Производство паркета: оборудование и технология
В производстве паркета важным этапом является выбор пород древесины, как исходного сырья для изготовления напольного покрытия любой формы. Паркетная доска занимает одно из первых мест по популярности среди покрытий для отделки пола. Изделие является отличной заменой паркету и по характеристикам ничем ему не уступает.
Виды паркетной доски
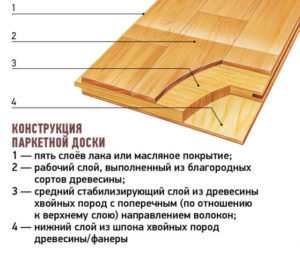
Конструкция паркетной доски
По структуре доска имеет три слоя разного типа древесины. Нижний и средний слой изготавливается из менее ценных пород дерева. В качестве исходного сырья берут сосну или лиственницу. Слои располагают так, чтобы волокна каждого были перпендикулярны друг другу. Для верхнего слоя используют дорогостоящую древесину, волокна которой направлены вдоль полотна. Благодаря такому расположению волокон паркетная доска становится прочной и не деформируется после укладки.
Паркетные доски отличаются по виду древесины и размерам. Верхний декоративный слой может выполняться из традиционных и экзотических пород деревьев. Каждый сорт отличается друг от друга по цвету, твердости и рисунку. Современные технологии способны придавать дереву различные оттенки, поверхность делать шероховатой, вносить элемент старения.
Паркетная полоса изготавливается из:
- дуба;
- бука;
- ореха;
- ясеня;
- шоколадного дерева;
- оливы.
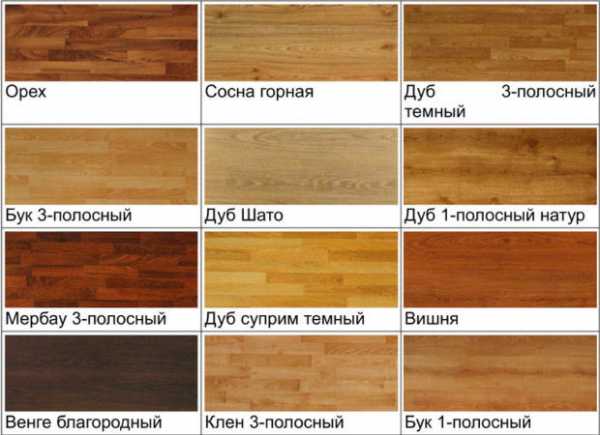
Виды паркета
По количеству ламелей доска подразделяется на однополосную, двух и трехполосную. Самое дорогое – производство однополосных изделий. Сверху изделие покрывается специальными лаками и маслами, которые делают поверхность ровной, прочной и стойкой к разным механическим воздействиям. Лаковое покрытие придает доске насыщенность и четкость. Благодаря замковому соединению процесс сборки не отнимает много времени. Поверхность приятная на ощупь. Продукция имеет высокие звукоизоляционные характеристики и не накапливает статического электричества.
Другие разновидности паркета
Кроме паркетной доски, существует ряд других напольных покрытий:
- террасная доска;
- массивная доска;
- художественный паркет.
Террасная доска или «декинг». Такое покрытие предназначено для террас, основой которого является дерево. Обладает высокими прочностными характеристиками и повышенной степенью влагостойкости. Применяется в местах, где существует вероятность прямого влияния солнечных лучей, дождя, снега и резких перепадов температур наружного воздуха.
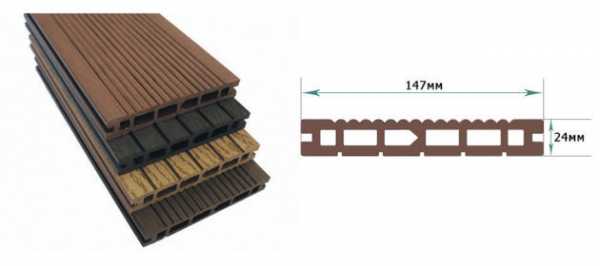
Террасная доска
Массивная доска – красивое и высокопрочное покрытие, выполненное из цельного куска дерева.
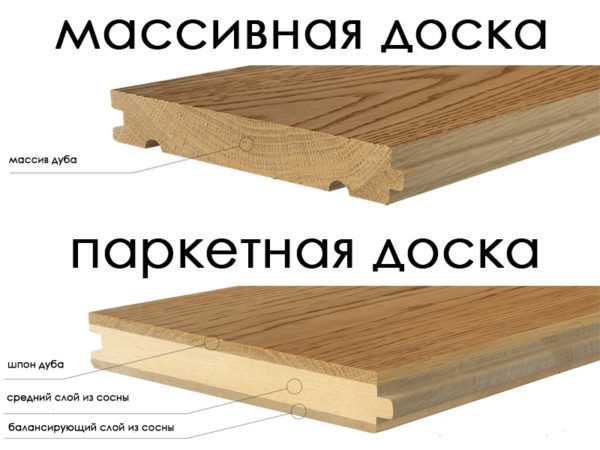
Сравнение массивной доски с паркетной
Модульный паркет. Пол из готовых модулей, неприхотлив в эксплуатации. Состоит из верхнего декоративного слоя и фанерного основания. Каждый отдельный модуль включает в себя сложные узоры штучного паркета.
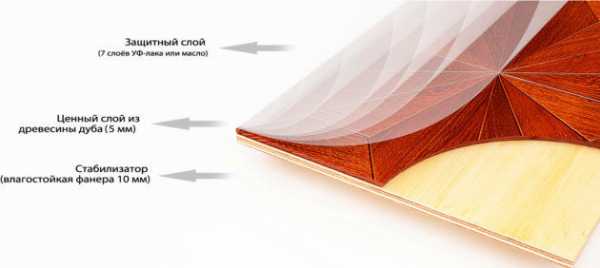
Модульный паркет
Художественный паркет. Элитное покрытие с оригинальным и гармоничным узором. Изготовление паркета основывается на применении планок разных цветов и нескольких пород дерева.
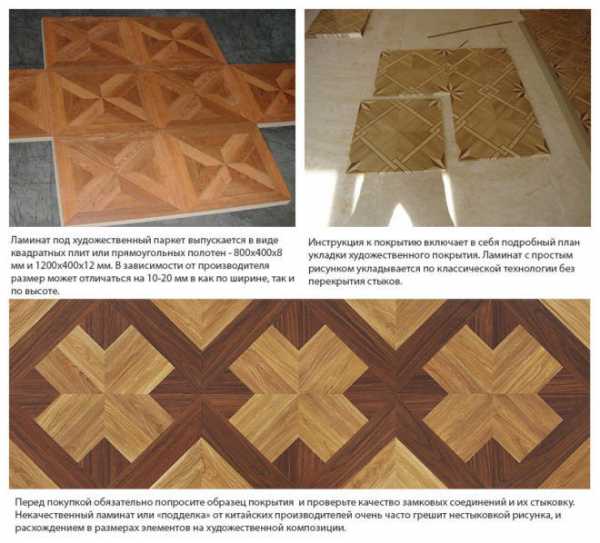
Художественный ламинат
Оборудование для производства паркетной доски
Для производства паркетных изделий требуется специальное оборудование:
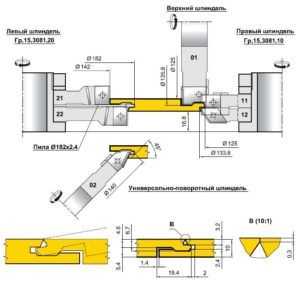
Чертёж машины для производства паркета
- распиловочные станки;
- заточные приспособления для пил;
- пресс для склеивания;
- сушилка.
Это основные приспособления, которые необходимы для производства штучного паркета и других изделий. Все это оборудование должно удобно размещаться в помещении.
Если цех небольшой по площади, то часть операций выполняют в других помещениях или на улице, где будет производиться первичная обработка леса. Подготовительные работы можно осуществить под навесом. После просушки и распиловочных станков дерево поступает на выходную линию, затем ему задается нужная толщина при помощи многопильных станков.
Основная обработка материала выполняется на четырехстороннем строгальном и торцовочном станке. Полосы получаются ровные, гладкие и определенной длины. Отдельные элементы склеиваются между собой специальным прессом.
При подборе оборудования следует учитывать, какой вид паркета будет выпускаться. Эконом-вариант потребует меньше инвестиций, а производство дорогостоящих элитных видов повлечет приобретение дополнительного оборудования.
Производство штучного паркета
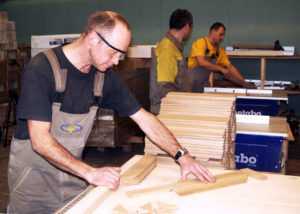
Производство паркетной доски
Необработанная древесина поступает в пункт хранения или склад, где его тщательно осматривают на наличие дефектов. Бракованное сырье к дальнейшей работе не допускается.
Далее, начинается процесс сушки отобранного качественного материала. В специальных сушильных камерах древесина несколько месяцев находится под действием высокой температуры. Здесь же происходит термическая обработка сырья. В итоге дерево получается плотным, прочным и стойким к различным видам деформации. После окончания манипуляций с древесиной приступают к изготовлению паркета. Подготовленная древесина поступает в распиловочный цех, где ее обрабатывают и придают правильную геометрическую форму.
Производство паркета основано на работе строгальных, фрезерных и торцевых станков, которые с точностью выполняют каждый элемент. Отшлифованный паркет покрывается лаком и упаковывается для дальнейшей реализации. Изготовление паркета не самый сложный процесс по сравнению с производством других видов паркетных изделий, где необходимо спрессовать между собой разные породы дерева.
Этапы производства паркетной доски
Натуральные дорогостоящие породы используются для изготовления верхнего слоя доски, а менее ценные – для основания и среднего слоя. Качество товара, срок эксплуатации и внешний вид зависят от вида древесины, способа проведения подготовительных работ и рабочего процесса, а также от качества клеящего состава.
Выделяют основные направления производства продукции:
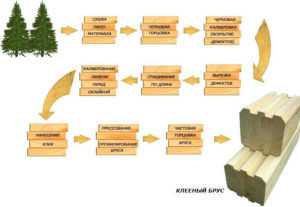
Подготовка древесины для производства паркета
- Изготовление основания и среднего слоя.
- Подготовка внешнего покрытия.
- Прессование всех частей под воздействием высокой температуры.
Сначала древесину раскладывают по породам. Затем приступают к просушке дерева в специальных сушильных камерах. За это время древесина приобретает упругость и прочность.
Материал распиливают, придавая ему правильные геометрические формы нужных размеров. Готовые изделия обрабатывают на фрезерном станке и шлифуют.
После того как основание и средний слой готов, приступают к внешнему декоративному слою. Ценную породу древесины распускают на полосы и обрабатывают на фрезерном станке. Все слои смазываются клеем и под действие пресса сдавливаются и склеиваются между собой. Верхняя часть покрывается лаком в несколько этапов.
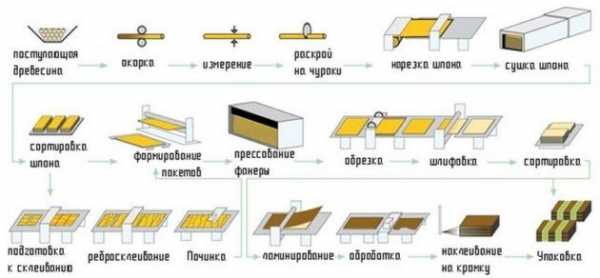
Производство паркета
Преимущества и недостатки паркетной доски
Основные недостатки продукта:
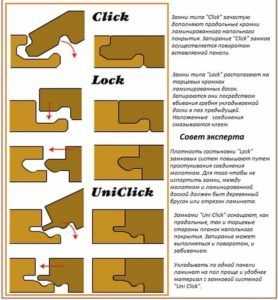
Варианты замковых соединений для паркетной доски
- изделие следует защищать от влияния высоких температур и влаги;
- портят структуру полотна химические реагенты и влага;
- односторонняя направленность узора.
Достоинства:
- отлично подходит для оформления интерьера в классическом стиле;
- сразу готово к применению после приобретения;
- длительный срок эксплуатации;
- простота монтажа за счет удобного замкового соединения;
- гибкость и устойчивость к внешним воздействиям;
- многообразие цветовой гаммы.
Недостатки материала перекрывает его функциональностью и практичностью.
Это экологически чистый продукт и настоящее деревянное покрытие. Длину полос можно подогнать под размеры комнаты, достаточно отрезать лишний кусок специальным ножовочным полотном. По всем четырем сторонам изделие имеет специальные боковые и торцевые замки, которые при замыкании с другой полосой обеспечивают жесткость соединения. После покупки материал не требует дополнительного обслуживания и подготовки к укладке.
Изделие можно укладывать на пол с подогревом, предварительно проложив гидроизоляцию.
Себестоимость производства доски в полтора раза дешевле изготовления штучного паркета.
Видео по теме: Как сделать паркет
promzn.ru
производство паркета. Технология и оборудование для производства паркетной доски. Стоимость производства паркета :: BusinessMan.ru
Сегодня есть основание утверждать, что производство паркета — один из тех видов бизнеса, который успешней развивается не в центре, а именно в регионах России.
Российский рынок паркета
Свидетельством сказанному являются два российских лидера паркетного производства – Обнинский з-д и фабрика «Заря», расположенные в Калужской области. Существование же многочисленных российских торговых марок паркета отражает тенденцию роста коммерческой привлекательности этого бизнеса, представим их неполный перечень: Alloro, Junglewood, «Адыгея-паркет», «Артпаркет «Янтарная прядь»», «Бонд», «Майкопский паркет», «Паркет Романовский», «Старый мастер», «Традиции русского паркета».
Главным потребителем паркета является строительная индустрия. Важно также сотрудничество с хозяйственными магазинами, а в особенности – с супермаркетами. Опрос, проведенный журналом «Дом и быт» показал, что 75% компаний-застройщиков России ощущают дефицит поставок качественного паркета. Технология производства паркета прогрессирует, что как раз и демонстрирует вышепредставленный букет различных торговых марок.
Где и как открыть бизнес?
Предприниматель, перед тем как войти в бизнес по производству паркета, должен одновременно учесть и увязать между собой несколько важных факторов.
Чрезвычайно важны «технические» вопросы. Поблизости должны функционировать лесозаготовительные предприятия либо лесопилки и, естественно, произрастать в промышленных объемах древесина, используемая для производства паркета.
Должна быть предусмотрена бесперебойная передача электроэнергии (идеально – из двух альтернативных ЛЭП). Важны предварительные договоренности о покупках продукции с застройщиками (СМУ и проч.).
Для минимизации возможных рисков при осуществлении производства оптимальным шагом выглядит аренда небольшого деревообрабатывающего завода на окраине города. Там, в специально обустроенном производственном помещении, устанавливается оборудование для производства паркетной доски. (При этом изначально самим бизнес-проектом предусмотрены организационные и технические требования контролирующих органов.)
Планирование территории производства
Размещение производства должно подчиняться порядку осуществления производственного процесса. Важна удобная подъездная дорога к лесопилке. Для лесопильного участка отводится площадь 50-100 м2, над ним оборудуется навес. Черновая доска — продукция лесопилки — складируется поблизости к подготовительному участку, под который в помещении выделена производственная площадь около 90 м2. Для конечного этапа – «чистовой обработки», осуществляемой при помощи паркетной линии, — потребуется 60 м2. Таким образом, общая расчетная площадь под производство паркета составляет около 200 м2.
Какой паркет изволите?
Как утверждает статистика, производство паркета находится «на подъеме». Своеобразным психологическим стимулом дальнейшего развития, как отмечают специалисты, является преобладание на рынке России (как и других стран СНГ) товара низкого уровня качества. Предприниматели, открывая паркетный бизнес, стремятся продемонстрировать более высокое качество своей продукции. Поэтому перспективу коммерческого успеха может иметь даже небольшое производство, наладившее производство пользующегося спросом товара.
Производство какого же паркета целесообразно развивать? Будем следовать от максимально востребованного, тогда вначале будет позиционироваться штучный, за ним – мозаичный, потом – паркетная доска (многослойный) и, наконец, щитовой. Многослойный паркет требует дополнительных инвестиций в клеевое производство. Безусловно, предпочтительней в этих целях использовать импортные станки для производства паркета.
И все-таки большинство российских предпринимателей производит штучный паркет. Он представляет собой стандартные технологичные фактурные планки, обычно изготовляемые в диапазоне толщины 1,5-2,2 см, ширины 3-15 см, длины 9,5-50 см. Как его классифицируют? Всем известен классический, привычный нам «советский» формат — 15 х 45 х 250 мм, остальное же считается европаркетом. Паркетины жестко крепятся между собой при помощи соединения двух боковых шпунтов с двумя пазами.
Разная древесина – разный паркет
Каждый предприниматель, изготовляющий паркет, ориентируется на определенный рынок и, соответственно, подбирает производственное сырье под его запросы. Общеизвестно, что фактура любого паркетного покрытия и его рисунок зависят от вида древесины. Творческого подхода к выбору сортов дерева требует производство художественного паркета.
Приведем пример некоторых видов паркета (в зависимости от использованного сырья). Дубовый паркет, наверное, наиболее популярен в Европе, возможно, из-за исторической традиции. Дуб издревле считается воплощением силы и крепости, возможно, поэтому изделия из него традиционно пользуются особым спросом. Среди изделий из древесины умеренных широт он — один из самых прочных. Цвет может быть различным: от светло-коричневого до темных благородных оттенков мореного дуба (самого дорогого).
Паркет из бука слабо текстурирован, однако обладает нежным теплым светлым рисунком: от белесого с желтоватым оттенком до насыщенного золотисто-коричневого. Тем не менее, его древесину ценят наряду с дубом настоящие ценители паркета – британцы.
Примечательно, что при дополнительной обработке паром эта древесина приобретает красноватый цвет. (Производство паркета иногда использует и этот способ.) Замечательный получается также паркет из ясеня. Кроме того что он не менее прочен, чем дубовый, ему присущ тонкий фактурный рисунок. Пестрая, с красноватым оттенком древесина ореха способна, будучи превращенной в паркет, создать на полу, благодаря своему яркому рисунку, действительно фантастические панно. Популярен также светлый паркет из березы.
Полный цикл производства паркета
Изготовление паркета полного цикла включает в себя несколько стадий.
Сначала идет первичная обработка леса при помощи лесопилки (стоимость российской — 50 тыс. $) и сушилки (соответственно – 15–20 тыс. $).
Затем – подготовительная стадия. В ее рамках – при помощи многопильного станка (5-15 тыс. $) задается толщина изделий. Основная же обработка производится на четырехстороннем строгальном станке (12-15 тыс. $) и торцовочном (2-4 тыс. $), режущем профилированную доску на стандартные «штуки».
И, наконец, собственно паркетная линия, оснащенная строгальным четырехсторонним станком, совмещенным с шипорезом (60 тыс. $ (от российского производителя), до 220 тыс. $ – импортная).
Если же предприниматель стремится организовать изготовление паркета, конкурентного на внешнем рынке, то ему следует руководствоваться стандартами ISO9001 и DIN. Понадобится хотя бы на конечной стадии производственного процесса импортное оборудование. При этом инвестиции в производство продукции составят 500 тыс. $. Стоит ли упоминать, что повышение качества продукции должно стимулировать оплату труда рабочим?
Производство полного цикла, обслуживаемое станками российского изготовления, обойдется дешевле — в 250 тыс. $. Оно будет соответствовать российским ГОСТам и ориентировано на российский рынок.
Художественный паркет
Производство художественного паркета в России началось еще в XVIII веке, когда возводились Петербургские дворцы. Мастера того времени использовали более 50 видов древесины. Современное промышленное изготовление основано на наклеивании цветных планок на основание (так называемая техника маркетри).
При изготовлении такого паркета слои древесины ложатся на основание перпендикулярно друг другу. В таком сочетании фактурность их волокон смотрится наиболее выигрышно. Лицевой слой изготавливается из высокосортного дерева толщиной 5-6 мм. Лакируется такое изделие основательно, обычно в 5 слоев.
Эконом-вариант производства паркета
Предприниматель, «примеряя на себя» любой бизнес, исходит из требуемой суммы инвестиций в него. Затраты для производства штучного паркета при покупке подготовленного сырья могут составить 50 тыс. $.При этом предприниматель избирательно покупает станки для паркета: паркетную линию российского производства стоимостью 20 тыс. $, а также оборудует подготовительный участок, что по минимуму обойдется тоже в 20 тыс. $. Покупка, монтаж, запуск оборудования, а также затраты на закупку сырья составят как раз упомянутые выше 50 тыс. $.
Впрочем предприниматель-производственник не останавливается на таком приобретении. Окупив этот эконом-вариант «запуска» бизнеса, он продолжает инвестировать в производство, стремясь организовать его полный цикл.
Паркетный бизнес и человеческий фактор
Не следует забывать старую истину — «кадры решают все». Изначально следует нанять себе надежных помощников: грамотного бухгалтера-экономиста, технолога и маркетолога-водителя.
Без бухгалтера-производственника также не обойтись. Ведь, кроме производственных моментов, понадобится оформлять множество документов: трудовые договора, трудовой распорядок, штатное расписание, личные карточки, учет трудовых книжек, регистрацию приказов.
«Крепкий» технолог – также залог успеха бизнеса. Ведь производство должно быть налажено соответственно ДСТУ 3819-98 и ГОСТом 862.1-85 и ДСТУ 3819-98, регламентирующим производственные допуска, кривизну и чистоту обработки, разрешенный уровень дефектов.
Сферой деятельности маркетолога-водителя является изучение рынка, заключение договоров с поставщиками, доставка сырья и отправка готовой продукции, осуществление ее сбыта.
Приоритетами в подборе рабочих является их умение работать на оборудовании, а при необходимости они должны уметь отремонтировать и настроить станок для изготовления паркета. Немаловажен также общий уровень здоровья рабочих, ведь им, кроме основной работы, предстоит производить погрузки, разгрузки, складирование.
Рентабельность паркетного бизнеса
В процентном соотношении затраты паркетного производства выглядят следующим образом: 60% — стоимость сырья, 15% — оплата электроэнергии и других энергоносителей, 20% — заработная плата персоналу. Важна ритмичная работа производства, его полная загрузка, отсутствие простоев и затоваривания. Оборудование для изготовления паркета должно работать без простоев. При соблюдении этих условий рентабельность бизнеса по производству паркета составляет 15%.
Впрочем, предприниматели не останавливаются на этом, далее повышая рентабельность за счет осуществления полного производственного цикла: от забора леса до укладки паркета. Ведь продажа паркета, совмещенная с его укладкой, повышает его розничную цену в 2,2 раза. Правильность кладки паркета требует квалификации. Развившие это направление производственные предприятия имеют в своем составе также бригаду строителей, осуществляющих укладку паркета.
Вывод
Производство паркета – это живой, творческий процесс.
В нем увязывается между собой множество факторов. Производственный процесс и бухгалтерский учет, ритмичная работа с поставщиками и покупателями продукции, производительность труда, качество продукции.
Достигнутый уровень производства прямо пропорционален доходности бизнеса. Так, квадратный метр высококачественного импортируемого паркета стоит 100 $, а «эрмитажный класс», который демонстрирует производство художественного паркета, — 300 $.
Ну и, конечно же, идеальным способом для предпринимателей-производственников оптимизировать спрос является сотрудничество с сетевыми строительными магазинами.
businessman.ru
Станки для паркета
Metabo TKHS 315 M 310
Metabo TKHS 315 M 310 проектировалась для последующей обработки изделий из древесины. С ее помощью можно осуществлять распил панелей, досок, брусьев и других элементов, осуществлять процесс изготовления деталей декоративного назначения. Пилу можно применять в стандартной мастерской или на предприятиях, которые работают в производственной сфере.
Корпус производится с применением листовой стали, которая обрабатывается с использованием краски порошкового типа. Она обеспечивает прекрасную защиту от неблагоприятных воздействий, а на столешницу наносится цинковый слой.
В пиле используется двигатель с мощностью 3,1 кВт, удается достичь частоты вращения полотна в 2990 оборотов в минуту. Такой скорости достаточно, чтобы выполнить быстрый и ровный рез. По транспортирному упору можно установить угол распила, он составляет 45 или 90 градусов.
Преимуществом станет удобство использования. В конструкцию установлена система удаления опилок, можно выполнить подключение пылесоса для их быстрого сбора во время работы. Присутствуют ручки и колеса, они существенно облегчают последующую транспортировку изделия.
Metabo KGS 315 Plus
Пила торцовочная Metabo KGS 315 Plus подойдет для профессионалов. Она разработана для пользователей, которые предъявляют к инструменту повышенные требования. Модель имеет мощность 2200 Вт, за счет чего отлично справляется с распилом элементов.
Пилу можно раздвигать и проводить последующую корректировку размеров. Такое решение позволяет обрабатывать даже материалы с существенной толщиной. Около зоны распила присутствует дополнительная точка для удаления пыли. Производитель позаботился о системе плавного пуска, она снижает нагрузку на агрегат при включении.
Пила имеет продуманные эргономичные формы, которые несколько облегчают работу с ней. По бокам установлены рукоятки, они будут полезны в процессе транспортировки. Удается легко отрегулировать глубину реза, чтобы добиваться прекрасных результатов.
Makita 2704
Makita 2704 – станок, который используется в процессе распила различных материалов. С его помощью можно быстро справляться со всеми процедурами, обеспечивать прекрасный результат, вас порадует производительность.
В изделии используется двигатель с мощностью 1650 Вт. При производстве была реализована система запуска и торможения, инструмент защищен от скачков напряжения и прослужит вам действительно долго.
Используется диск с диаметром 255 мм. Он вращается на высокой скорости, гарантирует прекрасный и точный рез. Присутствуют упоры, с ее помощью деталь можно зафиксировать и исключить последующее смещение.
Стол производится из алюминия и очень надежен. Отверстия позволяют расположить оснащение на верстаке и выполнить крепление с применением болтов. Можно провестиподключение пылесоса, который осуществляет дальнейшее удаление пыли. Присутствует защитный кожух, он исключает возможность получения травм. Встроена система защиты от случайного запуска устройства.
Makita Lh2200FL
Makita Lh2200FL – универсальная модель, которая покроет различные потребности пользователей. Пила прочная, стол отливается из сплавов на основе алюминия. Можно распиливать пластмассу, древесину, профили из алюминия с небольшой толщиной, добиваться идеальных результатов.
Система плавного запуска и торможения снижает степень износа при эксплуатации. Поворотная линейка обеспечивает поддержку прутка. Производитель предусмотрел защиту от случайного пуска. Устройство универсальное, в нем сочетается несколько видов оборудования.
Пользователи оценят наличие светодиодов для подсветки. Они позволяют проводить работы даже в условиях плохого освещения. Присутствует лазерный маркер, с его применением можно дополнительно увеличить точность. Пила продумана до мелочей и отлично собрана, подойдет для профессионалов, которые предъявляют высокие требования.
Материал оказался полезен? Поделитесь ссылкой с друзьями!
new-parket.ru
Станки для обработки паркета «Паркетный метр»
Станки для обработки паркета «Паркетный метр»Паркетный метр
Все виды работ по паркету
Паркетный
метр
Все виды работ по паркету
Все виды работ по паркету
Заказать звонок
Ежедневно, с 09:00 до 21:00
» Станки для обработки паркета
Ремонт паркета это очень сложная и кропотливая работа, требующая мастерства применения качественного оборудования. Поэтому в своей работе мы пользуемся только профессиональной техникой, от ведущих мировых производителей.
Станки для обработки паркета используются для подрезки паркетных плашек под необходимые размеры. Данные станки позволяют выполнять работу быстро и качественно.
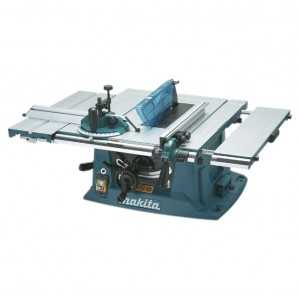
Распиловочный станок
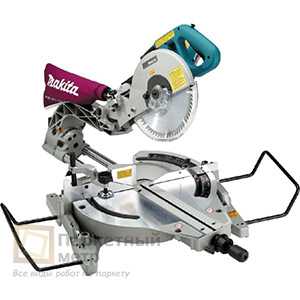
Пила торцевая
Пилы используются для таких работ как ремонт паркета, установка плинтусов и демонтаж паркета.
Правильно и ровно отрезать плинтус возможно только на торцевой пиле. А сделать подрезку паркета вдоль стены – только с помощью погружной пилы.
Использование качественного и надежного инструмента является залогом качественной работы специалистов компании “Паркетный метр”
Похожие материалы:
Полезная информация
Уход за паркетомЧтобы паркет долго оставался красивым после укладки или циклевки, необходимо за ним ухаживать и проводить профилактическую чистку специальными …
Еще сатьиЧасто задаваемые вопросы
parket-metr.ru
Художественный паркет
История
История компании берет свое начало в 1999 году. Небольшая команда единомышленников задалась целью возродить в стране богатые традиции паркетного дела, стремясь удовлетворить растущий спрос на эксклюзивный художественный паркет. В то время рядом с корпусами угольной шахты «Бельковская» (Тульская обл.) стояло лишь одно здание, в котором и расположили цех по изготовлению художественного паркета.
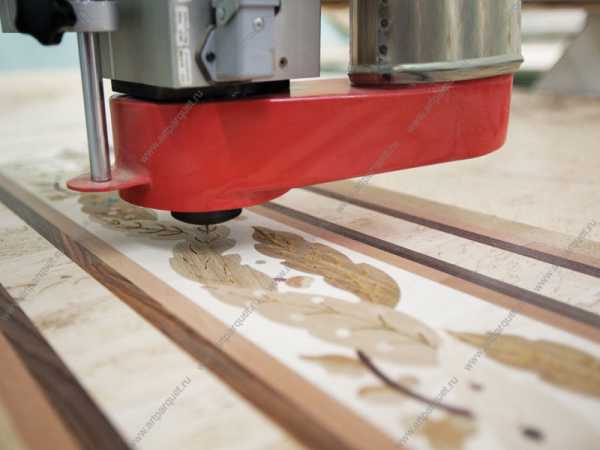
Общие сведения
Художественный паркет – орнаментальная композиция, состоящая из набора отдельных элементов и выполненная на основе сочетания древесины различных пород деревьев.
Современные станки позволяют с высокой точностью изготавливать самые сложные элементы паркета. На квадратном метре художественного паркета может быть до 2 – 3 тысяч деталей. Основную палитру составляют около 40 пород древесины разных цветов и текстуры.
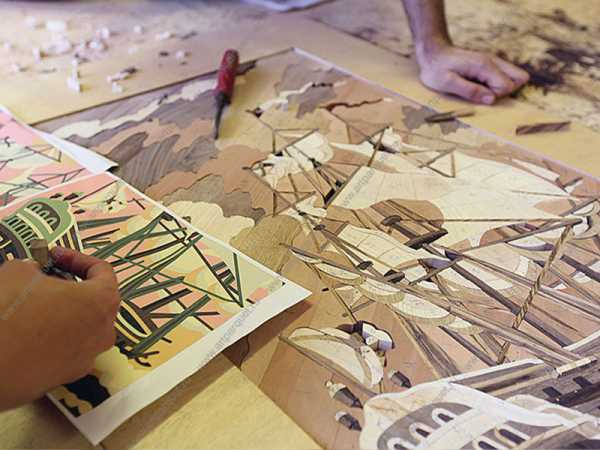
Производственные мощности
Сегодня цех по изготовлению художественного паркета занимает более 2 тыс. м2 (три этажа) и в нем трудиться более 20 мастеров.
Объёмы производства художественного паркета составляют 24000 м2 в год. Приоритетом компании является индивидуальный подход к каждому заказчику.
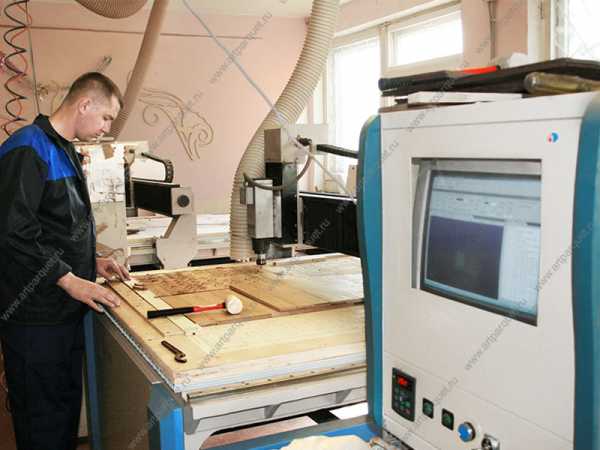
Процесс изготовления начинается с дизайн–проектирования, заключающегося в разработке изображения паркета, отражающего грамотное планировочное решение и оригинальный дизайн.
Дизайн–проектирование включает несколько последовательных этапов: набросок, эскиз, дизайн-проект, 3D визуализация и наряд.
На этапе дизайн–проектирования осуществляется подбор древесины по эстетическим и физическим параметрам (плотность, твердость, стабильность). Композиции строятся с учетом геометрии, стиля и технических возможностей производства.
Набросок
На основе обмерного плана помещения (с учетом расстановки мебели, расположения оконных и дверных проемов) наши дизайнеры предлагают художественные решения, раскрывающие потенциальные возможности пространства, и подбирают декоративные художественные элементы (бордюры, розетки, укладки и другие художественные элементы). В результате создается набросок будущего паркета.
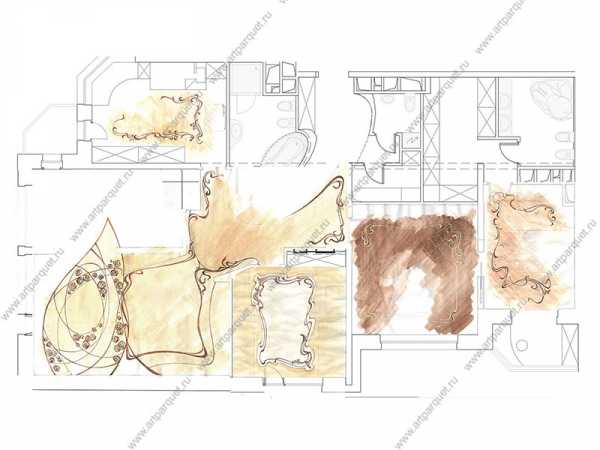
Эскиз
С учетом стилевого решения, индивидуальных предпочтений и цветового решения выполняется эскиз – подробный цветной рисунок будущего интерьера.
Дизайнеры создают уникальные эксклюзивные проекты на основе авторских идей, рисунков старинных дворцовых интерьеров или типовых элементов из нашего каталога.
В постоянно обновляемом каталоге компании представлено более 1000 элементов художественного паркета.
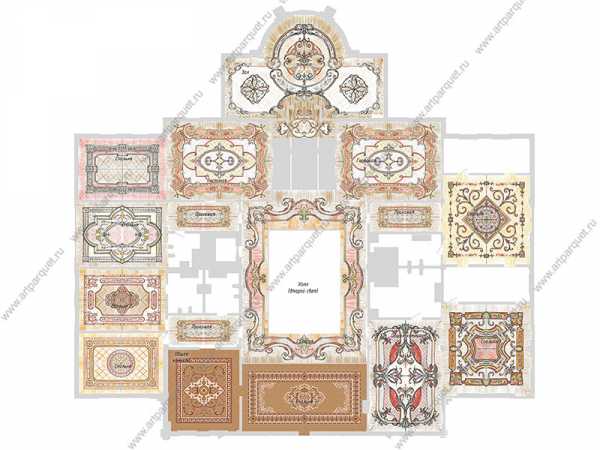
Дизайн–проект
Выполняется компьютерная визуализация паркета – наглядные изображения фотографического качества паркета (дизайн–проект). Дизайн–проекты помогают предварительно получить представление о конечном результате уже на этапе проектирования.
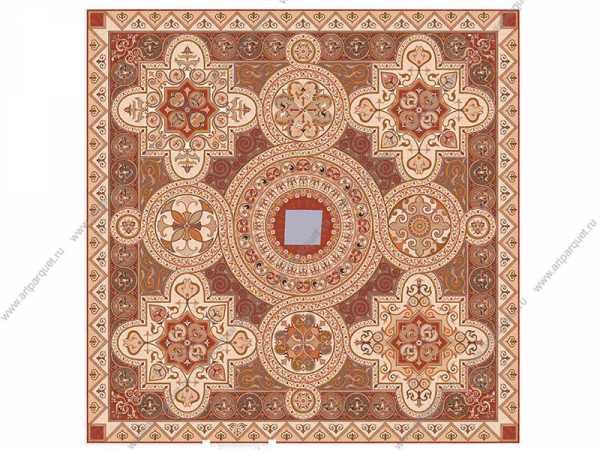
3D визуализация
При разработке масштабных проектов выполняется их 3D визуализация. Трехмерное моделирование позволяет получить фотореалистичные изображения полов в предполагаемом интерьере в мельчайших подробностях.
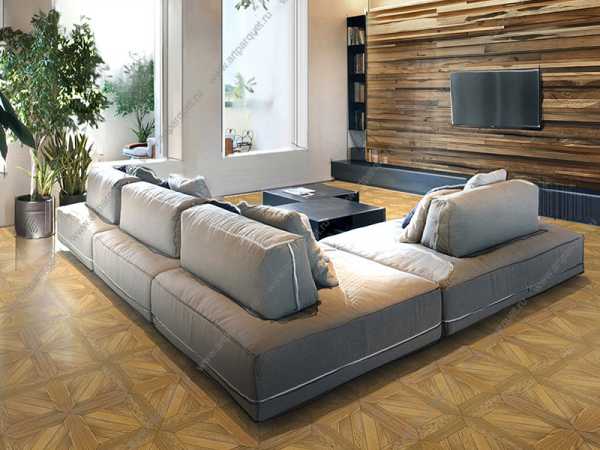
Наряд
После того как проект утвержден заказчиком конструктора выполняют наряд, представляющий собой чертеж, на котором точно указаны геометрические размеры каждой детали изделия и породы древесины. Наряд является четкой инструкцией для производственного цеха.
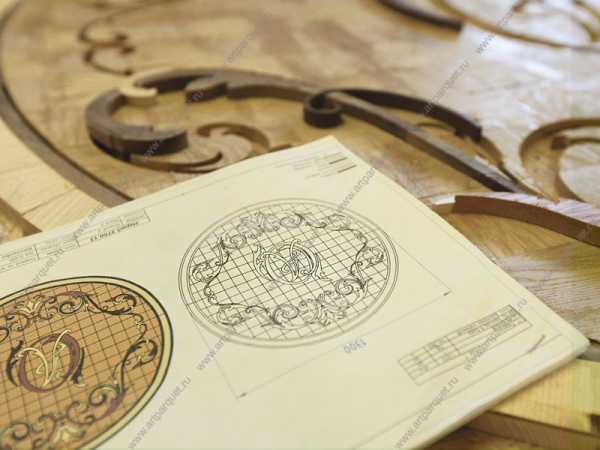
Художественный паркет в зависимости от геометрической формы деталей бывает трех типов. Различия между этими видами паркетов существенные, поэтому и технологии их изготовления отличаются.
Пильный | Фрезерный | Смешанный |
состоит из деталей прямолинейной формы | состоит из криволинейных деталей | состоит из деталей прямолинейной и криволинейной форм |
![]() |
![]() |
![]() |
В настоящее время мы производим два вида художественного паркета:
- с финишным покрытием;
- без финишного покрытия.
ЭТАПЫ ПРОИЗВОДСТВА ХУДОЖЕСТВЕННОГО ПАРКЕТА
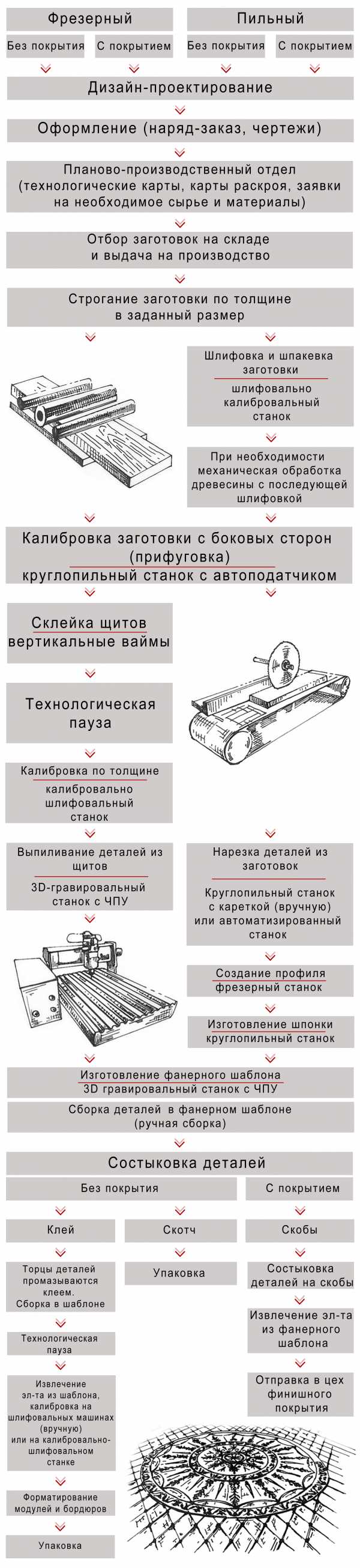
ОСОБЕННОСТИ ПРОИЗВОДСТВА ФРЕЗЕРНОГО ПАРКЕТА
Детали фрезерного художественного паркета, имеющие криволинейную форму, выпиливаются из щитов, которые склеиваются из паркетных заготовок.
ИЗГОТОВЛЕНИЕ ЩИТОВ
Отбор заготовок для щита
На складе для изготовления щита осуществляется тщательный отбор заготовок в соответствии с выполненным раскроем. Заготовки выбираются и по толщине. Толщина изготавливаемого нами художественного паркета бывает двух размеров: 15 и 20 мм. Также заготовки проходят тщательный отбор по цветовой гамме.
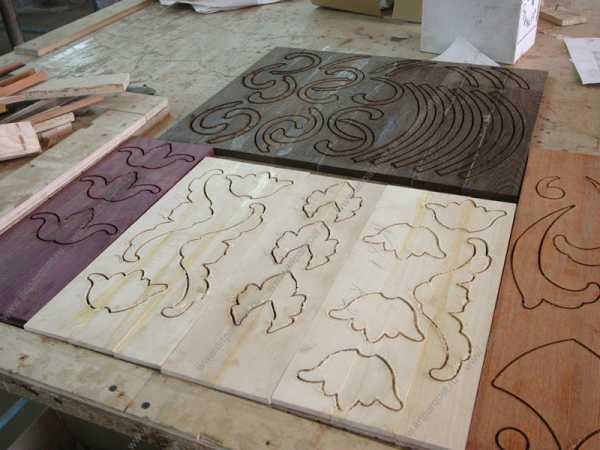
Выравнивание заготовок по толщине
Для выравнивания заготовок по толщине (как правило, заготовки имеют толщину на 1 – 2 мм, превышающую требуемый размер) используется односторонний рейсмусовый станок. Рейсмус предназначен для плоскостного строгания заготовок по толщине в заданный размер.
Современные модели, которыми оснащено наше производство, имеют облегченную систему смены рабочих ножей и увеличенный контроль глубины резания.
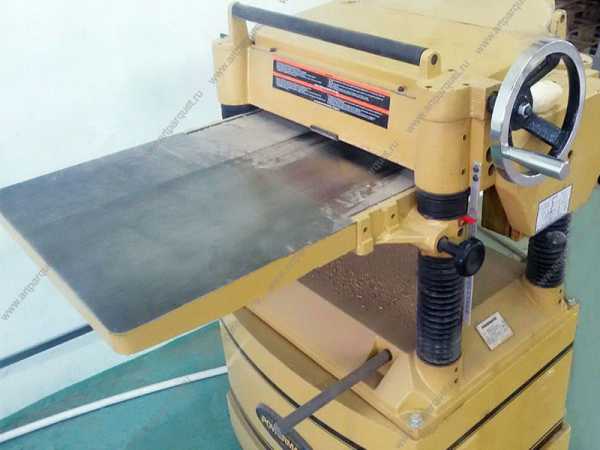
Породы, которые со временем окисляются на воздухе и меняют свой цвет, подвергаются обязательной шлифовке для выявления реального цвета древесины.
Калибровка заготовок
Затем осуществляется калибровка заготовки с боковых сторон (прифуговка) под склейку или сборку. Эта операция выполняется на круглопильных станках, предназначенных для точной и высокопроизводительной продольной прифуговке деталей. Для автоматизации процесса подачи станки снабжены автоподатчиками, позволяющими сделать их работу более производительной и безопасной.
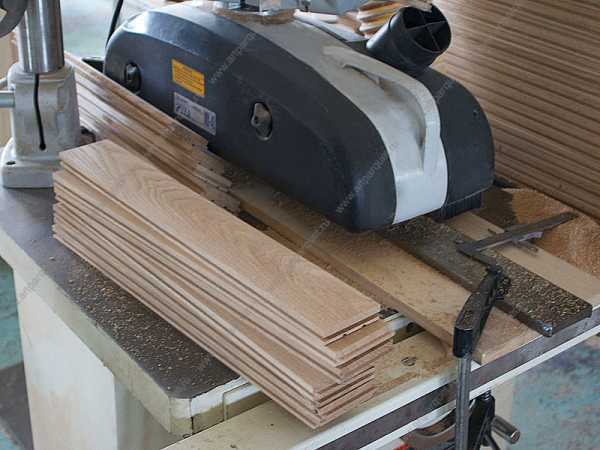
Склейка заготовок в щиты
Склейка заготовок в щиты осуществляется на промышленных вертикальных пневматических ваймах со встроенными нагревательными элементами, обеспечивающими оптимальный режим склейки.
Ваймы итальянского производства позволяют работать с самыми разнообразными типами и породами заготовок с предварительным подбором технологии и склеиваемых материалов.
Склейка – сложный процесс, зависящий от множества факторов (температуры, толщины склеиваемых деталей, клея и др.). Цех оснащен четырьмя ваймами, что обеспечивает непрерывный цикл погрузки и разгрузки заготовок и, как следствие, высокую производительность.
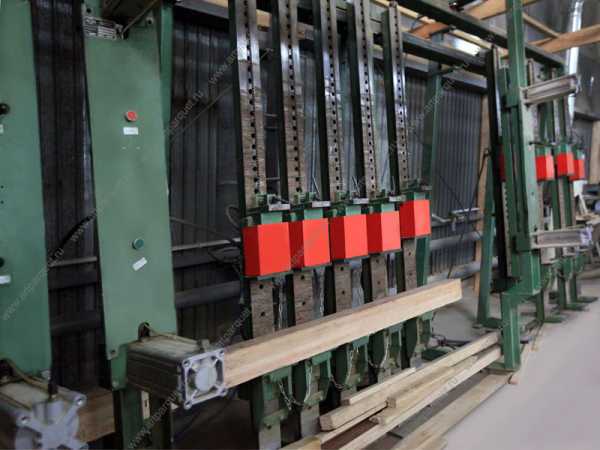
После склейки для отверждения клея выполняется технологическая пауза (сутки).
Выравнивание щитов по толщине
Щиты для выравнивания по толщине и получения требуемой шероховатости поверхности поступают на калибровально-шлифовальные станки.
Наше производство оснащено станками чешского производства Houfek. Станки позволяют производить калибровку и шлифовку большого количества различных материалов и поверхностей.
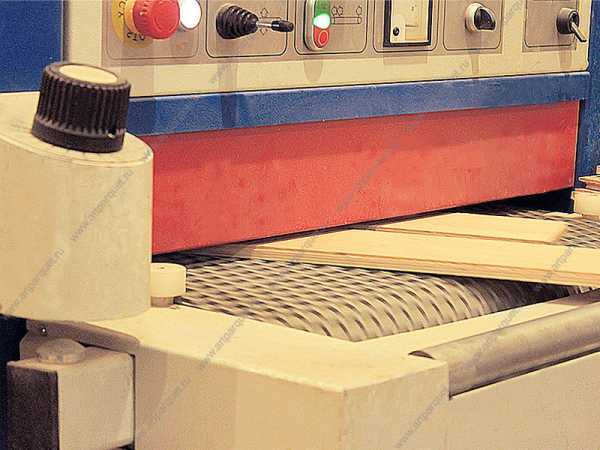
УЧАСТОК ФРЕЗЕРОВАНИЯ
Раскрой щитов
Конструкторами на основе наряда выполняется раскрой, заключающийся в распределение деталей в щите. Раскрой осуществляется в зависимости от размеров щита и деталей с учетом направления волокон.
Для нашей компании была создана специальная компьютерная программа, позволяющая в автоматическом режиме наиболее оптимально раскраивать щит, как по времени выпиливания деталей, так и по расходу материала.
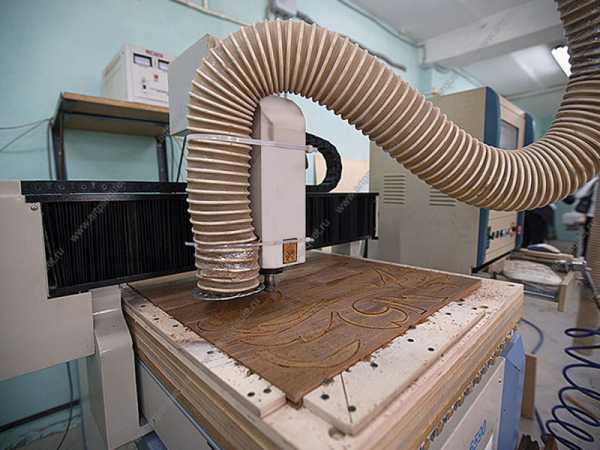
Из щитов согласно технологической схеме раскроя выпиливают детали с помощью 3D гравировальных станков с числовым–программным управлением (ЧПУ).
Оснащение участка
Для оптимизации работы и повышения производительности цех оснащен одиннадцатью разноформатными современными 3D гравировальными станками с ЧПУ. Это позволяет нам выполнять одновременно до 10 нарядов.
Станки отличаются высокой скоростью и предельной точностью, которая обеспечивается за счет высокоточной механики, дорогостоящих сервомоторов, современной стойки ЧПУ. Весь процесс обработки отражается на мониторе системы. В процессе работы могут быть задействованы программы оптимизации или ускорения процесса обработки. Станки снабжены устройствами для удаления стружки.
Детали более крупных размеров выпиливаются на широкоформатных станках от производителя Тайвань Fulltek.
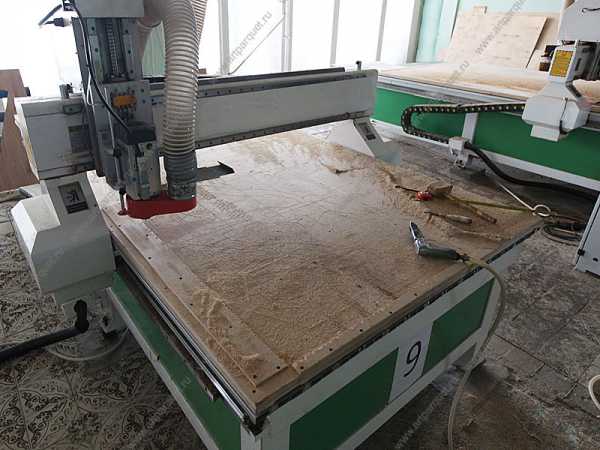
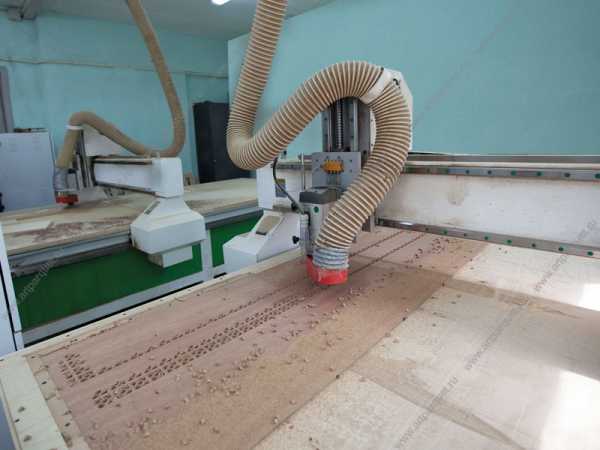
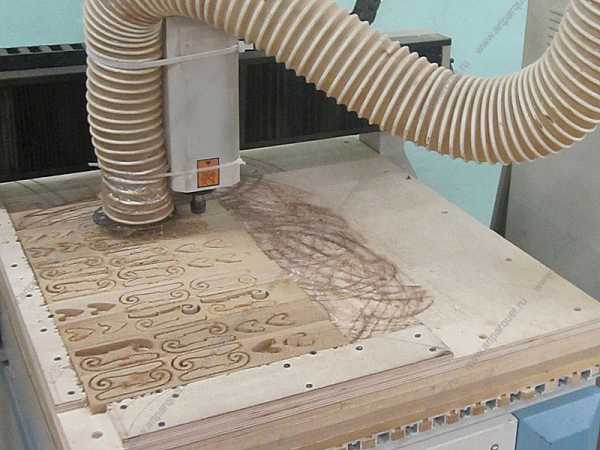
Точность изготовления
Точность изготовления криволинейных деталей составляет 0,05 мм. Такая поразительная точность практически исключает процесс подгонки деталей при сборке изделия, сократив его до контроля за качеством выполнения операций и мелкой доводкой лицевых поверхностей.

Фанерный шаблон
Параллельно, согласно чертежам, изготавливается фанерный шаблон, представляющий собой рамку сектора готового изделия. На 3D гравировальных станках с ЧПУ в фанере толщиной 15 или 20 мм (в зависимости от толщины паркета) выпиливается поле, которое может быть любой формы и размера.
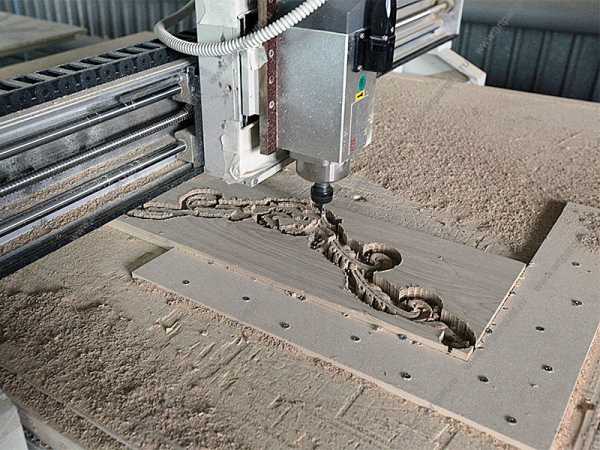
Интарсия
Часто используется технология интарсия, заключающаяся в установке рисунка на определенную глубину основного паркета. В этом случае шаблон изготавливается из основного паркета.
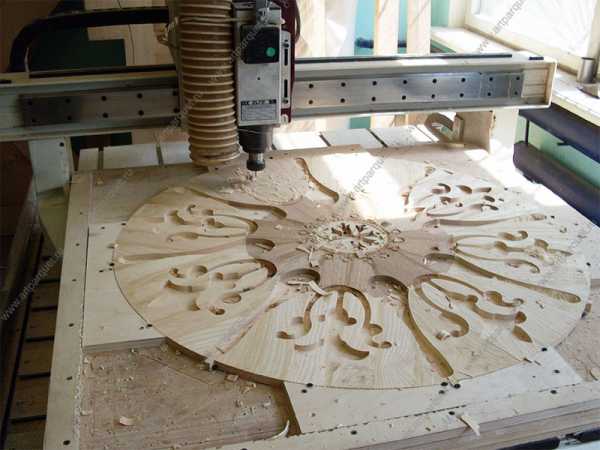
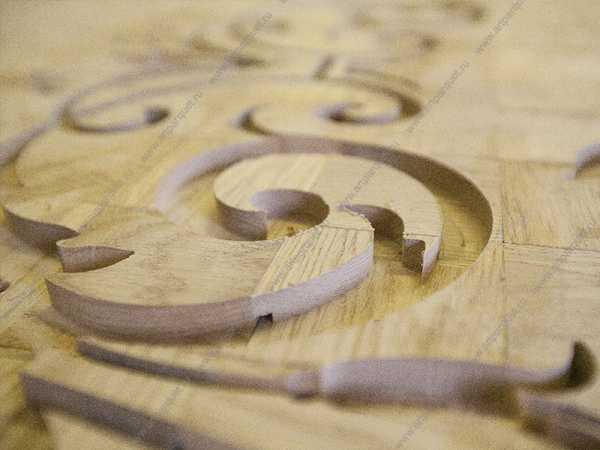
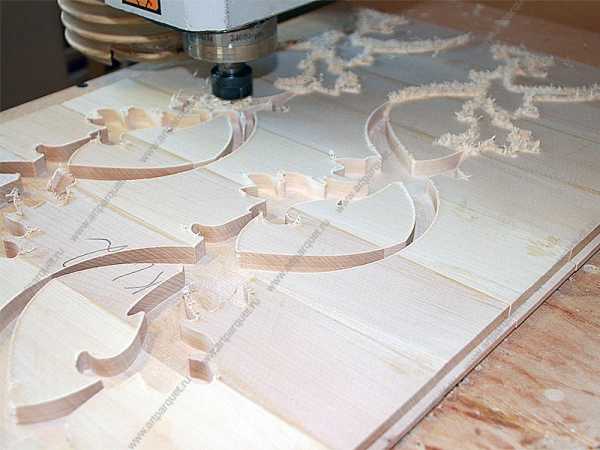
УЧАСТОК СБОРКИ
Выпиленные детали поступают на участок сборки. Сборка деталей в фанерном шаблоне осуществляется вручную согласно наряда. Детали собираются на сухую.
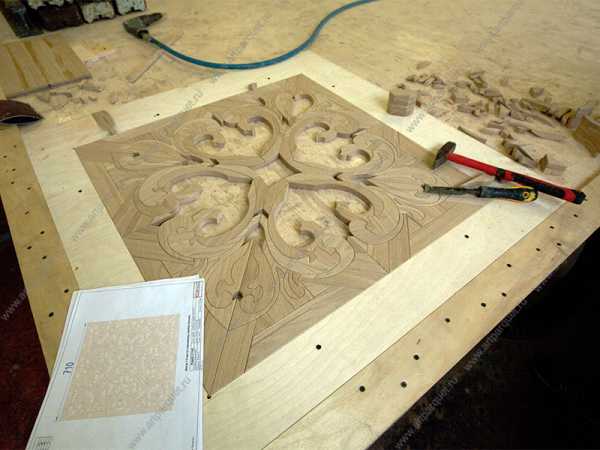
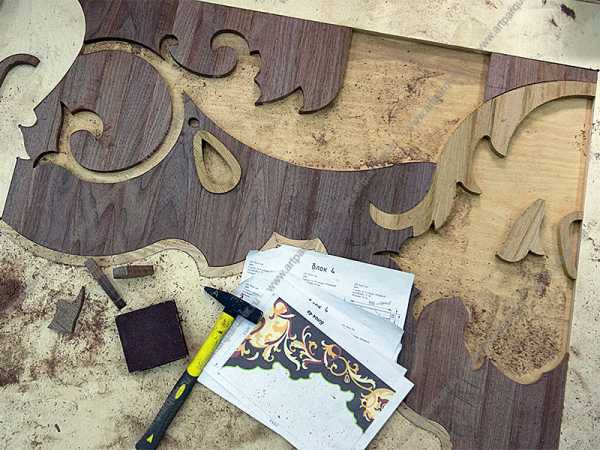
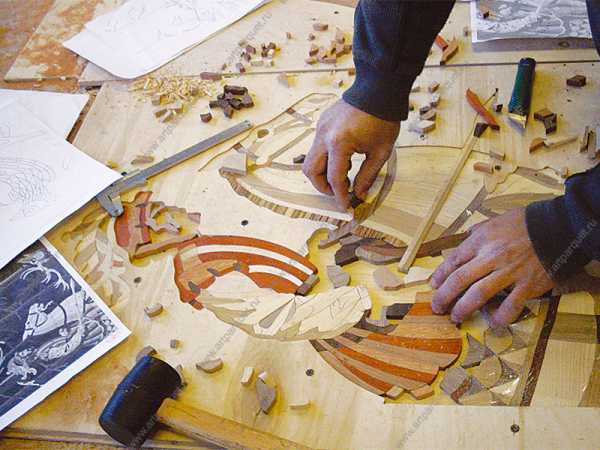
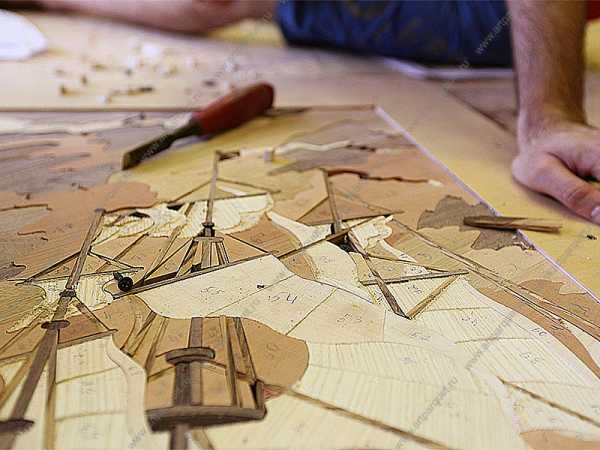
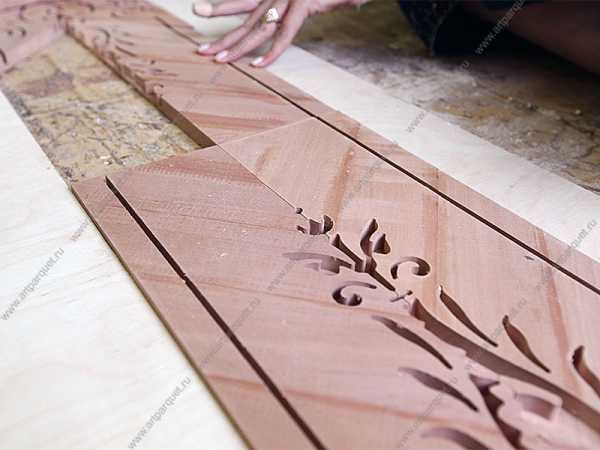
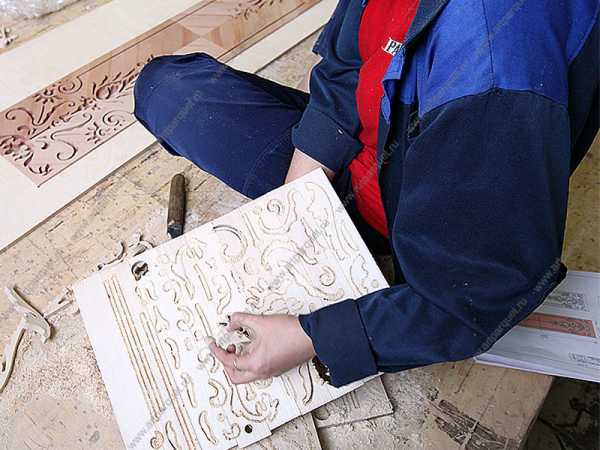
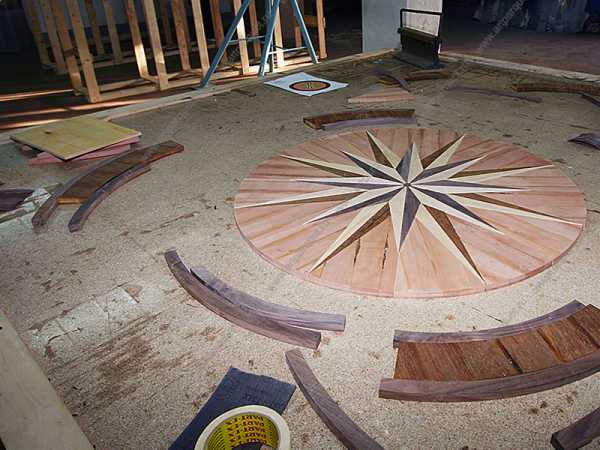
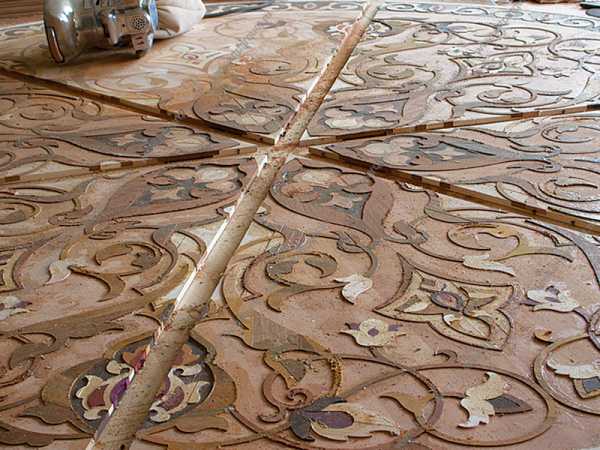
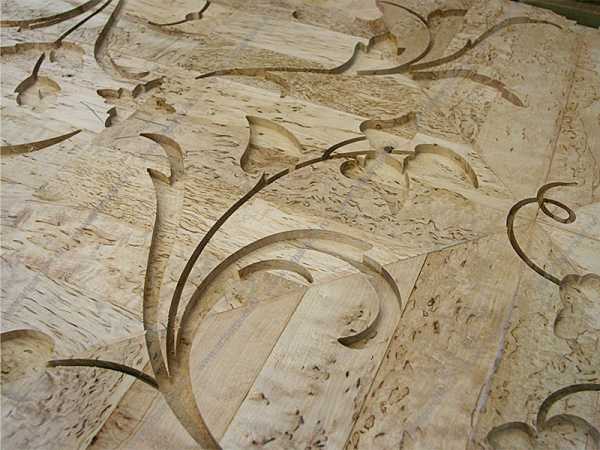
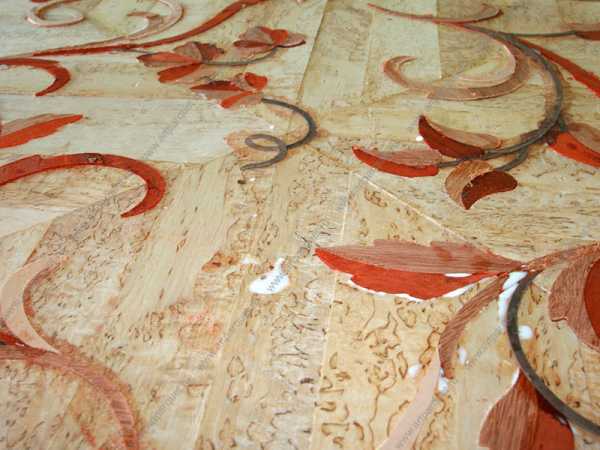
ОСОБЕННОСТИ ПРОИЗВОДСТВА ПИЛЬНОГО ПАРКЕТА
Пильный паркет собирается из деталей, нарезанных непосредственно из паркетных заготовок. Конструктора также тщательно осуществляют отбор имеющихся на складе заготовок (кратных размерам требующихся деталей) с учетом их оптимального раскроя. Затем заготовки калибруются по толщине на одностороннем рейсмусовом станке. При изготовлении паркета с финишным покрытием заготовки проходят этап шлифовки и шпаклевки. Если требуется в соответствии с дизайн–проектом, то и механическую обработку.
Шлифовка и механическая обработка (браширование) выполняется на шлифовально–калибровальных станках с Gridggio (Италия). Шпаклевка осуществляется вручную.
Далее выполняется калибровка заготовок по ширине на круглопильных станках Jet c автоматической подачей заготовок.
Следующий этап – нарезка деталей.
Нарезка деталей
На нашем производстве выполняется два вида нарезки: на круглопильном станке с кареткой вручную и на автоматизированном станке.
Преимущества ручной распиловки в быстрой перенастройке станка. Автоматизированная используется при выполнении больших объемов распиловки. Настройка станка требует больших временных затрат, зависит от ширины заготовки, породы древесины и подбирается индивидуально для каждой партии материала.
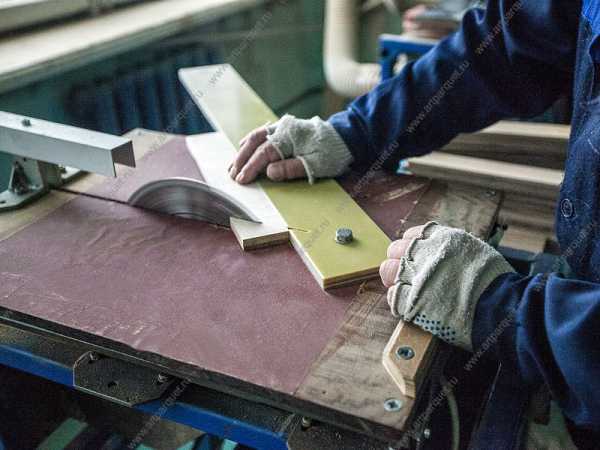
Создание профиля
Каждой детали для паркета с финишным покрытием придается необходимый профиль: нарезается фаска и паз на фрезерном станке JET. Станок отличается высокой точностью и большой мощностью.
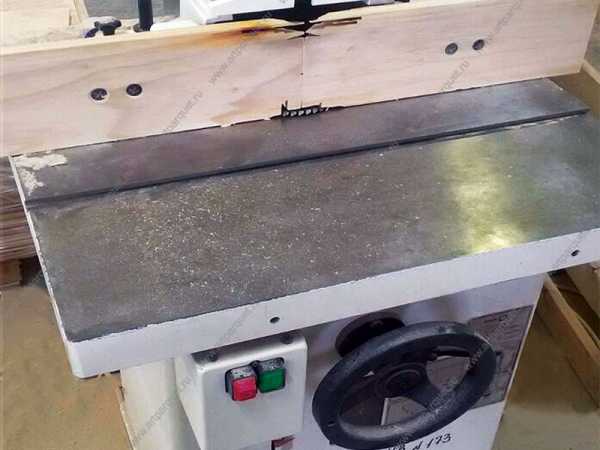
Сборка деталей в фанерном шаблоне
Далее производится сборка деталей в фанерном шаблоне стыковкой через шпонку. Шпонка изготавливается из фанеры на круглопильном станке.
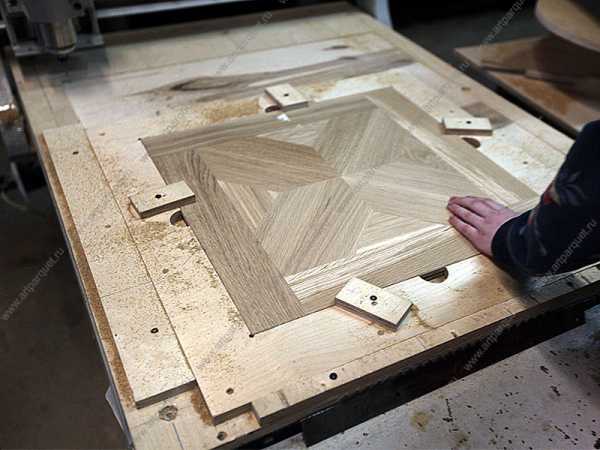
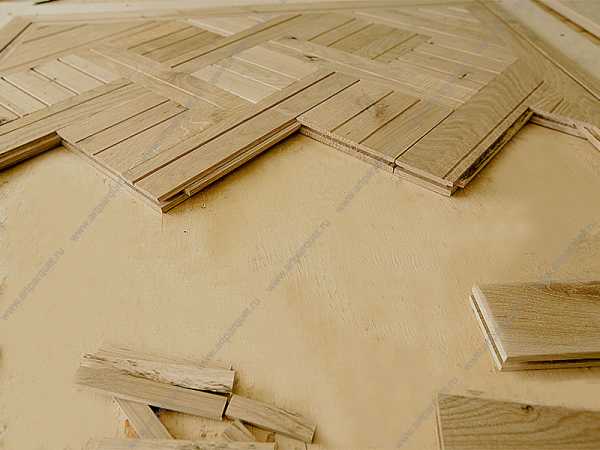
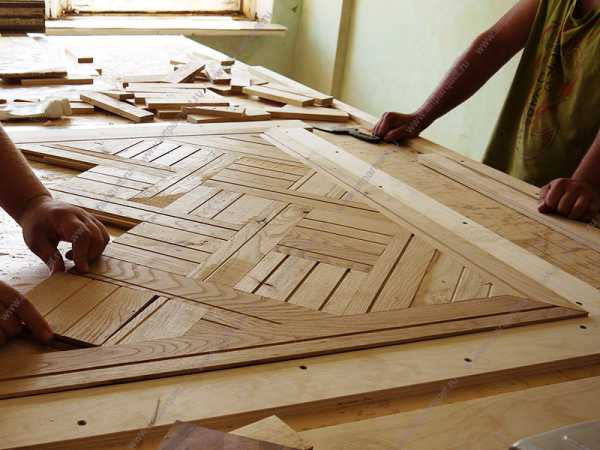
СКРЕПЛЕНИЕ ДЕТАЛЕЙ ПАРКЕТА
Для скрепления деталей мы используем три технологии.
Для паркета без финишного покрытия | Для паркета с финишным покрытием | |
на клей |
на скотч |
на скобы |
![]() |
![]() |
![]() |
Скрепление деталей на клей
Детали вытаскиваются из шаблона, их торцы промазываются клеем и снова вставляются в шаблон. После технологической паузы готовый элемент вынимается из шаблона и отправляется на калибровку.
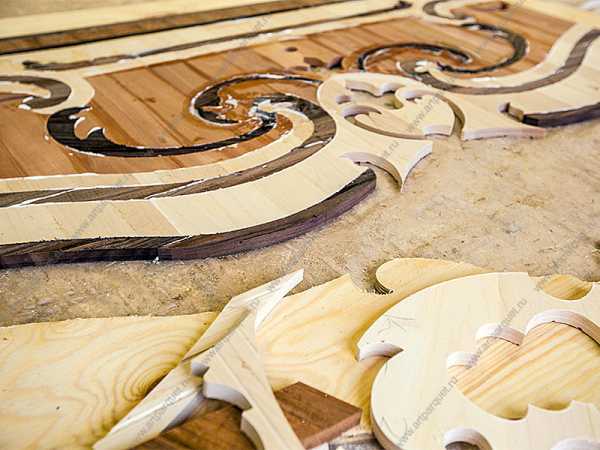
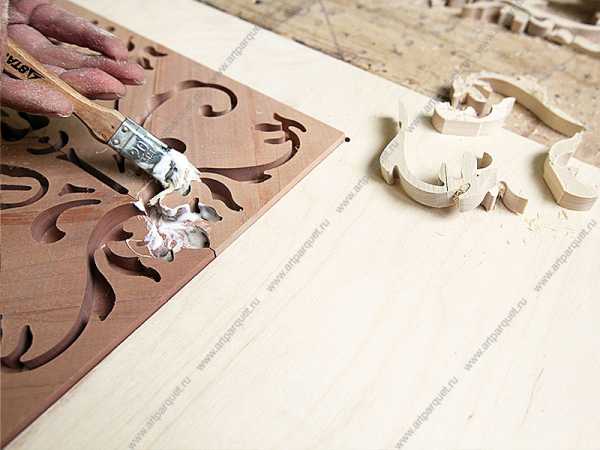
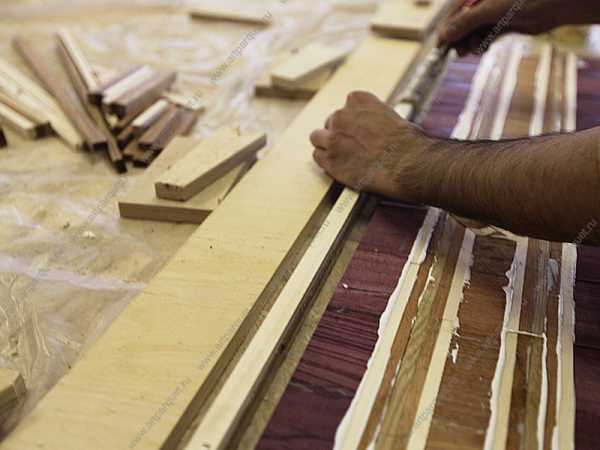
Калибровка выполняется сверху и снизу, чтобы убрать перепады по высоте из-за выступившего клея. Если размер элемента превышает 1100 мм, то калибровка осуществляется вручную с помощью шлифовальных машин, в противном случае – на калибровально–шлифовальном станке.
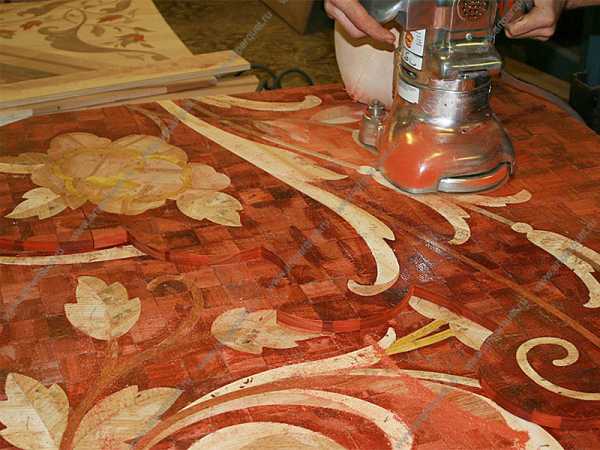
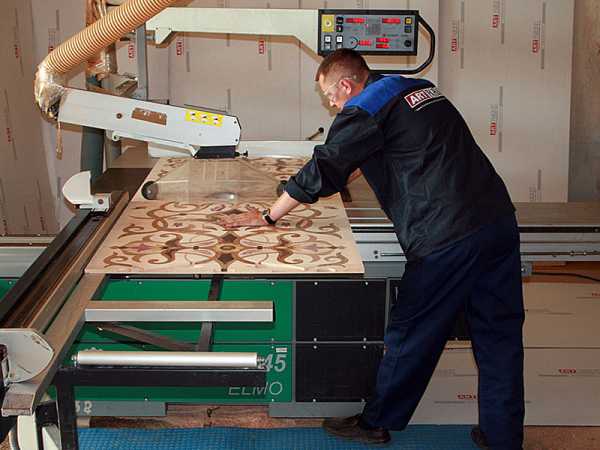
При изготовлении модулей и бордюров в обязательном порядке осуществляется обгонка, заключающая в придании им правильной геометрии. Это позволит на объекте осуществить стыковку изделий без зазоров.
Далее производится упаковка изделий.
Скрепление деталей на скотч
Детали, оставшиеся в фанерном шаблоне, скрепляются друг с другом (с лицевой стороны) скотчем. Готовое изделие упаковывается сверху и снизу транспортировочной фанерой.
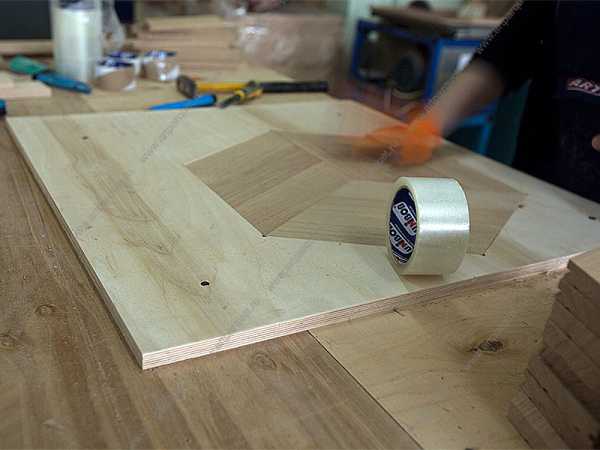
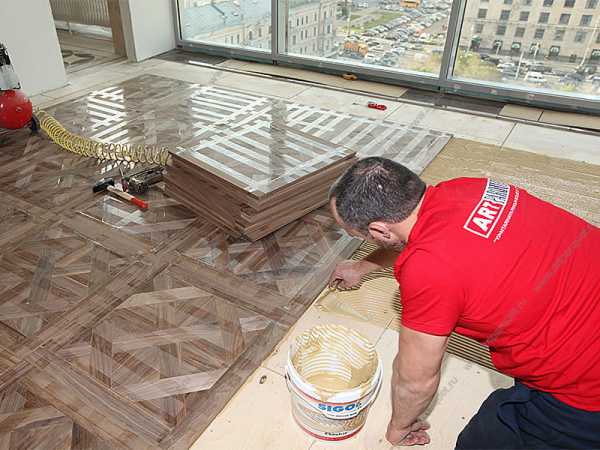
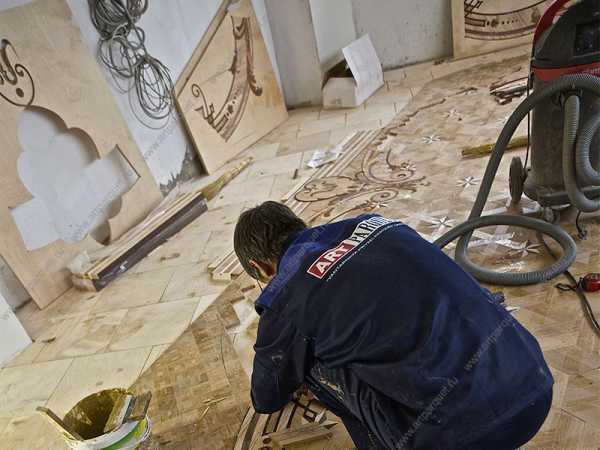
На объекте элементы вынимают из фанерного шаблона, который используют как шаблон для фрезерования в полу внешнего контура изделия, получая в результате этого идеальное качество стыка художественной вставки с основным паркетом.
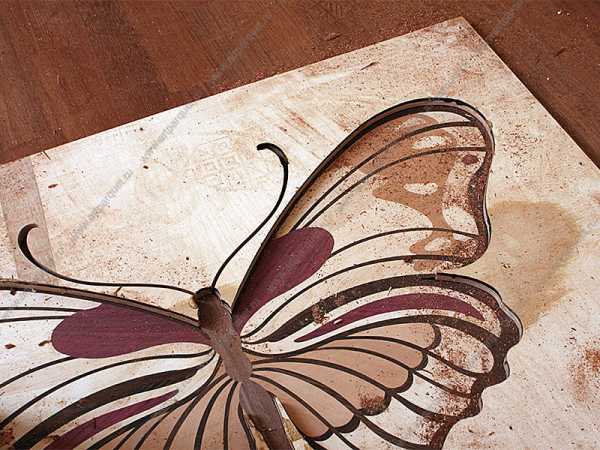
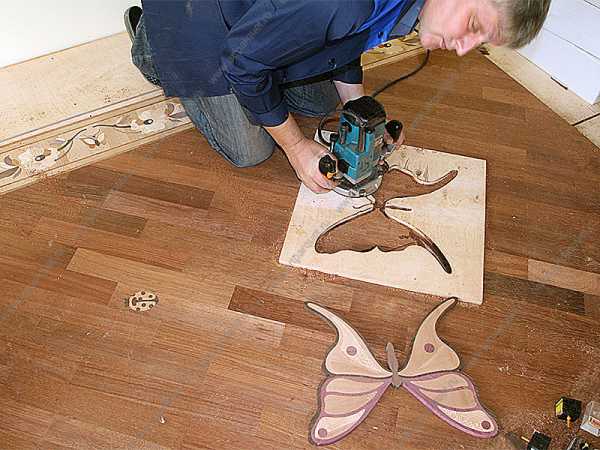
Скрепление деталей на скобы
Детали паркета с финишным покрытием скрепляются на скобы. Затем элементы паркета вынимается из шаблона и отправляется в цех финишного покрытия.
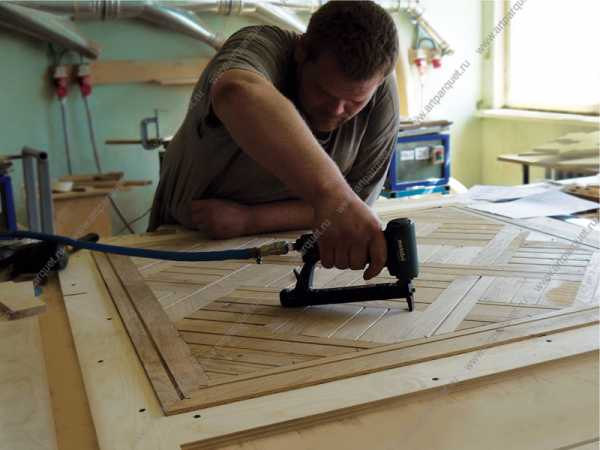
Техника графье
Минимальные размеры криволинейных деталей ограничены размером фрезы 3D гравировального станка. Для придания изящества паркетной композиции используют технику графье. Эта техника является своеобразной гравировкой по дереву. С помощью этой технологии создаются узоры, получаемые прорезными тонкими желобками, которые заполняются мастикой, как правило, контрастного цвета.
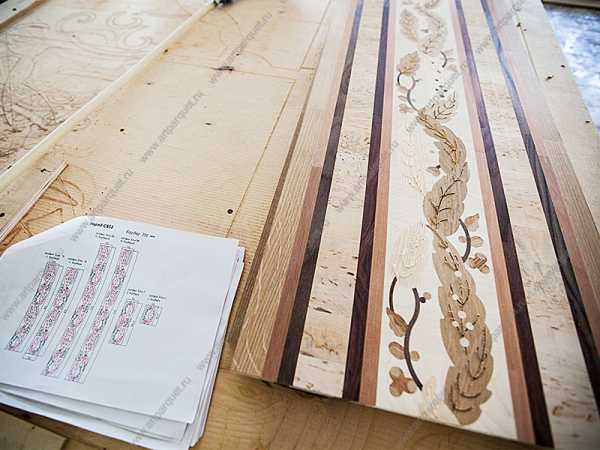
Паркет с металлом и камнем
При выполнении мозаичного паркета с камнем и металлом скрепление деталей производится только на клей.
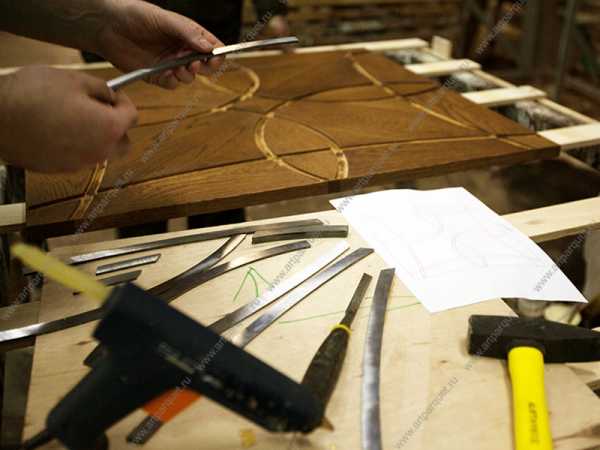
Стоит отметить, что на стоимость производства художественного паркета оказывают влияние следующие факторы:
- Сложность рисунка (кривизна и изогнутость линий).
- Количество деталей.
- Размер некоторых модулей паркета.
- Порода древесины и ее сортировки.
- Количество пород древисины.
artparquet.ru
Машина для циклевки паркета – какие инструменты нужны? + Видео
Время от времени паркету нужен капитальный ремонт, который подразумевает очистку поверхности от старого лака. Раньше это делалось вручную, сегодня же к вашим услугам машина для циклевки паркета.
Инструмент для циклевки паркета – что понадобится?
Избежать полностью ручного труда не удастся даже при наличии всех современных паркетошлифовальных машин. Всегда останутся углы, труднодоступные места за трубами или небольшие неровности, которые аппарат для циклевки паркета попросту не сможет достать. Вот в таких случаях вам и пригодится ручная цикля для паркета. Поэтому если этот дедовской инструмент завалялся в вашей мастерской, ни в коем случае не выбрасывайте его – он еще вам пригодится.
Если же цикли нет, а объем ручной работы на удивление оказался совсем небольшим, можно воспользоваться куском битого стекла – острый край отлично соскабливает слоя древесины. Только смотрите, не порежьтесь! Тем не менее, объем ручного труда за многие годы сократился в разы. Электрическая цикля для паркета позволяет за один день полностью справиться с циклеванием и шлифованием паркета в нескольких комнатах, так что покупать такие агрегаты нет никакого смысла – нужное оборудование многие строительные компании предлагают в аренду.
Изменился и сам принцип циклевания. Наверняка этот процесс вызывает у вас воспоминания о кадрах из фильма «Приключения Шурика», где ревущая машина, снимавшая стружку с паркета, перебивала пламенную речь прораба о балеринах, бороздящих просторы космоса. Принцип такого агрегата чем-то похож на работу газонокосилки – ножи, закрепленные на барабане, снимали слой стружки в несколько миллиметров.
Однако из-за такой потери ресурса паркета от этого способа в большинстве случаев отказываются – при средней толщине нового паркета в 10 мм его хватит максимум на два таких ремонта!
Поэтому машина для циклевки сегодня представляет собой особо мощную барабанную шлифовальную машину, в которой ножи заменены на шлифовальную бумагу грубой зернистости. Понятие «циклевка» осталось как обозначение процесса ремонта паркета, однако принцип совсем другой – абразив, закрепленный на барабане, зачищает слой лака вместе с древесиной. Даже таким способом можно снять слой в несколько миллиметров.
Для финишной шлифовки паркета применяется плоскошлифовальная машина. Процесс обработки возможен благодаря дискам с наждачной бумагой, которые двигаются в горизонтальной плоскости. Для обработки краев, углов и труднодоступных мест под батареями сегодня есть специальное оборудование – углошлифовальный бордюрный станок для паркета. Эта машинка для циклевки паркета получила в народе меткое название «сапожок», ввиду внешнего сходства с этой обувью.
Также вам понадобится много наждачной бумаги. Для машины барабанного типа применяют бумагу P40 или P60, в зависимости от породы дерева или степени циклевки паркета, а для финишной шлифовки используют P80 или P120. Не забудьте купить хороший респиратор, защитные очки и беруши – будет много древесной пыли! Чтобы убрать ее, вам понадобится мощный пылесос. Посчитав стоимость арендованной техники и затраты на расходные материалы, вы увидите цифру в несколько раз меньше, чем запросила бы за ремонтные работы строительная фирма.
Когда циклевка не поможет – определяем повреждения паркета
Приступать к реставрации паркета методом циклевки и шлифования можно в том случае, если паркет представляет из себя равномерно истоптанную поверхность без видимых повреждений. Однако во многих случаях циклевание невозможно или бесполезно:
- паркет рассохся или наоборот, размок;
- толщина половиц стала меньше 5 мм;
- пол влажный и почерневший;
- паркет точит жучок-древоточец.
В случае с первым пунктом паркет необходимо демонтировать и заново собрать, заменив растрескавшиеся дощечки или высушив их. Во втором случае можно попробовать обойтись лишь щадящей плоскошлифовальной обработкой, однако качество циклевания будет невысоким. Замена пола на новый – оптимальный вариант в таком случае.
Влажность паркета можно определить как на глаз, по наличию плесени, так и с помощью небольшого эксперимента. Для него вам понадобится кусок полиэтиленовой пленки со сторонами 1 м – постелите его на пол и придавите края рейками. Если в течение суток под пленкой появился конденсат, циклевку следует отложить. Влага свидетельствует о недостаточной гидроизоляции пола, поэтому паркет следует демонтировать, пол гидроизолировать и только потом начинать все паркетные работы.
Жучок-древоточец проявляет себя характерными кучками древесной пыли. Если вам удалось выявить его на ранних стадиях разрушительной деятельности, положение еще можно спасти. В этом вам поможет раствор нафталина с бензином, вазелиновое масло или смесь керосина и скипидара (один к трем). Выбранный раствор следует заливать шприцом в видимые отверстия, а также обработать половицы по всей поверхности.
Чтобы отрава задержалась в древесине надолго, заделайте отверстия воском или парафином. Эту процедуру следует повторить как минимум 2 раза с перерывами на три недели. Если новых отверстий не появилось, значит вам удалось вывести этого вредителя. Тем не менее, половицы, которые уже повреждены, скорее всего, придется заменить на новые. Если же повреждения несущественны, их можно замазать шпаклевкой.
Машина для циклевки паркета – правильное применение
Итак, оборудование для циклевки паркета арендовано, паркет к процессу пригоден, мебель из комнаты вынесена, и пол пропылесосен. Если в паркете есть шатающиеся, скрипучие или поврежденные половицы, их следует закрепить или заменить на новые.
Если это возможно, демонтируйте плинтусы. В случае если аккуратно их снять не получается, лучше оставить, как есть. Проверьте пол на наличие торчащих гвоздей или саморезов – такие следует забить или закрутить поглубже. Учтите, что оборудование для циклевки потребляет около 2,5 кВт энергии, не говоря уже о пусковой мощности. Не каждая проводка в состоянии выдержать такую нагрузку.
Как правильно пользоваться машиной для циклевки паркета — пошаговая схема
Шаг 1: Грубая обработка
На этапе грубой обработки может быть снят слой в несколько миллиметров. Ее задача – снять слой старого лака и избавиться от неровностей. На барабанную паркетно-шлифовальную машину установите наждачную ленту грубой зернистости. Если паркет образовывает рисунок «Палуба», то проходить машинкой следует от угла к углу, если «Елочкой» – то по прямой линии от стены к стене.
Главное, чтобы угол шлифования к направлению роста волокон составлял 45°. По мере необходимости меняйте абразив. Регулируйте давление барабана на пол – если двигатель работает нормально, а машина снимает слишком небольшой слой древесины, увеличьте давление. Иногда необходимо повторить грубую обработку до трех раз.
Шаг 2: Шлифовка
Работая плоскошлифовальной машиной, используйте наждачную бумагу более высокой зернистости, например, Р120. Проходы следует делать вдоль древесных волокон – если вы двигались из угла в угол, то теперь нужно двигаться от стены к стене вдоль плашек. Эта обработка сделает древесину совершенно гладкой.
Шаг 3: Обработка труднодоступных мест
Места, которые не достали крупные агрегаты, следует обработать ручной циклей или «сапожком».
На этом все! Вам останется только убрать помещение от древесной пыли и заняться его покрытием, а это уже другая тема для разговора.
remoskop.ru
Оборудование для паркета, станки для его производства
Во все времена паркетный пол был желанным покрытием, о котором мечтали и грезили. Но только в последнее время он действительно широко распространился и стал вхож в дома и квартиры по всему миру. А все потому, что красота, надежность, долговечность и экологичность выгодно выделяют его на фоне конкурентов.
Массовое производство паркетной доски невозможно без применения соответствующего оборудования и специализированных станков, которые появились относительно недавно. Вообще, производство данного напольного покрытия – сложнейший комплексный технологический процесс. Он включает в себя следующие стадии:
- Заготовка сырья, в качестве которого выступает круглый лес;
- Распиловка заготовок при помощи спецоборудования, получения досок;
- Просушивание досок в сушильных камерах;
- Роспуск готовых досок на бруски при помощи монопильных станков;
- Предварительная обработка при помощи форматно-раскроечных и поперечно-распиловочных станков;
- Высокоточная чистовая обработка на автоматизированных паркетных линиях;
На каждом этапе попутно производится контроль за качеством продукции при помощи различного измерительного инструмента и оборудования.
Именно на последнем этапе определяется качество будущего паркета. Оно зависит в первую очередь от качества и технологичности станков для производства планок. Например, лазерная обработка ускоряет процесс, но существенно снижает качество паркетных досок из-за опаленных краев.
На современных производствах на последнем этапе используются паркетные линии. Каждая такая линия состоит из следующих узлов: автоматического аппарата подачи, строгально-фрейзерного паркетного станка, ленточного конвейера, транспортировочного и подающего оборудования, а также двустороннего торцовочного станка. Успешная работа лини зависит от слаженной работы всех ее узлов.
На производстве используется только высококачественная крепкая древесина, которая позволяет получить действительно долговечный и износостойкий паркет. А, варьируя входные параметры оборудования, можно получать доски различных размеров и характеристик.
Готовые половицы проходят тщательный контроль качества поверхности, внешнего вида и точности распила. Затем они сортируются на специальном оборудовании, упаковываются в картонные ящики и оборачиваются полиэтиленом для защиты от влаги и механических повреждений.
parket.laminat-gid.ru