состав, свойства, виды и применение. Состав нержавеющей стали
Многие знают, что сталь — это продукт, получаемый в процессе плавки других элементов. Но каких? Что входит в состав стали? На сегодняшний день эта субстанция представляет собой деформируемый сплав железа с углеродом (его количество составляет 2,14%), а также малой долей других элементов.
Общие сведения
Стоит отметить, что сталью называют сплав, имеющий именно до 2,14% углерода в своем составе. Сплав же, в котором есть более 2,14% углерода, уже называется чугуном.
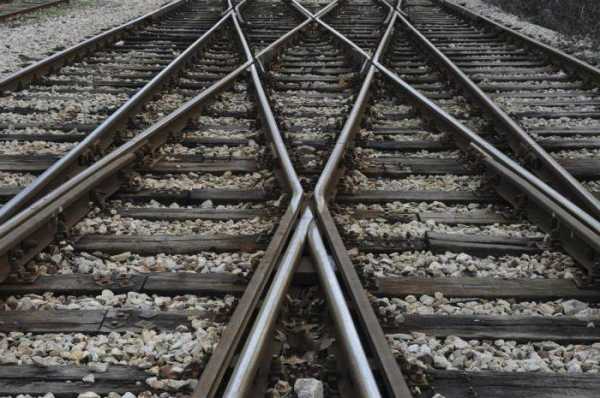
Известно, что состав углеродистой стали и обычной неодинаков. Если в обычный субстрат входит углерод и другие легирующие (улучшающие) компоненты, то в углеродистом продукте легирующих элементов нет. Если же говорить о легированной стали, то ее состав намного богаче. Для того чтобы улучшить эксплуатационные характеристики данного материала, в его состав добавляют такие элементы, как Cr, Ni, Mo, Wo, V, Al, B, Ti и др. Важно отметить, что наилучшие свойства этой субстанции обеспечиваются именно за счет добавления легированных комплексов, а не одного или двух веществ.
Классификация
Провести классификацию рассматриваемого нами материала можно по нескольким показателям:
- Первый показатель — это химический состав стали.
- Второй — это микроструктура, которая также очень важна.
- Конечно же, стали отличаются по своему качеству и способу получения.
- Также каждый вид стали имеет свое применение.

Более подробно состав можно рассмотреть на примере химического состава. По этому признаку различают еще два вида — это легированные и углеродистые стали.
Среди углеродистых сталей существуют три разновидности, главное отличие которых заключается в количественном содержании углерода. Если в состав субстанции входит менее 0,3% углерода, то ее относят к малоуглеродистой. Содержание этого вещества в районе от 0,3% до 0,7% переводит конечный продукт в разряд среднеуглеродистых сталей. Если же сплав содержит более 0,7% углерода, то сталь относится к разряду высокоуглеродистых.
С легированными сталями дела обстоят примерно также. Если в составе материала содержится менее 2,5% легирующих элементов, то он считается малолегированным, от 2,5% до 10% — среднелегированным, а от 10% и выше — высоколегированным.
Микроструктура
Микроструктура стали отличается в зависимости от ее состояния. Если сплав является отожженным, то его структура будет делиться на карбидную, ферритную, аустенитную и так далее. При нормализованной микроструктуре субстанции, продукт может быть перлитным, мартенситным или аустенитным.
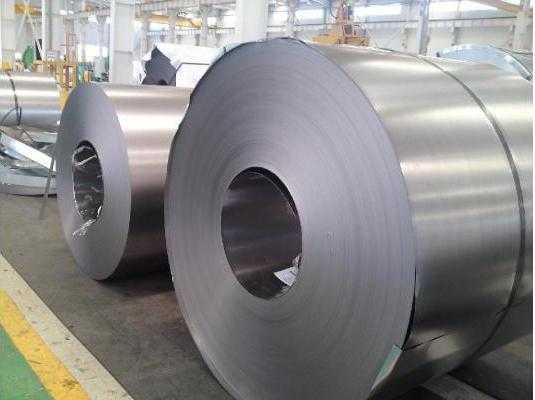
Состав и свойства стали определяют принадлежность продукта к одному из этих трех классов. Наименее легированные и углеродистые стали — это перлитный класс, средние относятся к мартенситному, а высокое содержание легирующих элементов или углерода переводит их в разряд аустенитных сталей.
Производство и качество
Важно отметить, что такой сплав, как сталь, может включать и некоторые негативные элементы, большое содержание которых, ухудшает показатели продукта. К таким веществам относят серу и фосфор. В зависимости от содержания этих двух элементов состав и виды стали разделяют на следующие четыре категории:
- Рядовые стали. Это сплав обыкновенного качества, содержит до 0,06% серы и до 0,07% фосфора.
- Качественные. Содержание вышеуказанных веществ в этих сталях снижается до 0,04% серы и 0,035% фосфора.
- Высококачественные. Содержат всего лишь до 0,025% как серы, так и фосфора.
- Высшее качество сплаву присваивается в том случае, если процентный показатель содержания серы не более чем 0,015, а фосфора — не более 0,025%.

Если говорить о процессе производства рядового сплава, то чаще всего его получают в мартеновских печах или же в бессмеровских, томасовских конвертерах. Разлив данного продукта производится в большие слитки. Важно понимать, что состав стали, ее строение, а также качественные характеристики и свойства определяются именно способом ее изготовления.
Для получения качественной стали также используются мартеновские печи, однако к процессу плавки здесь предъявляют более строгие требования, чтобы получить качественный продукт.
Плавка же высококачественных сталей осуществляется лишь в электропечах. Это объясняется тем, что применение этого типа промышленного оборудования гарантирует практически минимальное содержание неметаллических добавок, то есть снижает процентное соотношение серы и фосфора.
Для того чтобы получить сплав особо высокого качества, прибегают к методу электрошлакового переплава. Производство этого продукта возможно лишь в электропечах. После окончания процесса изготовления эти стали всегда получаются только легированными.
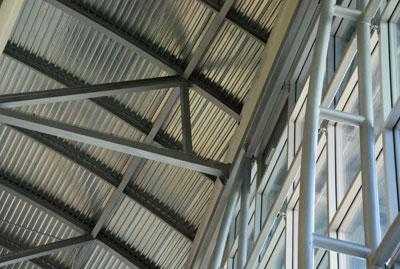
Виды сплавов по применению
Естественно, что изменение состава стали сильно влияет на эксплуатационные характеристики этого материала, а значит меняется и сфера его использования. Существуют конструкционные стали, которые могут применяться в строительстве, холодной штамповке, а также могут быть цементируемыми, улучшаемыми, высокопрочными и так далее.
Если говорить о строительных сталях, то к ним чаще всего относят среднеуглеродистые, а также низколегированные сплавы. Так как применяются они в основном для возведения зданий, то наиболее важной характеристикой для них является хорошая свариваемость. Из цементируемой стали чаще всего изготавливаются различные детали, основным предназначением которых являются работа в условиях поверхностного износа и динамическая нагрузка.
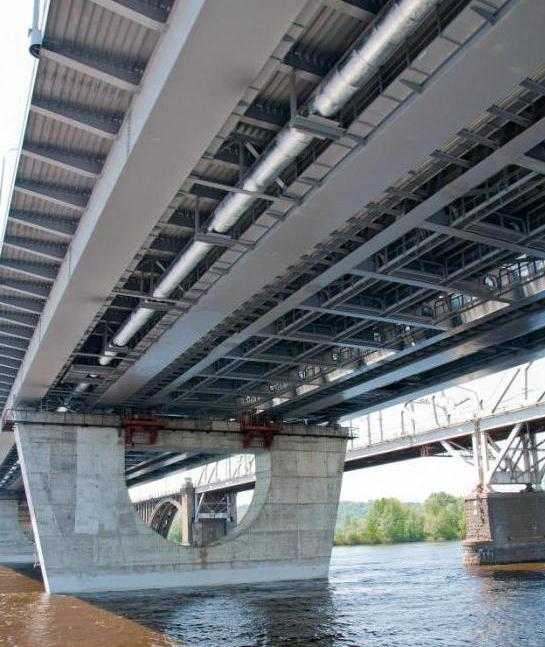
Другие стали
К другим типам стали можно отнести улучшаемую. Этот вид сплава используют только после проведения термообработки. Сплав подвергается воздействию высоких температур для закалки, а после этого подвергается отпуску в какой-либо среде.
К типу высокопрочных сталей относят те, у которых после подбора химического состава, а также после прохождения термообработки прочность достигает практически максимума, то есть примерно вдвое больше, чем у обычного типа этого продукта.
Можно выделить также пружинные стали. Это сплав, который в результате своего производства получил наилучшие качества по пределу упругости, сопротивлению нагрузкам, а также усталости.
Состав нержавеющей стали
Нержавеющая сталь относится к типу легированных. Основное ее свойство — это высокое сопротивление коррозии, которое достигается за счет добавления такого элемента, как хром, в состав сплава. В некоторых ситуациях вместо хрома может быть использован никель, ванадий или марганец. Стоит отметить, что при плавке материала и добавлении в него нужных элементов, он может получить свойства одной из трех марок нержавеющей стали.
Состав этих видов сплава, конечно же, отличается. Самыми простыми считаются обычные сплавы с повышенной устойчивостью к коррозии 08 Х 13 и 12 Х 13. Последующие два типа этого коррозионностойкого сплава, должны обладать высоким сопротивлением не только при нормальных, но и при повышенных температурах.
fb.ru
50. Автоматные стали. Состав, применение:
Стали, используемые при изготовлении деталей резанием на машиностроительных заводах, должны обладать:
• хорошей поверхностью резания;
• ломкой стружкой;
• хорошей теплопроводностью;
• малой прочностью (НВ).
Такие стали называются автоматными. Они используются на автоматизированных линиях, где смена резцов и сверл происходит без участия человека. В состав таких сталей вводят элементы: S, P, Si, Mn, Se, Te.
Эти элементы улучшают обработку резанием при комплексном легировании, снижается при этом расход инструмента (в 2 – 3 раза), сверл, резцов.
Маркируются стали буквой «А» – автоматные и цифрами, показывающими содержание углерода (А20 – 0,2 % С).
54. Пружинные стали. То. Маркировка:
Общая характеристика: сталь рессорно-пружинная, малочувствительна к флокенообразованию, склонна к отпускной хрупкости при содержании Mn≥1%, не применяется для сварных конструкций. Плотность при 20°С — 7,81х10³кг/м³. Модуль нормальной упругости при 20°С — 215 Гпа. Удельная теплоёмкость при 20-100°С — 490 Дж/(кг·°С) . Пружинная сталь содержит 0,5-0,75% углерода, до 2,8% кремния, до 1,7% никеля и по 1,2% ванадия, вольфрама, марганца и хрома.
Они работают в области упругой деформации металла под воздействием циклических нагрузок. Поэтому они должны иметь высокое значение предела упругости, текучести, выносливости при необходимости пластичности и высоком сопротивлении хрупкому разрушению.
Маркировка и основные характеристики:
Марки пружинных сталей:
· 50ХГ | · 50ХГА | · 50ХГФА | · 50ХСА |
· 50ХФА | · 51ХФА | · 55С2 | · 55С2А |
· 55С2ГФ | · 55ХГР | · 60Г | · 60С2 |
· 60С2А | · 60С2Г | · 60С2Н2А | · 60С2ХА |
· 60С2ХФА | · 65 | · 65Г | · 65ГА |
· 65С2ВА | · 68А | · 68ГА | · 70 |
· 70Г | · 70С2ХА | · 70С3А | · 75 |
· 80 | · 85 |
|
55. Подшипниковые стали. То. Маркировка:
Легированные стали, используемые для производства подшипников качения. Обычно производятся из высокоуглеродистых (1,00 %) и низкоуглеродистых (0,20 %) сталей. Высокоуглеродистые стали используются после индукционной поверхностной закалки. Низкоуглеродистые стали цементируют, чтобы обеспечить необходимую поверхностную твердость при сохранении основных свойств.
Подшипниковую сталь применяют главным образом для изготовления шариков, роликов и колец подшипников. В процессе работы эти элементы подшипника находятся под воздействием высоких знакопеременных напряжений. Каждый участок рабочей поверхности шарика или ролика и дорожки колец испытывает многократное нагружение, распределяющееся в пределах очень небольшой опорной поверхности.
Вредными примесями для шарикоподшипниковых марок стали являются фосфор, медь и никель. Фосфор увеличивает склонность стали к образованию крупнозернистой структуры при нагреве, повышает хрупкость стали и уменьшает ее прочность на изгиб.
Технология производства подшипниковой стали в кислородных конвертерах аналогична технологии выплавки рельсовой стали. Для повышения эффективности дефосфорации высокоуглеродистого металла плавку ведут с промежуточным скачиванием подвижного основного шлака содержащего 12 – 14% FeO, сформированного в результате присадок извести и плавикового шпата в первые 6 – 8 минут продувки кислородом при большой высоте фурмы над уровнем ванны. После скачивания первого шлака наводят новый присадками извести и плавикового шпата.
Маркировка: Подшипниковые стали по ГОСТ 801 — 78 обозначаются так же, как и легированные с буквой Ш в начале наименования. Подшипниковую сталь изготовляют марок ШХ15, ШХ4, ШХ15СГ и ШХ20СГ диаметром или толщиной до 250 мм. Маркируются подшипниковые стали буквами Ш ( шарикоподшипниковая), X ( хромистая) и числами, показывающим содержание хрома в десятых долях процента. Применяются стали ШХ4, ШХ9, ШХ15, а также ШХ15СГ и ШХ20СГ, легированные дополнительно кремнием и марганцем. Чем больше содержание легирующих элементов, тем для более крупных шариков и роликов можно использовать данную сталь.
Содержание углерода в подшипниковых сталях составляет около 1%. С увеличением содержания хрома и легирующих элементов увеличивается глубина прокаливаемости, т.е. увеличивается возможность изготовления из них деталей большего размера. Поставляется по ГОСТ 801-78.
Примеры маркировки:
ШХ6 — шарикоподшипниковая сталь, содержащая 1% углерода и 0,6% хрома;
ШХ15СГ — шарикоподшипниковая сталь; содержащая 1% углерода, 1,5% хрома, кремния и марганца до 1%.
studfiles.net
Медицинская сталь (хирургическая): состав, применение, свойства сплава
Медицинская сталь (или как ее еще называют – хирургическая) имеет особый сплав, который обладает определенными свойствами, необходимыми для применения в лечебном деле. Существует несколько марок, каждая из которых используется в той или иной медицинской сфере (хирургия, стоматология, травматология и т.д.).
Особенности медицинской стали
Для начала сразу определимся с понятиями. Сталь – это не железо, а его сплав с углеродом. Железо и углерод, по сути, это полезные ископаемые (минералы), добываемые из земли. Нагревая их до предельных температур и смешивая в определенных пропорциях с добавлением других элементов, и получают сплавы с самыми разными свойствами. Например, инструментальная сталь получается путем добавления в железо более 0,7% углерода. И она обладает отличными прочностными характеристиками.
Хирургическая сталь должна обладать коррозионной стойкостью. В противном случае скальпель или какой-нибудь зажим заржавеет спустя несколько применений. Опасность в том, что процесс коррозии начнется незаметно для глаза человека: на поверхности инструмента или посуды появятся трещины, в которые будет попадать пыль и микробы. А это чревато инфицированием.
Кстати! Понятие «медицинская сталь» подразумевает обобщенное название сотен марок высококачественных и дорогостоящих сплавов, применяемых в медицине, а также в некоторых других сферах (ювелирное дело, изготовление оружия).
Состав сплавов для хирургической стали
Но обычная нержавеющая сталь тоже не годится для изготовления медицинских инструментов и оборудования. Важны и другие свойства, которых добиваются путем добавления в сплав различных легирующих элементов. Для таких целей применяют медицинский сплав, преимущественно, молибден, хром и никель.
Молибденовый сплав
Из него изготавливают оборудование и инструментарий (скальпели, фрезы, стоматологические боры), а также высококачественную посуду, применяемую в медицинских целях. Молибден значительно улучшает механические прочностные характеристики стали: она становится устойчива к перепадам температур, сохраняя первичные свойства. Т.е., если даже инструмент сильно перегреть или переохладить, он не станет более хрупким и не будет подвергаться коррозии.
Количество молибдена в хирургической стали может варьироваться от 0,2 до 0,5%. Этого достаточно для обеспечения необходимой прочности и стойкости. Молибден – достаточно дорогой легирующий элемент, и увеличение его содержания в составе сплава повышает стоимость готового материала. Но все затраты оправдывают себя, когда речь идет о здоровье и жизни пациентов.
Хромоникелевый сплав
Идет на изготовление стоматологических и хирургических инструментов, посуды, оборудования. Главное свойство хромоникелевой стали – отличная стойкость к коррозии и окислению. Из нее делают, например, брекеты, которые человек может носить несколько лет. При этом замочки не заржавеют, во рту не будет ощущаться привкуса металла и т.д.
Самая популярная в медицине марка так и называется: сталь 18/10, где 18 – это процентное содержание хрома, 10 – процент никеля. Также она содержит 0,12% углерода. Все это придает стальным приборам высокую плотность (на их поверхности нет микропор, через которые могли бы попасть микробы и пыль) и твердость (поверхность не подвержена сколам и царапинам).
Ферритно-хромистый сплав
Сфера его применения – приборы и оборудование, часто подвергающееся воздействию высоких температур. Из ферритно-хромистой стали делают стерилизационные емкости для кипячения, а также стоматологические протезы, некоторые приборы. Дополнительно она обладает высокой пластичностью и длительным сроком службы.
От процентного содержания хрома в такой стали зависит предельная температура готового изделия. Максимально она достигает 1050 градусов. Если дополнительно легировать сплав молибденом и никелем, получится смешанная марка, которая будет выдерживать до 600 градусов.
Кстати! Лезвия некоторых инструментов обрабатывают дополнительно, например, алмазным напылением. Это позволяет придать им еще большую твердость и прочность, и, соответственно, повышает стоимость.
Изделия из хирургической стали
Хирургическая сталь фигурирует и в ювелирном деле. О ней наверняка слышали девушки, у которых проколоты уши. Первые серьги должны быть сделаны именно из этой стали, потому что они не вызывают кожных реакций; не ржавеют и надолго сохраняют блеск; достойно смотрятся (переливаются, сверкают) и напоминают драгоценные украшения. Когда ушки заживают, можно переходить на золото или серебро, хотя многие остаются верны стальным украшениям. По тем же причинам бусины для пирсинга тоже делают из медицинской стали.
Коллекционеры и просто любители холодного оружия отличного качества часто заказывают себе клинки из хирургической стали. Ведь хороший нож – это тот, который устойчив к агрессивным средам, нехрупкий, легко затачивается и долго служит. Все эти свойства присущи медицинским сплавам, поэтому самые лучшие ножи делают из них.
Основные свойства хирургической стали
Подведем итоги и выделим 5 самых главных отличительных свойств, которыми обладает медицинская сталь.
- Стойкость к окислению и коррозии.
- Плотность и отсутствие микропор на поверхности.
- Легкость затачивания (качественный скальпель прорезает кожные покровы, как горячий нож масло).
- Отсутствие токсичности, несмотря на присутствие легирующих элементов.
- Гипоаллергенность.
Чтобы стальные инструменты, используемые в хирургии и стоматологии, прослужили еще дольше, соблюдаются специальные правила ухода за ними. Для их мытья используются специальные растворы и материалы, никаких металлических мочалок: только фланелевые или поролоновые губки. Контролируется длительность пребывания инструментария в растворах и способ сушки. Хранятся скальпели, фрезы, зонды и другие инструменты в закрытых стерильных биксах, что обеспечивает еще большую защиту от внешней среды и продление свойств.
medoperacii.ru
Основные свойства и характеристики стали
В промышленном производстве для создания наиболее качественных материалов очень часто используют комбинации из нескольких химических элементов. Особенно распространен такой подход в металлургии, где получаемые сплавы способны работать в таких условиях, которые неподвластны чистым металлам.
Соединения нескольких элементов позволяет добиться уникальных свойств, которые необходимо в той или иной отрасли. Одним из наиболее распространенных сплавов является сталь. Она получается в результате соединения железа с углеродом. Также в массовую долю материала входит незначительное количество примесей. При необходимости в сплав вводят легирующие присадки или покрывают поверхность металла защитным слоем.
Химический состав стали
Свойства и характеристики стали зависят от количественного состава химических элементов в ее структуре. Углерод придает материалу твердости и вязкости, но его повышенное содержание приводит к хрупкости и ухудшает свариваемость. Наиболее качественная сталь получается после обработки отжигом, когда углерод внедряется в структуру металлической решетки железа на молекулярном уровне и образует устойчивое соединение цементит. Содержание кремния в сплаве повышает текучесть и прочность, а также упругость. Но избыток этого элемента ухудшает свариваемость и ударную вязкость. Марганец массовой долей до 2% позволяет повысить прочность материала. При большем процентном содержании сварка становится затруднительной.
Хром защищает сталь от окисления и значительно продляет срок ее эксплуатации. Но при неправильной термической обработке образует карбид, который препятствует сварке. Никель улучшает пластичность, вязкость и ковкость, а также является одним из немногих элементов, повышенное содержание которых не приводит к побочным эффектам. Молибден повышает термическую стойкость стали, а также предельно допустимые нагрузки, поэтому, активно используется в качестве присадок в конструкционных сплавах.
Ванадий улучшает вязкость и упругость, активно способствует процессу закалки, но ухудшает свариваемость. Вольфрам добавляет материалу твердости и стойкости при работе с высокими температурами. Титан повышает коррозийную стойкость стали, но его избыток может приводить к горячим трещинам при сварке. Медь повышает коррозионную стойкость и ковкость металла и не несет негативных эффектов при избытке. Кроме перечисленных элементов, наделяющих сталь положительными свойствами, есть и вещества, чье присутствие несет только негативную нагрузку.
Сера повышает ломкость материала при высоких температурах и затрудняет свариваемость. Фосфор влияет на повышение параметра ломкости при нормальных температурах и тоже ухудшает свариваемость. Азот, кислород и водород отрицательно влияют на прочность и приводят к быстрому старению стали. Содержание негативных элементов должно сводиться к минимуму, чтобы качество материала удовлетворяло потребностям рынка.
Характеристики стали
Твердость стали зависит от массовой доли углерода, а также количества специальных присадок. В основном твердые материалы используются в тех случаях, когда они не будут находиться под воздействием динамической нагрузки, так как с твердостью обычно повышается и хрупкость сплава. Предел прочности стали на растяжение составляет 60 килограммосил на миллиметр квадратный. Остальные значения прочностей напрямую зависят от марки материала. Стойкости к определенному виду негативного воздействия достигаются при помощи закалки металла или введения в сплав нужных присадок.
Предел прочности стали всегда отражается в маркировке, чтобы покупатель мог быстро выбрать нужный ему материал. Удельное сопротивление стали варьируется от 0,103 до 0,137 Ом*миллиметр в квадрате/метр. Величина зависит от количественного содержания химических элементов в сплаве. Для электротехнических сталей показатель сопротивления составляет 0,25-0,6 Ом*миллиметр в квадрате/метр. Столь высокое значение по сравнению с обычной сталью объясняется условиями эксплуатации и соответствует техническим требованиям. Расчетное сопротивление стали может быть разным даже для одной партии изделий, так как количество примесей распределяется не равномерно по всей структуре сплава.
Стальные проводники на практике применяются очень редко, так как есть металлы, обладающие гораздо лучшими параметрами, необходимыми для использования в электротехнике. А вот электротехническая сталь является одним из основных материалов, применяемых при изготовлении корпусов электроприборов и трансформаторов. Теплопроводность стали находится на высоком уровне, что позволяет с успехом использовать материал в отопительных системах. С ростом температуры этот показатель несколько снижается, но общие потери не критичны по сравнению с затратами энергии. Конечно, есть металлы и сплавы с гораздо более высокими параметрами теплопроводности, но их использование является нерентабельным ввиду больших затрат на их производство.
Удельная теплоемкость стали составляет 0,462 килоджоуля/килограмм*Кельвин. Это является неплохим показателем для металла. Данная характеристика показывает, сколько тепловой энергии необходимо передать телу, чтобы его температура изменилась на один градус. То есть, чем меньше этот показатель, тем быстрее нагревается вещество. Фактическое значение теплоемкости стали позволяет еще раз доказать оправданность ее использования в отопительных сетях. К тому же сталь очень хорошо сохраняет полученное тепло и медленно остывает, так что на поддержание температуры на нужном уровне понадобится меньше топлива.
Коэффициент трения сталь-сталь в состоянии покоя составляет 0,15 без использования смазки и 0,1 с ней. При скольжении этот параметр составит 0,15 и 0,05 соответственно. Химические свойства стали зависят от количественного и качественного содержания элементов в сплаве. При необходимости эксплуатации материала в агрессивной среде в его состав вводятся дополнительные присадки, позволяющие не допустить или сильно замедлить протекания разрушительных химических реакций.
promplace.ru
Внимание! Если Вы обнаружили ошибку на сайте, то выделите ее и нажмите Ctrl+Enter.
|
|
www.metotech.ru
состав, свойства, виды и применение. Состав нержавеющей стали
Многие знают, что сталь — это продукт, получаемый в процессе плавки других элементов. Но каких? Что входит в состав стали? На сегодняшний день эта субстанция представляет собой деформируемый сплав железа с углеродом (его количество составляет 2,14%), а также малой долей других элементов.
Стоит отметить, что сталью называют сплав, имеющий именно до 2,14% углерода в своем составе. Сплав же, в котором есть более 2,14% углерода, уже называется чугуном.
Известно, что состав углеродистой стали и обычной неодинаков. Если в обычный субстрат входит углерод и другие легирующие (улучшающие) компоненты, то в углеродистом продукте легирующих элементов нет. Если же говорить о легированной стали, то ее состав намного богаче. Для того чтобы улучшить эксплуатационные характеристики данного материала, в его состав добавляют такие элементы, как Cr, Ni, Mo, Wo, V, Al, B, Ti и др. Важно отметить, что наилучшие свойства этой субстанции обеспечиваются именно за счет добавления легированных комплексов, а не одного или двух веществ.
Классификация
Провести классификацию рассматриваемого нами материала можно по нескольким показателям:
- Первый показатель — это химический состав стали.
- Второй — это микроструктура, которая также очень важна.
- Конечно же, стали отличаются по своему качеству и способу получения.
- Также каждый вид стали имеет свое применение.
Более подробно состав можно рассмотреть на примере химического состава. По этому признаку различают еще два вида — это легированные и углеродистые стали.
Среди углеродистых сталей существуют три разновидности, главное отличие которых заключается в количественном содержании углерода. Если в состав субстанции входит менее 0,3% углерода, то ее относят к малоуглеродистой. Содержание этого вещества в районе от 0,3% до 0,7% переводит конечный продукт в разряд среднеуглеродистых сталей. Если же сплав содержит более 0,7% углерода, то сталь относится к разряду высокоуглеродистых.
С легированными сталями дела обстоят примерно также. Если в составе материала содержится менее 2,5% легирующих элементов, то он считается малолегированным, от 2,5% до 10% — среднелегированным, а от 10% и выше — высоколегированным.
Микроструктура
Микроструктура стали отличается в зависимости от ее состояния. Если сплав является отожженным, то его структура будет делиться на карбидную, ферритную, аустенитную и так далее. При нормализованной микроструктуре субстанции, продукт может быть перлитным, мартенситным или аустенитным.
Состав и свойства стали определяют принадлежность продукта к одному из этих трех классов. Наименее легированные и углеродистые стали — это перлитный класс, средние относятся к мартенситному, а высокое содержание легирующих элементов или углерода переводит их в разряд аустенитных сталей.
Производство и качество
Важно отметить, что такой сплав, как сталь, может включать и некоторые негативные элементы, большое содержание которых, ухудшает показатели продукта. К таким веществам относят серу и фосфор. В зависимости от содержания этих двух элементов состав и виды стали разделяют на следующие четыре категории:
- Рядовые стали. Это сплав обыкновенного качества, содержит до 0,06% серы и до 0,07% фосфора.
- Качественные. Содержание вышеуказанных веществ в этих сталях снижается до 0,04% серы и 0,035% фосфора.
- Высококачественные. Содержат всего лишь до 0,025% как серы, так и фосфора.
- Высшее качество сплаву присваивается в том случае, если процентный показатель содержания серы не более чем 0,015, а фосфора — не более 0,025%.
Если говорить о процессе производства рядового сплава, то чаще всего его получают в мартеновских печах или же в бессмеровских, томасовских конвертерах. Разлив данного продукта производится в большие слитки. Важно понимать, что состав стали, ее строение, а также качественные характеристики и свойства определяются именно способом ее изготовления.
Для получения качественной стали также используются мартеновские печи, однако к процессу плавки здесь предъявляют более строгие требования, чтобы получить качественный продукт.
Плавка же высококачественных сталей осуществляется лишь в электропечах. Это объясняется тем, что применение этого типа промышленного оборудования гарантирует практически минимальное содержание неметаллических добавок, то есть снижает процентное соотношение серы и фосфора.
Для того чтобы получить сплав особо высокого качества, прибегают к методу электрошлакового переплава. Производство этого продукта возможно лишь в электропечах. После окончания процесса изготовления эти стали всегда получаются только легированными.
Виды сплавов по применению
Естественно, что изменение состава стали сильно влияет на эксплуатационные характеристики этого материала, а значит меняется и сфера его использования. Существуют конструкционные стали, которые могут применяться в строительстве, холодной штамповке, а также могут быть цементируемыми, улучшаемыми, высокопрочными и так далее.
Если говорить о строительных сталях, то к ним чаще всего относят среднеуглеродистые, а также низколегированные сплавы. Так как применяются они в основном для возведения зданий, то наиболее важной характеристикой для них является хорошая свариваемость. Из цементируемой стали чаще всего изготавливаются различные детали, основным предназначением которых являются работа в условиях поверхностного износа и динамическая нагрузка.
Другие стали
К другим типам стали можно отнести улучшаемую. Этот вид сплава используют только после проведения термообработки. Сплав подвергается воздействию высоких температур для закалки, а после этого подвергается отпуску в какой-либо среде.
К типу высокопрочных сталей относят те, у которых после подбора химического состава, а также после прохождения термообработки прочность достигает практически максимума, то есть примерно вдвое больше, чем у обычного типа этого продукта.
Можно выделить также пружинные стали. Это сплав, который в результате своего производства получил наилучшие качества по пределу упругости, сопротивлению нагрузкам, а также усталости.
Состав нержавеющей стали
Нержавеющая сталь относится к типу легированных. Основное ее свойство — это высокое сопротивление коррозии, которое достигается за счет добавления такого элемента, как хром, в состав сплава. В некоторых ситуациях вместо хрома может быть использован никель, ванадий или марганец. Стоит отметить, что при плавке материала и добавлении в него нужных элементов, он может получить свойства одной из трех марок нержавеющей стали.
Состав этих видов сплава, конечно же, отличается. Самыми простыми считаются обычные сплавы с повышенной устойчивостью к коррозии 08 Х 13 и 12 Х 13. Последующие два типа этого коррозионностойкого сплава, должны обладать высоким сопротивлением не только при нормальных, но и при повышенных температурах.
autogear.ru
Сталь: состав, свойства, виды и применение. Состав нержавеющей стали
Многими людьми в обыденной речи часто употребляются понятия «сталь» и «железо», как синонимы. На практике они существенно отличаются друг от друга.
Что называется сталью
Сталью называют один из самых распространенных металлических сплавов. Он широко применяется при производстве различных машин, механизмов и приборов. Без нее немыслимо производство автомобилей и судов, железнодорожных вагонов и локомотивов. Стальная арматура используется в строительстве, из металлических конструкций сооружаются мосты, быстро возводимые сооружения. Этот сплав создается с заранее заданными свойствами, чтобы в наибольшей степени удовлетворять качественным характеристикам конкретного изделия. Обычно сталью называют сплав, в котором более 45 процентов железа. Для прочности и твердости в него добавляется углерод и легирующие компоненты.
Высокоуглеродистая сталь идет на изготовление различных силовых пружин и амортизаторов, рессор и других упругих деталей, рассчитанных на большие нагрузки. При изготовлении высокотехнологичного оборудования и приборов из такой стали изготавливают подвески, мембраны и множество других элементов разных форм и назначения. Отличаются детали из стали с повышенным содержанием углерода тем, что они выдерживают большие постоянные, ударные или циклические нагрузки, не имея остаточной деформации. Стали, у которых содержание углерода не велико, более пластичные и вязкие. Их удобно использовать для производства штампованных деталей, например, в автомобилестроении.
Для удобства применения стали классифицируют по различным параметрам.
Так по назначению они могут быть:
- Конструкционными.
- Нержавеющими.
- Инструментальными.
- Жаропрочными.
- Морозостойкими.
Для оценки химического состава их относят к углеродистым и легированным. Первые бывают низко, средне и высокоуглеродистыми. По такому же принципу, исходя их содержания легирующих компонентов, делятся легированные стали. Стали могут различаться и по другим характеристикам (удельный вес, плотность, температура плавления, содержание хрома, молибдена, вольфрама и пр.).
Есть такой металл – железо
Железом называется элемент, менделеевской периодической системы, обозначаемый символом Fe. Этот металл широко распространен в коре нашей планеты. Полагают, что из него состоит большая часть ядра Земли. Считается, что это один из самых распространенных элементов в Солнечной системе. Представляет собой серебристо-белого цвета металл, который поддается ковке. Горит в чистом кислороде. В чистом виде встречается редко. Комплекс уникальных свойств железа и его сплавов делают этот металл важнейшим для людей. Практически наиболее применяемые его сплавы с углеродом в виде стали, в том числе с добавлением марганца, хрома, никеля и чугуна.
Оно было известно еще в четвертом тысячелетии до н.э. в виде украшений и холодного оружия, которые изготавливались из железа, содержавшегося в метеоритах. Ценилось дороже золота. Позже его научились плавить из магнетитовых песков и железной руды в вырытых в земле печах. С изобретением примитивных доменных печей с использованием воздуходувных мехов древние римляне освоили производство чугуна и стали из него.
Железо содержится в большом количестве минералов, в частности, в таких:
- Магнетит (72,4%)
- Гематит (70 %)
- Марказит ( 46,6 %)
- Сидерит ( 35 %)
- Миспикель ( 34,3 %)
- Леллингит ( 27,2 %)
В числе стран с наибольшими месторождениями железа находятся Бразилия, Австралия, США, Канада, Швеция, Венесуэла, Либерия, Украина, Франция, Индия. Первое место в мире по его запасам занимает Россия. Перспективными являются железосодержащие месторождения, обнаруженные на дне океанов.
Промышленным способом железо получается из железной руды в виде агломерата, в основном в результате доменного процесса. В доменных печах при температуре 2000 °C его сначала восстанавливают углеродом. Полученный расплав железа, называемый чугуном, перенасыщен углеродом. Для получения стали он нуждается в дальнейшей переработке. Оно получается в твердом виде и переправляется в электропечах.
В чем отличия
Сталь и железо принципиально отличаются в следующем:
- Сталь является готовым продуктом металлоплавления и может использоваться в различных целях. Железо является элементом, который выступает основой и полуфабрикатом для производства стали.
- Стали за счет изменения рецептуры и технологии ее производства, могут задаваться определенные качества, необходимые для дальнейшего производства. В железе, как химическом элементе, его качества заложены природой.
- Сталь является сплавом, а в чистом железе содержится только оно.
- По прочностным характеристикам сталь значительно превосходит железо.
- Из стали изготавливают миллионы наименований изделий, из железа – десятки.
В жизни мы постоянно сталкиваемся со сплавами, самый распространенный из которых сталь. Поэтому нет ничего удивительно, что у кого-нибудь да возникнет вопрос о том, как делают сталь?
Сталь – это один из сплавов железа и углерода, получивший широчайшее распространение в повседневной жизни. Процесс производства стали многоступенчатый и состоит из нескольких этапов: добыча и обогащение руды, получение агломерата, производства чугуна и выплавка стали.
Руда и агломерат
Месторождения руд позволяют добывать как богатые, так и бедные породы. Богатую руду можно сразу использовать как производственное сырье. Чтобы можно было выплавлять и бедную руду, ее необходимо обогатить, то есть увеличить в ней содержание чистого металла. Для этого руду измельчают и, применяя различные технологии, отделяют частицы, богатые соединениями металла. Например, для железных руд применяют магнитную сепарацию – воздействие магнитным полем на исходное сырье с целью отделение частиц богатых железом.
Получается низкодисперсионный концентрат, который спекают в более крупные куски. Результат обжига железных руд и есть агломерат. Виды агломератов получили название по основному сырью, входящему в их состав. В нашем случае это железорудный агломерат. Теперь, чтобы понять, как делают сталь, необходимо проследить дальнейший технологический процесс.
Чугун выплавляют в доменных печах, которые функционируют по принципу противотока. Загрузка агломерата, кокса и другого шихтового материала осуществляется сверху. Снизу вверх, навстречу этим материалам, поднимаются потоки раскаленного газа от сгорания кокса. Начинается череда химических процессов, в результате чего происходит восстановление железа и насыщение его углеродом. Температурный режим при этом сохраняется в районе 400-500 градусов Цельсия. В нижних частях печи, куда постепенно опускается восстановленное железо, температура увеличивается до 900-950 градусов. Образуется жидкий сплав железа с углеродом – чугун. К основным химическим характеристикам чугуна относятся: содержание углерода более 2,14 %, обязательное наличие в составе серы, кремния, фосфора и марганца. Чугун отличается повышенной хрупкостью.
Теперь мы приблизились к последнему этапу, позволяющему узнать, как делают сталь. В химическом плане сталь отличается от чугуна пониженным содержанием углерода; соответственно, основная задача производственного процесса – уменьшить содержание углерода и других примесей в основном сплаве железа. Для производства стали используют мартеновские печи, кислородные конвертеры или электропечи.
По различным технологиям расплавленный чугун продувается кислородом при очень высоких температурах. Происходит обратный процесс – окисление железа на уровне примесей, входящих в сплав. Полученный шлак в дальнейшем убирается. В результате продувки кислородом понижается содержание углерода и происходит преобразование чугуна в сталь.
В сталь могут добавляться легирующие элементы, изменяющие свойства материала. Поэтому сталью считается сплав железо-углерод с содержанием железа не менее 45 %.
Вышеописанные процессы разъяснили, как делают сталь, из каких материалов и с применением каких технологий.
СТАЛЬ. сплавы ЖЕЛЕЗА с примесью УГЛЕРОДА. Исключительная прочность стали сделала ее чрезвычайно важным материалом в строительстве и производстве товаров.
иболее распространенным видом является простая углеродная сталь, так как углерод является ее основной примесью. В такой стали содержится около 1% углерода и незначительные количества других компонентов (марганца, кремния, серы и фосфора). В ЛЕГИРОВАННОЙ СТАЛИ также содержится определенное количество углерода, но благодаря присутствию в них марганца, никеля, хрома, ванадия и молибдена, они обладают рядом индивидуальных свойств. Низколегированная сталь, в которой содержится менее 5% легирующих добавок, чрезвычайно прочна и используется в строительстве зданий, мостов и частей машин. В высоколегированной стали содержится более 5% добавок. Сюда относится НЕРЖАВЕЮЩАЯ СТАЛЬ. Впервые сталь научились производить около 2000 лет назад, но ранние МЕТОДЫ ее получения были медленными и трудоемкими, поэтому ее удавалось получить только в малых количествах. Широкомасштабное производство стали стало возможным лишь в середине XIX в. с изобретением БЕССЕМЕРОВСКОГО и МАРТЕНОВСКОГО ПРОЦЕССА. Сейчас при изготовлении стали используется КИСЛОРОДНОЕ ДУТЬЕ. Некоторые виды стали производят в ЭЛЕКТРОПЕЧИ ( в том случае, если в ее состав входят материалы, которые подверглись бы окислению в ходе других процессов производства стали).
Сталь На иллюстрации показано, как из железной руды получают обыкновенную углеродистую сталь, состоящую из чистого железа и незначительного количества углерода.
железной руде железо связано с кислородом и другими примесями, главным образом, кремнеземом. Обозначения: A) Полученное сырье — уголь, известняк и железная руда B) После первичного дробления и сортировки сырье обогащается. Уголь коксуется для того, чтобы удалить лишние вещества и примеси. Железная руда подвергается магнитному обогащению, чтобы отделить магнитную руду от немагнитной породы. Известняк обычно не содержит примесей C) Сырье дробится для того, чтобы его можно было использовать в домне D) Слишком крупное сырье возвращается для дальнейшего дробления, а подходящее для домны отправляется прямо туда. Слишком мелкая железная руда смешивается с мелким извесг-няком и коксом и сжигается для получения шлака Е) Известняк, железная руда и кокс продуваются горячим воздухом Топливная нефть сжигается при доменном дутье и воспламеняет кокс Сжигаемый кокс так сильно повышает тем пературу в центре домны, что материал в ней наполовину плавится. Горячий кокс и газы, которые образовались в результате сжигания, удаляют кислород из железной руды и образуют угарный и углекислый газы, — газообразную смесь,которая выводится через выхлопное отверстие Другая важная примесь в железной руде — это кремнезем, реагирующий с известняком. Освобожденные от кислорода железо и кремнезем собираются внизу печи. Смесь железо-кремнезем легче, чем железо, и образует слой шлака,тем самым способствуя их легкому разделению через разделяющие отверстия вверху F) Расплавленное железо поглощает лишний углерод из кокса, уровень которого должен быть понижен для того, чтобы получить годную к употреблению сталь Это происходит посредством продувания чистого кислорода по поверхности расплавленного магериала в домне. Углерод соединяется с кислородом и сгорает с образованием угарного и углекислого газов Извесшяк, скапливающийся на поверхносги расплавленного металла, поглощает много примесей, оставшихся после продувки G) Очищенная сталь с соответствующим содержанием углерода готова к разливке, а примеси остаются в шлаках
novoevmire.biz