой для обрезки платы фрезы. Контролируем, зазор между краем платы и дорожками, чтобы контур не пересекалися с дорожками. Для того, чтобы плата после вырезки по не была выброшена из заготовки и не повредилась фрезой, оставляем перемычки, на которых плата будет держаться в заготовке. Их легко можно будет потом перекусить бокорезами при извлечении готовой платы. Выключаем лишние слои и предварительно осматриваем плату, рисунок 2.
рисунок 2
Открываем окно настройки «стратегий» фрезеровки, рисуноки 3 и 4.
рисунок 3
рисунок 4
В оконе «ширина дорожки» (рисунок 4) указываем толщину нашего режущего инструмента. Например гр
i-perf.ru
Как выбрать оборудование для производства печатных плат? :: BusinessMan.ru
По какому принципу целесообразно выбирать оборудование для производства печатных плат? Попробуем разобраться в этом в данной статье.
Изготовление печатных плат – как бизнес или для собственных нужд
Итак, в первую очередь необходимо руководителю фирмы решить – изготавливать печатные платы для собственного потребления или на этом строить бизнес. От этого зависит, какое оборудование для производства печатных плат необходимо приобрести. Так, внутреннее потребление будет требовать небольшого объема такого изготовления. Если же это будет основным видом деятельности, то нужно позаботиться о том, чтобы приобрести достаточно дорогостоящий станок для производства печатных плат.
Автоматизация производства – обязательное условие данной отрасли
Такой принцип обеспечит высококлассное оборудование для производства печатных плат. Это необходимо не только для снижения затрат на дополнительную численность персонала, но и для обеспечения максимального снижения риска влияния человеческого фактора на качество готовой продукции с целью автоматического управления производством (ведение электронного документооборота, электронной диспетчеризации и логистики).
Правильно подобранное оборудование для производства печатных плат позволит существенно снизить риск загрязнения экологии. Так, данный процесс зачастую связан с достаточно агрессивными стоками, если вовремя не принять специальные меры.
Конечно, нельзя забывать и о планировании своего будущего. В этом помогут новые технологии, внедрение которых можно заменить обычной модернизацией функционирующего уже на предприятии оборудования.
Технологии производства печатных плат
На самом деле, существует несколько технологий такого производства. Рассмотрим некоторые из них. Так, например, это тентинг-процесс, которые содержит, по сравнению с другими технологиями, меньше операций и требует оборудования попроще. Однако если использовать фольгированный алюминий для производства печатных плат, его осаждение и травление зачастую способствуют возникновению большого количества брака. Возможность несовмещения рисунков пленочного фоторезиста с необходимыми отверстиями способствует осторожности в оценке его преимуществ.
Существует и другая технология производства печатных плат – процесс прямой металлизации. В современном производстве при использовании субтрактивных методов (травления фольги) указанный процесс является достаточно прогрессивным. При использовании данной технологии производители избавляются от необходимости химического меднения и гальванической затяжки, что существенно повышает надежность всех внутренних межсоединений на печатной плате.
Однако если требуется высококачественное разрешение рисунка, то производителю нужно будет использовать химическое меднение.
В последние годы довольно успешно используются лазерные методы формирования рисунков с помощью испарений меди из зазоров. Данный процесс связан с боковым подтравливанием. При этом размер зазора в рисунках определяется длиной волн и апертурой оптических систем, выделяющих область энергии из излучения. Таким образом, с помощью лазерного метода можно делать толстые проводники. К примеру, ультрафиолетовые лазеры в медном покрытии воспроизводят зазор шириной до 20 мкм. При этом до основания освободить от меди зазор невозможно, так как при утончении фольги начинает нагреваться диэлектрик у основания и может произойти тепловой взрыв под фольгой. Именно поэтому данный процесс не доводят до самого конца, а оставляют около 3 мкм металла, который впоследствии вытравливают дифференциальным способом.
Преимущество полуаддитивного метода – лучшее разрешение рисунка. Однако многие производители печатных плат не спешат его использовать, так как субтрактивный метод гарантирует большую устойчивость при обеспечении адгезии меди с подложками.
Комплектование процесса производства
Оборудование для гальванических и химических процессов ориентируется на конкретный набор химикатов, которые используются при прямой металлизации, иммерсионных процессах, для гальваники и прочих концентратов, их применение избавляет данное производство от необходимости проведения химических анализов.
Достаточно высокая производительность у растровых лазерных фотоплоттеров обеспечивается фотошаблонами, что позволяет организовать трехсменную работу производства. Другими словами, изготавливать рабочие фотошаблоны сразу без фотооригиналов. Таким образом будут устранены существенные потери времени.
Вывод
С внедрением технологических новшеств требуются соответствующие доработки в существующих технологиях и модернизация действующего оборудования производства печатных плат. Это приводит к активному заимствованию эффективных зарубежных технических решений. Прослеживается постоянно возрастающий интерес со стороны инвесторов к вложению капитала в данное производство.
businessman.ru
экскурсия на завод Технотех / Madrobots corporate blog / Habr
Сегодня мы выступим в немного непривычном для себя амплуа, будем рассказывать не о гаджетах, а о технологиях, которые стоят за ними. Месяц назад мы были в Казани, где познакомились с ребятами из Навигатор-кампуса. Заодно побывали на расположенном близко (ну, относительно близко) заводе по производству печатных плат — Технотех. Этот пост — попытка разобраться в том, как же все-таки производят те самые печатные платы.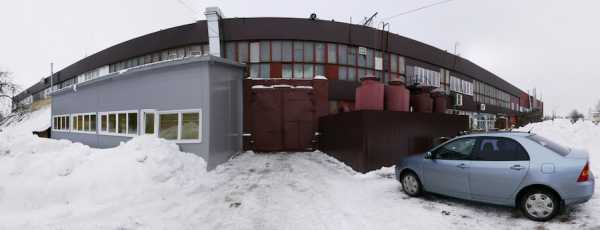
Итак, как же все-таки делают печатные платы для наших любимых гаджетов?
На заводе умеют делать платы от начала и до конца — проектирование платы по вашему ТЗ, изготовление стеклотекстолита, производство односторонних и двухсторонних печатных плат, производство многослойных печатных плат, маркировка, проверка, ручная и автоматическая сборка и пайка плат.
Для начала, я покажу, как делают двухсторонние платы. Их техпроцесс ничем не отличается от производства односторонних печатных плат, кроме того, что при изготовлении ОПП не производят операции на второй стороне.
О методах изготовления плат
Вообще, все методы изготовления печатных плат можно разделить на две большие категории: аддитивные(от латинского additio -прибавление) и субтрактивные (от латинского subtratio—отнимание). Примером субтрактивной технологии является всем известный ЛУТ(Лазерно-утюжная технология) и его вариации. В процессе создания печатной платы по этой технологии мы защищаем будущие дорожки на листе стеклотекстолита тонером от лазерного принтера, а затем стравливаем все ненужное в хлорном железе.В аддитивных методах проводящие дорожки, наоборот, наносятся на поверхность диэлектрика тем или иным способом.
Полуаддитивные методы(иногда их еще называют комбинированными. ) — нечто среднее между классическими аддитивными и субтрактивными. В процессе производства ПП по этому методу часть проводящего покрытия может стравливаться(иногда почти сразу после нанесения), но как правило это происходит быстрее/проще/дешевле, чем в субтрактивных методах. В большинстве случаев, это следствие того, что большая часть толщины дорожек наращивается гальваникой или химическими методами, а слой, который подвергается травлению — тонкий, и служит лишь в качестве проводящего покрытия для гальванического осаждения.
Я покажу именно комбинированный метод.
Изготовление двухслойных печатных плат по комбинированному позитивному методу(полуаддитивный метод)
Изготовление стеклотекстолита
Процесс начинается с изготовления фольгированного стеклотекстолита. Стеклотекстолит — это материал, состоящий из тонких листов стекловолокна(они похожи на плотную блестящую ткань), пропитанных эпоксидной смолой и спрессованных стопкой в лист. Сами полотна стекловолокна тоже не слишком просты — это плетеные(как обычная ткань в вашей рубашке) тонкие-тонкие нити обычного стекла. Они настолько тонкие, что могут легко гнуться в любых направлениях. Выглядит это примерно вот так:
Увидеть ориентацию волокон можно на многострадальной картинке из википедии:
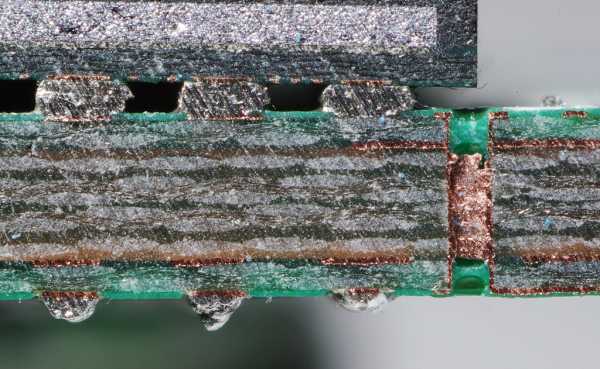
В центре платы, светлые участки — это волокна идут перпендикулярно срезу, участки чуть темнее — параллельно.
Или например на микрофотографии tiberius, насколько я помню из этой статьи:

Итак, начнем.
Стекловолоконное полотно поступает на производство вот в таких бобинах:
Оно уже пропитано частично отвержденной эпоксидной смолой — такой материал называется препрегом, от английского pre-impregnated — предварительно пропитанный. Так как смола уже частично отверждена, она уже не такая липкая, как в жидком состоянии — листы можно брать руками, совсем не опасаясь испачкаться в смоле. Смола станет жидкой только при нагреве фольги, и то лишь на несколько минут, прежде чем застыть окончательно.
Нужное количество слоев вместе с медной фольгой собирается вот на этом аппарате:
А вот сам рулон фольги.
Далее полотно нарезается на части и поступает в пресс высотой в два человеческих роста:
На фото Владимир Потапенко, начальник производства.
Интересно реализована технология нагрева во время прессования: нагреваются не части пресса, а сама фольга. На обе стороны листа подается ток, который за счет сопротивления фольги нагревает лист будущего стеклотекстолита. Прессование происходит при сильно пониженном давлении, для исключения появления воздушных пузырей внутри текстолита
При прессовании, за счет нагрева и давления, смола размягчается, заполняет пустоты и после полимеризации получается единый лист.
Вот такой:
Он нарезается на заготовки для плат специальным станком:
Технотех использует два вида заготовок: 305х450 — маленькая групповая заготовка, 457х610 — большая заготовка
После этого к каждому комплекту заготовок распечатывается маршрутная карта, и путешествие начинается…
Маршрутная карта — это вот такая бумажка с перечнем операций, информацией о плате и штрих-кодом. Для контроля выполнения операций используется 1С 8, в которую внесена вся информация о заказах, о техпроцессе и так далее. После выполнения очередного этапа производства сканируется штрихкод на маршрутном листе и заносится в базу.
Сверловка заготовок
Первый этап производства однослойных и двухслойных печатных плат — сверление отверстий. С многослойными платами все сложнее, и я расскажу об этом позже. Заготовки с маршрутными листами поступают на участок сверловки: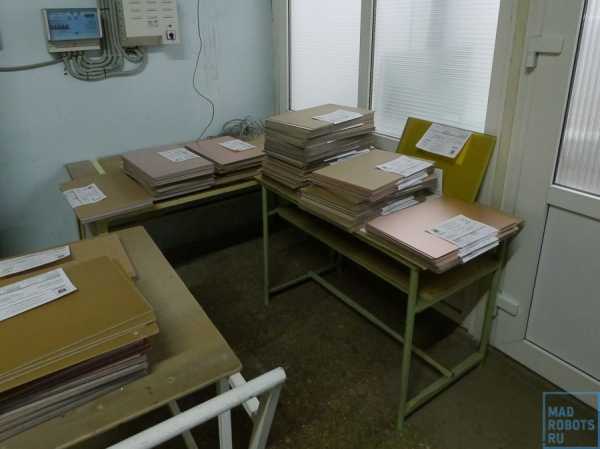
Из заготовок собирается пакет для сверловки. Он состоит из подложки(материал типа фанеры), от одной до трех одинаковых заготовок печатных плат и алюминиевой фольги. Фольга нужна для определения касания сверла поверхности заготовки — так станок определяет поломку сверла. Еще при каждом захвате сверла он контролирует его длину и заточку лазером.

После сборки пакета он закладывается вот в этот станок:
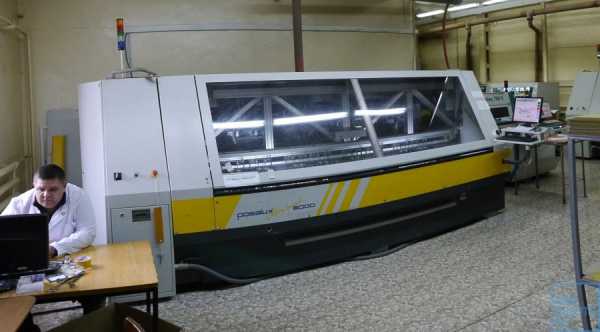
Он такой длинный, что мне пришлось сшивать эту фотку из нескольких кадров. Это швейцарский станок фирмы Posalux, точной модели, к сожалению не знаю. По характеристикам он близок вот к этому. Он ест

Программа разрабатывается отдельно, и подгружается по сети. Все что надо сделать оператору — отсканировать штрихкод партии и заложить пакет из заготовок внутрь. Емкость инструментального магазина: 6000 сверл или фрез.
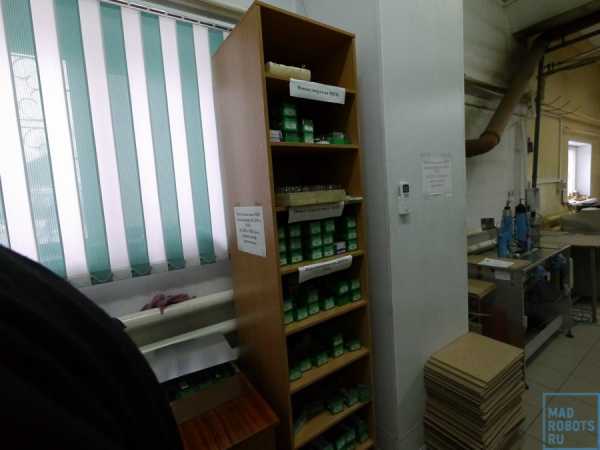
Рядом стоит большой шкаф со сверлами, но оператору нет необходимости контролировать заточку каждого сверла и менять его — станок все время знает степень износа сверл — записывает себе в память сколько отверстий было просверлено каждым сверлом. При исчерпании ресурса сам меняет сверло на новое, старые сверла останется выгрузить из контейнера и отправить на повторную заточку.
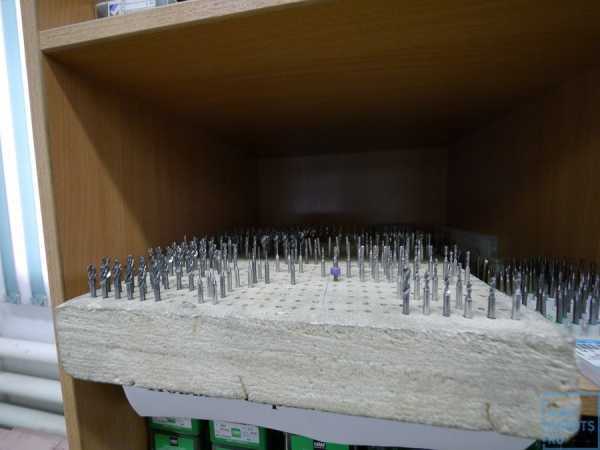
Вот так выглядят внутренности станка:
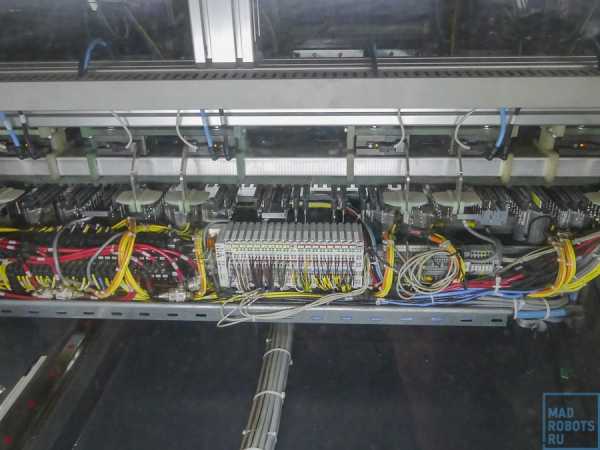
После сверловки в маршрутном листе и базе делается отметка, а плата отправляется

Очистка, активация заготовок и химическое меднение.
Хоть станок и пользуется своими «пылесосом» во время и после сверловки, поверхность платы и отверстий все равно надо очистить от загрязнений и подготовить к следующей технологической операции. Для начала, плата просто очищается в моющем растворе механическими абразивами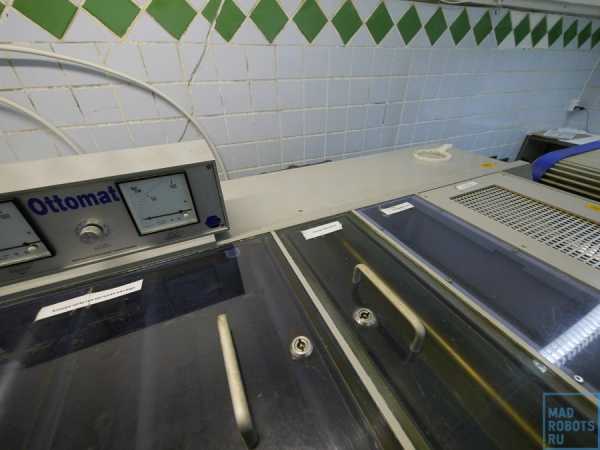
Надписи, слева направо: «Камера зачистки щетками верх/низ», «Камера промывки», «Нейтральная зона».
Плата становится чистой и блестящей:
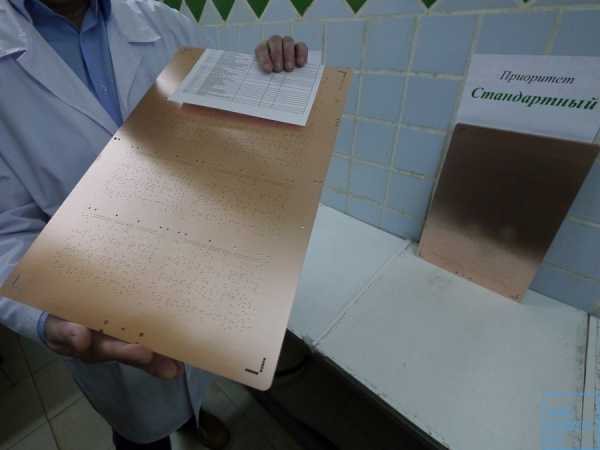
После этого в похожей установке проводится процесс активации поверхности.

После этого, последовательно проходя несколько ванн в еще одной похожей установке заготовка обзаводится тонким(меньше микрона) слоем меди в отверстиях.
Дальше этот слой гальваникой наращивается до 3-5 микрон — это улучшает стойкость слоя к окислению и повреждениям.
Нанесение и экспонирование фоторезиста, удаление незасвеченных участков.
Дальше плата отправляется в участок нанесения фоторезиста. Нас туда не пустили, потому что он закрыт, и вообще, там чистая комната, поэтому ограничимся фотографиями через стекло. Нечто подобное я видел в Half-Life(я про трубы, спускающиеся с потолка):
Собственно вот зеленая пленка на барабане — это и есть фоторезист.

Далее, слева направо(на первой фотографии): две установки нанесения фоторезиста, дальше автоматическая и ручная рамы для засветки по заранее подготовленным фотошаблонам. В автоматической раме присутствует контроль, который учитывает допуск по совмещению с реперными точками и отверстиями. В ручной рамке маска и плата совмещаются руками. На этих же рамах экспонируется шелкография и паяльная маска. Дальше — установка проявки и отмывки плат, но так как мы туда не попали, фотографий этой части у меня нет. Но там ничего интересного — примерно такой же конвейер как в «активации», где заготовка проходит последовательно несколько ванн с разными растворами.
А на переднем плане — огромный принтер, который эти самые фотошаблоны печатает:
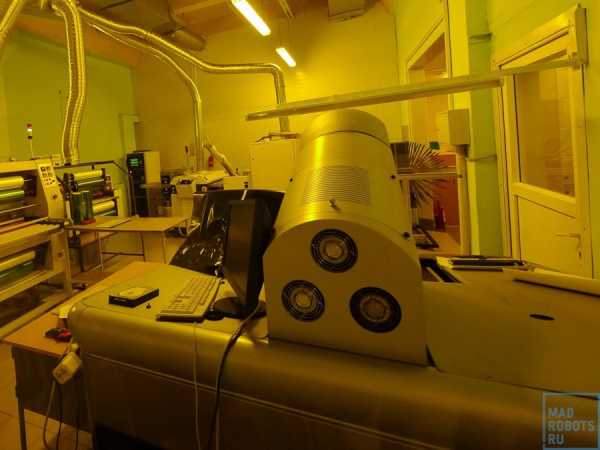
Вот плата с нанесенным, экспонированным и проявленным:
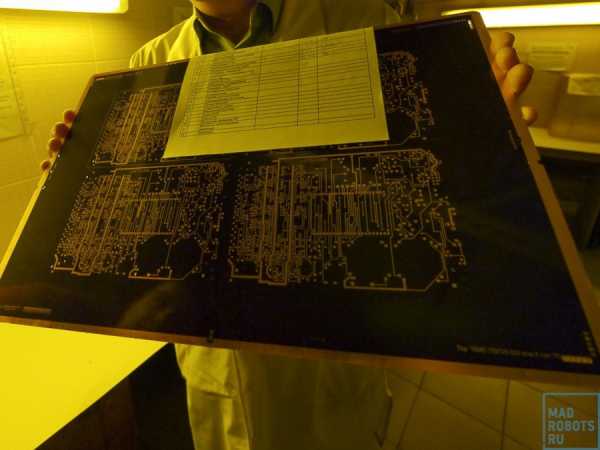
Обратите внимание, фоторезист нанесен на места, на которых в дальнейшем не будет меди — маска негативная, а не позитивная, как в в ЛУТ-е или домашнем фоторезисте. Это потому, что в дальнейшем наращивание будет происходить в местах будущих дорожек.
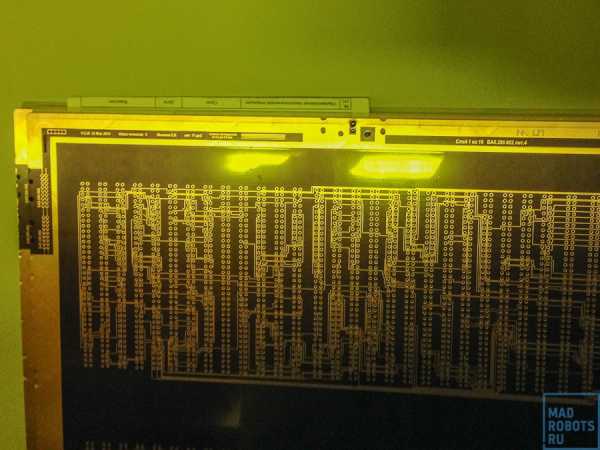
Это тоже позитивная маска:
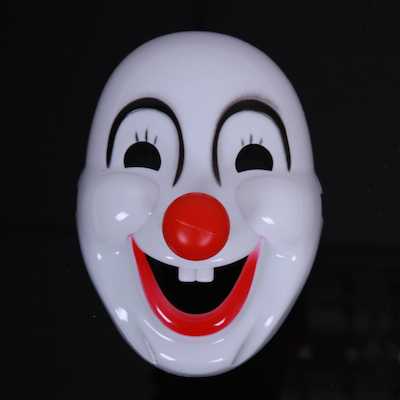
Все эти операции происходят при неактиничном освещении, спектр которого подобран таким образом, чтобы одновременно не оказывать влияния на фоторезист и давать максимальную освещенность для работы человека в данном помещении.
Люблю объявления, смысл которых я не понимаю:

Гальваническая металлизация
Теперь настал через ее величества — гальванической металлизации. На самом деле, ее уже проводили на прошлом этапе, когда наращивали тонкий слой химической меди. Но теперь слой будет наращён еще больше — с 3 микрон до 25. Это уже тот слой, который проводит основной ток в переходных отверстиях. Делается это вот в таких ваннах: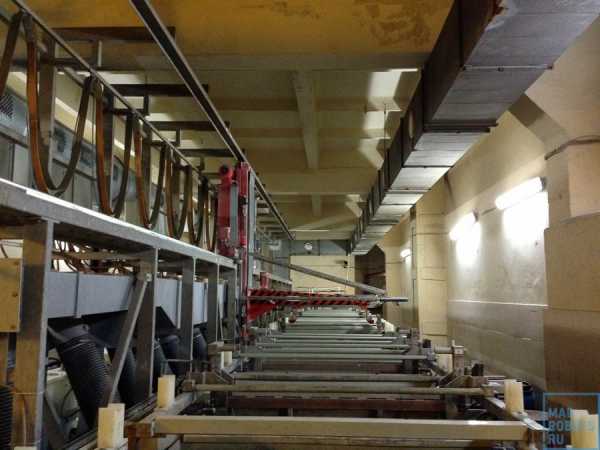
В которых циркулируют сложные составы электролитов:

А специальный робот, повинуясь заложенной программе, таскает платы из одной ванны в другую:
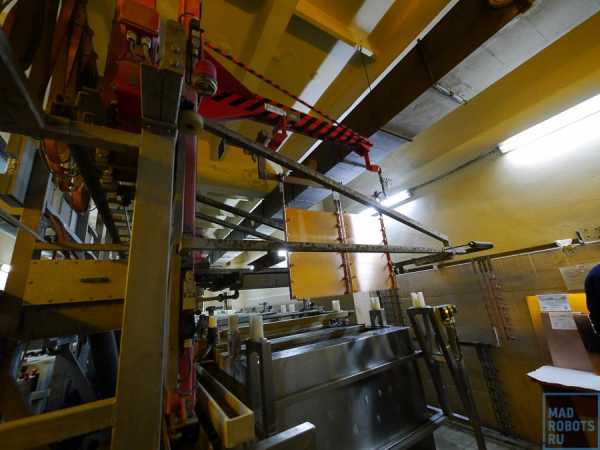
Один цикл меднения занимает 1 час 40 минут. В одной паллете могут обрабатываться 4 заготовки, но в ванне таких паллет может быть несколько.
Осаждение металлорезиста
Следующая операция представляет собой еще одну гальваническую металлизацию, только теперь осаждаемый материал не медь, а ПОС — припой свинец-олово. А само покрытие, по аналогии с фоторезистом называется металлорезистом. Платы устанавливаются в раму: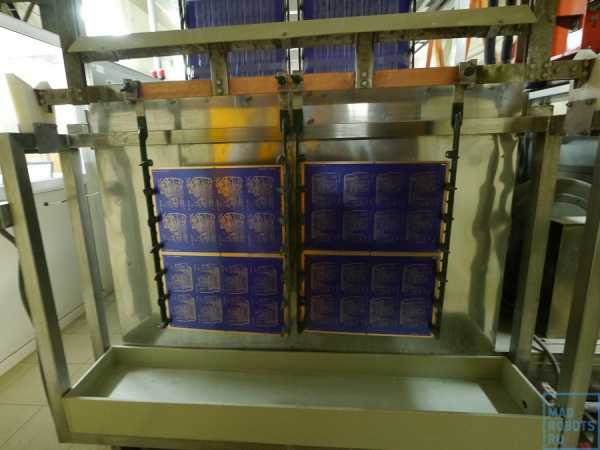
Эта рама проходит несколько уже знакомых нам гальванических ванн:

И покрывается белым слоем ПОС-а. На заднем плане видна другая плата, еще не обработанная:

Удаление фоторезиста, травление меди, удаление металлорезиста

Теперь с плат смывается фоторезист, он выполнил свою функцию. Теперь на все еще медной плате остались дорожки, покрытые металлорезистом. На этой установке происходит травление в хитром растворе, который травит медь, но не трогает металлорезист. Насколько я запомнил, он состоит из углекислого аммония, хлористого аммония и гидрооксида аммония. После травления платы выглядят вот так:
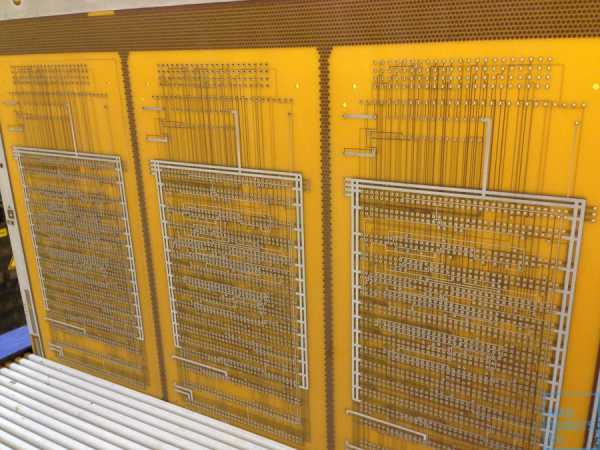
Дорожки на плате — это «бутерброд» из нижнего слоя меди и верхнего слоя гальванического ПОС-а. Теперь, другим еще более хитрым раствором проводится другая операция — слой ПОС-а убирается, не затрагивая слой меди.
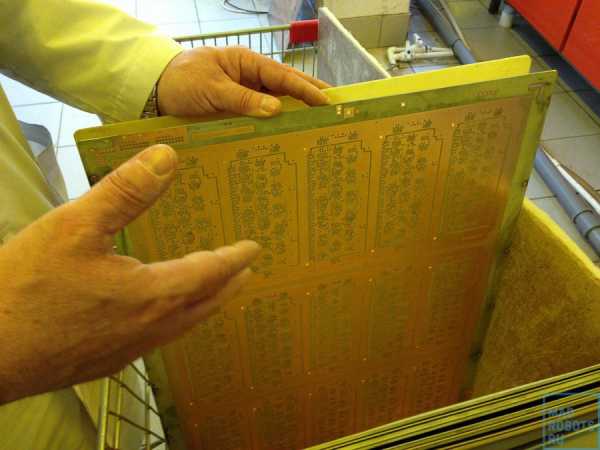
Правда, иногда ПОС не убирается, а оплавляется в специальных печах. Или плата проходит горячее лужение(HASL-процесс) — когда она опускается в большую ванну с припоем. Сначала она покрывается канифольным флюсом:
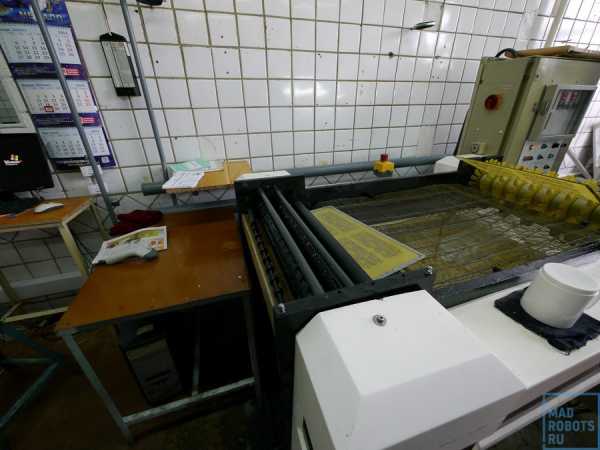
И устанавливается вот в такой автомат:
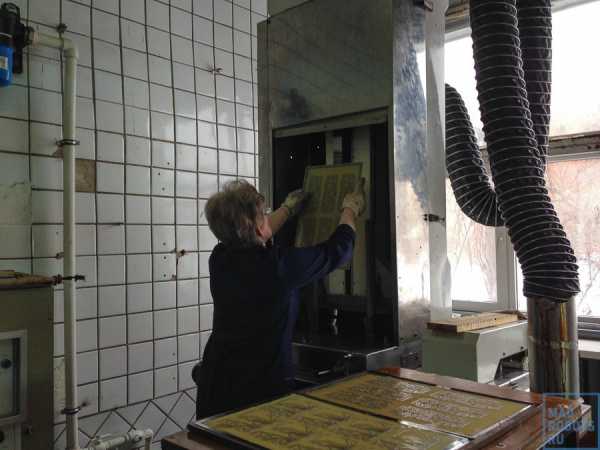
Он опускает плату в ванну с припоем и тут же вытаскивает ее обратно. Потоки воздуха сдувают лишний припой, оставляя лишь тонкий слой на плате. Плата получается вот такая:

Но на самом деле метод немного «варварский» и не очень действует на платы, особенно многослойные — при погружении в расплав припоя плата переносит температурный шок, что не очень хорошо действует на внутренние элементы многослойных плат и тонкие дорожки одно- и двухслойных.
Гораздо лучше покрывать иммерсионным золотом или серебром. Вот тут очень хорошая информация о иммерсионных покрытиях, если кому интересно.
Мы не побывали на участке иммерсионных покрытий, по банальной причине — он был закрыт, а за ключом было идти лень. А жаль.
Электротест
Дальше почти готовые платы отправляются на визуальный контроль и электротест. Электротест — это когда проверяются соединения всех контактных площадок между собой, нет ли где обрывов. Выглядит это очень забавно — станок держит плату и быстро-быстро тыкает в нее щупами. Видео этого процесса можно посмотреть у меня в инстаграме(кстати, подписаться можно там же). А в виде фото это выглядит вот так: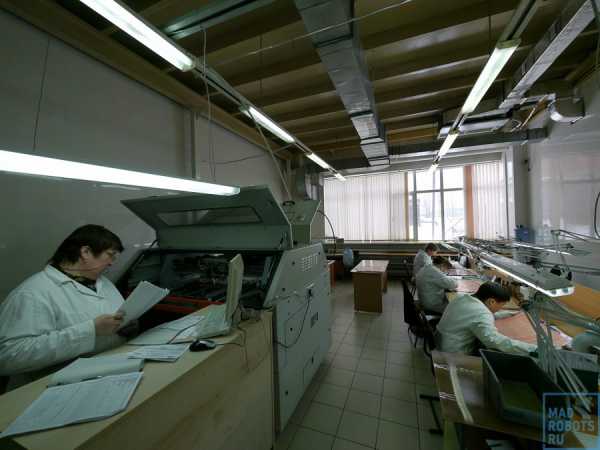
Та большая машина слева — и есть электротест. А вот и сами щупы ближе:
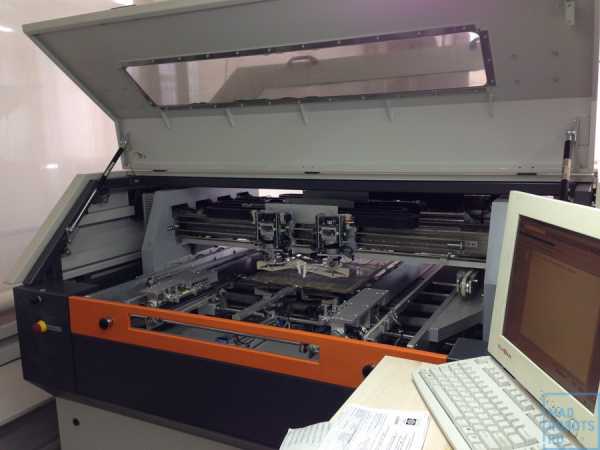
На видео, правда, была другая машинка — с 4 щупами, а тут их 16. Говорят, гораздо быстрее всех трех старых машинок с четырьмя щупами вместе взятых.
Нанесение паяльной маски и покрытие контактных площадок
Следующий технологический процесс — нанесение паяльной маски. То самое зеленое(ну, чаще всего зеленое. А вообще оно бывает очень разных цветов) покрытие, которое мы видим на поверхности плат. Подготовленные платы:
Закладываются вот в такой автомат:
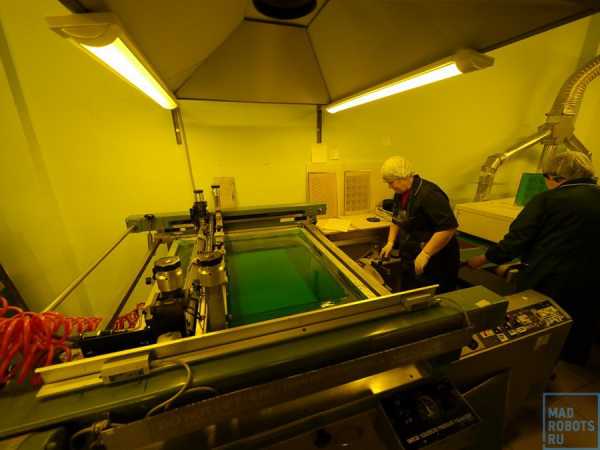
Который через тонкую сеточку размазывает полужидкую маску по поверхности платы:
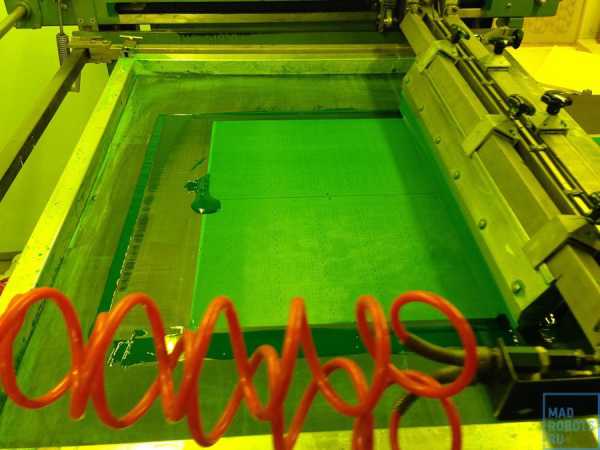
Видео нанесения, кстати, тоже можно посмотреть в инстаграме(и подписаться тоже:)
После этого, платы сушатся, пока маска перестанет липнуть, и экспонируются в той же желтой комнате, что мы видели выше. После этого, неэкспонированная маска смывается, обнажая контактные пятачки:
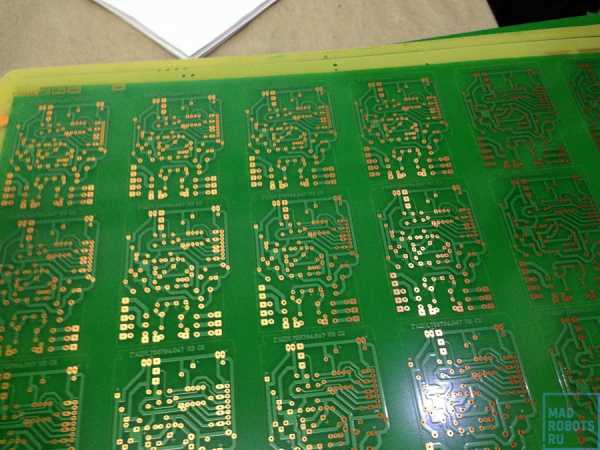
Потом их покрывают финишным покрытием — горячим лужением или иммерсионным нанесением:
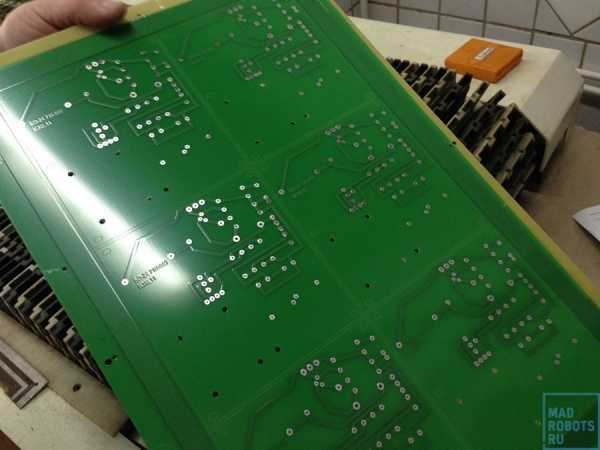
И наносят маркировку — шелкографию. Это белые(чаще всего) буковки, которые показывают, где какой разъем и какой элемент тут стоит.
Она может наносится по двум технологиям. В первом случае все происходит так же, как и с паяльной маской, отличается лишь цвет состава. Она закрывает всю поверхность платы, потом экспонируется, и неотвержденные ультрафиолетом участки смываются. Во втором случает ее наносит специальный принтер, печатающий хитрым эпоксидным составом:

Это и дешевле, и гораздо быстрее. Военные, кстати, не жалуют этот принтер, и постоянно указывают в требованиях к своим платам, что маркировка наносится только фотополимером, что очень огорчает главного технолога.
Изготовление многослойных печатных плат по методу металлизации сквозных отверстий:
Все, что я описал выше — касается только односторонних и двухсторонних печатных плат(на заводе их, кстати, никто так не называет, все говорят ОПП и ДПП). Многослойные платы(МПП) делаются на этом же оборудовании, но немного по другой технологии.Изготовление ядер
Ядро — это внутренний слой тонкого текстолита с медными проводниками на нем. Таких ядер в плате может быть от 1(плюс две стороны — трехслойная плата) до 20. Одно из ядер называется золотым — это означает, что оно используется в качестве реперного — того слоя, по которому выставляются все остальные. Ядра выглядят вот так: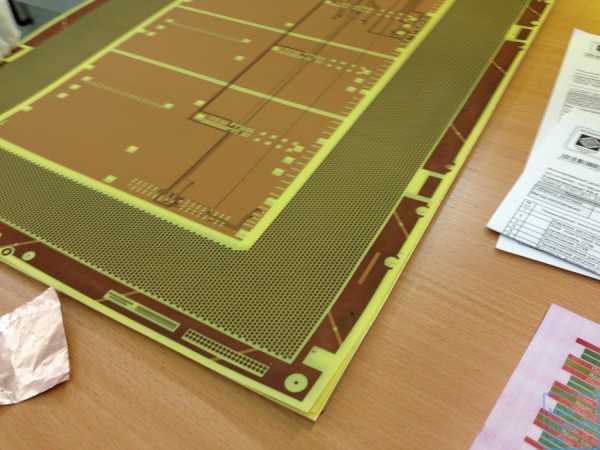
Изготавливаются они точно так же, как и обычные платы, только толщина стеклотекстолита очень мала — обычно 0,5мм. Лист получается такой тонкий, то его можно изгибать, как плотную бумагу. На его поверхность наносится медная фольга, и дальше происходят все обычные стадии — нанесение, экспонирование фоторезиста и травление. Итогом этого являются вот такие листы:
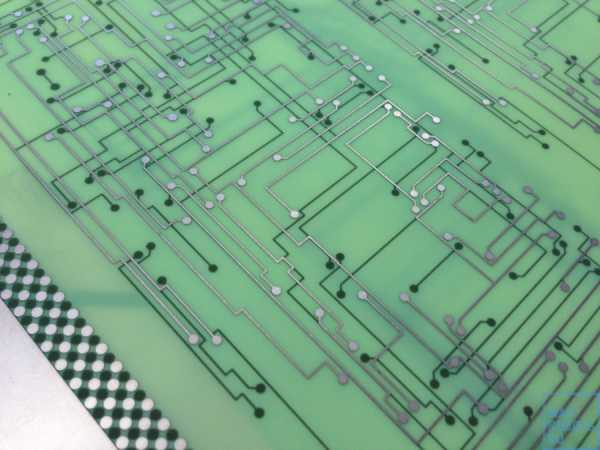
После изготовления дорожки проверяются на целостность на станке, который сравнивает рисунок платы на просвет с фотошаблоном. Кроме этого, существует еще и визуальный контроль. Причем реально визуальный — сидят люди и смотрят в заготовки:

Иногда какая-то из стадий контроля выносит вердикт о плохом качестве одной из заготовок(черные крестики):
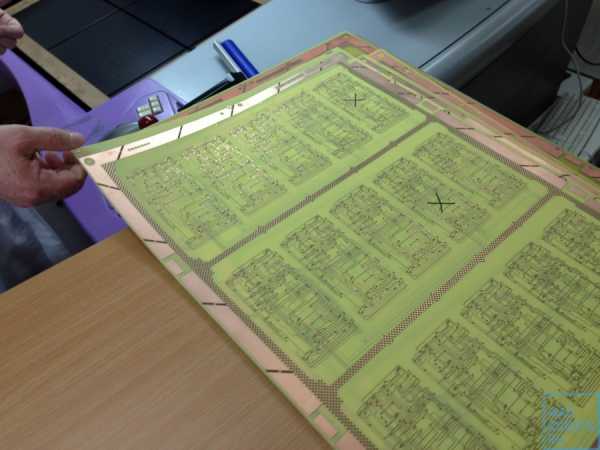
Этот лист плат, в которой случился дефект все равно изготовится полностью, но после нарезки бракованная плата пойдет в мусор. После того, как все слои изготовлены и проверены, наступает черед следующей технологической операции.
Сборка ядер в пакет и прессование
Это происходит в зале под названием «Участок прессования»: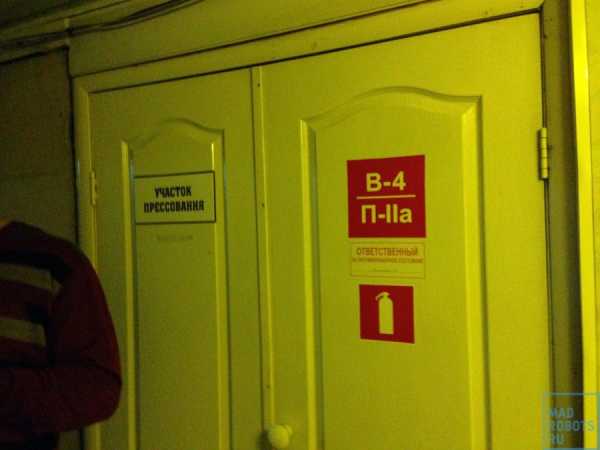
Ядра для платы выкладываются вот в такую стопочку:
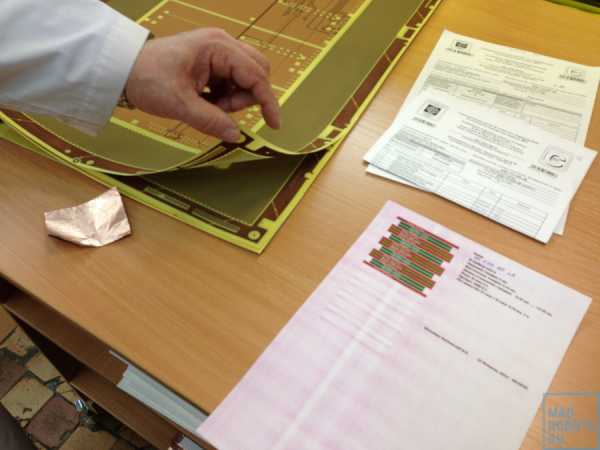
А рядом кладется карта расположения слоев:

После чего в дело вступает полуавтоматическая машина прессования плат. Полуавтоматичность ее заключается в том, что оператор должен по ее команде подавать ей ядра в определенном порядке.
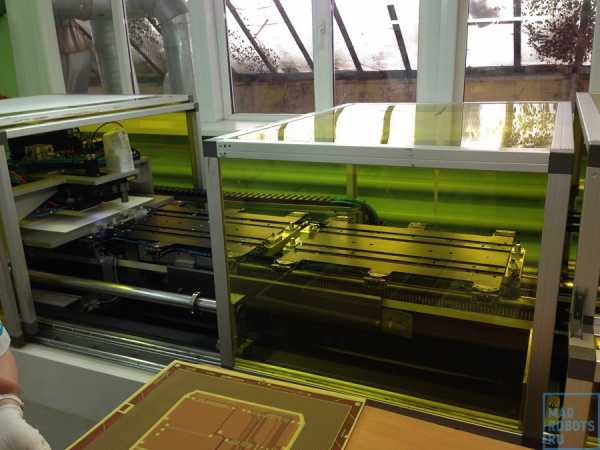
Перекладывая их для изоляции и склеивания листами препрега:
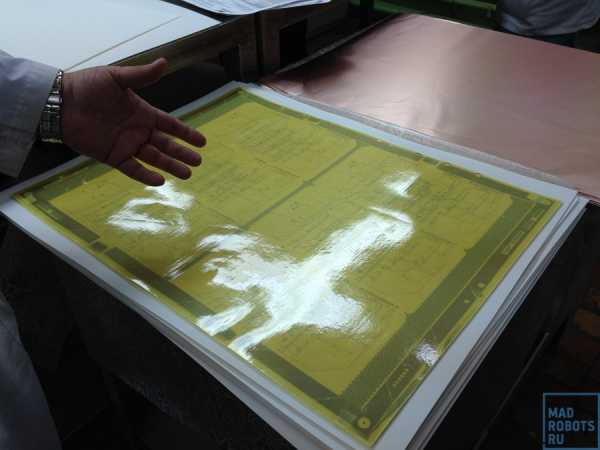
А дальше начинается магия. Автомат захватывает и переносит листы в рабочее поле:
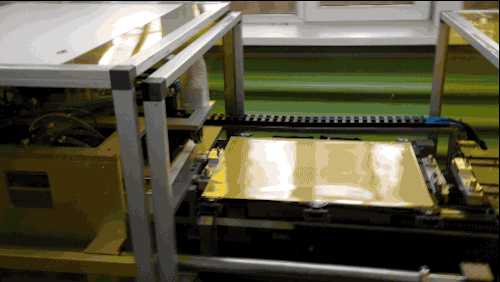
А затем совмещает их по реперным отверстиям относительно золотого слоя.
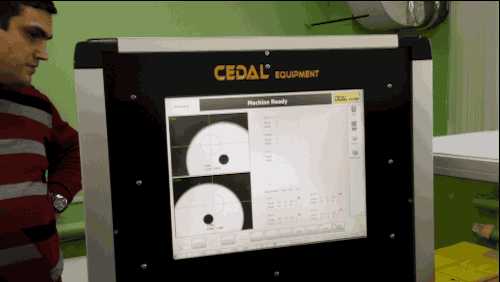
Дальше заготовка поступает в горячий пресс, а после прогрева и полимеризации слоев — в холодный. После этого мы получаем такой же лист стеклотекстолита, который ничем не отличается от заготовок для двухслойных печатных плат. Но внутри у него
Сверловка заготовок
При сборке пакета ОПП и ДПП для сверловки его не нужно центровать, и его можно собирать с некоторым допуском — все равно это первая технологическая операция, и все остальные будут ориентироваться на нее. А вот при сборке пакета многослойных печатных плат очень важно привязаться к внутренним слоям — при сверловке отверстие должно пройти насквозь все внутренние контакты ядер, соединив их 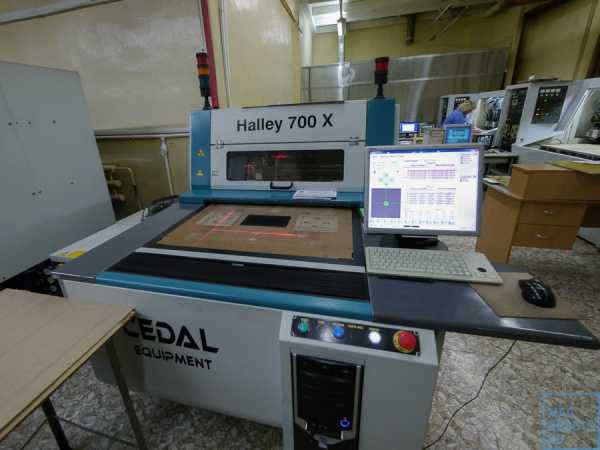
Это рентгеновский сверлильный станок, который видит сквозь текстолит внутренние металлически реперные метки и по их расположению сверлит базовые отверстия, в которые вставляются крепежи для установки пакета в сверлильный станок.

Металлизация
Дальше все просто — заготовки сверлятся, очищаются, активируются и металлизируются. Металлизация отверстия связывает между собой все медные пяточки внутри печатной платы:Таким образом, завершая электронную схему внутренностей печатной платы.
Проверка и шлифы
Дальше от каждой платы отрезается кусочек, который шлифуется и рассматривается в микроскоп, для того, чтобы удостовериться, что все отверстия получились нормально. 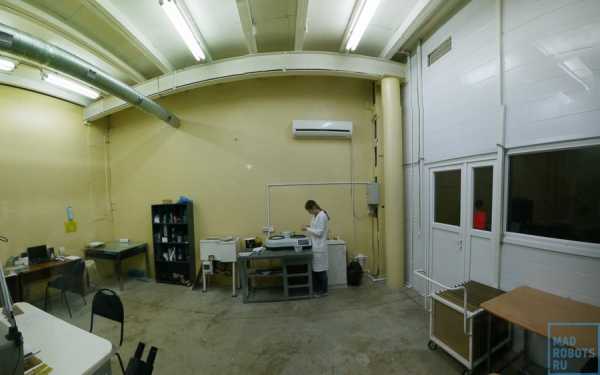
Эти кусочки называются шлифы — поперечно срезанные части печатной платы, которые позволяет оценить качество платы в целом и толщину медного слоя в центральных слоях и переходных отверстиях. В данном случае, под шлиф пускают не отдельную плату, а специально сделанные с краю платы весь набор диаметров переходных отверстий, которые используются в заказе. Шлиф, залитый в прозрачный пластик выглядит вот так:

Фрезеровка или скрайбирование
Далее платы, которые находятся на групповой заготовке необходимо разделить на несколько частей. Делается это либо на фрезерном станке:
Который фрезой вырезает нужный контур. Другой вариант — скрайбирование, это когда контур платы не вырезается, а надрезается круглым ножом. Это быстрее и дешевле, но позволяет делать только прямоугольные платы, без сложных контуров и внутренних вырезов. Вот скрайбированная плата:

А вот фрезерованная:
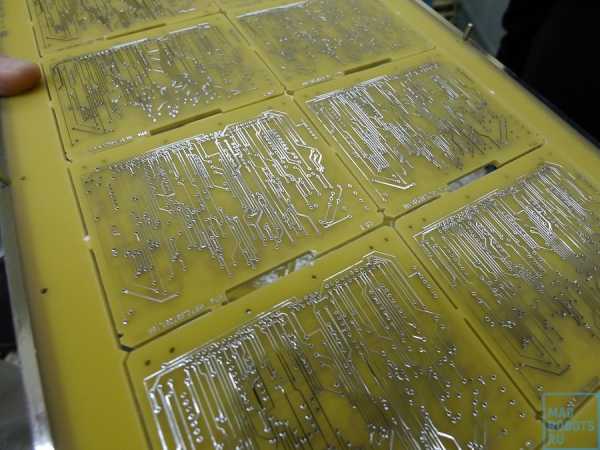
Если заказывалось только изготовление плат, то на этом все заканчивается — платы складывают в стопочку:
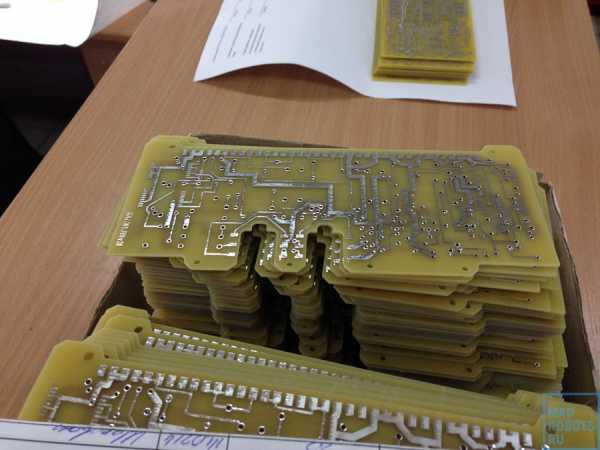
Оборачивается все тем же маршрутным листом:

И ждет отправки.
А если нужна сборка и запайка, то впереди есть еще кое-что интересное.
Сборка

Дальше плата, если это необходимо поступает на участок сборки, где на нее напаиваются нужные компоненты. Если мы говорим о ручной сборке — то все понятно, сидят люди(кстати, в большинстве своем женщины, когда я к ним зашел, у меня уши в трубочку свернулись от песни из магнитофона «Боже, какой мужчина»):
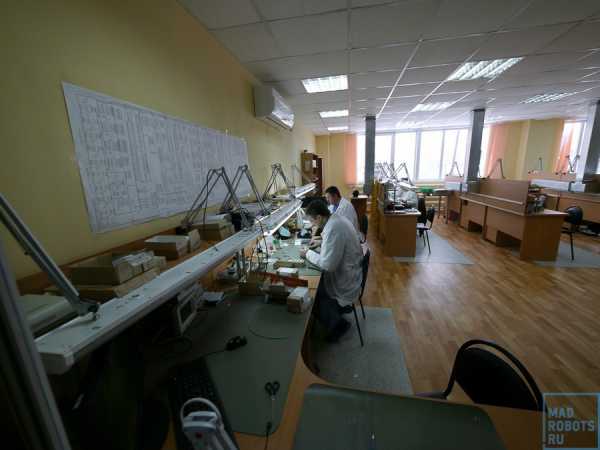
И собирают, собирают:
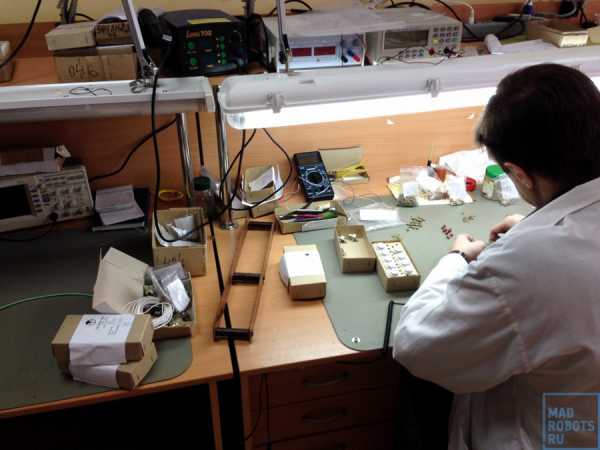
А вот если говорить о автоматической сборке, то там все гораздо интереснее. Происходит это вот на такой длинной 10-метровой установке, которая делает все — от нанесения паяльной пасты до пайки по термопрофилям.
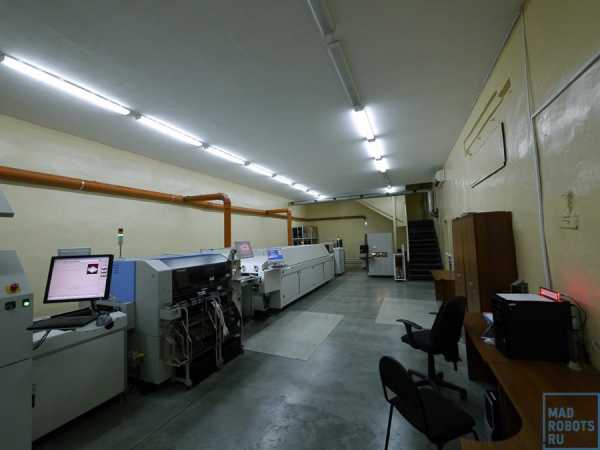
Кстати, все серьёзно. Там заземлены даже коврики:

Как я говорил, начинается все с того, что на неразрезанный лист с печатными платами устанавливают вместе с металлическим шаблоном в начало станка. На шаблон густо намазывается паяльная паста, и ракельный нож проходя сверху оставляет точно отмерянные количества пасты в углублениях шаблона.
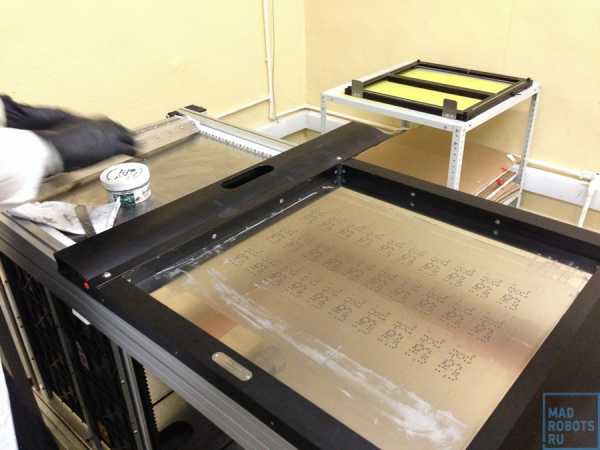
Шаблон поднимается, и паяльная паста оказывается в нужных местах на плате. Кассеты с компонентами устанавливаются в отсеки:
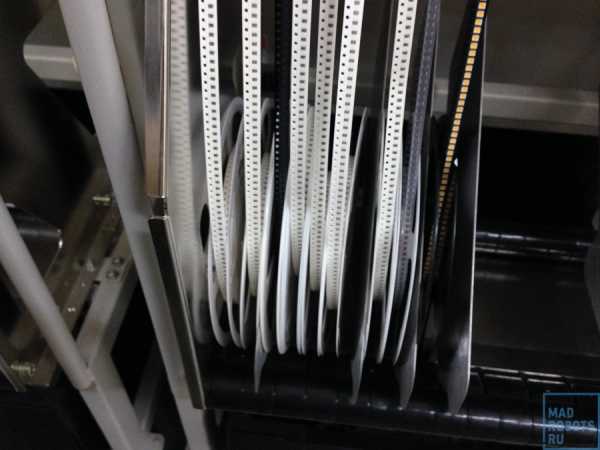
Каждый компонент заводится в соответствующую ему кассету:
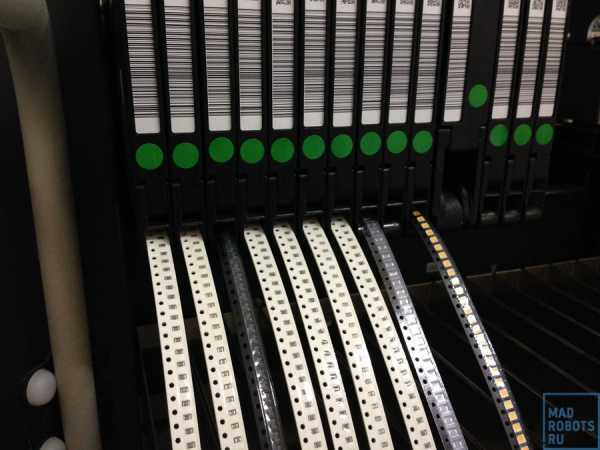
Компьютеру, управляющему станком, говорится где какой компонент находится:

И он начинает расставлять компоненты на плате.
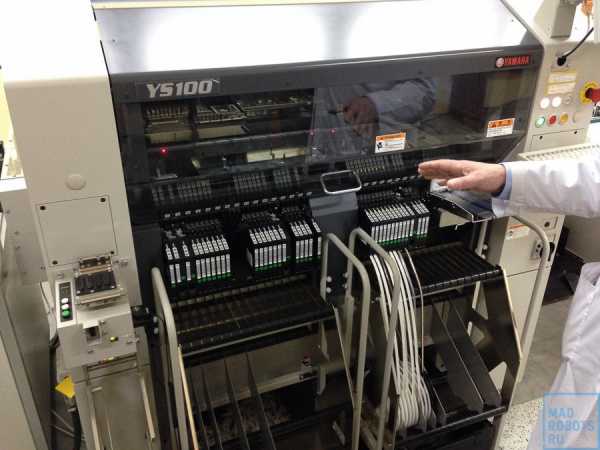
Выглядит это вот так(видео не мое). Можно смотреть вечно:
Аппарат установки компонентов называется Yamaha YS100 и способен устанавливать 25000 компонентов в час(на один тратится 0.14 секунды).
Дальше плата проходит горячую и холодные зоны печки(холодная — это значит «всего» 140°С, по сравнению с 300°С в горячей части). Побыв строго определенное время в каждой зоне со строго определенной температурой, паяльная паста плавится, образуя одно целое с ножками элементов и печатной платой:

Запаянный лист плат выглядит вот так:

Все. Плата разрезается, если нужно и упаковывается, чтобы вскоре уехать к заказчику:
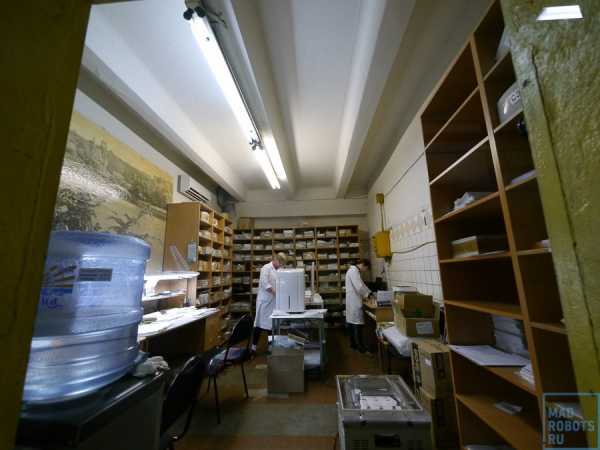
Примеры
Напоследок, примеры того, что технотех может делать. Например, конструирование и изготовление многослойных плат(до 20 слоев), включая платы для BGA компонентов и HDI платы: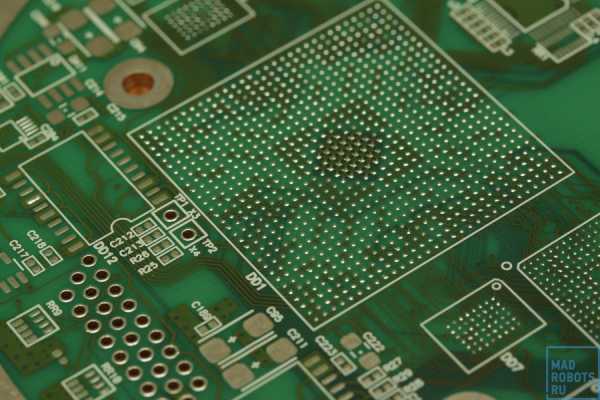
C со всеми «номерными» военными приемками(да, на каждой плате вручную ставится номер и дата изготовления — этого требуют военные):

Проектирование, изготовления и сборка плат практически любой сложности, из своих или из компонентов заказчика:

И ВЧ, СВЧ, платы с металлизированным торцом и металлическим основанием(фотографий этого я не сделал, к сожалению).
Конечно, они не конкурент резониту в плане быстрых прототипов плат, но если у вас от 5 штук, рекомендую запросить у них стоимость изготовления — они очень хотят работать с гражданскими заказами.
И все-таки, в России производство еще есть. Что бы там не говорили.
Напоследок можно отдышаться, поднять глаза на потолок и попытаться разобраться в хитросплетениях труб:
Что почитать?
Субтрактивный комбинированный позитивный метод в домашних условиях ДПП в картинках
Несколько разных технологий изготовления ДПП и МПП
Производство в фотографиях(правда, без описания)
habr.com
«Российское оборудование для производства печатных плат» в блоге «Производство»
Компания «ДИАЛ Электролюкс» является современным, высокотехнологичным, непрерывно развивающимся предприятием. Продукция, изготавливаемая на нашем брянском заводе при помощи современного оборудования с использованием высококачественных электронных компонентов зарубежного производства, отличается высокой степенью надежности и достаточно низкой ценой. Современное техническое оснащение собственной производственной базы позволяет нам изготавливать широкий спектр технологического оборудования для поверхностного монтажа. Современные технологии и высокий уровень инженерной подготовки технических служб позволяют предприятию «ДИАЛ Электролюкс» работать стабильно и постоянно развиваться. Конструкторские и технологические системы проектирования обеспечивают высокие темпы разработок и выпуска новой продукции.
Автоматический принтер трафаретной печати »BURAN B100»
Автоматический принтер трафаретной печати «BURAN B100» разработан в соответствии с требованиями современной электронной индустрии и предназначен для использования как в составе производственных линий в режиме «inline», так и на небольших производствах в качестве автономного устройства в режиме «offline». Все системы принтера отличаются высокой надежностью, гибкостью, простотой эксплуатации и обслуживания.
Основные технические характеристики «BURAN B100»:
— несущая рама принтера изготовлена из высококачественной стали и благодаря продуманной конструкции обеспечивает стабильное функционирование всех движущихся блоков, что в свою очередь гарантирует высокую точность и повторяемость печати
— печатающая головка принтера предназначена для установки на ней двух ракелей, имеет электрическое и пневматическое управление, перемещается со скоростью 5мм/с-200 мм/с и обеспечивает стабильное давление печати (30-240Н) в областях от 75х75мм до 508х508мм. Опционально головка принтера может оборудоваться приводом для поворота ракелей на требуемый угол (максимально 90°). Размер рамки для трафарета может варьироваться в диапазоне от 540х540мм (с адаптером) до 740х740мм. Программное обеспечение позволяет выбирать оператору режим работы печатающей головки наиболее подходящий для нанесения материала на конкретное изделие, а также сохранять данный режим в памяти компьютера
— программное обеспечение позволяет оператору и техническому персоналу производить все необходимые операции по управлению и обслуживанию систем принтера нажатием нескольких клавиш или несколькими щелчками «мыши». Интерфейс пользователя, управляющего компьютером, информативен и удобен в использовании. Все параметры печати и функции принтера отображены в главном окне и доступны после загрузки компьютера
— конвейерная система принтера оборудована специальным устройством обеспечивающим надежную и точную фиксацию печатной платы перед началом процесса печати. Конвейер оборудован световыми барьерами контролирующими перемещение печатных плат. Опционально принтер может быть оборудован механическим стопором для остановки печатных плат. Под конвейерной системой находится поднимающийся стол, на который устанавливаются магнитные подставки для поддержания печатной платы или вакуумная система поддержки (опция), используемая при работе с хрупкими или тонкими платами
— точное совмещение печатной платы и трафарета достигается благодаря использованию видеосистемы, перемещающейся посредством портала по осям X и Y в пространстве между конвейером и трафаретом. Видеосистема состоит из двух CCD-камер одна из которых направлена вверх для поиска точек совмещения находящихся на трафарете, вторая камера направлена вниз для распознавания реперных знаков на печатной плате. После установки рамки с трафаретом в позицию печати (опционально возможна установка на принтер системы автоматической загрузки трафарета) и подачи печатной платы на конвейер происходит фиксация печатной платы и распознавание реперных знаков на плате и трафарете. Далее производится коррекция отклонений посредством установки конвейерной системы в точную позицию, совмещение печатной платы с трафаретом и нанесение материала через трафарет посредством печатающей головки. Точность печати принтера BURAN составляет 15мкм при 6 Сигма
— автоматическая система чистки трафарета (опция) состоит из привода перемещающего систему по оси Y и привода вращения рулона чистящей ткани. Кроме того система чистки оборудована диспенсером чистящей жидкости и вакуумной планкой с соплами. Оператор может выбирать необходимый режим чистки и задавать периодичность чистки трафарета посредством программного обеспечения. Возможен выбор отдельного режима чистки: сухая, влажная или вакуумная, а также любая комбинация вышеперечисленных способов чистки, например, влажная с вакуумом
— контроль над качеством нанесения материала на печатную плату, а также контроль над чистотой апертур трафарета осуществляется посредством видеосистемы при помощи опции «2D инспекция». Программным обеспечением предусмотрена возможность создания максимально 1024 окон для проведения контроля интересующих оператора участков печатной платы. Поле обзора видеокамеры 20х16мм, 1280х1024 пикселей, размер пикселя — 15мкм. Инспекция проводится с большой скоростью — 1 окно/1секунда
Полуавтоматический принтер трафаретной печати В70
Данный полуавтоматический принтер предназначен для нанесения паяльных паст на печатные платы. Печатная плата вручную устанавливается на стол и фиксируется пневматическими зажимами. После нажатия оператором педали стол перемещается в зону печати при помощи серводвигателя. Нанесение паяльной пасты на плату и возврат стола в исходную позицию осуществляются автоматически. Загрузка программ печати и изменение параметров печати проводятся оператором посредством управляющего компьютера.
Краткие технические характеристики
Макс.формат печати 460х460мм
Точность печати +/-10мкм
Скорость печати 10-200мм/сек
Давление печати 10-250Н
Габариты принтера (дхшхв) 1620х1350х1380мм
Вес~600кг
Ручной принтер трафаретной печати В10
Компактный настольный принтер, предназначенный для печати через трафарет и оптимально подходящий для опытного или мелкосерийного производства. Принтер используется для нанесения паяльных паст на печатные платы. В10 оборудован ракельной головкой (2 ракеля) с пневмоуправлением. Фиксация платы на столе печати также осуществляется пневматически. Позиции стола печати по осям Х/Y, углу и высоте выставляются оператором вручную. Также вручную осуществляется перемещение ракельной головки.
Краткие технические характеристики
Мин.формат печати 50х50мм
Макс.формат печати 350х450мм
Точность печати +/-10мкм
Габариты принтера (дхшхв) 800х800х350мм
Вес~70кг
Печь конвекционного оплавления REHM VXs air 2100 (тип 421)
Финальную стадию процесса сборки печатной платы обеспечивает специальное оборудование – печь оплавления. Печатные платы с нанесенным слоем паяльной пасты и установленными компонентами помещают на конвейер печи. Далее печатные платы, перемещаясь по конвейеру, проходят через зоны предварительного нагрева, пиковые зоны и зоны охлаждения. Паяльная паста оплавляется и затем фиксирует электронные SMD компоненты на поверхности платы.
Печь VXs 2100 предназначена для мелко- и среднесерийного производства и может интегрироваться в технологическую линию поверхностного монтажа или работать как автономное устройство. Функциональность, технологичность, высокое качество сборки и применяемых материалов, оптимальные температурные характеристики, приспособленность к бессвинцовой технологии и невысокая стоимость — все это достоинства печи Rehm VXs 2100.
Печь VXs 2100 предназначена для пайки в воздушной среде. Процесс-камера печи состоит из 8 зон:
— 4 зоны предварительного нагрева
— 2 зоны пикового нагрева
— 2 зоны охлаждения
Общая длина зон нагрева 2100мм. Длина каждого нагревательного модуля и модуля охлаждения — 350мм.
Максимальная температура в зонах предварительного нагрева — 300оС, в зоне пикового нагрева — 350оС. Длина зоны охлаждения — 700мм.
Контроль над внутренней температурой осуществляется при помощи термодатчиков, расположенных внутри каждой рабочей зоны. Благодаря близкому расположению датчиков к уровню конвейера, возможно получение реальных значений температуры в каждой зоне процесс-камеры.
Производительность системы: 75 печатных плат в час (при условии, что длина печатной платы 300мм и расстояние между платами 100мм).
Печатные платы перемещаются в процесс-камере печи по игольчатому конвейеру. Ширина конвейера с цепью центральной поддержки настраивается в пределах от 65 до 400мм. Длина игл конвейера 3мм, опционально возможна установка цепи с иглами длиной 5мм.
Скорость конвейера устанавливается в зависимости от требований технологического процесса в пределах от 180 до 1800мм/мин.
Для предотвращения коробления печатных плат во время пайки, в конструкции печи используется система центральной поддержки платы, конструктивно выполненная в виде цепи, состоящей из плоских звеньев.
Смазка цепей конвейера производится автоматически, при помощи специальной смазочной системы. Использование этой системы позволяет экономить средства на смазочных материалах за счет оптимального распределения смазки на цепи конвейера.
Энергопотребление: 380В, 50/60Гц, 40/7.5кВт.
Габаритные размеры:
— 3590х1480х1738мм (ДхШхВ), высота с открытыми кожухами 2300мм.
— занимаемая площадь 5.31м2.
Масса печи: 1800 кг.
Конвейерная система B1a
Описание системы
Транспортная система с длиной сегмента 530мм.
Конвейер используется как промежуточная система между двумя устройствами в технологической линии SMT монтажа.
Особенности системы:
•Регулируемая скорость конвейера
•Функция контроля печатной платы
•Интерфейс SMEMA
•Ширина конвейера от 60мм до 460мм
•Электропитание: 230 В / 115 В, 50 / 60 Гц, ± 10%
•Потребляемая мощность — 0,2 кВт
•Высота конвейера 950 мм ± 50 мм.
Конвейерная система B1b
Описание системы
Транспортная система с длиной сегмента 600мм.
Конвейер используется как промежуточная система между двумя устройствами в технологической линии поверхностнго монтажа. Установка ширины конвейера производится вручную. Фиксация ширины производится при помощи специальных зажимов.
Особенности системы:
* Антистатические ремни конвейера
* Интерфейс SMEMA
* Кнопка управления Start / Stoр
* Ширина конвейера: 60-460 мм.
* Потребляемая мощность — 0.2 кВт.
Опции:
* Функция контроля печатной платы
* Регулировка скорости конвейера
Конвейерная система B2b
Описание системы:
Транспортная система c двумя сегментами. Длина каждого сегмента 600мм. Конвейер используется как промежуточная система между двумя устройствами в технологической линии. Установка ширины конвейера производится вручную. Фиксация ширины производится при помощи специальных зажимов.
Особенности системы:
* Антистатические ремни конвейера
* Интерфейс SMEMA
* Кнопка управления Start / Stoр
* Ширина конвейера: 60-460 мм.
* Потребляемая мощность — 0.2 кВт.
Опции:
* Функция контроля печатной платы
* Регулировка скорости конвейера
Конвейерная ремонтная станция B1R
Данный конвейер главным образом предназначен для выполнения операций по контролю поверхностного монтажа SMD компонентов, установленных на печатную плату и исправлению дефектов монтажа, обнаруженных в результате оптического (рентгеновского) контроля. Система оборудована удобной передней панелью, рассчитанной на два рабочих места для операторов. Каждое рабочее место оборудовано кнопками «Старт» и «Стоп» для пуска/остановки сегмента конвейера. Каждый из сегментов имеет независимое управление.
Технические данные:
• высота — регулируемая
• ширина — 910мм
• длина — 1500мм
• 2 рабочих места
• освещение рабочего места
• регулируемая полка
• 2 независимо работающих сегмента
• 4 розетки для подключения инструмента
Рабочая конвейерная станция B3R
Описание системы:
Данный конвейер главным образом предназначен для выполнения операций по контролю монтажа компонентов установленных на печатную плату и исправлению дефектов монтажа, обнаруженных в результате контроля. Система оборудована удобной передней панелью, системой освещения и электророзетками для подключения внешнего оборудования
Особенности системы:
— 3 рабочих сегмента общей длиной 1800мм
— регулируемая полка для инструментов и материалов
— лампа освещения рабочего места
— интерфейс SMEMA
Мобильный стол Т01 для сращивания лент с компонентами
Стол Т01 предназначен для использования на производстве, оснащенном автоматическими установщиками SMD-компонентов. Мобильность и оснастка стола позволяют производить сращивание лент с компонентами за короткий период времени, что естественным образом значительно снижает потери производственного времени, требуемого на пополнение компонентов в питателях.
Описание:
* Инструмент Splice Tool крепления для катушек с лентами и инструмента для сращивания;
* Хорошая маневренность;
* Вместительная корзина для катушек;
* Ячейки для инструментов и расходных материалов;
* Запатентованный инструмент компании Siemens для скрепления лент с компонентами.
Вот такой вот интересный набор) Есть и другие производители. К сожалению SMT установщиков отечественного производства пока найти не удалось. Может кто-нибудь знает?
sdelanounas.ru